Chapter 11: Surface Grinders
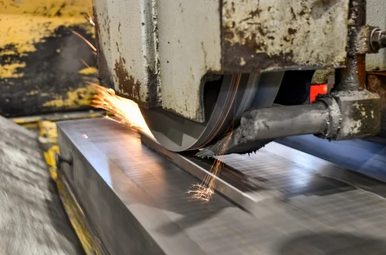
Overview
Did you know that surfaces such as bearings and shafts that operate in planes, trains, and automobiles must fit precisely together in order to function properly and efficiently? What makes this possible is the process of grinding.
The growth of industries such as automotive, aerospace, machinery, electronics, and construction drives the demand for grinding machines. These industries rely on grinding processes for precision machining, surface finishing, and material removal operations, creating a continuous demand for grinding machines to support manufacturing activities. (Global Market Insights, 2024, para. 1)
Grinders are typically operated by trained professionals who use them to create high-precision components for a wide range of applications. Another unique aspect of grinding is that when two parts are perfectly flat and placed together, they create a vacuum between them. When the parts are small, the vacuum will keep the two parts together as if they were magnetized. This characteristic is used to keep gauge blocks together when taking measurements. Precision grinding is typically the final operation for parts that are hardened and often can’t be finished with traditional tools.
OBJECTIVES
- Explain proper safety procedures when using a precision grinder.
- Explain the functions of various components of the surface grinder.
- Correlate grinding wheels to the operations being performed.
- Predict work holding for surface grinding.
- Associate wheel grit size to finish, and material removal.
- Describe the process of dressing a grinding wheel
KEY TERMS
- Grinding
- Blanchard
- Ingoing nip
- Outgoing nip
- OD (outside diameter)
- ID (inside diameter)
- Shape
- Abrasive
- Grit
- Grade
- PPE (personal protective equipment)
- ring test
- dressing
- glazing
- burning
- scratches
- waviness
11.1 Common Surface Grinders
In machining, a grinder is a machine tool that removes material from a workpiece through the use of an abrasive grinding wheel. Grinders are used to achieve high precision, surface finish, and the overall shape of a workpiece that cannot be achieved through other machining processes like turning, milling, or drilling.
There are different types of grinders used in machining, each designed for a specific purpose. The main three types are Horizontal, Vertical, and Cylindrical grinders.
11.1.1 Horizontal
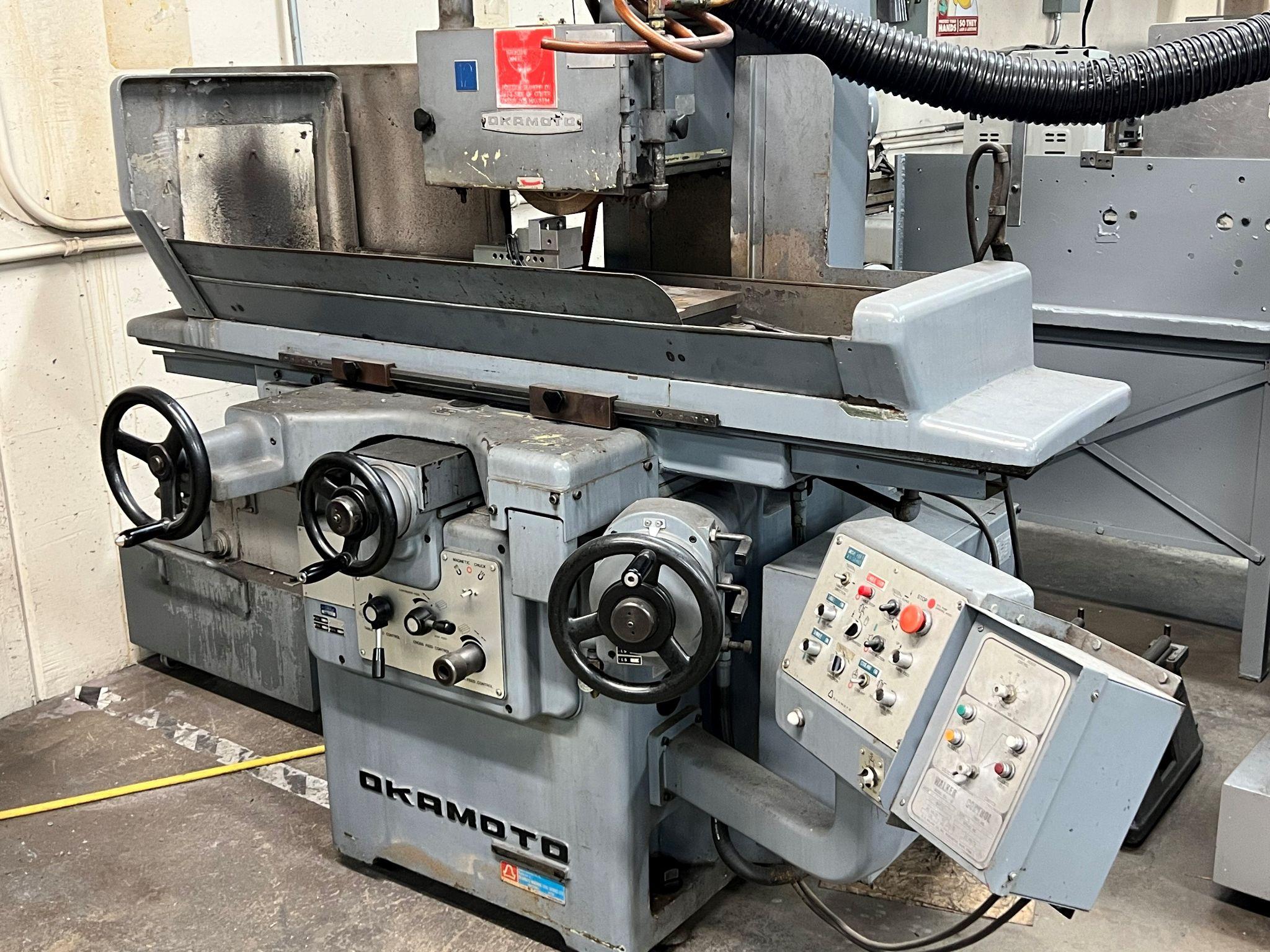
Horizontal spindle surface grinders typically use the outside diameter of the solid wheel to grind the part surface, as seen in the picture at the start of the chapter.
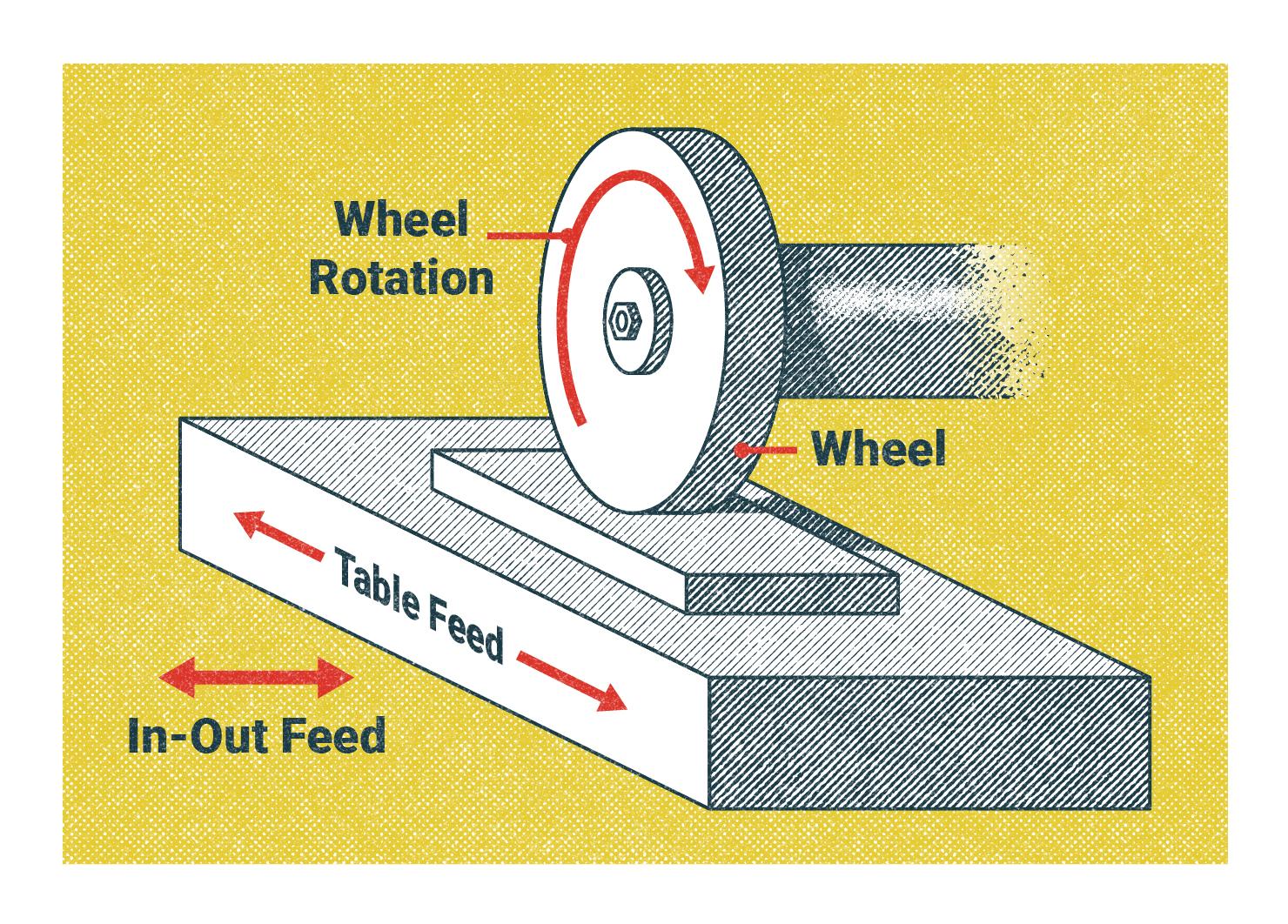
The most common type of grinding machine is the horizontal spindle with a reciprocating table. The “head” of the machine holds the grinding wheel while it spins. It is moved up and down in a direction perpendicular to the table. This is also referred to as the Z axis. The hand wheel of the head controls the movement in the Z axis. The amount of movement per gradation, or line on the dial, is typically .0001. This is called a “tenth” by a machinist.
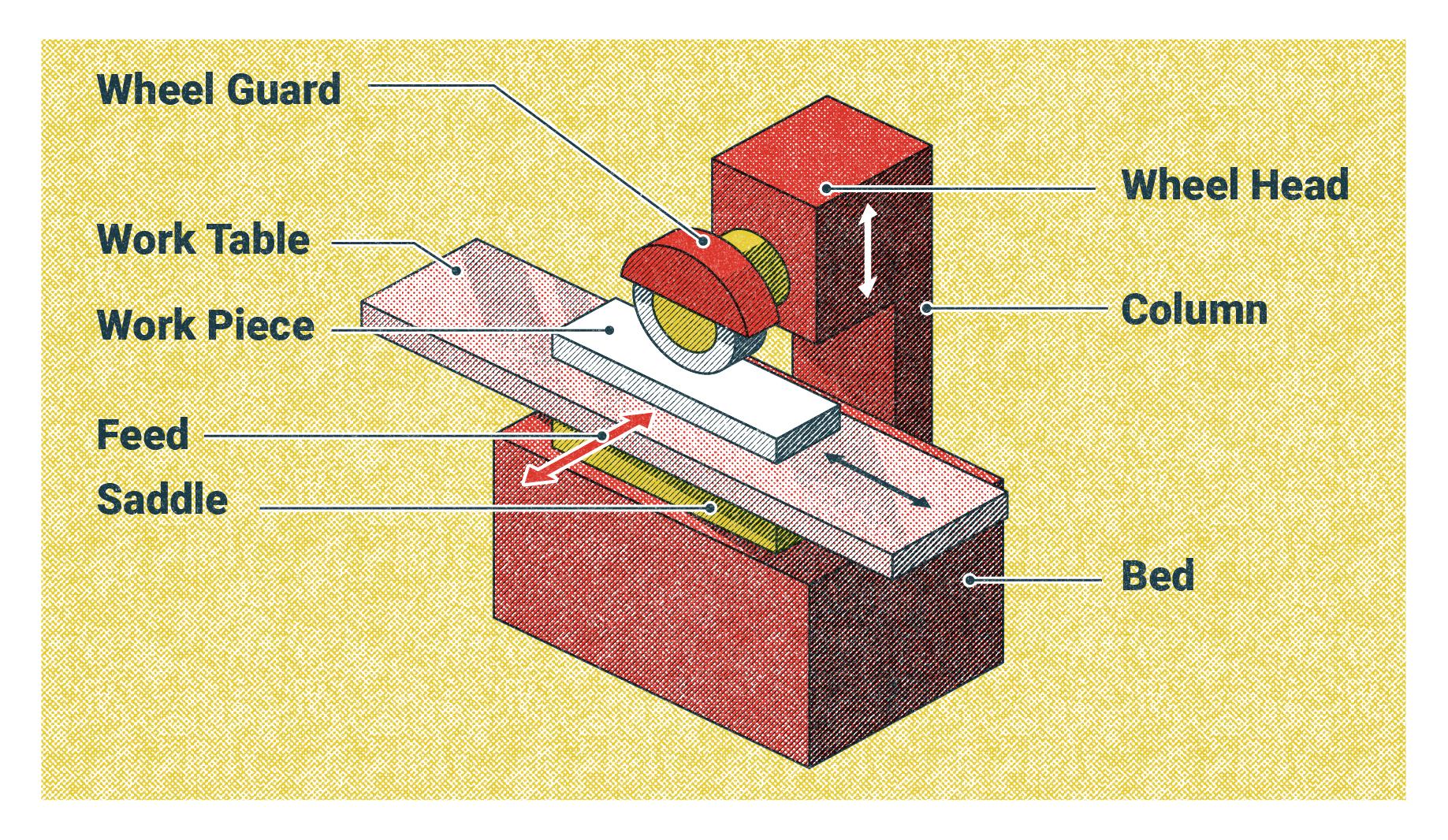
Visualizing the axis in the image above on the horizontal grinder as you face the machine. The X positive is to the right, Y positive is up away from the part, and the Z positive movement is towards the machinist. The X is Workspeed, the Y is In-feed, and the Z is the Crossfeed.
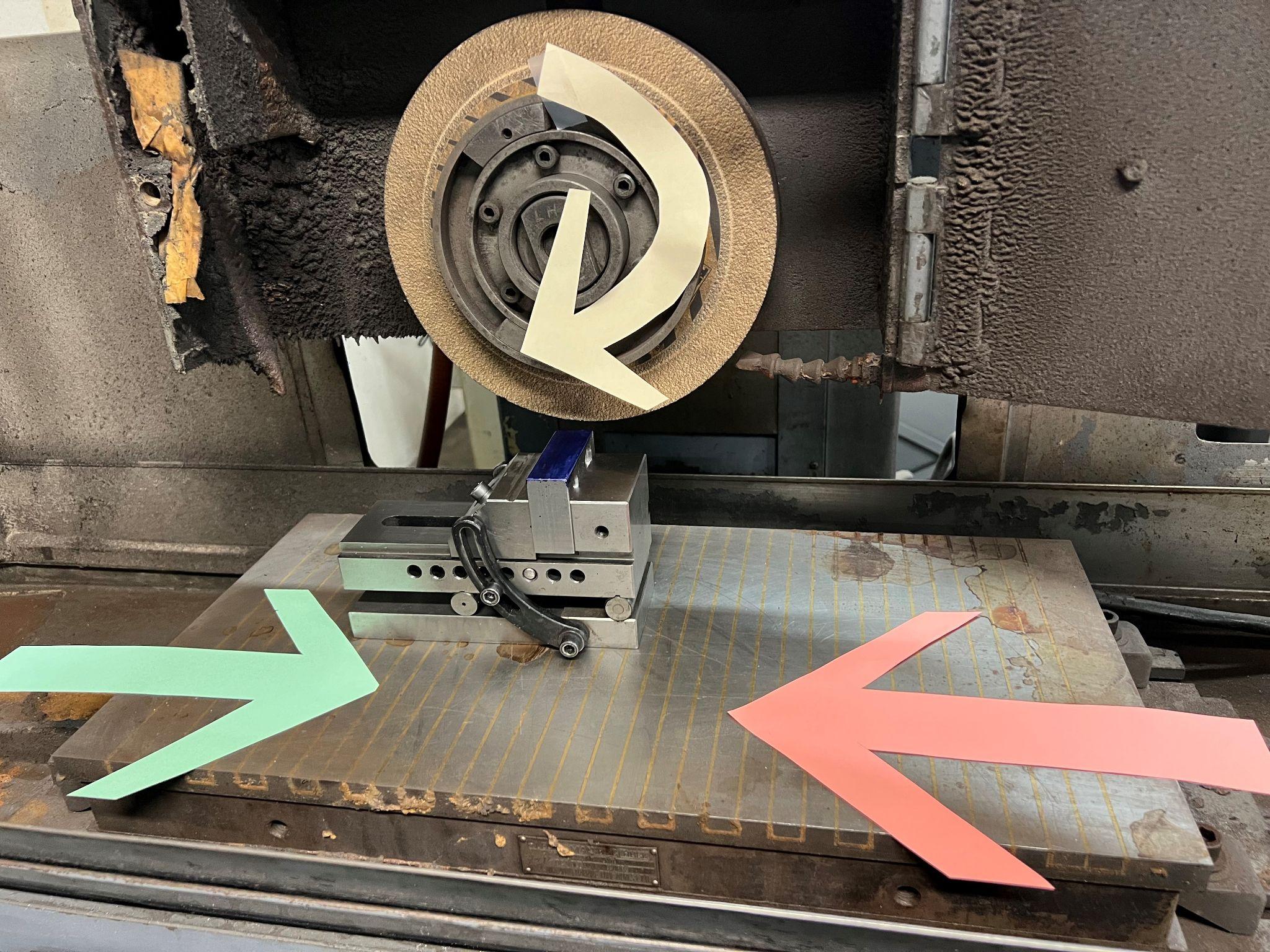
The part will travel back and forth along the long dimension of the table, the X axis, and the short dimension of the table, the Y axis. The X axis is the “work speed” direction, and the Y axis is the “cross feed” direction. The wheel will spin in a clockwise rotation. The right side of the wheel is the ingoing nip that will pull the part in. The left side of the wheel is the outgoing nip that pushes the part away. Consider that passing a part under the grinding wheel from right to left would be similar to making a climb cut on a manual mill. Similarly, moving from left to right is a conventional cut on a manual mill.
CRITICAL SAFETY NOTE:
Never walk or stand on the left side of the grinder when the grinder is being used. The left side of the surface grinder is where parts are ejected if they come loose.
11.1.2 Vertical
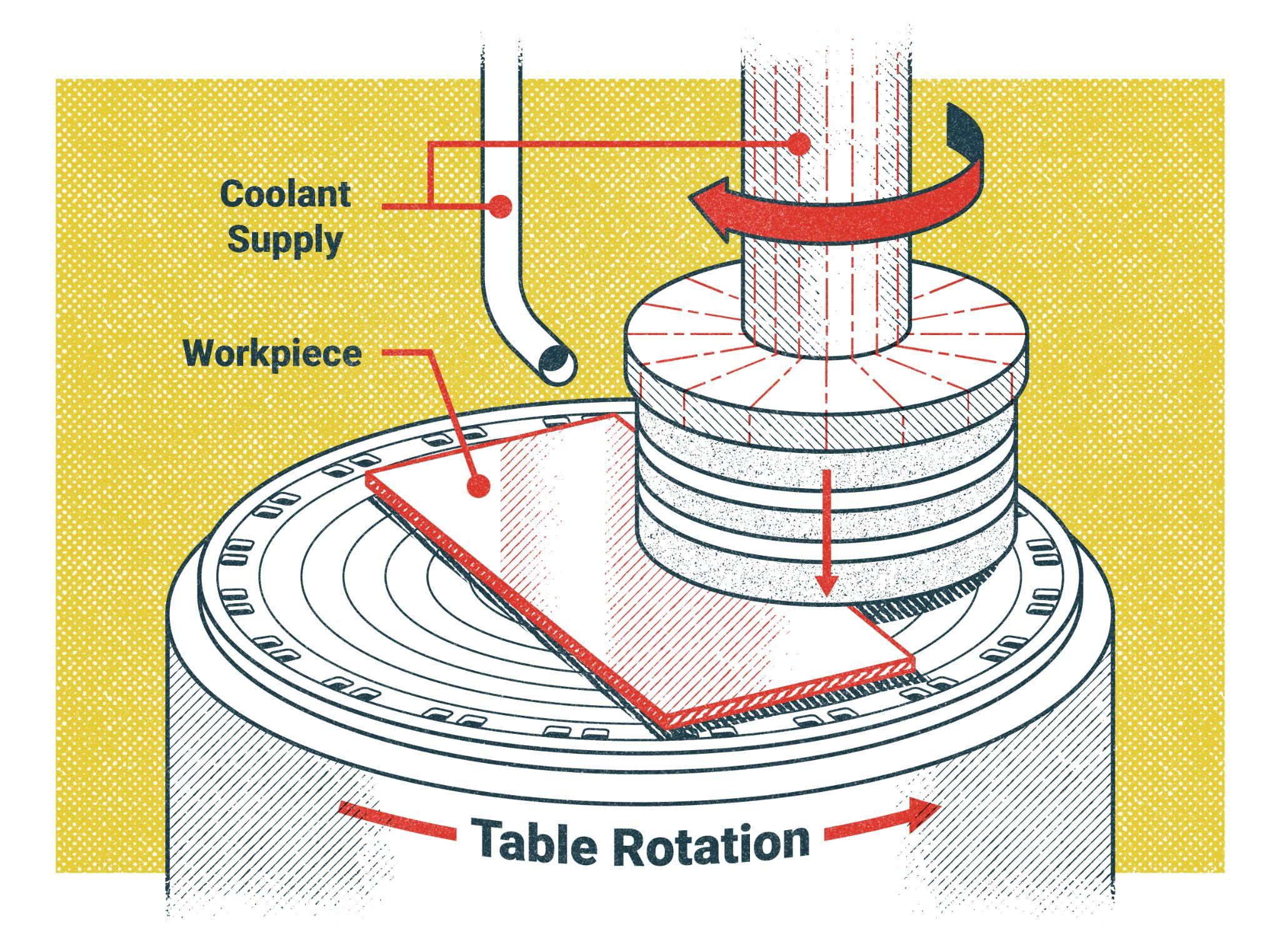
Pictured above is a vertical grinder performing a blanchard operation where the part can rotate independently from the grinder. Machines with reciprocating tables move the work back and forth beneath the wheel. The grinding is done on the side of the wheel. This is also referred to as Blanchard grinding.
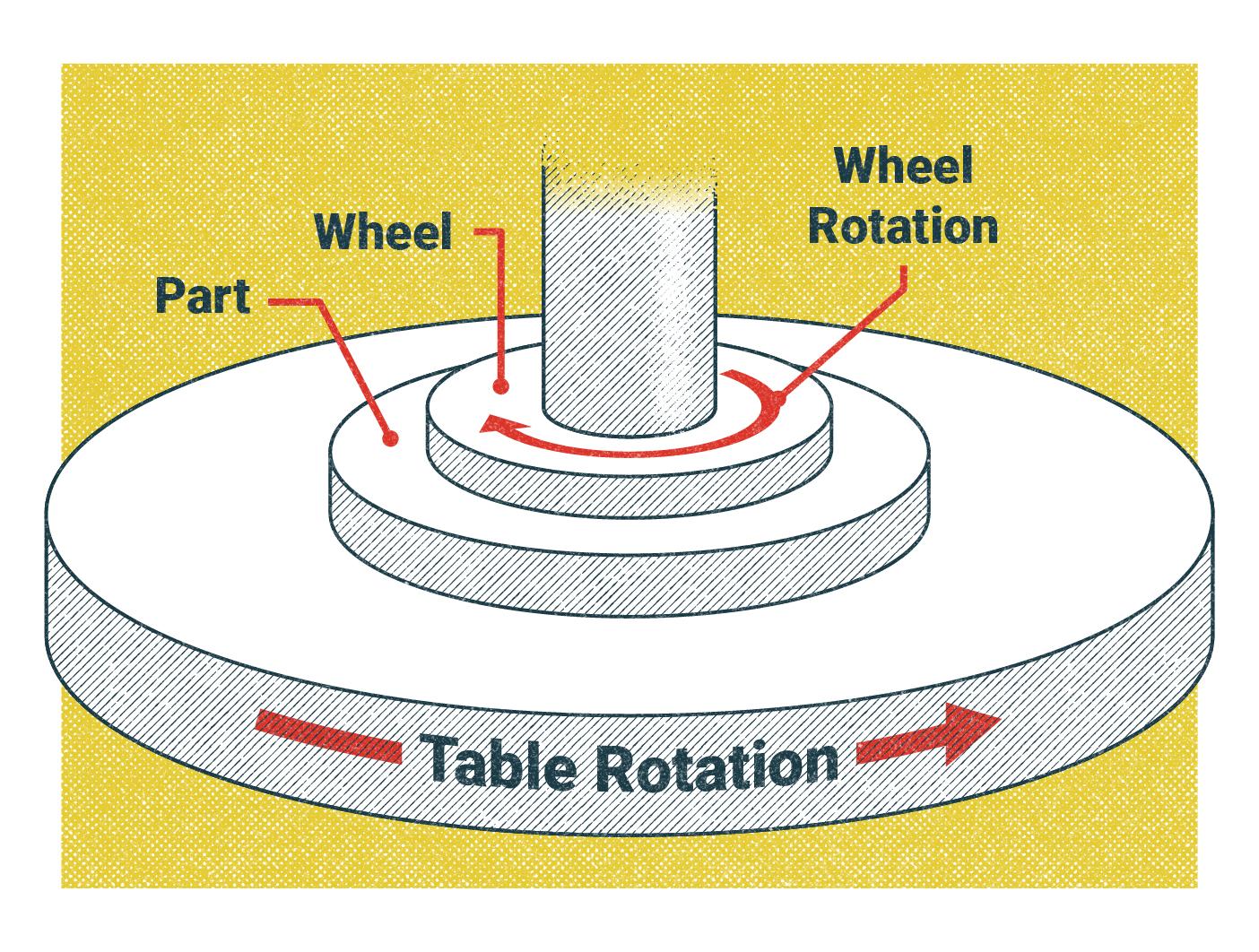
Vertical spindle grinders typically use the side of the grinding wheel to grind the workpiece. The wheel may be solid or cup-shaped. The tables will either be reciprocating or rotary in motion, just like the horizontal grinder. Vertical surface grinders are also referred to as Blanchard grinders. These grinders are mainly used for large, flat plates. In the automotive industry, large flywheels will be blanchard ground for proper clutch assembly.
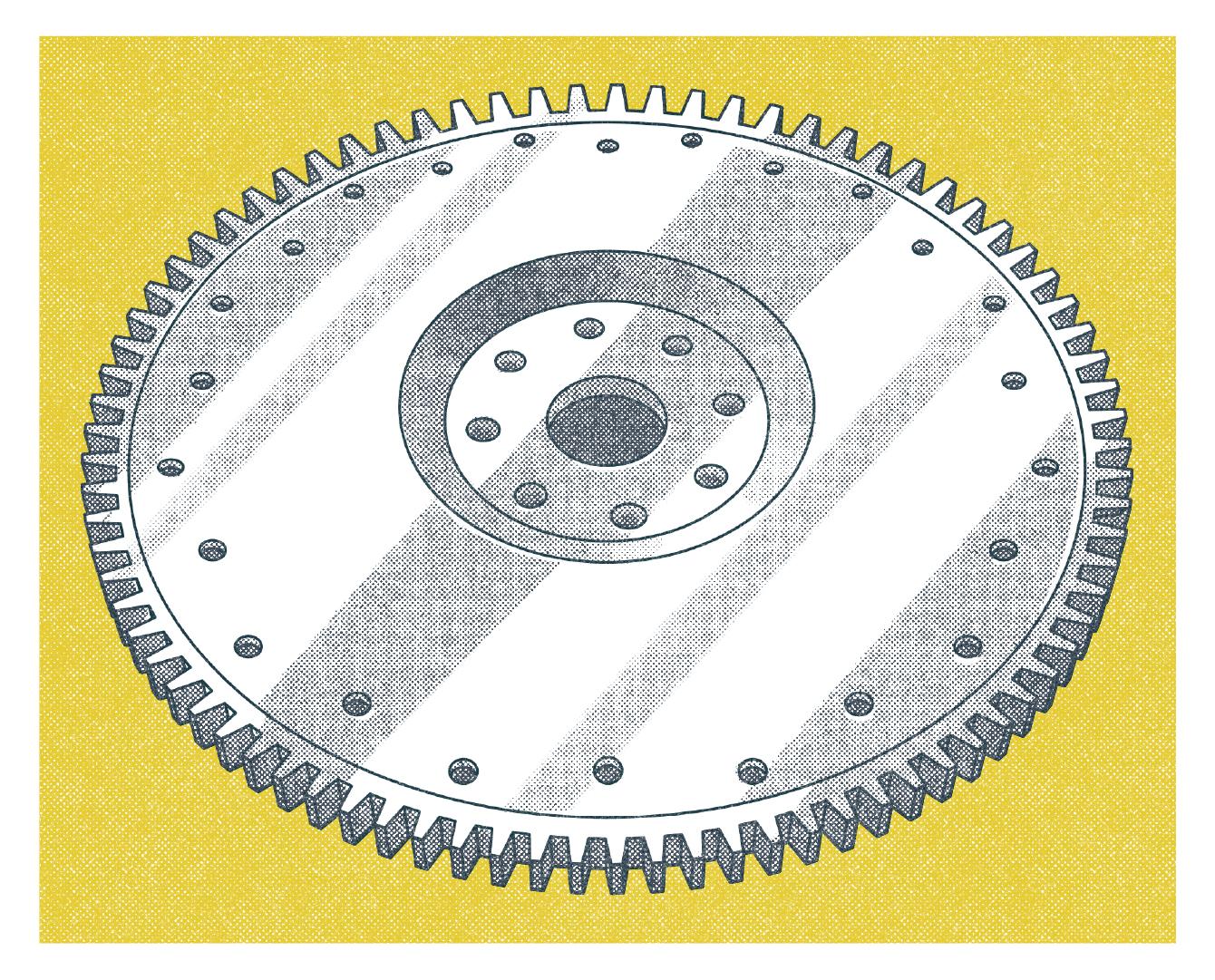
Vertical surface grinders will remove substantial amounts of material quickly and efficiently due to the large surface area of the wheel being engaged. Blanchard grinding can also result in a cross-hatched pattern on the surface finish. Cross-hatching is cosmetically desirable and provides improved wear characteristics where two parts have movement between them.
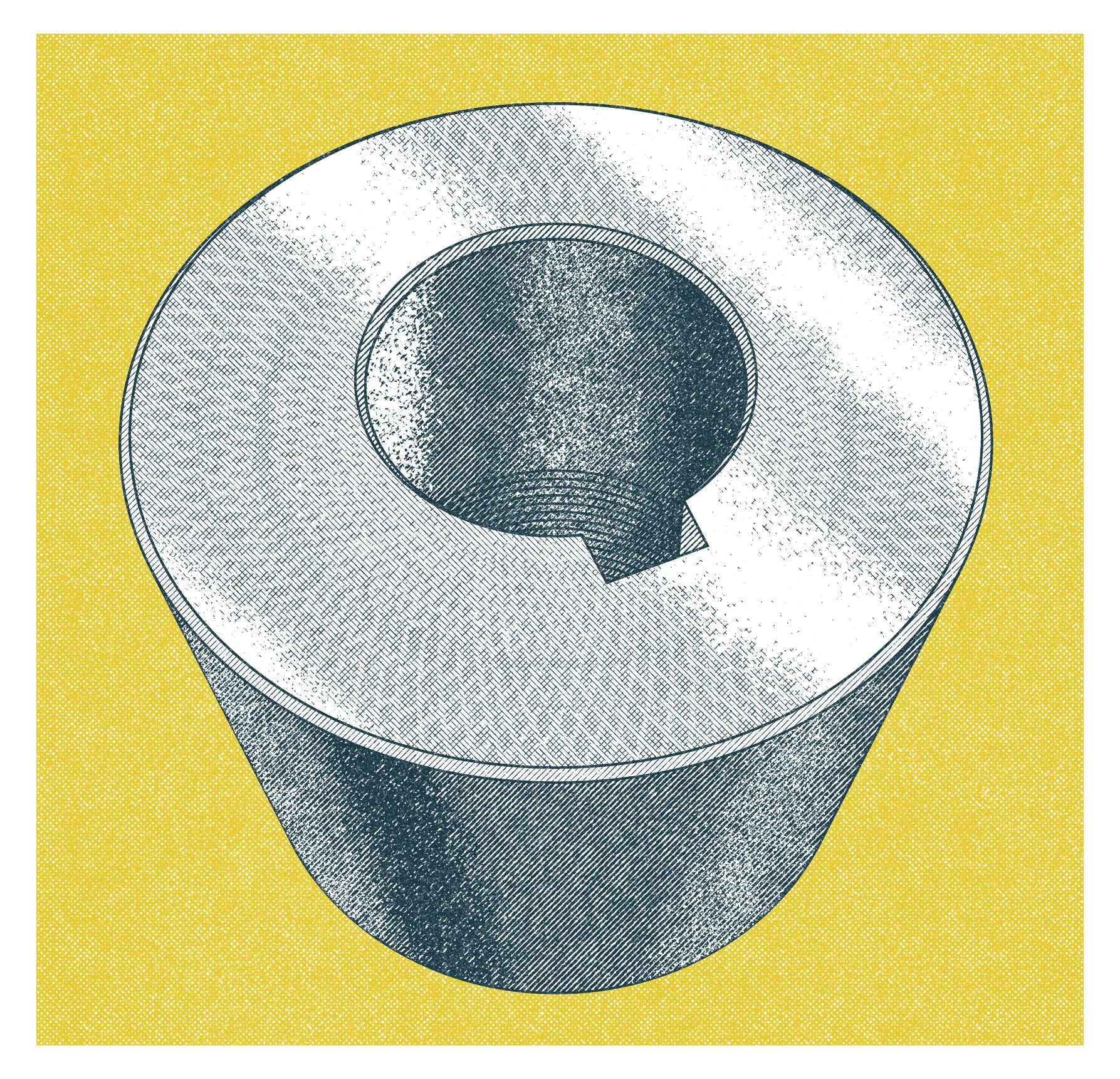
11.1.3 Cylindrical
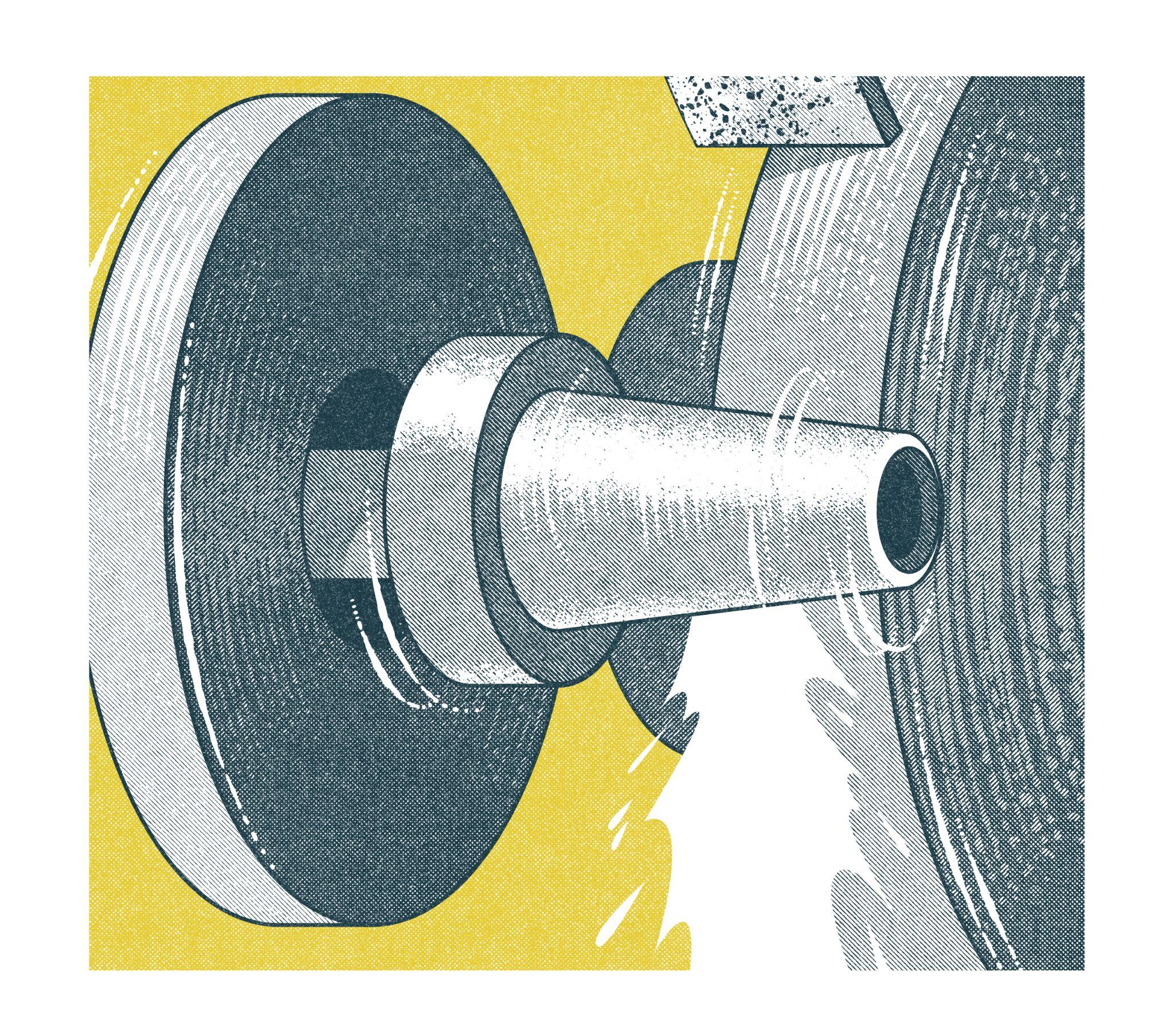
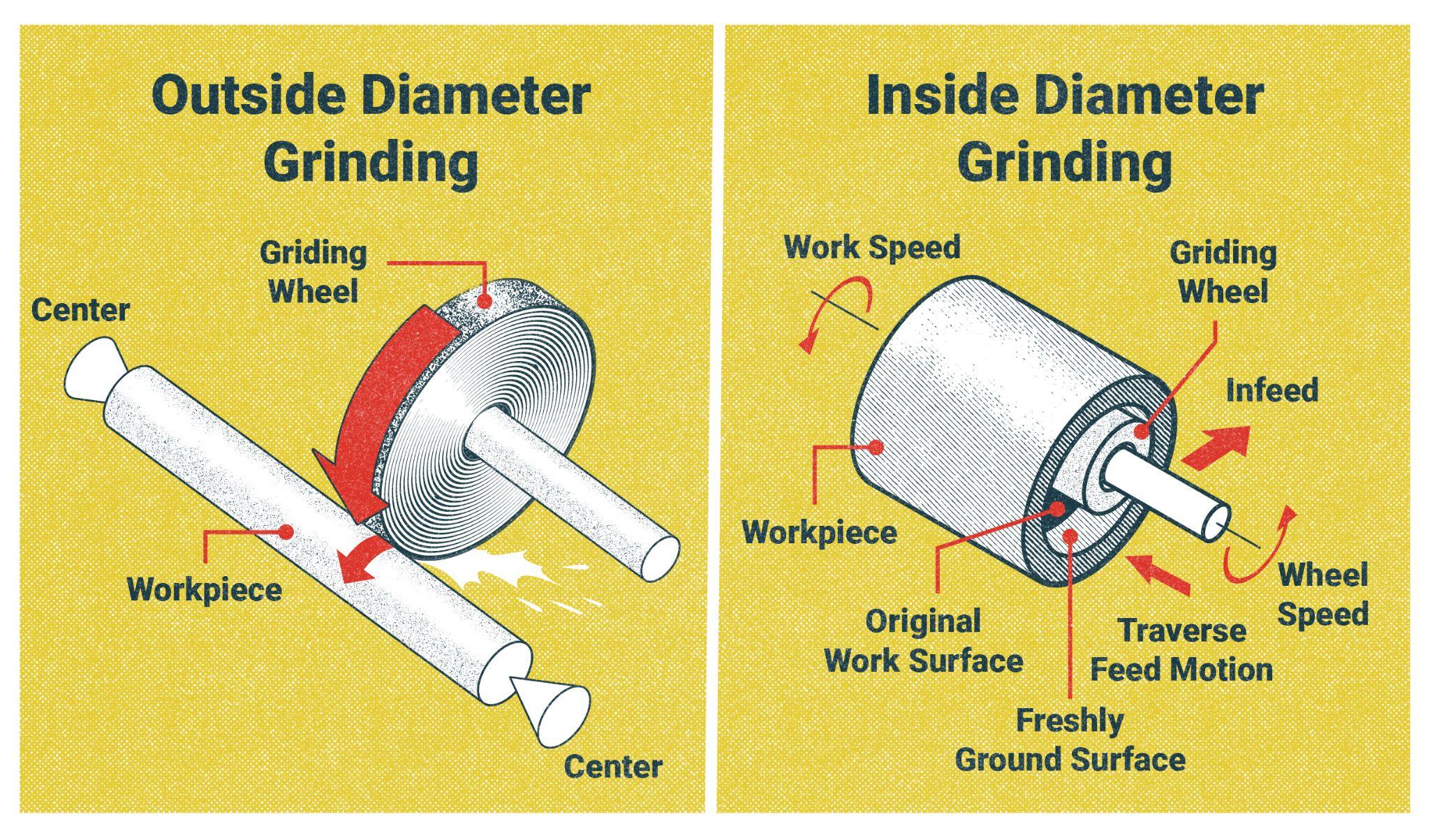
Cylindrical grinders can be either external (a), or internal (b). They are used to grind diameters, shoulders, and faces much like the features that are cut on a lathe. The workpiece is rotated against the surface of the grinding wheel as it turns. A hand wheel is used to make precise movements of the wheel head to set the cut depth. A power table moves the grinding wheel along the axis of the part’s rotation.
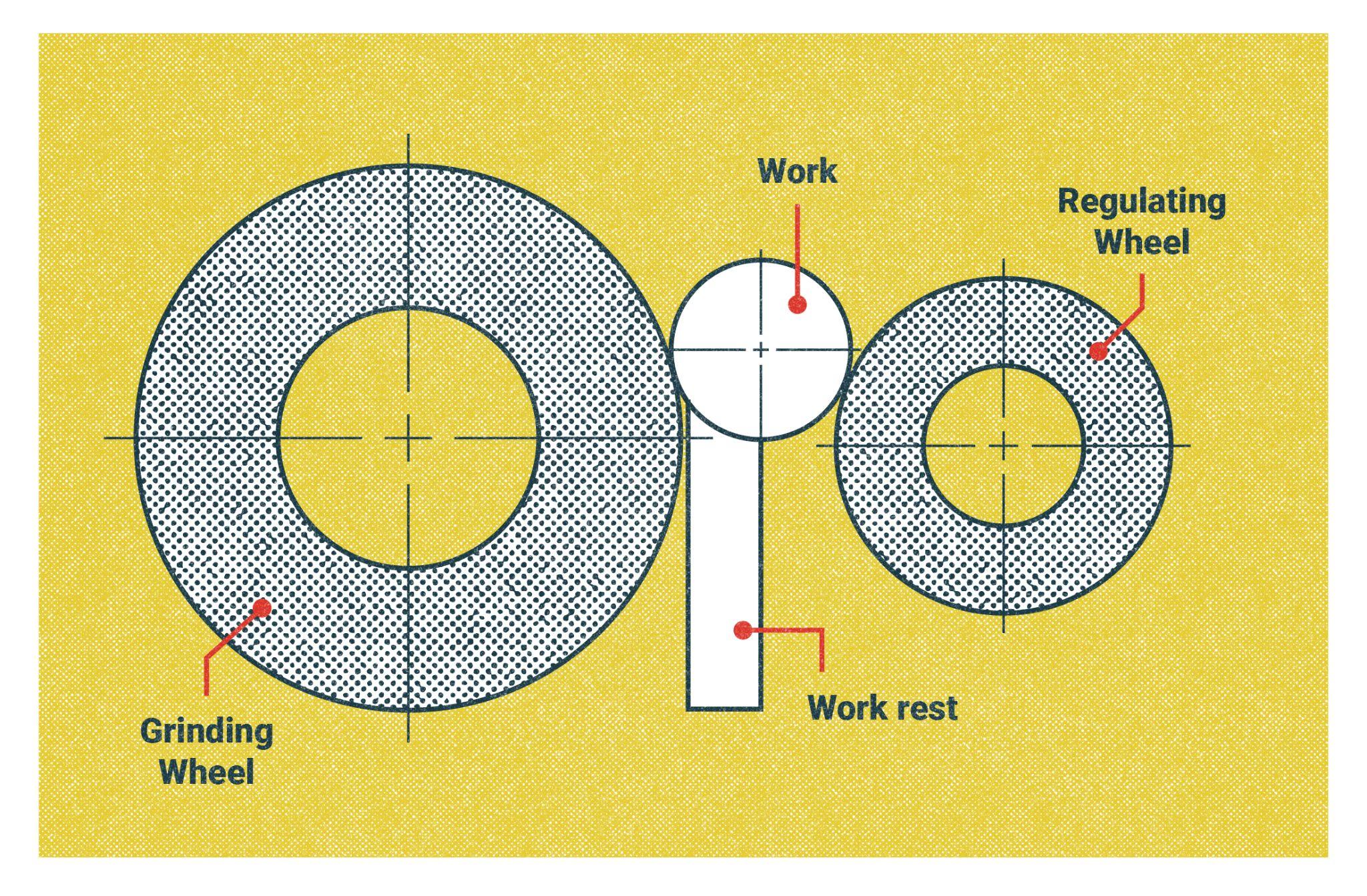
If a grinder is configured to cut only the outside diameter of the part, the OD, it is referred to as an OD Grinder. The same can be said for a machine set up to grind internal diameters, or ID. Faces, and shoulders can also be ground with the side of the wheel on either style of machine mentioned previously. An ID grinder uses a wheel mounted on an arbor. The arbor is a shaft that supports the grinding wheel as it removes material in a cylindrical shape inside a part.
11.2 Grinding Wheels
The grinding wheel is the cutting tool used in precision grinding operations. These wheels are similar to the ones used for offhand grinding, covered in the chapter on Hand Tools, and Benchwork. They are made of abrasive grain held together with a bonding material. Offhand grinding wheels are typically straight in shape. The motion of the machine can be accurately controlled. This allows a selection from a variety of wheel shapes that will best fit the application.
11.2.1 Shape
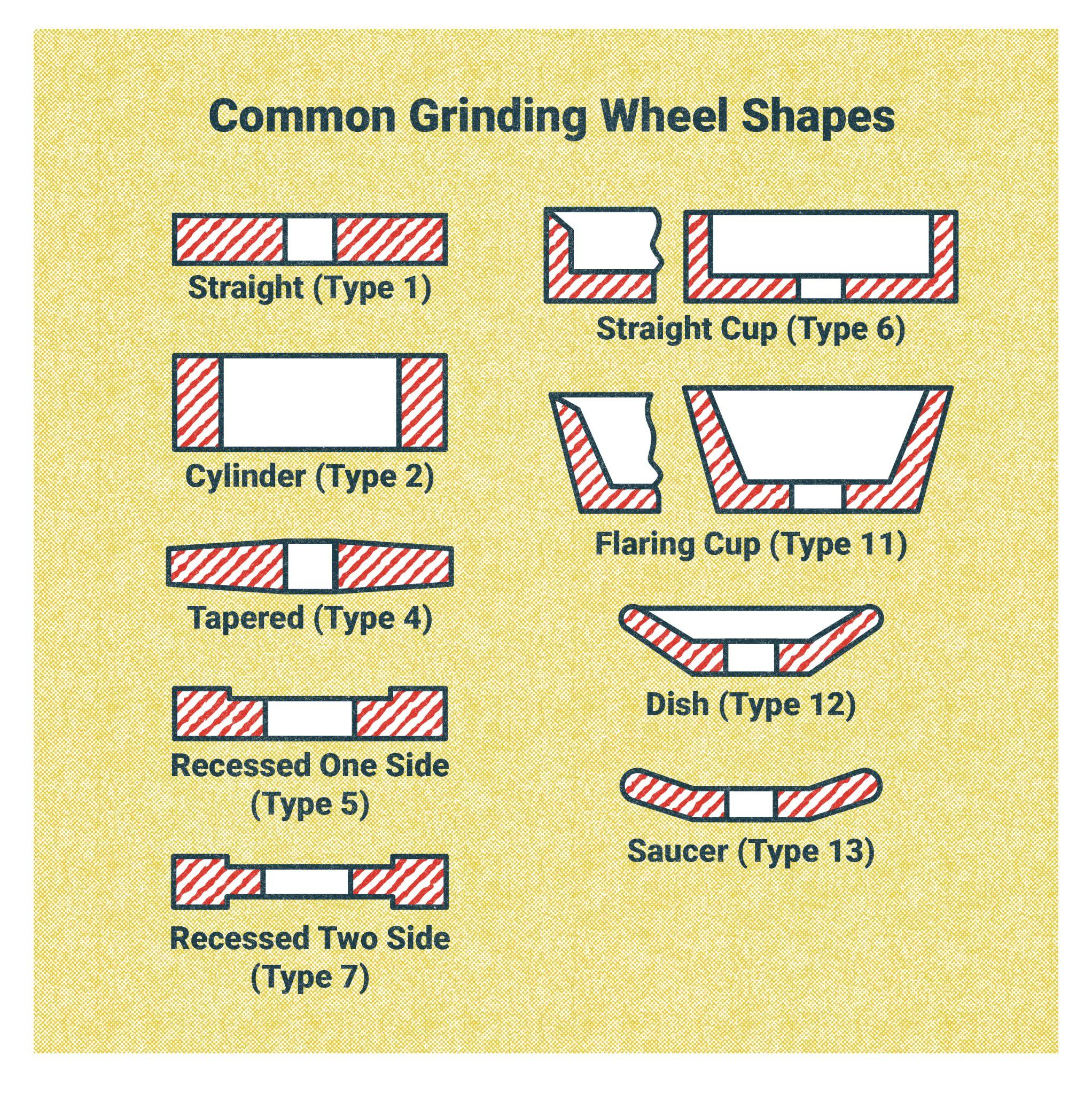
Types of wheels seen above; Straight (Type 1), Cylinder (Type 2), Tapered (Type 4), Recessed One Side (Type 5), Recessed Two Side (Type 7), Flaring Cup (Type 11), Dish (Type 12), and Saucer (Type 13).
The feature that is being ground will help identify the shape of the grinding wheel that is needed. A small part with a groove would require a narrow, straight wheel. Dressing, or modifying a tool would use a cup style wheel.
A straight wheel, as used on offhand grinders, is the most common wheel for a precision grinder. A wheel may also have features that are relieved or recessed. These wheels will minimize contact between the sides of the wheel and the workpiece. Cup, saucer, and dish shaped wheels are usually used for tool grinding, or modification.
The face of the wheel is the surface that is designed for grinding. The face is usually defined as the periphery, or outside circumference, of the wheel. In some applications, with a vertical grinder, the face of the wheel is the flat surface. When grinding two surfaces that are perpendicular to each other, the side of the wheel may be engaged at the same time as the face. This may be done to produce features such as a shoulder, slot, or groove.
11.2.2 Abrasive
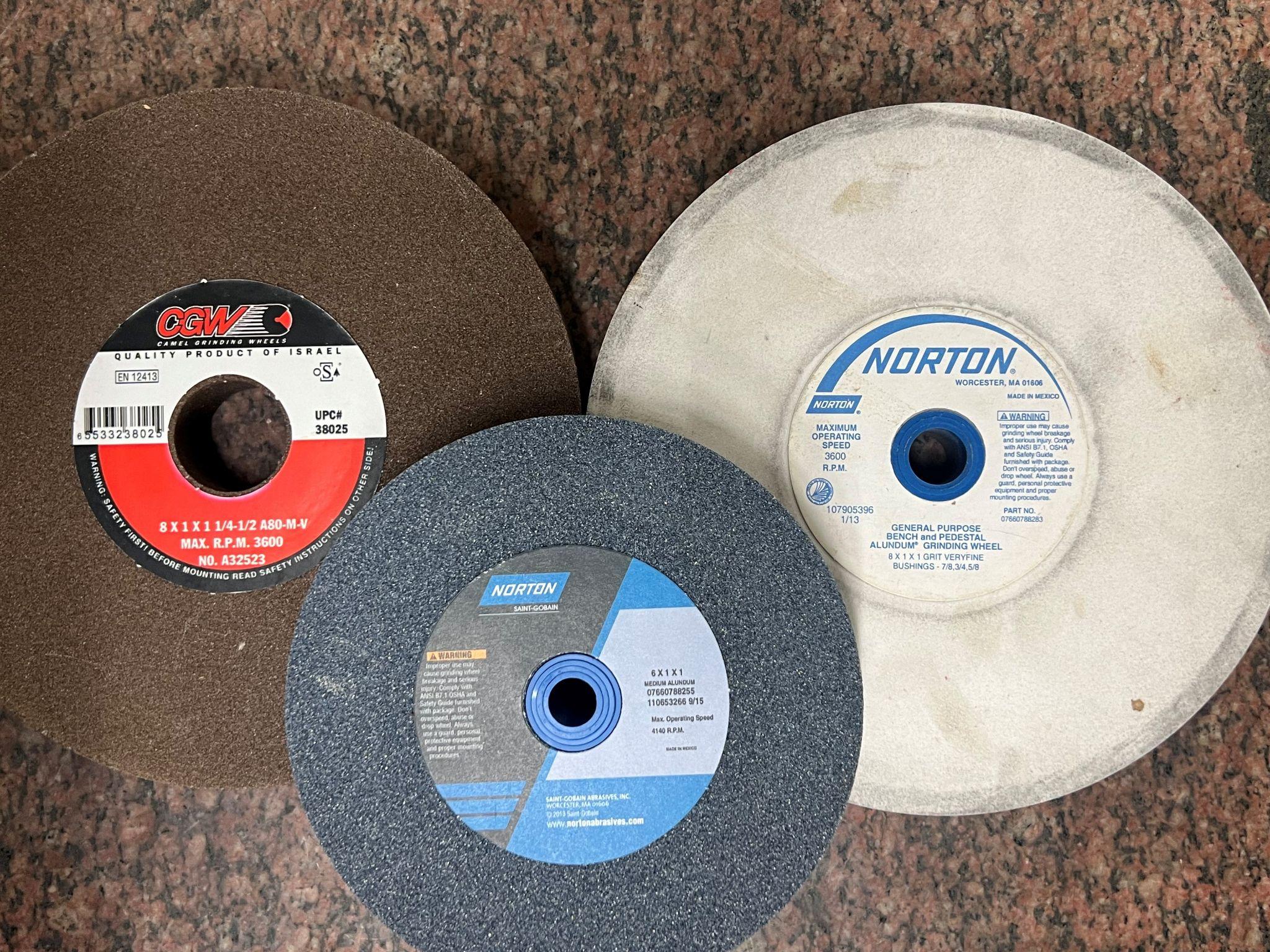
The abrasive material that grinding wheels are typically made of is one of these three combinations; Aluminum oxide, Ceramic aluminum oxide, or Silicon carbide. Aluminum oxide, and ceramic aluminum oxide wheels are identified by the letter A. The silicon carbide wheel will have the letter C on it.
Aluminum Oxide is used for steels. Ceramic Aluminum Oxide is for grinding materials containing iron. Silicon Carbide wheels are referred to as Green wheels. They are for grinding carbide.
It is important to only grind material appropriate for the specific abrasive wheel being used. For example, grinding aluminum on a wheel designed for steel will plug up the wheel, and build up heat. Excessive heat will cause the wheel to explode.
11.2.3 Grit
The grit, or grain size of the abrasive type is descriptive of the material that makes up the wheel. The lower the number, the coarser the wheel. Higher numbers indicate a finer grain pattern. Coarse wheels with a large grain structure will remove material quickly, and create a rough surface finish. A finer wheel will remove material more slowly, and produce a smoother surface finish. Coarse wheels will cut soft metals better because the larger grains can penetrate the workpiece more easily.
When grinding harder metals, a finer wheel with a tighter grain pattern provides more cutting points for rapid material removal. A consideration is that as the grit becomes finer, the heat from grinding increases. This means a slower work speed is necessary when finishing a part.
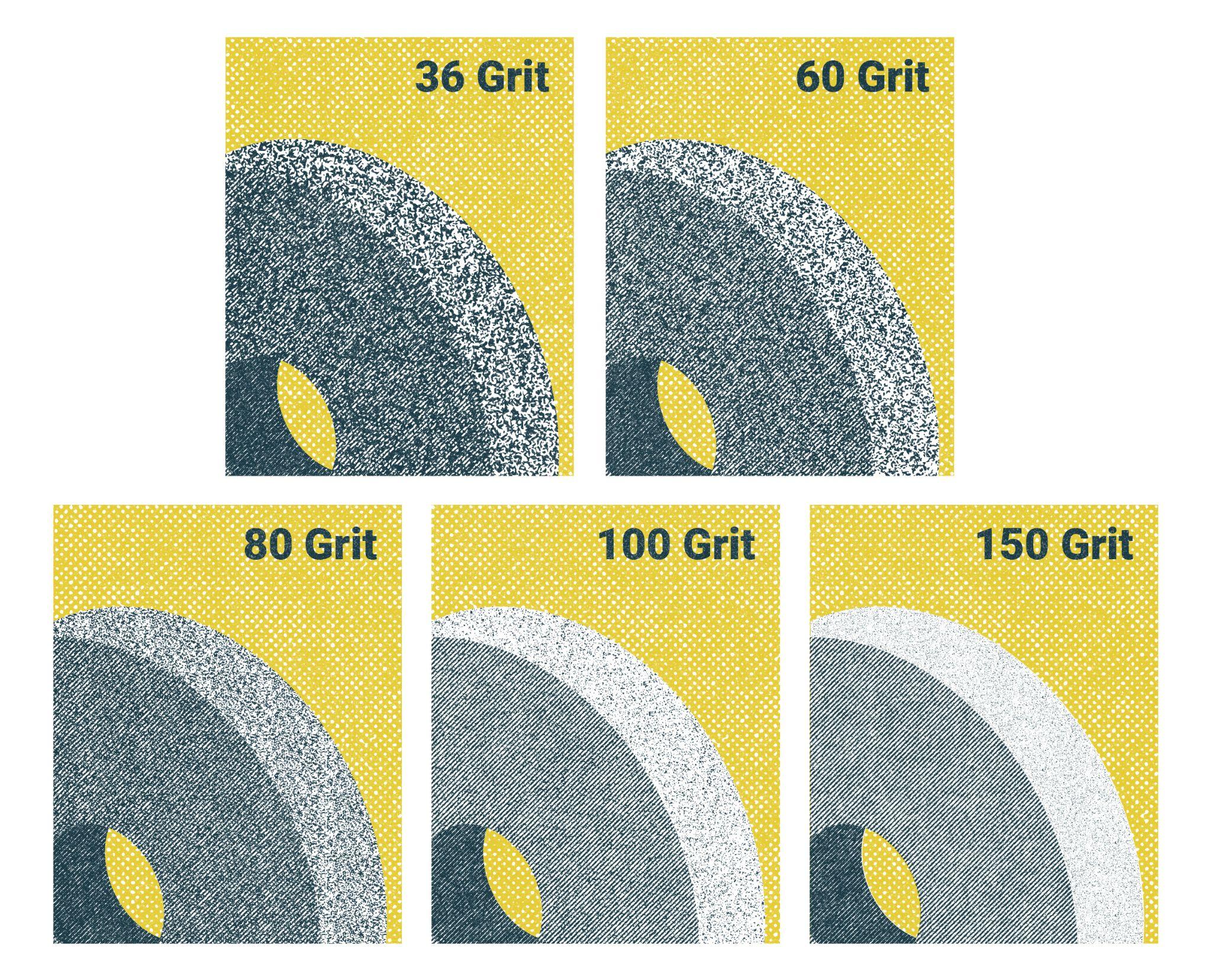
11.2.4 Grade
The grade of the grinding wheel refers to the hardness, or strength, of the bond. Grade A is the softest, and Z is the hardest.
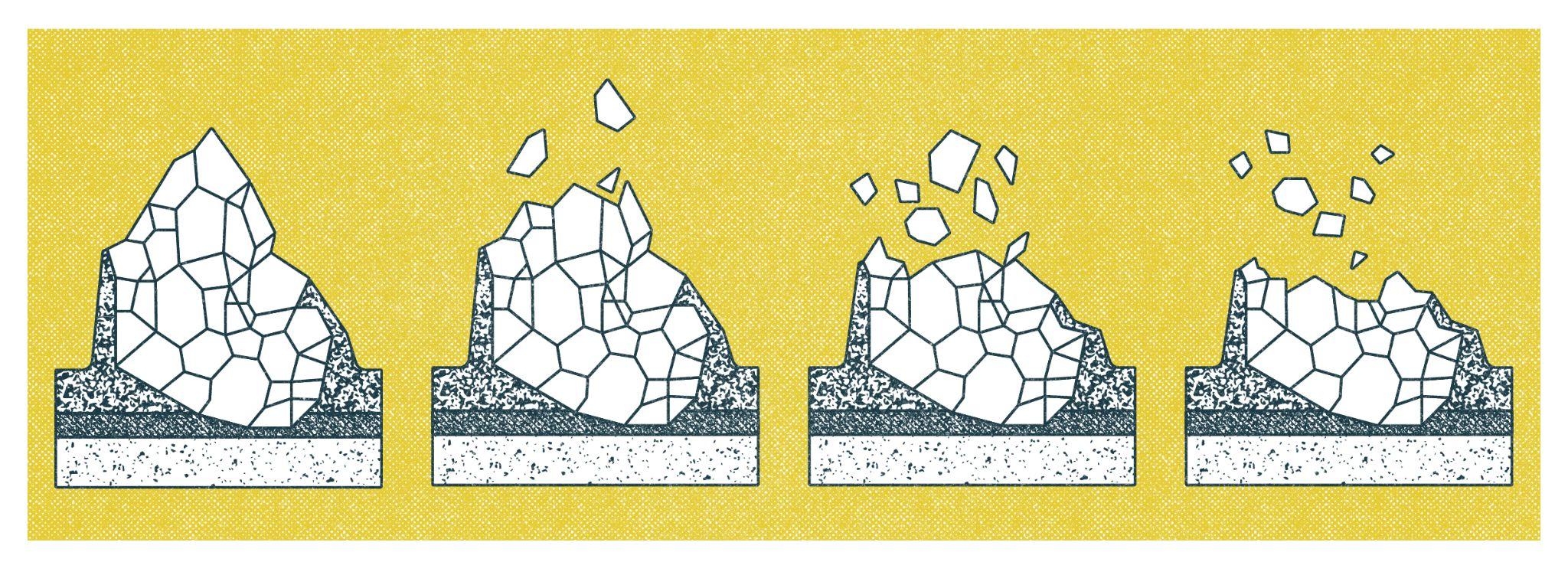
On the left is the sharp “new” grain. As the wheel breaks down, moving to the right, the grain becomes dull.
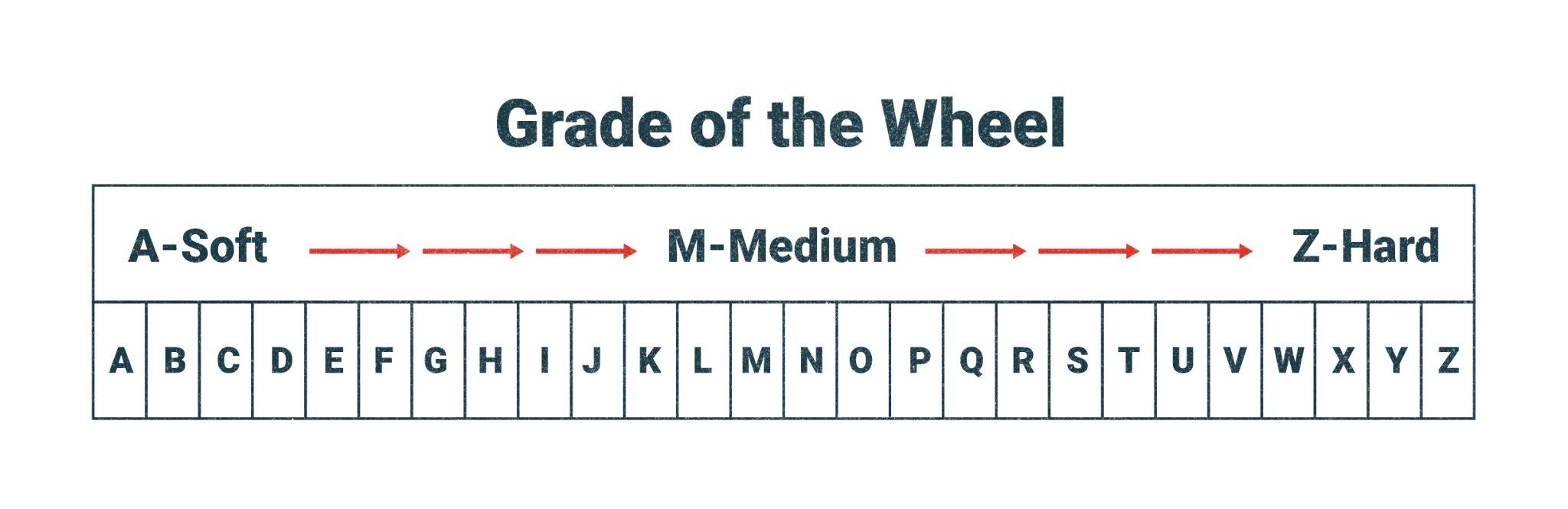
Generally, a softer wheel is used for hard materials because the wheel will release old grains before it becomes dull. This exposes new, sharper grains and helps to maintain the cutting process of the wheel. If a hard wheel is used for grinding a hard material, the grains will not release, and then the wheel will become dull. This causes wheel glazing, overheating, and burning of the work surface. A harder wheel should be used when the area of contact is small. Hard wheels are more wear resistant and are the best choice when a larger amount of material is to be removed. Selecting a softer wheel when making lighter finish cuts will increase the quality of the finish and assist in achieving dimensional accuracy.
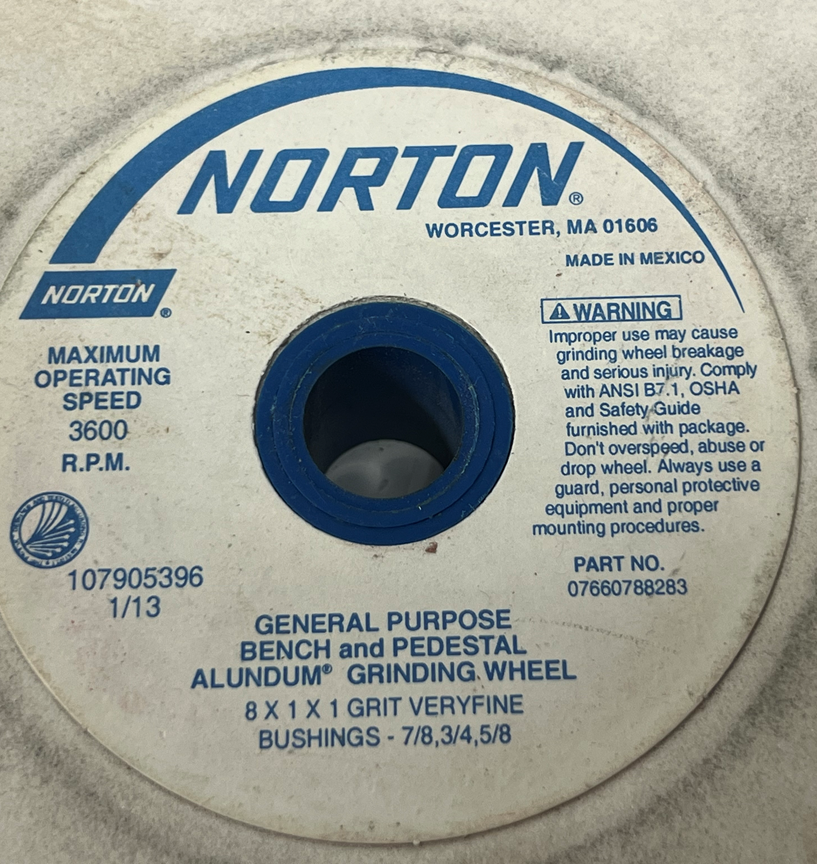
11.3 Operations
Surface grinders are primarily used for grinding flat surfaces. The work holding and setups are similar to those used in milling. When surface grinding, the wheel face is the outside diameter of the wheel.
11.3.1 Safety
Surface grinders, like the other machines in the shop, are dangerous. Follow some basic precautions to help ensure a successful operation.
- Personal Protective Equipment (PPE) starts with safety glasses.
- Some processes may require a dust mask.
- Wear appropriate closed toed shoes.
- Do not wear loose fitting clothing.
- Remove jewelry, watches, and tie back long hair.
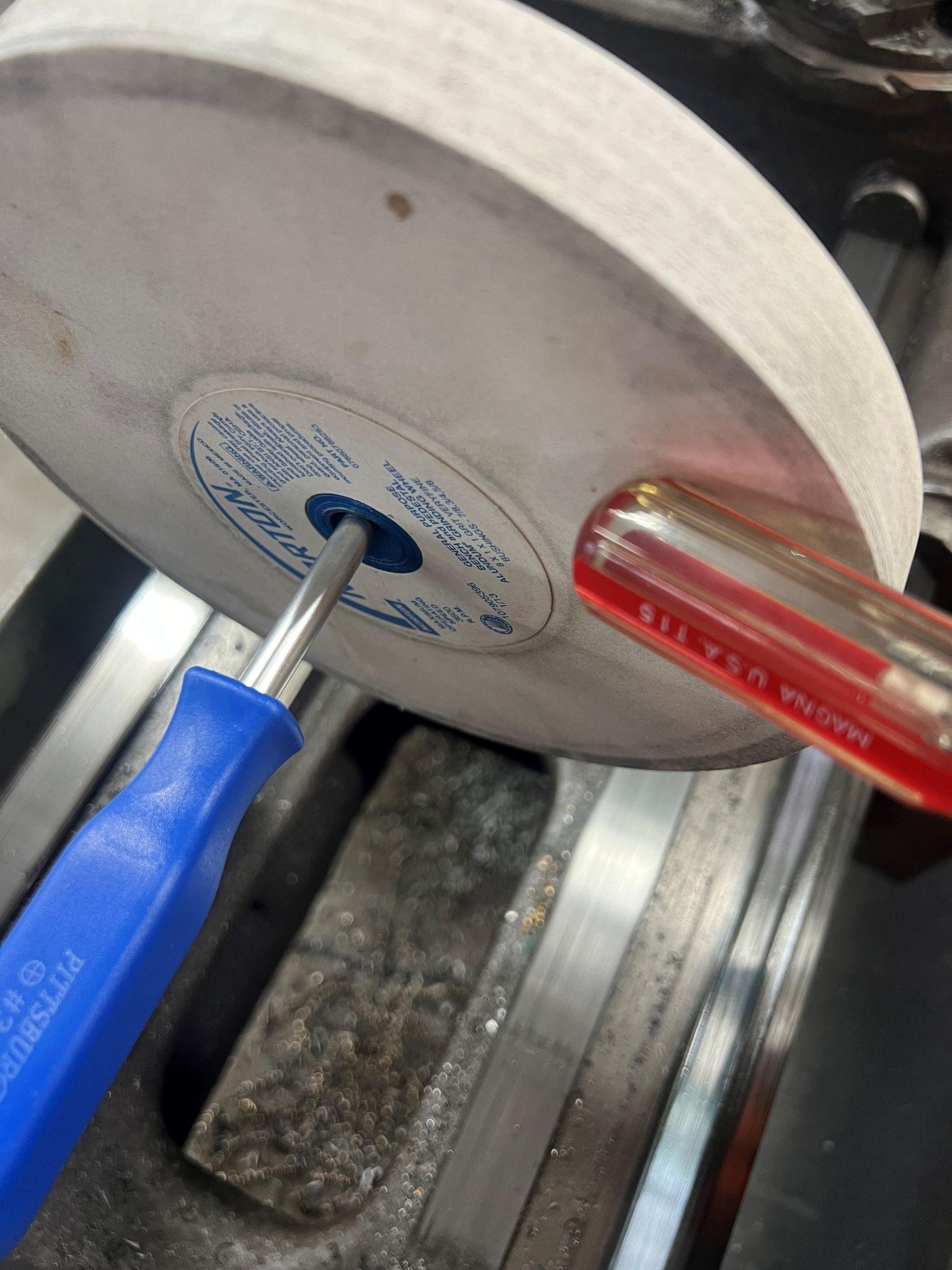
Another precaution is to perform a ring test before installing a grinding wheel. Hold the wheel with a small rod in the middle of it, as pictured below, and tap the side with the handle of a screwdriver. If there is a dull sound, that will indicate that there is a crack in the wheel. Discard it immediately. If it makes a high “ring” sound, proceed with installation.
Always ensure that the machine is off and that the wheel is not spinning before making any adjustments to the machine or the workpiece.
When removing, or installing a wheel, remember that the nut holding the wheel on the arbor will tighten as it spins. Depending on which side of the grinder the wheel is mounted on, the threads may be left-handed. Having a left-handed thread makes the nut tighten on the wheel as the wheel spins. If it was a right-handed nut, it would come off when the wheel started up.
11.3.2 Work holding
A surface grinder can have T-slots like those on a manual mill table. These can be used to directly clamp the parts down to the table. However, the clamps can be in the way of the grinding operation. A better workholding choice is to use a magnetic plate, or “chuck,” that is bolted to the table. Parts can then be placed on the magnet, and when the magnet is switched on, it holds the part in place while grinding.
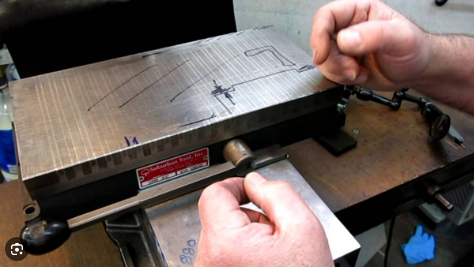
The magnetic plate is made from alternating segments of ferrous and nonferrous materials. When placing a part on the plate, the part should span at least three of the nonferrous segments, or the magnetic force may not be strong enough to secure the part to the chuck. If the workpiece is taller than its own length or width, the magnetic chuck may not be strong enough to hold the part.
Blocking can be used to help secure the part to the chuck and prevent it from tipping or being pulled off the magnet. Blocks are placed tightly around the workpiece before activating the magnet. Since the main force while grinding is in the direction of the longitudinal table feed (X axis), blocking on the left and right sides of the workpiece is critical. Blocking can also be used when grinding nonferrous parts. Accessories such as magnetic parallels, and magnetic v-blocks along with the usual clamping hardware, can be employed to hold a workpiece down while grinding.
CRITICAL: When using a magnetic work holding device, always double-check that the magnetic field is engaged, securing the workpiece to the table. After the grinding is completed, a demagnetizer may be necessary to remove the magnetism from the workpiece.
11.3.3 Wheel dressing
Before beginning any grinding operation, the wheel should be dressed. Dressing the wheel will true it up. Truing makes the wheel precisely round, removes deposits, and eliminates wheel runout. The dresser uses a single point diamond tip to cut against the grinding wheel. The dressing tool is mounted to the table using a magnetic chuck, as seen below.
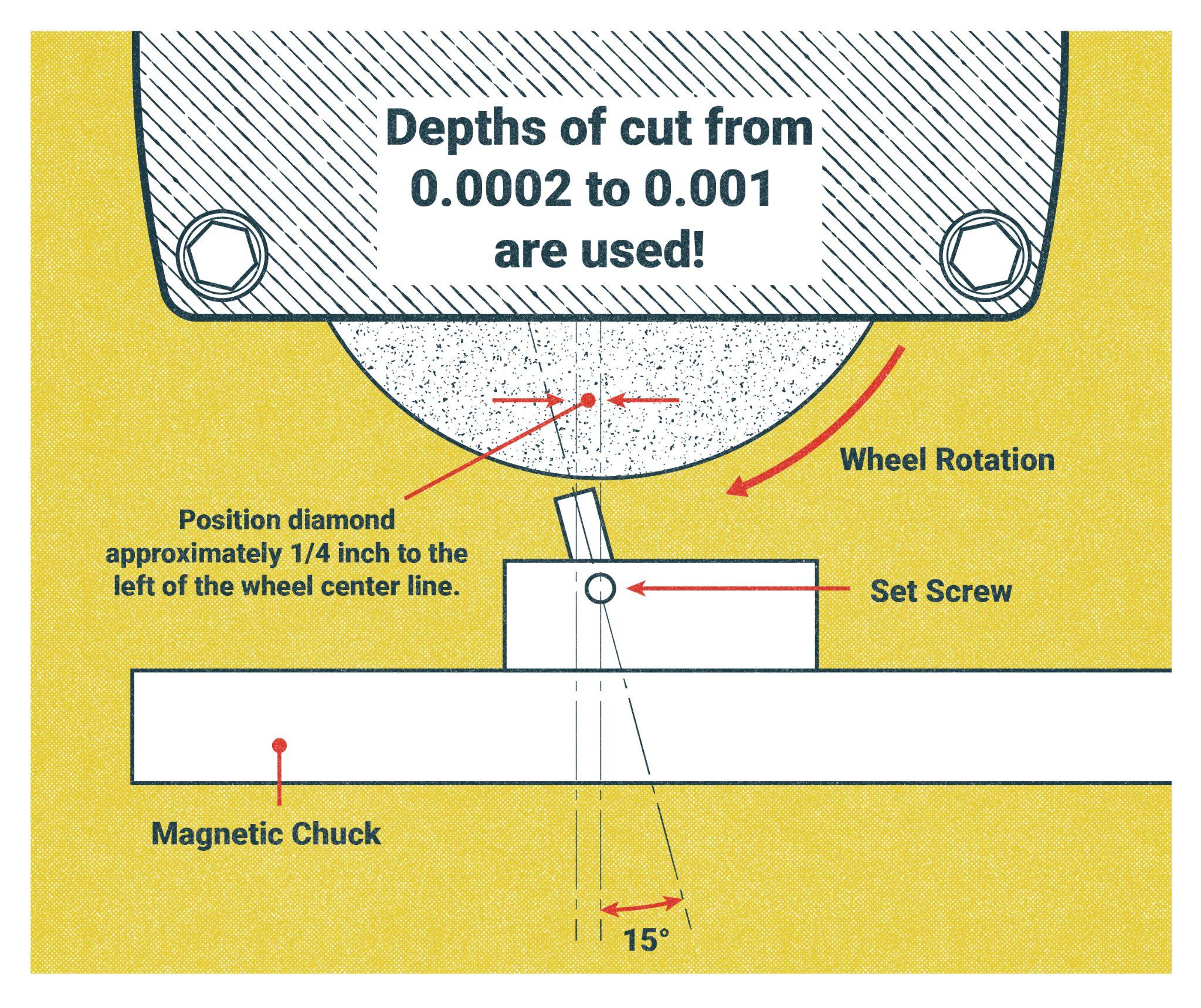
Here are the steps to follow for dressing a grinding wheel prior to use.
- The dresser must be placed on the exit side of the wheel (left), and point slightly away from the center of the wheel.
- Lock the long motion of the table. This is usually the X axis.
- Engage the magnet or clamping device.
- When starting the wheel, give it a spin to start the rotation, and then activate the power. This will help to keep the wheel from shifting on the arbor due to rotational torque on startup.
- When moving the dresser across the wheel, a fast pass will make a course finish. Moving it slowly will result in a fine finish. Dress the wheel according to the type of work, and the type of material; for example, roughing or finishing, hard or soft material.
11.3.4 Grinding
- Before placing the workpiece on the table, ensure that the wheel is not moving!
- Once everything is set up, the part is secure, and the wheel has been dressed, bring the wheel down next to the part, and slightly past the top.
- Next, “gently” move the table horizontally until the part touches the wheel. This process is referred to as “touching off”.
- Now slowly raise the wheel while keeping in contact with the part.
- When the part slides under the wheel, stop raising the wheel.
- Move the part away from the wheel on the exit side of the rotation.
- Now press the power switch to start the grinder wheel rotating.
- Once the grinder is moving and the workpiece has been touched off, the coolant can be started. Angle the nozzle towards the ingoing nip for best cooling. This will flush the grit away and keep the part from overheating.
- When the wheel is lowered to cut, the workpiece should make initial contact to the wheel on the outgoing nip side (left side).
CRITICAL: Remember, never stand or walk around the outgoing side of the wheel, the left side. The left side of the grinder is where parts go, and chunks of the grinder wheel go when parts get knocked off the table.
11.3.5 Problems
It’s not a perfect world. The grinding machine may need to be slightly adjusted to achieve the quality of finish that is required. Challenges that may be encountered are surface finish burning, scratches, or waviness. Adjustments to the process will improve performance.
Burning the surface happens when there is too much heat. This may be from overly aggressive cuts, and/or lack of coolant on the part. There will be a visible spiral with yellow or brown discoloration in some areas of the surface. Check the wheel dressing, work speed of the table, the cross feed, or redirect the coolant.
Scratches on the surface can be caused by grinding without coolant or not thoroughly cleaning the table before loading the part.
Waviness, or chatter, is a result of an out-of-round wheel. This happens when the wheel is not “trued” or “dressed” before using it. The wheel could also be loose on the spindle. If chatter is present, double-check that the wheel is secure, and then dress it. Waviness can also be caused by an unbalanced wheel. The wheel may need to be remounted.
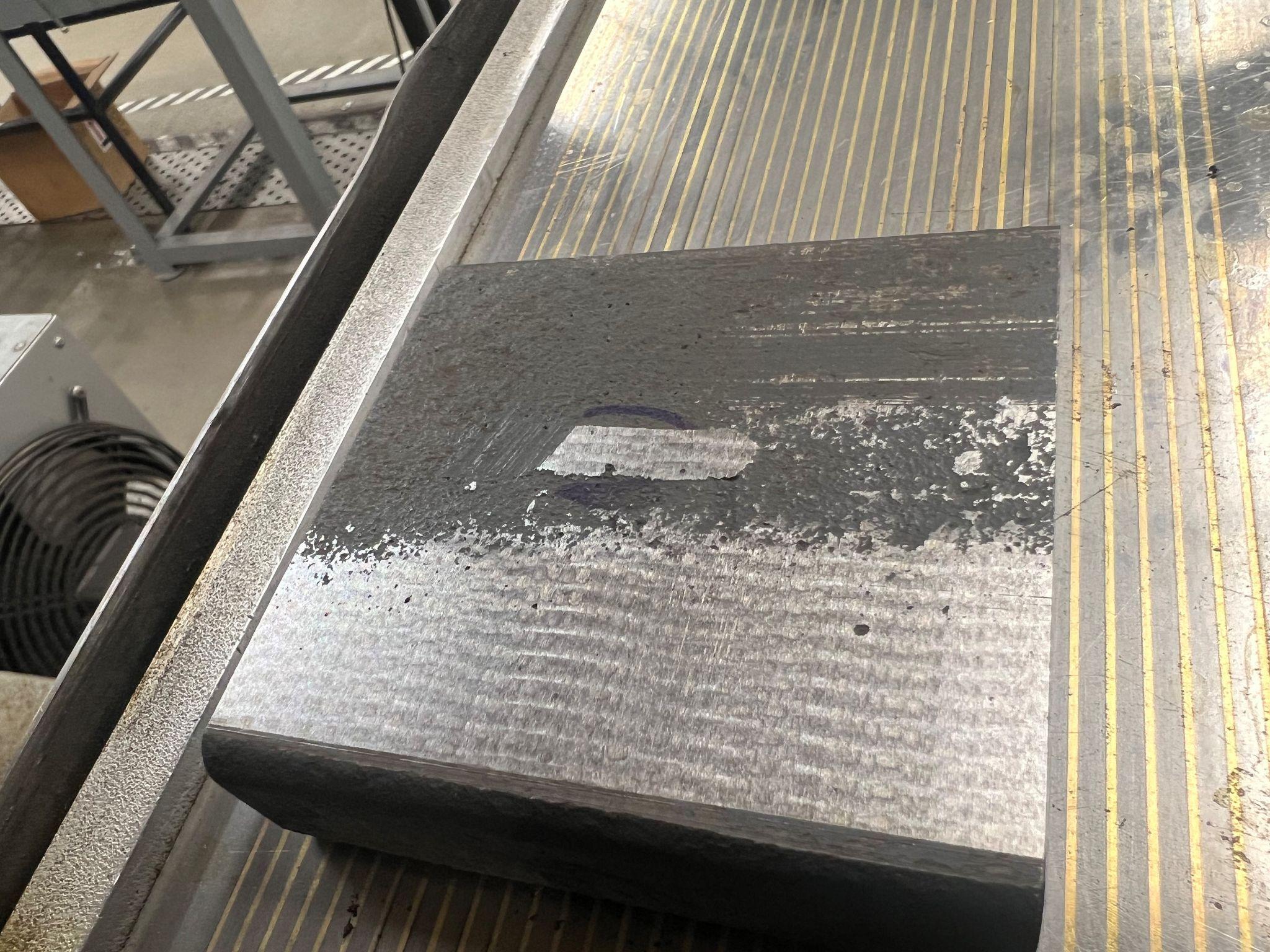
11.4 Application
Now let’s go grind a bench block! The following is a step-by-step sequence of operations that can be directly applied to most projects.
- Safety first – Wear safety glasses, remove jewelry, and tie back loose clothing, and long hair.
- Gather equipment – Have some towels nearby to aid in coolant clean up. Create a clean location to place the tools.
- Choose a grinder – The workpiece is square, so use a horizontal surface grinder.
- Choose the wheel – The material for the Bench Block is mild steel. A straight grinding wheel will be used, with the cutting surface on the circumference of the wheel. The wheel is an Aluminum Oxide abrasive for the steel workpiece. A grit of 60 is for general purpose grinding applications.
- Perform a ring test – Ring test the grinding wheel before the wheel is placed on the spindle. If a high ring note is heard, proceed with installation. If the sound is dull, get a new wheel.
- Mount the wheel – The grinding wheel will be mounted on the grinding spindle. To tighten the nut that holds the wheel in place, turn it the opposite of the direction the grinding wheel turns when grinding. This nut usually has left-handed threads.
- Dress the wheel – Set the dressing diamond just past the center of the wheel, on the exit nip side (typically the left). Ensure that the magnet is on, and the diamond is secure. Start the wheel rotating by hand. With your hand clear of the wheel, turn on the power to bring the wheel up to speed. Bring the wheel down to just touch the diamond dresser. Move the crossfeed out towards the operator, and then in away from the operator to evenly dress the wheel. Bring the head down .0002 to .001 and move the crossfeed again. Repeat until the wheel is evenly cleaned up, then stop the wheel before continuing.
- Workholding – Ensure that the grinding wheel is not spinning; clean the table thoroughly. Place the part on the magnetic table with concave side down. Turn the magnet on, and check that the workpiece is secure.
- Touch off – While the wheel is stationary, bring the wheel head down slightly past the top of the part, and on the outgoing nip side of the wheel. “Gently”’ move the table workspeed direction, X-axis, so that the part touches the wheel. Raise the head until the workpiece passes below the grinding wheel. This process stages the wheel within a few thousandths of the part to expedite grinding, and to avoid excessive plunging into the part on first contact.
- Instructor Note – Once a complete understanding of manually controlling the surface grinder is demonstrated, the automated functions can be introduced if the machine has the capability. Caution is strongly advised. If the grinder is not set correctly, the part may be destroyed, the machine may be damaged, and/or bodily harm may be caused to anyone nearby, including yourself.
- Turn on coolant – Position the coolant nozzle to spray at the ingoing nip side of the wheel on top of the workpiece.
- Turn the grinding wheel on – Start the wheel by rotating it by hand in a clockwise direction. With hands clear, start the motor to bring the wheel up to speed. This will help keep the wheel centered on the spindle if the electric motor has a sudden power surge.
- Start position – Start with the workpiece close to the operator, away from the side of the grinding wheel, and to the left of the outgoing nip.
- Make a complete pass – Use the left hand on the hand wheel to move the part along the workspeed direction from the outgoing nip to the ingoing side, and back to the beginning. The workpiece must clear the grinding wheel before changing direction. Now use the right hand on the hand wheel to move the crossfeed towards the grinding wheel. The crossfeed direction distance should be less than the width of the wheel to create an overlap grinding pattern.
- Repeat as needed – Continue this pattern of moving right, left, and in until the workpiece is on the far side of the grinding wheel.
- Back to the beginning – Move the part to the far left of the grinding wheel, and reposition the workpiece to its starting position.
- Are we there yet? – Turn the wheel off, and inspect the workpiece. Determine if more grinding is required. Continue alternating between making a complete pass, and checking the finish, and/or dimensions before lowering the head to resume grinding.
- Adjust the head – Lower the head down .0002 tenths to thousandths to remove more material.
- Make a complete pass – Make another complete pass, moving the workpiece right, left, and in. See description above.
- Back to the beginning – Move the part to the far left of the grinding wheel, and reposition the workpiece to its starting position.
- Are we there yet? – Turn the wheel off, and inspect the workpiece. Repeat these last three steps until the desired results are reached.
- Level one Complete – When the workpiece has a consistent finish, it may be removed from the grinder.
- Wait for it – Wait until the grinding wheel has stopped before continuing.
- Power down – Turn off the table magnet to release the workpiece.
- Clean up – Wipe down the table and the workpiece to remove the silt. This is the grinding dust mixed with the coolant.
- What’s next? – It is likely that at this point only one side has been ground. Flip the part over, and repeat the above sequence. If both large faces of the workpiece are ground, then the project will go to the mill to square up the short sides.
AUTHOR’S TIP
On thin parts, it may be necessary to take a small amount of material off of each side and flip the part over several times. This will help ensure that the part stays flat without being restrained by accounting for the stress relieving of the material being removed.
SUMMARY
Precision grinding is a specialized manufacturing process that produces parts with both a high degree of accuracy and surface finish. In precision grinding, the objective is to achieve the desired shape, size, and finish of the part by removing material with an abrasive wheel.
The basic principle of precision graining is the interaction between the grinding wheel, and the workpiece. The grinding wheel is made of abrasive particles bonded together. It has a high Revolutions Per Minute (RPM) when in use. The work is held securely on a table below the wheel and oscillates back and forth to provide full surface coverage of the work area.
A benefit of precision grinding is being able to achieve extremely high tolerances. This process allows manufacturers to attain precise dimensions that are critical for the fit and function of the assemblies. Precision grinding is typically the only means of achieving accuracy at this level.
REVIEW QUESTIONS
- What type of grinder would be used to grind a 123 block?
- Horizontal grinders are typically used to finish what types of parts?
- Vertical grinders are typically used to finish what types of parts?
- Cylindrical grinders are typically used to finish what types of parts?
- What are three basic shapes of surface grinder wheels?
- Explain why it is important to know the material used to make a grinding wheel.
- What is the general term for the material?
- Describe two ways to hold parts on a surface grinder.
- What is the purpose of performing a ring test on a grinding wheel?
- What can happen if a wheel is not dressed?
- Why should you always approach the grinding wheel with the workpiece from the outgoing nip side when starting to grind?
REFERENCES
Global Market Insights. (2024, April). Grinding machine market size – by type (non precision grinder, precision grinder), by application (automotive, aerospace, medical, construction, industrial manufacturing, electrical and electronics, marine industry, others), & forecast, 2024 – 2032. Retrieved May 14, 2024, from https://www.gminsights.com/industry-analysis/grinding-machine-market