9.6 Tool Holding
Micky R. Jennings
Tool holding devices on a milling machine are designed to securely hold the tools for various operations. They need to be simple, quick, and easy to use. The most common tool holding solutions on milling machines are drill chucks and collets. These solutions come in many different styles, but they all perform the same function of holding the tools. Not all tool holding devices are right for every job though. Drill chucks are only used to hold the hole making tools outlined in the drill press chapter. Tools that cut in a lateral motion require more support than a drill chuck can provide.
End Mill Holder
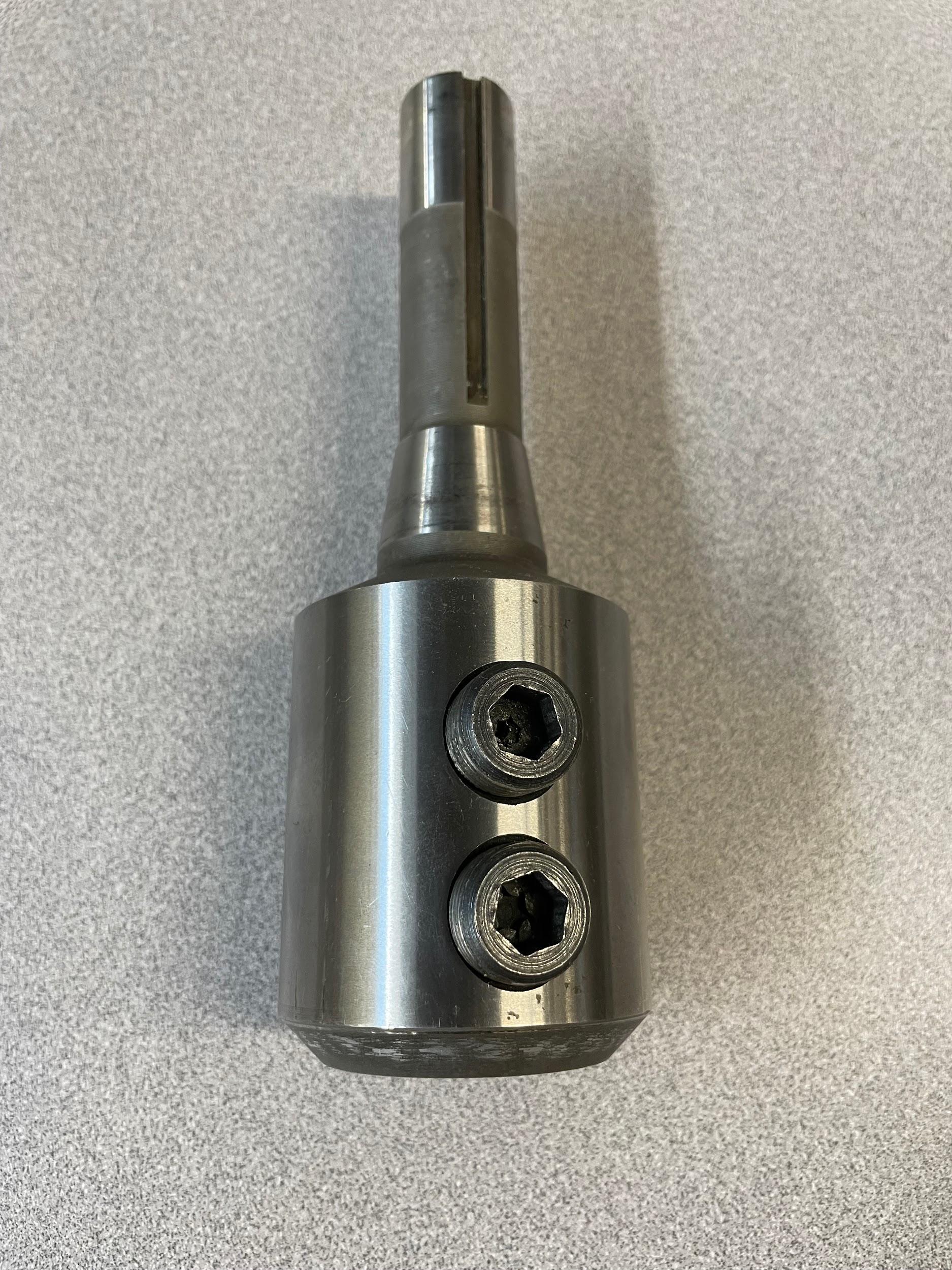
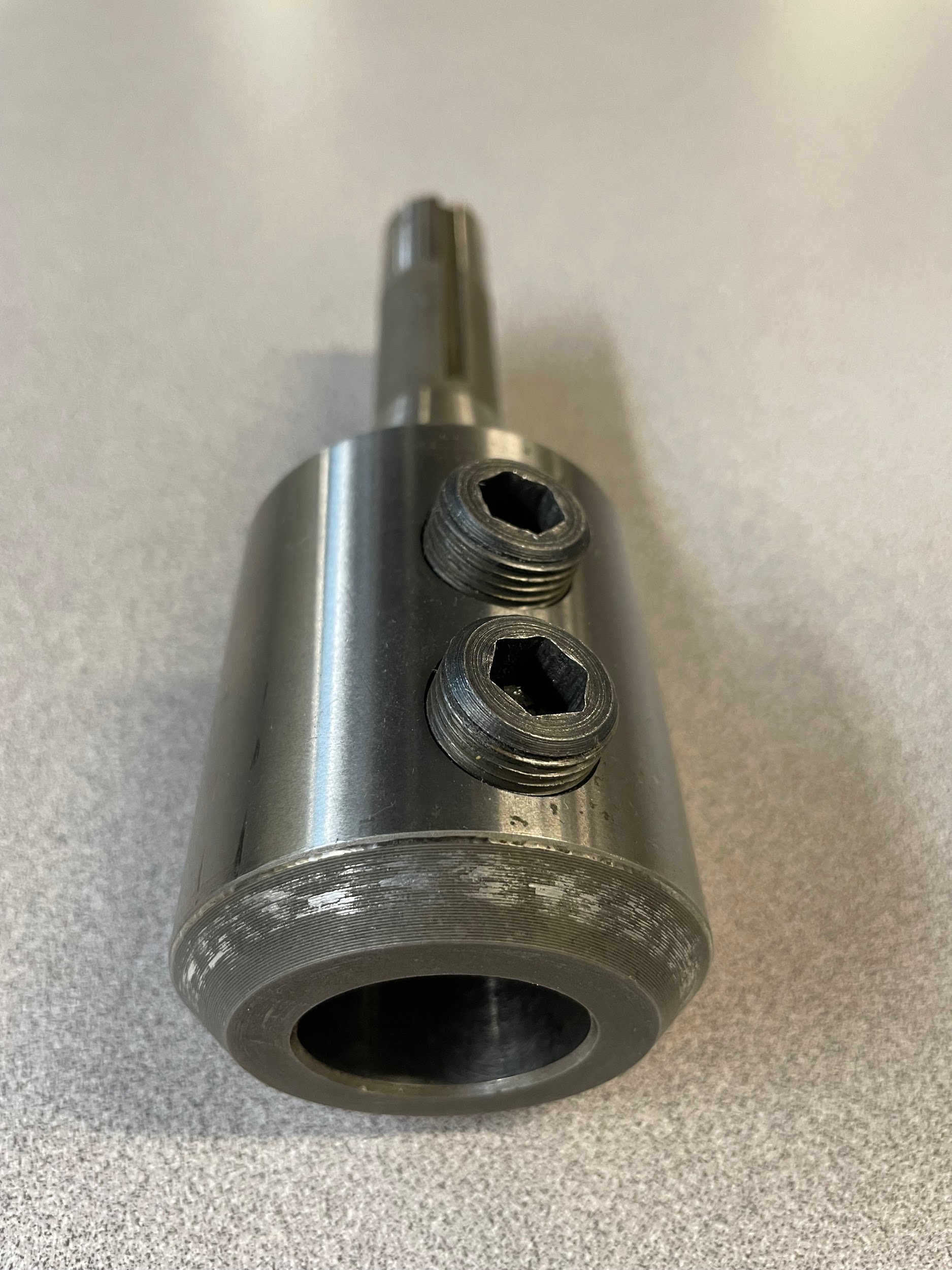
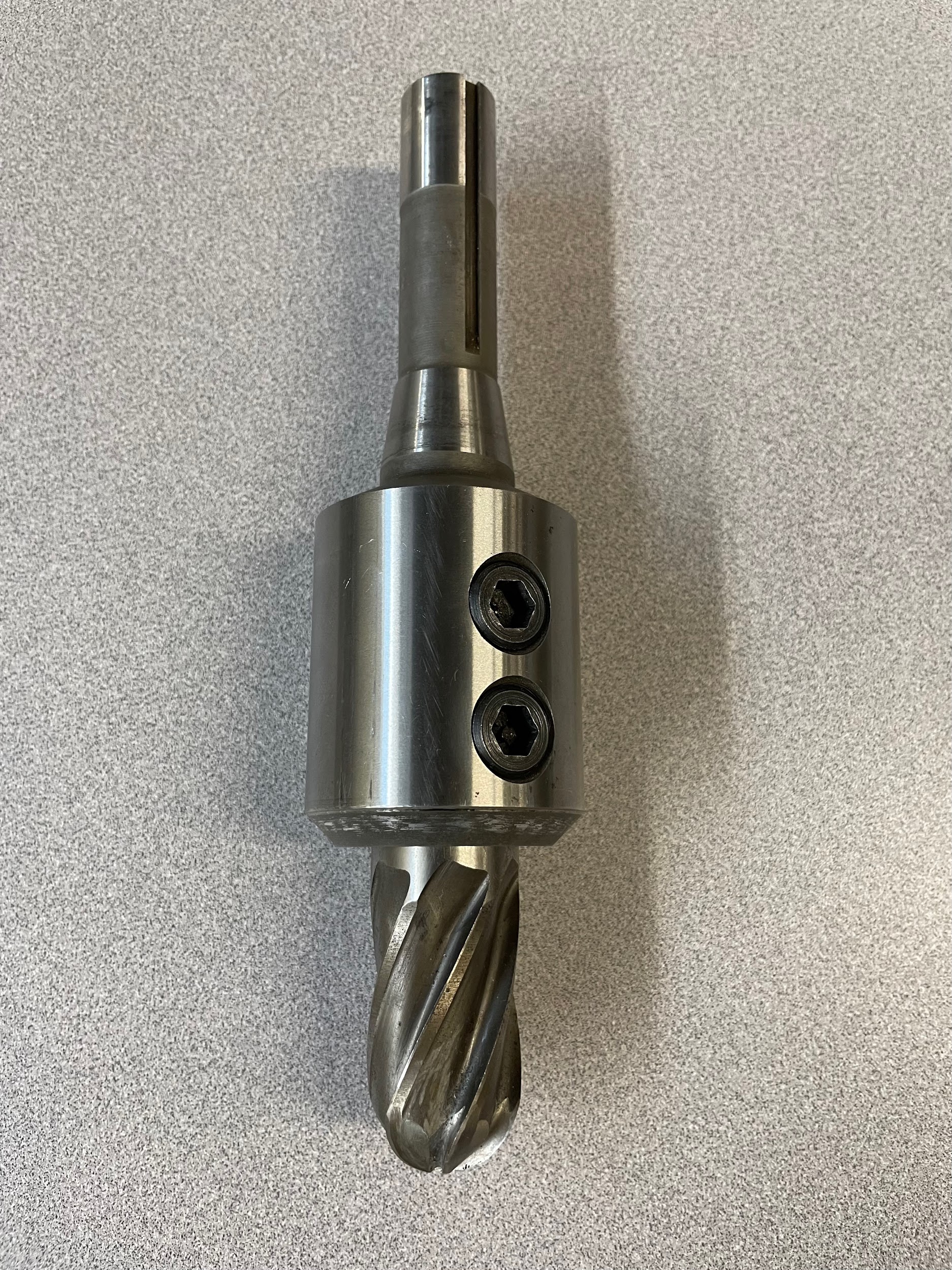
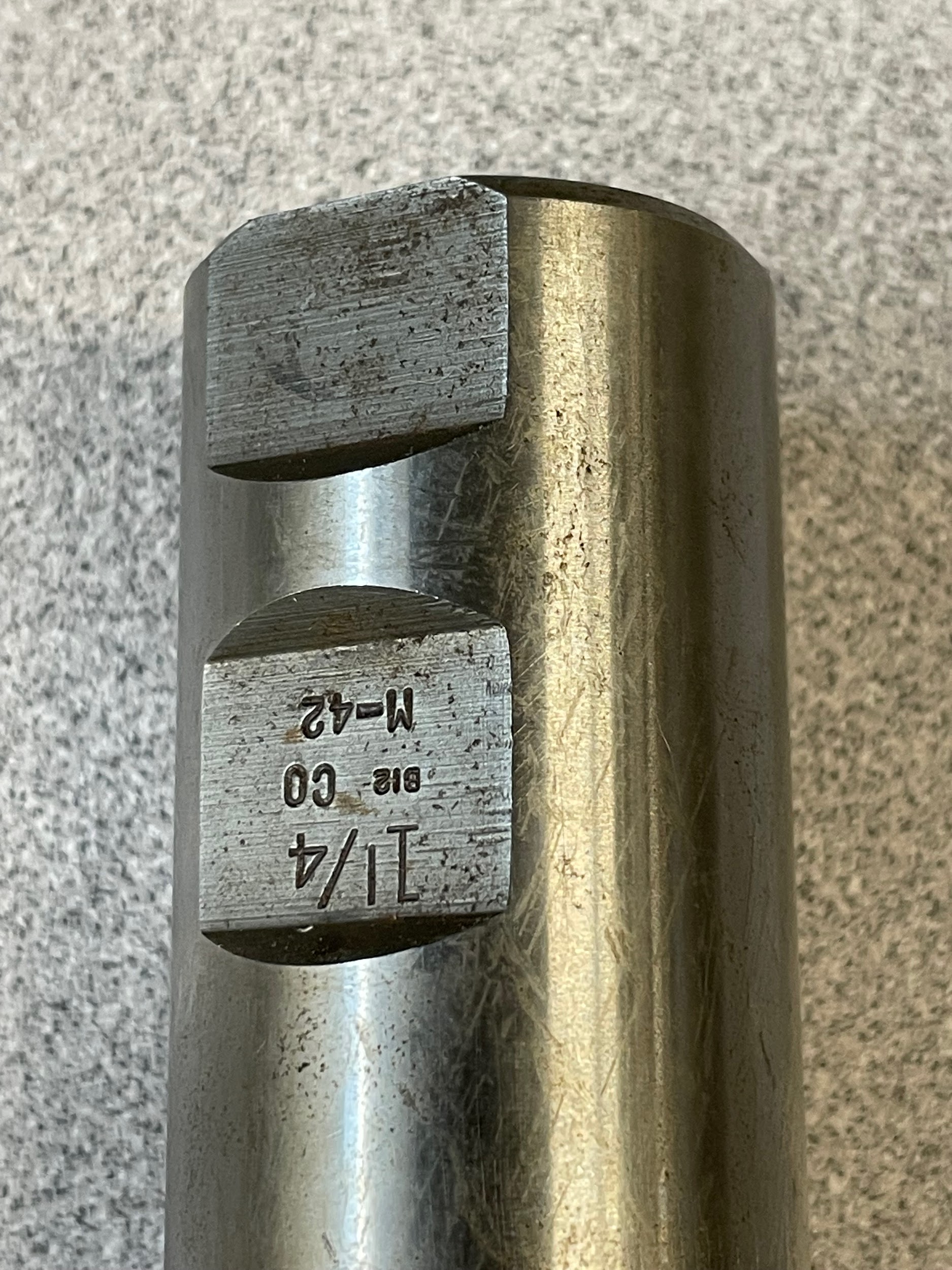
An end mill holder is a solid R8 tapered holder that has a set screw for securing an end mill or other side cutting tool. In addition to the precision taper, there is also a precision diameter. These features mate against or inside the precisely ground spindle. The holder also has a thread in the end to tighten the tool into the spindle.
Spring Collet
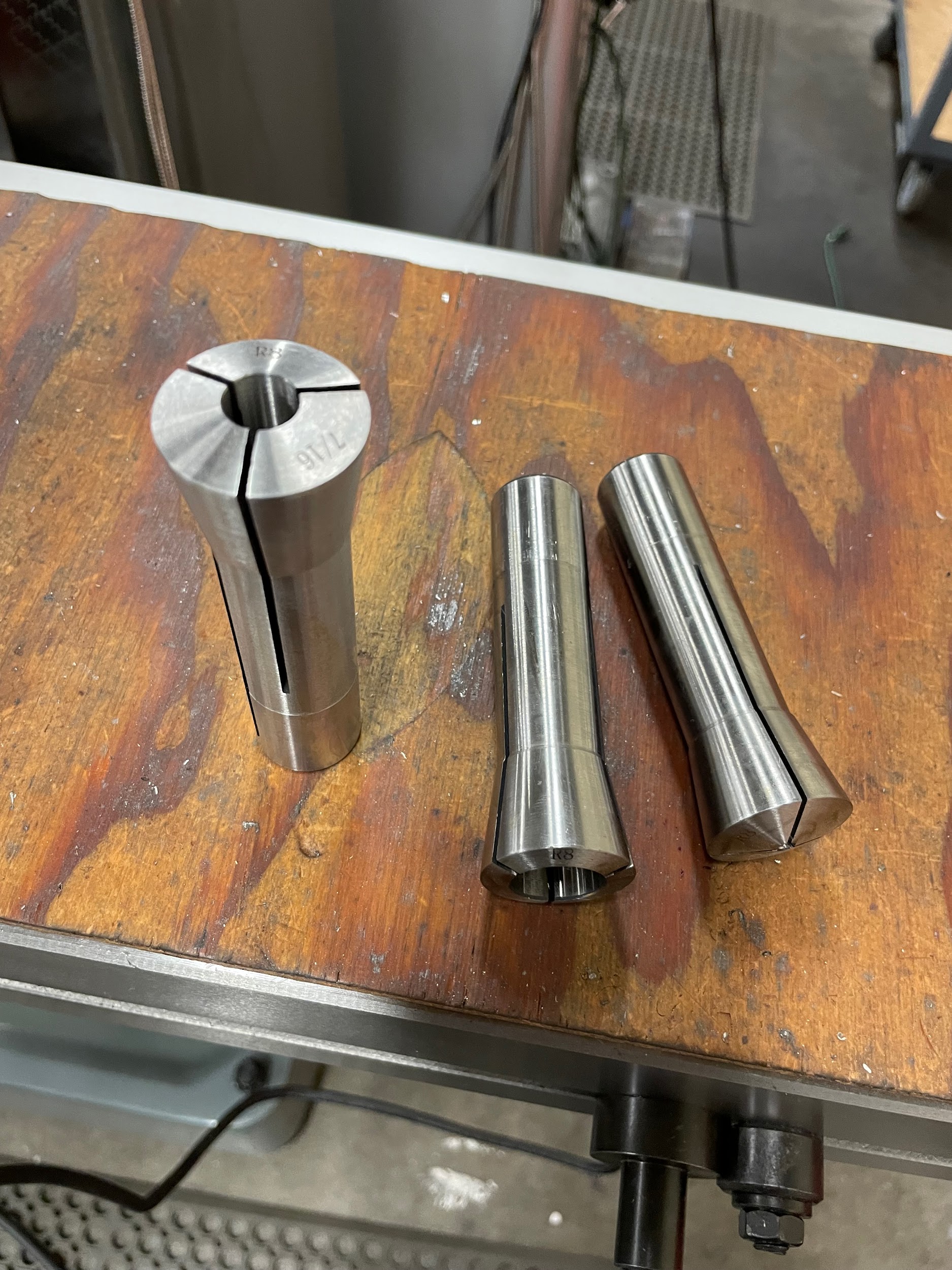
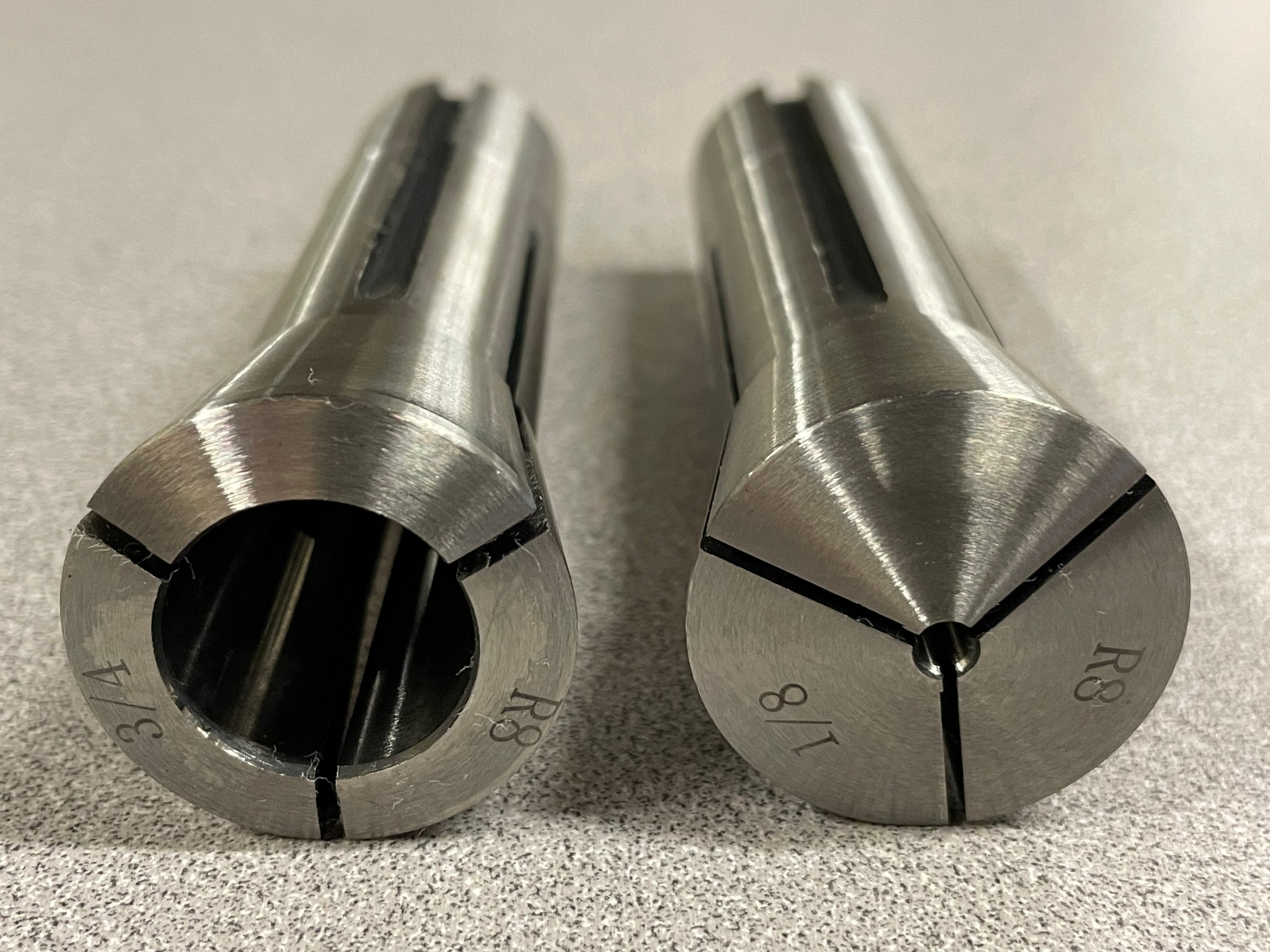
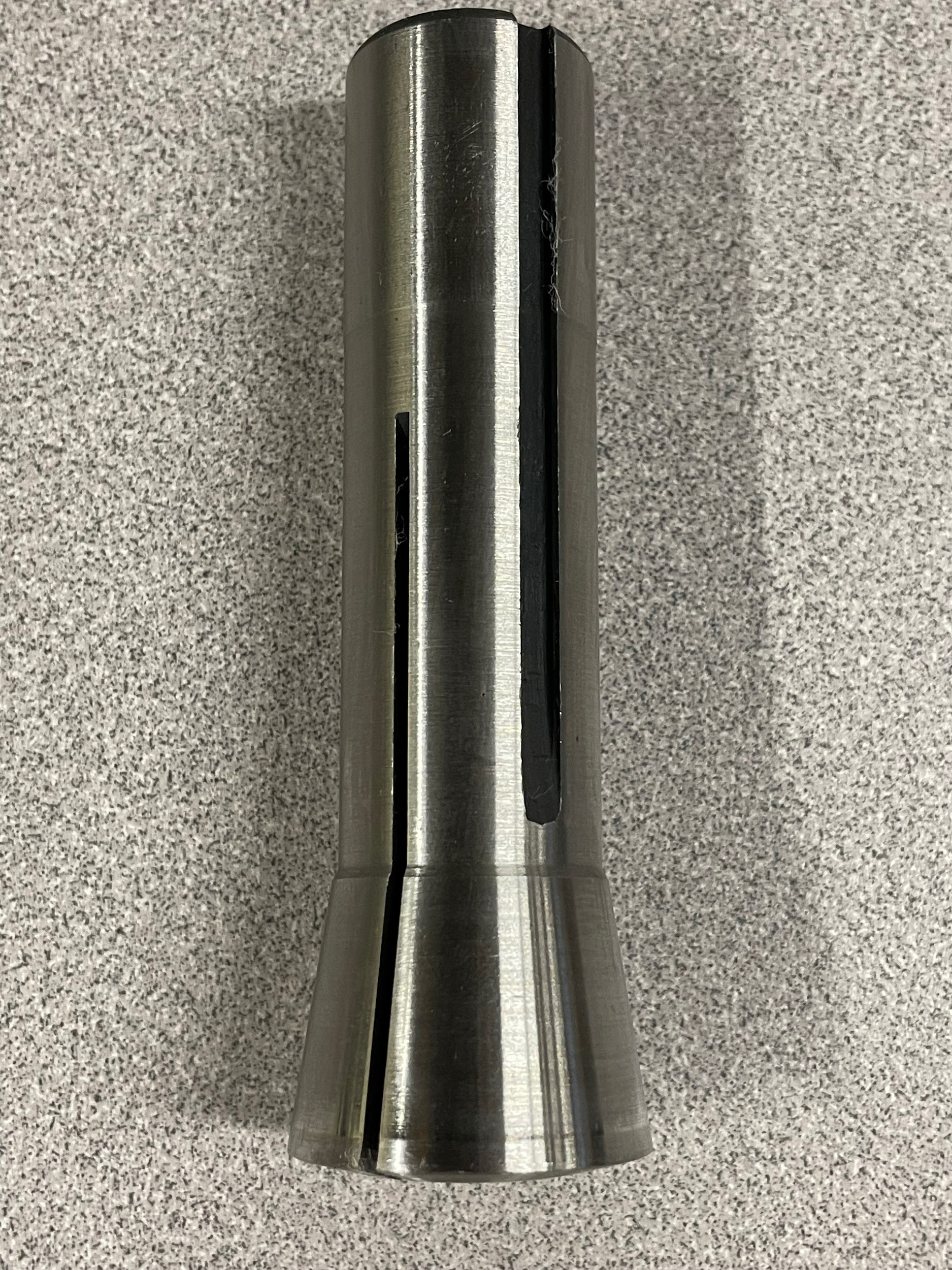
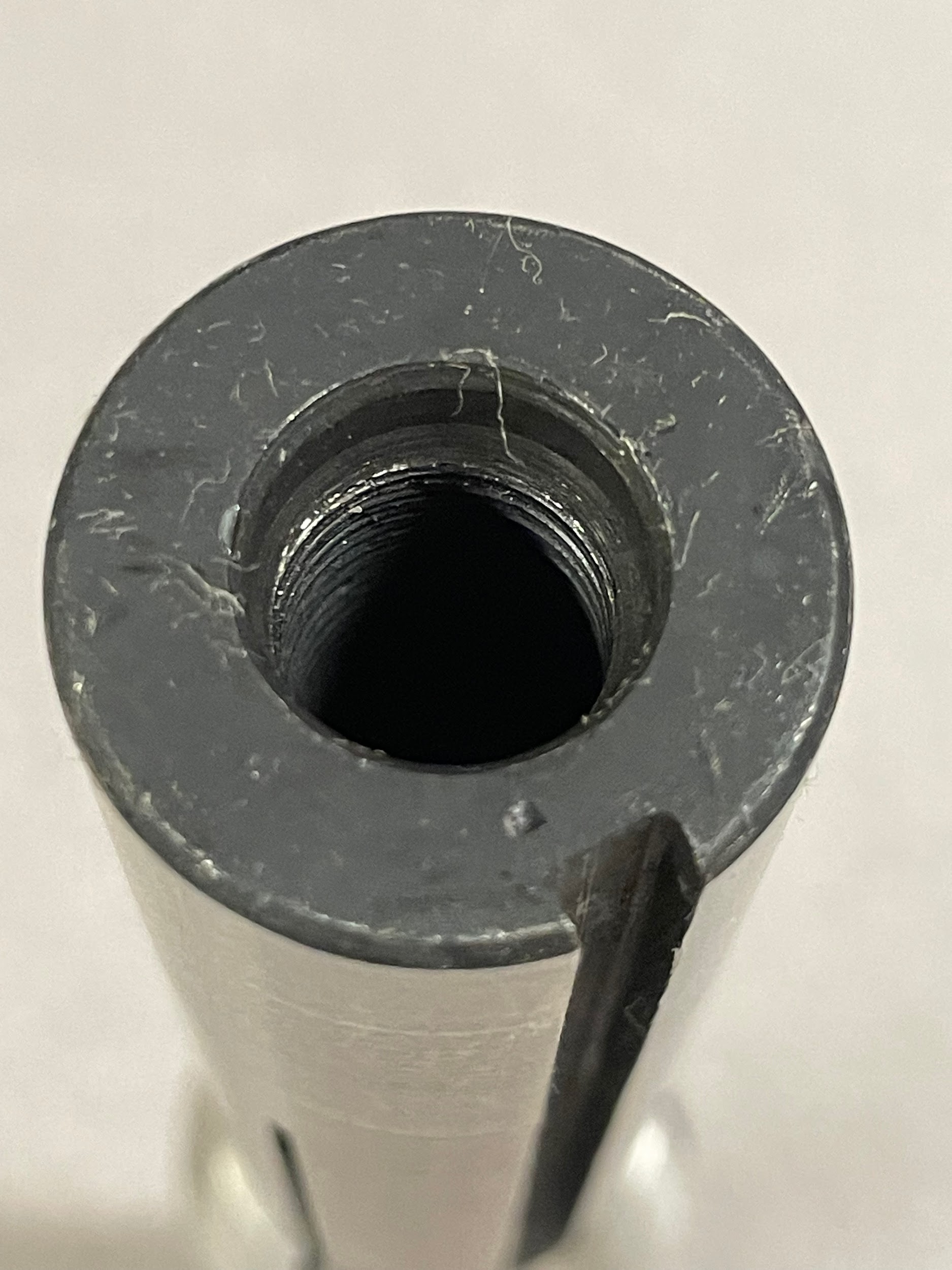
A spring collet, often just called a collet, also has an R8 taper, a precision diameter, and a thread in the end. However, these holders are not solid; they are flexible. The collets use this flexibility to clamp onto the tool as the drawbar pulls the collet up into the taper of the spindle. Collets are not designed to grip on diameters larger or smaller than the advertised size. Doing so could damage the tooling and the collet or allow the cutting tool to slip during the machining process.
Draw Bar
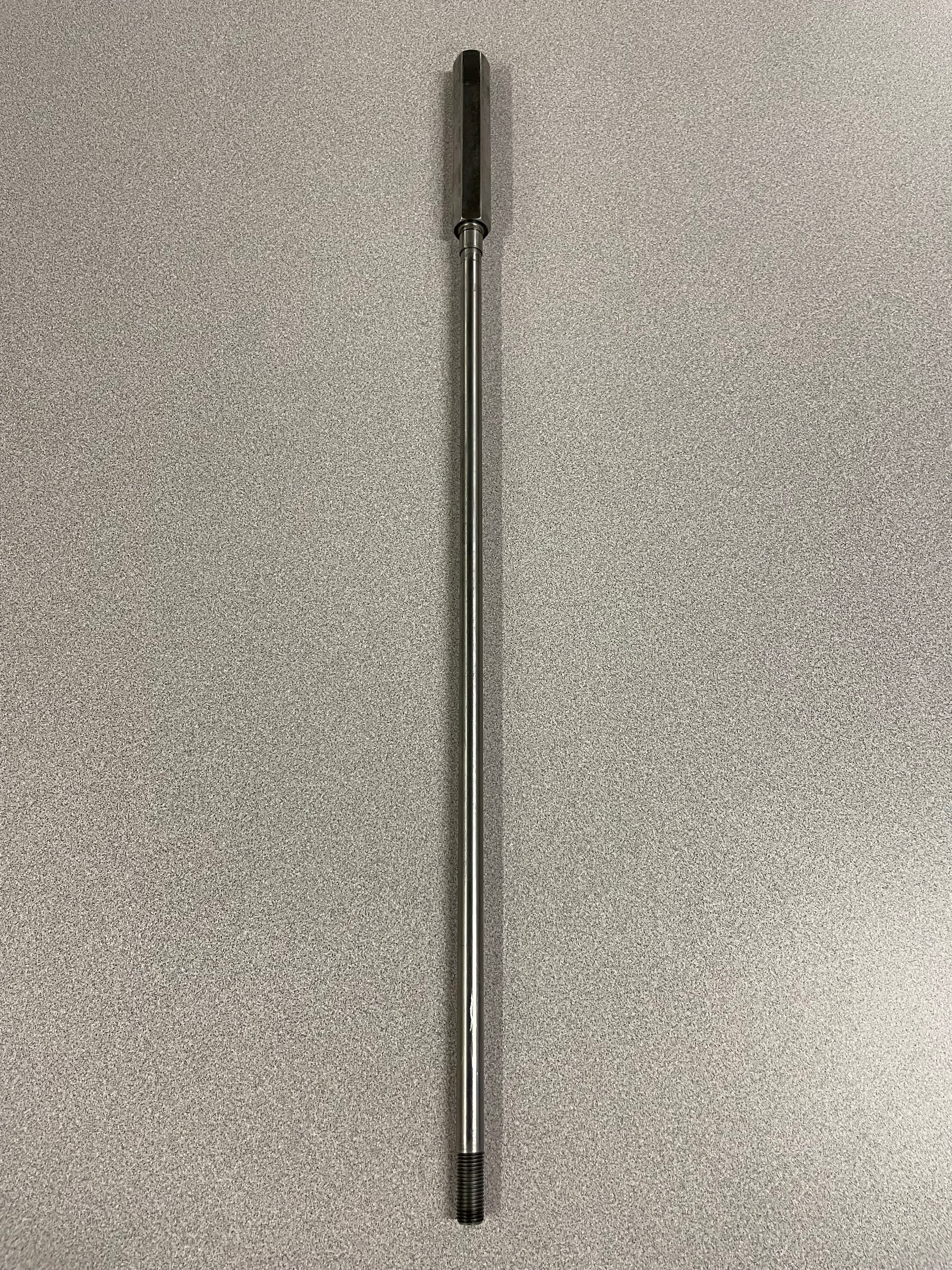
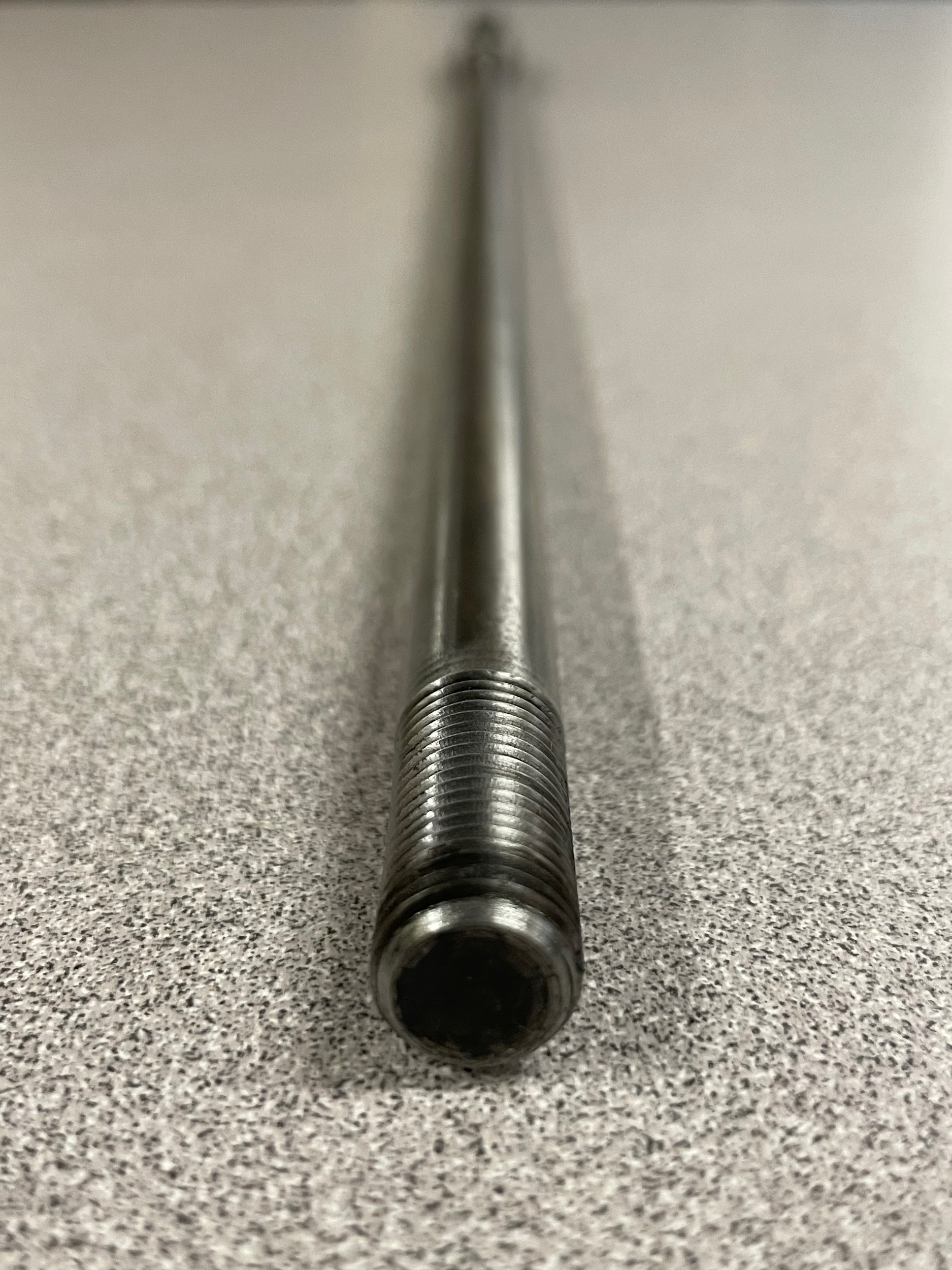
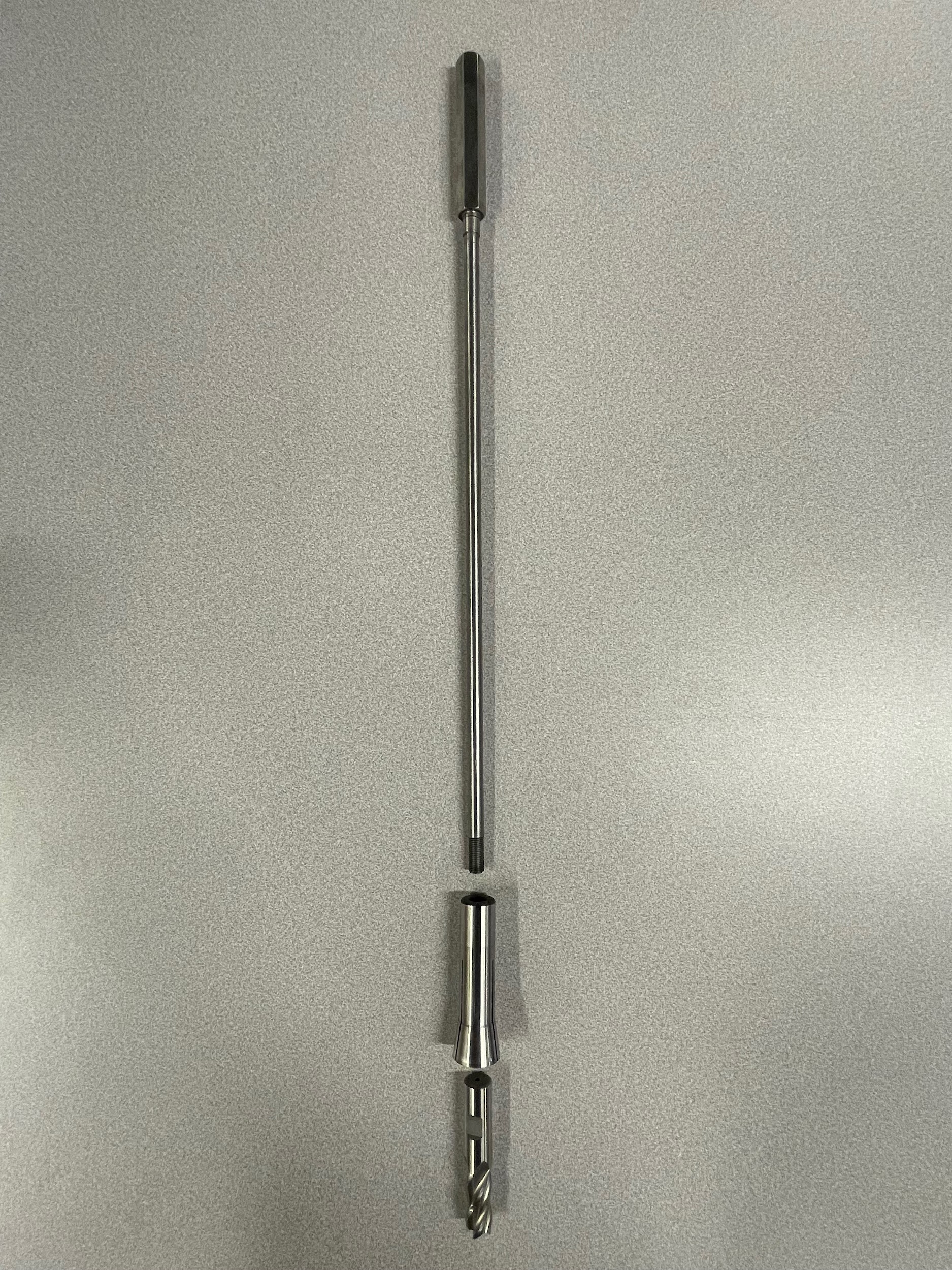
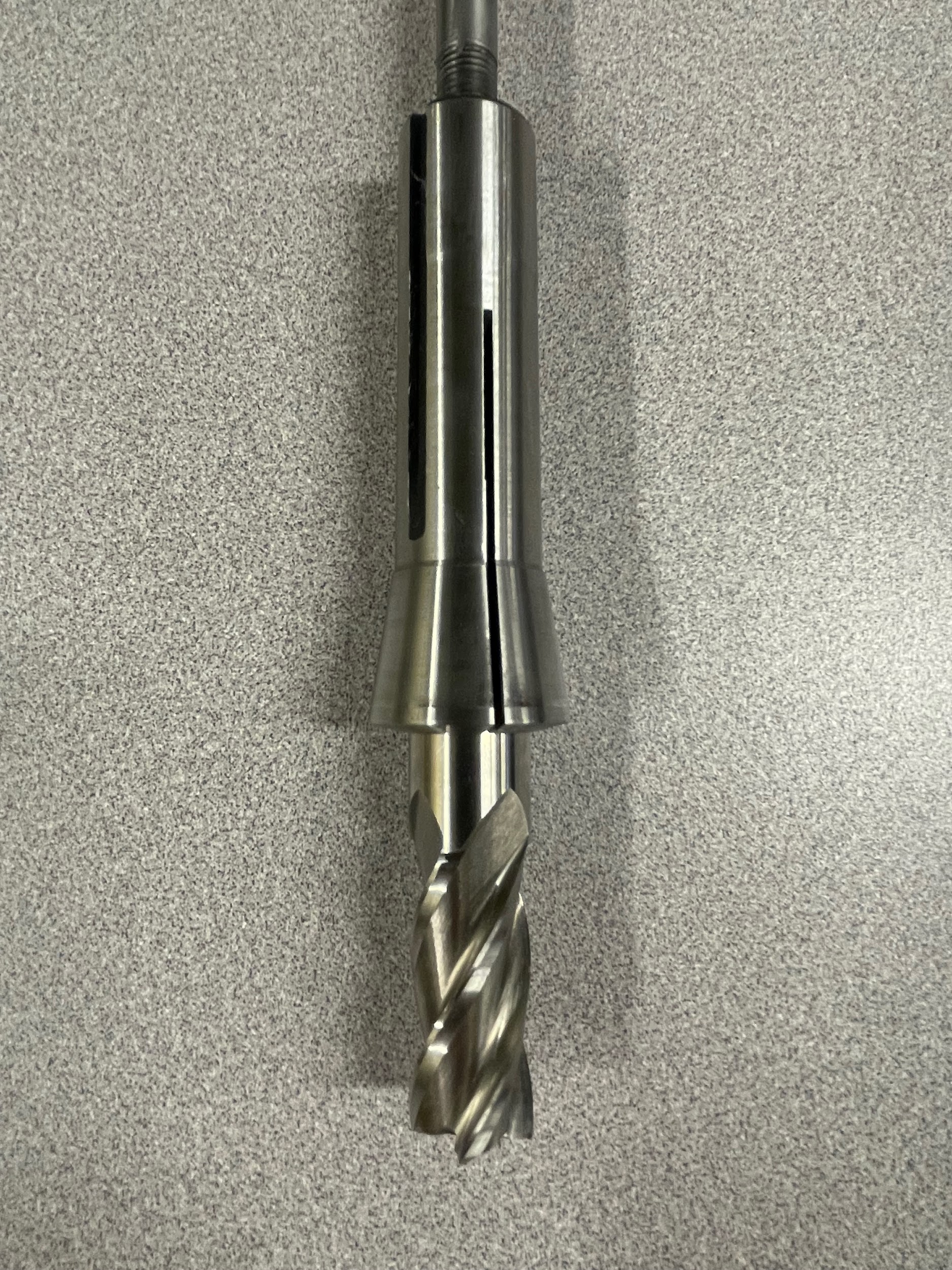
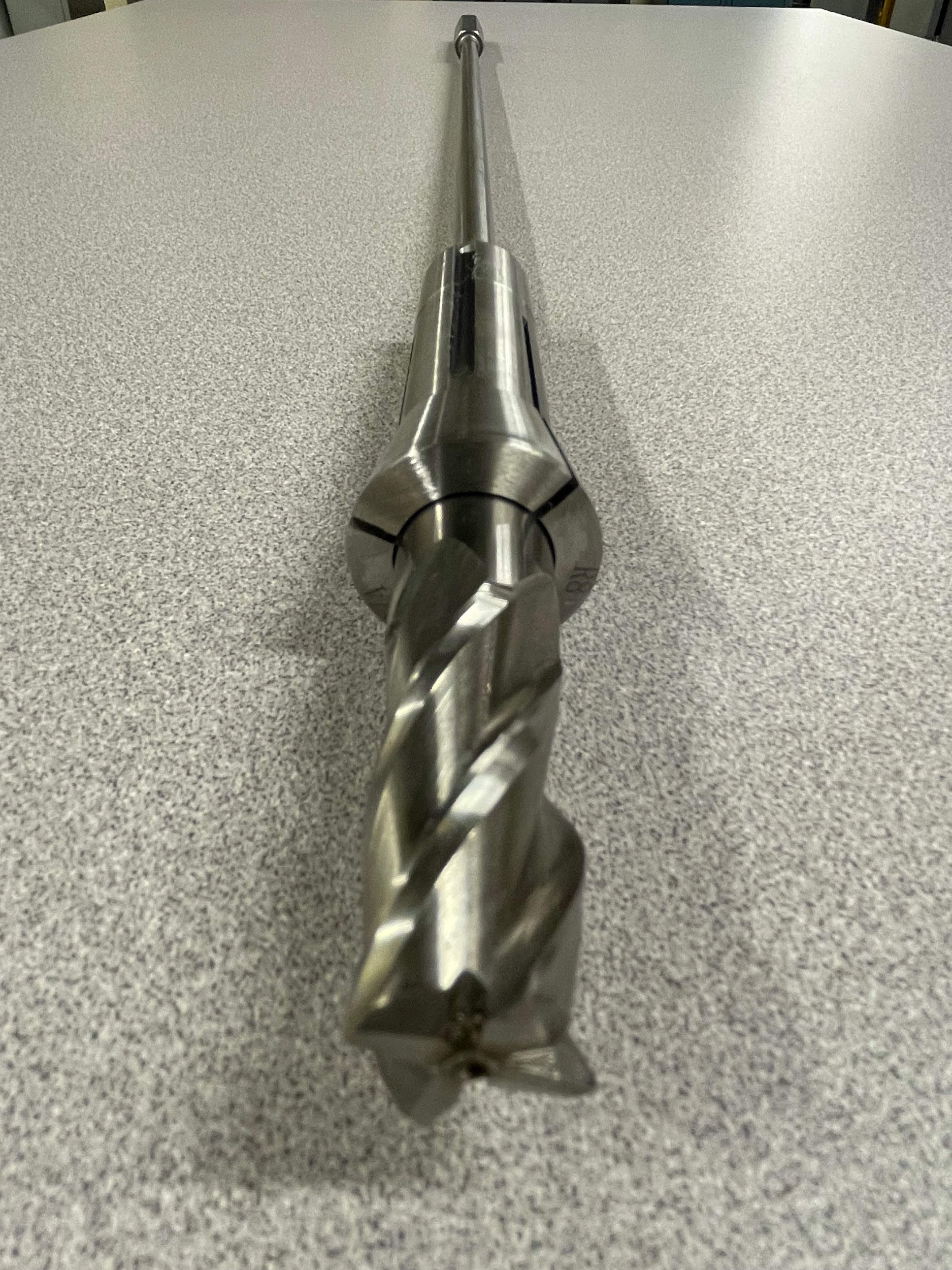
A draw bar is a long rod that has a head with a hex on one end and threads on the other. The draw bar sits inside the spindle, and the larger diameter head rests against the top. The threaded end of the draw bar is used to screw into the ends of various tool holders that may be inserted into the spindle. As the draw bar is tightened, the tool holder gets pulled further into the spindle and increases the engagement of the R8 taper, locking it in position.
Drill Chuck
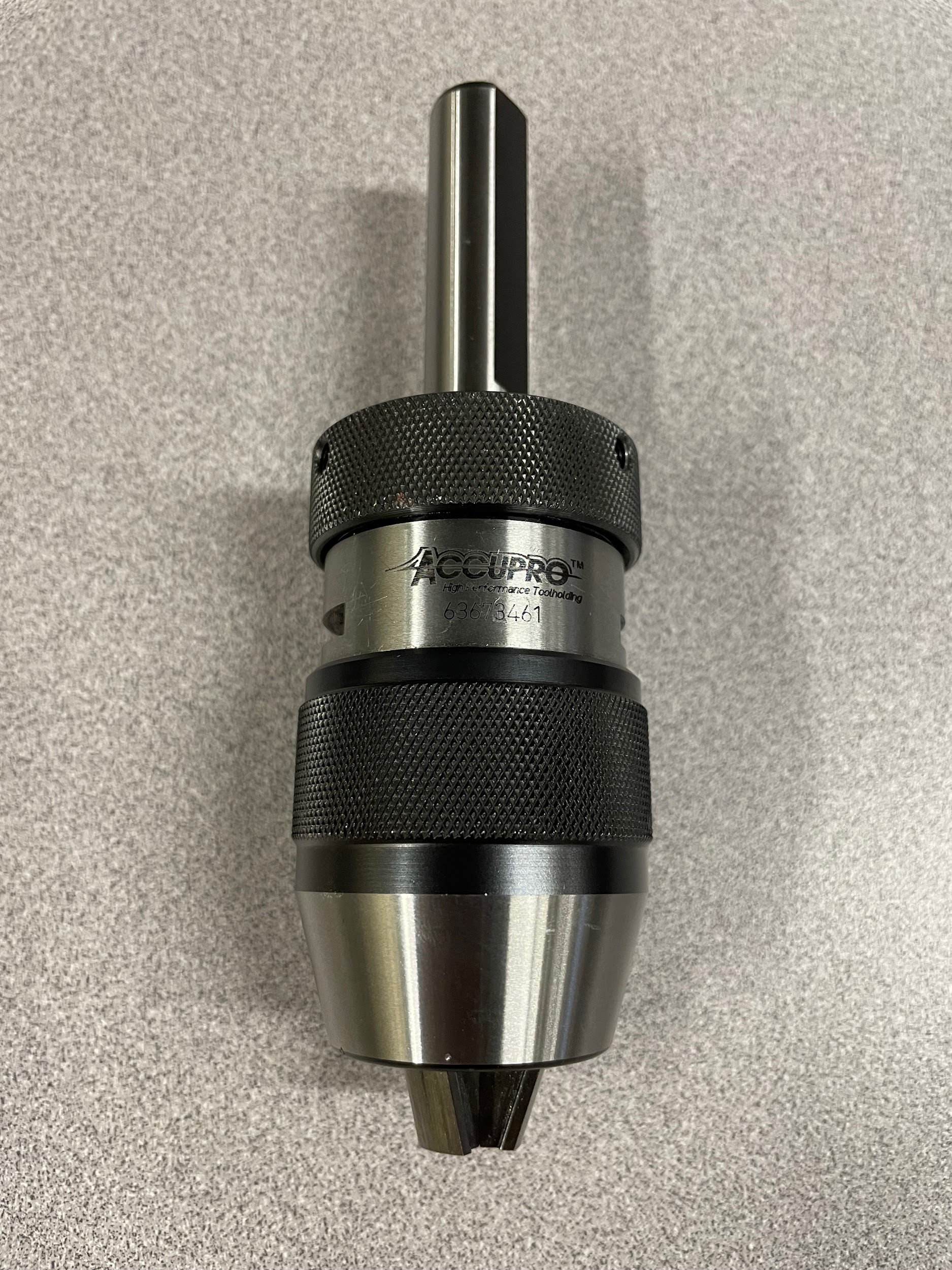
A drill chuck for milling machines can be similar to those of the drill press but is often of better quality and may be of the keyless variety. Keyless chucks have a couple advantages over keyed chucks. The first is that they are easy to use and require only hand strength to tighten. The second is that if they start to slip, the internal mechanism will twist, tightening the chuck and stopping the slipping action. One thing to note is that drill chucks are only for holding plunging style tools that are capable of stabilizing themselves. End mills and all other side cutting tools cannot be held securely in a drill chuck.
Attributions
- Figure 9.87: End mill holder by Micky R. Jennings, courtesy of Wenatchee Valley College, for WA Open ProfTech, © SBCTC, CC BY 4.0
- Figure 9.88: End mill holder 2 by Micky R. Jennings, courtesy of Wenatchee Valley College, for WA Open ProfTech, © SBCTC, CC BY 4.0
- Figure 9.89: End mill holder with tool by Micky R. Jennings, courtesy of Wenatchee Valley College, for WA Open ProfTech, © SBCTC, CC BY 4.0
- Figure 9.90: Setscrew flats by Micky R. Jennings, courtesy of Wenatchee Valley College, for WA Open ProfTech, © SBCTC, CC BY 4.0
- Figure 9.91: Three spring collets by Micky R. Jennings, courtesy of Wenatchee Valley College, for WA Open ProfTech, © SBCTC, CC BY 4.0
- Figure 9.92: Two spring collets by Micky R. Jennings, courtesy of Wenatchee Valley College, for WA Open ProfTech, © SBCTC, CC BY 4.0
- Figure 9.93: Spring collet by Micky R. Jennings, courtesy of Wenatchee Valley College, for WA Open ProfTech, © SBCTC, CC BY 4.0
- Figure 9.94: Spring collet thread by Micky R. Jennings, courtesy of Wenatchee Valley College, for WA Open ProfTech, © SBCTC, CC BY 4.0
- Figure 9.95: Draw bar by Micky R. Jennings, courtesy of Wenatchee Valley College, for WA Open ProfTech, © SBCTC, CC BY 4.0
- Figure 9.96: Draw bar threads by Micky R. Jennings, courtesy of Wenatchee Valley College, for WA Open ProfTech, © SBCTC, CC BY 4.0
- Figure 9.97: Draw bar, collet, and tool by Micky R. Jennings, courtesy of Wenatchee Valley College, for WA Open ProfTech, © SBCTC, CC BY 4.0
- Figure 9.98: Draw bar, collet, and tool 2 by Micky R. Jennings, courtesy of Wenatchee Valley College, for WA Open ProfTech, © SBCTC, CC BY 4.0
- Figure 9.99: Draw bar, collet, and tool 3 by Micky R. Jennings, courtesy of Wenatchee Valley College, for WA Open ProfTech, © SBCTC, CC BY 4.0
- Figure 9.100: Keyless drill chuck by Micky R. Jennings, courtesy of Wenatchee Valley College, for WA Open ProfTech, © SBCTC, CC BY 4.0
A tool holding device that utilizes an accurate bore and set screw to secure tools.
A tool holding device that utilizes the flexibility and collapse of the device under force to secure tools.
A bar that pulls tools, or tool holding devices, into a machine taper.
A device used to easily hold hole making tools.