9.1 Safety
Micky R. Jennings
Safety needs to be the first concern with any piece of equipment in a machine shop. This is especially true when working with a milling machine. The milling machine poses many risks, and operators must consider their safety at every step. For example, this piece of equipment has a larger motor with enough torque to cause serious injury. Machinists using the milling machine need to follow all the standard safety rules of the shop in addition to knowing the specific potential hazards they may encounter while using the milling machine.
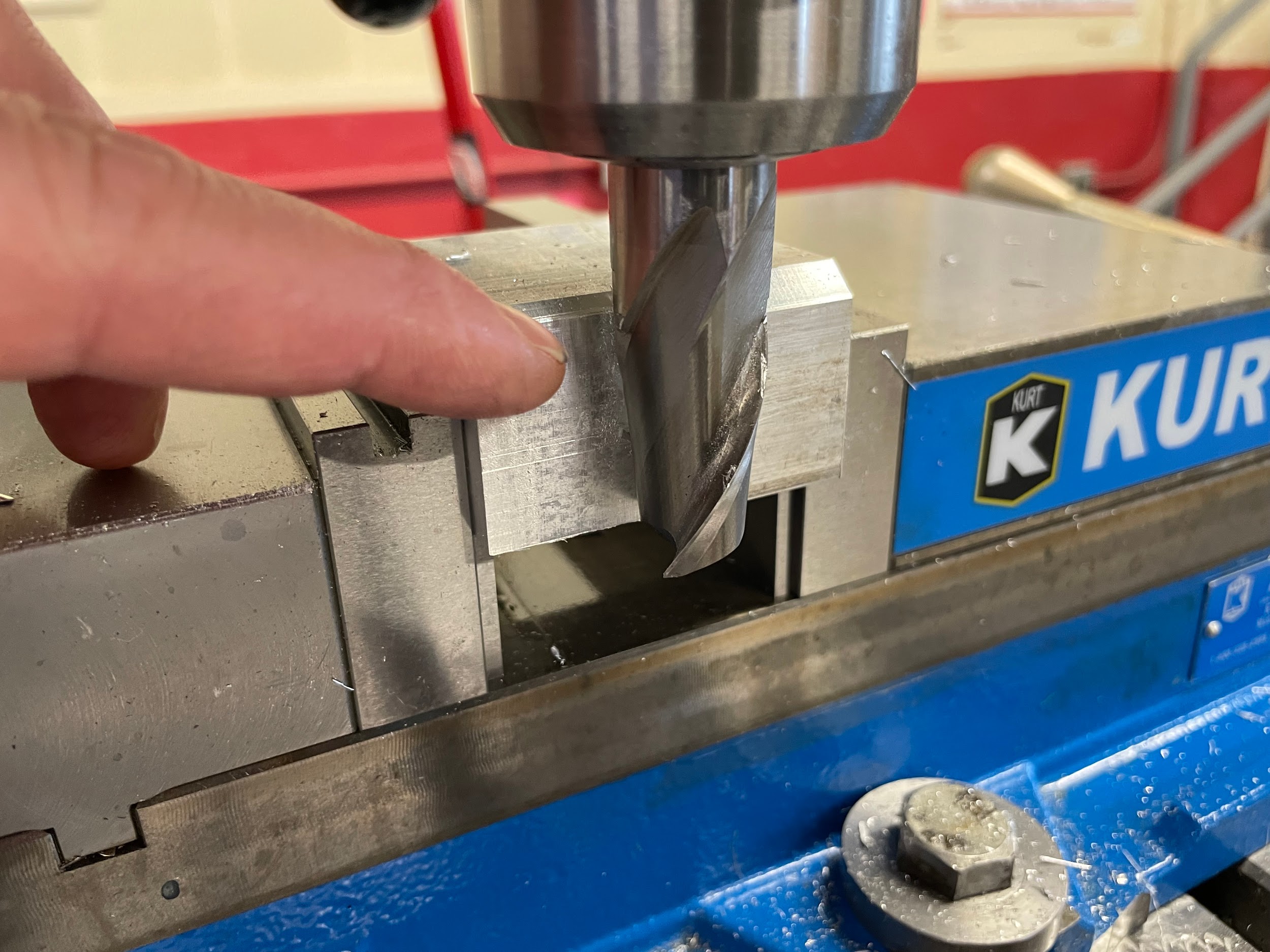
Rotational Hazards
Milling machines have a rotating spindle and tooling that can catch clothing, jewelry and hair. These rotating devices can also be dangerous to fingers and hands. Machinists need to be aware of these hazards and take the necessary precautions to eliminate danger. Roll up sleeves and tuck in baggy clothing. Remove all jewelry and tie back hair. Do not bring hands or fingers near rotational cutting tools.
Sharp Hazards
Twist drills, end mills, and other cutting tools used on milling machines are sharp. The machinist should take care when handling cutting tools and avoid holding or sliding hands and fingers along the cutting edges. Hold tools by the shank of the tool when possible.
Chips that are produced on the milling machine are also sharp. During the cutting process, chips are often thrown in many directions. For this reason, the machinist should be prepared to protect themselves. The first line of protection is safety glasses. Safety glasses are worn to protect the eyes and are a necessary precaution anywhere in a machine shop. The manual milling machine is particularly hazardous to eyes because the chips are often flying at a height closer to the face of the operator than from other equipment. Hot chips can also find their way into loose clothing and shoes. The machinist should wear long pants and reasonably fitting clothing that protects them from sharp flying chips.
Slipping Hazards
Cutting oil and chips, produced in the cutting process, can be slippery and dangerous if allowed to accumulate on the floor around the machinery. The operator should be aware of these hazards and periodically sweep chips from the work area and clean up oil messes as soon as they occur. The causes of slip and fall accidents are easily overlooked, but they result in many hours of missed work and L&I claims each year (National Floor Safety Institute, n.d.). Time for occasional cleaning, for safety’s sake, should be considered in each job, making operator safety a priority.
Pinch Points
One possible pinch point on a milling machine is the engagement of the belts and pulleys. Some mills will have belts and stepped pulleys that require a change of position in order to adjust speed. If a machinist is not careful, this could create a pinch. Ensuring the motor is fully stopped before changing pulleys is a good precaution.
Some mills also have power feeds that could create a pinch if the operator becomes complacent. Specifically, this could be between any of the machine’s components and/or the work while the machine is moving automatically. To prevent hazardous situations, the operator must be aware of the setup and always be near the power feed levers to disable them if needed. A good rule is to never let go of a feed lever once it is activated.