4 Pipe Connections
Welding is the most common method of joining pipe. Pipe joints are typically butt-welded or made with socket fittings. Socket fittings are typically used on small diameter pipe and tubing with less than 2” OD. The socket fitting forms a lap joint that is welded with a fillet weld.
The most commonly used joint design for joining pipe is the open root single-V groove joint. If the joint is to be welded with an open root, a root face (land) is typically ground on each bevel. The size of the root face varies with the wall thickness of the pipe and the welding process used.
A backing ring, or chill ring, can be used depending on the application. If a backing ring is used, no root face is required. This is commonly referred to as a feather edge.
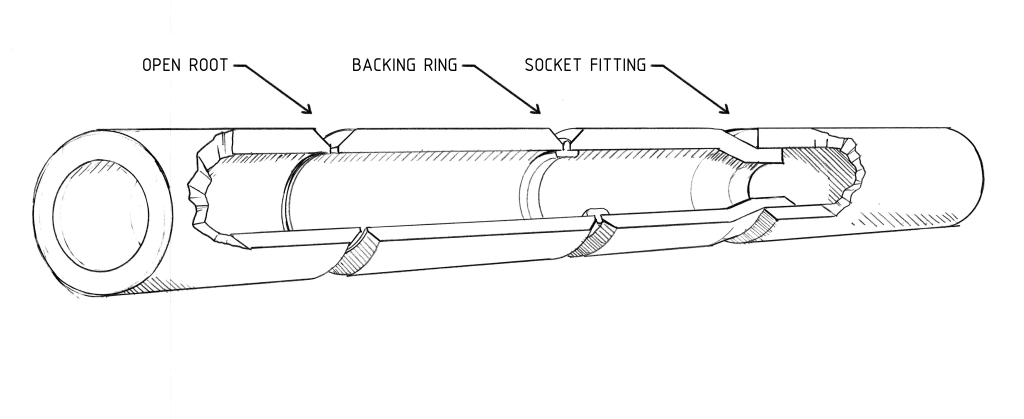
Joint Design
Joint preparation involves several factors, including pipe diameter, wall thickness, the type of pipe to be welded, and the welding process used. Pipe up to 3/16” wall thickness can be welded without any joint preparation. Most pipes over 3/16” wall thickness require some joint preparation.
A wide groove angle may not be the best choice for thin-wall pipe because it would require more passes to fill the joint than a narrower groove angle. Each pass would add heat to the weld zone, which may result in overheating. This can create problems with distortion due to excessive heat buildup in the weld zone. Narrower groove angles require fewer passes, which result in less overall heat build-up.
The type of pipe must be considered as well. For example, carbon steel pipe requires a single-V groove joint design, typically with a root face unless a backing ring is used. However, stainless steel pipe does not require a root face. Instead, each bevel is prepared with a feather edge, also called a knife edge. Aluminum pipe typically calls for a single-U groove joint preparation.
The welding process also influences joint design. For example, SMAW and GTAW require large groove angles so the arc can reach into the root of the joint to ensure complete penetration. GMAW and FCAW require smaller groove angles because wire electrodes are narrow, which give them better access to the root area.
Pipe with a wall thickness between 3/16” and 5/16” requires a groove angle in the range of 60º to 70º with a root face of 3/32” to 1/8”. Thicker pipe requires a 75º groove angle, with a root face between 3/32” and 1/8” and a root opening between 3/32” and 1/8”.
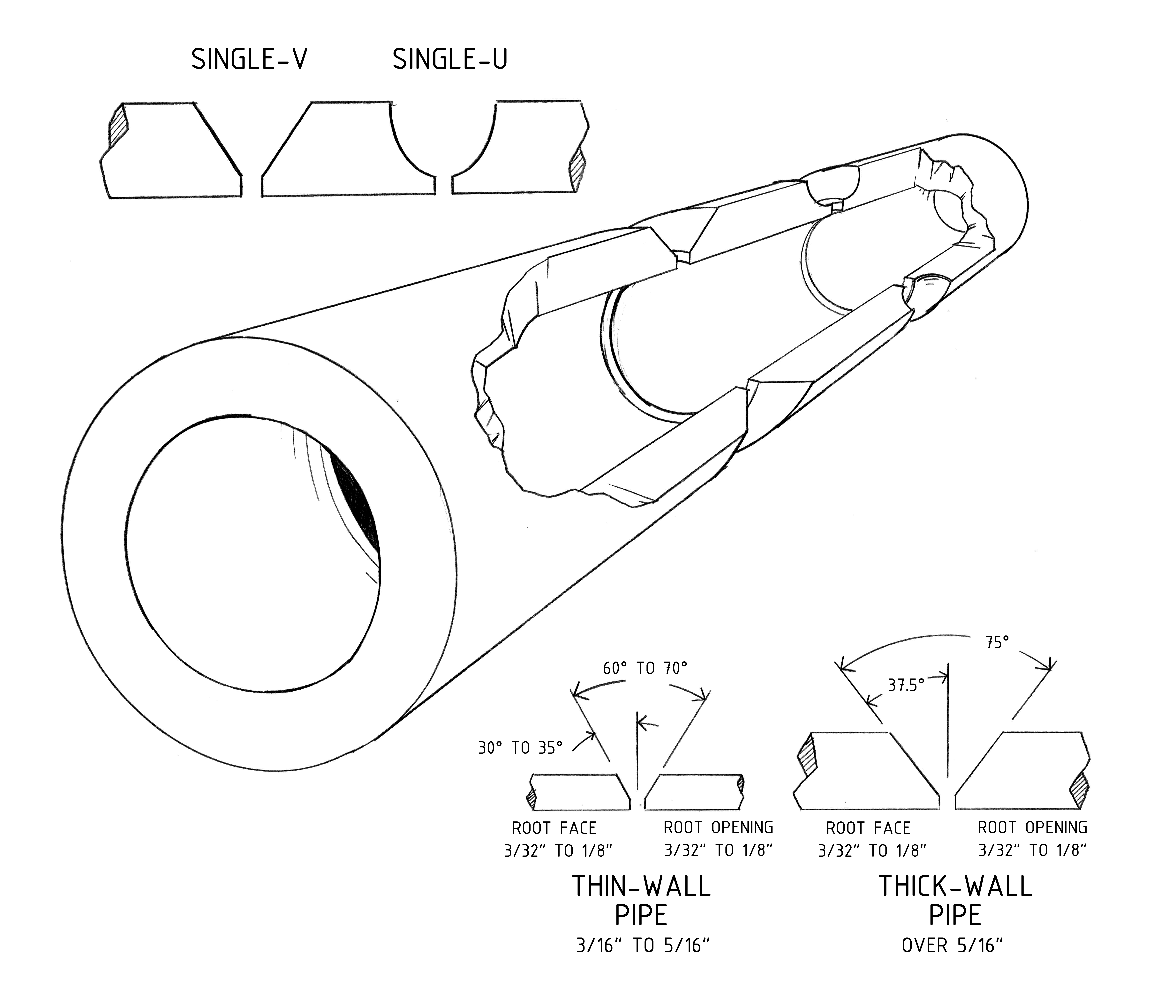
Joint Preparation
To prepare a pipe joint, each section of pipe must be beveled to the proper angle. The best way to produce a smooth, even bevel is to use a mechanized beveller with an OFC or PAC cutting torch. If necessary, bevels can be cut manually. However, manual preparation is time-consuming and less accurate than mechanized beveling.
Typically, the groove angle, the size of the root face, and the root opening are detailed in the WPS. If a backing ring is specified, no root face is required. A file should be used to deburr the inside edge of each section of pipe, and a wire brush should be used to clean the groove surfaces. When necessary, an appropriate cleaning solvent should be used to remove any oil, grease, or other contaminants.
Joint Alignment and Fit-up
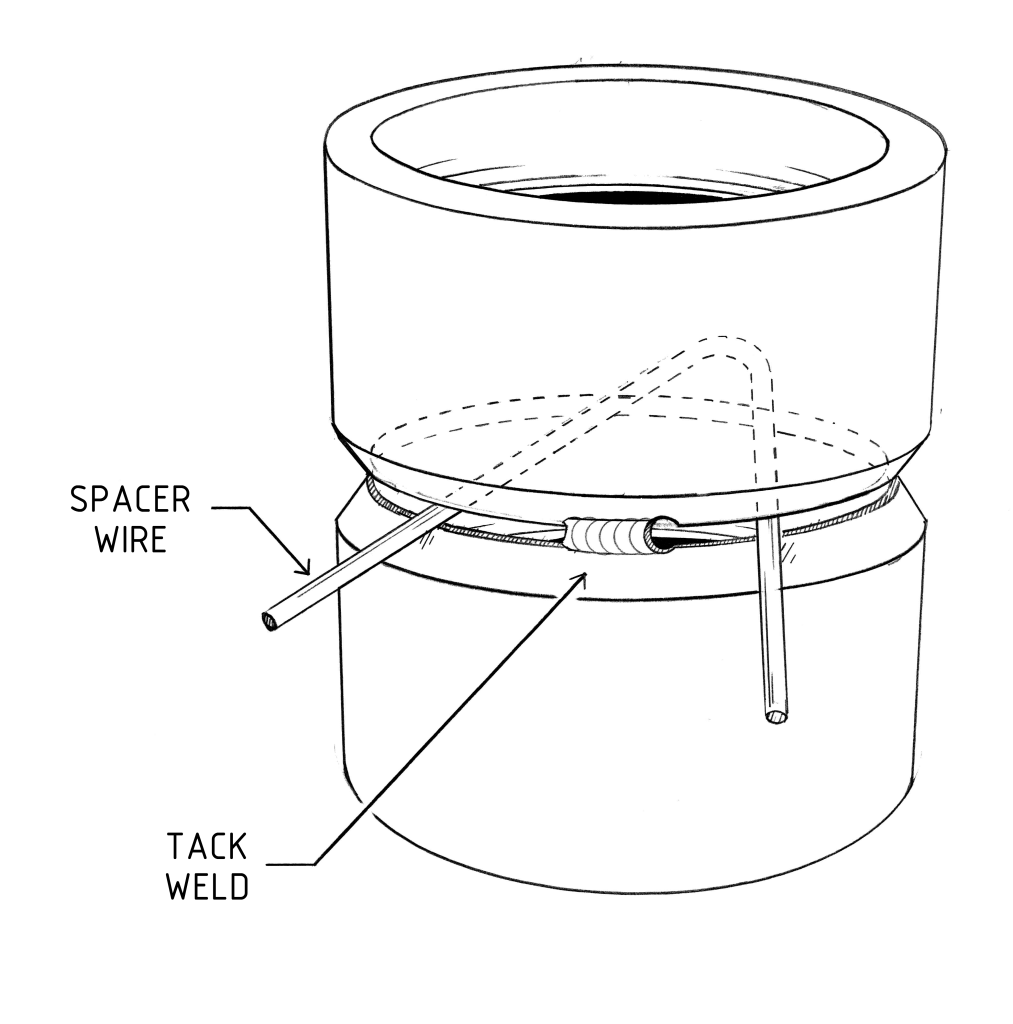
Joint fit-up must be as consistent as possible around the circumference of the pipe to ensure a quality weld. Typically, pipe line-up clamps are used to hold pipe sections and keep them aligned during tacking and welding of the root pass. On large-diameter pipe, it may be necessary to leave the line-up clamp in place until most of the root bead is deposited in order to prevent cracking caused by the weight of the pipe. Pipe line-up clamps are available for pipes ranging from 1” to over 9” in diameter.
There are two types of line-up clamps-those that attach to the inside of the pipe and those that attach to the outside of the pipe.
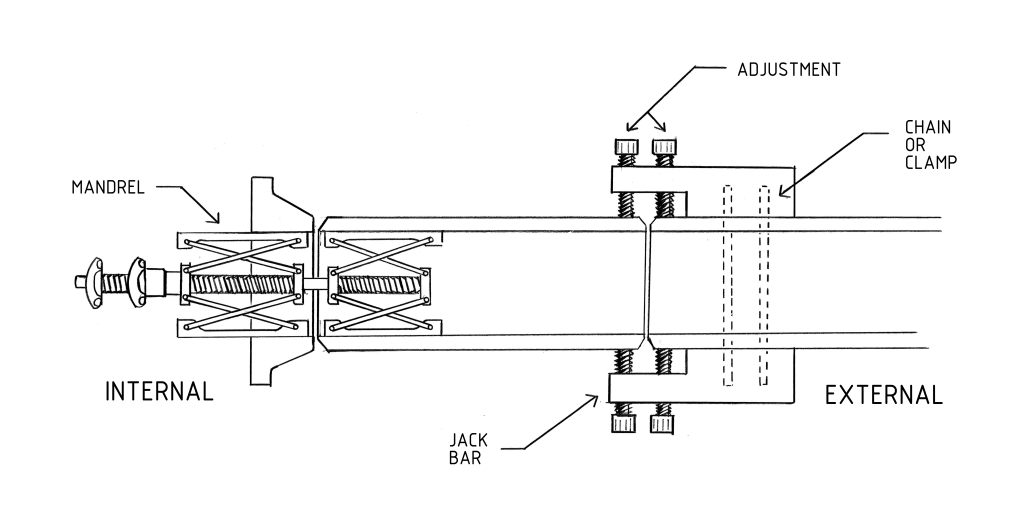
Consumable inserts can also be used as spacers to ensure a properly spaced root opening. Consumable inserts become part of the root bead. Five classes of inserts are available.
Backing Rings/Chill Rings
Backing rings, or chill rings, are commonly used in pipe welding. Backing rings prevent excessive burn-through and keep spatter and slag from falling into the pipe. They also eliminate the need for backing gas on base metals prone to sensitization, such as stainless steel or titanium. Backing rings have spacers to ensure a consistent root opening for tack-up.
Some backing rings are equipped with spacers that are designed to be broken away once the tack welds are deposited. Other rings have spacers consisting of consumable inserts that become part of the root bead. However, backing rings may not be appropriate for some applications because they can provide a source of turbulence and resistance to the flow of material through the pipe.
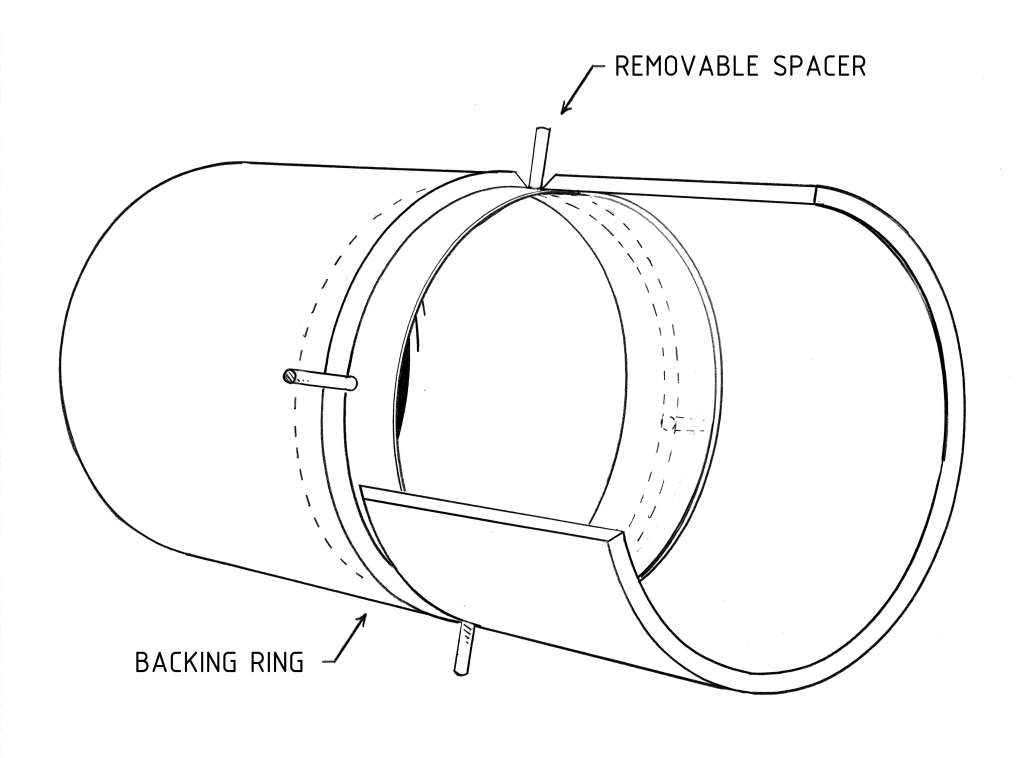