Chapter 5 Part 3 : Benchwork
5.10 Workholding
Workholding is the process of securing and holding a workpiece firmly in place during various machining operations. The primary goal of workholding is to ensure that the workpiece remains stable and properly positioned while it undergoes cutting, shaping, drilling, milling, or other machining processes.
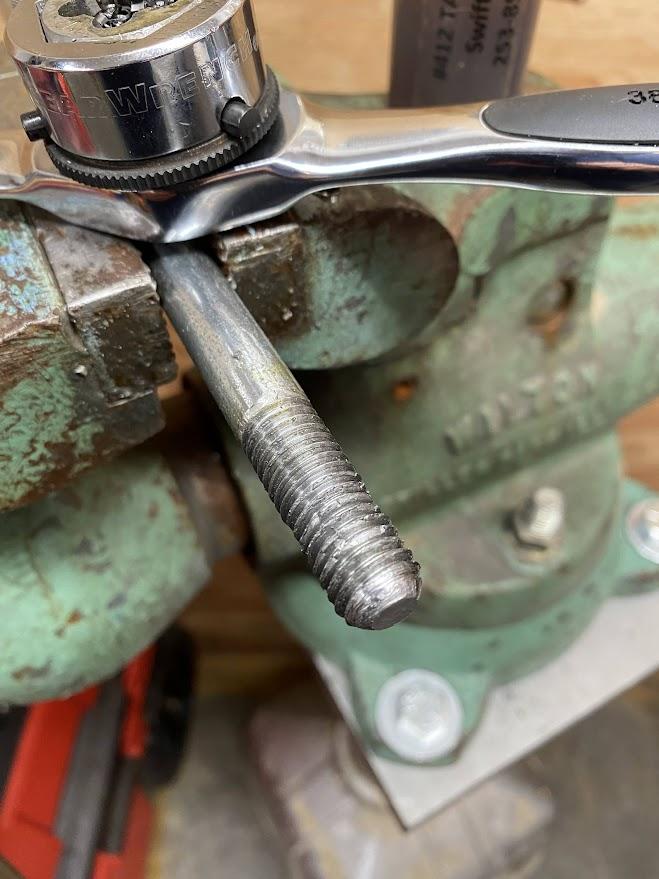
Benchwork is usually performed with the work securely clamped in a bench vise because most workbenches have a vise secured to the top.
5.10.1 Bench Vise
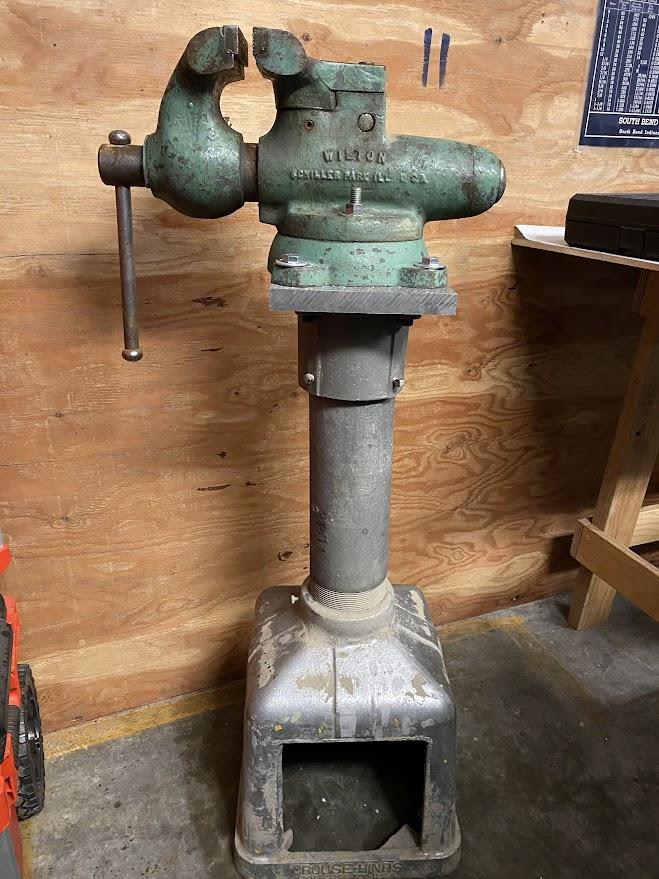
The bench vise in the figure above is mounted on a pedestal, which makes it a pedestal vise. We use a vise to hold material while we perform machining operations on it. One reason you find these vises mounted to a workbench is due to the mass of the work bench and its tendency to stay in place while we twist, turn, pull, and hammer on the stock, which is clamped into its jaws. The example above not only wobbles but also requires a foot placed on the base to prevent motion.
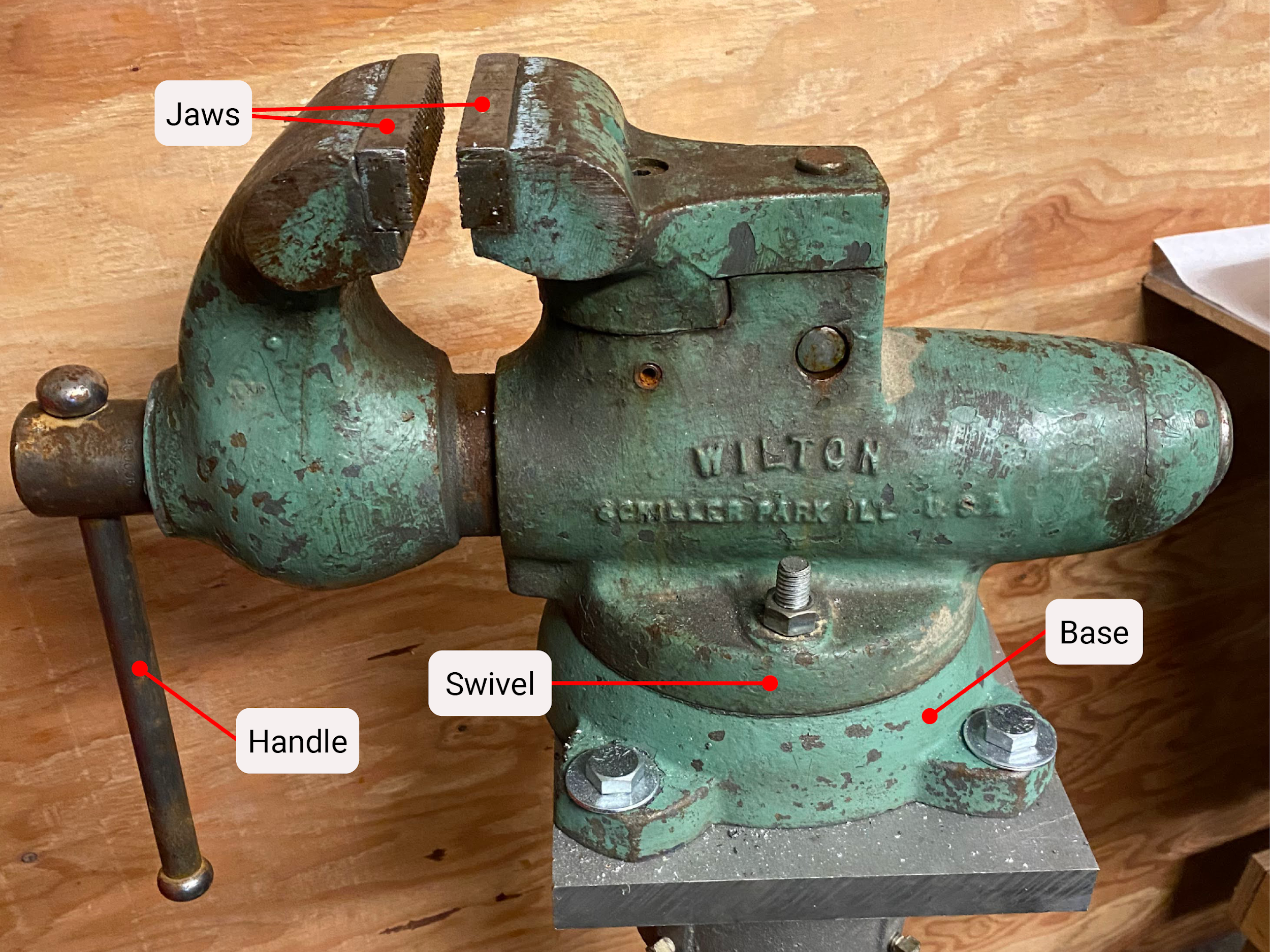
The features of a vise make it a useful workholding device. The base of the bench vise is secured with four ⅝” hex bolts, providing extremely high shear strength. The top of the vise has a swivel joint to allow convenient positioning of the clamping jaws around this pivot. The jaws are replaceable, allowing for different jaws to be installed depending on the desired use. Vise sizes refer to how far the vise jaws open as measured between the jaw faces. Lastly, the vise handle is robust, allowing for extreme lever forces to be applied.
The amount of clamping applied by a bench vise is a product of the handle (lever) length times the force applied to the handle divided by the pitch of the vise screw. Let’s substitute some numbers here and give you an idea of the clamping force of this bench vise.
Assume the following: weight applied to the handle= 150 lbs
The vise handle length is = 9”
And the pitch of this vise’s lead screw is .200”
150X9/.200=6750lbsofforce
That is a considerable amount of force considering we have not added a cheater bar yet or added another person to the force applied to the handle. A cheater bar is a longer lever applied to a wrench/handle to increase the lever force applied.
5.10.2 Clamps
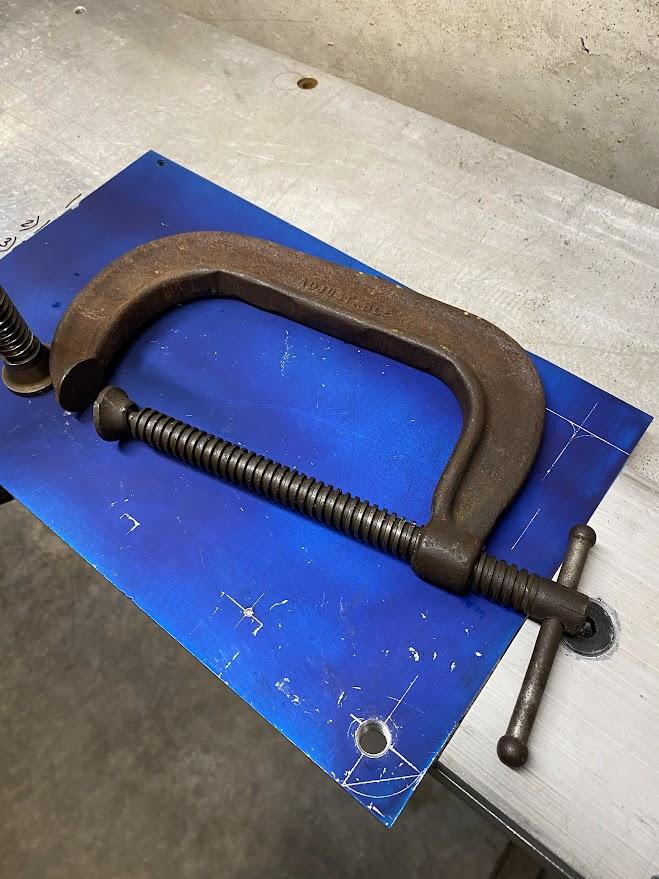
C-clamps get their name from the shape of their body. A very simple clamping tool, they come in many sizes and materials. It is harder to find quality C-clamps these days because they require high quality hammer forged steel to perform to the maximum design intent.
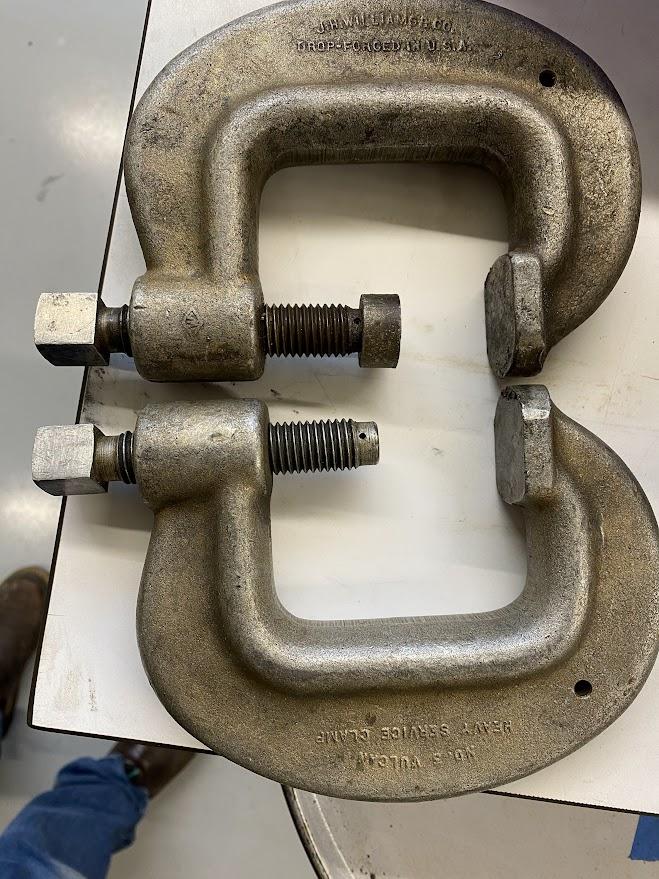
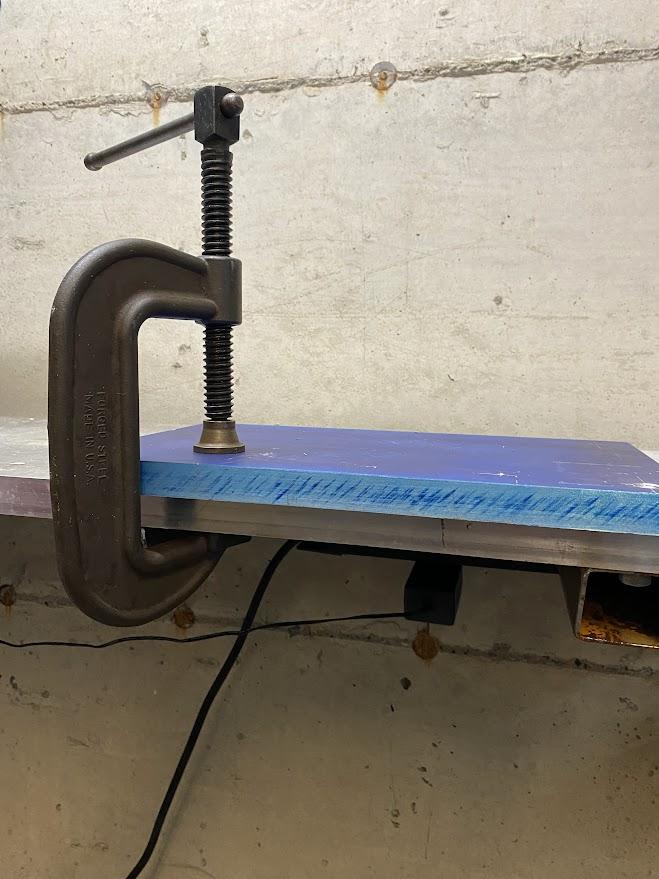
The figure above is an example of a sturdy C-clamp. The body is made from thick forged steel which will prevent flexing under clamping forces. The acme style thread is made of quality steel able to withstand the axial forces of the screw. At the end of the threaded shaft is a swivel foot which provides a sturdy interface between the twisting clamp and the stationary stock material. The threaded shaft terminates with a ball which acts as a bearing pressing against the foot which has a slip fit with the ball and a roll crimp on top of the ball feature to prevent separation. Add to that a quality handle, and the clamping forces available are considerable.
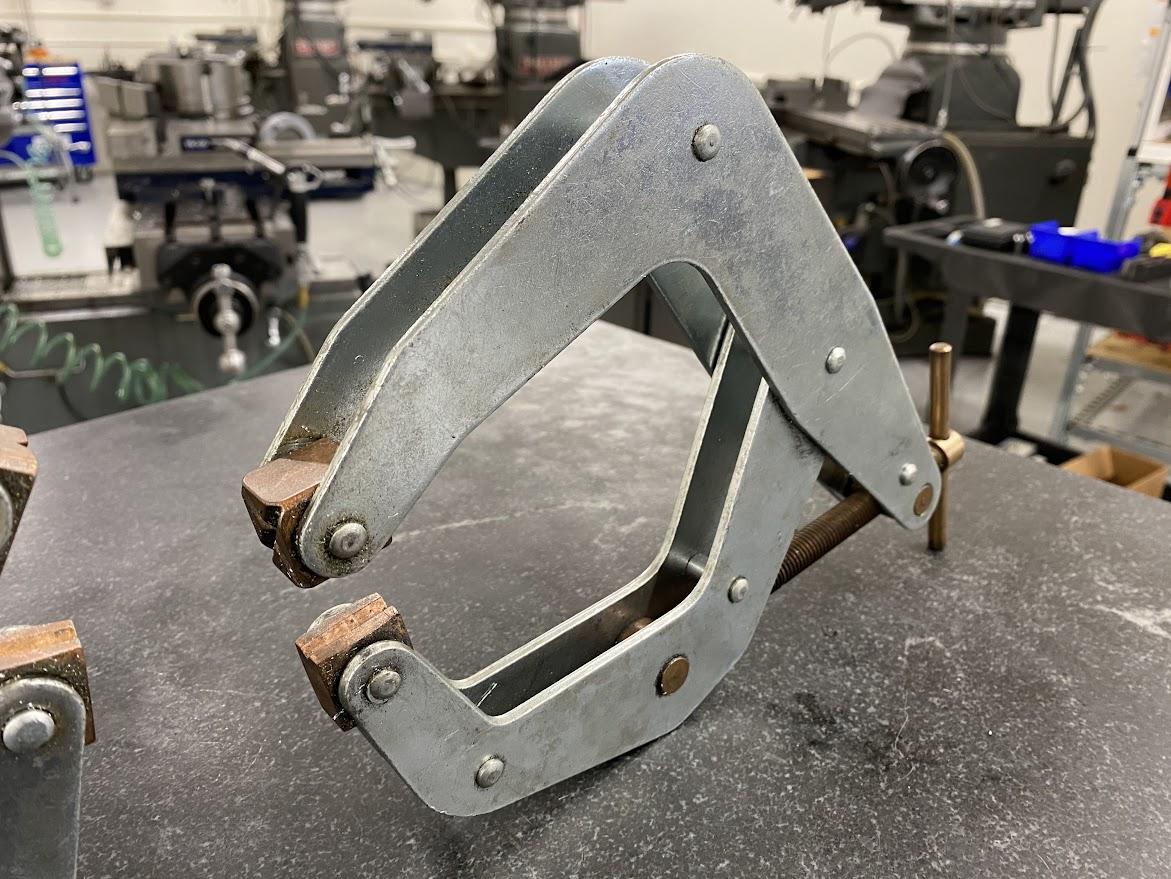
With the lack of affordable forged steel C-clamps, innovation has created a popular style of clamp called a Kant Twist© Clamp. It is made from simple sheet steel, rivets and brass. They come in many sizes and perform well.
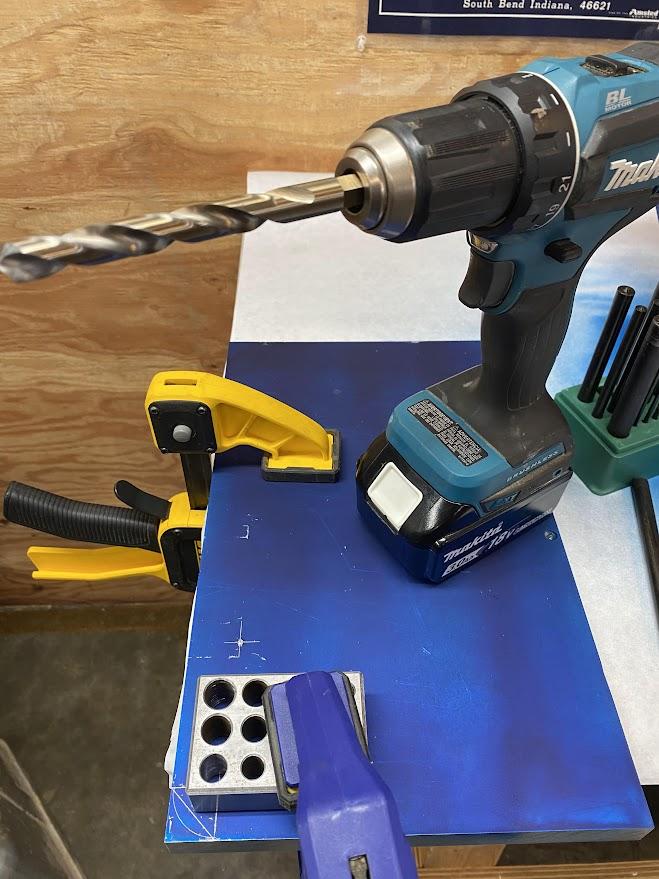
Another economical clamp solution are bar trigger clamps which apply a considerable force and come in many sizes allowing for clamping larger materials.
5.11 Off-Hand Grinding
Off-hand grinding is the process of using a bench grinder to perform grinding operations by holding the part or tool in your hand. As you may imagine, having your hand that close to a machining operation can be a dangerous endeavor and you would be right. This section will provide you with the necessary education to perform safe quality work on a bench grinder.
5.12 Bench Grinders
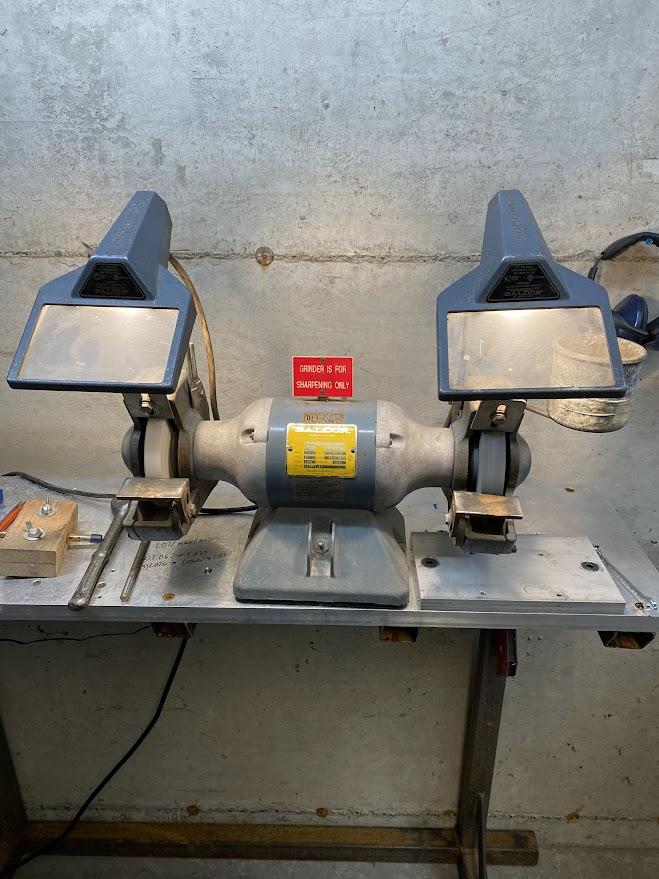
For the entirety of this section the grinding operations will be relative to a bench grinder. A bench grinder is a motorized tool which rotates abrasive wheels in such a manner as to allow accurate repair of metal tooling.
A bench grinder is not the only equipment capable of performing quality grinding operations. It is arguable that a quality belt sander can perform just as well. The intent of this section is to provide enough information to allow the operator to apply these principles to different grinding activities.
5.12.1 Grinding Wheels
Bench grinders are categorized by the size of wheel diameter which fits the machine, with 6” and 8” models being most common. Bench grinding wheels come in varying widths and are composed of many different materials.
What allows a grinder to be so useful is its ability to remove material in a controlled manner. The material removal rate of a grinding wheel is a factor of grain size and binder composition. Abrasive grains found in most grinding wheels are aluminum oxide and silicon carbide. These abrasive grains are held together by special bonding agents which are designed to serve specific purposes. The bonding agent holding all the separate grains together must break down in a controlled manner, which allows dull grains to fall away, exposing new sharp grains of abrasive material.
A basic concept of grinding wheels is the understanding of abrasive grit. Grit relates to the size of the individual grain of the abrasive found in grinding wheels. The larger the size of grit, the more aggressively an abrasive will remove metal. Due to the larger spacing between individual grains of large abrasives, there is more room for air to get into a cut and provide some ability to cool the cut. This means that a larger grit wheel is designed to perform roughing operations, while a finer grit wheel is to be used for finish grinding operations. Using a finer grit wheel for rough material removal will result in excessive heat and clogging of the wheel’s grain structure. Clogging is a natural occurrence where foreign material becomes lodged between individual grains of grit on a grinding wheel. Special tools are used to clean the grinding wheel and remove clogged grains.
In the figure above, notice the low number 40# and the high number 2000#. 40 represents a coarse abrasive with large grit size and 2000 represents a finer grit. The “#” symbol is used in place of the term grit, so read grit when you see this symbol.
Another way to envision grit is to imagine you have a 1X1” surface. On this surface, you spread grit material. The more material that can be evenly spread across this surface, the higher the grit number, and the less amount of grit that fits this surface, the lower the grit number.
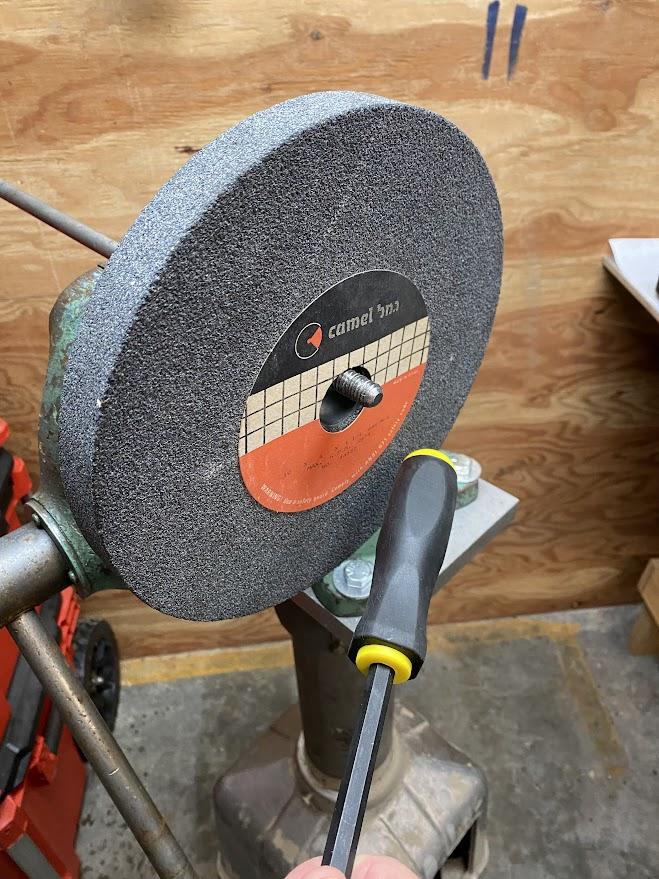
The figure above illustrates an operator performing a ring test before installing a grinding wheel on the machine. A ring test is a process performed by an operator to ensure the grinding wheel is without defect. A ring test is performed by supporting the wheel with a screwdriver or other object that can allow the wheel to be isolated from any interference. The wheel is then struck with a solid object, such as the handle of a screwdriver. A satisfactory sound would be a resonant ring like a bell. A dull sound would be an indication that the structural integrity of the wheel is compromised and that it may shatter under use. This test is performed when the wheel is first installed or when damage is suspected.
Bench grinders typically have two wheels: one coarse grit wheel for roughing and one fine grit wheel for finishing. Most grinding operations will require the use of both wheels. The grit size for roughing wheels is usually at 36-40# and the fine side at 80-100# depending on the use of the grinder. The finer the grit, the easier it can become clogged and require cleaning by the operator.
5.12.2 Tool Rests
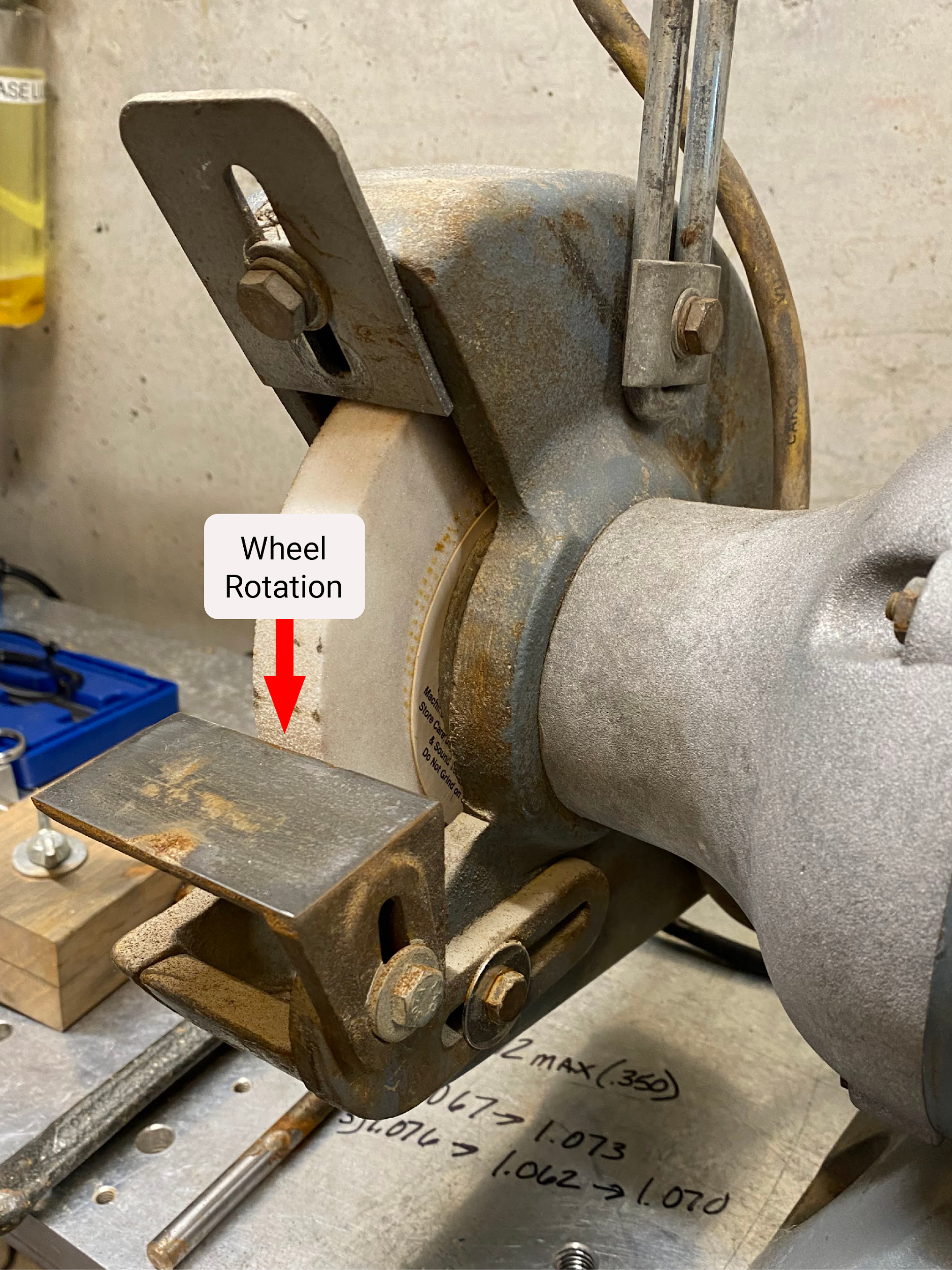
When a grinder is powered, the direction of wheel rotation is in a forward direction, which causes grinding forces to pull the part down and into the tool rest. The tool rest is an adjustable platform that is used to support the part during grinding. Grinders should not be used without a tool rest or any guards in place to prevent injury to the operator.
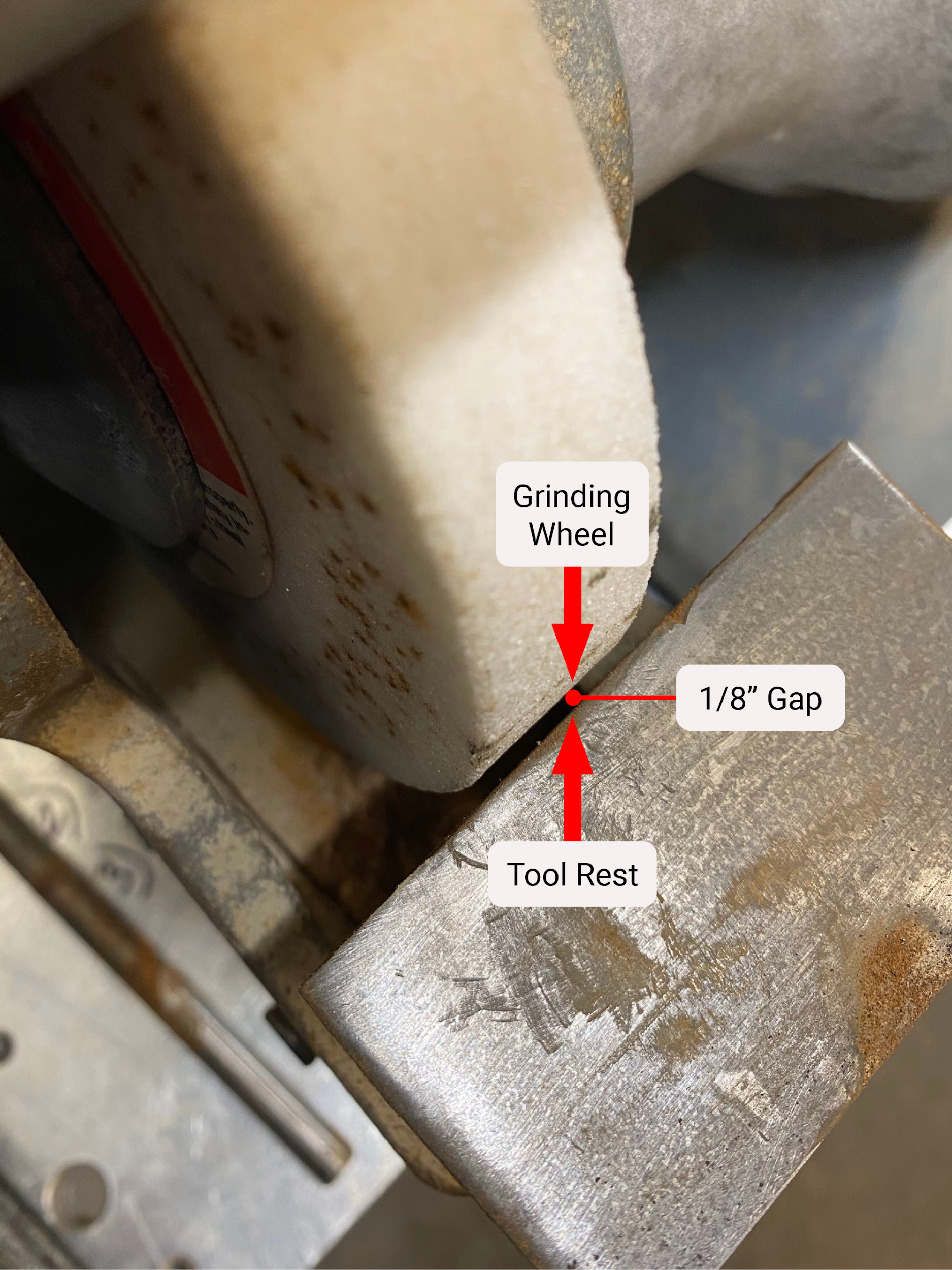
The relationship between the grinding wheel and the tool rest is an important factor for safety. Due to the very hard nature of grinding wheels, if an object were to get caught between the tool rest and the wheel during operation, the wheel could break and send pieces out at high speed.
Since the grinding forces are pulling the part down against the tool rest, the space between the wheel and rest must be controlled to prevent parts from getting lodged there. The acceptable gap between wheel and tool rest is ⅛” maximum. If the gap is larger, loosen the tool rest and reposition the rest to obtain an acceptable spacing.
5.12.3 Bench Grinder Operation
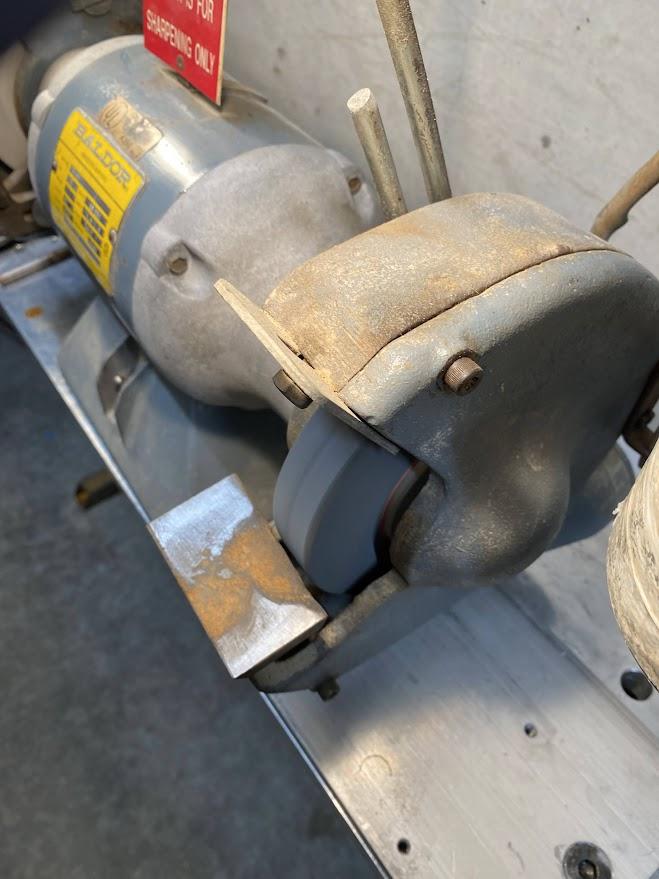
As with all equipment, a preoperational check should be performed to verify the equipment is free from any observable damage. Rotate the grinding wheel by hand and look for any damage to the wheels. If there is observable damage, remove the wheel and perform a ring test. Verify all guards are in place and tightened to prevent inadvertent contact with the grinding wheel during operation. Inspect the gap between tool rest and grinding wheel and adjust if necessary. Inspect the area around the grinder for any material that may encounter hot sparks from the grinder. All flammable material should be stored well away from spark producing equipment. Lastly, ensure the grinder is mounted securely to prevent movement during use.
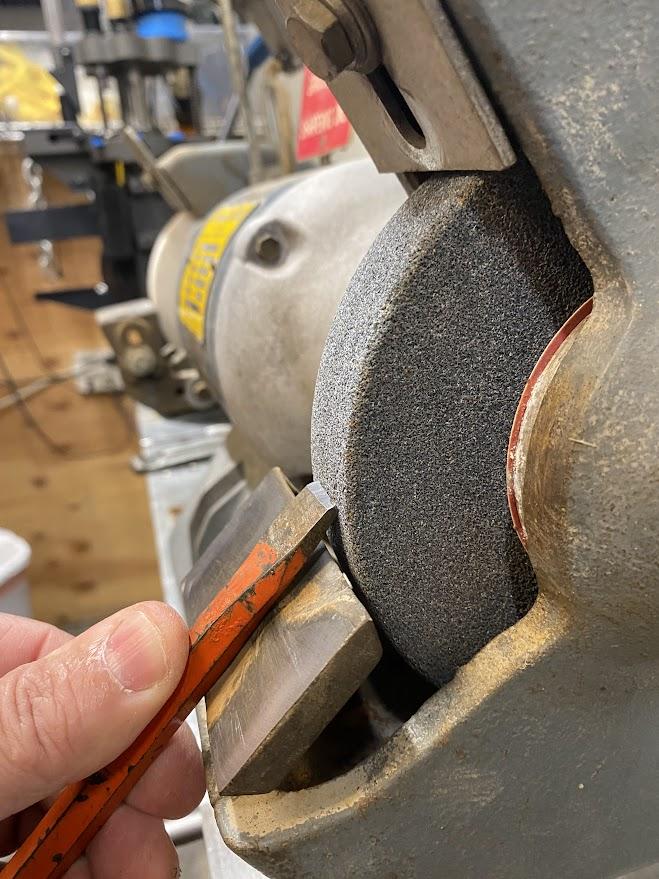
The figure above illustrates the spark shield at the top of the grinding wheel which limits the amount of sparks traveling over the top of the wheel to impact the operator.
5.12.3.1 ON/OFF switch
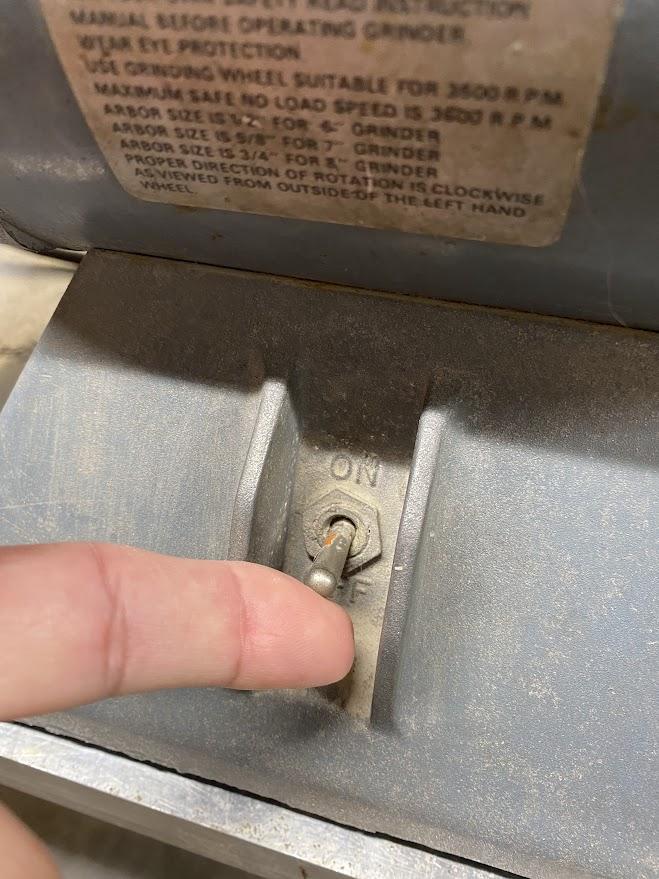
When first turning on a grinder, the operator should stand to the side in case the wheel flies apart due to unseen damage. The centrifugal force created by the spinning wheel will send wheel fragments out in a vertical line parallel with the wheel.
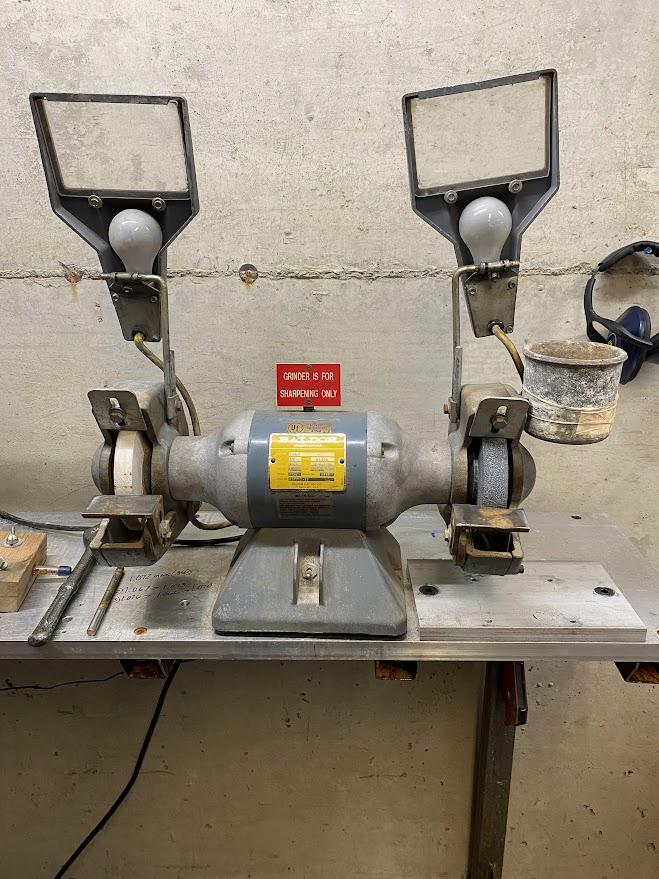
If a wheel failure occurs, the debris will fry outward toward the operator.
5.12.3.2 Dress for success!
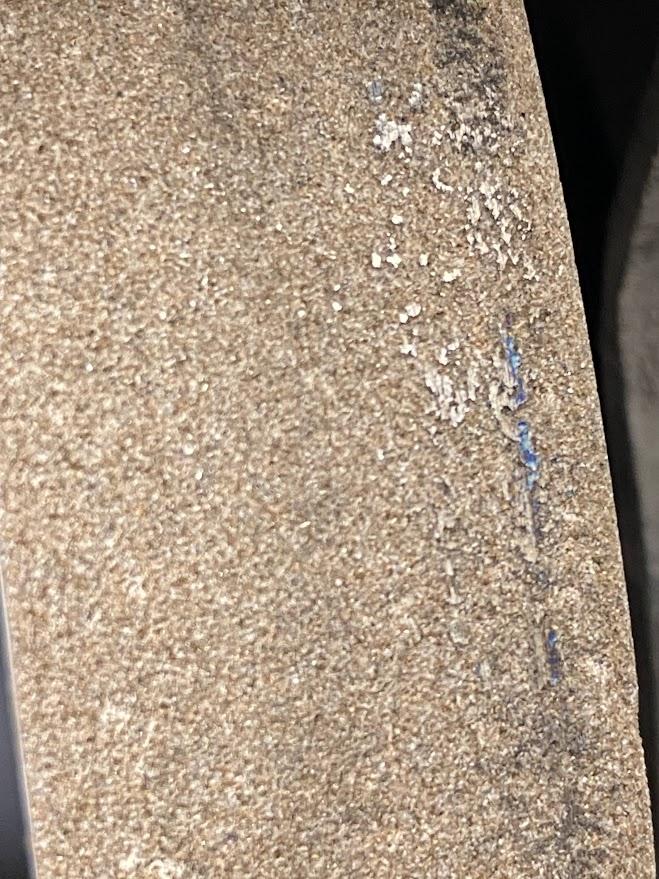
During normal use of the grinding wheels, the surface will dull and become clogged with debris. A normal procedure an operator must perform is to clean the grinding wheel surface to remove debris and expose new, clean and sharp grit.
This process is referred to as dressing the wheel. Wheel Dressing is a grinding wheel maintenance task where the surface of the grinding wheel is restored to improve performance.
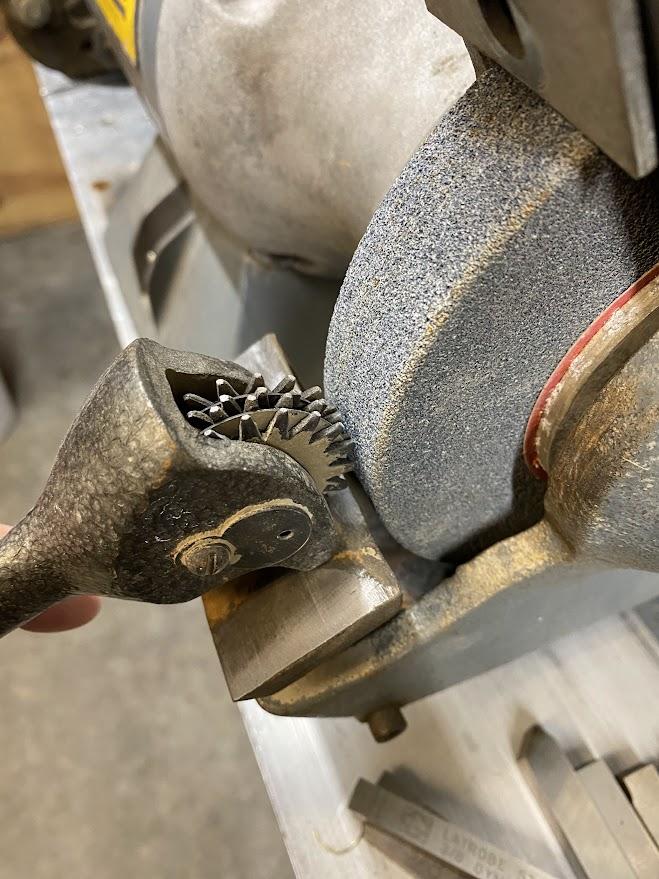
The disc cutter wheel dresser in the figure above abrades the cutting face forcing contaminants from the surface. This is to be used when debris has clogged the wheel which limits the cutting ability and creates excessive heat in the part.
Turn ON the grinder, place the dressing wheel’s body on the tool rest and contact the wheel surface with the wheel. Sweep back and forth across the grinding wheel until the surface is clean.
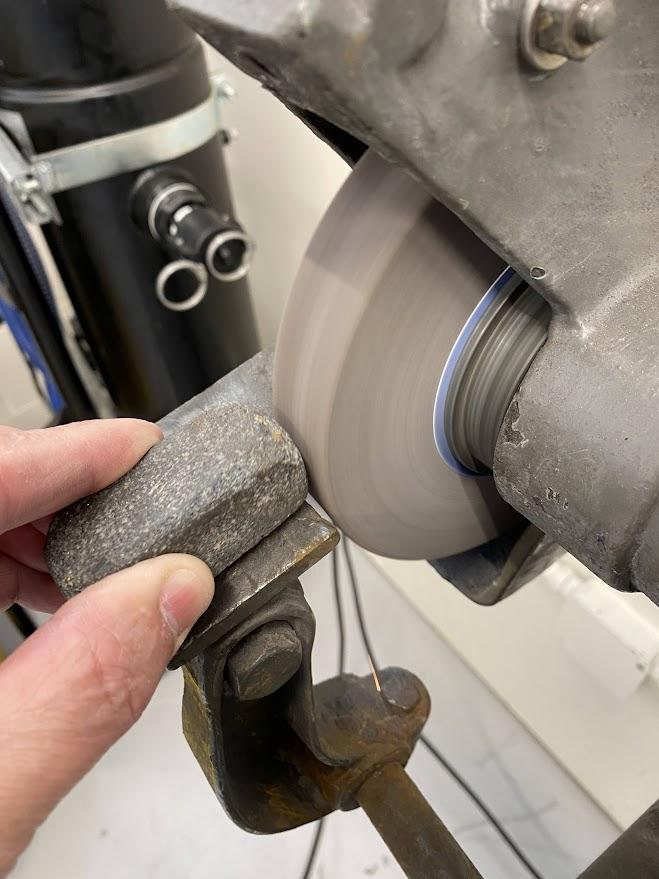
A dressing stick is made from the same material as the grinding wheels (aluminum oxide or silicon carbide) and is pressed against the grinding wheel to restore the shape of the grinding wheel.
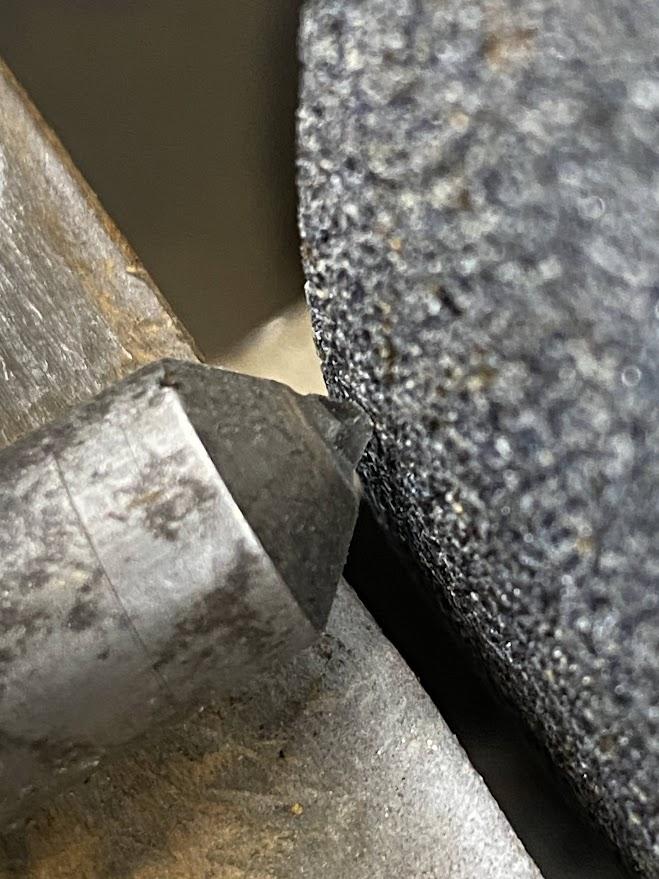
The final tool we will discuss for dressing a grinding wheel is the diamond dresser. Aluminum oxide and silicon carbide are very hard minerals which can take a lot of use. When the surface of a grinding wheel is severely fouled or misshapen, a diamond tipped dresser should be used. Industrial diamonds retain the hardness of fancy jewelry diamonds but lack all the clarity features of their expensive cousins.
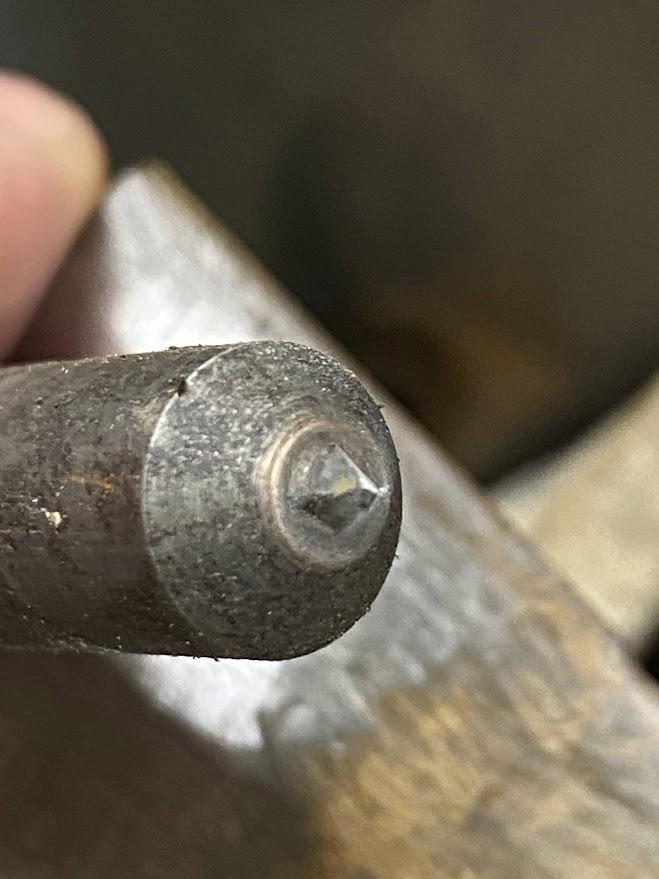
A diamond dresser has an industrial diamond attached to the end of a bar and is used to perform severe grinding wheel dressing.
5.12.3.3 Position the tool rest
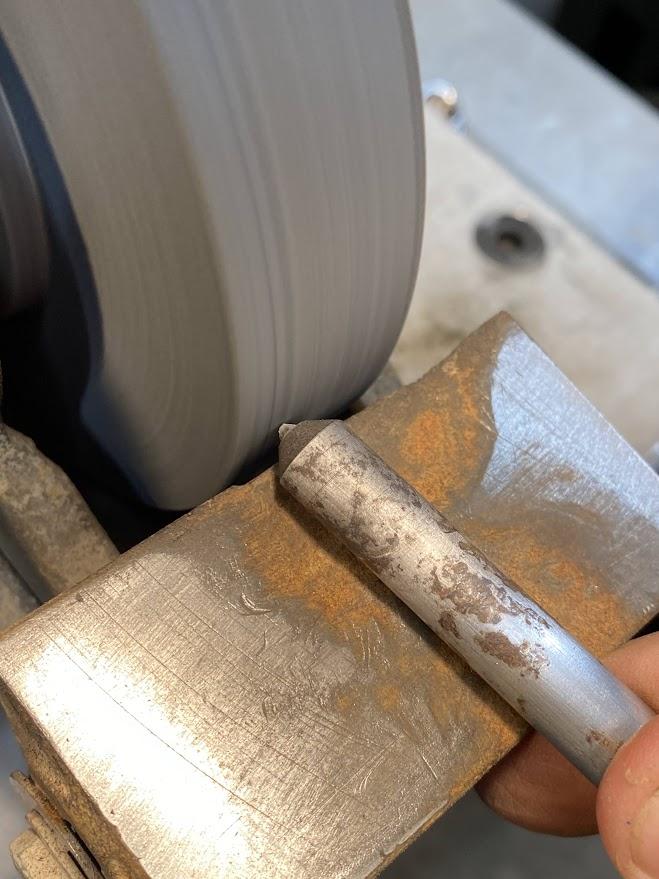
Use a diamond wheel dresser whenever the condition is too severe for other methods such as when metal gets fused onto the surface of the wheel or when a fresh wheel is installed on a grinder and the surface needs to be tried to eliminate runout. Runout is when the surface deviates from the axis of rotation around the circumference of the grinding wheel. A grinding wheel with excessive runout will only contact the part on a small portion of the grinding wheel surface and the operator will experience a skipping action as the part only contacts the wheel on the high spots.
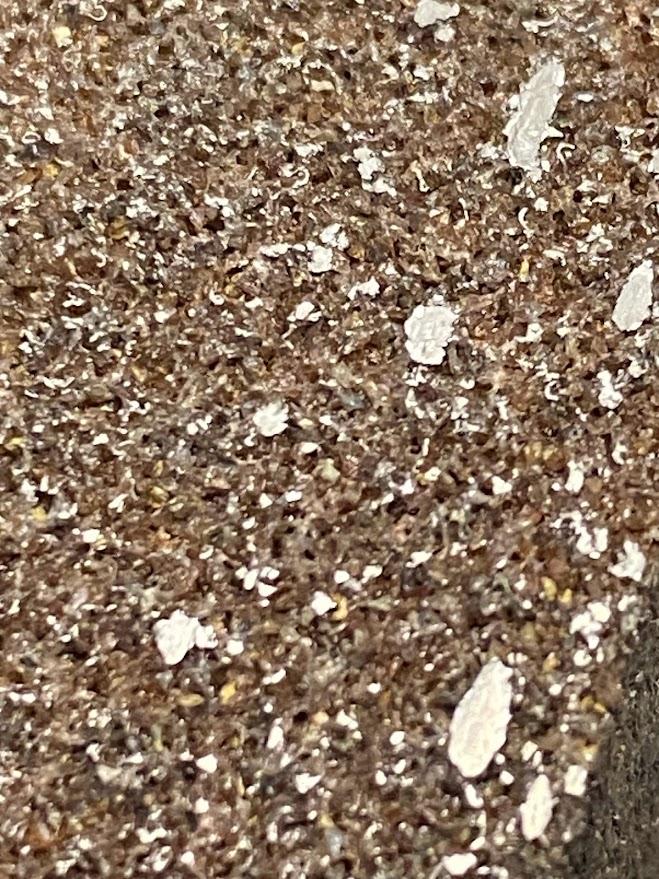
In the figure above a metal has fused into the grain of the grinding wheel and must be removed for improved performance. This fused material is very hard and must be removed in gradual depths. The dressing diamond must be in contact with the tool rest to create a rigid platform for the operation.
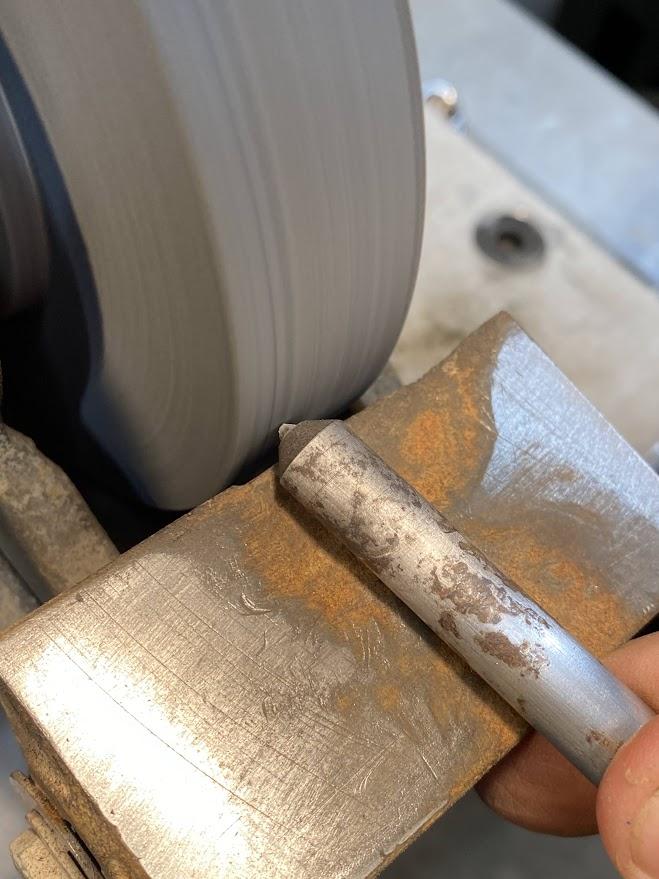
To dress the wheel with a diamond dresser make sure the tool rest is set in a rigid manner because the tool must remain in contact with the rest during the dressing operation.
Rest your finger on the edge of the work stop to function as a guide for this dressing operation. The goal is to create a flat surface on the face of the grinding wheel with square corners and no low spots.
Drag the diamond back and forth across the face of the wheel, taking shallow cuts. This process takes time and precision to achieve the goal. Continue to take small light passes back and forth until the surface is restored.
When truing a new grinding wheel, the runout will be excessive, and the dressing operation will require several passes and create quite a mess in the process as the grinding wheel material accumulates on the floor at the base of the grinder.
5.12.3.4 Roughing and finishing
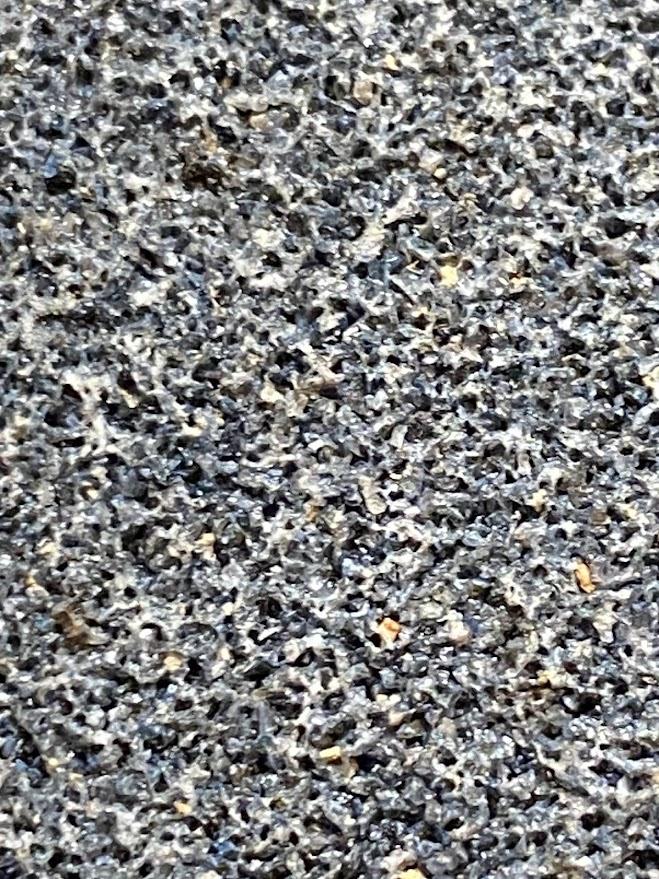
Always start a rough grinding operation on the coarse wheel. It will remove material quicker than a fine grit and will create less heat build up in the part.
Use the entire surface of the wheel to prevent uneven wear on the wheel’s surface.
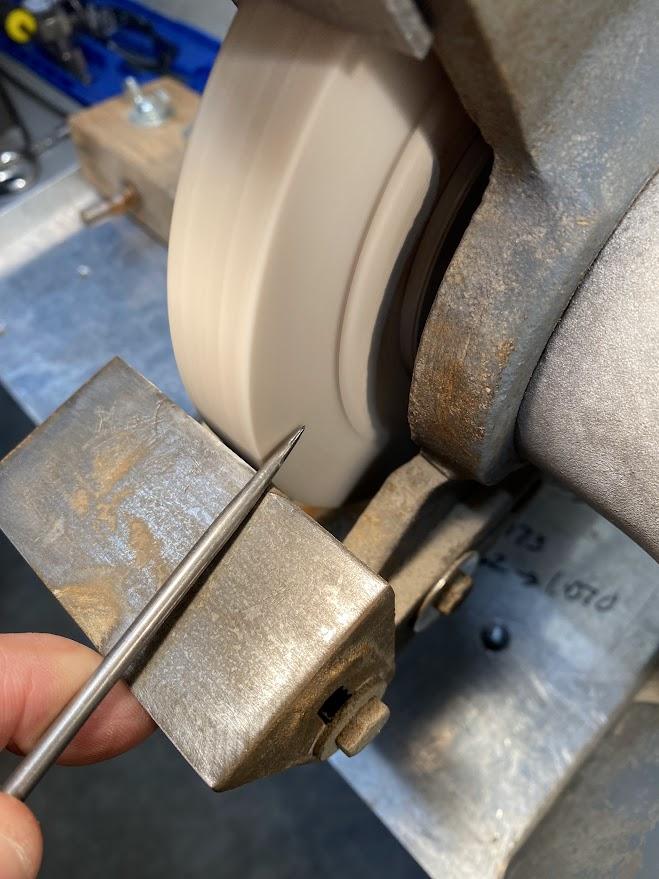
It is not recommended to use the side of the grinding wheel to shape parts. The force this creates is on an unsupported plane and can cause severe damage if the wheel fails.
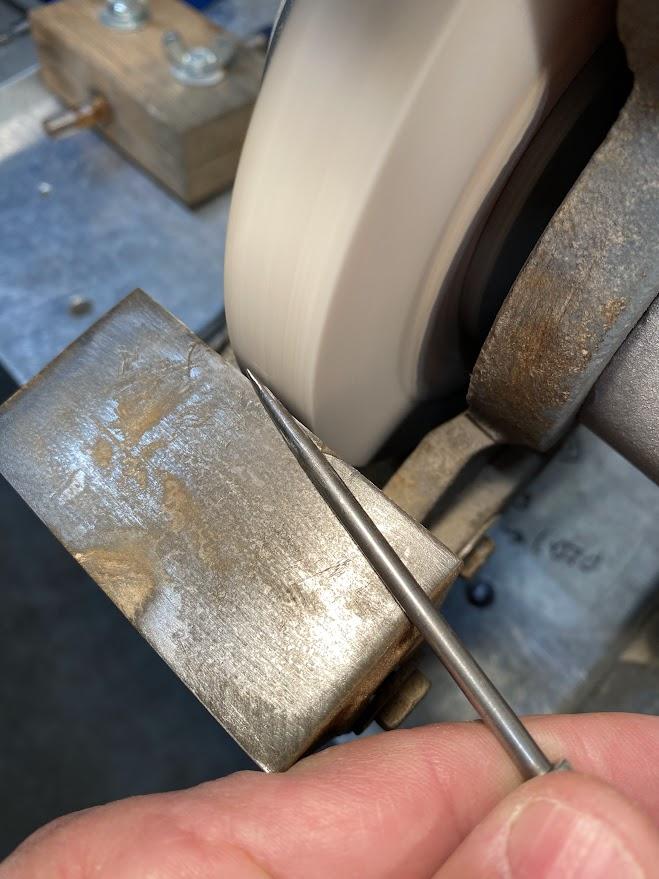
Finish grinding operations are for final cuts, which establish a sharpened edge and smooth surface finish. When roughing, a heavy hand may be used to apply enough force to remove material; however when performing finish grinds, a light, delicate touch is required.
5.12.3.5 Controlling heat
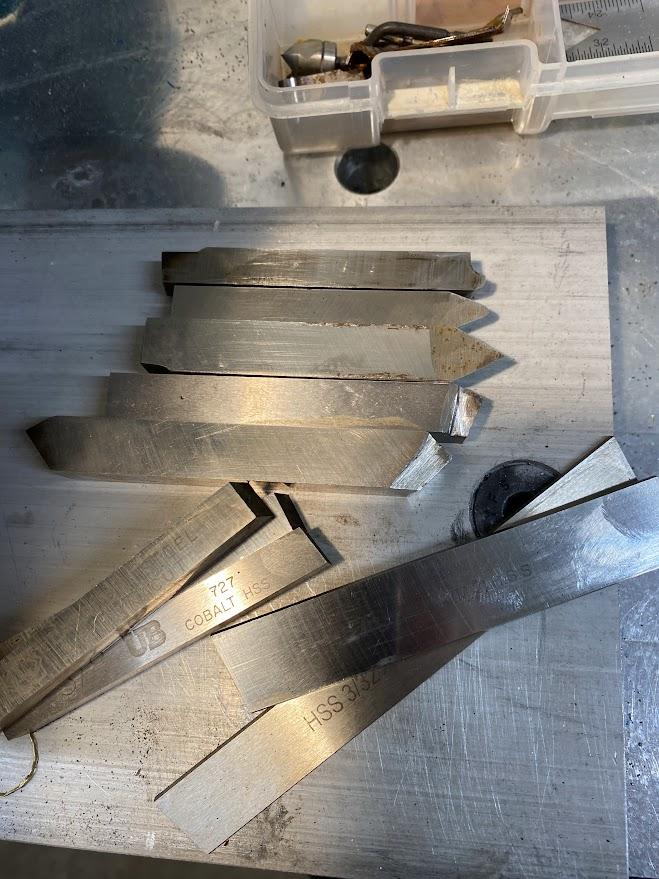
When performing grinding operations on material such as high speed steel (HSS), the part will get hot enough to cause discomfort to the operator.
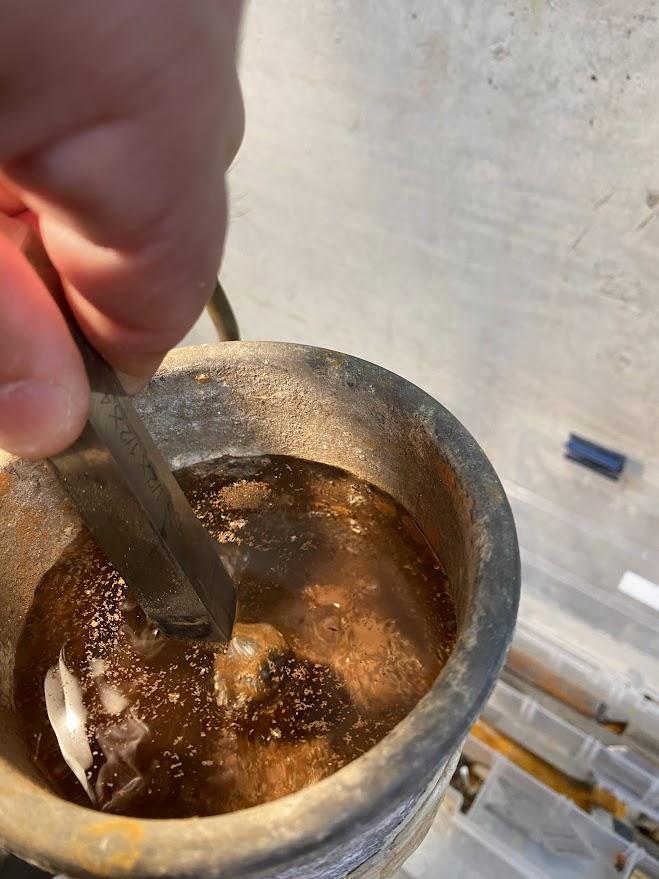
Keeping a bowl of water nearby will provide relief by quenching the hot part into the water with the hope of transferring the heat from the part into the water. Repeated quenchings are necessary during long grinding operations.
5.12.3.6 Sparks
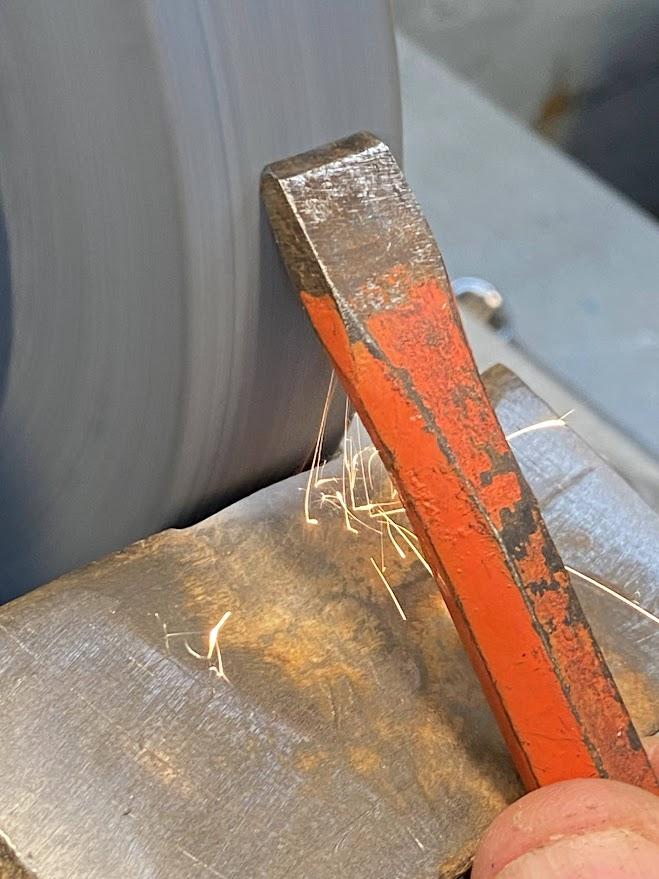
A byproduct of grinding is the creation of sparks. Reading the sparks can assist in your grinding operations.
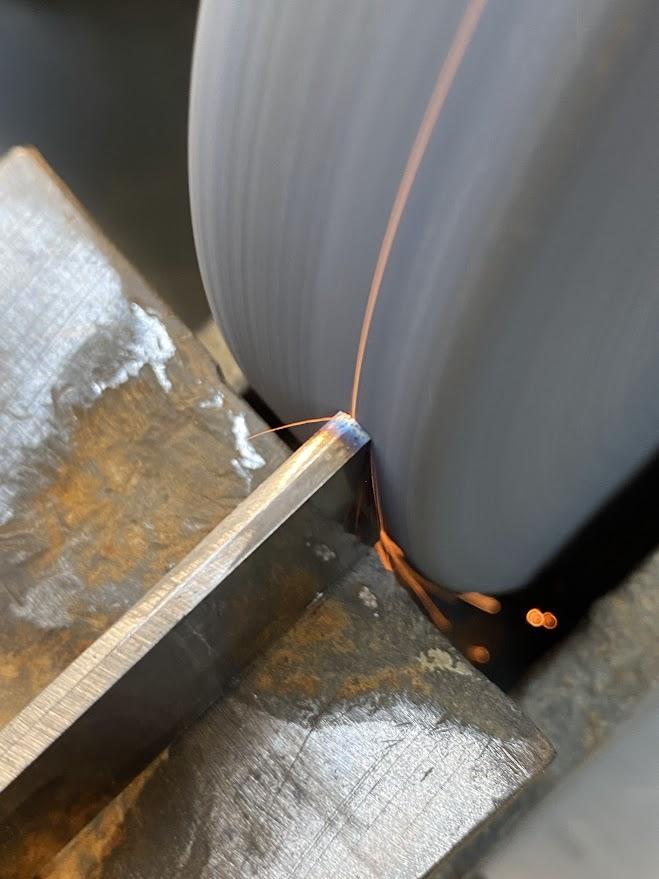
In the figure above, a lathe parting blade is being sharpened. Notice the sparks have wrapped around the wheel and are bouncing off the top of the part. What this indicates is that the top edge of the part is not in contact with the wheel, and the sparks cannot go under this edge. This is an indication that the cutting edge is now sharp, and you need to remove it and inspect the edge.
5.12.3.7 You can’t grind that!
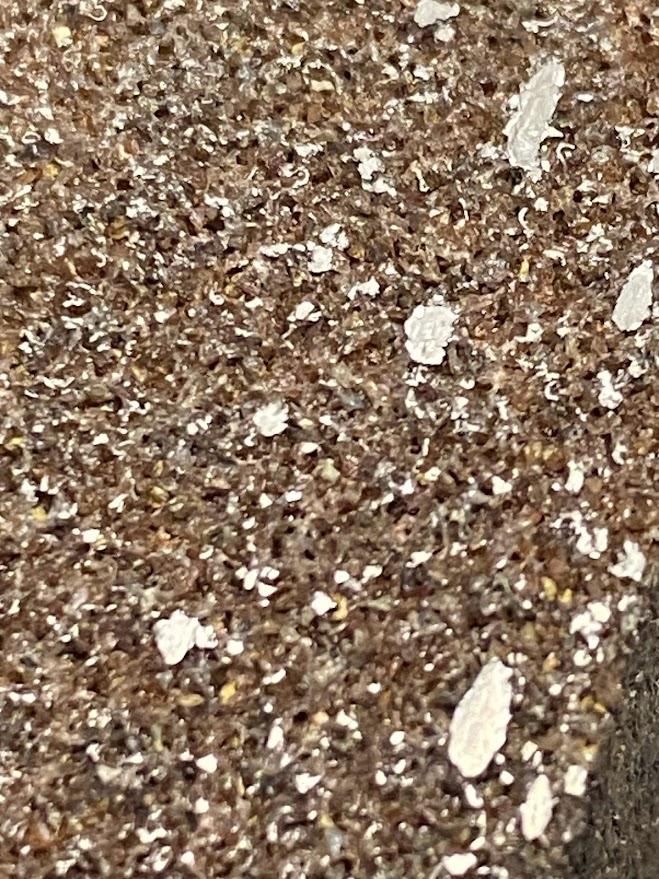
The grinding wheel in the figure above has become clogged because an operator has selected a material that should not be ground on a grinding wheel. This is common when inexperienced operators have access to a grinder. A material such as aluminum, if placed against the wheel, builds up heat, melting and solidifying on the wheel. Aluminum transfers to the grinding wheel, where it cools and creates very hard contamination zones.
To restore this wheel, a diamond dresser must be used to remove these hard contamination zones.
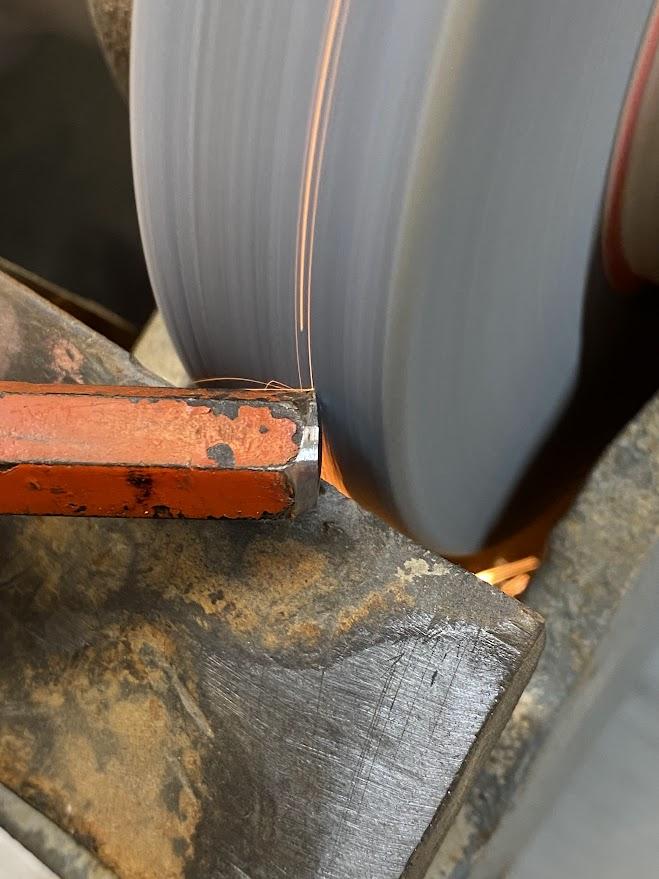
The rule for which material is allowed on a grinder is simple. If it creates a spark, you can grind it. If it doesn’t create a spark, find another method, such as belt sanding. Belt sanders do not build up heat like a grinding wheel but offer all the characteristics grinding does, such as aluminum oxide/silicon carbide grit, tool rests, and robust power.
SUMMARY
Benchwork skills allow a machinist to perform quality repair and fabrication operations with the use of simple tools. With refined technique, benchwork skills can be used to create prototype parts that have not been evaluated enough to warrant costly CNC machine space. Good benchwork skills are necessary to perform repair work on equipment to return it to a safe state of operation.
A quality bench grinder makes our jobs easier by shaping and sharpening the tooling we are using, such as drill bits and punches. Having a solid understanding of the operating process performed on a bench grinder will aid you in a successful machining operation.
I hope you will take the time necessary to learn the techniques necessary to become a well rounded machinist by incorporating benchwork practices into your skill set.
REVIEW QUESTIONS
- List safety concerns when performing offhand grinding.
- Explain the purpose of a saw blade kerf.
- Describe steps to replace a grinding wheel
- Explain the 3X rule as it applies to saw blades?
- Calculate the tap drill for a 75% engagement ⅝-11 UNC 2B thread.
- What material can be used on a bench grinder?
- List some of the shapes of hand files?
- What type of operations can you perform with hand files?
- List the tools used to scribe straight lines on stock.
- Name the tools used to scribe curved lines on stock.
- Define TPI.
- Explain the function of a flute on a tap.
- What is a tap drill?
- List, in order, the processes for using a threading die.
- List in order the steps to create threads with a die.
REFERENCES
McGeough, J. A., & Hartenberg, R. S. (2023, September 20). Hand tool: File. Britannica. Retrieved May 7, 2024, from https://www.britannica.com/technology/hand-tool/File