Chapter 3: Technical Drawings
Overview
The term “blueprints” refers to the technical drawings created by engineers that convey all the information necessary for manufacture. With technological advancements, engineer drawings are no longer blue and, in most instances, are transmitted digitally between entities. Engineers utilize a design tool called Computer Aided Design (CAD). CAD is a tool that allows engineers to use the advanced technology of software based design to create digital models that can be transmitted electronically to manufacturers across the globe. It is common for machine shops to receive these models, which are then entered into Computer Aided Manufacturing (CAM) software used by CNC programmers to create tool paths that are translated into G-Code and posted to machines, which ultimately create the part.
With all this advanced technology, we still have “blueprints” (which are no longer blue) referred to as engineer drawings or just prints, which we use on the shop floor to ensure we are machining the part within specifications. This is the reason machinists must be proficient at interpreting drawings and extracting all necessary details expressed by the design engineer.
There are industry standards for engineer drawings, but you will be surprised how different they are from one company to the next. It is for this reason a machinist must be educated in the information communicated in engineer drawings. The American Society of Mechanical Engineers (ASME) Y14.100 standard defines a drawing as: “an engineering document or data set that discloses directly or by reference, by means of graphic or textual presentations, or combinations of both, the physical or functional requirements of an item” (2013a, para. 3.12). Print, blue print, drawing and engineer drawing are used interchangeably within the manufacturing industry and within this text.
OBJECTIVES
- Identify different sheet sizes and their use.
- Apply information from the title block to the parts being made.
- Define terminology used on a technical drawing.
- Identify different pictorial views.
- Identify part dimensions.
- Identify American National Standards Institute (ANSI), International Organization of Standardization ( ISO) standards
- Explain the difference between different line applications within a drawing.
KEY TERMS
- Allowance
- American National Standards Institute (ANSI)
- American Society of Mechanical Engineers (ASME)
- Best Practice
- Bill of Materials (BOM)
- Computer Aided Design (CAD)
- Computer Aided Machining (CAM)
- Datum
- Detail Drawing
- Detail View
- Dimension
- DIM tags
- Drawing Area
- First Angle Projection
- First Article Inspection
- Hidden Lines
- In-process checks
- International Organization of Standardization (ISO)
- Nominal
- Orthographic Projection
- Section View
- Third Angle Projection
- Title Block
- Tolerance
- Surface Profilometer
3.1 Industry Drawing Standards
Drawings function as a contract between the engineers who designed the part and the manufacturers who are tasked with creating the part. All information needed to manufacture a part must be communicated in written form in such a manner as to communicate subtle and complicated information. As you may imagine, there are many difficulties in executing this task. For example, what unit of measurement is used? Metric or Inch? How much error may be allowed in manufacture while still performing reliably? What material is the part made from? Has the part been revised over the years, and do you have the latest revision? In an effort to standardize this process, industries have adopted universal standards created by the American National Standards Institute (ANSI), which is centered around the inch unit of measure and is predominant in North America, and the International Organization of Standardization (ISO), which uses the metric standard and is used extensively in Europe.
A few of the standards that pertain to this chapter are as follows:
- ASME Y14.1 Decimal Inch Drawing Sheet Size and Format (2020b). Sheet sizes for printing and layout purposes are defined. Metric version of this standard is ASME Y14.1M
- ASME Y14.2 Line Conventions and Lettering (2015)
- ASME Y14.3 Orthographic and Pictorial Views (2013b)
- ASME Y14.5 Dimensioning and Tolerancing (2019)
- ASME B46.1 Surface Texture (2020a)
In the text that follows, we will provide a basic knowledge of technical drawing content that will allow you to get started.
3.2 Sheet Size and Format
3.2.2 The Sheet
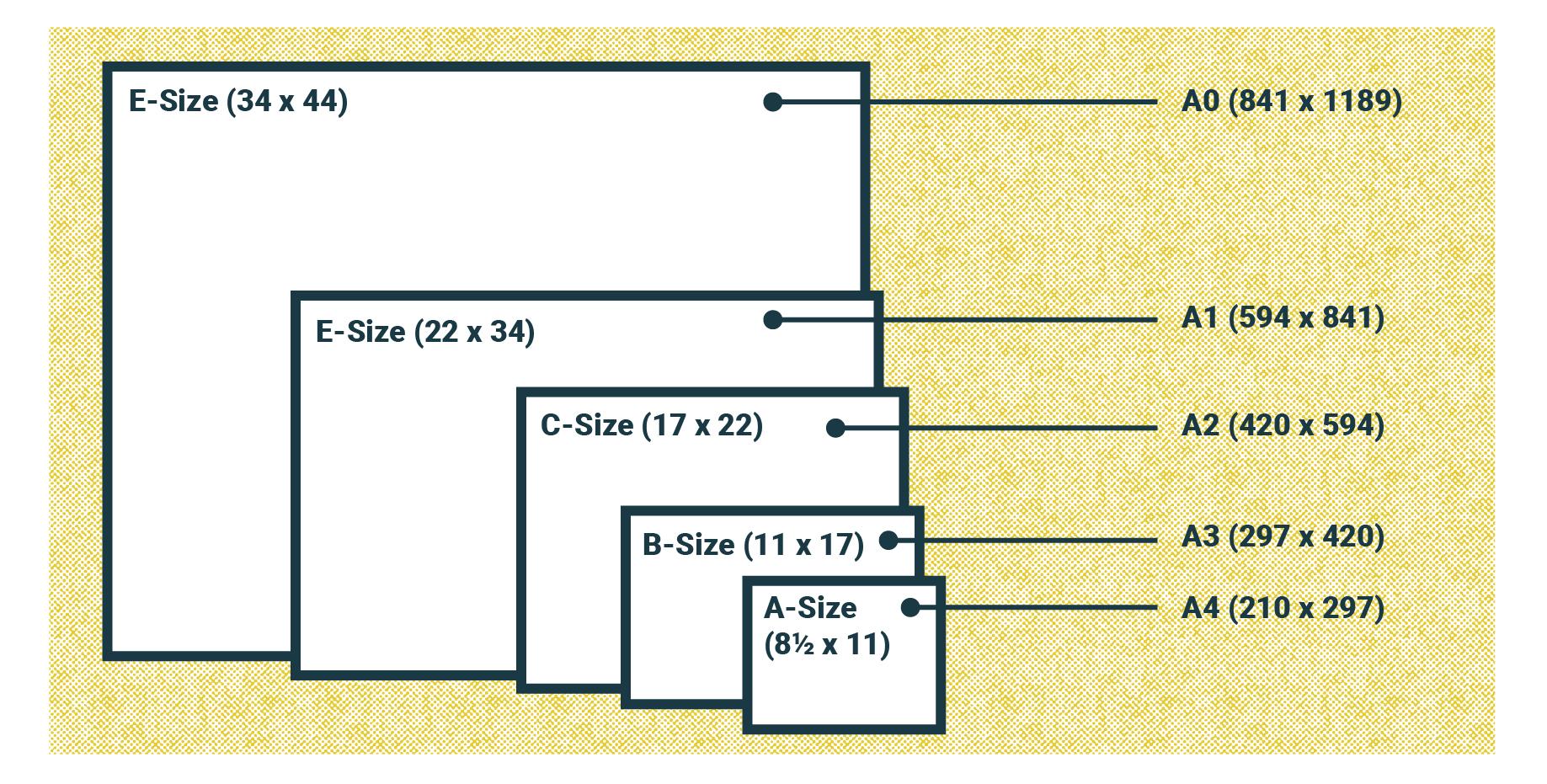
The physical size of the drawing sheet is based on the A size which is 8.5 X 11” (standard copy paper), and subsequent sizes are multiples of this. Size B is 11 X 17”, Size C is 17 X 22”, Size D is 22 X 34”, Size E is 34 X 44” and size F is 28 X 40”. Since these are all scaled in inches, they are the ANSI standard.
Drawing margins have minimal standards of 0.50” and engineers may modify them as they see fit.
For the machinist, the larger the sheet size, the easier it is to extract details. If you are fortunate to have a computer at your workstation, you may open the sheet and zoom in to arrive at any detail you desire. An advantage of the printed sheet is the ability to mark up the sheet with any helpful annotations.
3.2.3 Title Block
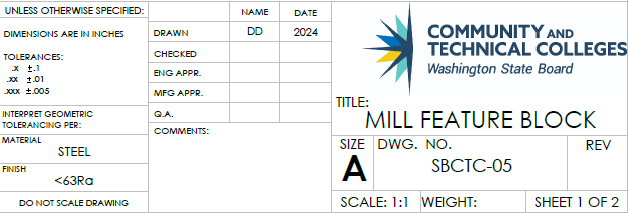
The title block is a section of a drawing that has information that pertains to the entire set of drawings. In the case of multiple pages drawings, the title block must be used on page one and may be used on following pages. Title blocks are important because they explain how to interpret information found in the drawing area. Most companies adopt a best practice to define how they will use the tile block within their organization. Best practices are procedures agreed upon within an organization to standardize information, also referred to as standard operating procedures. This explains why you will find subtle differences in prints and title blocks used by engineers. The ASME standards set forth the following guidance for title blocks (2013a, Section 6).
Information found in a title block includes company name, title of the drawing, the drawing number, revision number, date of drawing, scale of drawing, the sheet number if multiple sheets are used, tolerance information, materials used, surface finish, projection view used and comments.
3.2.4 Drawing Area
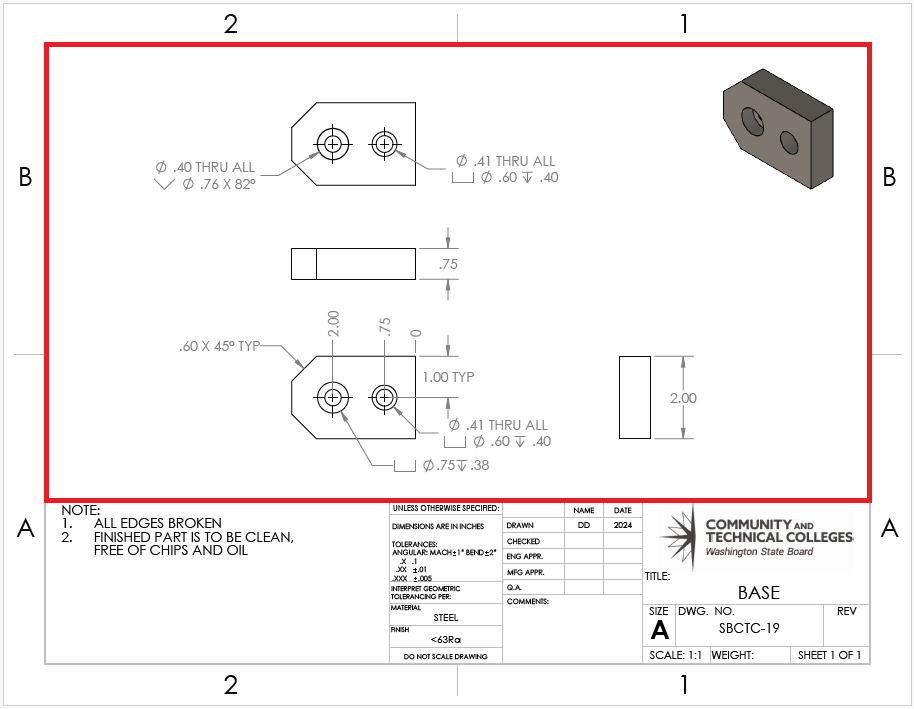
All of the information you will need is found in two places on a drawing: the drawing area and the title block, so these two topics deserve special attention.
The drawing area (illustrated in red above) refers to the designated area within the drawing sheet where the graphical representation of the component, part, or assembly is created. It’s the space where the actual visual and geometric details of the object being documented are illustrated using lines, dimensions, symbols, annotations, and other graphical elements.
The drawing area is critical because it serves as the primary visual representation of the engineering design. It allows engineers, manufacturers, and other stakeholders to interpret the design intent, dimensions, and specifications necessary for the construction or fabrication of the component or assembly.
3.3 Drawing Views
3.3.1 Assembly drawing
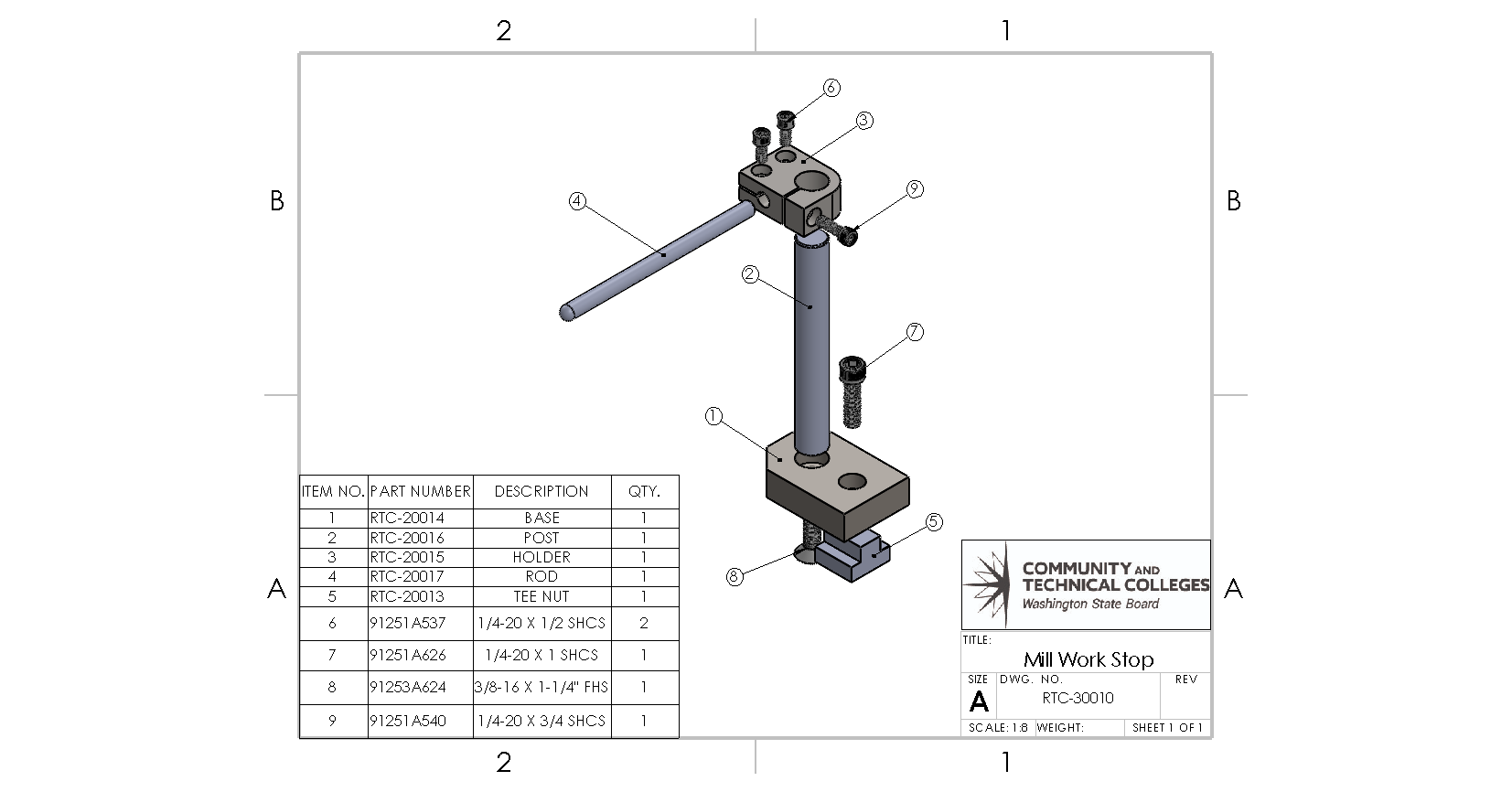
Assembly drawings show how all the parts of an assembly fit together and the functional relationship between them. The above figure of a mill work stop illustrates how all the parts of the object go together. Two views are used in the drawing space. On the right is the mill work stop assembled into the final configuration for use. The view on the left is an exploded view where all the pieces of the object are separated from the assembly but still maintain a relationship as to the order in which they fit in the assembly. From the exploded view drawing, the viewer can understand that item 9, a ⅜” socket head cap screw, mates with the counterbore in item 1, the base, and threads into item 5, a T-nut.
The assembly view has the added advantage of incorporating a Bill of Materials (BOM) a BOM is a comprehensive list of all the materials, parts, components, and sub-assemblies needed to manufacture or build a product as depicted in an engineering drawing. The assembly drawing in the figure above has a BOM in the bottom left corner of the print. It provides detailed information about the quantity, description, part numbers, and other relevant attributes for each item.
In the context of an engineering drawing, a BOM typically accompanies the drawing to ensure that all the necessary components and materials are accounted for in the manufacturing or assembly process. The BOM serves as a reference for procurement, production planning, cost, and inventory management.
3.3.2 Detail Drawings
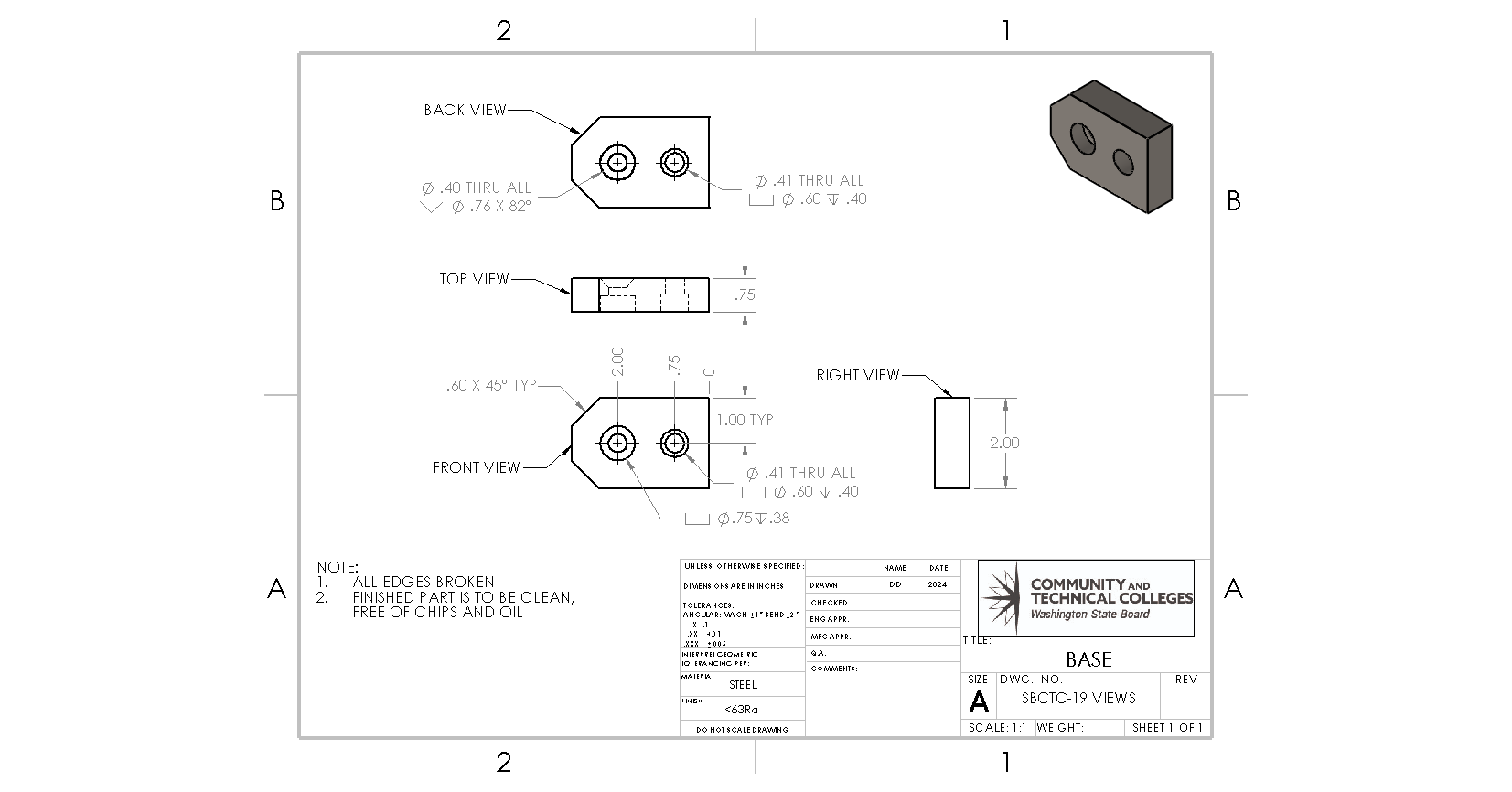
Detailed drawings are graphical representations that provide specific and comprehensive information about an individual component, part, or section of a larger product, structure, or system. Detail drawings are the primary type used by machinists on the shop floor. The drawing must communicate all the desired features in a detailed manner, which allows the technician to measure each feature as it is made.
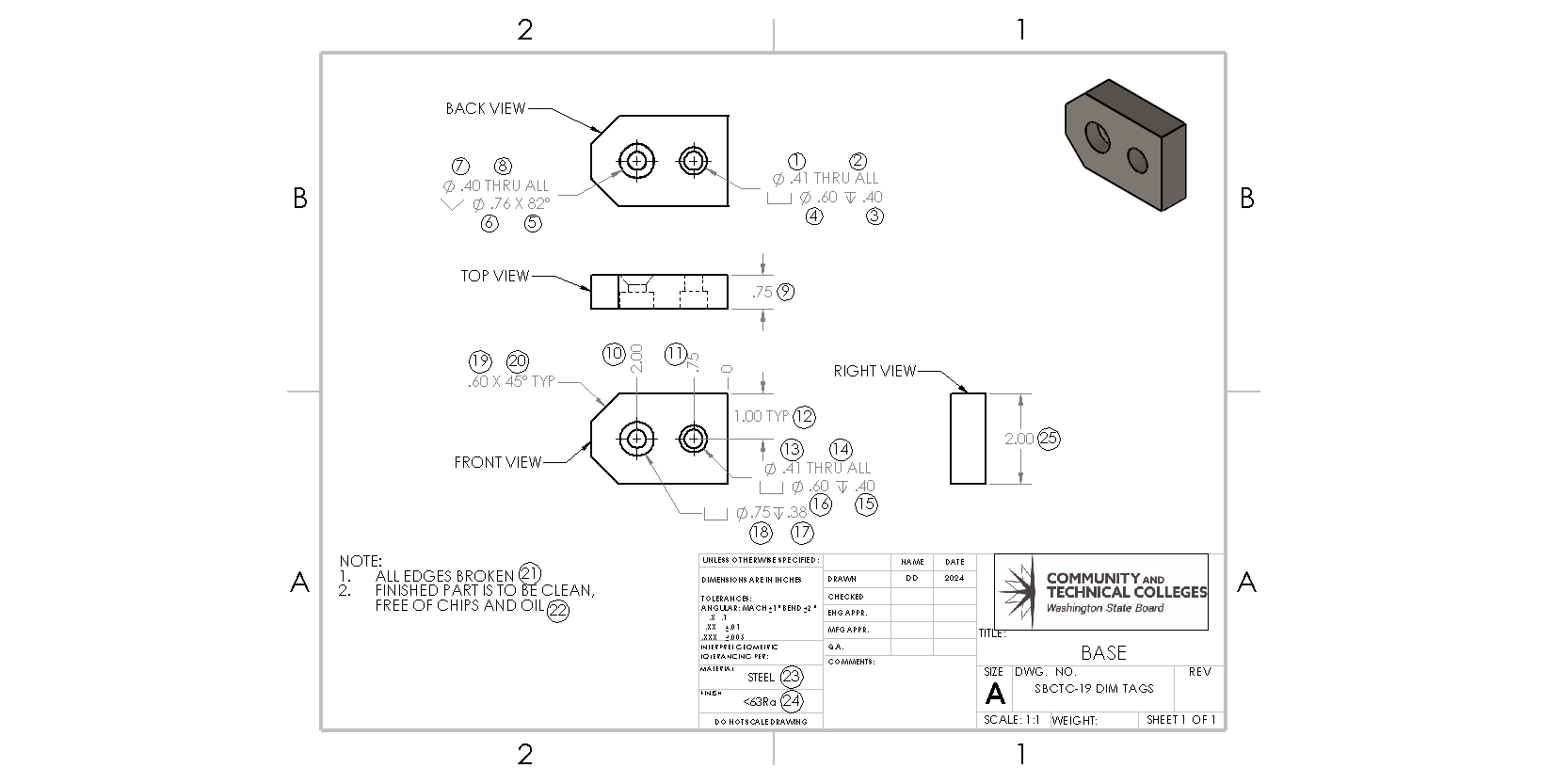
It is common practice for machine shops to modify detail drawings by adding Dimension Tags (DIM tags) which correlates a specific dimension to a simple numbering system that is used to complete FAIs and In Process Checks. For example, the height of the part in the above figure is controlled by DIM tag 25.
Table 3.1
First Article Inspection for a Specific Part
SBCTC-19 BASE FAI |
||
DIM TAG |
DIM |
MEASURED DIMENSION |
1 |
0.41 |
|
2 |
THRU |
GOORNO-GO |
3 |
0.40 |
|
4 |
0.60 |
|
5 |
82° |
GO/NO-GO |
6 |
0.76 |
|
7 |
0.40 |
|
8 |
THRU |
GO/NO-GO |
9 |
0.75 |
|
10 |
2.00 |
|
11 |
0.75 |
|
12 |
1.00 |
|
13 |
0.41 |
|
14 |
THRU |
GO/NO-GO |
15 |
0.40 |
|
16 |
0.60 |
|
17 |
0.38 |
|
18 |
0.75 |
|
19 |
0.60 |
|
20 |
45° |
|
21 |
EDGE BREAK |
GO/NO-GO |
22 |
CLEAN |
GO/NO-GO |
23 |
STEEL |
CERTS GO/NO-GO |
24 |
<63Raμ” |
|
25 |
2.00 |
|
26 |
3.00 |
|
When a setup machinist is producing the first part of a new run, they must complete a First Article Inspection (FAI). A FAI is a production validation process that verifies that a new or modified production process produces conforming parts. It’s an important step in the manufacturing process that ensures products are made to the correct specifications and meet customer requirements.
The FAI is an inspection document from which the inspection plan is created, and it lists all the dimensions found on a detailed drawing. The FAI has provisions for the setup machinist to record actual measurements taken from the first run part (setup part). The FAI is a critical document that the manufacturer uses to ensure they are indeed making the part as designed. This FAI process takes a considerable amount of time and effort, and production may not proceed until it is complete. Not all parts require a FAI. If the customer is not from a sector that requires them, such as aviation, they must be completed; however, not all sectors demand them, such as food processing.
In-Process Checks (IPCs) are routine checks performed during production to ensure that the product quality is met. These checks can be performed during manufacturing or packing. IPCs are performed by production machinists throughout the manufacturing process to ensure DIMs stay within tolerance. A manufacturing planner decides which DIMs from the FAI need to be verified throughout production,and the production machinist is tasked with performing these inspections and documenting the results.
Notes on a detail drawing are common, and they communicate information that is outside the built in features of a detail sheet. In the example above, the edge break is called out (DIM tag 21) in a note, as are the parts needing to be clean and free of oils (DIM tag 22). Both of these notes are important, especially since most parts proceed to some sort of outside processing before ultimately returning to the customer.
3.3.3 PART VIEWS
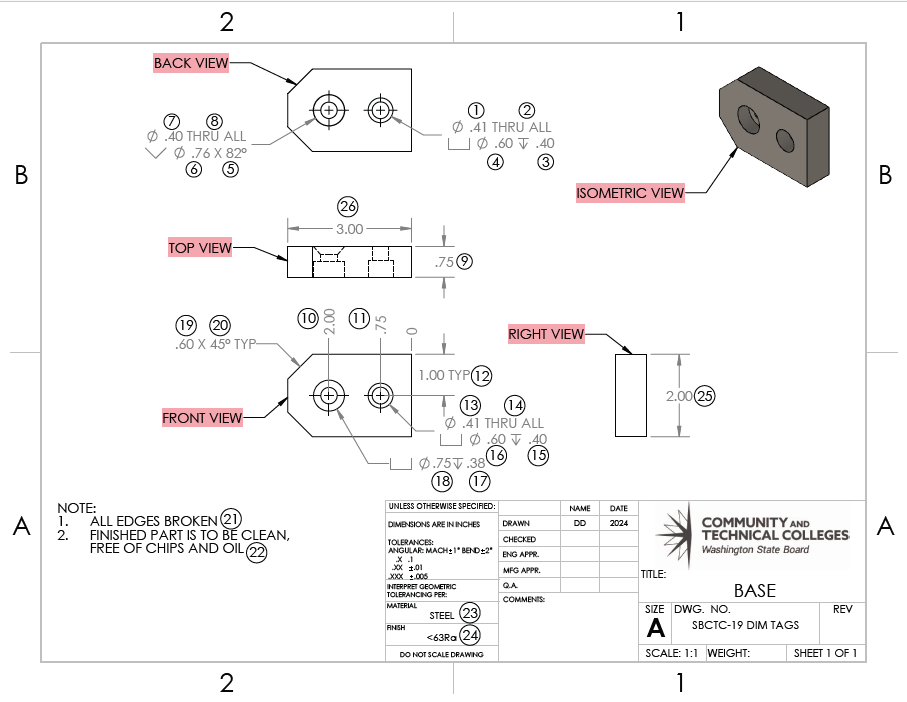
The primary views are the fundamental pictorial views utilized to illustrate the most information about the part. This procedure is referred to as orthographic projection. Orthographic projections are used to represent a three-dimensional object in a two-dimensional drawing. These views provide a comprehensive and accurate representation of the object from different directions, enabling a complete understanding of its shape, size, and features.
The most common primary views are: front, top and right side view. These three primary views are typically arranged orthogonally to each other, forming the foundation of orthographic projection. The combination of front, top, and right side views gives a comprehensive understanding of the object’s geometry in three dimensions. When necessary, more views may be added to convey a better understanding of the object.
An orthographic view is created by projecting a viewing side of the part onto a plane parallel to that surface. That surface is then turned to be parallel to the front plane of the part.
3.3.4 Orthographic Projected View
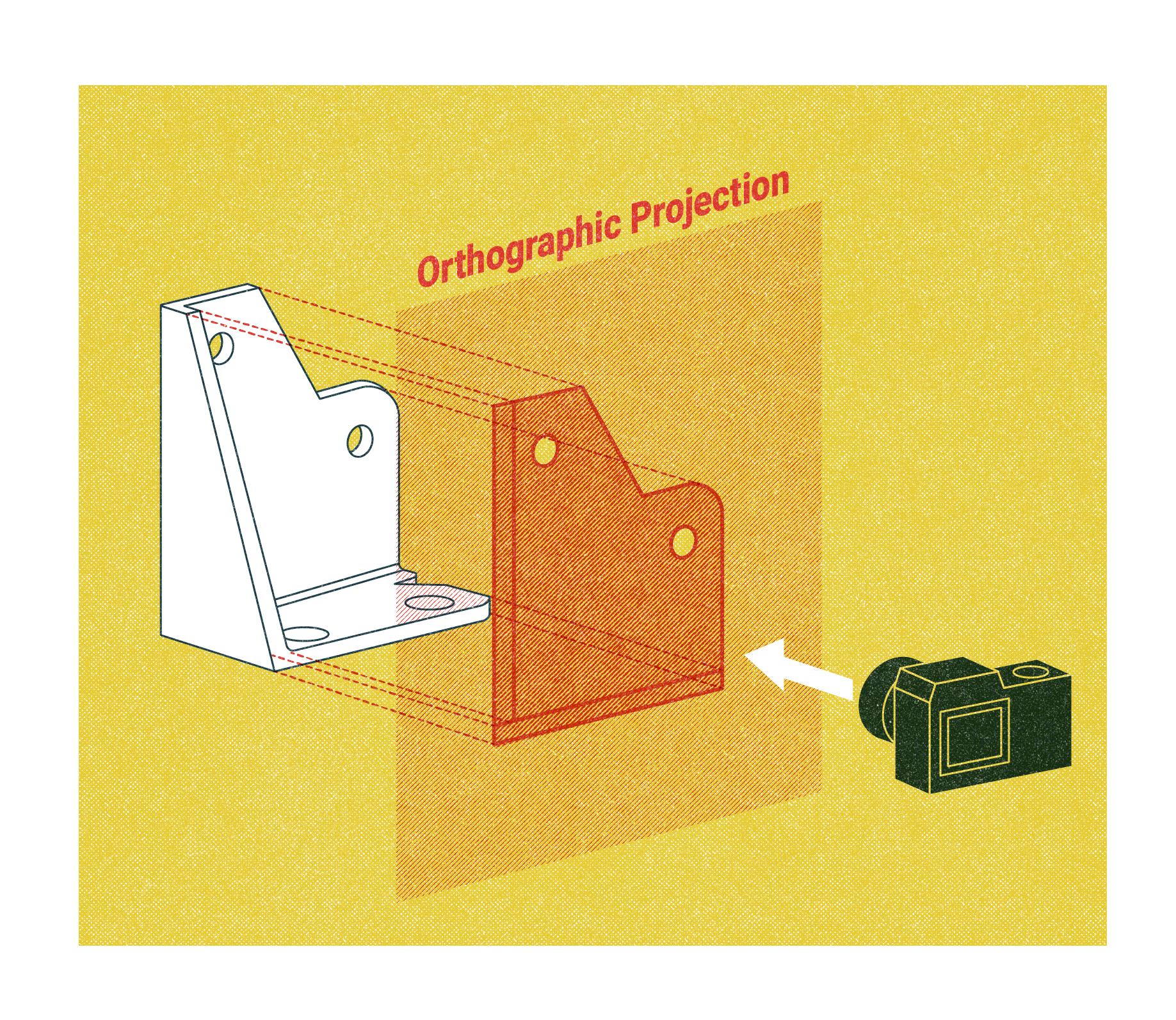
In the figure above, the parts defining edges are projected onto a plane parallel to the face of the part and between the part and the viewer. This is called third angle projection.
If the image was projected onto a plane behind the part in relation to the viewer, this would be first angle projection. Solid lines represent edges, which are visible from that view. Dashed lines are hidden lines that are not visible but are represented for clarity.
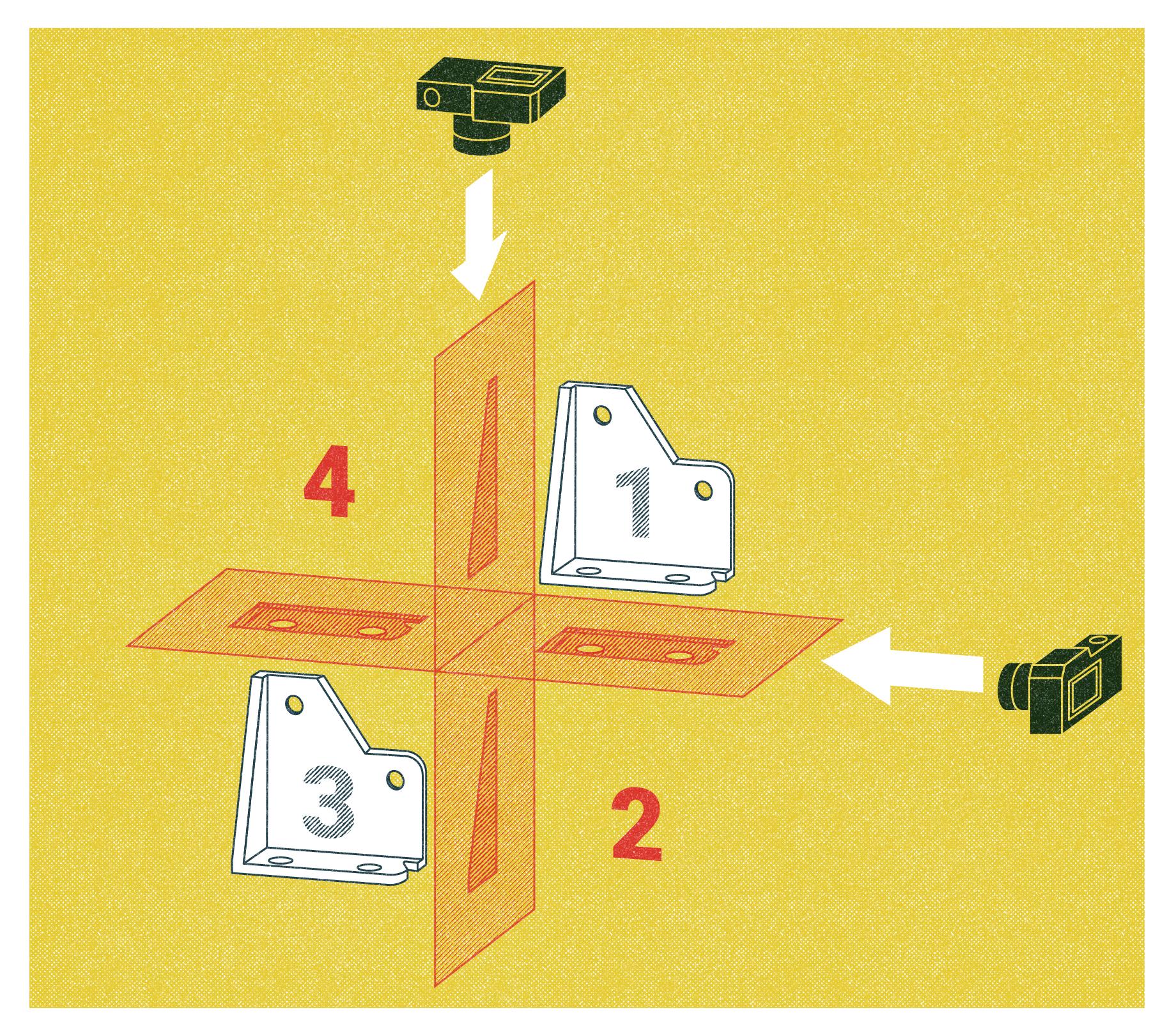
The term First Angle Projection refers to a four quadrant assimilation of planes in which the viewing direction is from the right and the top of the quadrants. If an object is placed in the first quadrant and lines are projected onto the adjacent planes, the projection would be from the back of the part in relation to the viewer. The First Angle Projection is primarily used in European countries.
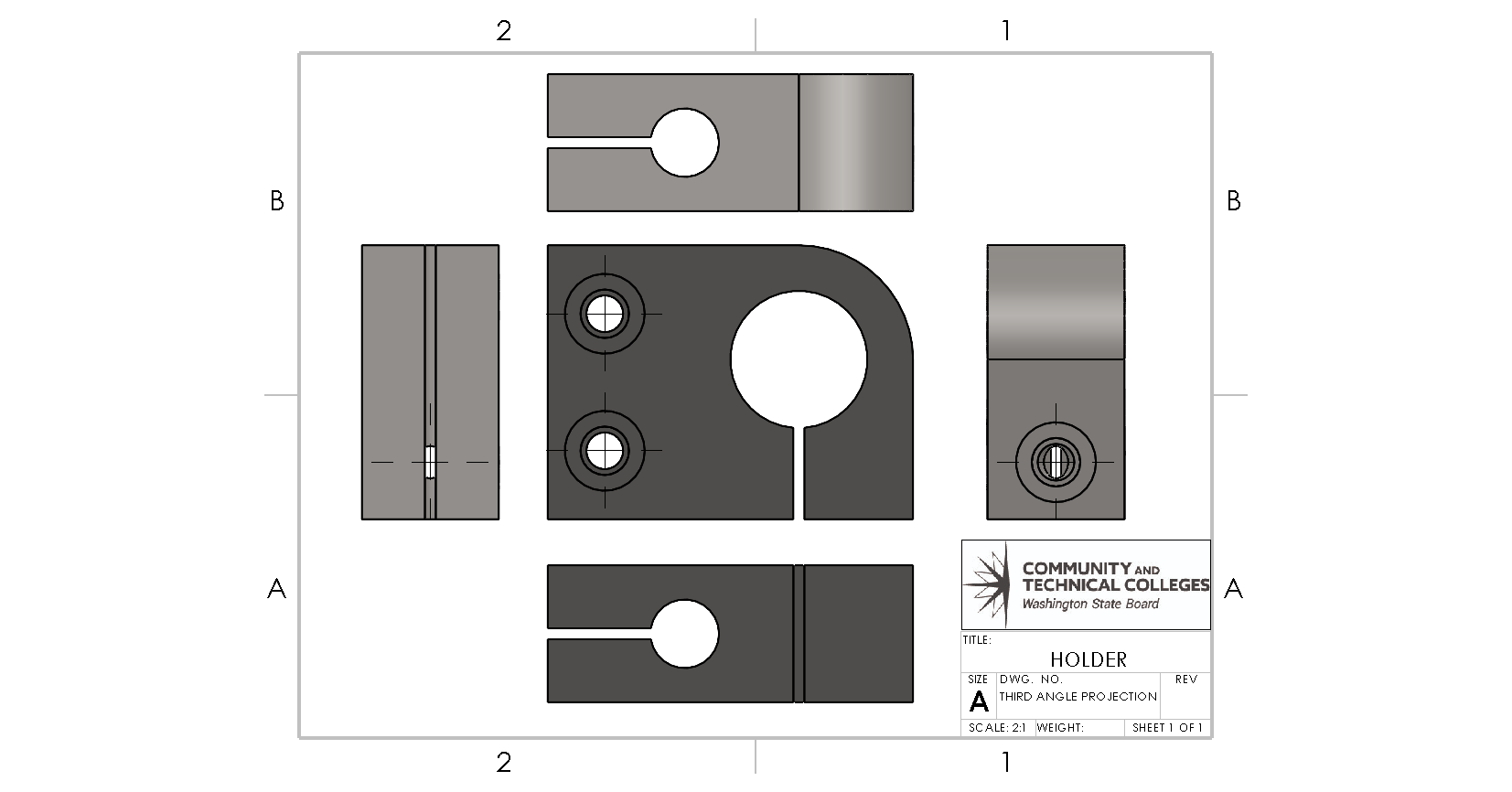
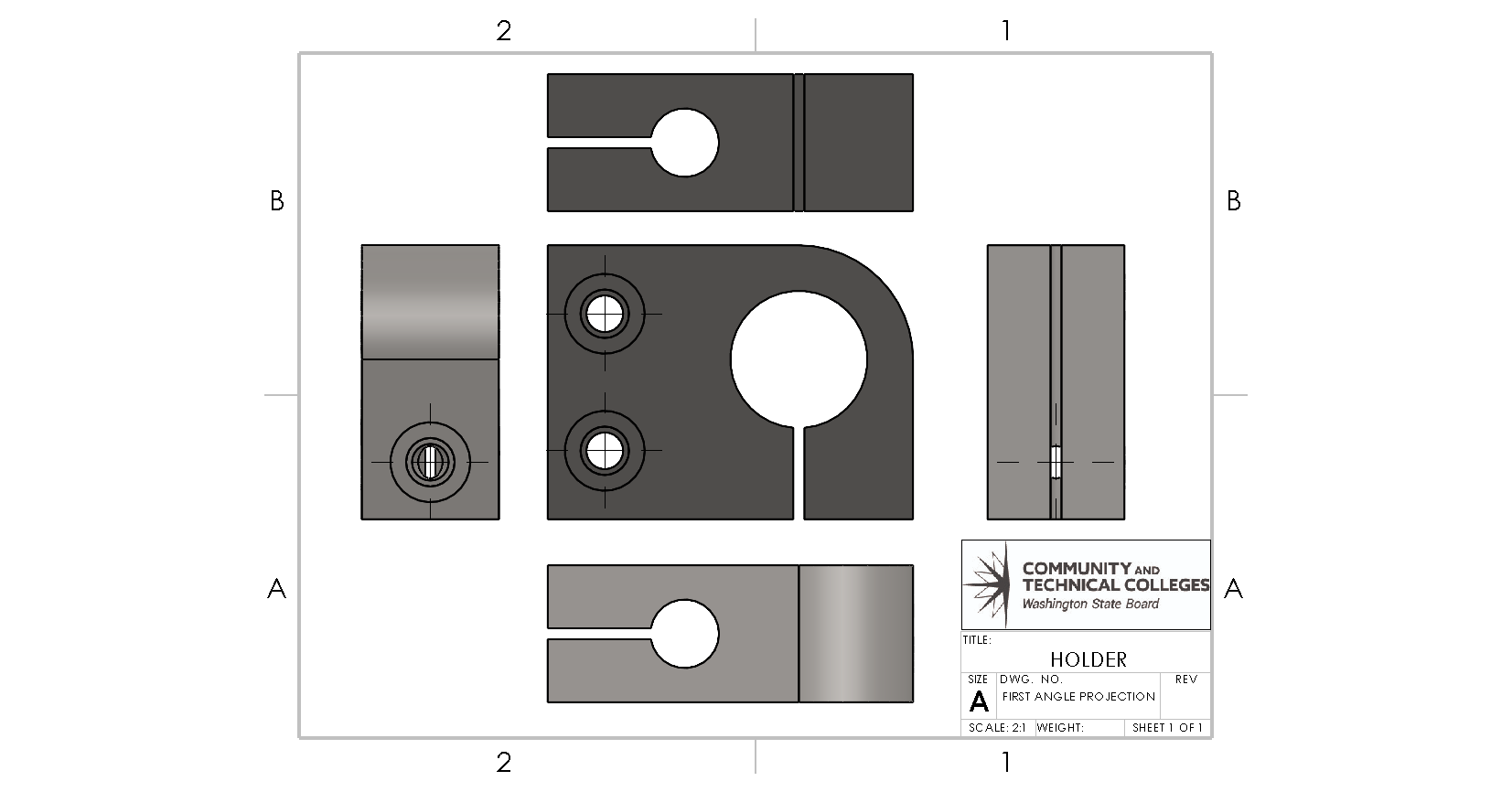
When an object is placed in quadrant three, lines are projected onto the planes between the object and the viewer. This is what is predominately used in North America.
3.3.5 Front view
One view is chosen to be the front view. This view usually communicates the most information about an object. Two more views are selected to better define the object in three dimensions. The TOP and RIGHT view are given primary consideration; however, the engineer may choose which views provide the most information
3.3.6 Detail View
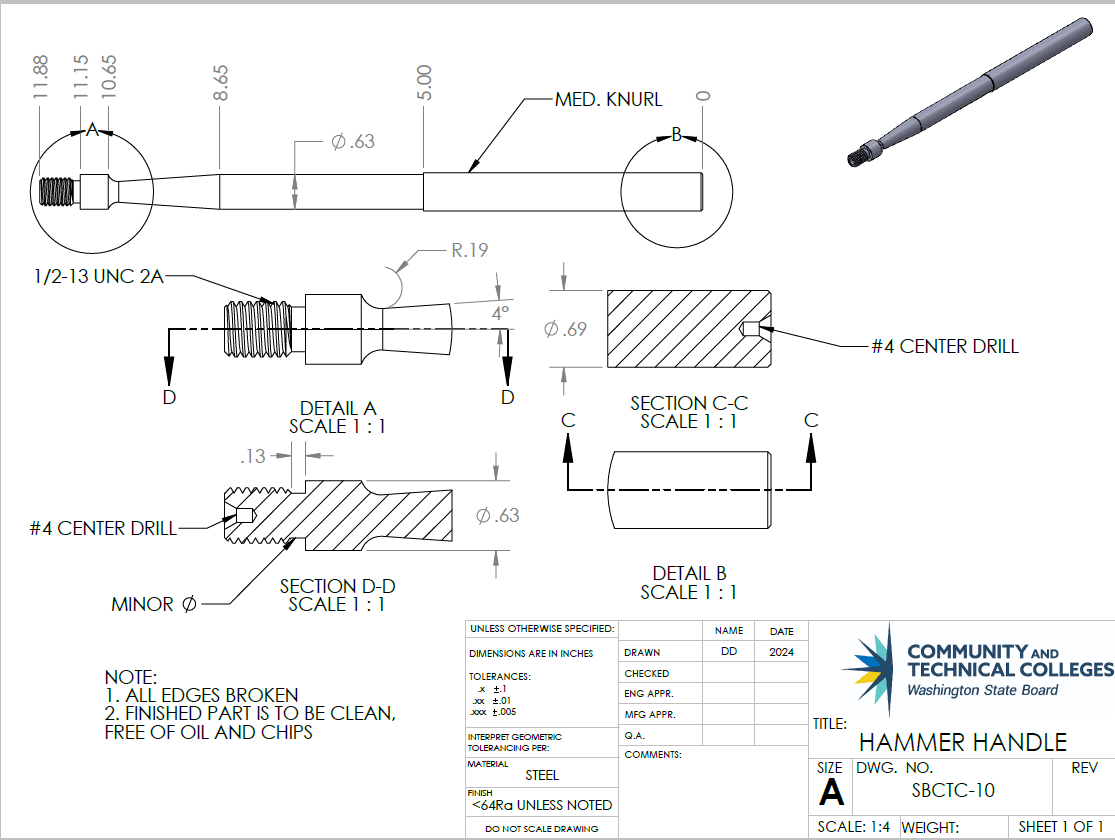
A detail view on a drawing provides a close-up of a selected section of a larger view. It can be especially useful when a large part has many important dimensions in a small area. Detail views can improve the readability of these measurements. Detail views have a circle outlining the area to be examined (see detail A enclosing the threaded end of the handle threads above). There is a letter attached to detail views as a method to align the two images’ information. The detail view is enlarged and provides additional space for dimensioning. The figure above has two detail views (A & B), allowing the engineer to accurately dimension both ends of the hammer handle.
3.4 LINES
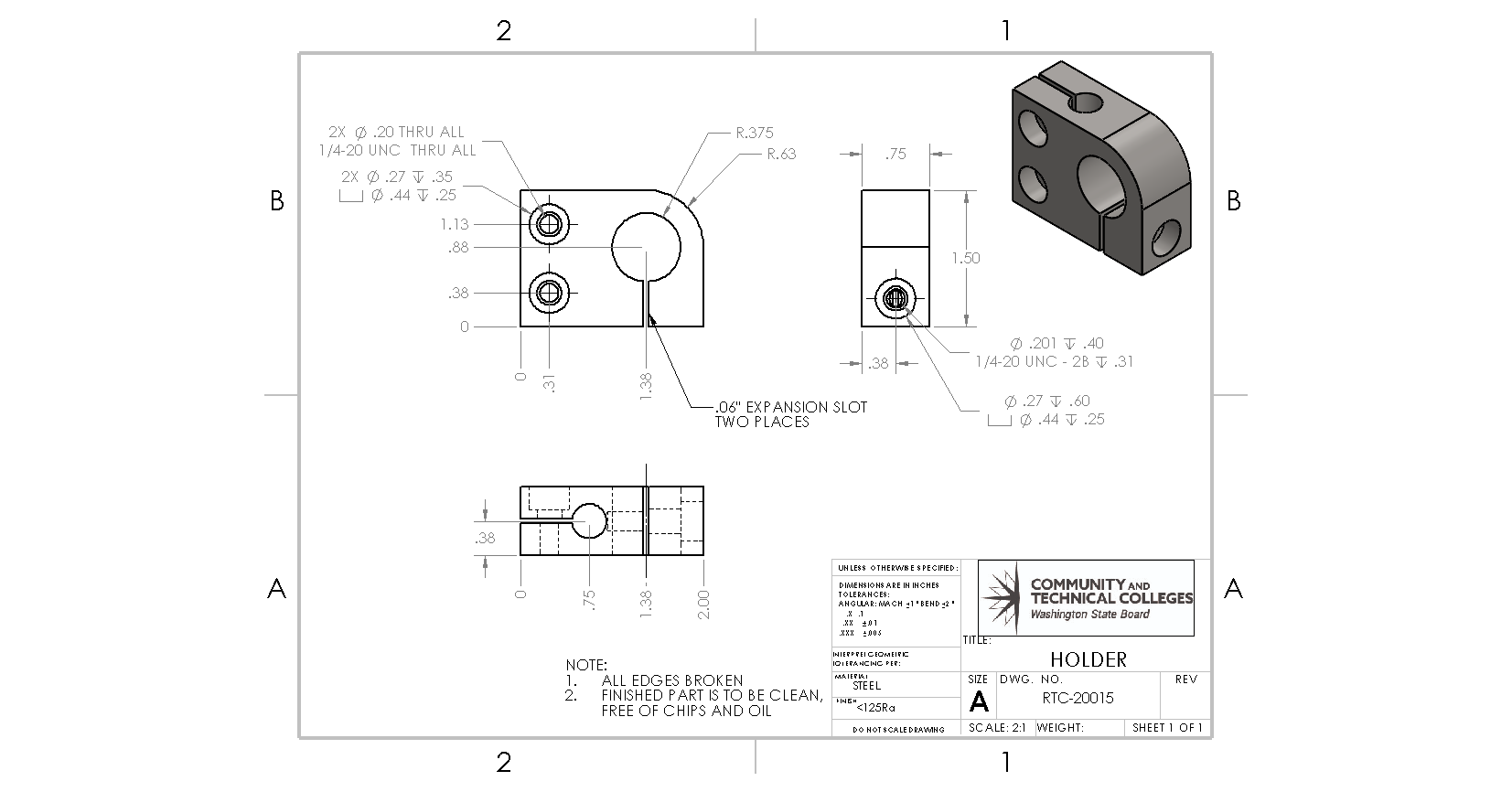
3.4.1 Solid Lines
Solid lines projected in any view are considered to be the lines visible from that view. In other words, all visible edges are projected onto the viewing plane.
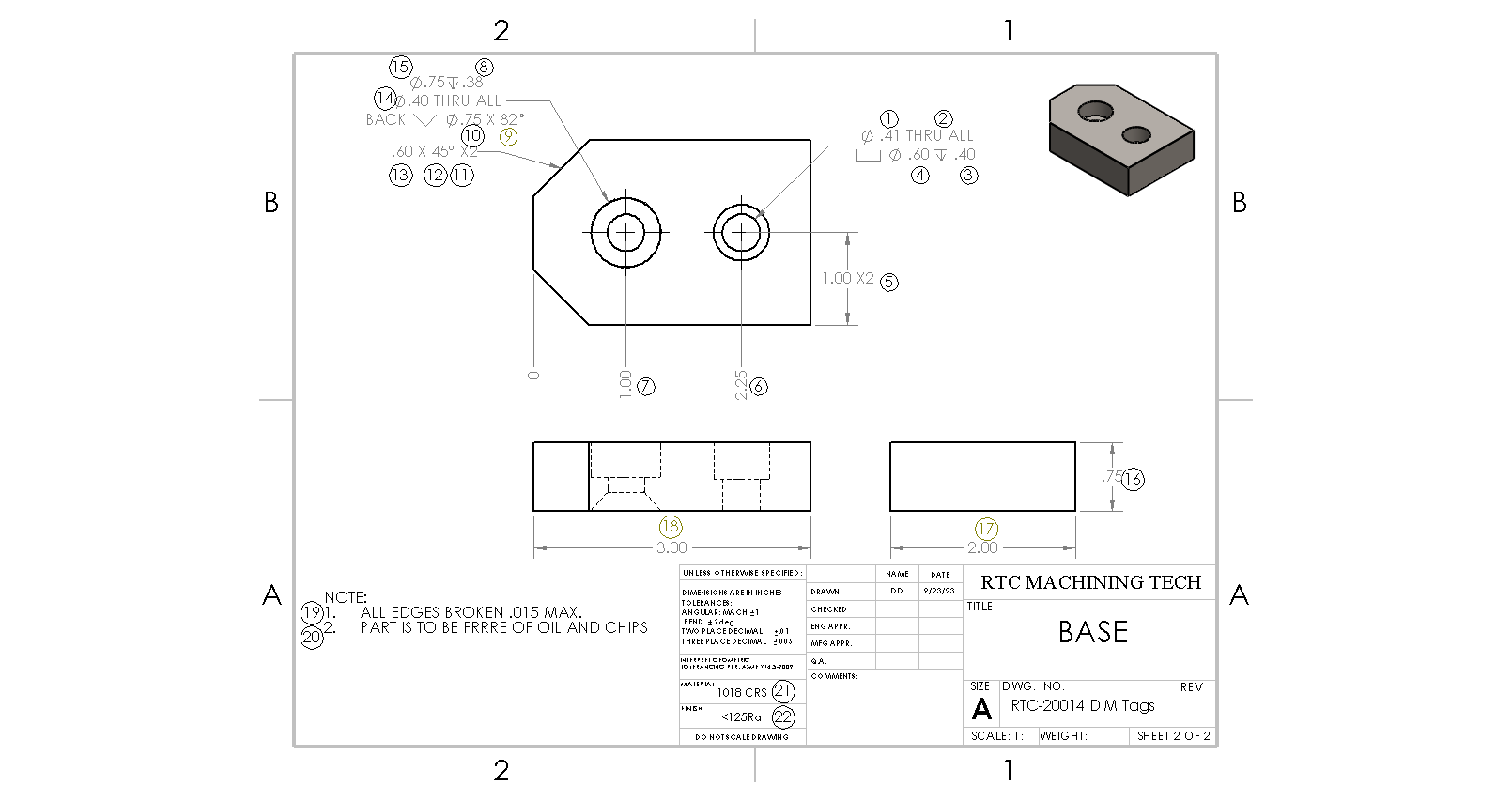
3.4.2 Hidden Lines
Hidden lines are feature lines which are not visible from the viewing plane and are represented by a broken or dashed line. They are either on the other side of the object or inside the object. Hidden lines are projected onto the view to provide useful information about a feature. In the above figure, the bottom left object uses hidden lines to help explain the hole features. The left hand hole has a countersink on the top surface and a counterbore on the bottom surface. This is a non-standard use of these features, so using hidden lines will help the machinist understand this hole feature better.
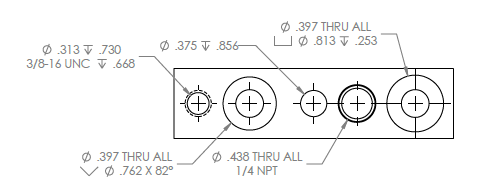
3.4.3 Leader Lines
A leader line in a drawing is a thin, continuous line that connects a feature in a drawing to text. In the above figure, a part has five different holes, all with specific information that details how a machinist must create the hole. The use of a leader line provided an easy to understand relationship between the text and the feature.
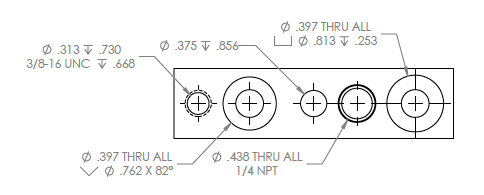
3.4.4 Center Lines
Center lines are thin, long-short-long lines that indicate the centers of symmetrical objects, arcs, and holes. They can also represent symmetry and paths of motion.
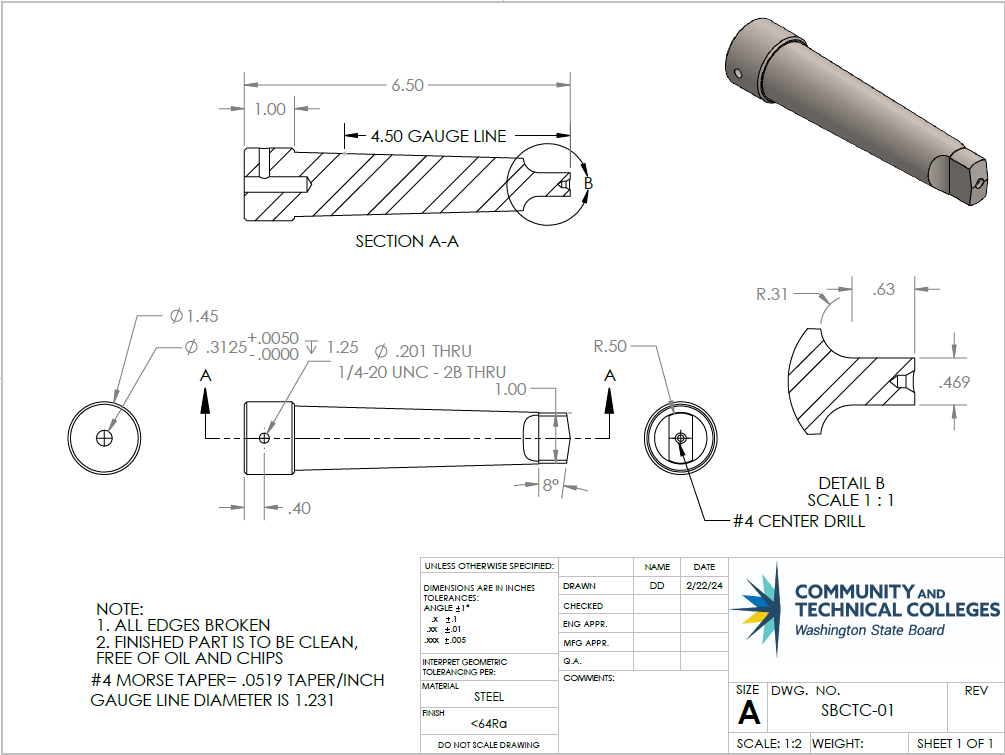
3.4.5 Cutting Plane Lines
Cutting plane lines are thick, dashed lines that run through the inside of an object to show where an imaginary cut has been made. Cutting plane lines allow the viewer to understand the orientation of a section view, by creating the insertion of this plane. In the image above, the cutting plane lines are denoted as A-A.
3.4.6 Section View
When parts become complex and solid or hidden lines can not express the detail necessary, section views are created using cutting planes. In the above figure, the cutting plane (A-A) is through the center of the part lengthwise and pointed up. The section view below the cutting plane represents what you will see at that instance.
3.5 Dimensions, Tolerance and Allowance
As a machinist, you will spend the vast majority of your day measuring, calculating, and verifying dimensions from a print. Using the proper equipment to obtain measurements and then comparing them to the engineer’s drawing is a large part of what we do. Here we will focus on obtaining the dimension from the print and determining what the tolerance is for our measured feature.
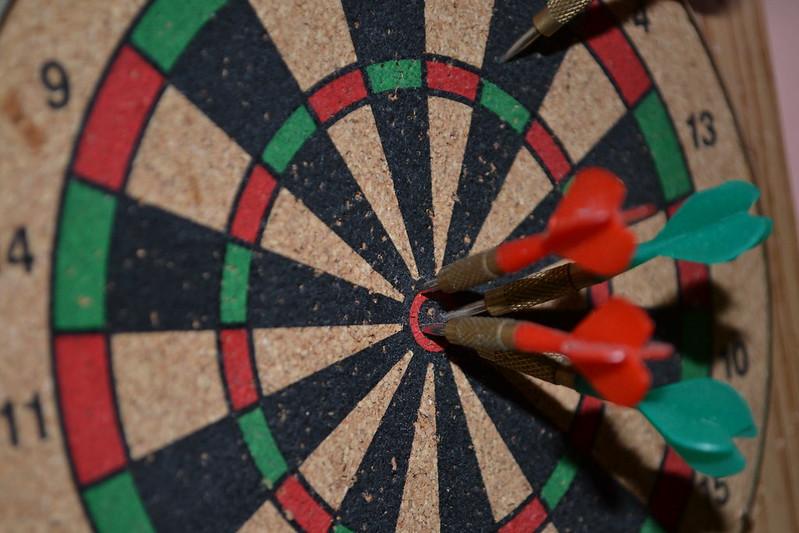
A Tolerance is the accepted amount of variation between part measured dimensions and the nominal dimension from the print. The center area of a dart board is called a bullseye. Any dart that lands within the bull’s eye will score points. Think of tolerance as a bull’s eye that is allowed to change size. If a part tolerance can vary by a greater amount, the bull’s eye can be larger, and any measurement that falls within that tolerance is acceptable. If the engineer requires a tighter tolerance for a dimension, the bullseye will be smaller, allowing less variance; however, any dimension that falls inside the tolerance is acceptable.
You may hear tolerance and allowance used interchangeably, but in fact, they are different. An Allowance is the engineered difference from nominal, which allows parts to function as necessary. If a slip fit needs to exist between a shaft and a hole, the engineer will use an allowance of .01” between the two part dimensions. In order to ensure the allowance is met, the engineer may allow a .005” tolerance to the nominal dimensions.
A Nominal dimension refers to the standard or intended size, value, or dimension of a component or part without considering variations or deviations that may occur due to manufacturing processes or other factors. It represents the theoretical or target value used as a reference point for design, analysis, and communication in technical specifications.
In simpler terms, the nominal value is the ideal or planned measurement, size, or characteristic that a part or feature is expected to have according to the design or specification. However, due to inherent variability in manufacturing processes and other factors, the actual measured values may deviate slightly from this nominal value. These deviations are taken into account using tolerances and allowances to ensure that the manufactured part is still within an acceptable range of functionality and performance.
All manufactured parts have inherent variations caused by many factors, such as work holding, tool holding, tool wear, human interaction with the system, temperature, and stock variations, just to name a few. There is no such thing as the perfect part. It is vital that you understand this principle because many hours can be wasted chasing this impossible standard. The machinist does not operate in the perfect world, but we do exist in the realm of allowed variation. The engineers who design the parts we make also understand this principle, and they design this variation into the part.
3.5.1 Overall Dimensions (OD)
Overall dimensions are the primary dimensions that define the overall size of the part in terms of length, width, and depth.

Dimensions that define the height, width, and depth of features or components provide important size information. Think of the overall dimensions as the smallest box in which the part will fit. This image becomes useful when a machinist must determine what size stock to make a part from.
When using terms to reference features of a part, such as length, width, and depth, there is room for uncertainty due to the numerous words in our vocabulary that may define the part shape we are referring to. Some of these terms are: thick, tall, wide, deep, long, and short, just to name a few. As an example, how would you define how tall a part is? Which dimension would you apply “tall” to? For this reason, standard terms such as length, width, and depth are used to define the overall size of an object if it is not cylindrical. Cylindrical size would be referred to as diameter and length.
Which side of the part gets which label? The figure above of a 1-2-3 block has labels on three sides. In this example. A defines length, B defines width, and C defines depth. Almost all parts have length, width, and depth, so they must be defined on a drawing. In practice, machinists are referencing a specific dimension on a print, and the feature it measures is illustrated for us. Our job is to understand what the feature is and then utilize measuring equipment to ensure it is within tolerance.
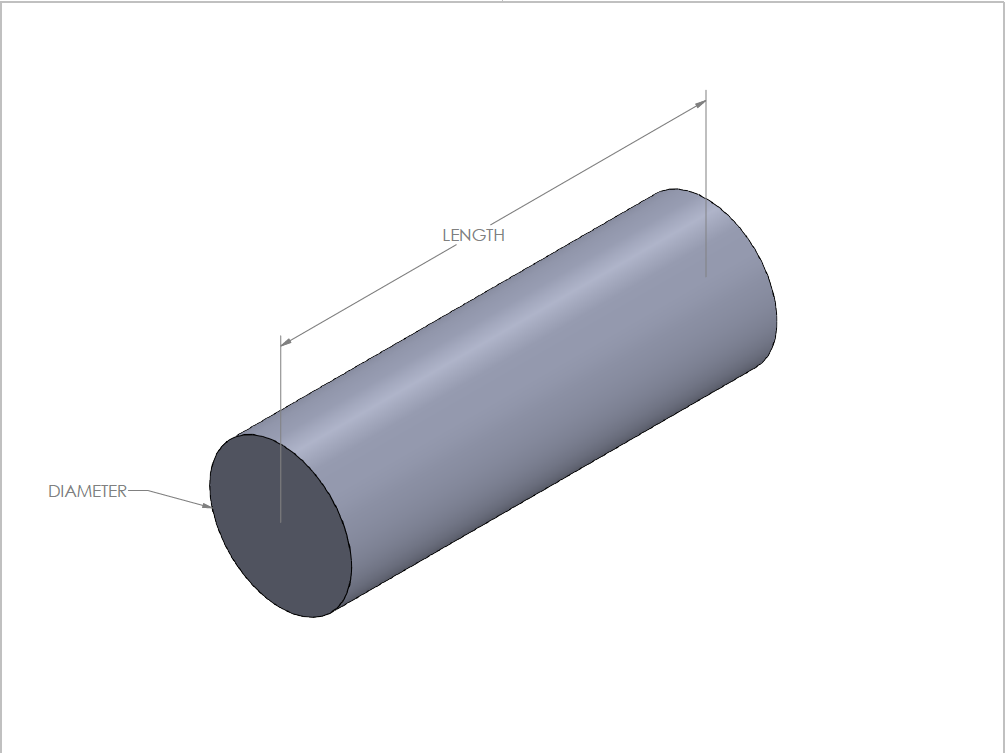
Items that will not have all three overall definitions will be cylindrical parts when diameter replaces width and depth. This is due to symmetry, where the diameter measures the same in width and depth.
Overall dimensions are linear dimensions that reference some sort of datum as a zero reference to measure from. In engineering and drafting, a datum is a reference point, surface, or axis on an object against which measurements are made.
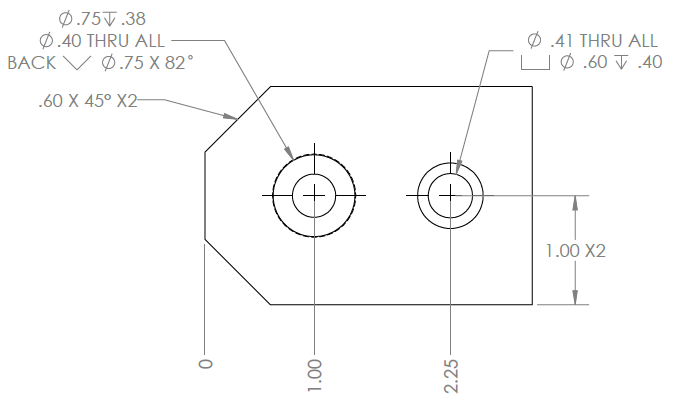
3.5.2 Diameter (Ø) Dimensions:
Diameter dimensions are critical for circular features, such as holes, shafts, and other cylindrical parts. The above drawing has several diameter dimension callouts, such as counterbores, thru holes, and countersink features. It is not uncommon for lathe operators to refer to OD dimensions as Outside Diameter dimensions.
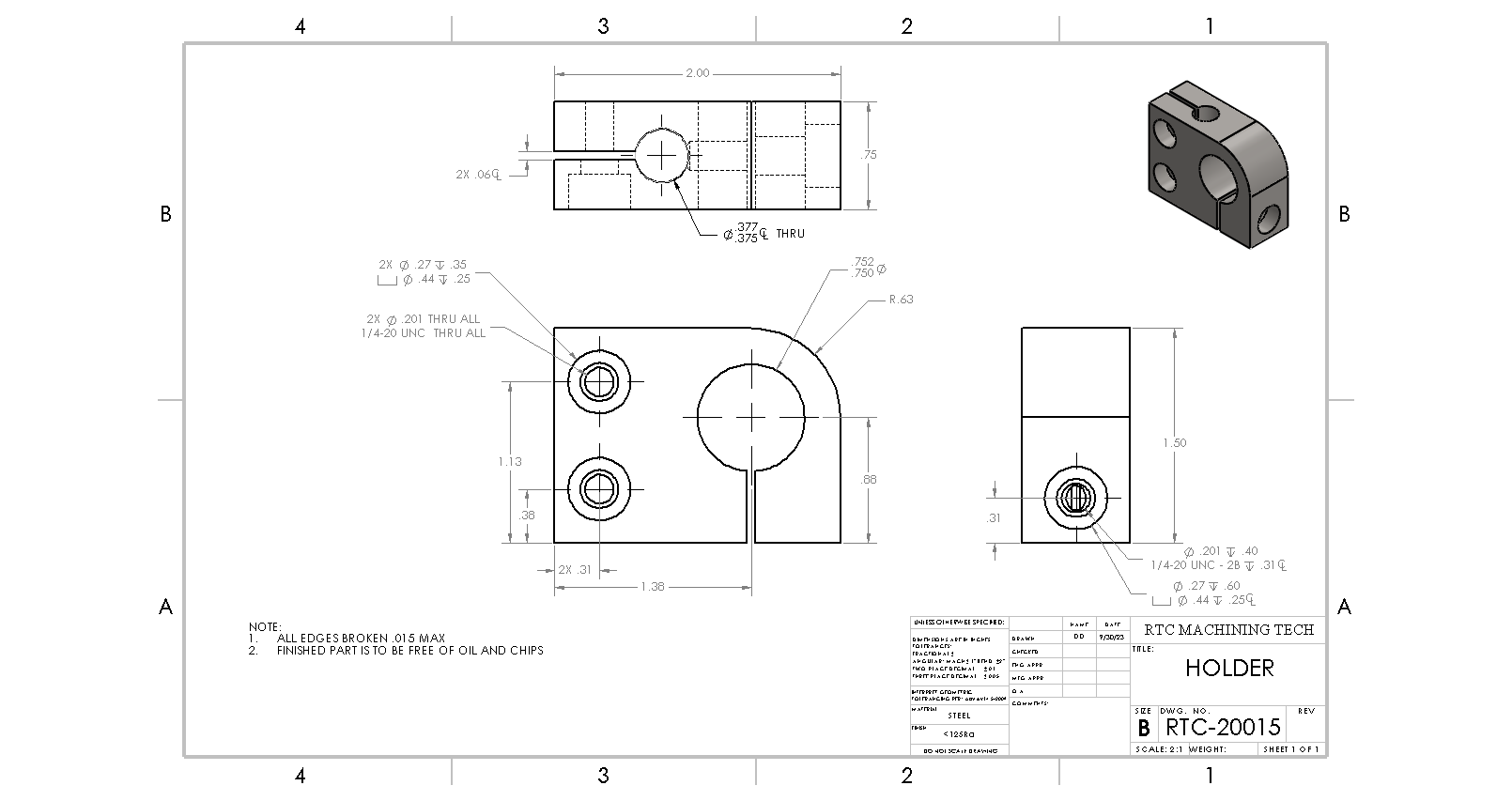
3.5.3 Radial Dimensions:
Radial dimensions define the distance from the center of a circular feature to a point on its periphery, often used for holes or circular cutouts. Radius callouts are used on arc type features, which do not constitute a full radius or circle. As simple as radius and diameter seem, they are two of the most confused dimensions used.
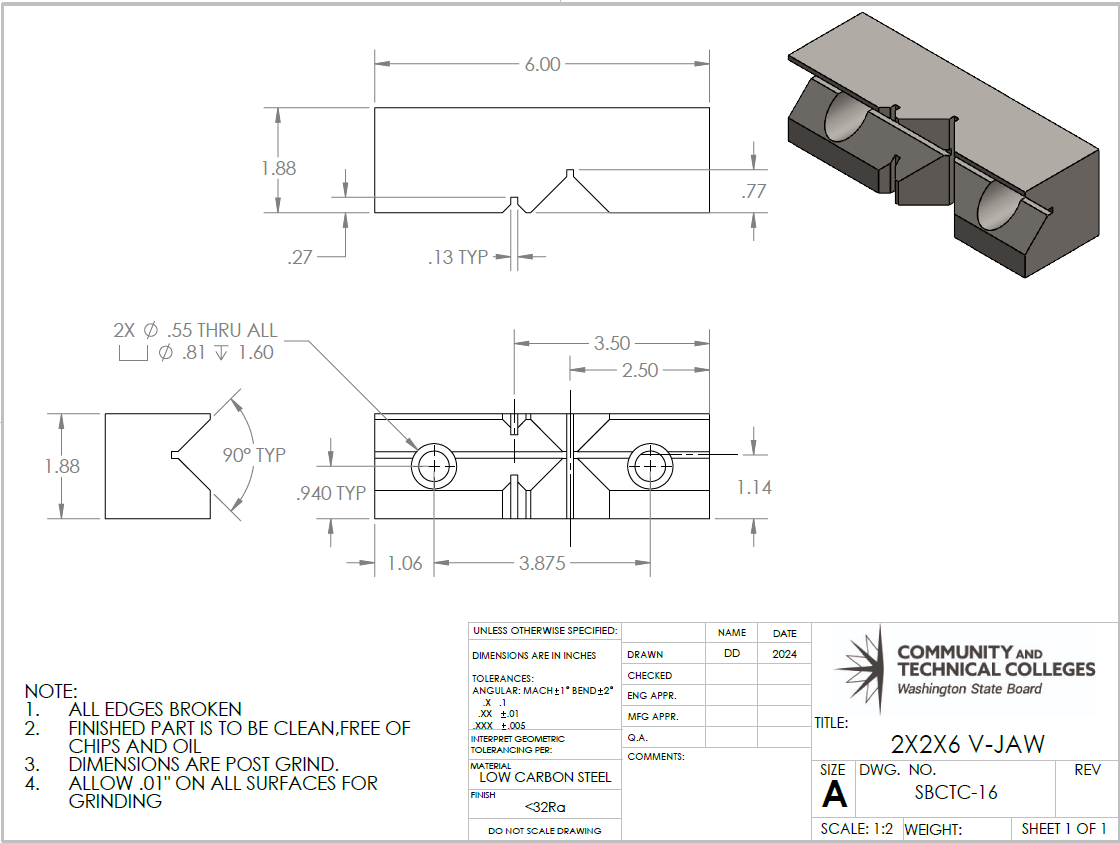
3.5.4 Angular Dimensions:
These dimensions define the angle between two lines or surfaces, which are crucial for specifying orientations and alignments. Countersink features use angular dimensions to define the fastener’s included angle used in the feature. The deep V-cut on the vise jaws is defined as 90° on the print with the added note of “TYP.” TYP means typical and can be applied to similar areas on the print. The engineer could have also used “3X” to specify that the 90° appeared in three places on this drawing.
3.5.5 Center-to-Center Dimensions:
Center-to-Center dimensions define the distance between the centers of two features, often used for holes, screws, or bolts. In the drawing above, the counterbores used to mount the jaw to a vise have their locations relative to each other called out as center to center.
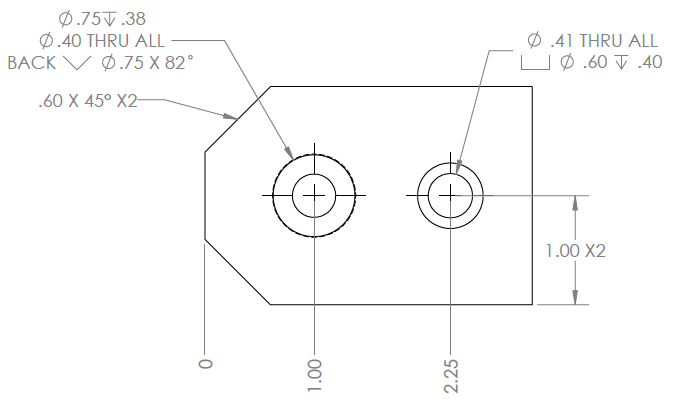
3.5.6 Chamfer Dimensions:
A chamfer is a sloped or angled edge between two connecting surfaces of a part. It can be used on either an internal or external edge. Dimensions specify the size and type of chamfers on the edges or corners of a part and usually reference an angle and length. The above parts have a 45° angle measuring .60” in length.
3.5.7 Hole Patterns and Spacing Dimensions:
These dimensions define the arrangement and spacing of holes in a pattern, often specifying the distances between holes. Hole patterns or bolt hole circles (BHC) have a diameter that the holes are centered on and then a number of holes evenly spaced about that circle.
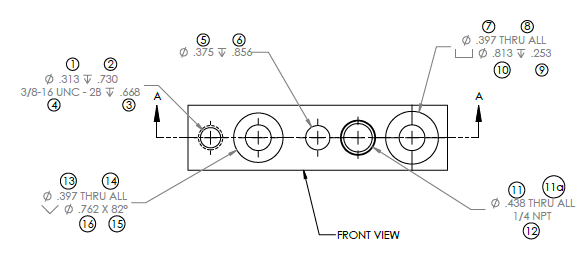
3.5.8 Counterbore Dimension (⌴):
A counterbore is a blind hole that does not go through the part with a depth and diameter designed to house the head of a fastener so as to not sit above the face of the part. The counterbore symbol (⌴) needs both a depth and a diameter (⌀) DIM to establish its features. The depth of the counterbore is prefaced with a symbol that looks like a “T” with an arrow at its base. Since the counterbore is created to house a fastener, there will also be a thru hole diameter called out. In the figure above, DIM tags 7 through 10 define a counterbore feature.
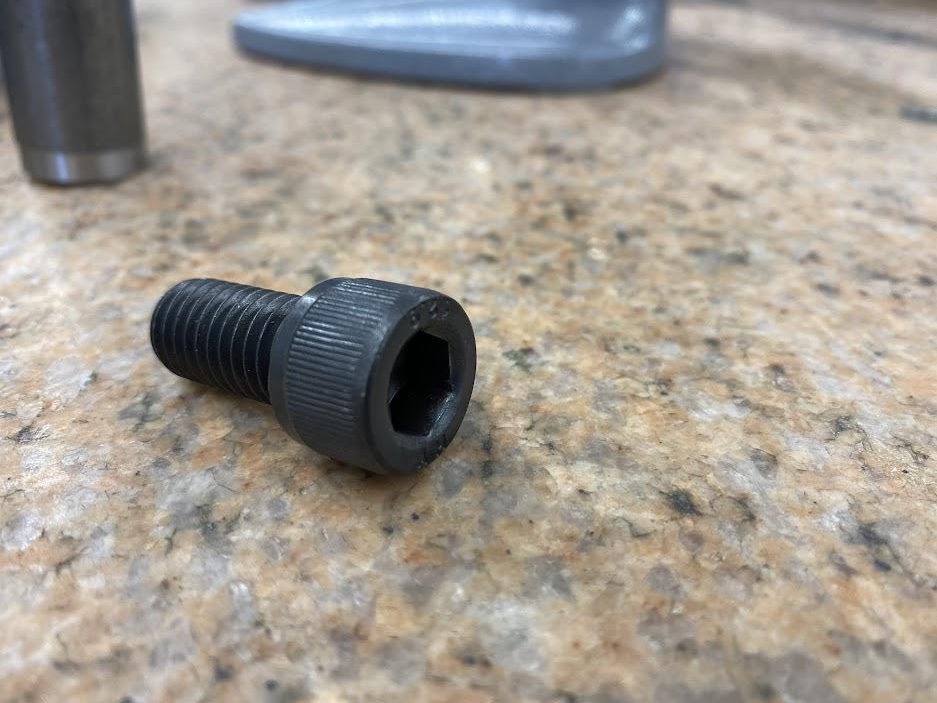
The above socket head cap screw is used extensively in many industries and is a common feature in many parts we make. There are a few similar headed screws, such as the Button Head Cap Screw (BHCS), which has a lower profile, but the SHCS is most common.
3.5.9 Countersink Dimension (⌵)
A countersink is a hole feature that provides a flat head screw to sit flush with the face of a part.
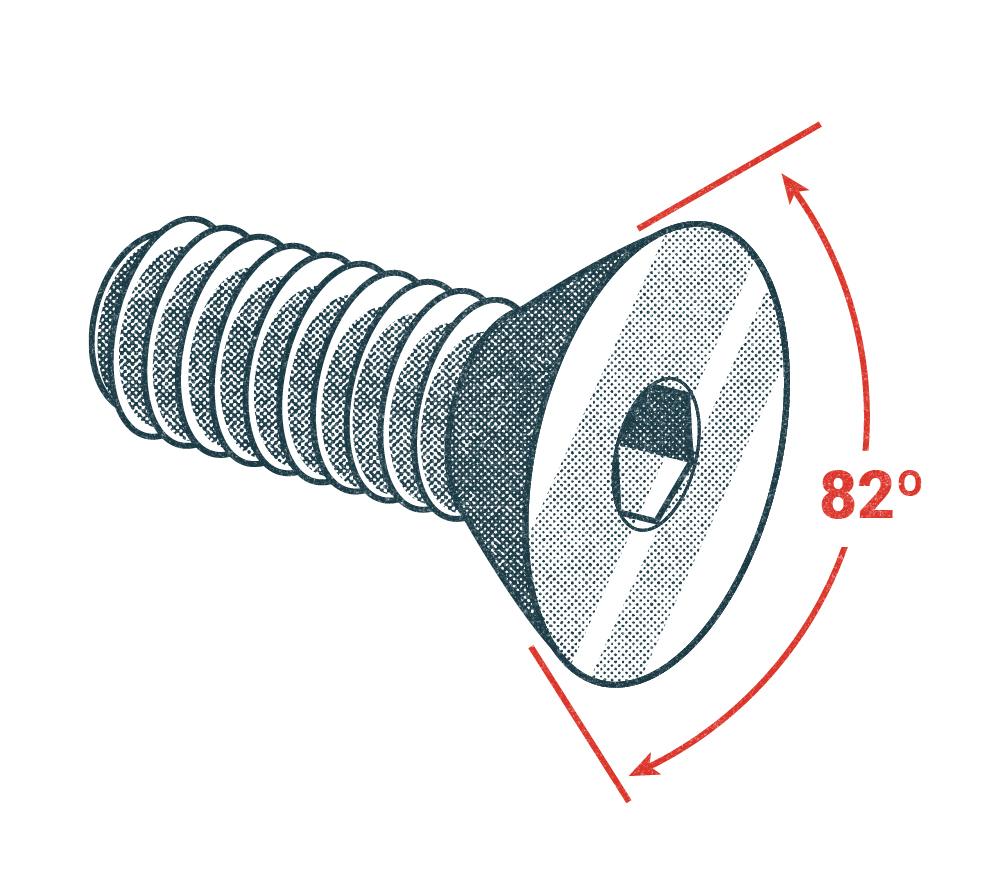
Inch flat head screws have an 82° angled head, and metric use 90° angle heads. There are some aviation applications where there are 100° flat head screws, but the most common hardware is 82°. This hole callout feature requires the angle and diameter to be specified. Measuring these features requires a chamfer gage or optical comparator. Verifying the angle is just a matter of measuring the tool used to make the feature. In the figure above, DIM tags 13 through 17 define a feature with a countersink.
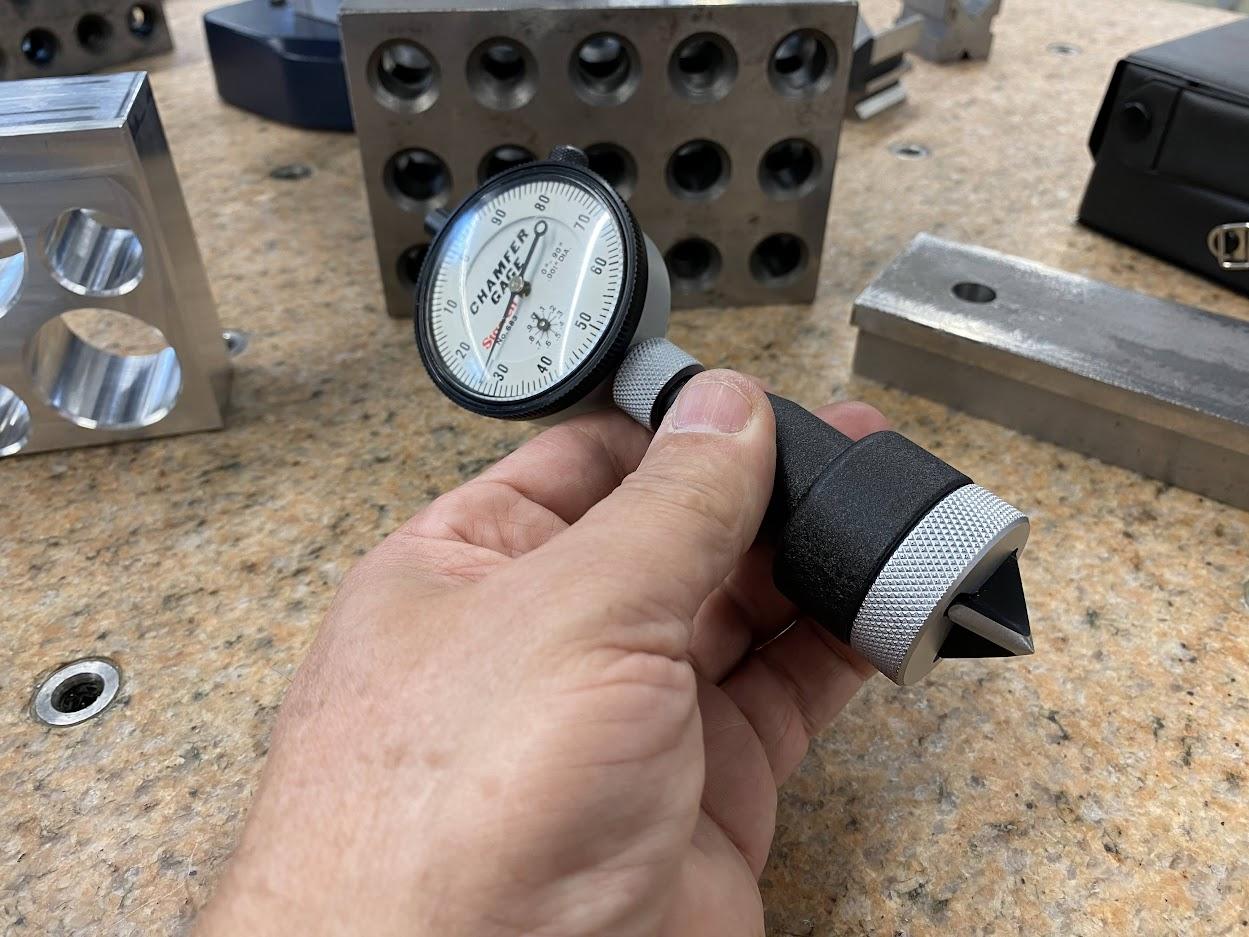
A special piece of inspection equipment can be used to take diameter readings on counterinks to ensure the diameter is within tolerance (more on this in chapter 4, Metrology).
3.5.10 Threaded Hole Callout
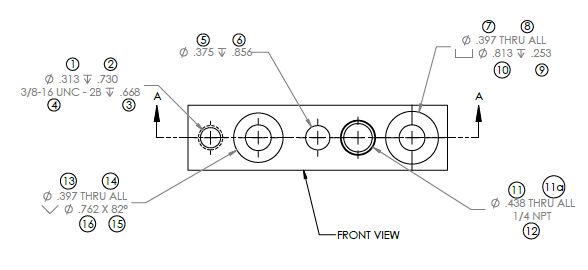
A threaded hole callout presents all the hole feature information using a series of symbols, numbers, and text that you must decipher. Threaded hole callouts must list the following information:
- Thread series (Inch, metric)
- UNC (Unified National Coarse)
- UNF (Unified National Fine)
- Metric (M)
- Pitch (how far the fastener advances in one revolution)
- Major diameter (½’, ⅜”, ¼”…)
- Class of fit (2A, 2B…)
- Tap Drill diameter and end condition (thru or depth).
- Thread end condition (thru or depth).
In the figure above, DIM tags 1 through 4 define a threaded feature. The feature is a blind ⅜-16 UNC 2B threaded hole. DIM 1 defines the tap drill size used for the thread (.313”). This is a 5/16” (.3125”) drill expressed in three decimal places. DIM tag 2 defines the depth of the tap drill hole at .730”. It is important to note that this is the depth of the full diameter, not the depth to the drill tip, since the conical drill tip portion of the hole is unusable for threads. DIM tag 4 states the actual thread to be cut into the drilled hole; ⅜-16 UNC – 2B. And lastly, the end condition of the threads is .668” depth. The depth symbol is in the shape of a capital T with a V at the bottom. This depth symbol will be used on all features that do not pass through the part.
3.6 Surface Texture/Finish
Figure 3.31
Surface Finish Comparison Standards

All manufacturing processes create tooling marks on the finished part. If you create a snowman in the front yard, you will leave behind an indentation where your gloves packed the snow together. If you are from warmer climates, maybe you made sand castles on the beach by packing wet sand into a bucket and then turning it over to leave a bucket shaped mound. Any marks from inside the bucket transfer onto the sand that was molded from it. Or maybe you notice the pattern left behind by the vacuum cleaner on a nice plush carpet. That’s right, that’s a surface finish. Manufacturers must create the correct surface finish as per the engineer’s drawing.
The above figure has a sample surface finish that an operator must examine and compare to the tooling marks on the finished part. Both metric and inch Ra (Roughness Average) scales are listed on either end of the samples. The tooling mark samples are some of the most commonly used equipment for reaming, grinding, milling, and turning. Grinding and lapping create the finest surface finishes, and those processes are usually used to gain those types of results.
3.6.1 Units of Measure
Surface texture or roughness is a very fine definition because the tools that tools leave behind are usually small enough that you can not catch a fingernail on them. The symbol (µ) meaning micro is used to express a micro inch (µin) or a micrometer (µm), reflecting a millionth of an inch (.000001 inch) or a millionth of a meter (0.000001 meter). This is small stuff and may not be used in all industries. Aviation and the medical field use it extensively due to the very nature of the product. For example, if you send a part out for anodizing and the surface finish is out of tolerance, the anodized surface will magnify any blemish, resulting in scraped parts.
The title block will call out the surface finish/texture if it applies, and the tolerance is expressed in maximum allowed tolerance. For example, if the print calls out a surface finish of 32 Ra µin, then any number less than 32 is acceptable.
3.6.2 Roughness Average (Ra)
Surface finish roughness average (Ra) is a common unit of measurement for surface roughness. It’s the arithmetic average of the heights of the microscopic peaks and valleys across a surface. This requires a special piece of measuring equipment called a surface profilometer. A surface profilometer is used to measure the surface texture of a part.
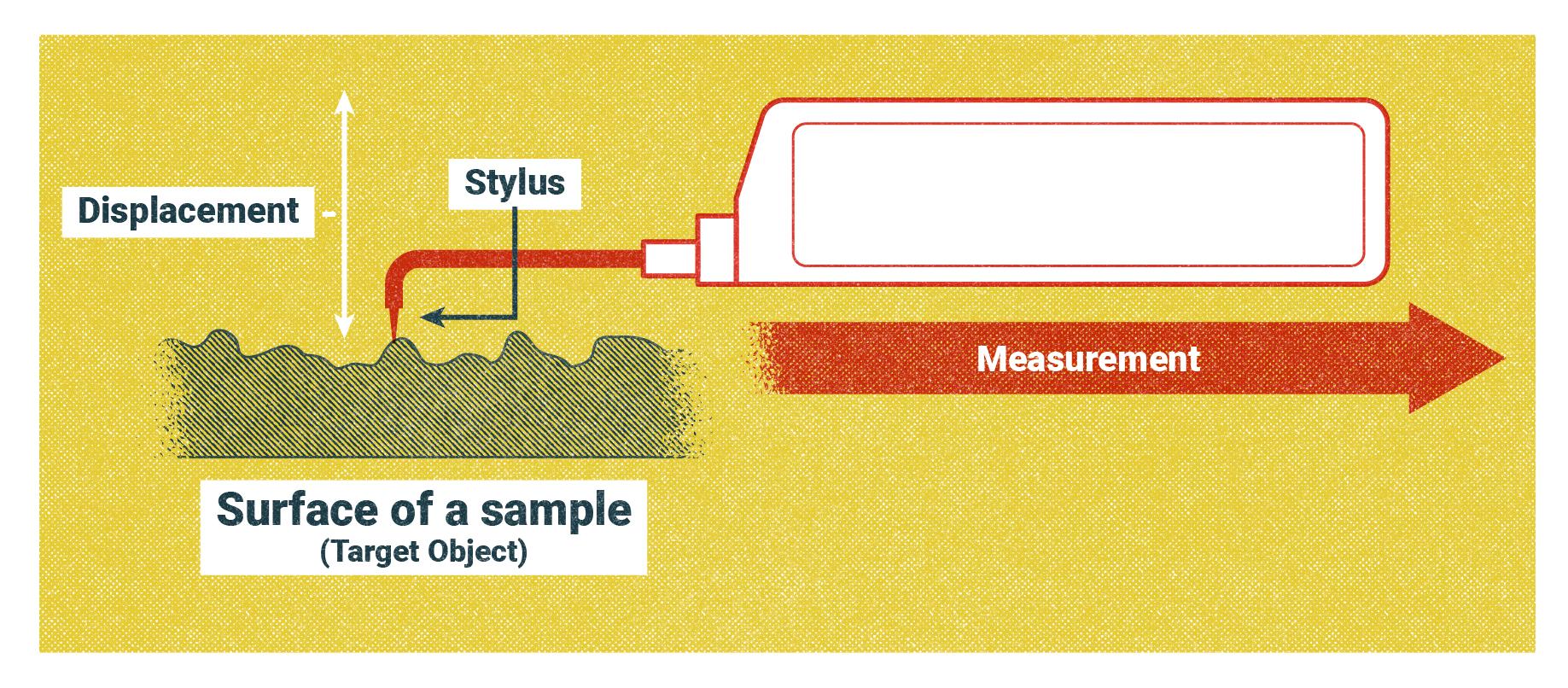
A surface profilometer has a very fine needle that is pulled across the surface to be measured. The needle and measuring equipment are sensitive enough to measure the peaks and valleys found on the surface. The Ra is expressed as a function of the length along which the needle has traveled, i.e., .250” by the maximum and minimum travel of the needle. How this functions is not necessary to understand; just know that it is an average of the length of travel. The travel of the meter can be varied, and where you place the needle is important to the final reading.
3.6.3 Symbols
The basic symbol used for surface texture is (✓), a rather simple check mark. The purpose of surface texture marks is to call out specific surfaces on the print for which the surface finish is specified.
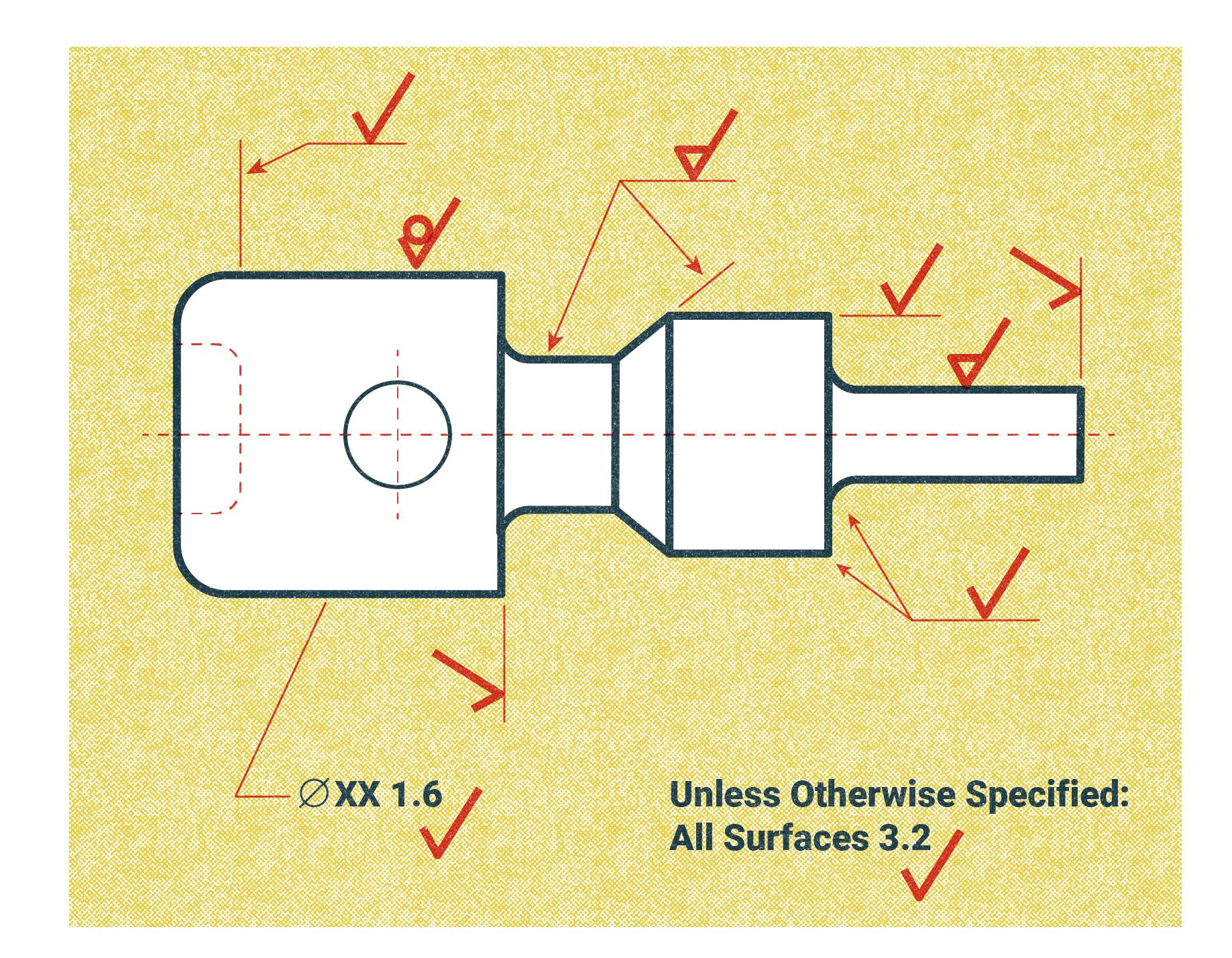
The scope of all the surface finish symbols from the figure above have different meanings, the purpose here is to demonstrate how they will be shown in the drawing area if a specific finish is needed on a surface.
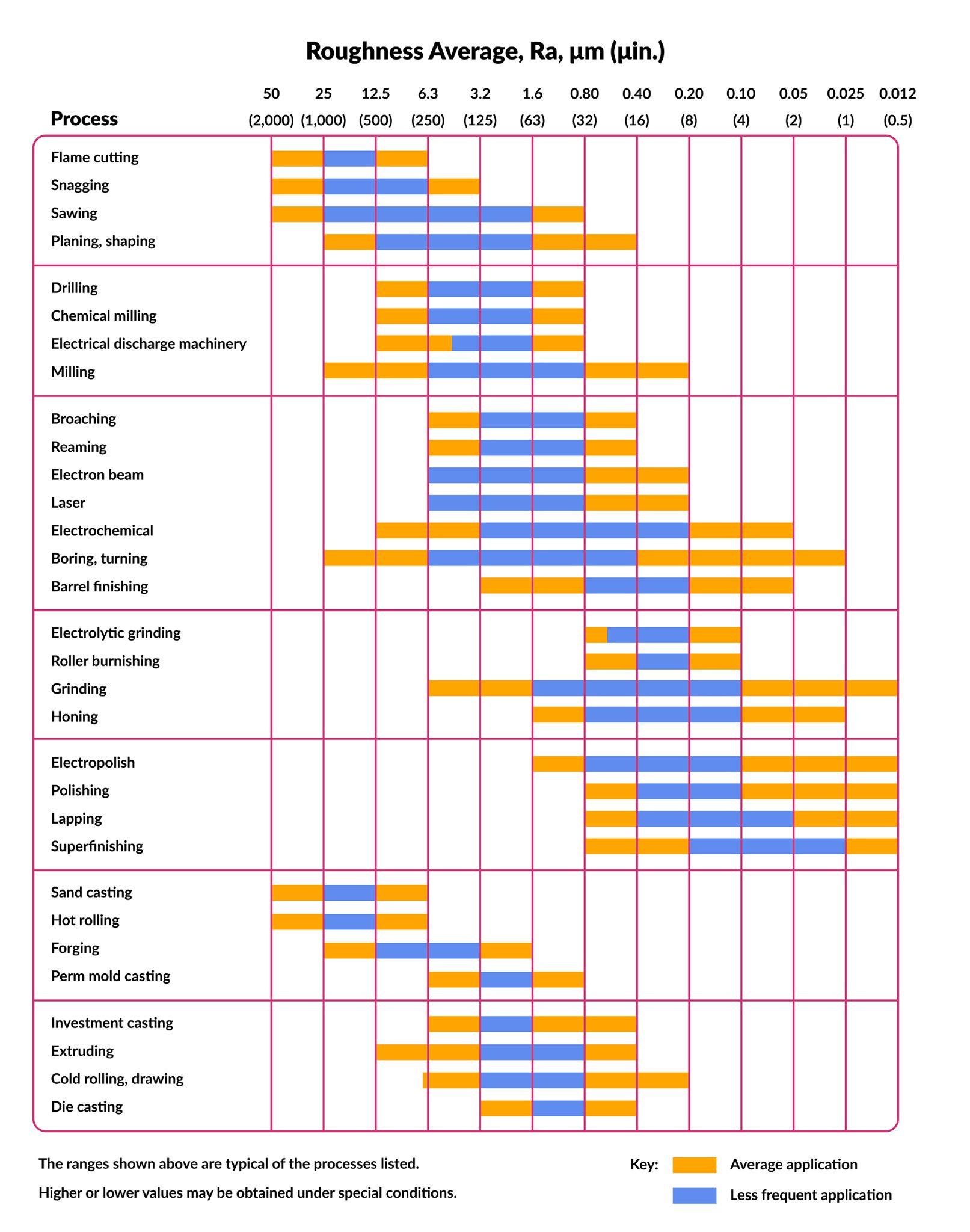
The figure above is a common graphic found in industry. The graphic tells us several things about surface finish. This is a basic two-axis diagram where the top section represents desired surface finishes in both metric and inch. The inch callout is in parentheses.
The vertical left side column demonstrates which manufacturing process is capable of creating the desired finish. Since a 32 Ra µ in callout is most common, (µ in spoken “micro inch” and is one millionth of an inch) notice which processes permit such a finish. Since most of our work is centered around lathe and mill work, see where those two processes correspond. There is a bar with a dark portion and a lighter portion, where the dark section indicates the average application and the lighter section indicates a less frequent application. In realistic terms, this means you must monitor the finish tool that creates the surface finish to ensure it is performing optimally.
Table 3.2
Ra Preferred Values
μm |
μin |
μm |
μin |
μm |
μin |
0.012 0.025a 0.050a 0.075a 0.10a 0.125 0.15 0.20a 0.25 0.32 |
0.5 1a 2a 3 4a 5 6 8a 10 13 |
0.40a 0.50 0.63 0.80a 1.00 1.25 1.60a 2.0 2.5 3.2a |
16a 20 25 32a 40 50 63a 80 100 125a |
4.0 5.0 6.3a 8.0 10.0 12.5a 15 20 25a … |
160 200 250a 320 400 500a 600 800 1000a … |
Note. The entire scale of surface finish numbering presented in a table with the smallest on the left and the largest on the right. 1, 2, 4, 8, 16, 32, 125, 250 and 500 are indicated as the recommended surface finish callouts for the micro inch scale (Jones et al., 2004, Table 3, p. 734).
The above graphic has all the preferred values for the Ra scale in both metric and inch, with the superscript a representing the recommended values.
SUMMARY
The ability to read and understand an engineer drawing as well as the vocabulary used will greatly benefit the student who wishes to join the manufacturing industry. This chapter has provided a basic understanding of the most common information found on production drawings.
REVIEW QUESTIONS
- Explain the primary sheet size that all others are multiples of.
- Define the two major areas of a drawing.
- Explain which detail view is chosen for the “front” view on a drawing.
- State the type of view is created by projecting visible lines onto a viewing plane.
- Which two entities govern the inch and metric standards for prints?
- What type of line connects a dimension to the feature on a print?
- Define orthographic projection
- Explain the 32 µin RA surface finish
- Define specific hole call out features.
- Where is the tolerance information located on a print?
- Explain the dimensions found on a counterbore callout.
- Why are hidden lines used on a drawing?
References
American Society of Mechanical Engineers. (2013a). ASME Y14.1-2012: Decimal inch drawing sheet size and format. ASME.
American Society of Mechanical Engineers. (2013b). ASME Y14.3-2012: Orthographic and pictorial views. ASME. https://www.asme.org/codes-standards/find-codes-standards/y14-3-orthographic-pictorial-views/2012/print-book
American Society of Mechanical Engineers. (2015). ASME Y14.2-2014: Line conventions and lettering. ASME. https://www.asme.org/codes-standards/find-codes-standards/y14-2-line-conventions-lettering
American Society of Mechanical Engineers. (2019). ASME Y14.5-2018: Dimension and tolerancing. ASME. https://www.asme.org/codes-standards/find-codes-standards/y14-5-dimensioning-tolerancing/2018/print-book
American Society of Mechanical Engineers. (2020a). ASME B46.1-2019: Surface texture (surface roughness, waviness, and lay). ASME. https://www.asme.org/codes-standards/find-codes-standards/b46-1-surface-texture
American Society of Mechanical Engineers. (2020b). ASME Y14.1-2020: Drawing sheet size and format. ASME. https://www.asme.org/codes-standards/find-codes-standards/y14-1-decimal-inch-drawing-sheet-size-format/2020/print-book
Jones, F. D., Ryffel, H. H., Oberg, E., McCauley, C. J., & Heald, R. M. (2004). Machinery’s handbook (27th ed.). Industrial Press.