2.5 Personal Protective Equipment
D.M. Donner
Personal protective equipment (PPE) is protective clothing or equipment that protects the wearer against injury. PPE is the last line of defense from injury when all other options have been exhausted. Before selecting PPE for protection, the hazard must be evaluated for possible controls. The hierarchy of controls for hazards are: elimination, substitution, engineering controls, administrative controls, and then PPE.
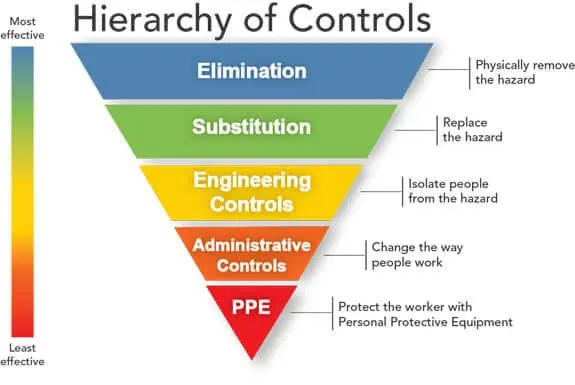
Consider workers who operate rotating equipment such as manual lathes and milling machines. One of the hazards associated with the operation of this equipment is the creation of hot and sharp metal chips caused by the cutting process. Can this hazard be eliminated from the process? If so, use that method. If not, proceed to substitution. Can another process be used that has fewer hazards? Has a new process been created that may be used in place of the current process? 3D printing and other additive methods do not have the same hazards. Next is engineering controls; can we isolate the worker from the hazards? CNC lathe and milling centers do this by creating an enclosure around the cutting operation, which solves the problem. However, this is not feasible for small quantities or repair operations. Administrative controls are processes tailored to reduce injuries. These are often referred to as best practices, and they vary from shop to shop. Using rough cutting passes on the mill, which sends the chips away from the operator, is a good best practice if possible.
Finally, we get to PPE. For the hazards that have progressed through our efforts at mitigation without a solution, we must find equipment or clothing to protect the operator. The list of PPE for manual lathes and mills includes:
- Machine shields to intercept chips coming off the cutter
- Face shields
- Eye protection
- Cotton clothing to protect the skin
Let’s take a look at PPE commonly used in the machining industry.
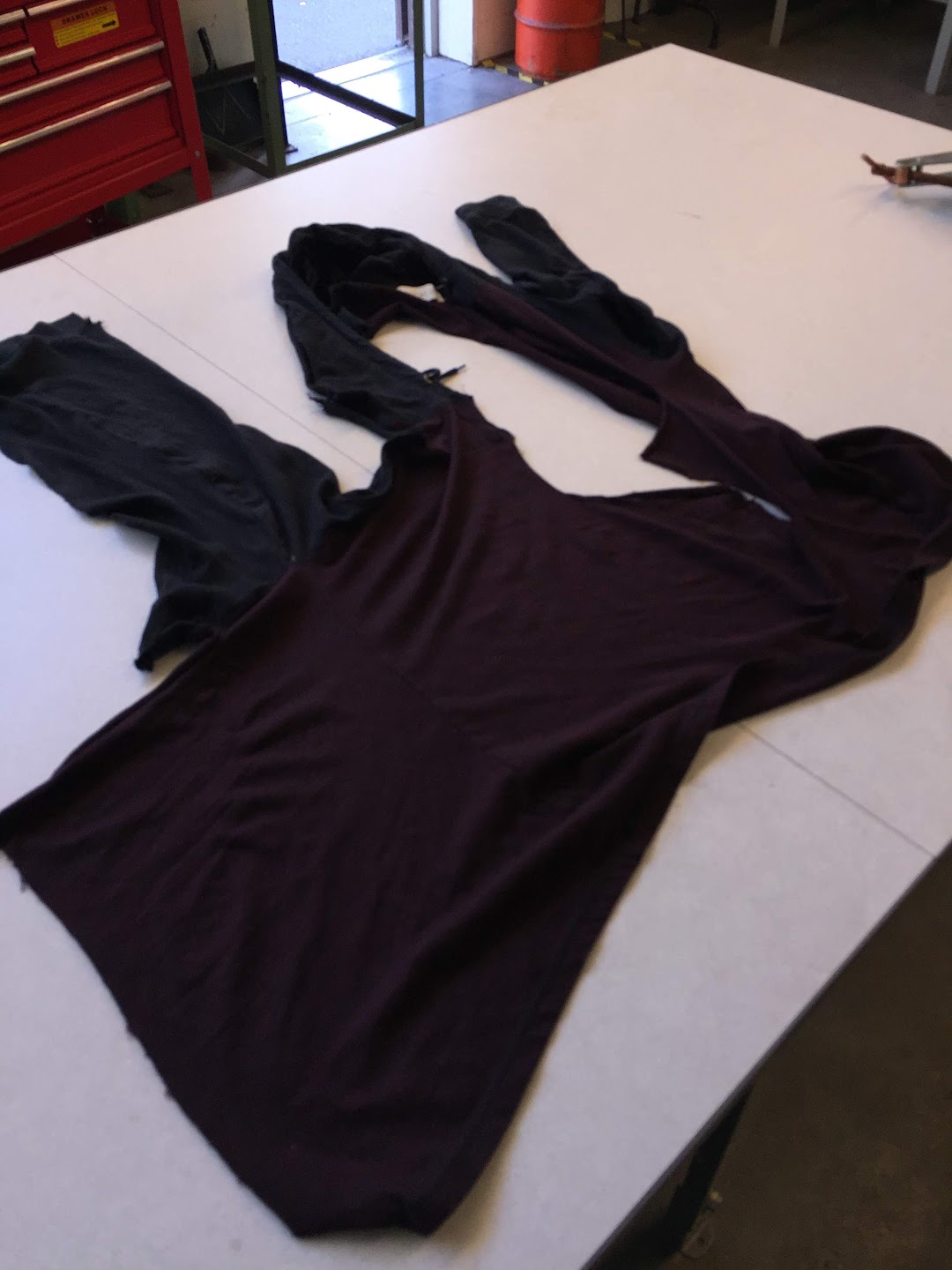
Clothing and Accessories
What you wear in a machine shop impacts your safety. Long sleeves and loose-fitting clothes such as “hoodies” can get caught in the rotating assemblies of equipment and pull you into the rotating mechanisms.
In the image above, a shirt sleeve was caught in the knurling of a part being turned on the lathe. The garment quickly wrapped around the part, and the lathe’s powerful motor tore the shirt off the operator as he braced himself against the machine.
To prevent getting caught in the rotating assemblies of machines, roll sleeves above the elbow, and do not wear gloves while operating equipment. Remove jewelry from around your neck, wrists, and hands. Tie long hair up and away from the front of your body.
Synthetic materials such as nylon and polyester will melt when in contact with hot metal chips formed during the cutting processes. Cotton is a better choice when selecting work clothes for the machinist. A close-fitting neck will also aid in preventing hot chips from contacting your neck and causing burns.
Wearing the correct footwear will protect you from several hazards, such as dropping materials on your feet, slipping on oil spills, and preventing hot metal chips from embedding in the soles of your shoes. Some shops will require steel toes, and they may offer to supplement the purchase. Leather is the best choice of shoe material, and an oil non-slip sole will help you avoid losing your footing when walking in slippery areas.
Synthetic materials found in shoes should be avoided due to the hot nature of chips that melt the materials. For convenience, an operator will often bring a second pair of shoes/boots to work to change into before heading home after work. Metal chips get embedded in the soles of your footwear and can cause damage to nice flooring found in most homes.
Hearing Protection
When choosing hearing protection, you should consider the following:
- Noise Reduction Rating (NRR): This determines the device’s ability to reduce sound exposure.
- Comfort: Hearing protection that isn’t comfortable will most likely not be worn.
- Style: Ear plugs come in several varieties, and muffs fit over the ears. These can be combined to reduce sound levels further.
Noise Reduction Rating (NRR) is a measure of the effectiveness of a hearing protection device to reduce noise levels. Higher values indicate greater noise reduction. NRR values range up to approximately 30 dB.
Technology has made advancements in noise-canceling devices that only filter out background noise and permit conversational sound. These devices may reduce some noise, but only approved hearing protection that is certified to use an NRR should be used.
The primary OSHA standard related to hearing protection is titled “Occupational Noise Exposure” (1970b). Here are some key provisions of the standard:
Permissible Exposure Limit (PEL): The PEL for occupational noise exposure is 90 decibels (dBA) as an 8-hour time-weighted average (TWA). This means that over the course of an 8-hour work shift, employees should not be exposed to noise levels exceeding 90 dBA. If noise levels exceed this limit, employers must take action to reduce noise exposure.
Action levels: OSHA has defined two action levels:
85 dBA: When employee noise exposures reach or exceed 85 dBA as an 8-hour TWA, employers are required to implement a hearing conservation program.
90 dBA: If noise exposures exceed 90 dBA as an 8-hour TWA, more stringent requirements apply for the hearing conservation program.
140 dBA: Exposure to noise greater than 140 dBA can cause permanent hearing loss.
Hearing conservation program: Employers are required to establish and maintain a hearing conservation program whenever employees are exposed to noise levels at or above the action level. The program includes noise monitoring, annual audiometric testing for exposed employees, the provision of hearing protection devices (HPDs), employee training, and recordkeeping.
Hearing Protection Devices (HPDs): When noise exposures exceed the PEL or action level, employers must provide suitable hearing protection devices (e.g., earplugs or earmuffs) to affected employees. The employer is responsible for ensuring the proper use and maintenance of the hearing protection provided.
Employee training: Employers must provide training to employees exposed to high noise levels. Training should cover the risks of noise exposure, proper use of hearing protection, the purpose and procedures of audiometric testing, and other relevant information.
Audiometric testing: Employers are required to provide free annual audiometric testing to employees exposed to noise levels at or above the action level. Audiometric testing is used to monitor changes in hearing and identify any potential hearing loss.
Health Effects of Excessive Noise Exposure.
Excessive noise exposure can have a range of negative health effects on both physical and mental well-being. The effects can vary depending on the intensity, duration, and frequency of the noise exposure, as well as individual susceptibility. Some of the health effects of excessive noise exposure include:
Hearing loss: Prolonged exposure to loud noises, especially those above 85 decibels (dB), can lead to permanent hearing loss. This is often gradual and cumulative, affecting the ability to hear high-frequency sounds.
Tinnitus: Excessive noise exposure can lead to tinnitus, the perception of ringing, buzzing, or hissing sounds in the ears. It can be temporary or chronic and can significantly affect quality of life.
Stress and anxiety: Noise pollution can cause chronic stress and anxiety These conditions are associated with an increased risk of cardiovascular diseases, high blood pressure, and other stress-related health issues.
Sleep disturbances: Noisy environments can interfere with sleep leading to difficulties falling asleep, staying asleep, or experiencing restorative sleep. This can result in fatigue, impaired cognitive function, and an overall reduced quality of life.
Cardiovascular issues: Chronic noise exposure, particularly to loud and persistent noises, has been linked to an increased risk of cardiovascular problems such as hypertension, heart disease, and stroke.
Cognitive impairment: Noise pollution can impair cognitive function and concentration. It may lead to reduced attention span, learning difficulties, and decreased performance in tasks that require focus.
Social isolation: High noise levels can lead to social isolation and communication difficulties as people may avoid noisy areas or situations where conversation is challenging.
Workplace safety: Hearing loss and excessive noise can reduce workers’ awareness of their surroundings, leading to safety hazards.
Annoyance: Excessive noise can cause annoyance and dissatisfaction, impacting overall well-being and mental health.
It is important to note that the impact of noise exposure varies depending on individual susceptibility, age, and health status. To mitigate the health effects of excessive noise exposure, individuals can take measures such as using ear protection in noisy environments, limiting exposure to loud noises, and advocating for noise reduction in communities. Public health policies and regulations related to noise control and urban planning can also play a crucial role in reducing noise pollution and its associated health impacts.
Respirator Protection
The OSHA respiratory protection standard (1970d) is designed to protect workers from harmful airborne contaminants and ensure the proper use of respirators when necessary.
Here are some key elements of respiratory protection regulations:
Written respiratory protection program: Employers must develop and implement a written respiratory protection program when respirator use is required in the workplace. This program should outline the procedures and policies related to respirator selection, fit testing, medical evaluations, training, and maintenance.
Respirator selection: Employers must ensure that the appropriate type of respirator is selected for the specific hazards present in the workplace. Different types of respirators (e.g., filtering facepiece respirators, half-face respirators, full-face respirators, and powered air-purifying respirators) may be necessary based on the nature of the airborne contaminants.
Fit testing: Employees required to use respirators must undergo fit testing to ensure that the respirator fits properly and forms an effective seal on their face. Fit testing should be conducted before the initial use of the respirator and at least annually thereafter.
Medical evaluations: Workers who are required to wear respirators must undergo a medical evaluation to determine if they are physically capable of using a respirator safely. This evaluation should be performed by a licensed healthcare professional.
Training: Employers must provide comprehensive training to employees who use respirators. The training should cover topics such as the proper use, limitations, and maintenance of respirators, as well as the potential health hazards associated with workplace contaminants.
Maintenance and cleaning: Employers are responsible for ensuring that respirators are maintained in a clean and sanitary condition. Respirators should be inspected regularly, and any damaged or malfunctioning respirators should be removed from service.
Voluntary use of respirators: If employees choose to wear respirators voluntarily (when not required by the employer), certain requirements still apply, and the employer should provide information and training on the proper use and limitations of such respirators.
It’s important to note that respiratory protection regulations may be updated or revised over time, so employers in each state should regularly check the state’s Department of Labor & Industries website for the most current and specific requirements related to respiratory protection. Additionally, employers should always follow federal OSHA standards in addition to any state-specific regulations.
Dust Mask Respirator
Dust masks are flexible paper pads held over the nose and mouth by elastic or rubber straps for personal comfort against non-toxic nuisance dust. They are not intended to provide protection from toxic airborne hazards.
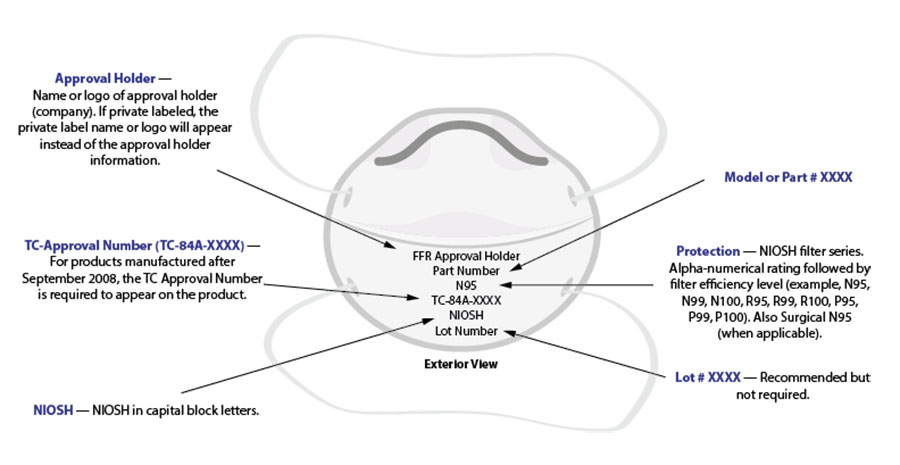
When selecting a respirator, be aware of the filtering efficiency of the mask. Quality masks are N95 rated to remove at least 95% of airborne particles when properly fitted (National Institute for Occupational Safety and Health, 2021).
If 95% filtration is all you need, the above respirator is fine. However, if you need 100% protection you must use a respirator that fits snugly on your face and permits a clean seal. These masks come in ¼ face and full face. They accept disposable cartridges designed to remove specific contaminants from the air. If your job requires this type of respirator, you will be fitted by a specialist to ensure the fit is correct.
Respirators that provide 100% protection not only filter dust particles but also provide certain chemicals and gases that purify the air before respiration.
These types of respirators only filter the air; they do not supply breathable air. If the space in which you are working does not have sufficient air, you must use a forced respirator with its own air source. These types are beyond the scope of this text.
Health Effects of Respiratory Hazards
Respiratory hazards are substances or conditions that can negatively impact the respiratory system, leading to a range of health effects. These hazards can be present in various environments, including workplaces, homes, and outdoor spaces. The health effects of respiratory hazards can vary depending on the type of hazard, the duration of exposure, and individual susceptibility. Here are some common respiratory hazards and their associated health effects:
Airborne particulate matter: Fine particles and dust present in the air can be inhaled into the respiratory system. Prolonged exposure to high levels of particulate matter is linked to respiratory conditions such as bronchitis, aggravated asthma, decreased lung function, and an increased risk of respiratory infections.
Chemical fumes and vapors: Inhalation of harmful chemicals and gases, such as volatile organic compounds (VOCs), solvents, and industrial emissions, can cause irritation of the respiratory tract, lung inflammation, and exacerbation of respiratory conditions like asthma and chronic obstructive pulmonary disease (COPD).
Occupational hazards: Workers in certain industries may be exposed to respiratory hazards like asbestos, silica dust, and other harmful substances. Prolonged exposure to these hazards can lead to occupational lung diseases such as asbestosis and silicosis.
Outdoor air pollution: Exposure to high levels of outdoor air pollutants like ozone, nitrogen dioxide, sulfur dioxide, and carbon monoxide can lead to respiratory irritation, worsened asthma symptoms, decreased lung function, and an increased risk of respiratory infections.
Respiratory infections: Exposure to respiratory hazards can weaken the immune system’s defenses, making individuals more susceptible to infections such as pneumonia, bronchitis, and influenza.
Aspiration hazards: Inhaling food, liquids, or foreign objects into the respiratory tract (aspiration) can lead to respiratory distress and infections like aspiration pneumonia.
Radon gas: Radon is a radioactive gas that can accumulate in homes and buildings. Prolonged exposure to high levels of radon is a significant risk factor for lung cancer.
It’s important to address and mitigate respiratory hazards to protect respiratory health. This can be done through measures such as creating proper ventilation, the use of personal protective equipment, avoiding smoking and exposure to secondhand smoke, and minimizing exposure to pollutants and allergens. In occupational settings, following safety guidelines, implementing proper ventilation systems, and providing appropriate protective gear are essential to preventing respiratory hazards.
Eye Protection
The OSHA eye protection standard (1970c), is incorporated into each state’s own regulations.
Here are the key elements of the eye protection standards:
Eye protection requirements: Employers are required to assess the workplace for potential eye hazards and provide appropriate eye protection to employees where there is a risk of eye injury. Eye protection must be provided free of charge to affected workers.
Selection of eye protection: Employers should select eye protection devices, such as safety glasses, goggles, face shields, or full-face respirators with built-in eye protection, based on the specific hazards present in the workplace.
Use of eye protection: Employees must wear the provided eye protection whenever they are exposed to potential eye hazards. Eye protection should be worn in designated areas or during specific tasks where eye injuries are likely to occur.
Training: Employers must provide training to employees on the proper use, maintenance, and limitations of the eye protection provided. Employees should understand how to wear, adjust, and clean eye protection for maximum effectiveness.
Maintenance and replacement: Employers are responsible for ensuring that eye protection devices are maintained in good condition. Damaged or worn-out eye protection should be replaced promptly to ensure continued safety.
Emergency eyewash and shower stations: If workers are exposed to corrosive substances or hazardous chemicals that can cause eye injuries, the employer should provide accessible emergency eyewash stations and safety showers.
Prescription eyewear: If an employee requires prescription eyewear, the employer must ensure that the eye protection is capable of accommodating the prescription lenses or provide the necessary eye protection that incorporates the prescription.
Voluntary use of eye protection: If employees choose to wear eye protection voluntarily (when not required by the employer), certain requirements may still apply, and the employer should provide information and training on the proper use and limitations of such eye protection.
It is essential for employers to comply with these eye protection standards to prevent eye injuries and maintain a safe work environment. Employers should regularly review and update their eye protection program as needed, and employees should be informed and trained on the proper use and care of eye protection devices.
American National Standard for Occupational and Educational Personal Eye and Face Protection Devices
The American National Standards Institute, ANSI is a private, non-profit organization that oversees the development and implementation of voluntary consensus standards for various industries and sectors in the US. The standard for eye protection is the ANSI Z87.1 standard, titled “American National Standard for Occupational and Educational Personal Eye and Face Protection Devices.”
The ANSI Z87.1 standard establishes the requirements and performance criteria for eye and face protection devices used in occupational and educational settings (Kelechava, 2020). It covers a wide range of protective equipment, including safety glasses, goggles, face shields, and welding helmets. When purchasing safety glasses, ensure the “ANSI Z87.1” standard is printed on the glasses.
Key aspects covered by the ANSI Z87.1 standard include:
Impact resistance: Eye protection devices must be capable of withstanding high-velocity impacts from flying objects or particles, protecting the eyes from potential injuries.
Optical quality: The standard specifies optical requirements to ensure clear vision and minimal distortion through the protective lenses.
Lens marking: The eye protection devices should be permanently marked with specific information, such as the manufacturer’s identification, lens type (e.g., basic impact, high impact, welding filter), and any additional markings indicating compliance with specific tests.
Face shield performance: For face shields, the standard sets requirements for coverage, thickness, and resistance to penetration and ignition.
UV protection: The ANSI Z87.1 standard includes requirements for providing adequate protection against ultraviolet (UV) radiation.
Splash and dust protection: The standard addresses the performance of eye protection devices against liquid splashes and dust particles.
Flammability resistance: Certain eye protection devices are tested for their resistance to ignition and flame spread.
Compliance with the ANSI Z87.1 standard ensures that eye protection devices meet specific performance and safety criteria, making them suitable for protecting against various workplace hazards. Employers should choose eye protection products that are ANSI Z87.1-compliant and provide proper training to employees on their correct use and maintenance.
Health Effects of Eye Hazards
Eye hazards can lead to a range of health effects varying in severity from minor irritation to permanent damage. These hazards can arise from exposure to many substances, conditions, or activities that can harm the eyes. It’s important to protect your eyes from potential hazards to prevent these negative outcomes. Here are some common eye hazards and their associated health effects:
Chemical exposure: Contact with corrosive or irritating chemicals, such as acids, alkalis, solvents, and cleaning agents, can cause eye irritation, redness, tearing, and even chemical burns. Severe chemical exposure can lead to permanent damage, vision loss, or blindness.
Foreign objects: Particles, debris, or foreign objects like dust, wood chips, metal shavings, and grit can get into the eyes, causing discomfort, redness, pain, and potential damage. In some cases, foreign objects can scratch the cornea, leading to infection and impaired vision.
Sharp objects: Accidents involving sharp objects like knives, shards of glass, or other sharp tools can cause cuts or punctures to the eye, leading to potential infections and damage to the eye’s structures.
Particulate matter: Dust, sand, or other airborne particles can irritate the eyes and cause discomfort, redness, and tearing. Prolonged exposure to particulate matter may lead to chronic irritation and dry eyes.
Physical impact: Accidental impact to the eye, such as a blow, can result in eye trauma, bruising, swelling, and potential damage to the eye’s structures.
It is crucial to take appropriate precautions to protect your eyes from potential hazards. This includes wearing appropriate eye protection such as safety goggles, face shields, or helmets with protective visors when working in hazardous environments or participating in activities with potential eye risks. Regular eye check-ups and prompt medical attention following any eye injury are essential to ensure early detection and proper treatment of eye-related health issues.
Attributions
- Figure 2.6: NIOSH Hierarchy of Controls by NIOSH is released under CC BY 4.0
- Figure 2.7: A Shirt caught in a lathe by Damon Donner, for WA Open ProfTech, © SBCTC, CC BY 4.0
- Figure 2.8: Required approval markings on a NIOSH Approved N95® FFR by CDC.gov in the Public Domain; Materials produced by federal agencies are in the public domain and may be reproduced without permission.
is a private, non-profit organization that oversees the development and implementation of voluntary consensus standards for various industries and sectors in the United States.
standard establishes the requirements and performance criteria for eye and face protection devices used in occupational and educational settings