51 Lamellar Tearing
Lamellar tearing is a subsurface cracking pattern in wrought steel base metal caused by welding. The cracking runs parallel to the working direction and has a terraced, step-like pattern.
Lamellar tearing occurs when tensile stresses from welding develop through the thickness of the base metal and act upon planes of weakness running parallel to the metal surface causing them to separate. The planes of weakness are caused by nonmetallic inclusions consisting of metallic oxides, sulfides, and silicates.The inclusions are formed during solidification in the steelmaking process from additives to the melt or contamination from refractory in the mold. Hot or cold working elongates nonmetallic inclusions in the working direction if they are plastic at the working temperature. The net result of the elongated nonmetallic inclusions is to decrease through-thickness ductility. This results in lamellar tearing parallel to the direction of the inclusions.
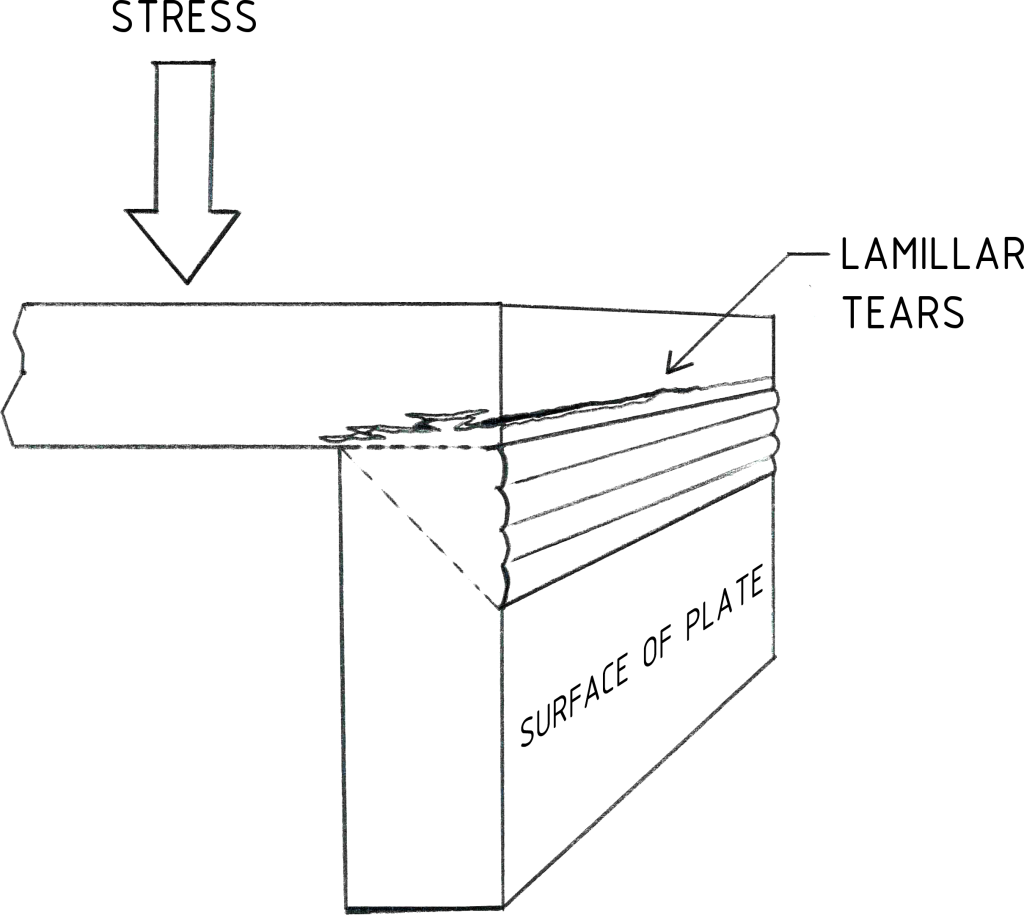
Lamellar tearing is most likely to occur when welding a steel plate using groove welds, fillet welds, or combinations of them.
T-joints may be especially susceptible to lamellar tearing. The two members of a T-joint are located at approximately right angles to each other in the form of a T. Under these conditions, high tensile stresses can develop perpendicular to the mid-plane of the steel plate. The magnitude of the tensile stresses depends on the size of the weld, the welding procedure, and the amount of joint restraint imposed by the welding design.
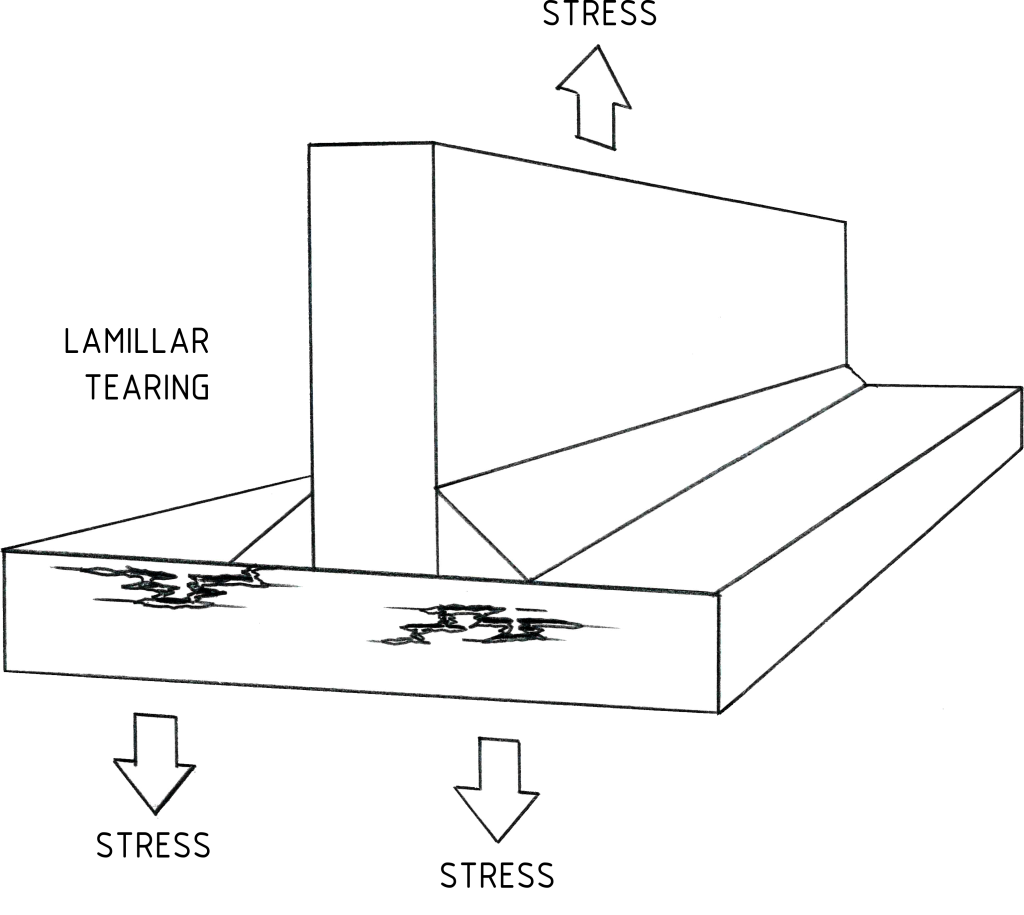
Lamellar tearing detection is difficult because it usually does not break to the surface. Radiographic examination (RT) and ultrasonic examination (UT) are the most applicable methods for detection of lamellar tearing, which has the appearance of step-like, jagged cracking, with each step nearly parallel to the mid-plane of the plate.
Lamellar Tearing Prevention
Lamellar tearing is prevented most reliably by the use of specially processed steel products that do not contain elongated nonmetallic inclusions. Such steel products are used in critical applications where lamellar tearing is detrimental.
Other methods of reducing lamellar tearing in regular steel products rely on reduction of the stress in the welded joint. These methods include changing the location and/or design of the weld joint to minimize through-thickness strains, using a lower strength weld metal, reducing hydrogen in the weld, using preheat and interpass temperatures of at least 200ºF, and peening the weld bead immediately after completion of a weld pass. However, peening should never be performed on the root pass or on the cover pass (the final pass). Peening the root may lead to issues with cracking, and peening the cover pass may mask discontinuities on the surface of the weld.
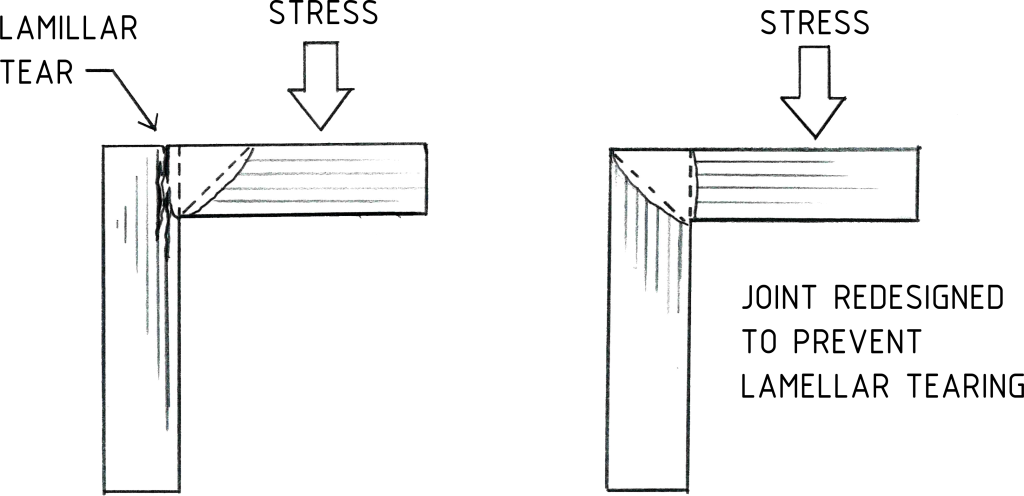