Chapter 1: Introduction to the Machining Industry
OVERVIEW
The Book
This book was written by authors who have worked in the machining industry and now are educators in Washington State. They provide a varied perception of the machining industry that the student can benefit from. The industries they found themselves in were dependent on their location and education.
This chapter will provide a general presentation of the machining industry and many of its differences, with the emphasis being on providing you with enough knowledge to decide if becoming a machinist is for you.
The Job
Finding a job and discovering a career can be two totally different experiences. Finding a job can feed you for a day, but finding a career can feed you for a lifetime. That may be a bit poetic, but the sentiment places value on finding a career that can sustain you through a lifetime and that can provide for today’s needs as well as those of the future.
There was a time when machining was a large industry in this country. A shift in the economy drove skilled trade jobs overseas, and machining was one of them (Adamson, 1994). Generations would pass before we would see the machining industry come back to our shores in volume.
Off-shoring created considerable problems, one of them being a shortage of well-trained and skilled machinists able to perform the technical tasks of manufacturing (Manufacturing Extension Partnership, 2022). Fortunately, there are community and technical colleges that offer training in current machining processes, which can prepare you for a career in this growing industry.
This chapter will equip you with a general understanding of the machining industry and the people who make it possible.
OBJECTIVES
- Describe what machinists do.
- Identify potential industry jobs for machinists in your location.
- Review the specific skills listed in a machinist job description.
KEY TERMS
- Stock
- Industry Sector
- Subtractive machining
- Additive manufacturing
1.1 What is Machining?
Machining is a sector of the manufacturing industry that concerns itself with using machines to convert stock materials such as steel and aluminum into finished products. A sector is a portion of an industry that allows for the ability to segregate information. The aviation sector has different machining demands than the agricultural sector. More on this later in the book.
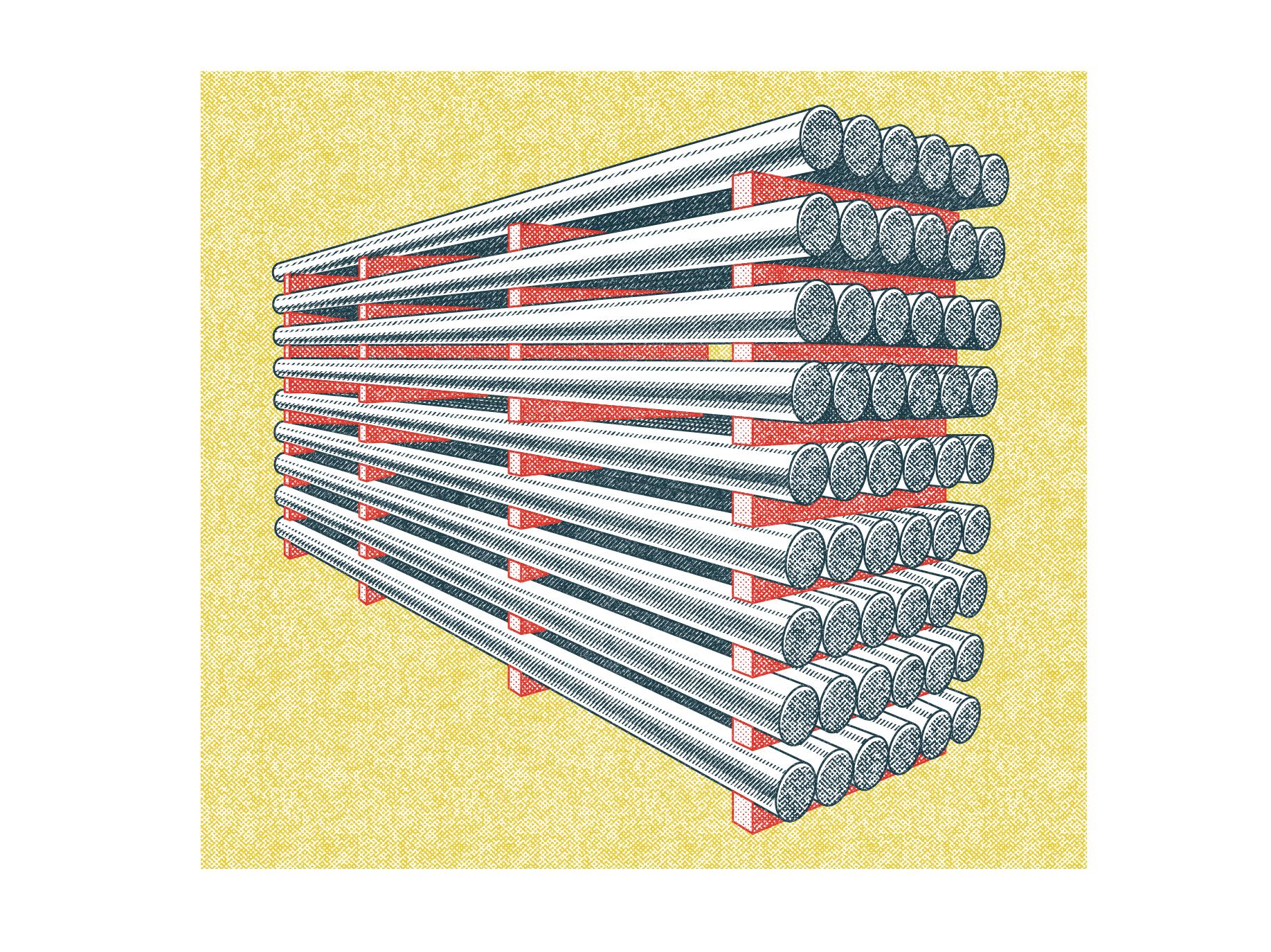
Stock is the term used by machinists when referencing the beginning material size and composition before work has begun to form it into the finished product. Stock can be in bars, billets, castings, extrusions, forgings, or any form that can be held securely while machined.
Bars can be round or rectangle in shape, with lengths of ten feet up to twenty feet. Bar stock requires cutting to predetermined sizes before the machining process can begin. The saw used to cut stock can be a CNC programmed saw, a band saw, or a chop saw.
A billet is a large piece of stock that does not need to be cut down before machining. Billet material usually arrives pre-cut on pallets, and the machinist transfers the stock from the pallet to the machine for processing.
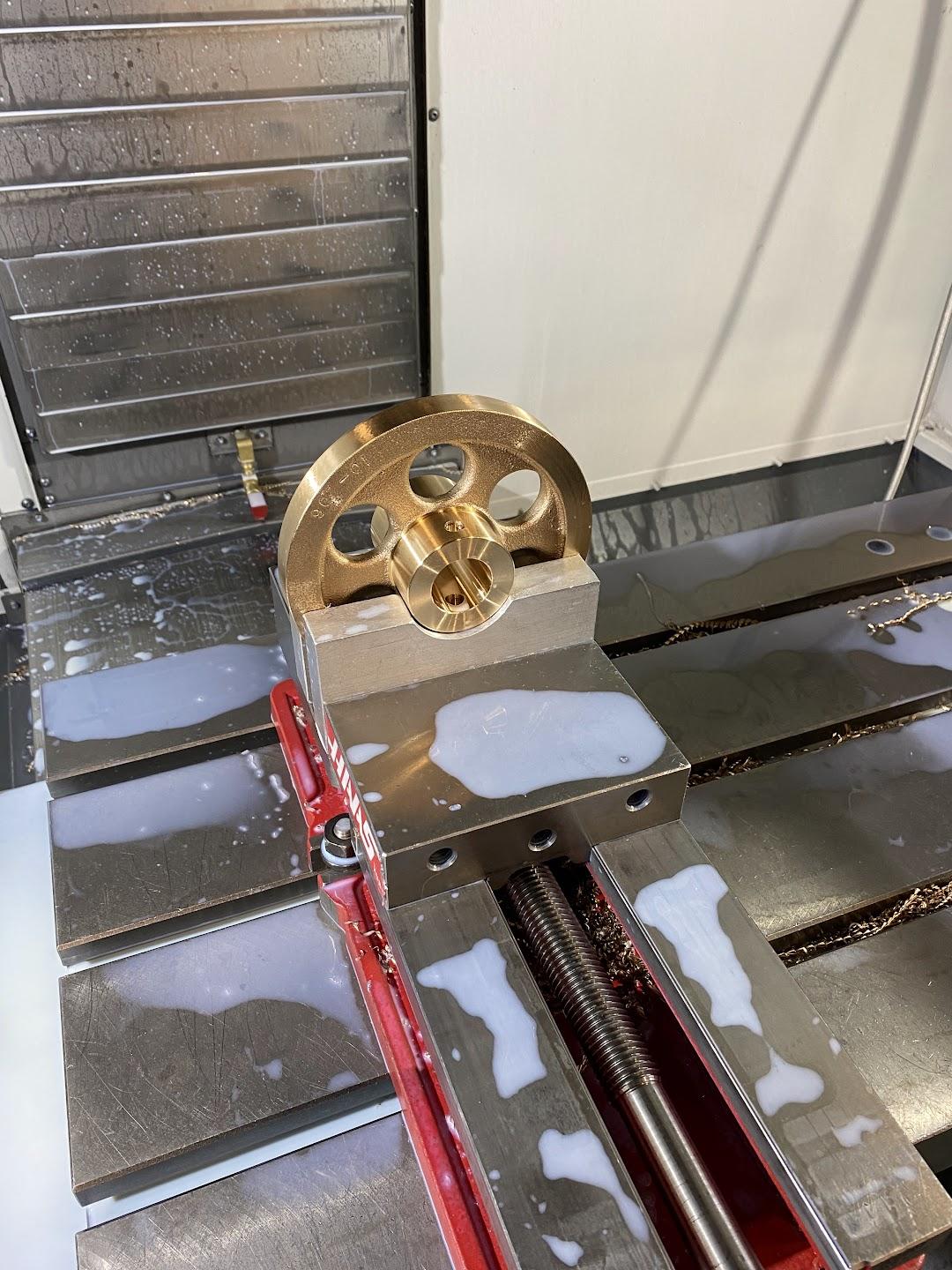
Castings are created by pouring molten metal into a form and letting it cool and solidify into a solid. They are often cast iron, aluminum and steel.
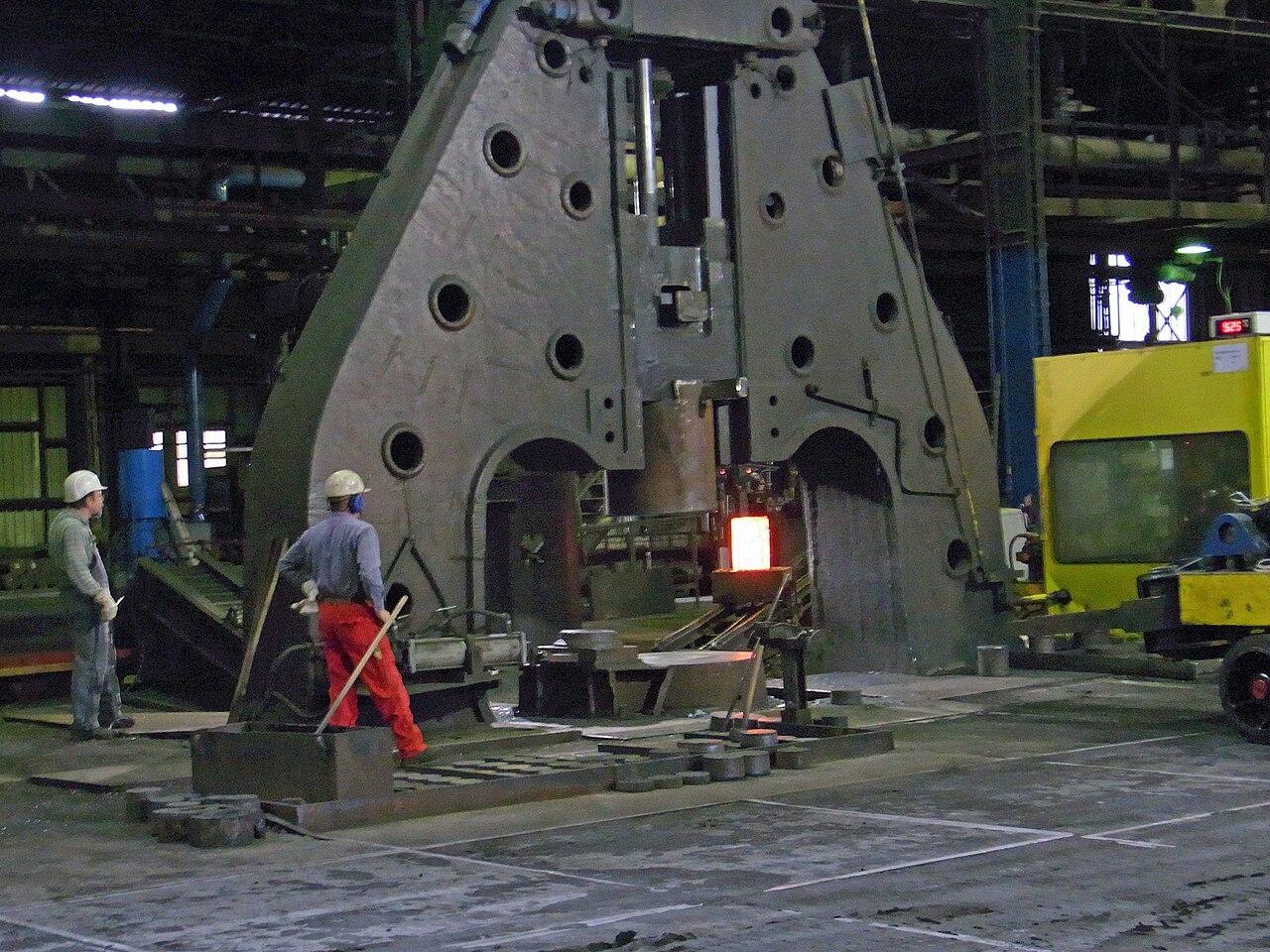
Forgings are parts which have been formed by extreme pressure sandwiching a hot piece of metal between two tool steel dies, giving it a specific shape, such as a mechanics wrench.
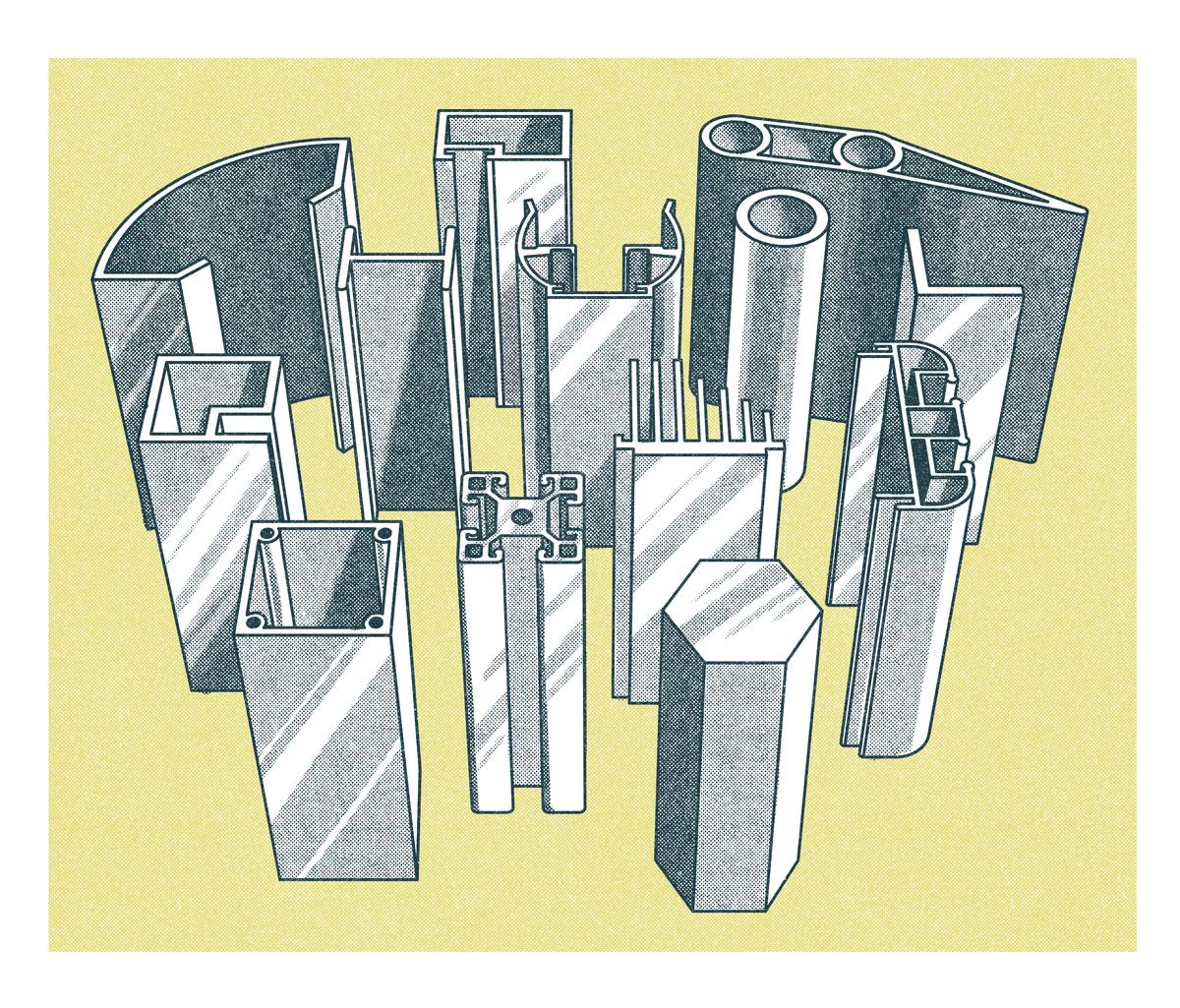
Extrusions are usually made of aluminum which has been heated and forced through a die, giving the stock its finished shape.
There are two basic types of machines used in the machining industry, and they are the mill and the lathe. In general, the lathe machines (or turns) round objects, and a mill machines objects that are not round but rather rectangular in shape.
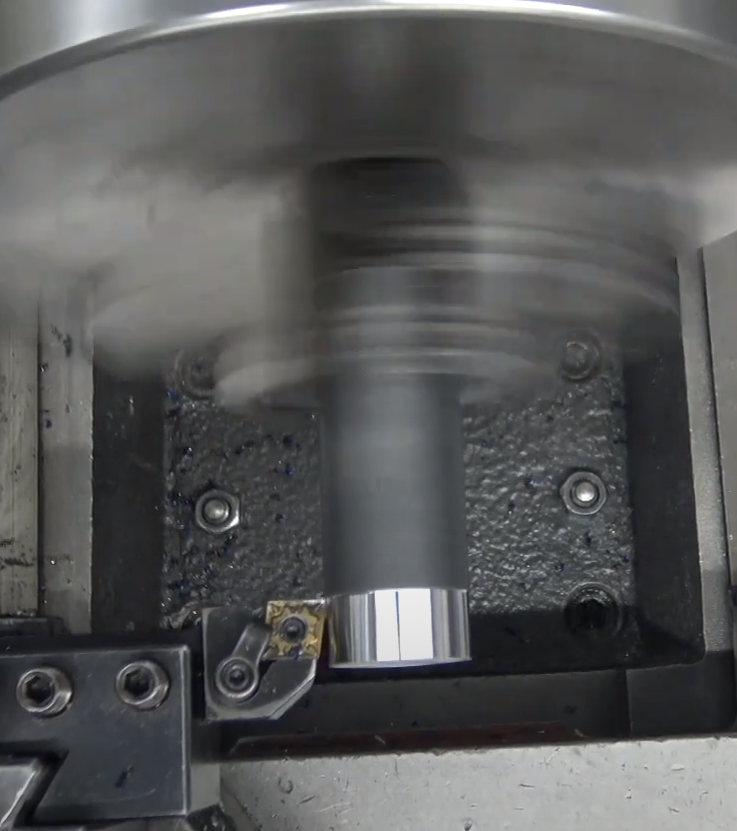
A milling machine holds the stock in a workholding device such as a vise. The tool rotates and removes material from the stock. The table where the vise is bolted moves, which permits the cutter to progress through a cut. All of these topics will be discussed in detail in further chapters.
On a lathe, the stock is held in a rotating vise called a chuck, and the tool is moved, which results in material removal.
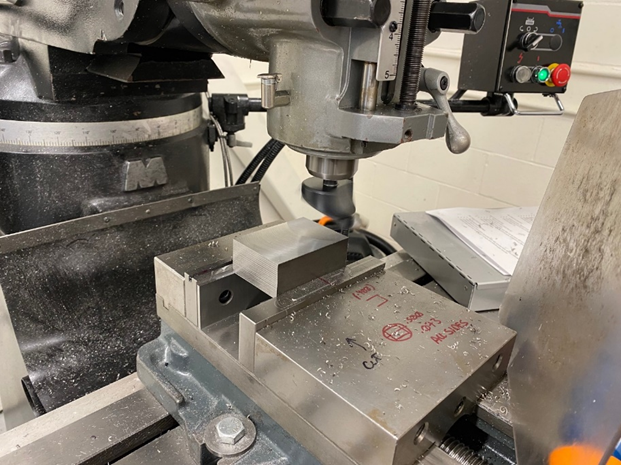
As a student in a machining program, you will become familiar with using both pieces of equipment to produce finished parts.
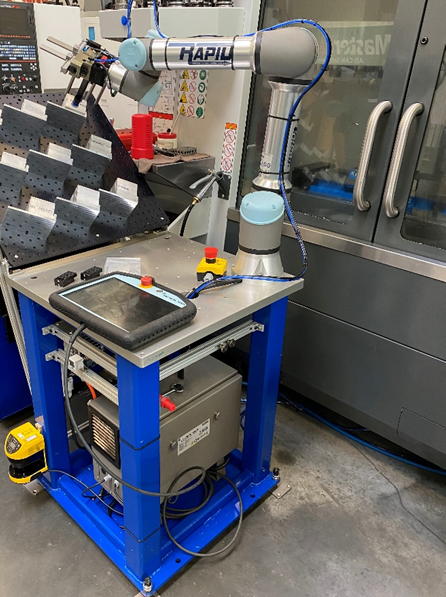
Advancements in technology have influenced the machining industry in the same manner as all other industries. Where the time-honored process of “subtractive” machining would start with a piece of stock material large enough to encompass the finished part and remove material until the finished part was all that’s left. Today we also have “additive” manufacturing , where parts can be created by fusing powders in special machines one layer at a time until the finished part is created. We call this “additive” manufacturing process printing, and the advancements in 3D printing technologies are still in their infancy with a promising future in manufacturing.
1.2 What Do We Call Ourselves?
You would think a person who operates a machine all day would be called a “machiner,” but that is not the case. The skilled workers who operate the lathes, mills, and printers of today are called Machinists. There are distinct levels of skill and qualifications among machinists because the machining industry is so vast.
There are companies that specialize in the use of manual machines, and there are those that use only Computer Numerical Control (CNC) machines. As you may expect, these companies require different skill sets to perform the duties of a machinist.
As a rule, there are three levels of machinists:
Level I is the entry level and operates under the direct supervision of another operator and shop lead. This is where you can expect to start in your first machining job. Being new to the industry requires time for you to understand how your specific company does things. All shops are different, and they all have a learning curve that you will have to negotiate.
Level II is the first level supervisor who operates under the direct supervision of the shop lead to complete assigned work and train level I personnel. Over time, you will advance to this level as you complete more difficult tasks and understand how your company does things.
Level III operates under the general supervision of the shop lead but performs tasks as they deem necessary and does not need direct supervision while performing tasks. If you want to ascend to the position where you can solve problems on your own and help improve the processes in your shop, this is where you want to be. If you work hard, learn all you can, and take on new challenges, you may reach this goal in about 3-5 years.
1.3 What Do Machinists Do?
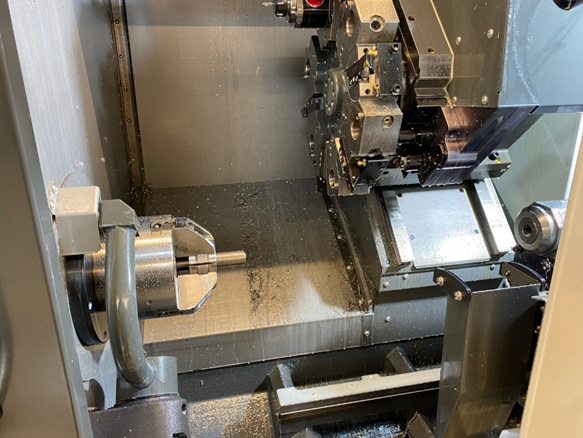
Common machinist duties found in job postings today, such as these on the Career One Stop site, include:
- Fabricates, maintains, repairs, and/or alters metal parts and metal objects using a variety of hand tools, metalworking machines, arc or gas welding equipment and following instructions, specifications, technical manuals, etc.
- Sets up and operates metalworking machines such as lathes and milling machines to machine parts to established specifications.
- Compares finished work to specifications using measuring instruments such as scales, calipers, and micrometers.
- Review plans, specifications, diagrams, etc. to determine the dimensions and tolerances of metal components to be machined and to determine the tools, materials, and equipment required to complete assigned projects.
- Measures, marks, and scribes metal stock following blueprints, diagrams, and/or specifications and using square rule and scribe to prepare metal for machining operations.
- Performs related duties such as cleaning work areas, tools, and equipment; maintaining records and logs; and drawing sketches of metal parts or metal components to be machined.
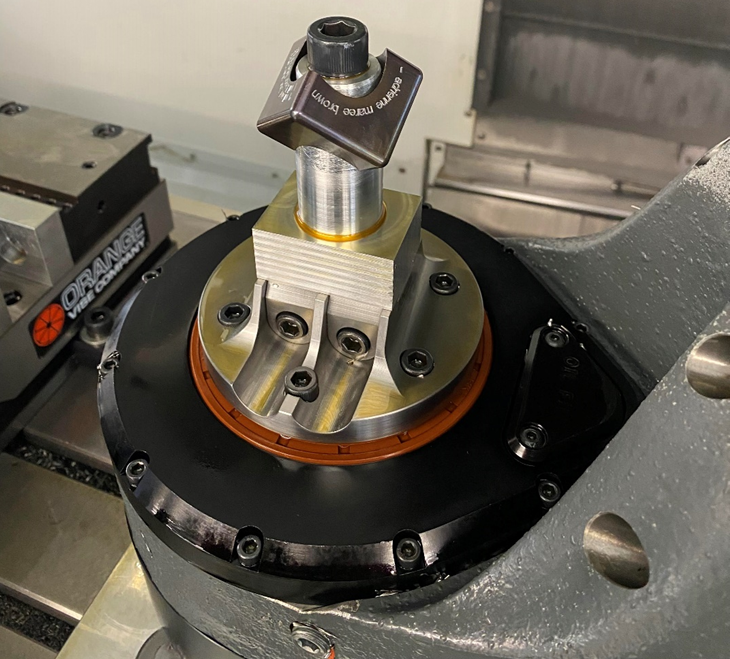
1.4 What Qualifications Does a Machinist Need?
The following list was compiled from machining industry job postings. Not all apply to all positions, but they are all included to provide an understanding of the knowledge, skills, and abilities (KSAs) employers are looking for.
Some of the qualifications commonly expected by employers include:
- Knowledge of the principles and techniques of machine shop practice.
- Knowledge of the fundamentals of metalworking.
- Knowledge of the methods used in shaping metal to precise dimensions.
- Knowledge of safety practices and procedures followed in machine shop practice.
- Knowledge of the terminology, coding, symbols, and standard abbreviations used in machine shop practice.
- Knowledge of the characteristics and properties of a wide variety of metals and alloys.
- Knowledge of the types and uses of tools, equipment and materials used in machine shop practice.
- Knowledge of the types and uses of precision measuring equipment and devices such as micrometers, calipers, rulers, etc.
- Knowledge of the methods followed in the lubrication of machine shop machinery and equipment.
- Knowledge of the types and uses of small hand tools such as reamers, drills, sanders, taps, dies, etc.
- Knowledge of the types and uses of hand-held power tools such as drills, electric hand saws, etc.
- Skill in using machine shop equipment such as lathes, milling machines, drill presses, bench sanders, etc.
- Skill in the use of precision measuring equipment and devices such as micrometers, calipers, rulers, etc.
- Skill in using small hand tools such as reamers, drills, sanders, taps, dies, etc.
- Skill in using small hand-held power tools such as drills, electric hand saws, etc.
- Ability to understand and apply the policies, procedures, specifications, standards, and guidelines governing assigned unit activities.
- Ability to read and interpret documents such as plans, specifications, standards, and guidelines governing assigned unit activities.
- Ability to make arithmetical computations with speed and accuracy (addition, subtraction, multiplication, and division).
- Ability to maintain accurate records.
- Ability to follow oral and written instructions.
- Ability to lift and carry heavy objects, usually around fifty pounds.
- Ability to work well with others.
- Ability to stand for long periods of time.
- Ability to work independently.
- Ability to exercise sound judgment.
- Ability to adjust to changing situations to meet emergencies or changing production requirements.
- Manual dexterity.
- Mechanical aptitude.
Many of these qualifications will be gained from training at a technical or community college. Many of the skills an employer is seeking are related to individual traits. An example of desirable traits include: being punctual, thorough, respectful, courteous, willing to communicate, having a desire to learn, and having the ability to listen to directions.
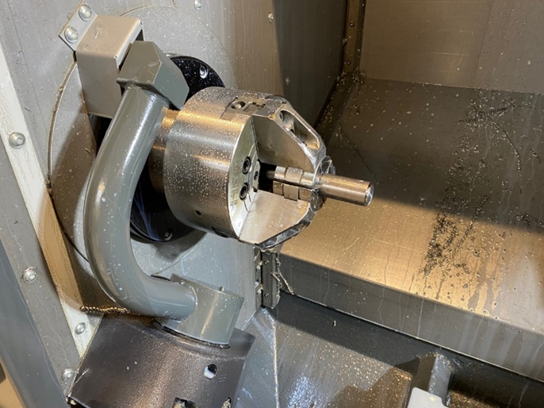
Your personal traits, willingness, and desire to perform these tasks cannot be overstated. Many new machinists come into a machining program only to find out they do not enjoy detail-oriented work, which requires accurate measuring, recording of precise tolerances, and straining over details to make quality parts.
If you enjoy details, are satisfied by creating varied and intricate parts, and are willing to abide by well-defined processes that ensure accuracy and repeatability, then this just may be the job for you.
Meticulous people often find themselves in the machining industry because they feel satisfaction from creating intricate, accurate, and complex parts to precise standards. These people are often willing to fixate on the details, desire to know all the facts about a process, and are willing to learn the factors that contribute to accurate parts.
Mechanics who love to rebuild motors and transmissions and build unique cars and trucks also often find themselves working in a machine shop.
Designers who want to have complete control over the manufacturing process from concept through manufacture find a home in the machining industry because they can dream of a part, model a part in CAD software, and then use their skills to manufacture that part.
1.5 How Much Training Do Machinists Need?
We established earlier that you can find quality and accredited training at community and technical colleges. These types of colleges specialize in two-year degree programs referred to as associate degrees (AS degrees). Associate degrees require around ninety credits of schooling, with classes ranging from two to five credits requiring a C or above to pass (as of this writing). It is common to spread this schooling over six quarters, in which the summer quarter is an OFF quarter when program classes are not offered.
Technical and community colleges have the added benefit of delivering programs that are in demand in the surrounding area. The colleges do this by partnering with local industry and having them consult on knowledge, skills and abilities that they would like future employees to have when applying for a position.
It is widespread practice for these two-year training programs to offer certificates in the trade. Certificates are for those who are not able to attend the full two-year program but have learned the basic skills that will allow entrance to the job market. There is continuing progress being made in the certificate programs, which allow for better alignment with local industry needs.
If you are reading this book as part of a machining program, you have already found an educational resource that will put you on the path toward a career. If you are not enrolled in a training program, research the local community and technical colleges in your area and find those programs in demand, such as machining.
For more occupational and job outlook information about machinists and related jobs, see the “Machinists and Tool and Die Makers” entry in the Occupational Outlook Handbook site.
1.6 Do Machinists Do Math?
This is a common question from students. There seems to be a general reluctance to perform basic math (Aguilar, 2021). It could be due to a negative experience in high school when math classes really had no logical purpose other than to perform orders of operations on equations. Many in the trades are visual learners, which means they rely heavily on what they see or can simulate in some graphical manner within their brains. Math can be a challenge for these types of learners, but it is not a good reason to resist the use of math skills. Re-learning basic math skills during your training is a great opportunity as you solve real-world problems.
This is a two-part question; do I have to take math during my training? And do machinists have to do complicated math in the industry? The answer is Yes, and No. Yes, you will need to take a math class during your training at a community college or technical college. These math classes are usually “math for the trades” or something similar where you perform functions like measuring the area of a piece of sheet metal or calculating the volume of a cylinder so you can build a tank that holds enough fluid. Addition, subtraction, multiplication, and division are the principle skills necessary for an entry level machinist.
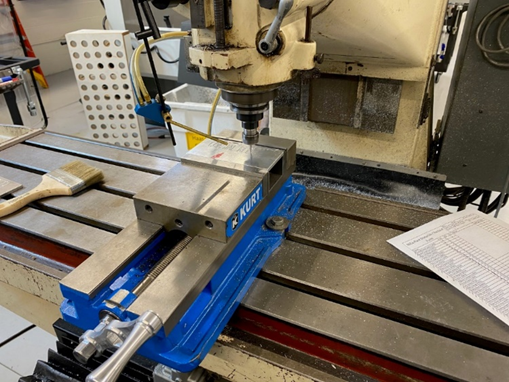
Machinists perform math to determine whether their parts are within tolerance and to determine how much to compensate a tool to achieve the desired dimension. All the examples above require the ability to add, subtract, multiply, and divide. If you need to calculate how much further to compensate an 82° spot drill to achieve the desired diameter chamfer, you can use a trigonometric calculator.
It is this author’s opinion that you use the tools at hand. Gone are the days of slide rules and trigonometry tables. The calculator on your phone, a website, or, better yet, a simple free app to download on your phone can provide all the math assistance you need until you are comfortable performing these basic functions yourself.
1.7 Where do you Find Machinists?
Most machinists work at businesses referred to as “Machine Shops.” It is common for machine shops to specialize and be known for that specialty. For example, aerospace shops have the extra certifications necessary to manufacture parts that will ultimately find themselves on aircraft or maybe spacecraft, which will leave Earth’s gravity. Some shops specialize in structural parts used in buildings; another shop may manufacture expensive custom furniture or fixtures. All these shops are considered machine shops. This is some great news! Machine shops can be anywhere. You can find them in cities or out in the county.
The primary needs of a building to house a machine shop are the necessary power requirements to run the equipment, a large enough structure to house all the equipment, a concrete floor that can support heavy equipment or be modified to support equipment, and the ability for a truck to receive the materials from which you will make parts.
Once the parts are made, they are shipped out to the customer using varying conveyances, such as UPS, FEDEX, freight shipping companies, or a delivery van if the customer is close.
1.8 What Industries Do Machinists Support?
This is the exciting part! Depending on the certifications of your shop and the type of equipment it uses, such as multi axis lathes and mills, Swiss lathes, horizontal mills, precision grinding, Electrical Discharge Machining (EDM), as well as the inspection equipment selection and the engineering know-how of the staff, you can be making parts that will go into space.
The requirements a shop must follow are very important to be able to machine for the Aerospace industry. When manufacturing for the Aerospace industry, the shop must have an AS 9001/ISO 9001 certification, which provides a means to track the material used from mill to customer, manage inspection equipment, document employee training, and have inspection plans to control all the variables of the manufacturing process.
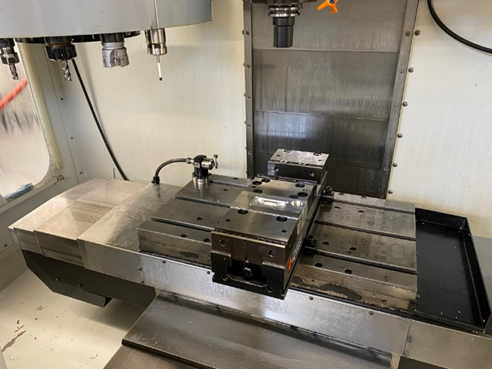
Other industries machinists supply parts to are: robotics, transportation, medical, demolition, performance race car parts, computers, structural buildings, hydroelectric, climbing equipment, bicycles, motorcycles, prosthetics, and many more.
SUMMARY
A career in machining can be challenging and rewarding. There are paths for advancement within a machine shop as you gain knowledge and experience performing ever more challenging tasks. If you find you do not like the area or workload of your current shop, your skills are still marketable across differing shop types.
I hope this chapter and this book will aid you in deciding whether a career in machining is for you. Machining and the manufacturing industry is a growing job market with exciting opportunities for those who are looking for a demanding career.
REVIEW QUESTIONS
The intent of these review questions is for you to spend some time to help determine whether becoming a machinist is a good fit for you. There are plenty of trades available to you, and narrowing down the possibilities can help ensure you find the best “fit” for your abilities and desires.
- What industries do machinists operate in?
- Of the industries that machinists support, which draws your interest, and why?
- What is a contributing factor to the current lack of qualified machinists available to support industry?
- What aspects of machining do not interest you?
- Which aspects of the machining industry interest you?
- How does the subject of math affect your decision to become a machinist?
- Where would you like to work? Can you find any machine shops in that area?
References
Adamson, D. M. (1994). The decline of the U.S. machine-tool industry and prospects for recovery [Research brief]. RAND. https://doi.org/10.7249/RB1500
Aguilar, J. J. (2021). High school students’ reasons for disliking mathematics: The intersection between teacher’s role and student’s emotions, belief and self-efficacy. International Electronic Journal of Mathematics Education, 16(3), em0658, 1-11. https://doi.org/10.29333/iejme/11294 CC BY.
Manufacturing Extension Partnership. (2022, October 27). Training: Responding to the skills gap. National Institute of Standards and Technology, U.S. Department of Commerce. Retrieved May 7, 2024, from https://www.nist.gov/mep/manufacturing-infographics/training-responding-skills-gap