2.2 Hazardous Materials (HAZMAT)
D.M. Donner
Hazardous materials (HAZMAT) refers to substances or materials that pose a risk to human health, the environment, or property due to their inherent physical, chemical, or biological properties.
If you are uncertain if something is a hazardous material, best practice is to treat it as one until you are able to ascertain it is not. To find out if something is a hazardous material, you should consult the Safety Data Sheet which can be obtained from the manufacturer or retailer.
Safety Data Sheets (SDS)
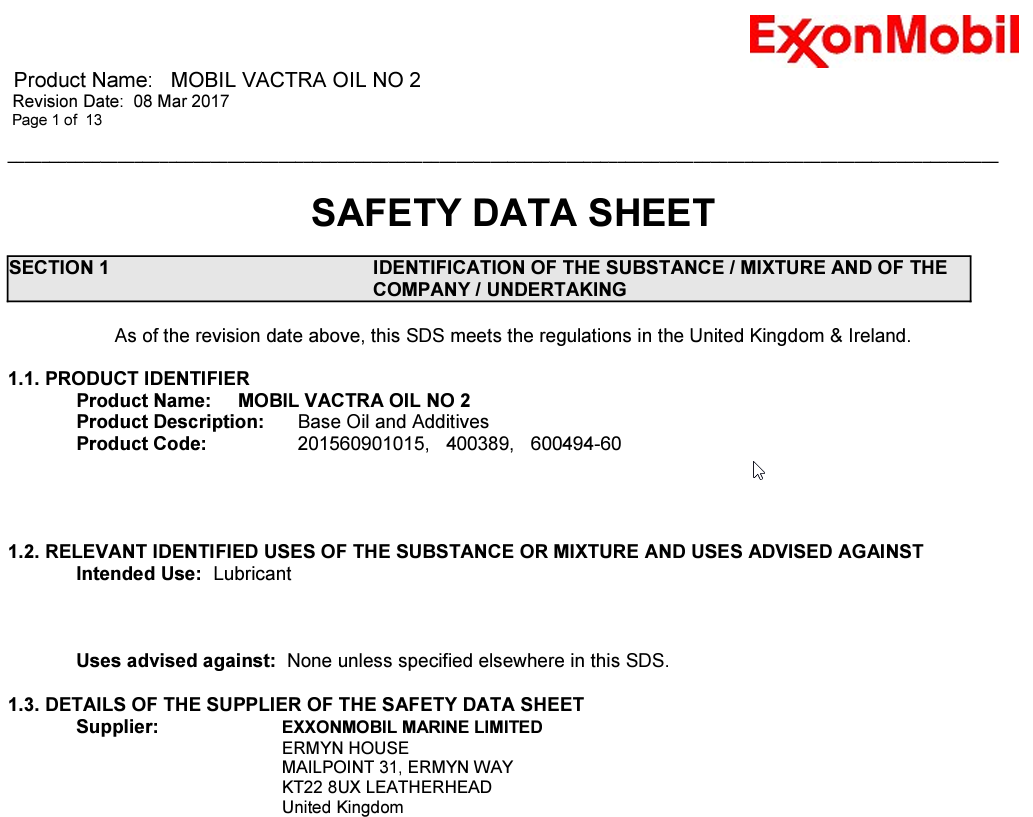
NotesAlt text: Safety Data Sheet information for Vactra No. 2 Way oil
Safety Data Sheets formerly known as Material Safety Data Sheets (MSDS), are essential documents that provide comprehensive information about hazardous chemicals or substances. These sheets are used to communicate critical safety information to employees, emergency responders, and other stakeholders who handle, store, transport, or work with potentially dangerous materials.
The SDS format is standardized and regulated by various agencies worldwide, including the Occupational Safety and Health Administration (OSHA) in the United States, the European Chemicals Agency (ECHA) in Europe, and similar agencies in other countries.
The 16 component sections of Safety Data Sheets typically include:
Identification: Essential details about the chemical, including its name, brand, manufacturer, supplier information, and emergency contact numbers
Hazard identification: The potential hazards associated with the chemical, including its physical, health, and environmental hazards. This information is crucial for understanding risks and determining appropriate safety precautions.
Composition/ingredients: The chemical ingredients and their concentration ranges. This helps users identify any substances that might cause allergies or other health concerns.
First aid measures: In case of accidental exposure or ingestion, this section outlines the immediate steps to take for providing first aid to affected individuals.
Fire-fighting measures: Appropriate fire-fighting methods and any specific hazards related to fires involving the chemical are described.
Accidental release measures: This section provides guidance on how to contain and clean up spills or leaks safely.
Handling and storage: Advice on the safe handling, storage, and transportation of the chemical to prevent accidents and exposures is provided.
Exposure controls/personal protection: Recommended exposure limits, engineering controls (e.g., ventilation), and personal protective equipment (PPE) necessary for handling the chemical safely is included.
Physical and chemical properties: Provides information on the chemical’s appearance, odor, boiling and melting points, solubility, and other relevant characteristics.
Stability and reactivity: Discusses the chemical’s stability and potential reactivity hazards, such as incompatibilities with other substances.
Toxicological information: Details potential health effects and toxicological data based on studies and known information about the chemical.
Ecological information: Discusses the potential impact of the chemical on the environment.
Disposal considerations: Offers guidance on proper disposal methods for the chemical, considering its environmental impact.
Transport information: Provides information about the safe transport of the chemical, including any regulatory requirements.
Regulatory information: Highlights relevant regulations and requirements concerning the chemical.
Other information: Additional information that may not fit into other sections, including date of preparation or revision.
Safety Data Sheets are essential tools for ensuring the safe handling and management of hazardous chemicals. Employers must make SDS accessible to their employees, and individuals should familiarize themselves with SDS before working with any potentially hazardous substance.
Hazardous Material Labeling
The standards for hazardous material labeling are primarily governed by two key systems: the Globally Harmonized System of Classification and Labeling of Chemicals, (GHS), an internationally agreed-upon system developed by the United Nations, and the Hazardous Materials Identification System, (HMIS), a hazard communication system developed by the National Paint & Coatings Association (NPCA), now known as the American Coatings Association (ACA). Both systems provide standardized labels to communicate the potential hazards of chemicals and other hazardous materials in the workplace.
Globally Harmonized System (GHS): The GHS is an internationally agreed-upon system developed by the United Nations to standardize the classification and labeling of chemicals (United Nations Economic Commission for Europe, n.d.). The GHS aims to harmonize hazard communication globally, making it easier for countries to understand and implement consistent labeling and Safety Data Sheets. GHS labels typically include the following elements:
Pictograms: Easily recognizable symbols representing the type of hazard (e.g., health hazard, flammability, corrosivity, etc.).
Signal word: A single word (either “Danger” or “Warning”) that indicates the level of severity of the hazard.
Hazard statements: Standardized phrases describing the nature of the hazard.
Precautionary statements: Recommended measures to be taken to minimize or prevent adverse effects.
GHS labels are designed to be easily understood by workers, consumers, and emergency responders worldwide.
Hazardous Materials Identification System (HMIS): The HMIS is a hazard communication system developed by the National Paint & Coatings Association (NPCA) to provide consistent hazard ratings for chemicals used in the workplace. HMIS labels use a color-coded system and include the following elements:
Hazard rating: A numerical rating from 0 to 4 indicates the degree of the hazard (0 represents minimal hazard, and 4 indicates severe hazard).
Health, flammability, and physical hazard: Each hazard category is assigned a color (blue for health, red for flammability, and yellow for physical hazards) with a corresponding symbol and label text.
Personal Protection
To keep people safe when handling hazardous materials, personal protective equipment (PPE) is essential. PPE is designed to protect people from severe injury and illness when in contact with hazardous material. It is important to choose the right equipment and use it properly.
A: Safety glasses should be worn when handling this material. This is the minimal rating given to any material.
B: Safety glasses and protective gloves should be worn when handling this material. This rating is given to materials that have the potential for skin irritation or may be harmful if absorbed through the skin.
C: Goggles, protective gloves, and a laboratory apron should be worn when handling this material. This rating is given to materials that have the potential for splashing and are listed as having a HEALTH HAZARD RATING of 2 or higher.
D: A face shield, goggles, protective gloves, a laboratory apron, and an exhaust fume hood should be used when handling this material. This rating is given to materials that are capable of detonation or explosive reactions. This rating would apply to all materials receiving a REACTIVITY HAZARD rating of 3 or 4.
E: Safety glasses, protective gloves, and an exhaust fume hood should be used when handling this material. This rating is given to materials that have the potential to release harmful vapor, mist, or dust into the air.
H: Splash goggles, a laboratory apron, protective gloves, and an exhaust fume hood should be used when handling this material. This rating is given to materials that, in addition to having the potential for releasing harmful vapor, mist, or dust into the air, also have the potential for splashing. Strong acids, strong bases, and strong organic solvents would fall into this category.
HMIS labels are commonly used in the US and are often found in conjunction with other labeling systems, such as GHS.
It’s important to note that individual countries or regulatory agencies may have specific requirements for hazardous material labeling, and employers should ensure compliance with applicable regulations when handling and labeling hazardous materials in the workplace. Both the GHS and HMIS systems are widely used and recognized, providing valuable information to help workers and emergency responders understand and respond appropriately to the hazards of chemicals and hazardous materials.
Hazardous Waste (HAZWASTE)
Managing hazardous waste is crucial to protecting human health and the environment. Hazardous waste includes materials that are toxic, flammable, corrosive, or reactive. Proper management ensures safe handling, storage, transportation, treatment, and disposal. Here is a general guide on how to manage hazardous waste:
Identify and classify waste: Determine if the waste is hazardous by assessing its characteristics (ignitability, corrosivity, reactivity, toxicity) and comparing it to regulatory definitions. Classify the waste based on its hazardous properties.
Waste minimization: Minimize waste generation by adopting practices like source reduction, process modification, or using less hazardous materials. This reduces the overall quantity of hazardous waste.
Segregation and storage: Segregate different types of hazardous waste to prevent chemical reactions and ensure compatibility. Store hazardous waste in appropriate containers that are in good condition and designed to handle the specific waste type. Label containers with clear, legible information about the waste’s contents and hazards.
Handling and transportation: Train personnel in proper handling procedures, including the use of PPE. Use suitable equipment for loading and unloading to prevent spills or accidents. Comply with transportation regulations, including proper labeling, placarding, and paperwork.
Treatment and recycling: If feasible, treat hazardous waste on-site to reduce its toxicity or volume. Explore opportunities for recycling, reusing, or reclaiming waste materials, following applicable regulations.
Disposal: Choose disposal methods based on the waste’s characteristics and regulatory requirements, such as landfilling, incineration, or deep-well injection. Ensure that disposal facilities are properly permitted and comply with environmental regulations.
Documentation and record keeping: Maintain accurate records of waste generation, handling, treatment, and disposal. Keep records for the required time period as mandated by regulations.
Training and awareness: Provide regular training to personnel involved in hazardous waste management to ensure they understand proper procedures and safety measures. Promote awareness of hazardous waste management practices throughout the organization.
Regulatory compliance: Stay informed about local, state, and federal regulations governing hazardous waste management. Obtain necessary permits and licenses for handling and disposal activities.
Emergency preparedness: Develop and communicate emergency response plans for spills, leaks, or other accidents involving hazardous waste. Provide appropriate emergency equipment, containment materials, and PPE.
Auditing and continuous improvement: Regularly audit your hazardous waste management practices to identify areas for improvement and ensure compliance. Implement corrective actions based on audit findings to enhance safety and environmental protection.
The shop supervisor can provide information relating to best practices within specific shops. Not all shops handle the information found in this chapter in the same manner. Getting to know the specific culture within a shop will assist you in understanding specific shops’ interpretation of safety guidelines.
Hazard Communication Standard
Hazard communication, HAZCOM short for hazard communication training, is a workplace safety program designed to educate employees about the potential hazards of chemicals and how to safely handle, use, and store them. The “right-to-know” standard requires employers to inform and train workers about hazardous chemicals in the work area (OSHA, n.d.). Employer responsibilities for HAZCOM are:
- Provide workers with training and information.
- Maintain a current list of hazardous materials.
- Ensure hazardous chemicals are labeled with the chemical’s identity and its hazards
- Maintain Safety Data Sheets (SDSs): formally known as Material Safety Data Sheets (MSDSs) which provide detailed information about chemical hazards, their effects, how to prevent exposure, and emergency treatment if an exposure occurs.
Attributions
- Figure 2.2: Safety Data Sheet © Exxon Mobil Corporation Used with permission.
Short for Hazardous Materials, refers to substances or materials that pose a risk to human health, the environment, or property due to their inherent physical, chemical, or biological properties.
Safety Data Sheets, formerly known as Material Safety Data Sheets (MSDS), are essential documents that provide comprehensive information about hazardous chemicals or substances.
Globally Harmonized System is an international approach to hazard communication, providing agreed criteria for classification of chemical hazards, and a standardized approach to label elements and safety data sheets.
a hazard communication system developed by the National Paint & Coatings Association (NPCA) to provide consistent hazard ratings for chemicals used in the workplace
is a workplace safety program designed to educate employees about the potential hazards of chemicals and how to safely handle, use, and store them
Please look for related terms in the Glossary