42 Incomplete Fusion and Incomplete Penetration
Incomplete fusion (lack of fusion) and incomplete joint penetration (lack of penetration) are similar discontinuities. They result from incomplete melting at the interface between weld passes or in the root of the joint.
Incomplete Fusion
Incomplete fusion is a lack of union (fusion) between adjacent weld passes or base metal. It is usually elongated in the direction of welding, with either sharp or rounded edges. Incomplete fusion leads to undesirable stresses and is severely restricted in most fabrication standards and codes.
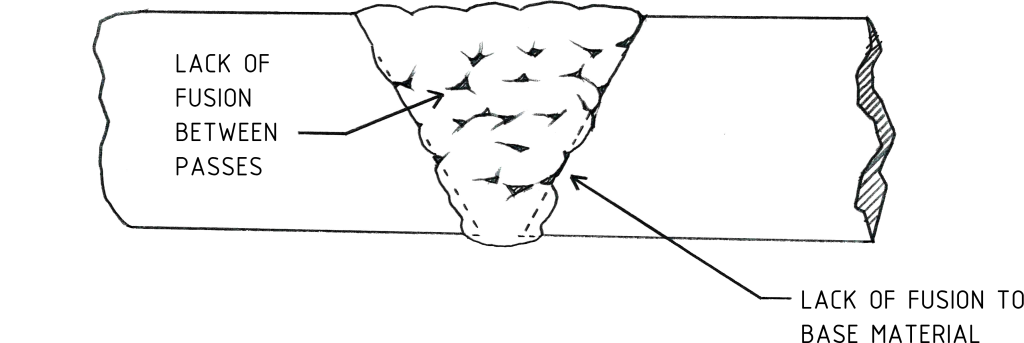
Incomplete fusion may be caused by failure to raise the temperature of the surface layers of base metal or previously deposited weld metal to the melting temperature. It may also be caused by incorrect electrode manipulation by the welder.
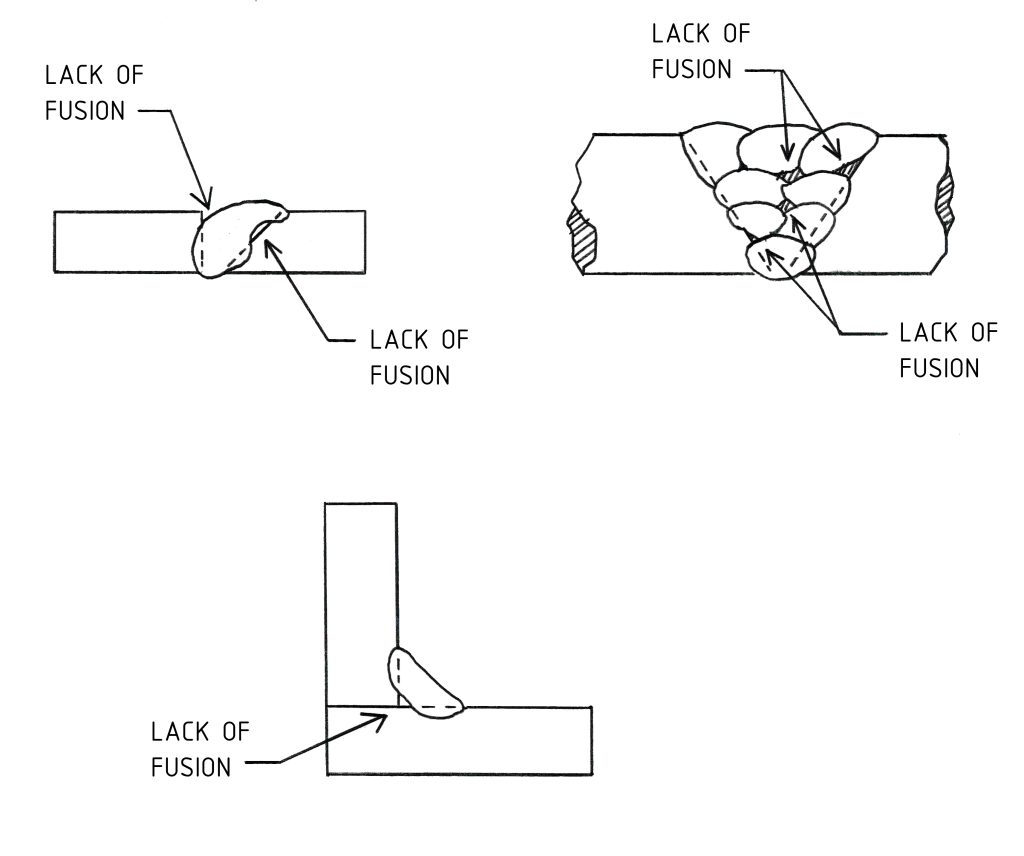
Incomplete fusion occurs more commonly with some welding processes than with others. For example, the reduced heat input in the short circuiting transfer mode of GMAW results in low penetration into the base metal. This may be desirable on thin-gauge materials and for out-of-position welding, but can also result in incomplete fusion, especially in the root area or along groove faces.
Incomplete Fusion Prevention
This may be achieved by reducing travel speed, increasing welding current, using a joint design that allows the electrode to access the joint, and using proper electrode manipulation. Incomplete fusion is also prevented by ensuring an adequate surface temperature to raise the temperature of the surface layers to the melting point, which allows the deposited metal to fuse with the surface below it.
Incomplete Penetration
Incomplete penetration is a condition in a groove weld in which weld metal does not extend through the joint thickness.
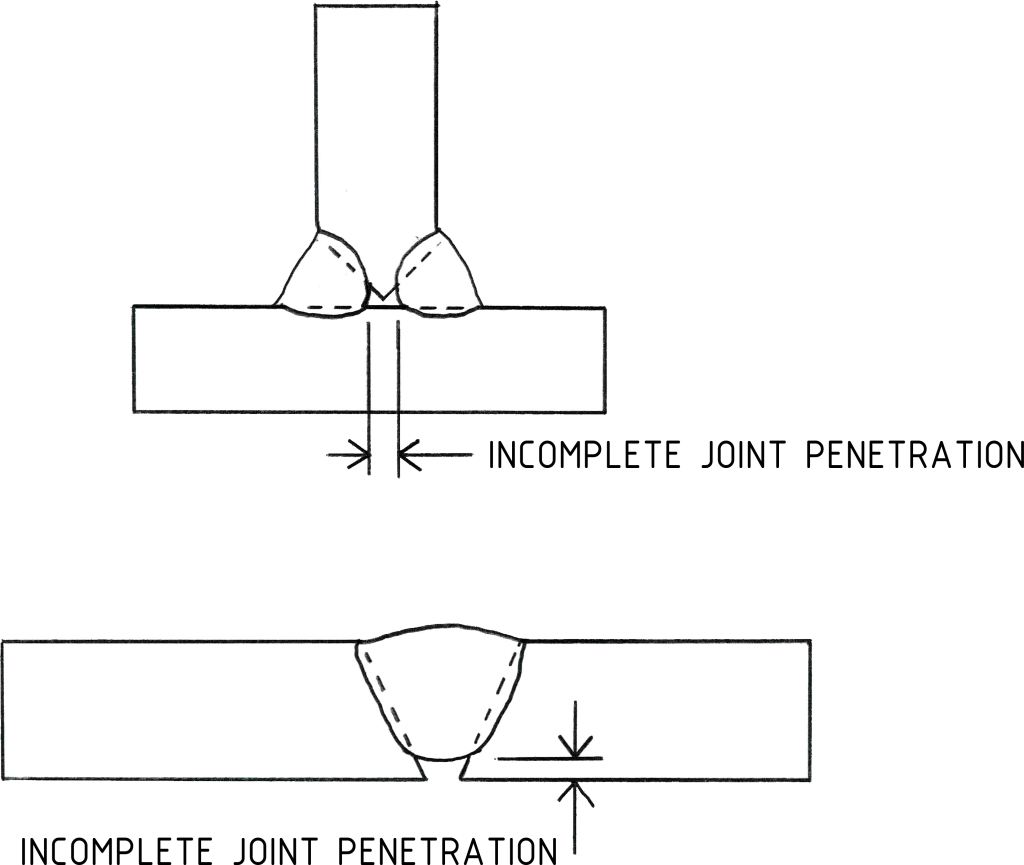
In arc welding, the arc is established between the electrode and closest part of the base metal. All other areas of the base metal receive heat principally by conduction. If the region of base metal closest to the electrode is a considerable distance from the joint root, heat conduction may be insufficient to attain adequate temperature to achieve fusion of the root.
There are a variety of other possible causes of incomplete fusion. It may occur when a groove weld is welded from one side only if the root face dimension is too great, if the root opening is too small, or if the groove angle of the V-groove is too narrow, even with an adequate root opening and a satisfactory joint design. It can also be caused by electrodes that are too large or that have a tendency to bridge; or by using abnormally high rates of travel or insufficient welding current.
Incomplete penetration is not always undesirable because some weld joints are designed to be a partial joint penetration (PJP) weld detail. The applicable fabrication standards and codes indicate permissible levels of incomplete penetration.
Incomplete Penetration Prevention
The most frequent cause of incomplete penetration is the use of an unsuitable joint design for the welding process or the conditions of the actual weld construction. Unsuitable joint designs make it difficult to reproduce qualification test results under conditions of actual production.