11.2 Grinding Wheels
Tim A. Bacon
The grinding wheel is the cutting tool used in precision grinding operations. These wheels are similar to the ones used for offhand grinding, covered in the chapter on hand tools and benchwork. They are made of abrasive grain held together with a bonding material. Off-hand grinding wheels are typically straight in shape. The motion of the machine can be accurately controlled. This allows a selection from a variety of wheel shapes that will best fit the application.
Shape
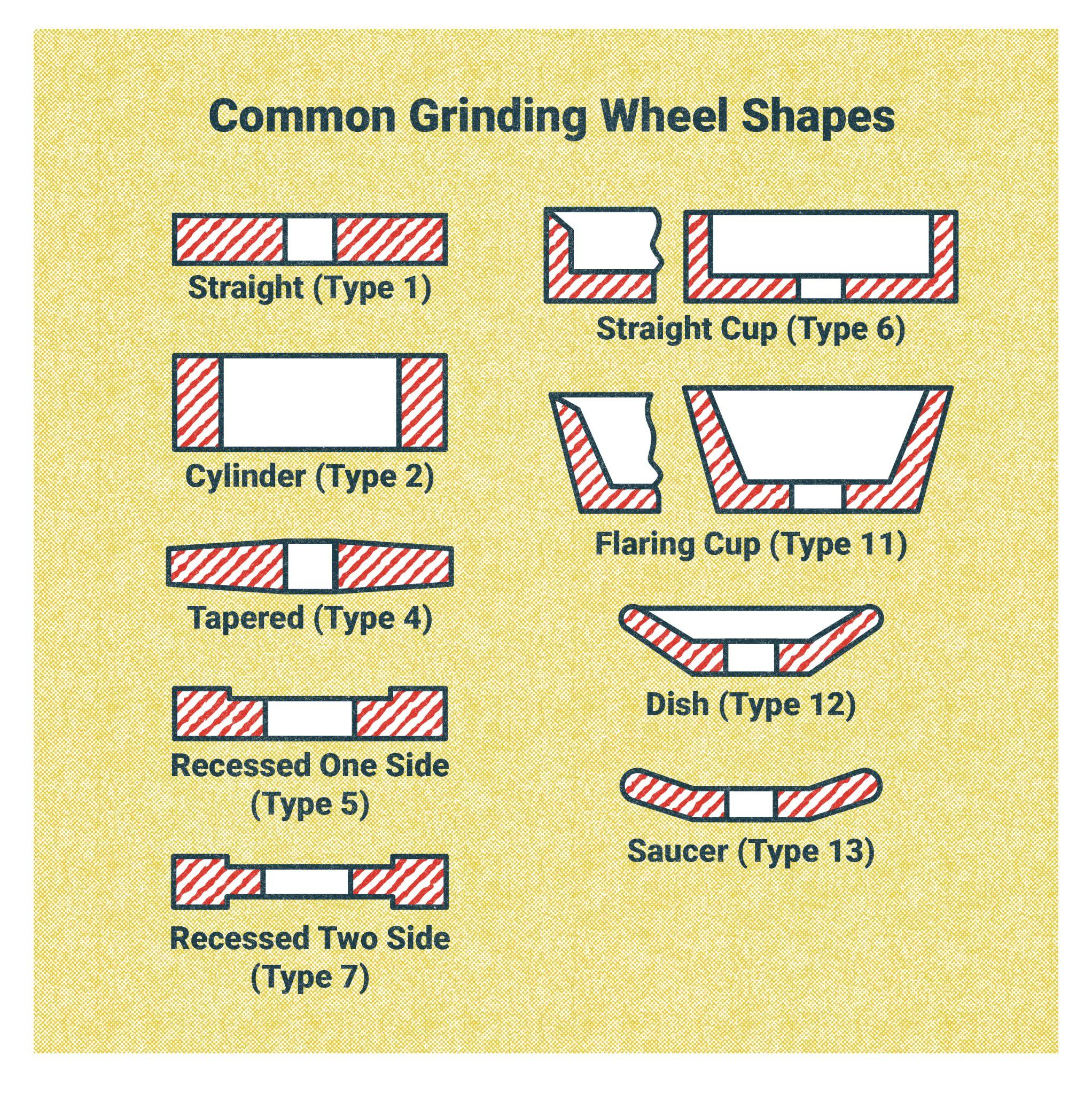
Types of wheels seen above; Straight (Type 1), Cylinder (Type 2), Tapered (Type 4), Recessed One Side (Type 5), Recessed Two Side (Type 7), Flaring Cup (Type 11), Dish (Type 12), and Saucer (Type 13).
The feature that is being ground will help identify the shape of the grinding wheel that is needed. A small part with a groove will require a narrow, straight wheel. Dressing, or modifying a tool will use a cup style wheel.
A straight wheel, as used on off-hand grinders, is the most common wheel for a precision grinder. A wheel may also have features that are relieved or recessed. These wheels will minimize contact between the sides of the wheel and the workpiece. Cup, saucer, and dish shaped wheels are usually used for tool grinding, or modification.
The face of the wheel is the surface that is designed for grinding. The face is usually defined as the periphery, or outside circumference, of the wheel. In some applications, with a vertical grinder, the face of the wheel is the flat surface. When grinding two surfaces that are perpendicular to each other, the side of the wheel may be engaged at the same time as the face. This may be done to produce features such as a shoulder, slot, or groove.
Abrasive
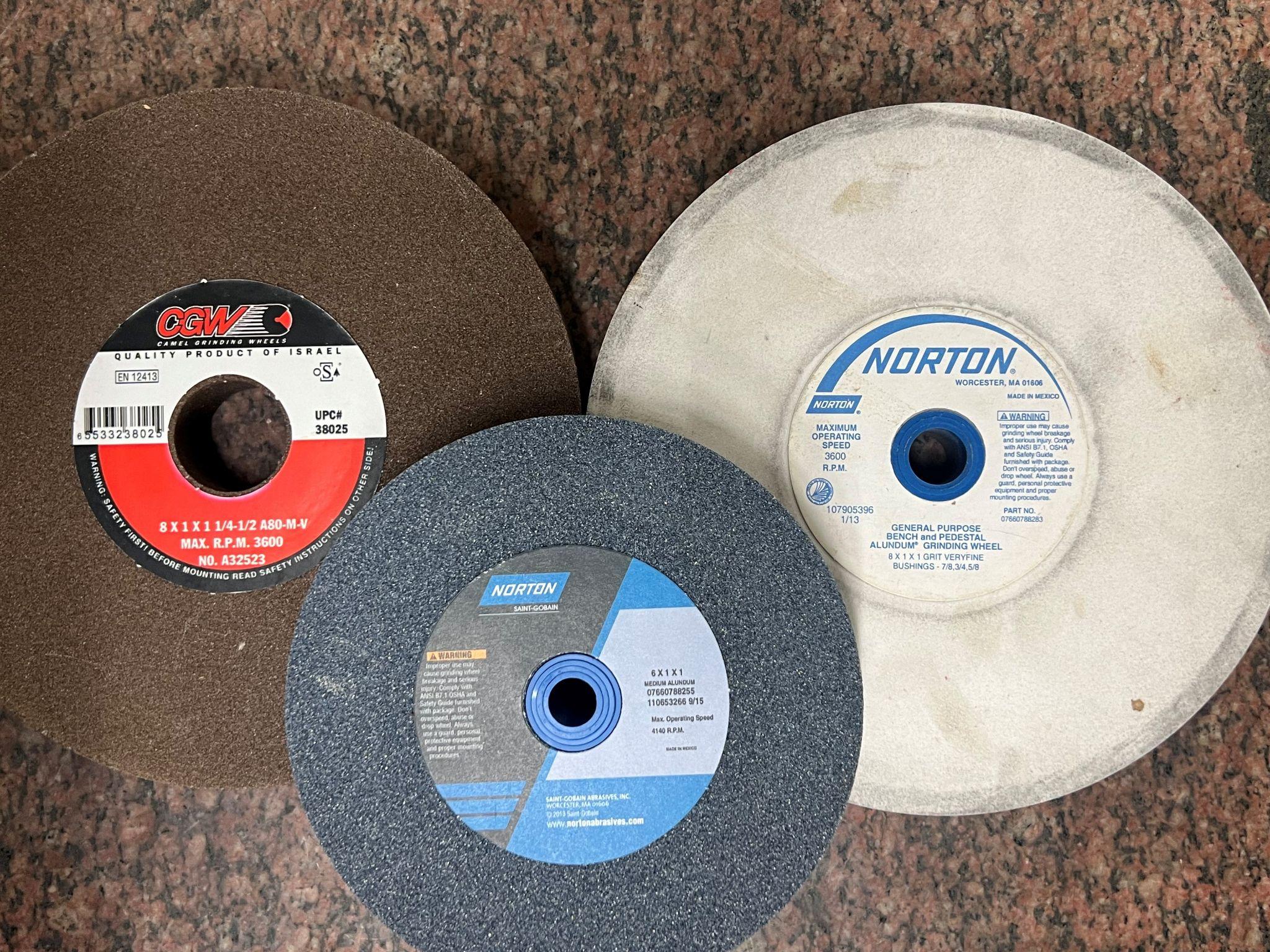
Grinding wheels are typically made of one of three combinations of abrasive material. These combinations are aluminum oxide, ceramic aluminum oxide, or silicon carbide. Aluminum oxide, and ceramic aluminum oxide wheels are identified by the letter A. The silicon carbide wheel will have the letter C on it.
Aluminum oxide is used for steels. Ceramic aluminum oxide is for grinding materials containing iron. Silicon carbide wheels are referred to as green wheels. They are for grinding carbide.
It is important to only grind material appropriate for the specific abrasive wheel being used. For example, grinding aluminum on a wheel designed for steel will plug up the wheel, and build up heat. Excessive heat will cause the wheel to explode.
Grit
The grit, or grain size of the abrasive type is descriptive of the material that makes up the wheel. The lower the number, the coarser the wheel. Higher numbers indicate a finer grain pattern. Coarse wheels with a large grain structure will remove material quickly and create a rough surface finish. A finer wheel will remove material more slowly and produce a smoother surface finish.
Coarse wheels will cut soft metals better because the larger grains can penetrate the workpiece more easily. When grinding harder metals, a finer wheel with a tighter grain pattern provides more cutting points for rapid material removal. A consideration is that as the grit becomes finer, the heat from grinding increases. This means a slower work speed is necessary when finishing a part.
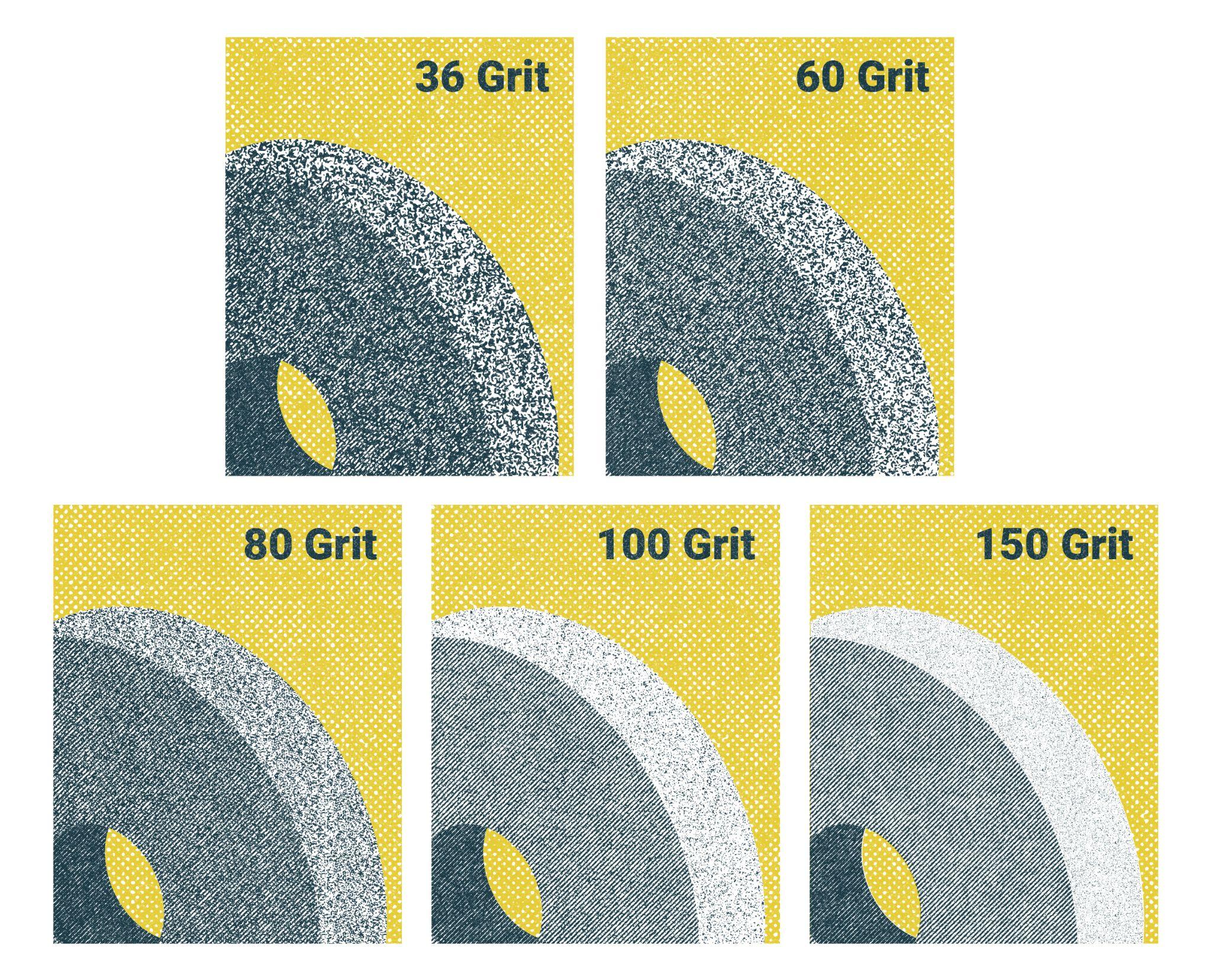
Grade
The grade of the grinding wheel refers to the hardness, or strength, of the bond. Grade A is the softest, and Z is the hardest.
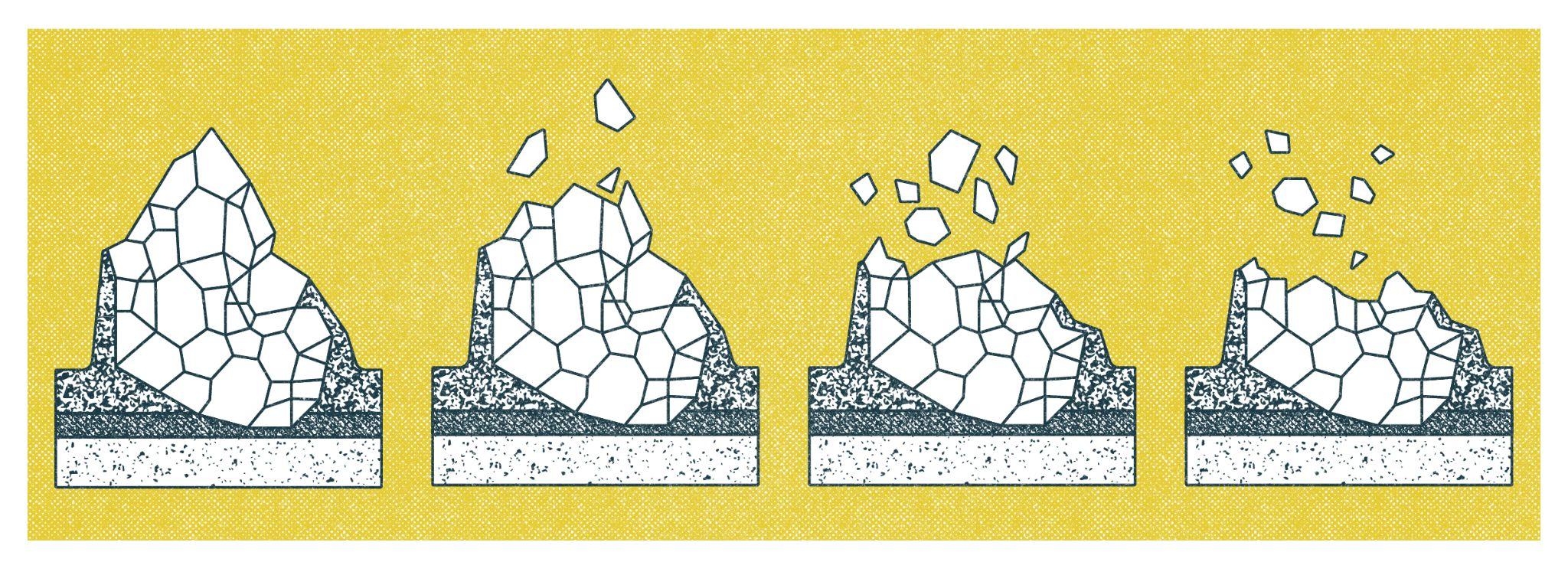
On the left is the sharp “new” grain. As the wheel breaks down, moving to the right, the grain becomes dull.
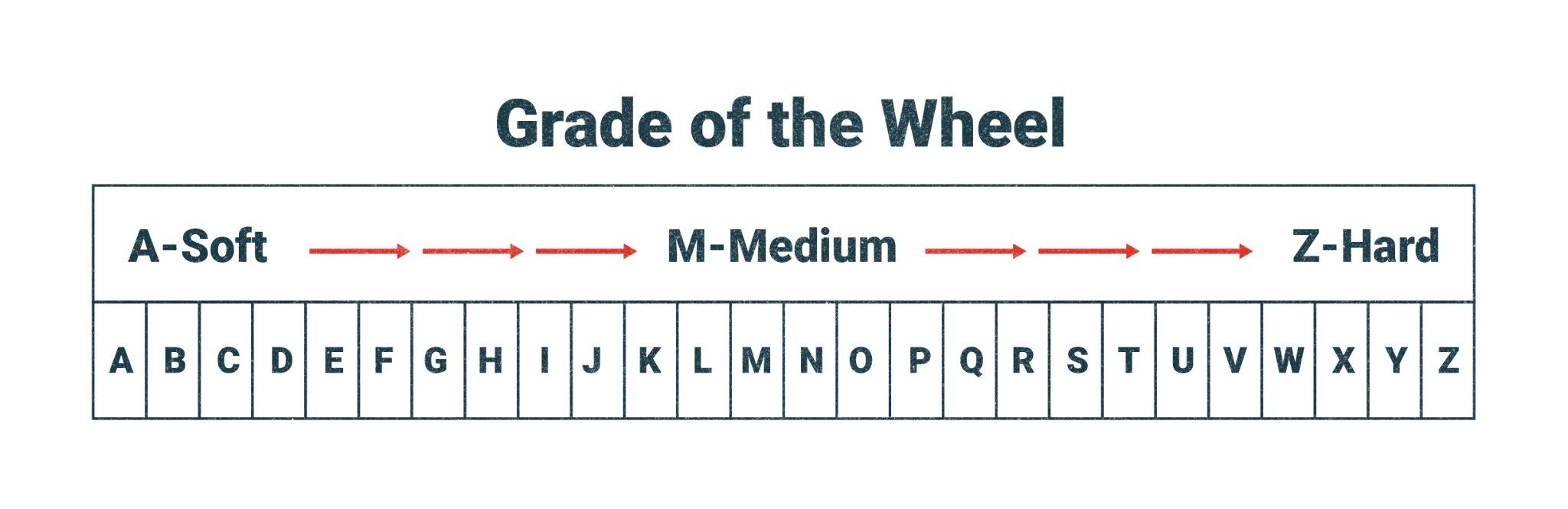
Generally, a softer wheel is used for hard materials because the wheel will release old grains before it becomes dull. This exposes new, sharper grains and helps to maintain the cutting process of the wheel. If a hard wheel is used for grinding a hard material, the grains will not release, and then the wheel will become dull. This causes wheel glazing, overheating, and burning of the work surface. A harder wheel should be used when the area of contact is small. Hard wheels are more wear resistant and are the best choice when a larger amount of material is to be removed. Selecting a softer wheel when making lighter finish cuts will increase the quality of the finish and assist in achieving dimensional accuracy.
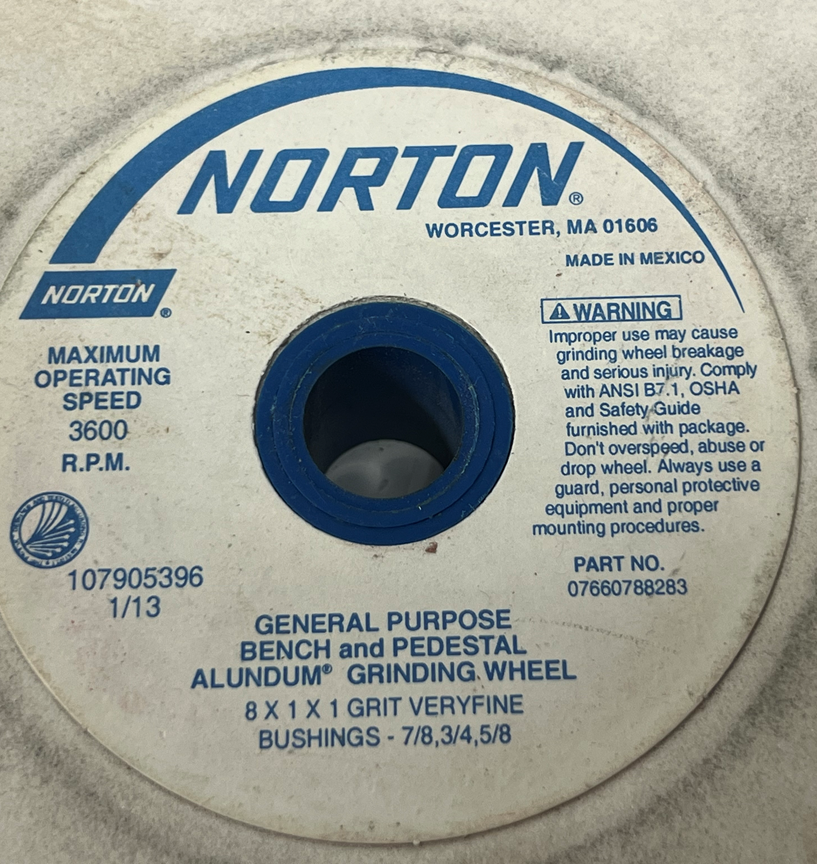
Attributions
- Figure 11.9: Grinding wheel shapes by Nicholas Malara, for WA Open ProfTech, © SBCTC, CC BY 4.0
- Figure 11.10: Grinding wheels by T Bacon, courtesy of Bates Technical College, for WA Open ProfTech, © SBCTC, CC BY 4.0
- Figure 11.11: Grinding wheel grit by Nicholas Malara, for WA Open ProfTech, © SBCTC, CC BY 4.0
- Figure 11.12: Grinding wheel grade by Nicholas Malara, for WA Open ProfTech, © SBCTC, CC BY 4.0
- Figure 11.13: Hardness chart related to the grade of the wheel by Nicholas Malara, for WA Open ProfTech, © SBCTC, CC BY 4.0
- Figure 11.14: Example of label by T Bacon, courtesy of Bates Technical College, for WA Open ProfTech, © SBCTC, CC BY 4.0
the profile of the grinding wheel
A slight concave shape of the grinding wheel
A significant concave, or undercut feature of the grinding wheel
The grit that removes material by rubbing (grinding)
relates to the size of the individual grain of the abrasive found in grinding wheels
see grit. also known as grit
refers to the hardness of the abrasive bond on the grinding wheel
when the grinding wheel builds up material, and becomes too smooth to grind efficiently