6.6 Work holding
Tim A. Bacon
As the job plan is developed, a critical aspect of the project is the workholding. The primary choice is between a mill and a lathe. The following sections will introduce workholding on these machines.
Mill workholding
The list of workholding possibilities is exceedingly long. Two of the most common ways of securing a part on a mill is to use a vise, or a system of strap clamps. When using a mill, the main two objectives are holding the part and keeping it from spinning. For the best outcome, the machinist must ensure a secure setup before starting to cut.
The way in which the part is held will depend to some extent on how aggressively the material is being removed. The vise, a mainstay in almost every machine shop, relies on compressive forces and friction to keep the part in place. To increase the holding power, a dovetail design is used. This design allows less engagement of the vise jaws and therefore, more of the part is accessible to be worked on.
The vise jaws can also be cut into a pattern that matches the part. This is called creating “form jaws.” Form jaws will increase the surface area and the friction that is keeping the part from moving.
On a lathe, there will be a three, or four jaw chuck although there are others. There may be an option for a collet chuck. The main difference is that a collet is going to retain concentricity better than a jaw style chuck if the part has to be taken out and put back into the machine. More detail on lathes and workholding will be covered in Chapter 10.
(A vise holding a part on a mill)
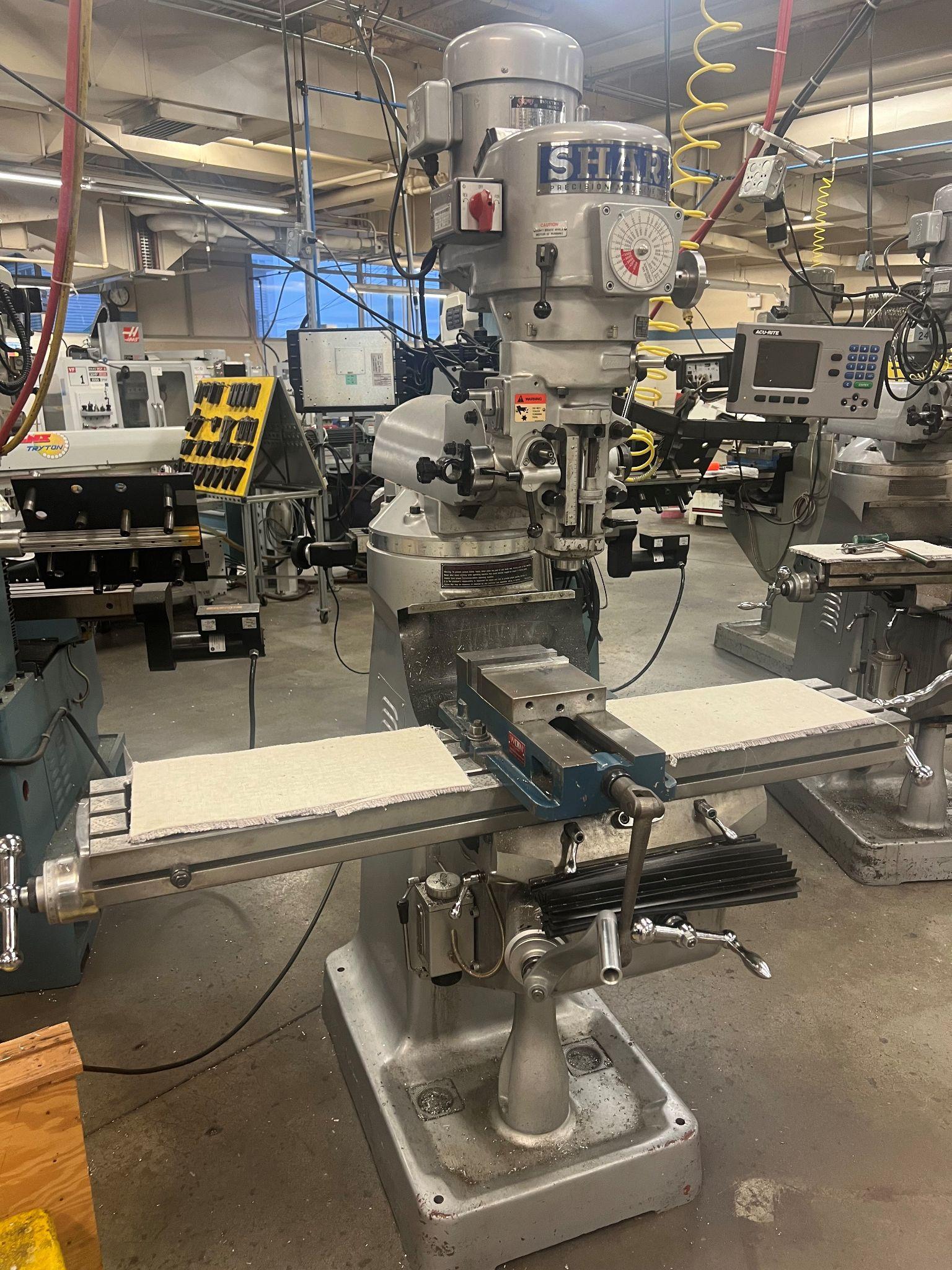
How effectively parts are held is greatly influenced by how much extra material is provided from the supplier. If a customer provides minimal material, it will be more difficult to make the part due to the challenges of holding it while it is being cut.
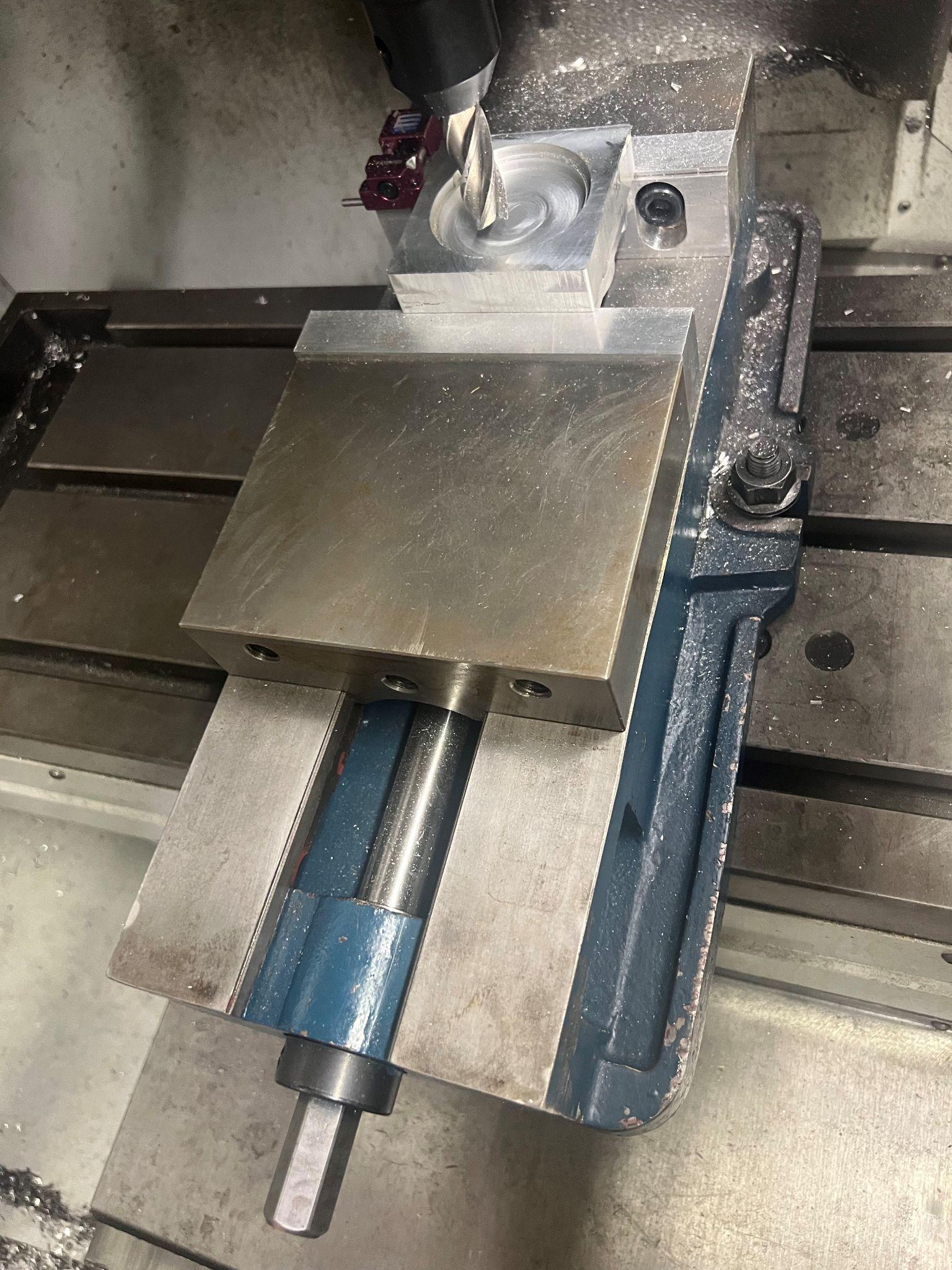
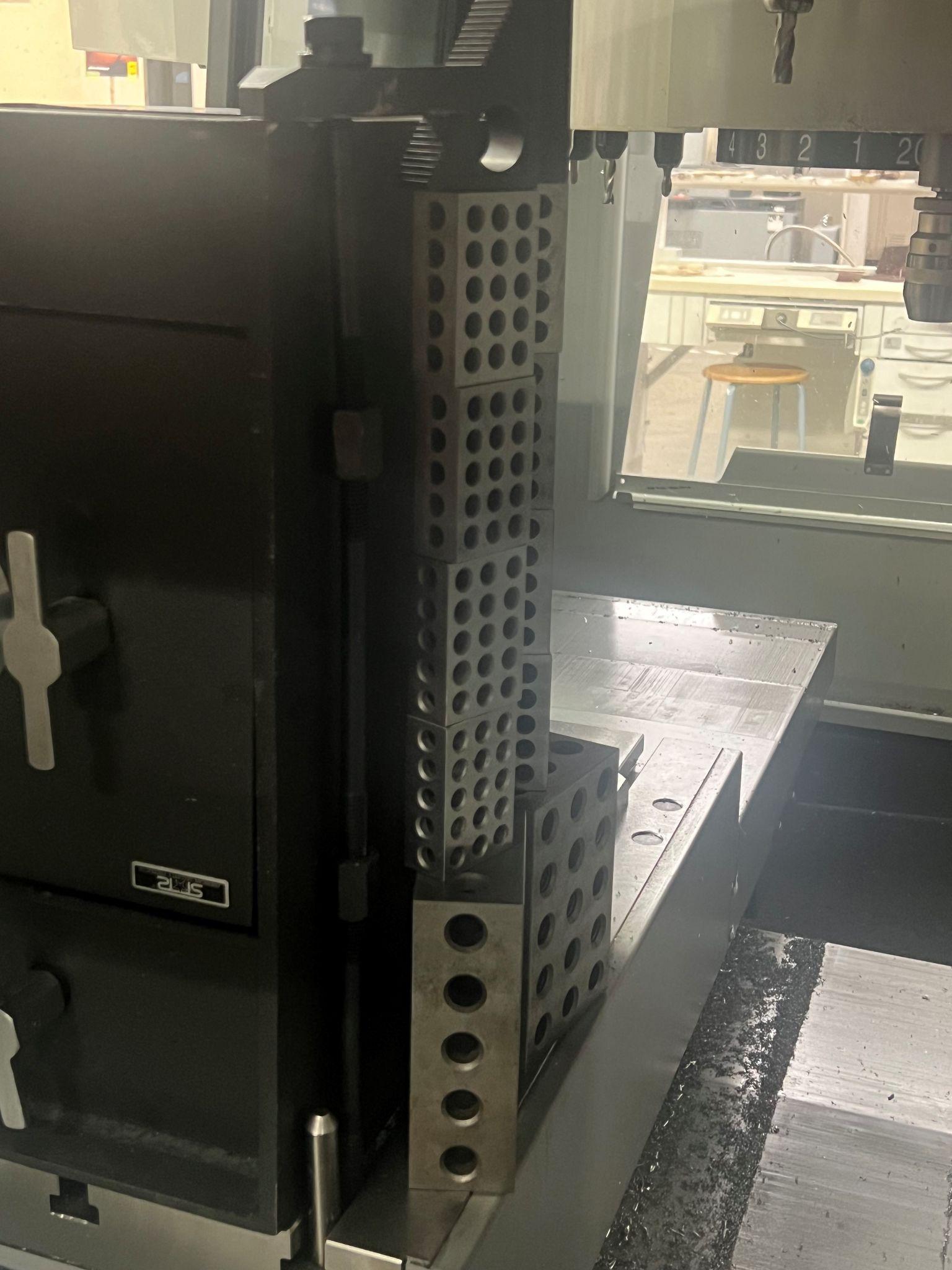
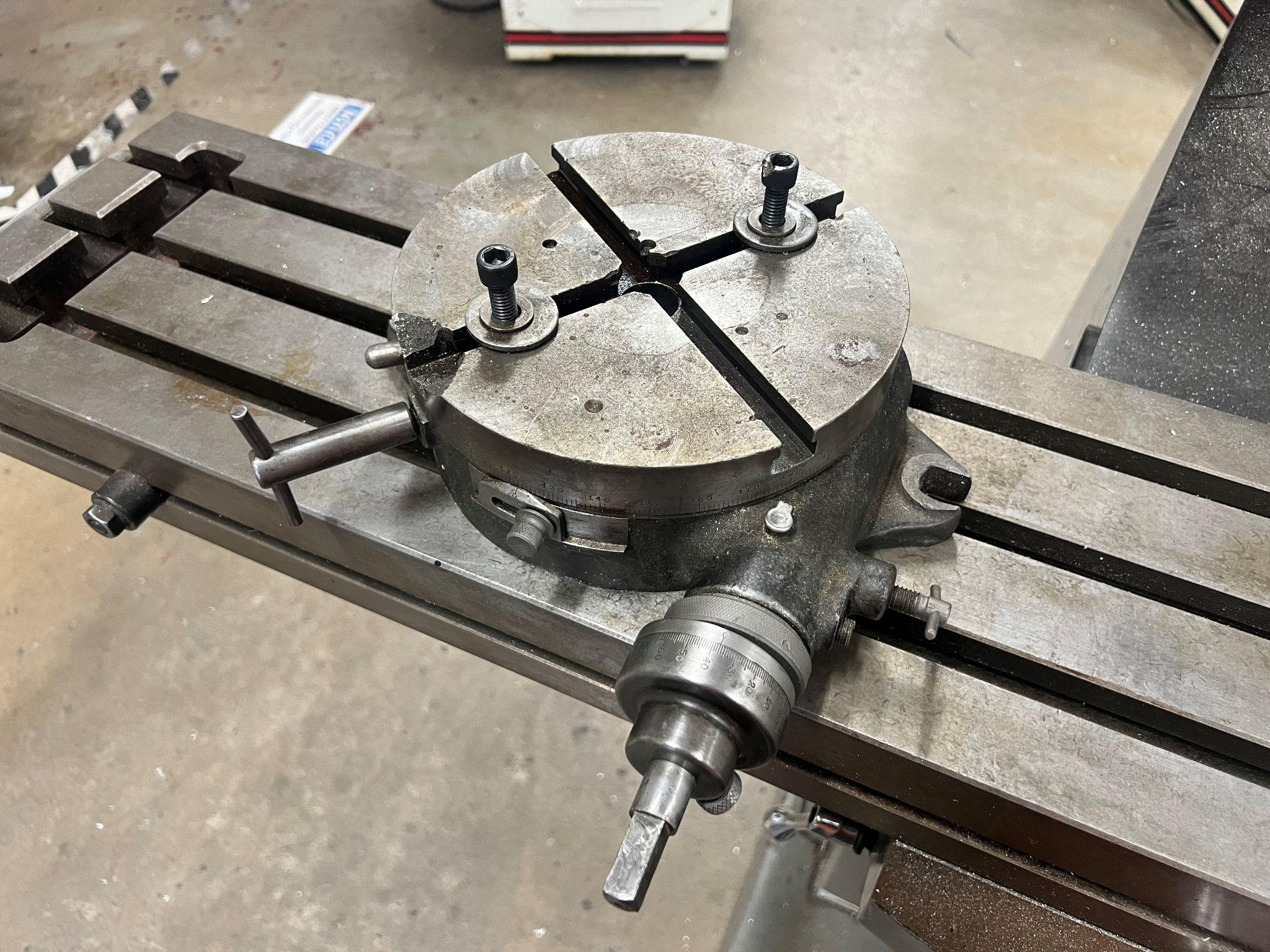
Pictured above is a rotary table. Mounting this to a vertical mill will allow the part to be rotated while being cut for circular features.
Lathe workholding
The three common ways of holding parts on a lathe are to use a three jaw chuck, a four jaw chuck, or a collet chuck.
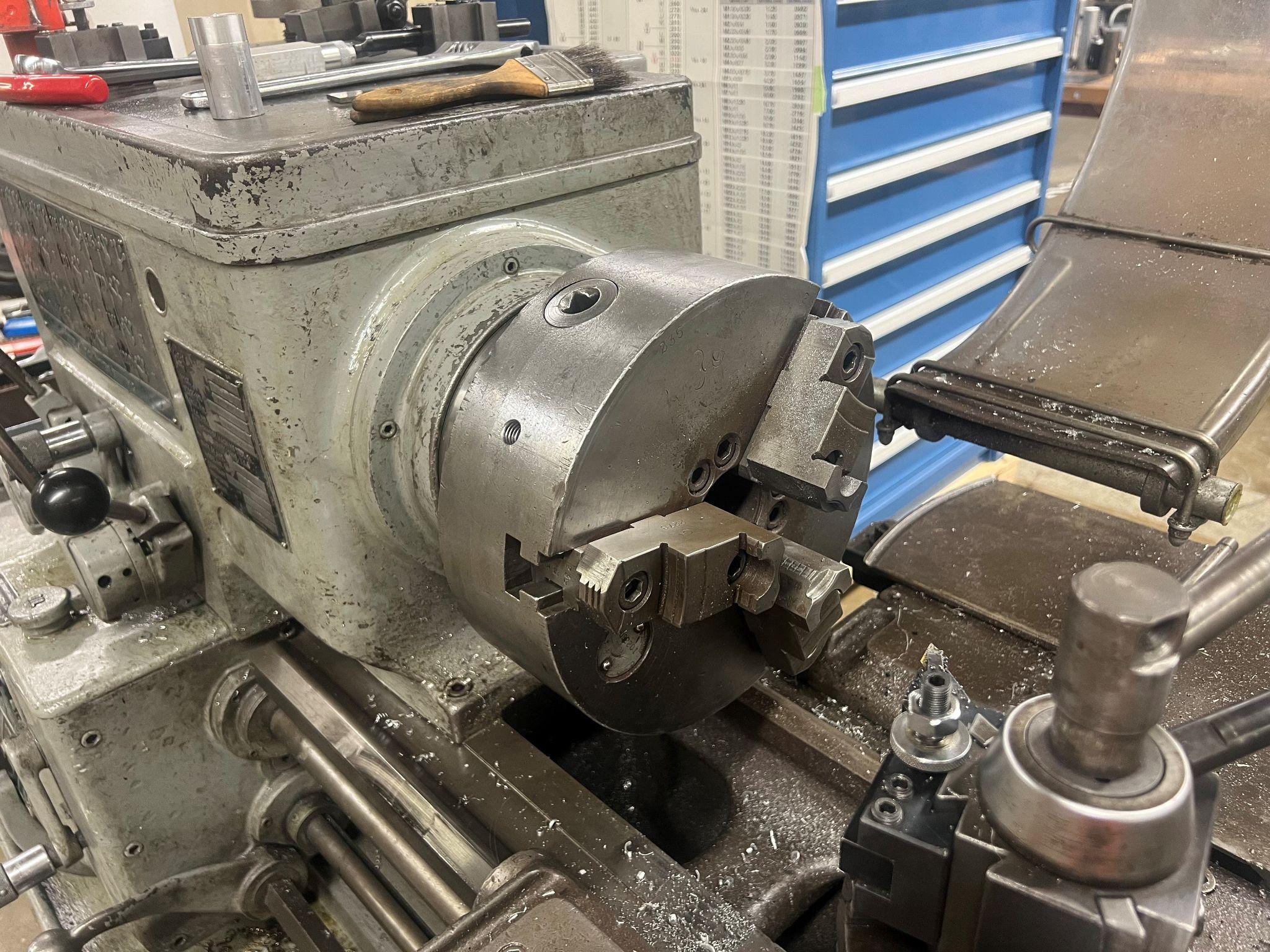
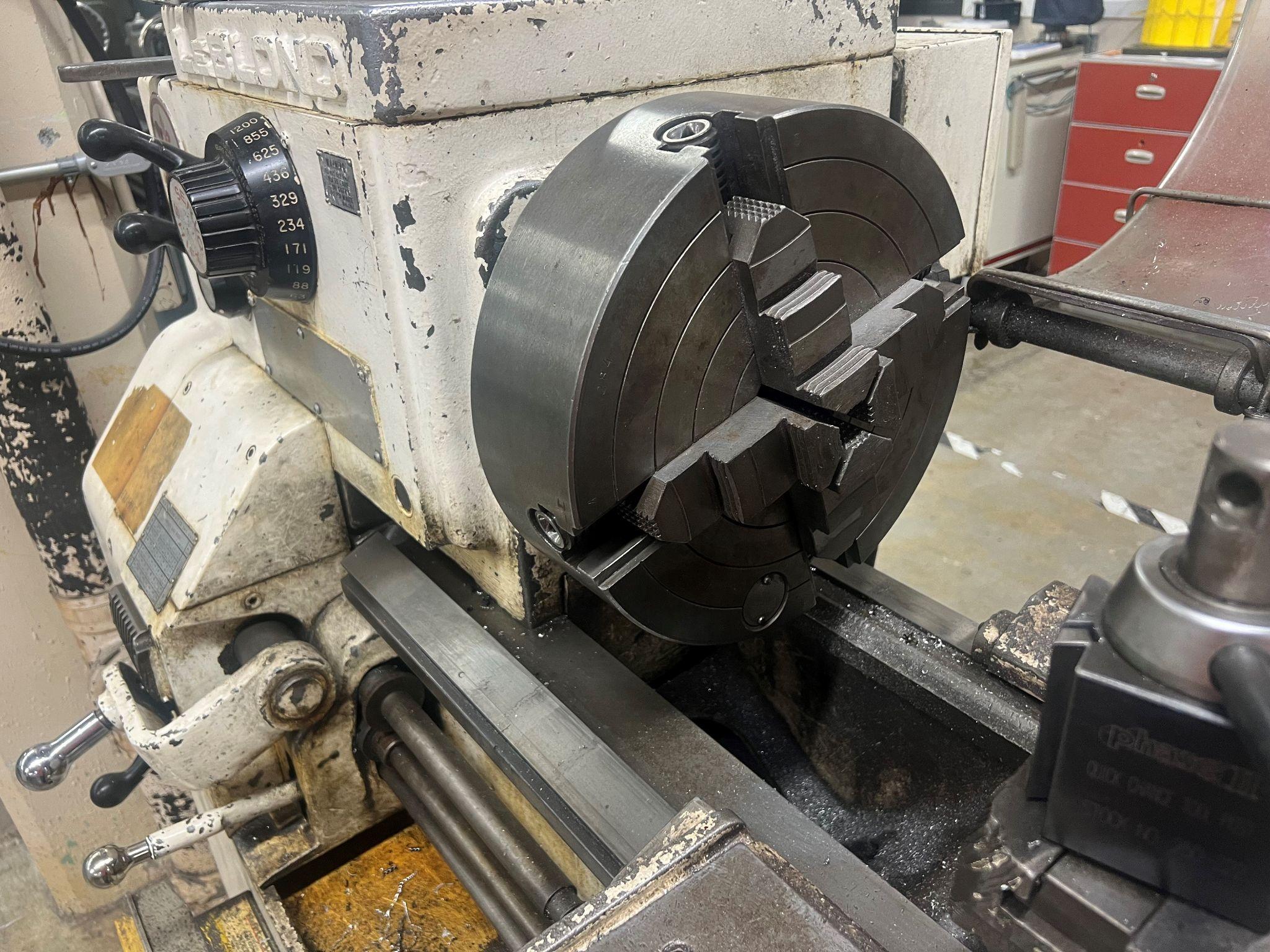
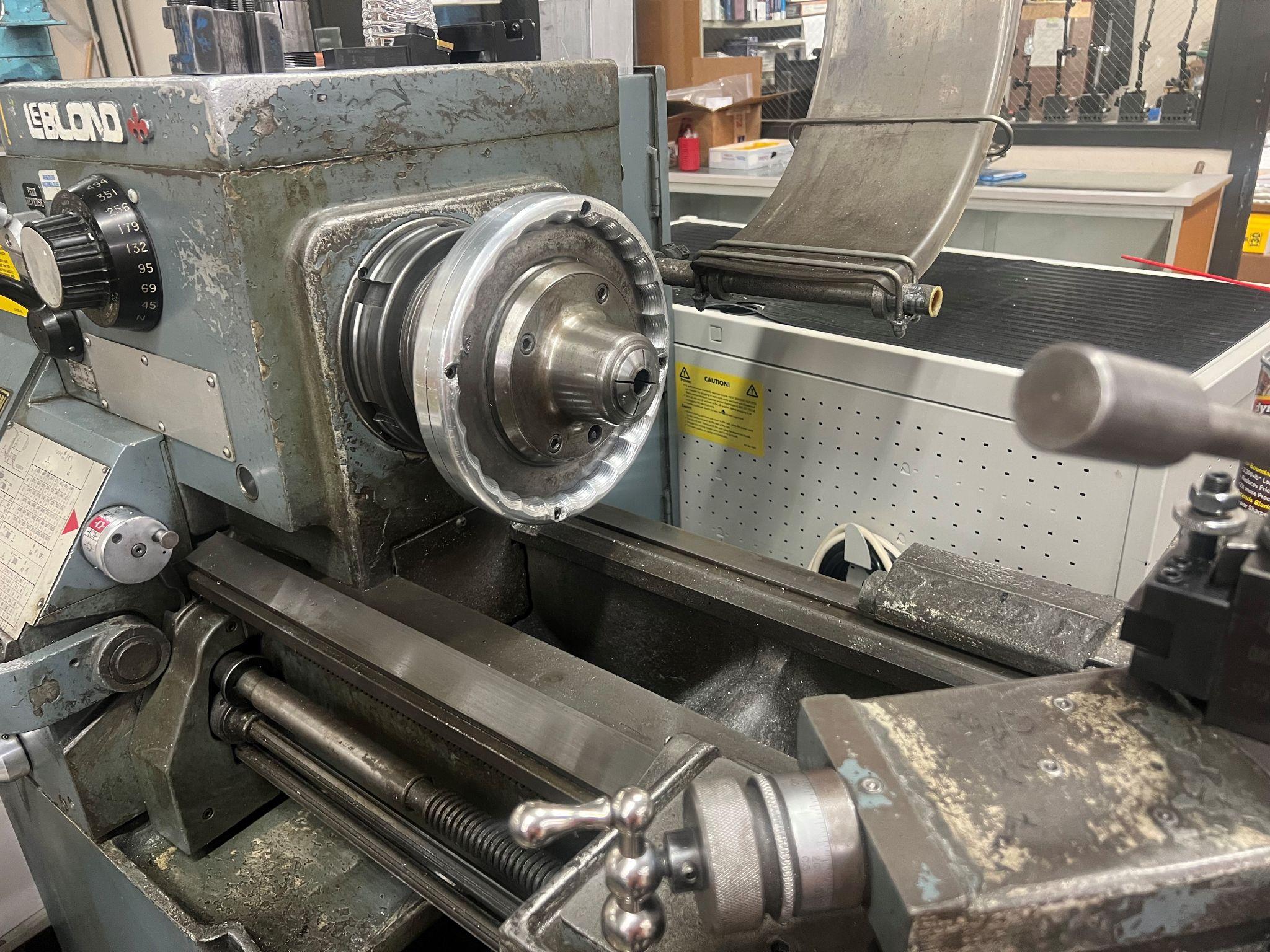
The three jaw chuck centers the part when clamped but is not as accurate or repeatable as a collet chuck. Use the collet chuck for clamping on finished surfaces to retain minimal runout. The four jaw chuck is ideal for square parts and can be dialed in to ensure that they are centered on the chuck. The downside is that it takes more time to set up.
Attributions
- Figure 6.14: Workholding on a mill by T Bacon, courtesy of Bates Technical College, for WA Open ProfTech, © SBCTC, CC BY 4.0
- Figure 6.15: Close up view of workholding on a mill by T Bacon, courtesy of Bates Technical College, for WA Open ProfTech, © SBCTC, CC BY 4.0
- Figure 6.16: Extreme workholding by T Bacon, courtesy of Bates Technical College, for WA Open ProfTech, © SBCTC, CC BY 4.0
- Figure 6.17: Rotary table by T Bacon, courtesy of Bates Technical College, for WA Open ProfTech, © SBCTC, CC BY 4.0
- Figure 6.18: Three jaw lathe chuck by T Bacon, courtesy of Bates Technical College, for WA Open ProfTech, © SBCTC, CC BY 4.0
- Figure 6.19: Four Jaw lathe chuck by T Bacon, courtesy of Bates Technical College, for WA Open ProfTech, © SBCTC, CC BY 4.0
- Figure 6.20: Collet lathe chuck by T Bacon, courtesy of Bates Technical College, for WA Open ProfTech, © SBCTC, CC BY 4.0