6 Tack Welds
Tack welds keep pipe joints aligned during welding. They also maintain a consistently spaced root opening on open root joints. Typically, four evenly spaced tack welds are made around the pipe at approximately the 12, 3, 6, and 9 o’clock positions or the 11, 2, 5, and 8 o’clock positions, depending on welder preference.
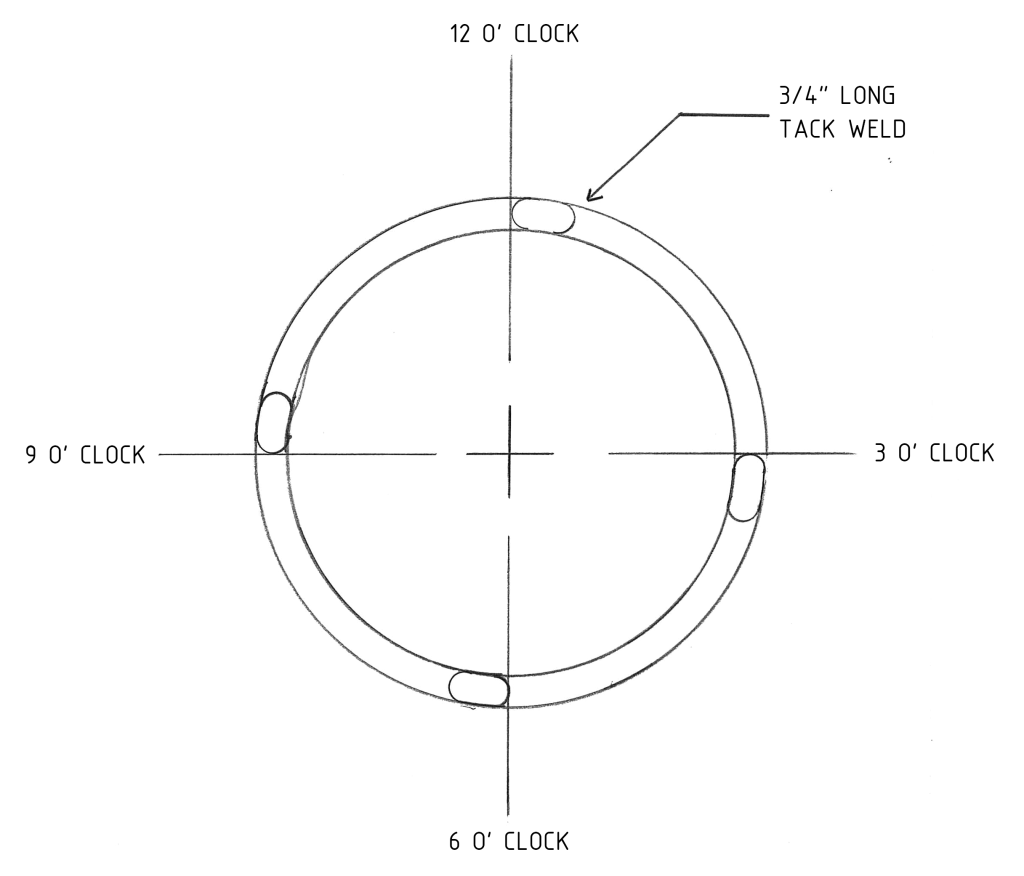
Each tack weld should be about ¾” long and should penetrate to the root of the joint.
The larger the pipe, the longer the tack welds required. As a general rule, tack welds on large-diameter pipe should be about 5-10% of the pipe diameter. After tack-up, the joint should be inspected to be sure the root opening is consistent and any misalignment (hi-lo) falls within acceptable limits.
Depositing Tack Welds
- Strike the arc in the root of the joint about ½” in front of the starting position for the tack weld.
- Pull the electrode back to establish a long arc length.
- A long arc length helps to stabilize the arc. It also allows time for shielding gas formers in the flux coating to break down and form a gas shield to protect the molten metal.
- Hold a long arc and move the electrode back to the starting position with a slow steady motion to preheat the base metal.
- Push the electrode into the joint until the arc length is about 1/16” above the root face.
- Hold the electrode in position until the keyhole forms.
- Once the keyhole forms, increase the arc length to about one electrode diameter.
- Use a steady travel to deposit the tack.
Note: It may be necessary to use a slight whipping motion to control the weld pool and keyhole size.
Extinguishing the Arc
A common technique for extinguishing the arc after depositing a tack weld with SMAW is to push the electrode through the keyhole with a quick thrust and then withdraw it when the arc is extinguished. This technique ensures that the keyhole retains the correct size. It also aids in obtaining complete penetration when restarting the root bead and when making tie-ins. A tie-in is a point where a weld bead fuses into a tack weld or into another weld bead.
Cleaning and Feathering Tack Welds
It is important that all slag is removed from tack welds and they are brushed thoroughly with a wire brush to prevent slag inclusions in the first intermediate weld bead (hot pass).
Tack welds can be feathered using a hand grinder on both sides of the tack to ensure good tie-ins. The minimum thickness of the feathered edge of a tack weld should be no less than 1/16”.
Over-grinding tacks may weaken them and cause them to break, allowing the root opening to close up.
Avoid scarring the groove faces or root face when feathering tacks. Feathering tack welds can weaken them and cause them to break under the stress of welding, especially on large diameter pipe. Therefore, it is good practice to feather only the tack at the starting position and the adjacent tack in the direction of welding.
The remaining tacks should then be feathered as welding progresses around the pipe.