Chapter 11: Surface Grinders
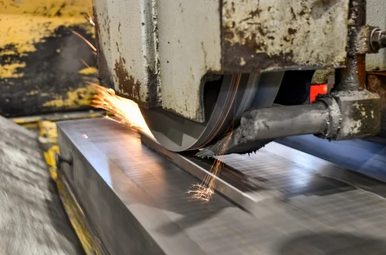
Overview
Did you know that surfaces of parts such as bearings and shafts that operate in planes, trains, and automobiles must fit precisely together in order to function properly and efficiently? What makes this possible is the process of grinding.
The growth of industries like automotive, aerospace, machinery, electronics, and construction drives the demand for grinding machines. These industries rely on grinding processes for precision machining, surface finishing, and material removal operations, creating a continuous demand for grinding machines to support manufacturing activities. (Global Market Insights, 2024, para. 1)
Grinders are typically operated by trained professionals who use them to create high-precision components for a wide range of applications. Precision grinding is typically the final operation for parts that are hardened and often can’t be finished with traditional tools. In fact, grinding is more than just finishing a part or tool. It also provides an essential element for some parts. For example, when two parts are perfectly flat and placed together, they create a vacuum between them. When the parts are small, the vacuum will keep the two parts together as if they were magnetized. This characteristic is used to keep gauge blocks together when taking measurements. Grinding is the process used to allow this function to occur.
Objectives
- Explain proper safety procedures when using a precision grinder.
- Explain the functions of various components of the surface grinder.
- Correlate grinding wheels to the operations being performed.
- Predict workholding for surface grinding.
- Associate wheel grit size to finish and material removal.
- Describe the process of dressing a grinding wheel
Key Terms
- Grinding
- Blanchard
- Ingoing nip
- Outgoing nip
- OD (outside diameter)
- ID (inside diameter)
- Shape
- Abrasive
- Grit
- Grade
- PPE (personal protective equipment)
- Ring test
- Dressing
- Glazing
- Burning
- Scratches
- Waviness