Chapter 6: Job Planning
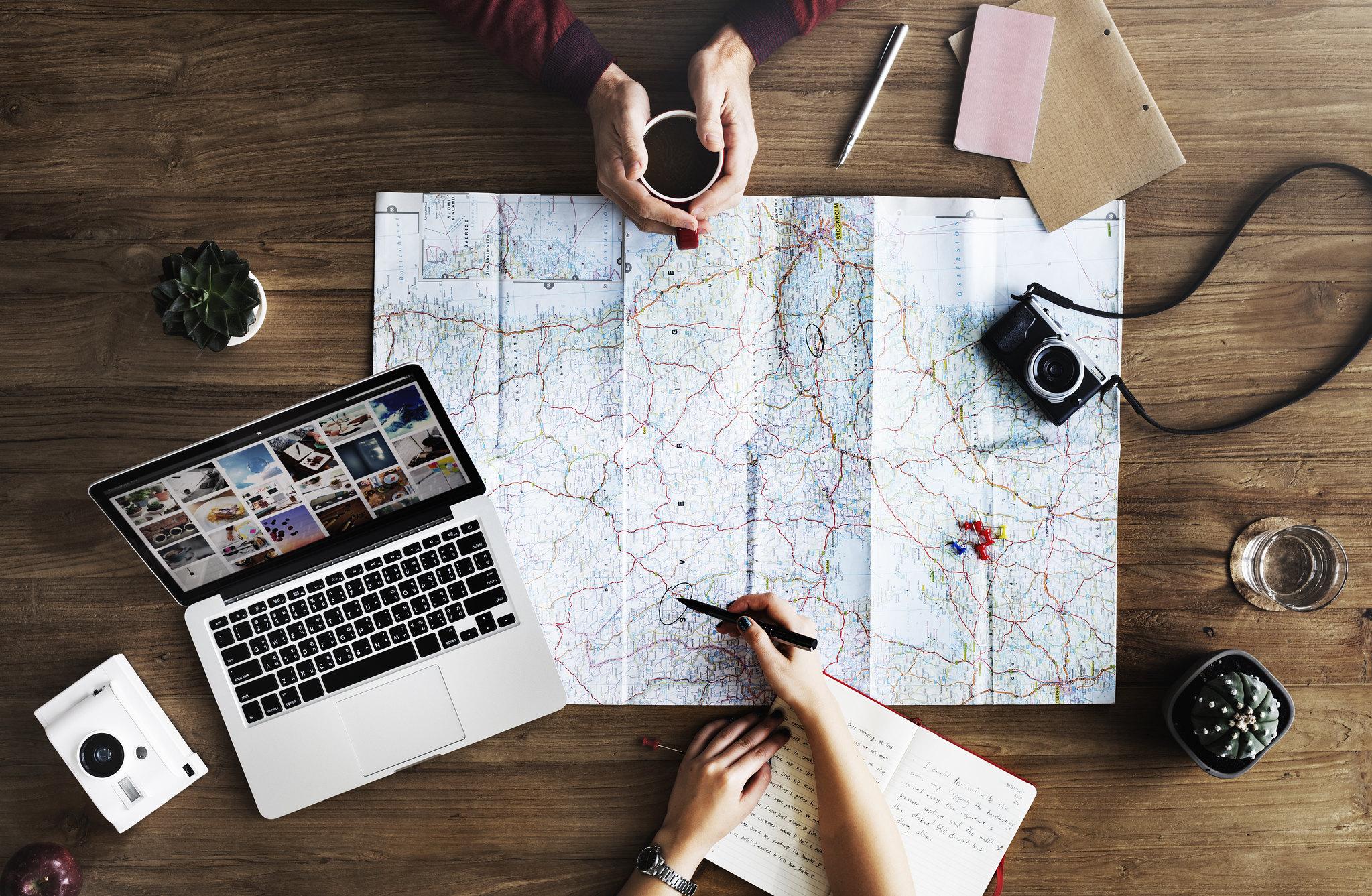
Overview
Creating a Job Plan is analogous to preparing for a trip. Have you ever gone on a camping trip where you forgot something important? Maybe you didn’t bring matches, arrived too late to get a good camping spot, or didn’t bring marshmallows for roasting. When you don’t have a detailed plan, it is easier to forget important supplies that will help make your trip relaxing and enjoyable. As the old adage goes, “If you fail to plan, you plan to fail.” In Machining, a good job plan is necessary to optimize your material, tools, time, labor, and effort in making the parts. A job plan will help you visualize the steps needed for a specific part. Doing so will enable you to work more efficiently and productively.
Sometimes, a new machinist may get so excited to start making parts that the first cuts end up making more work to finish the part. While it is tempting to start working to be productive, creating a job plan will be more efficient. This chapter will describe the process of job planning and demonstrate how to make a job plan for a specific part.
OBJECTIVES
- Identify and analyze the required features and specifications of the part.
- Develop a comprehensive plan for making the part, considering dimensions, tolerances, and key features.
- Determine the optimal machining sequences for cutting and shaping the identified features.
- Choose the necessary tooling based on the selected processes.
- Select the appropriate machine, equipment, and/or material that aligns with the chosen processes.
- Establish a strategy for securely holding the part during machining.
- Organize the machining steps logically to minimize downtime, and optimize production flow.
- Create detailed documentation that captures all aspects of the machining process.
KEY TERMS
- Technical Drawings
- Tolerance
- Platting
- Features
- Heat treat
- surface quality
- Subtractive Manufacturing
- Machine Capability
- Layout
- End mill
- Drill
- Face mill
- Turning tool
- Knurling tool
- high-speed steel
- Carbide
- Insert
- Mild steel – 1018
- Stainless Steel – 304
- Aluminum – 6061
- Cold drawn steel bar – 12L14
- Acetal
- Band Saw
- Manual Mill
- Manual Lathe
- Surface Grinder
- Vise
- Strap clamps
- Collet Chuck
- Three jaw chuck
- Four jaw chuck
6.0 Introduction
In school, we practice planning to help prepare us for the opportunity to advance in the workplace. Planning shows critical thinking and problem-solving, which are sought-after traits of a machinist. Critical thinking is second on the worker required skills as reported by the U.S. Department of Labor on their O*NET OnLine site (2024).
A job plan is a written out sequence of general steps that will be taken when making a part. Writing the plan down forces the machinist to think through the complete process before starting. The best way to learn about job planning is to go through the process, especially when you have a part to make. This chapter will look at building a bench block so that you can follow the process of making a job plan. As you read, make note of how the chapter explains how the decisions are made and are noted so that the machinist can follow the job plan when it is time to start making the part. After you have read about how an experienced job planner lays out a plan, you can replicate the process when you need to.
Project Planning Worksheet
Project Planning For |
|||||
Sequence |
Feature |
Holding |
Machine |
Tooling |
Notes |
1 |
Grind |
Magnetic Chuck |
Surface grinder |
|
Minimal Material Removal |
2 |
Spot Drill |
Vice with parallels |
Vertical Mill |
Add step to square up stock |
|
3 |
Drill |
Vice with parallels |
Vertical Mill |
|
|
4 |
Bore |
Vice with parallels |
Vertical Mill |
Adjustable boring head |
|
5 |
Groove |
Vice with parallels |
Vertical Mill |
Flat End Mill |
Tilt head to 45 deg |
6 |
Counter Bore |
Vice with parallels |
Vertical Mill |
Flat End Mill |
Rotary Table |
7 |
Profile |
Through holes with fixture in three jaw |
Vertical Mill |
Flat End Mill |
Rotary Table |
8 |
Knurl |
Through holes with fixture in three jaw |
Lathe |
Pinch Knurl Tool |
|
9 |
Turn |
Through holes with fixture in three jaw |
Lathe |
Turning tool |
|
|
|
|
|
|
|
1.5 |
Square up stock |
Vice |
Vertical Mill |
Face Mill |
|
option |
Counter Bore |
Three jaw Chuck or Form jaws |
Lathe |
Boring Bar |
|
option |
Profile |
Through holes with fixture in three jaw |
Lathe |
Turning tool |
|
|
|
|
|
|
|
|
|
|
|
|
|
Note: A table showing the project planning for the bench block.
A bench block is a tool that is used when working with hand tools such as drills and taps. It will assist in keeping the drill and tap perpendicular to the part that is being worked on. A machinist can also use it to hold small round cylindrical parts when working on them, which is a type of workholding. Bench blocks are useful tools, and every machinist should have one. You can buy them, but making one will help students practice, and it is a common assignment because of the many skills needed to build it.
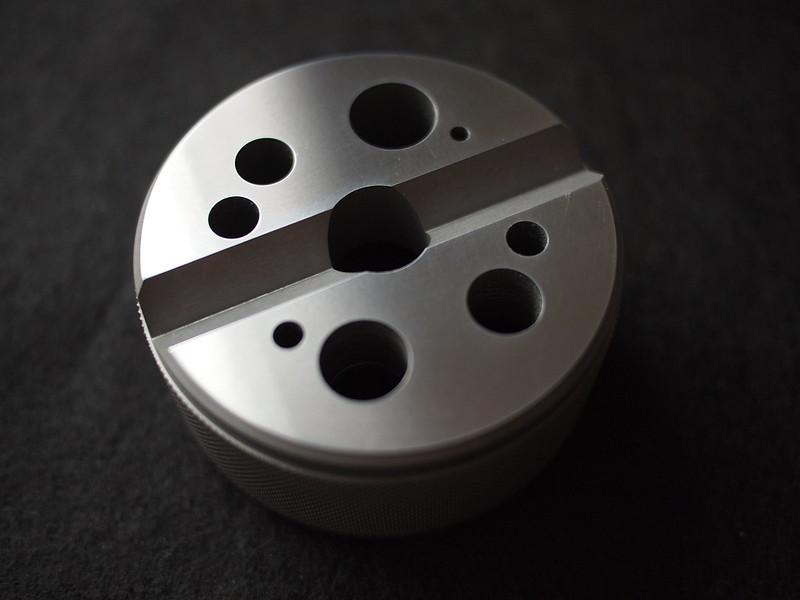
6.0.1 The Role of Job Planning in Machining
Job planning is a best practice in terms of saving yourself time and effort in making a part. It is also an expectation in the workplace because it saves the employer time and money.
One way job planning saves an employer money is by reducing the material used to make a part. In machining, material is typically removed by physically cutting or grinding. This removal of material is referred to as subtractive manufacturing .
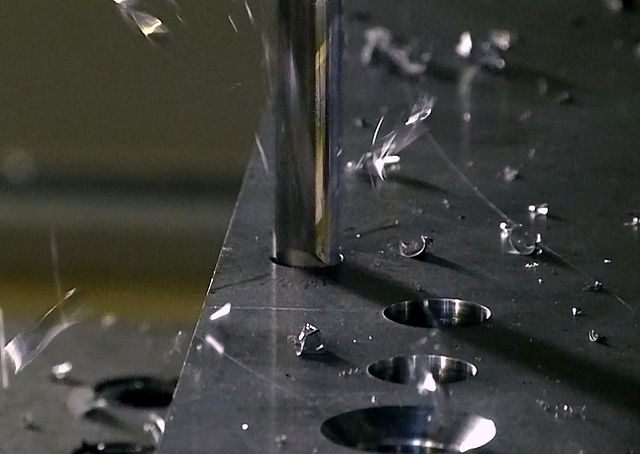
Some benefits of having a job plan are:
- Keeping the project on track.
- Less effort is needed to make a part because problems have been solved.
- Critical features have been identified prior to starting the part.
- Material conservation due to reduced waste, which saves costs in producing the part.
When the part’s complexity increases, so does the equipment it is made on. CNC machines are commonly used when large numbers of complex parts with tight tolerances are required. A mistake at one of these workstations can be costly. So always be thinking of how you might plan a job, but determine if one is needed before you spend time making something that is not needed. A benefit of thinking of a plan is that if it is not needed, a more productive or cost-saving process may be discovered.
Developing a job plan is vital to ensuring the successful machining of a part. Job planning involves a structured approach to organizing the various machining operations.
The basic elements of job planning are:
-
- Examine the technical drawing
- Identify the tools needed to create the features
- Select the appropriate material
- Choose a machine that the work will be done on
- Identify how the part will be held while being worked on
As noted in step one above, job planning begins by examining the technical drawing of a part. The features that need to be made will become apparent. The next section introduces technical drawings and how to read them.
6.1 Technical Drawings
6.1.1 A picture is worth a thousand words.
Since this chapter describes how to do job planning to make a bench block, let’s explore the technical drawing for the bench block.
Understanding technical drawings, covered in Chapter 3, is essential for a machinist to ensure that the final machined part meets the designed specifications, dimensional accuracy, material requirements, and functional expectations of the customer. A technical drawing is considered a contract between the customer and the machinist. It should clearly state what the customer requires so that the machinist knows what is expected and acceptable.
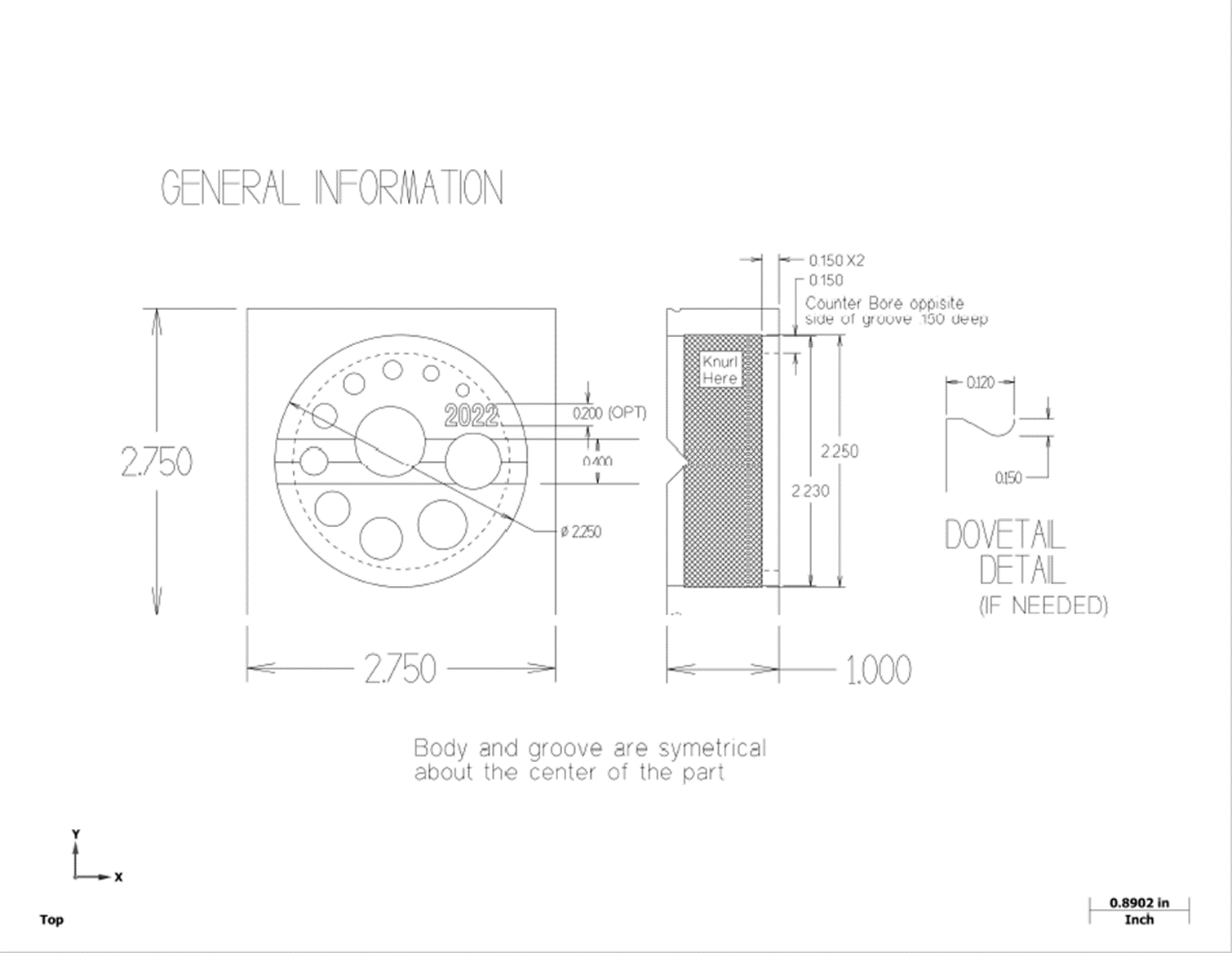
When you first look at this drawing, note that it starts out as a square part that measures 2.75 inches by 2.75 inches by 1.0 inch. The finished part will retain most of the 1.0-inch thickness, but it will have a diameter of 2.25 +/-.002. Also, note that a series of holes will need to be established, along with a V groove down the middle. There is also a recessed pocket on the bottom and knurling on the side of the part.
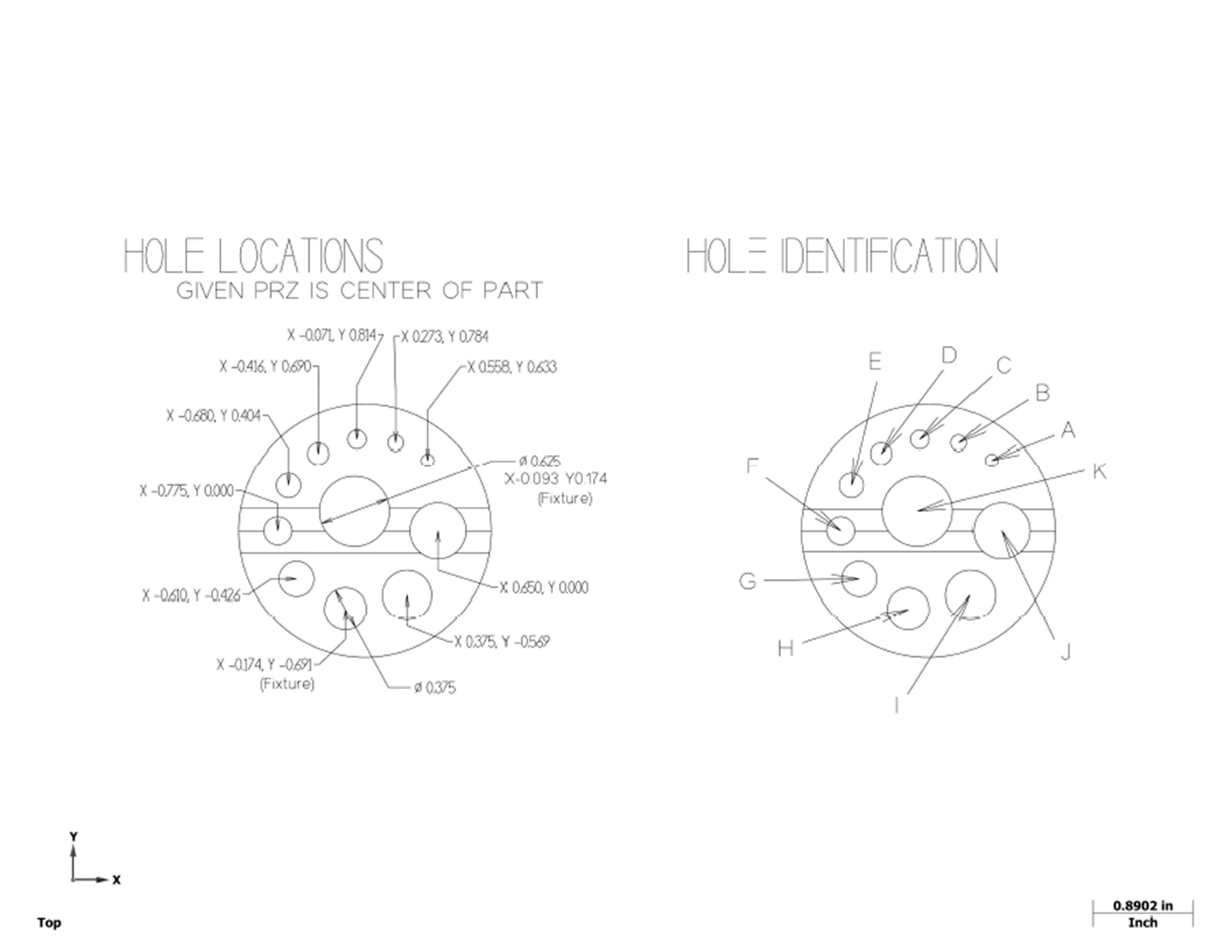
The second drawing shows the hole locations on the part. As you lay out your job plan, it is important to note the steps for making holes, because you will need to know what processes are needed to drill a hole correctly. Once we find the center of the part, the tool that will cut the hole can be moved to the coordinate shown. A proper hole will go through a series of steps. First, it will be spot-drilled so that the next drill doesn’t walk off the precise point where you need it. Then, the drilling starts. Ensure the hole is completely through the part before continuing. The last stage, when needed, is to bore the hole. This opens up the holes while maintaining a quality finish.
When a machinist receives an order for a part, several papers, and information will be provided. This can be considered the job packet, or work order. The data sheet is all of the specific information about creating the holes in the part brought together in one place. When making the holes, the machinist would only have to refer to this page.
Hole |
Position |
Drill |
Decimal |
|
Guide for |
|
|
X |
Y |
Thru |
Size |
Notes |
Tap size |
A |
0.558 |
0.633 |
#32 |
0.116 |
CB .140 to .6 deep |
4-40 |
B |
0.273 |
0.784 |
#28 |
0.140 |
|
6-32 |
C |
-0.071 |
0.814 |
#19 |
0.166 |
|
8-32 |
D |
-0.416 |
0.690 |
#9 |
0.196 |
|
10-24 |
E |
-0.680 |
0.404 |
7/32 |
0.218 |
|
12-24 |
F |
-0.775 |
0.000 |
6.5mm |
0.256 |
|
1/4-20 |
G |
-0.610 |
-0.426 |
P |
0.323 |
|
5/16-18 |
H |
-0.174 |
-0.691 |
3/8 |
0.375 |
Bore to .380 |
3/8-16 |
I |
0.375 |
-0.569 |
7/16 |
0.438 |
Bore to .446 |
7/16-14 |
J |
0.650 |
0.000 |
1/2 |
0.500 |
Bore to .508 |
1/2-13 |
K |
-0.093 |
0.174 |
5.8 |
0.625 |
Bore to .634 |
5/8-11 |
Note: This table shows the hole name, the letter, the location based off of the center of the part on the X and Y axis; the name of the drill with a decimal equivalent, notes for special directions, and the size of tap that will fit into the hole for aligning perpendicularly to a part.
The holes have letters associated with them to be used to help keep track of which one is being worked on. The next two columns give the location of the hole. The drill name and decimal equivalent for the hole size are listed next. The notes column is used to indicate that some of the holes need to be made bigger. The last column is a note as to what the hole would be used for, i.e., a ½-13 tap will slide through hole J.
The work order for the bench block will include several papers. A technical drawing has general information and dimensions. A detailed drawing shows the coordinates of each hole based off of the center of the part. A data table is included to show the hole locations, sizes of holes, and any special notes. Looking at the data table, the notes indicate that some of the holes will have to be opened up with a boring operation.
Recall from Chapter 3 that technical drawings are of the utmost importance in the field of machining. These drawings serve as a primary means of communication between designers, engineers, and machinists. They provide precise instructions, and specifications for making the products, and will help determine the job plan. Machining involves shaping raw materials into intricate parts, and components. Any inaccuracies, or misinterpretations can lead to costly errors, and delays in production. By comprehending the technical drawings, machinists can accurately interpret dimensions, tolerances, feature relationships, and material requirements. This will ensure that the final product meets the customer’s specifications.
Often, there is never a right or wrong choice in determining the sequence of events in a project plan. Some decisions may result in more work, while others are more efficient. For example, by cutting the outside of a part first, the machinist may be required to make special tooling to hold the part to finish the rest of the part.
The quantity can also affect the plan. If only one part is being made, a reliable process will take precedence over efficiency. If the order is for a significant number of parts, efficiency will be foremost in the planning stage. The decisions made when determining the job plan should also take into consideration the accuracy required and the lead time.
Other factors to consider are when does the customer need the parts, and will a secondary operation be required? Secondary operations will include activities such as applying paint or plating. Heat treating can also be performed to help improve the material’s characteristics, such as strength or durability. In the grand scheme of the project, the job plan is made from the best information available.
6.2 Tool selection
There are numerous tools to choose from when deciding on what to use. We can divide the tools into smaller groups.
- Face mills and fly cutters will cut large areas.
- End mills and corner rounders to cut the outside of parts.
- Boring bars and grooving tools are used to cut the inside of parts.
- Drills and reamers that make holes.
- Pattern or form tools that cut a specific thread or chamfer.
Initially, the selection of tools will be guided by the type of material being worked on.High Speed Steel (HSS) tools were exclusively used up until 1920. After 1960, the use of carbide tools significantly increased. More on the history of cutting tools can be found on this Tool Grades site (n.d.).
With carbide tools, they will typically have a longer tool life, and the tool will be able to endure heat when cutting the part. In the shops today, there are a plethora of inserts to choose from. They come in a multitude of finishes and shapes. Because of this, oftentimes it is the tool vendor that can offer suggestions for productive feeds and speeds to start cutting parts with.
The type of tool selected to make a hole can depend on the finish requirements. For example, if a smooth finish is not needed, then just drilling the hole may be adequate. If it is a deep hole, the drill may “wander” off of its location. This will require the machinist to straighten out the hole by plunging an endmill into it or using a boring bar to open it up. A reamer can follow the endmill process to open the hole slightly more and attain a good finish.
If a tool is unavailable, plans will need to be made, and this happens prior to starting. It is common to find that extra tooling and/or workholding needs to be made to complete the job.
Referencing the Bench Block drawings from 6.1, we can determine that the tools needed are Spot drill, Drills, End Mills, Boring bars, Pinch knurling tool, and Turning tool. These tools should be listed on the planning sheet at the start of the chapter.
6.2.1 Mill tools
If a hole is needed in a part, a drill is used.
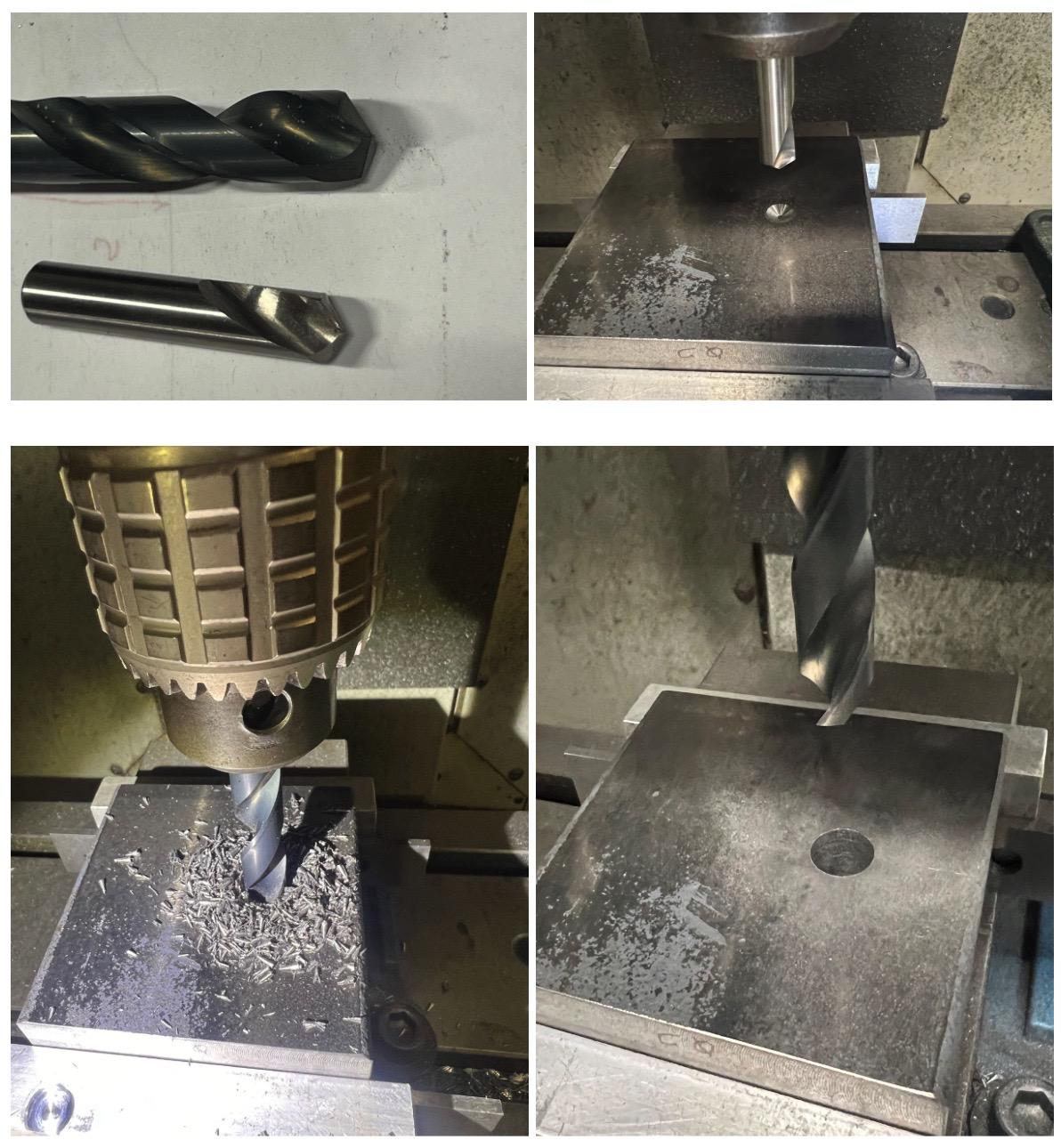
When cutting around the outside of a part, an End Mill would be used. If a large surface needs to be cut, such as the top of the material, a Face Mill can be used. For more information on milling and the tools used, refer to chapter 9.
Tools fall into three sub categories; High Speed Steel (HSS), Carbide, and tools with inserts, also referred to as indexable tools. The HSS tools are susceptible to heat. A ½ inch diameter end mill cutting mild steel will run at 500 Revolutions Per Minute (RPM). A Carbide tool can withstand higher heat and higher RPMs. This tool will turn at 1000 RPMs in the same material. The higher speeds will yield higher productivity with an increase in the cost of tooling.
Tools that have carbide inserts have a higher cost when purchasing the tool holder, but a lower cost when replacing the inserts over time. The RPM of the insert tool will be similar to that of the solid carbide tool in general. All of these accomplish the same thing, material removal.
The tools have to be paired with the type of material that they are cutting. For tools around 1⁄2 inch in diameter, if cutting steel, then use an end mill with four or more flutes. A flute is the cutting edge of the tool, sometimes referred to as a tooth or teeth when there are more than one. If aluminum is being cut, use an end mill with three or less flutes. A face mill can be used to remove the scale from large surfaces. To save material and keep the part as thick as possible, use the surface grinder (see chapter 8) to reduce the amount of material removed.
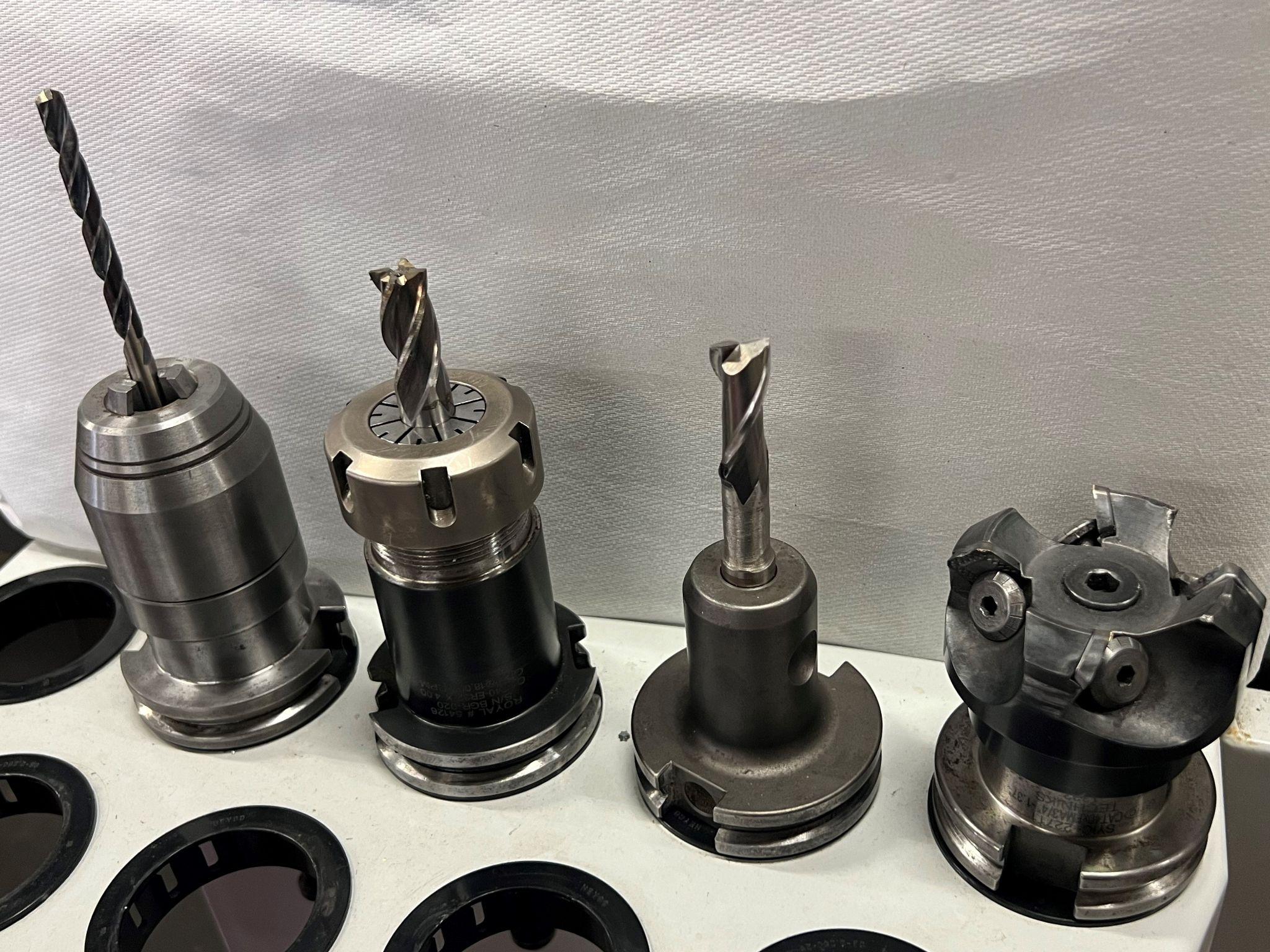
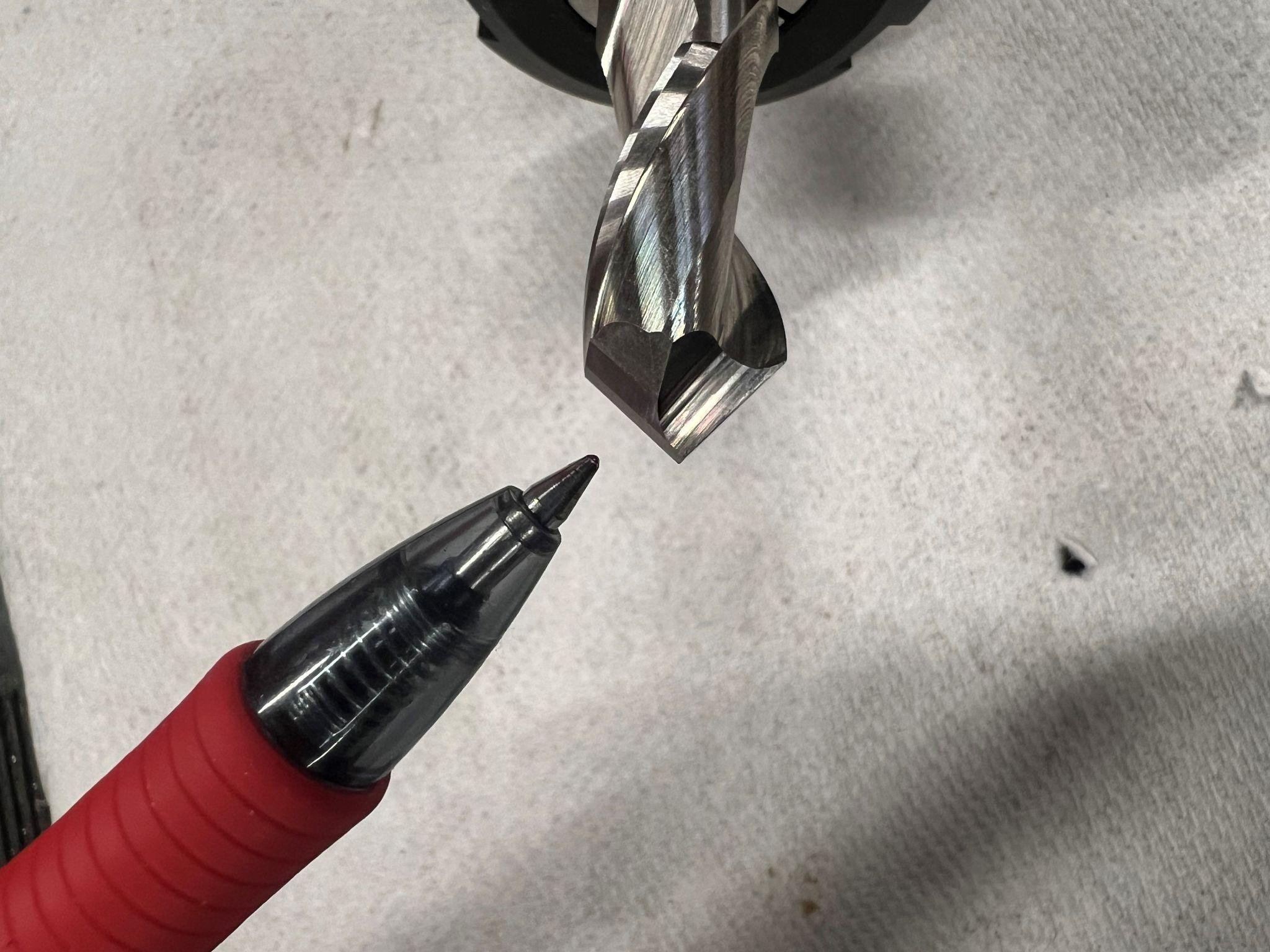
6.2.2 Lathe Tools
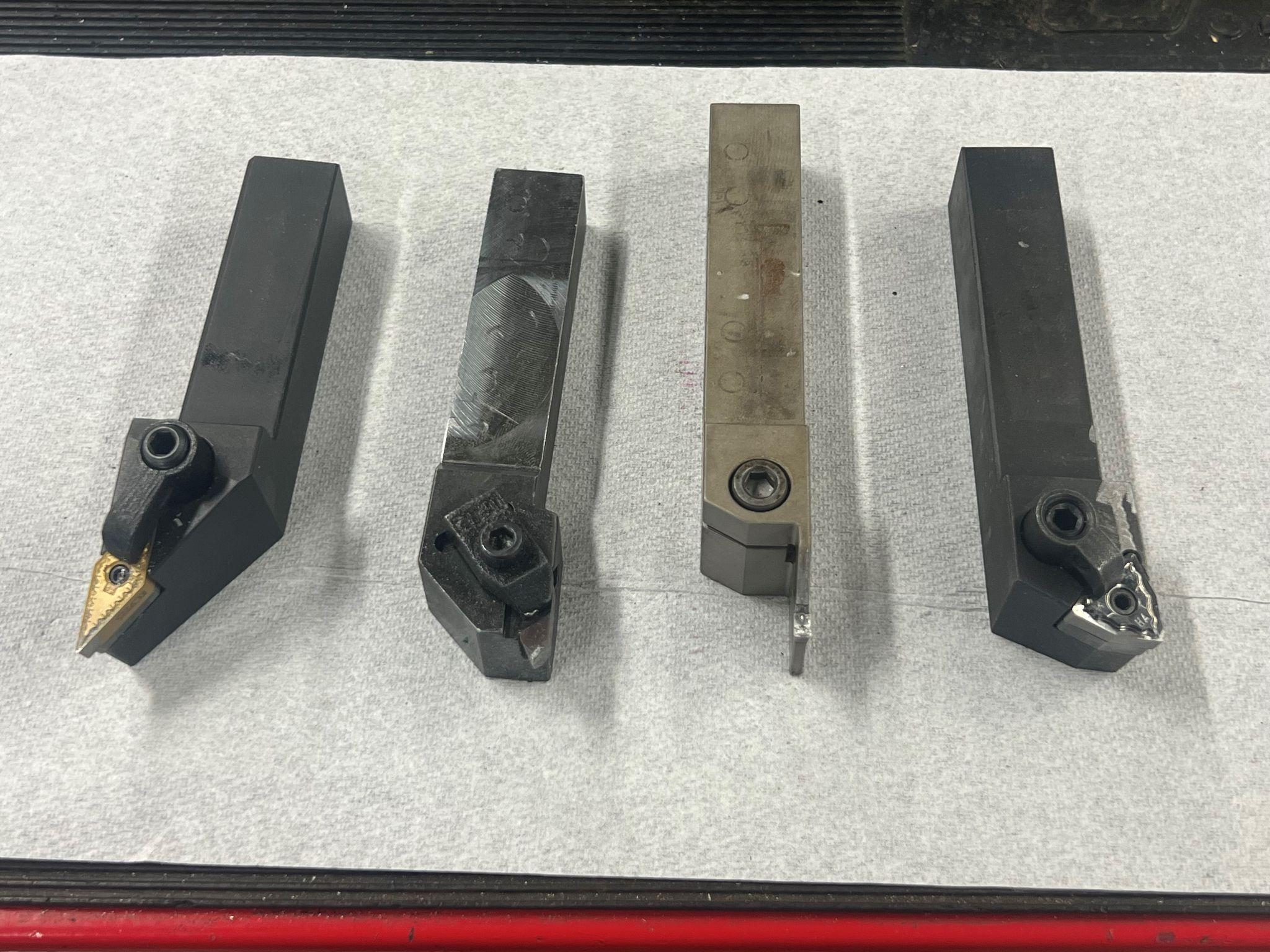
Lathe tools share a common theme but generally have only one point of contact with the part. This type of cut would be called a continuous cut. This type of cut is less abusive on tools due to the reduction of vibration when cutting. Above is a small sample of turning tools. There are also internal tools to create features inside the part.
Our project will use a knurling tool on the left and a turning tool on the right.
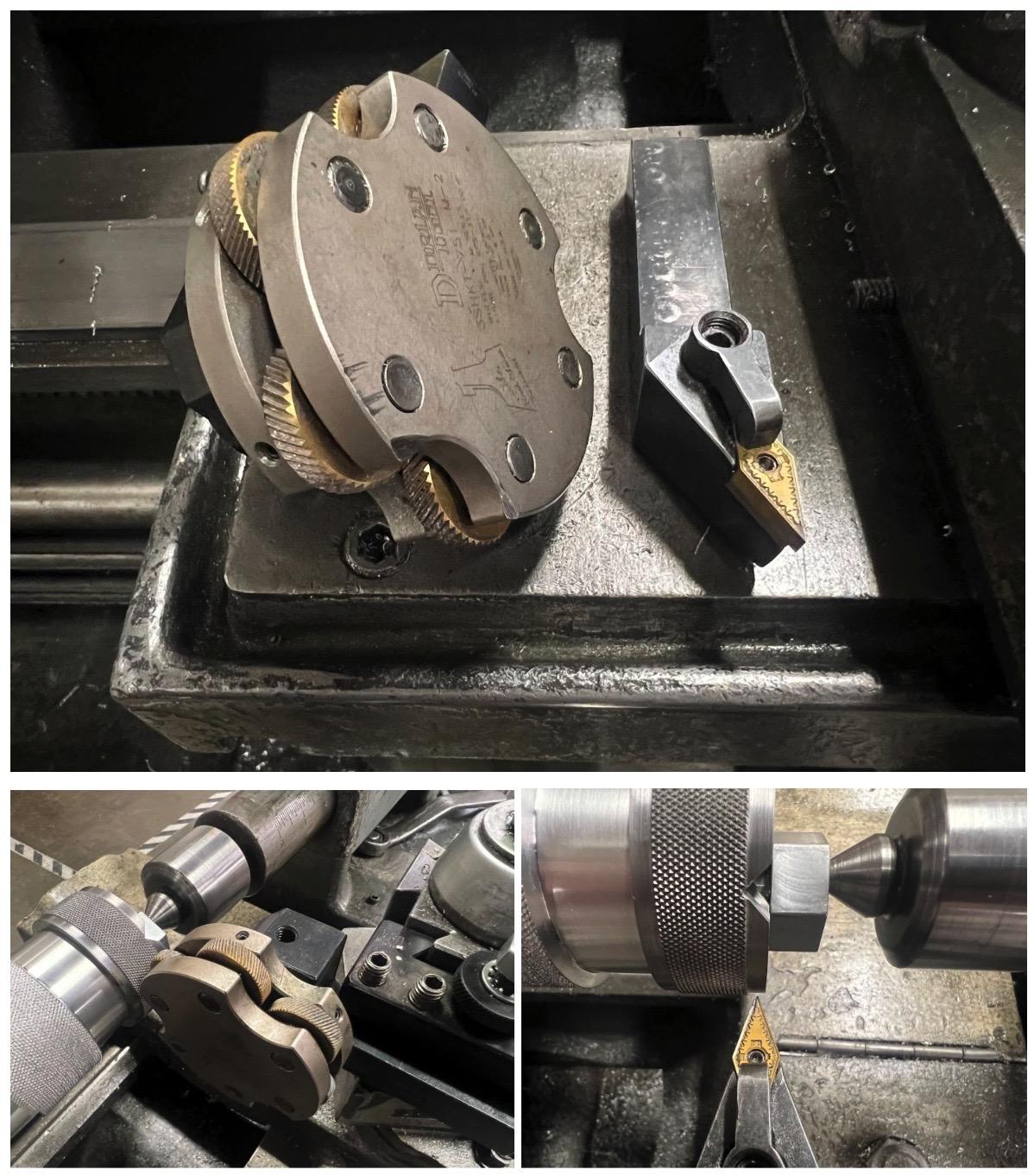
The part will be knurled first. Then the turning tool will cut the relief on both ends. This will provide a clean transition between features. Orient the turning tool so that once it is set up, both sides can be cut.
6.3 Material Selection
Unless it is an in-house job where the machinist has a choice of materials, this selection is mandated by the customer. In the Aerospace industry, customers require specific material for their parts. The certifications that accompany the material establishes that the material being used is appropriate for the job. The type of material required for a part is typically called out on the technical drawing. Common types of material are Aluminum 6061, Mild Steel 1018, Cold rolled steel 12L14, or Acatal.
Aluminum 6061 is a strong, lightweight material that can be used in structural applications.
Mild Steel 1018 is good for fastener parts, and can be case hardened.
Cold drawn 12L14 is a free machining material. This means it is easily machined. It is good for parts that require a considerable amount of machining.
Acetal is commonly used as an alternative to metals. Mechanical gears, electrical components, and medical products are examples of its applications.
Typically, the material callout will be in the title block of the drawing. For our bench block project, we will use 1018 mild steel or something similar.
6.4 Choosing a machine
A machine will be selected for its ability to efficiently remove material, and its ability to repeatedly achieve a consistent tolerance. When “roughing out a part,” the majority of material will be removed in the most productive manner possible. To illustrate, grinders are designed to typically remove around .01 of material at the most. This would not be a good choice of machine if there needed to be .5 inches of material removed. For a hobbyist, the enjoyment might come just from the process of removing material. If this job is connected to employment, there will be a time limit in which to produce the part.
Referencing the picture of the bench block in Section 6.0, you’ll note that it is round. The outside shape of the part being made is called the profile of the part. The sample bench block we are making is made of 1018 mild steel, which comes in a flat bar that is band sawed into smaller squares so that the machinist can handle the part as it is being made and the material isn’t wasted. If the outside of the profile is cut first, it will be more difficult to hold on to because a circle requires special tooling for workholding. This means if you immediately start cutting a circle out of your material, you will create more work, and the part will take more time to produce. From what we see of the bench block, the vertical mill is the machine that will be used for this project. This is an example of why it is necessary to do job planning before beginning the part. Efficiency equals profitability.
Machine Capability is the natural accuracy a machine can hold when making parts without user influence. All machines are not created equal. A band saw might be used for the first step of cutting a block of material to +/- .06. If the requirements were +/- .01, a table saw might be chosen as it is more accurate. The same conditions exist in machining and are referred to as Machine Capability. When deciding on the machine to use, consider the tolerance requirements and pair them up with a machine that is capable of achieving those results. Machine capability can be aligned with the technical requirements to help establish a productive process. A profitable operation will factor in material usage and conservation. For large quantity jobs, the project should be revisited for optimization after the process has been validated.
Making 100 of the same part is different from making 1 of that part. When the number of parts increases, repeatability and reliability need to be considered. The plan may also shift to one that has batch processing, where a small number of features are cut on all parts before continuing instead of making a complete part one at a time.
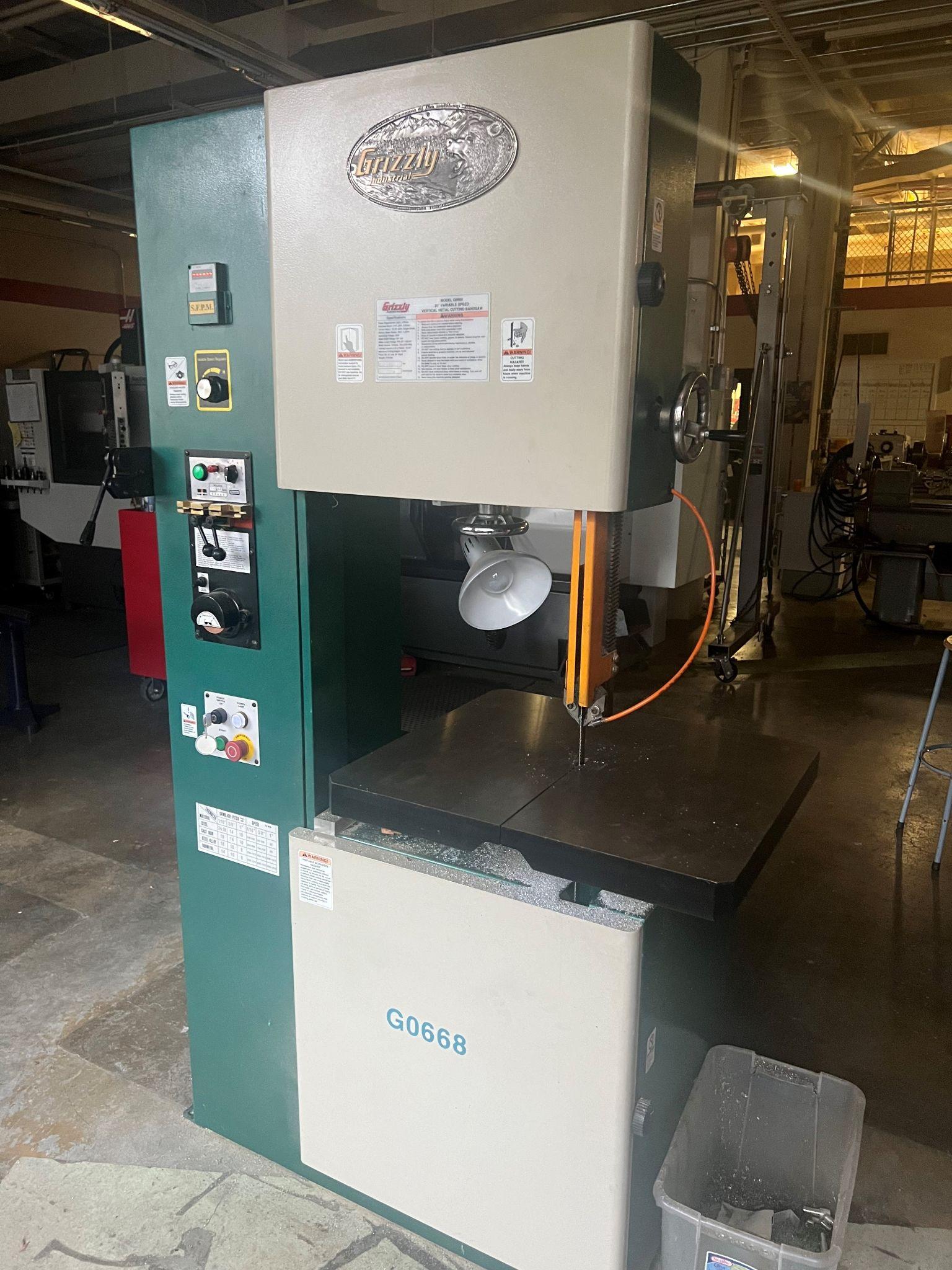
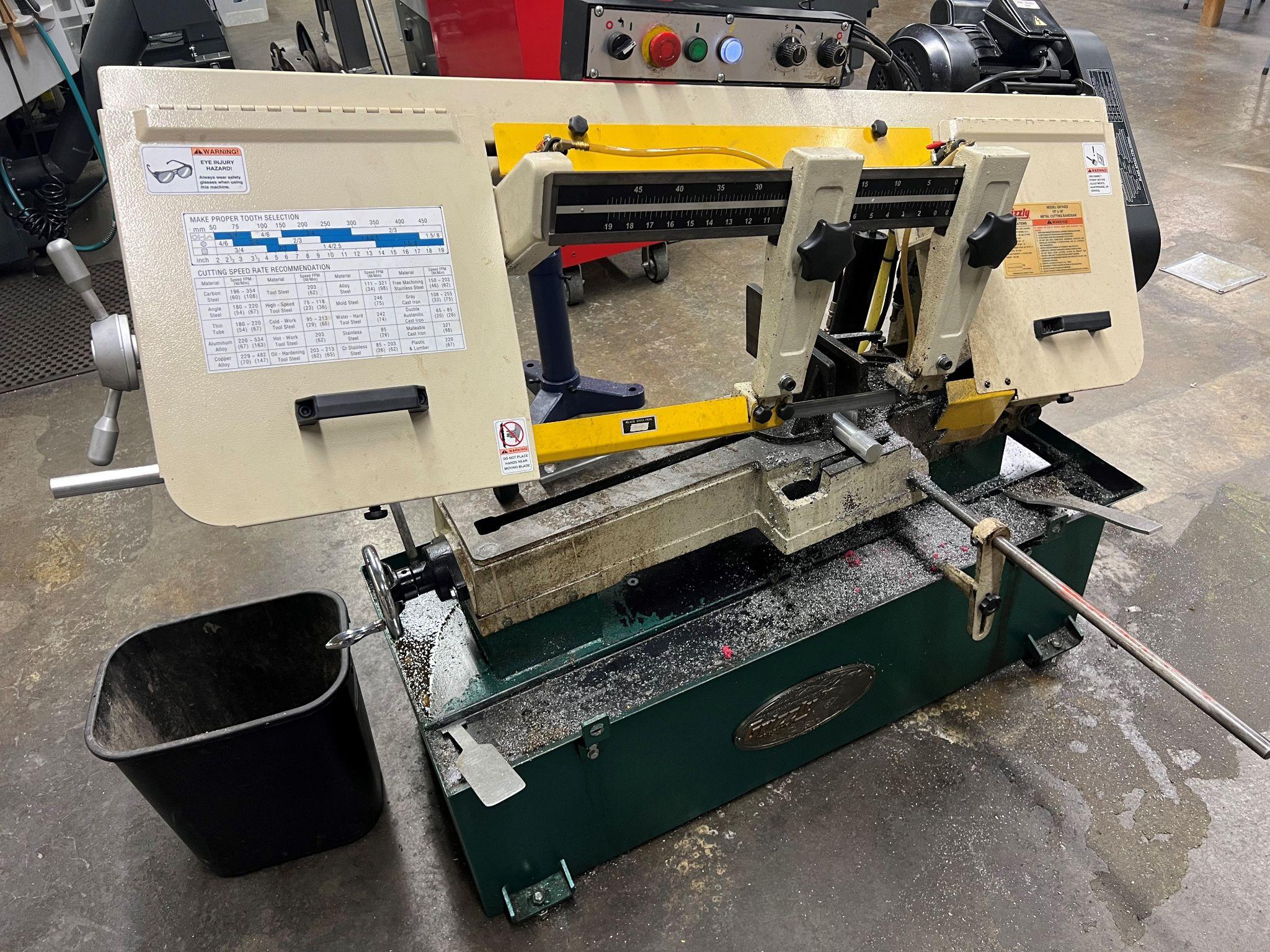
Choosing the right machine for the job requires a comprehensive understanding of the machining process, materials used, tooling, equipment, and the ability to comprehend technical drawings accurately. By meticulously planning each stage of the machining process, potential risks and challenges can be anticipated. This will help to improve productivity, efficiency, and overall success.
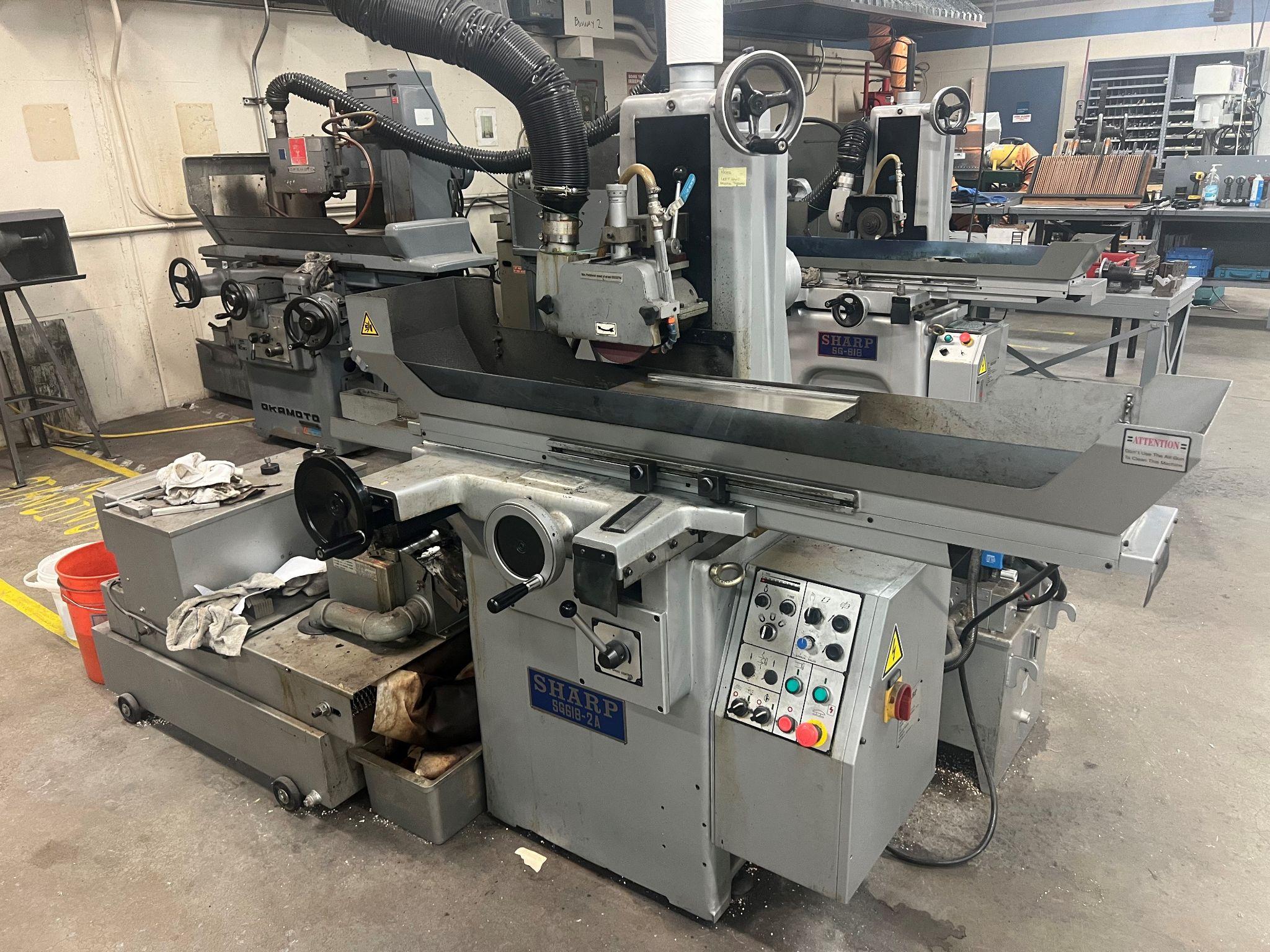
A surface grinder can achieve an almost mirror finish with tolerances less than the thickness of a piece of paper (.003). A band saw, mentioned earlier in this book, can cut parts to within 1/16th, or .0625. Spoken as sixty two and a half thousandths.
The accuracy difference between machines is referred to as Machine Capability. It will be beneficial to pair a job with a machine that can easily meet the requirements of the part.
We will create a project plan for the Bench block to be made with Manual machines because we are only making one. If we had to make 100, we might want to automate the process by using CNC machines.
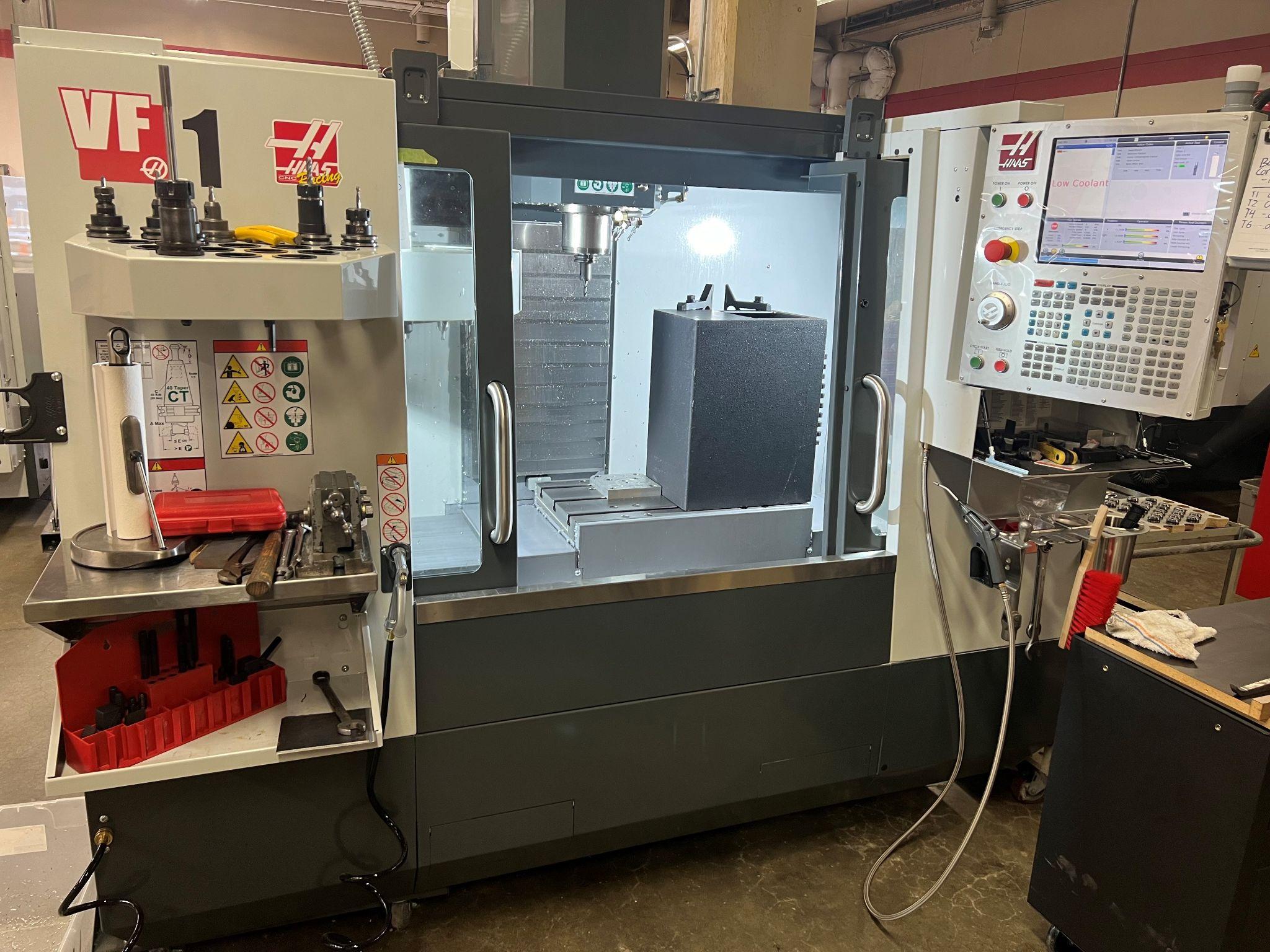
Indicators for this choice would be large quantities, high precision, and repetitive actions. Typically, when bidding on jobs, the greater the technology of the equipment, the higher the cost to the customer. If the part can be made by Manual machines, the cost to the customer could be $150 per hour. If a CNC mill was used, the customer might be charged $500 per hour. Machines that have automation or are controlled by computers are capable of running more efficiently with higher, more consistent accuracy.
Outside processes, sometimes referred to as Secondary Operations are a consideration when planning. A part might be only partially finished. Material is purposely left on to be removed later, then sent out for heat treating to improve the characteristics of the material, such as hardness. Upon returning to the shop, the rest of the material is removed. Some other Secondary Operations are painting, anodizing, and polishing.
6.5 Work holding
As the job plan is developed, a critical aspect of the project is how will the part be held? The primary choice is between a mill and a lathe. The following sections will introduce workholding on these machines.
6.5.1 Mill workholding
Two of the most common ways of securing a part on a mill is to use a vise, or a system of strap clamps. The list of types of workholding possibilities is exceedingly long. The main two objectives when on a mill are to hold the part down, and keep it from spinning. Ensure that the setup is secure before starting to cut the part.
The vise is a mainstay in just about every machine shop. The way in which the part is held will also depend on how aggressively the material is being removed. In a regular vise, the compressive forces, and friction keep the part in place. To increase the holding power, a dovetail design is used. This can result in less engagement of the vise jaws and allow more of the part to be worked on.
The vise jaws can also be cut into a pattern that matches the part. This is called creating “form jaws.” Form jaws will increase the surface area and the friction that is keeping the part from moving. Mill workholding will be covered in greater detail in Chapter 9.
On a lathe, there will be a three, or four jaw chuck (there are others). There may be an option for a Collet chuck. The main difference is that a collet is going to retain concentricity better than a jaw style chuck if the part has to be taken out and put back into the machine. More detail on lathes and workholding will be covered in Chapter 10[crossref].
(A vise holding a part on a mill)
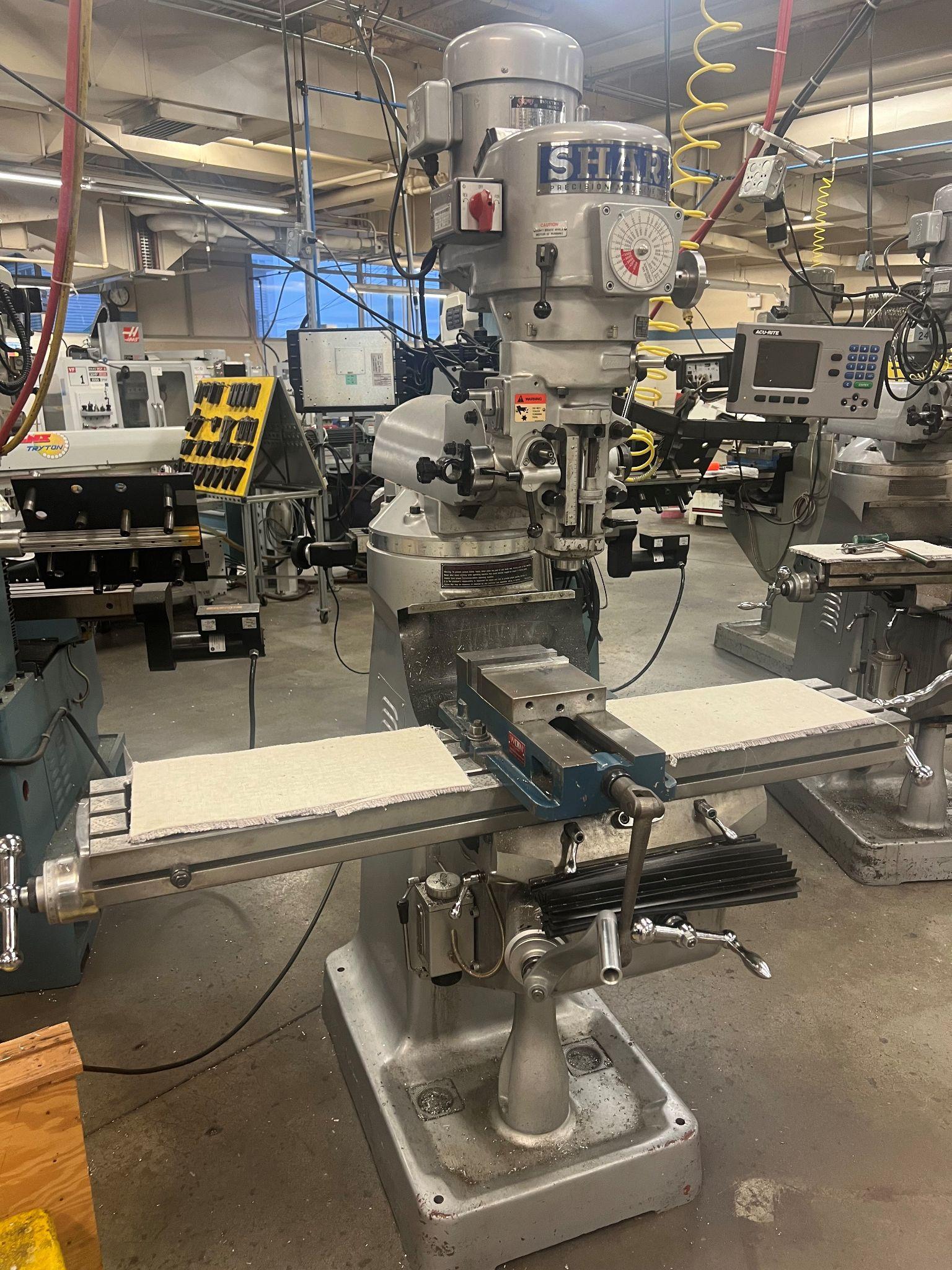
Holding parts is greatly influenced by how much extra material is provided from the supplier. If a customer provides minimal material, it will be more difficult to make the part due to the challenges of holding it while it is being cut.
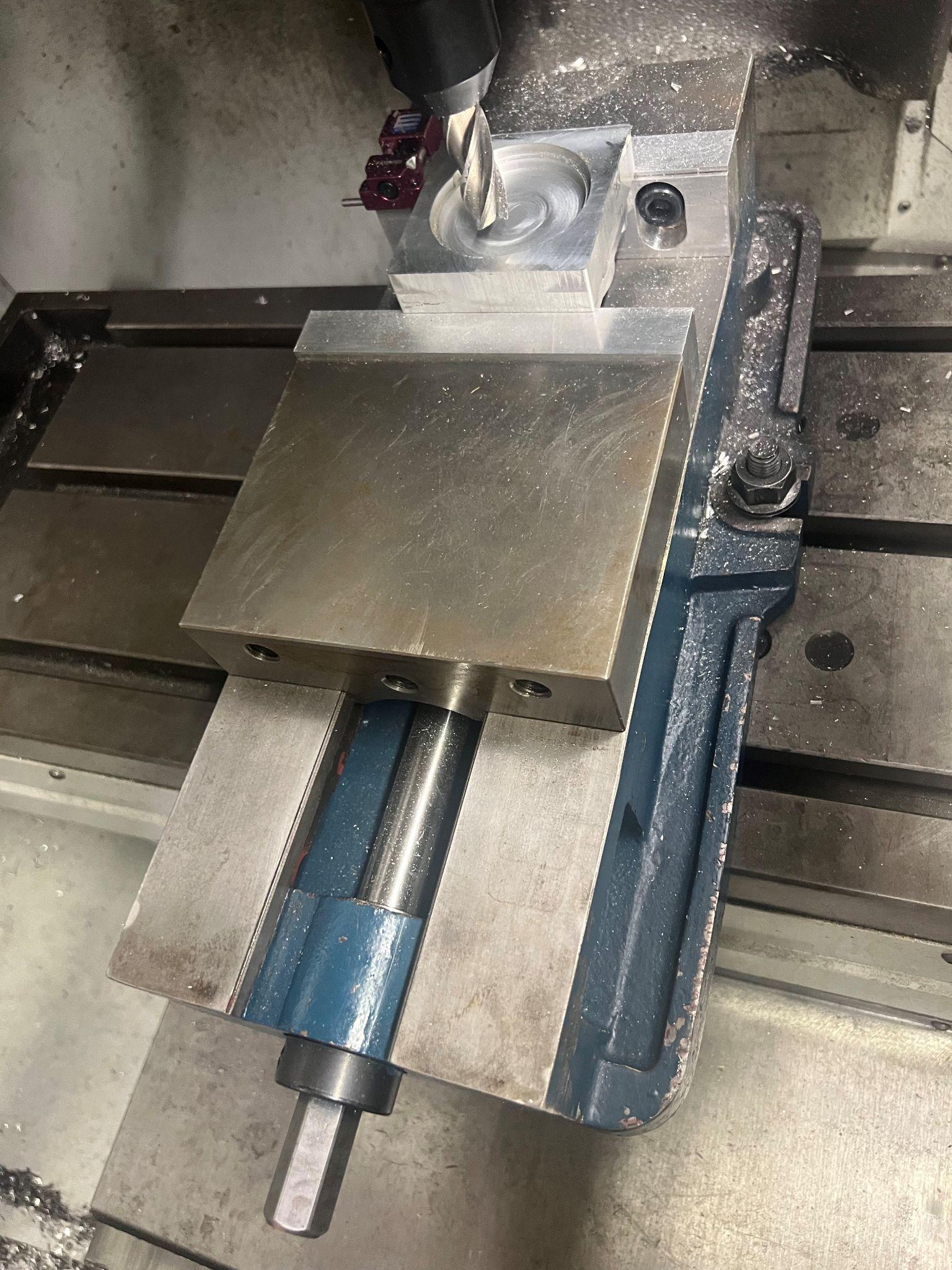
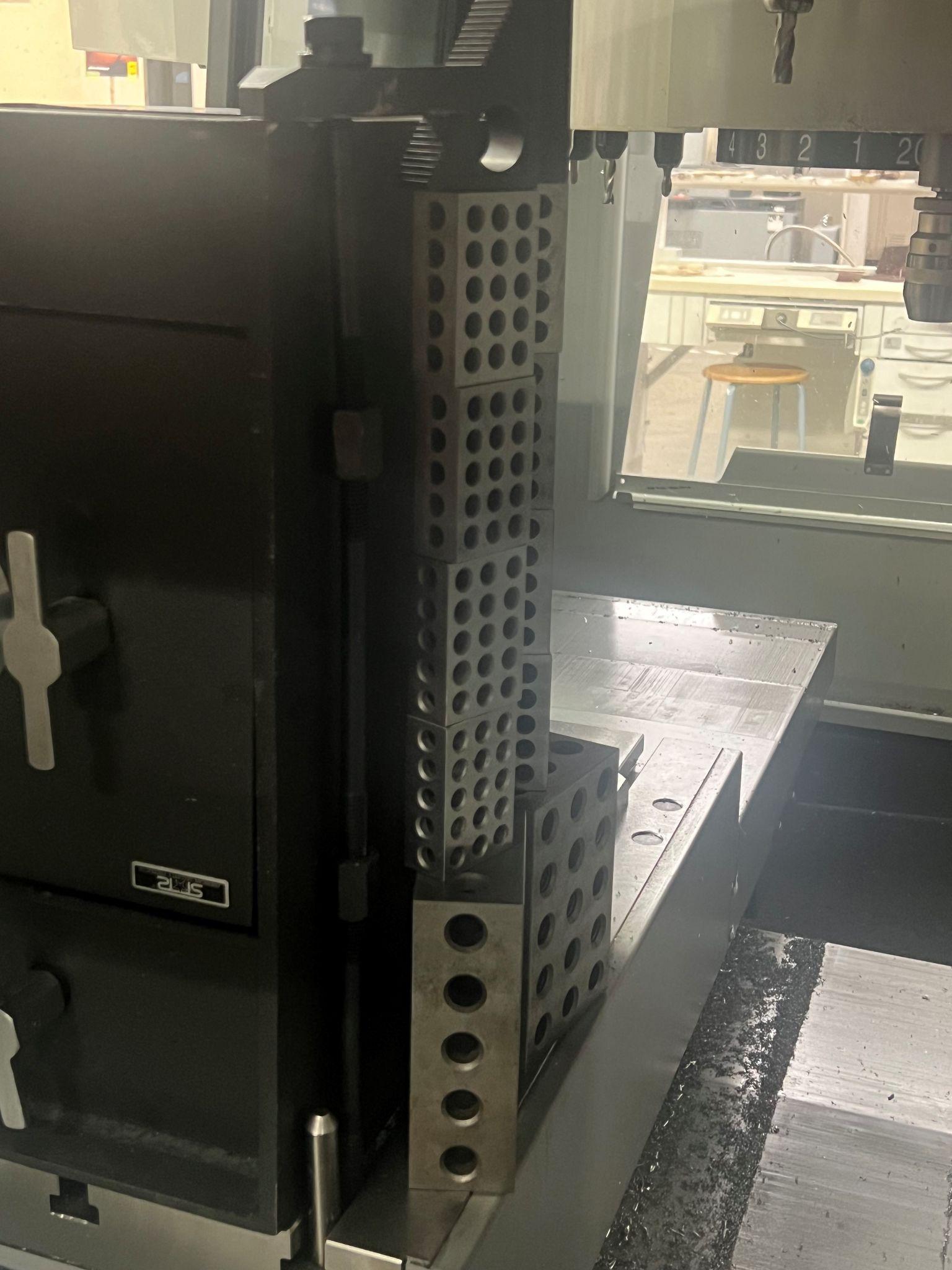
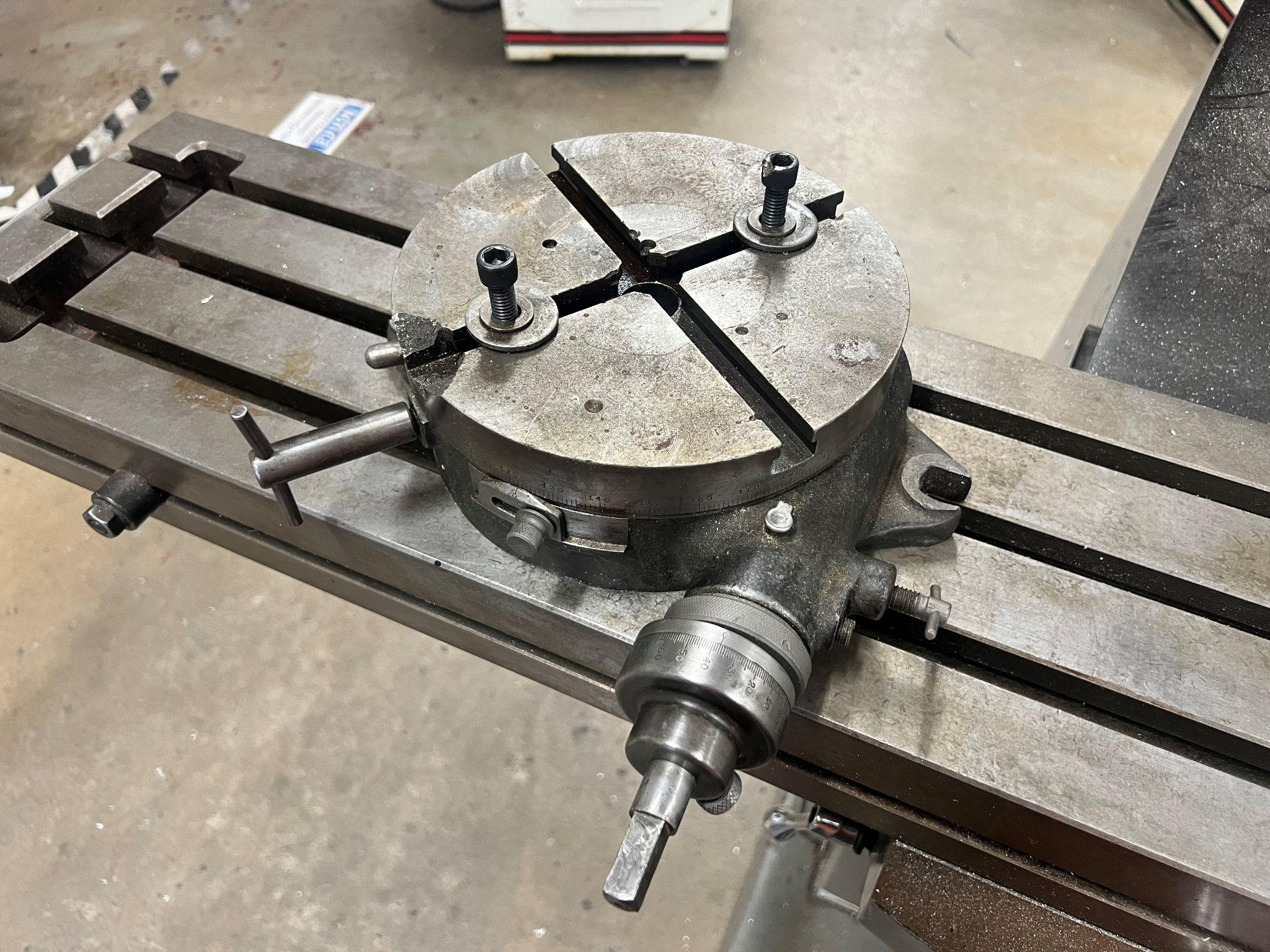
Pictured above is a rotary table. Mounting this to a vertical mill will allow the part to be rotated while being cut for circular features.
6.5.2 Lathe workholding
The three common ways of holding parts on a lathe are to use a three jaw chuck, a four jaw chuck, or a collet chuck.
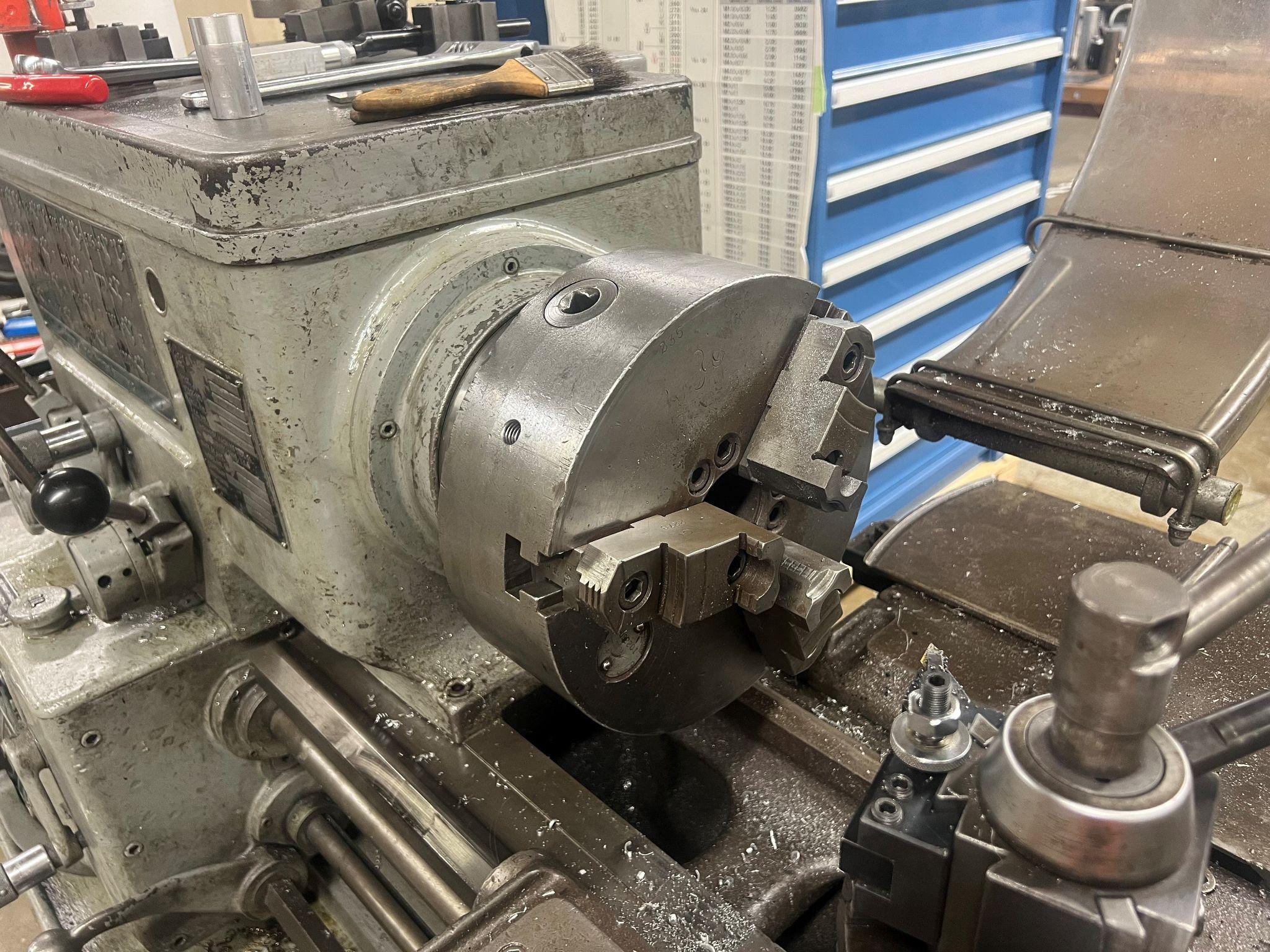
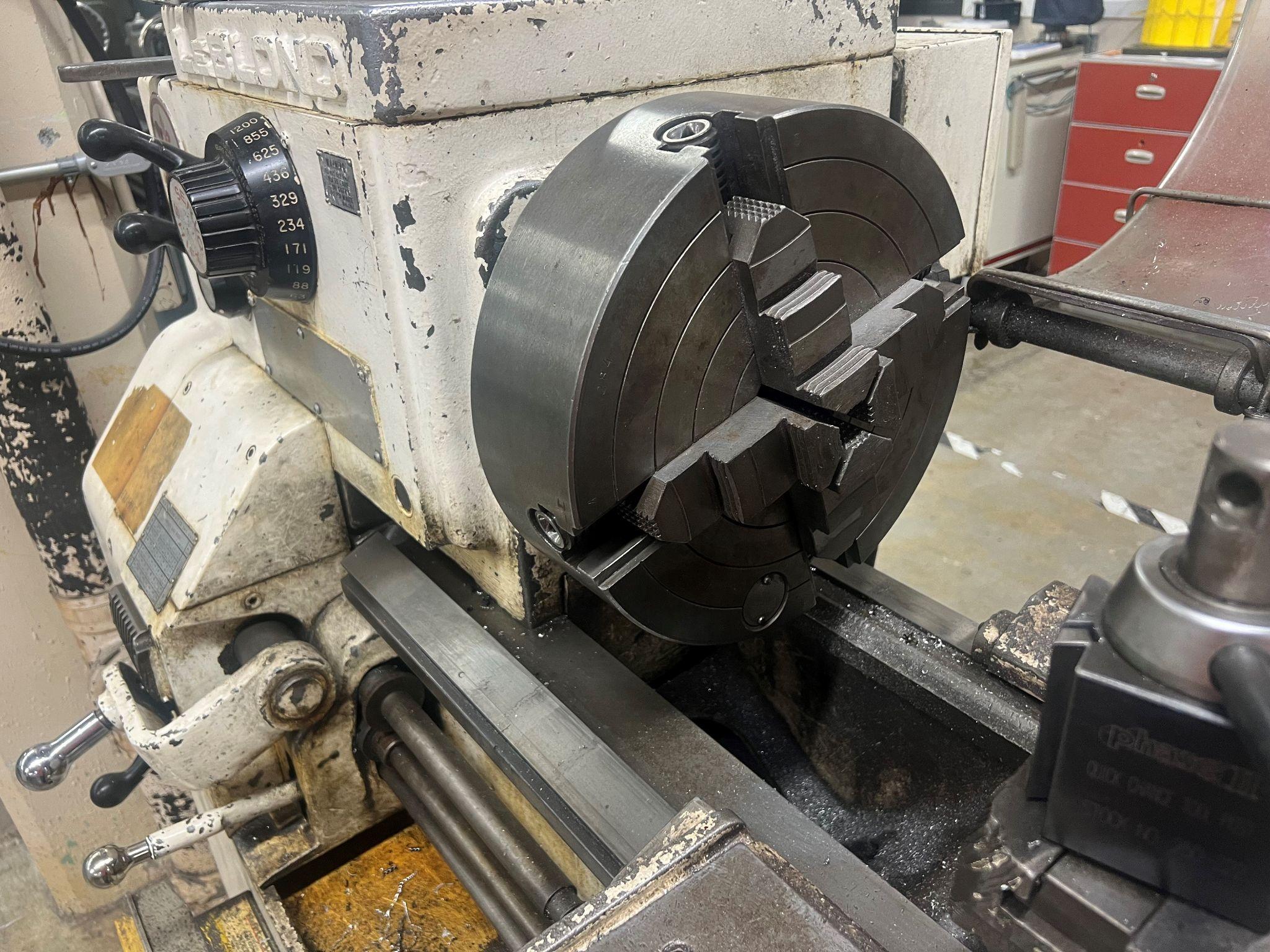
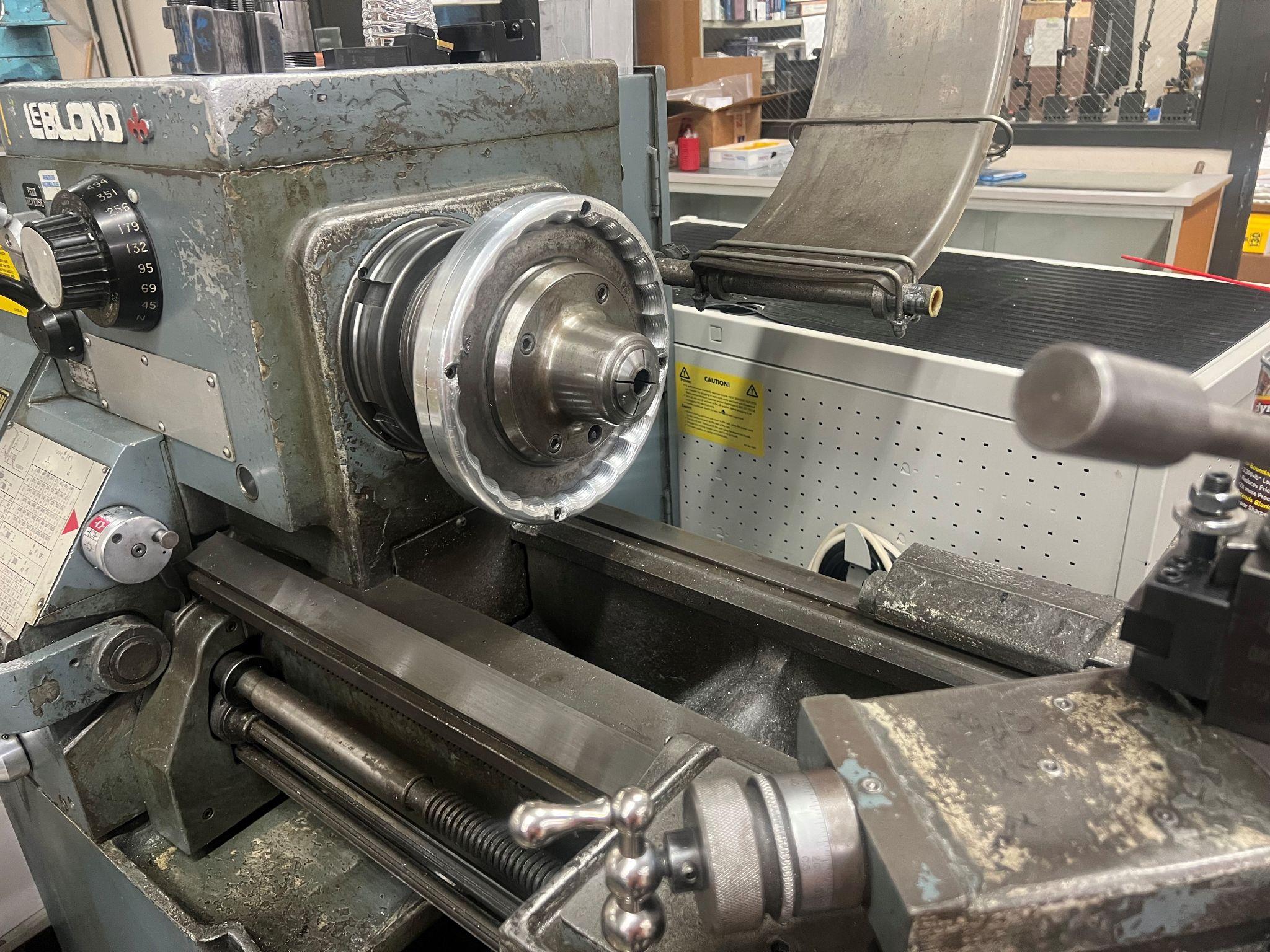
The three jaw chuck centers up the part when clamped, but is not as accurate, or repeatable as a collet chuck. Use the collet chuck for clamping on finished surfaces to retain minimal runout. The four jaw chuck is ideal for square parts, and can be dialed in to ensure that they are centered up on the chuck. The downside is that it takes more time to set up.
6.6 Documentation
6.6.1 Keep notes
Taking notes is a lost art with today’s machinists, but it still has value and a purpose. The more complex a job is, the more steps need to be remembered. A Machinist will come to appreciate the process of thoroughly thinking, visualizing the complete job, and writing down the steps. The documentation will help to ensure consistency if multiple parts are needed. Planning out the job will also provide a list of tools to gather before starting the project.

6.7 Application
6.7.1 Reading the drawing
When looking at the technical drawing, specific information such as tolerances, and finish requirements will help determine the process used to create the part. It is important to note that tolerance can be viewed subjectively. A person cutting blocks of material to be supplied to a machine shop may have +/-.06 for tolerance. So, a tolerance of +/-.01 would require an extra amount of attention and effort to achieve. At another shop, they routinely make parts that are +/-.001. To them, a +/-.01 is nothing to worry about.
The drawing will typically state the type of material required to be used for the part. A machinist could choose the material to use if it was for a fixture to be used on a job. The bench block job will require a fixture to complete the part. Other customers may provide the material that is to be used for the job. This may indicate that the material is expensive, and/or that there isn’t any extra material in case a mistake happens. If this is the situation, it is allowable for the machinist to again choose a piece of material to make a first part, provided that it is clearly marked as a setup part. The part must say “set up” or NCM (non conforming material) on all sides, and be visible at all times. Remember, ensure you have the correct material before starting. Whenever you are unsure, ask, and take notes so you don’t have to ask again.
Making a part for the first time for even a Journeyman Machinist is a learning process. Learning from the mistakes that may happen is part of the learning process. If a mistake is made, try to save the part by repairing it. This will improve problem solving abilities. Learning from the choices made will also aid in future decisions.
Sample Job Planning List of Operations for the Bench Block
Project Planning For |
|||||
Sequence |
Feature |
Holding |
Machine |
Tooling |
Notes |
1 |
Grind |
Magnetic Chuck |
Surface grinder |
|
Minimal Material Removal |
2 |
Spot Drill |
Vice with parallels |
Vertical Mill |
Add step to square up stock |
|
3 |
Drill |
Vice with parallels |
Vertical Mill |
|
|
4 |
Bore |
Vice with parallels |
Vertical Mill |
Adjustable boring head |
|
5 |
Groove |
Vice with parallels |
Vertical Mill |
Flat End Mill |
Tilt head to 45 deg |
6 |
Counter Bore |
Vice with parallels |
Vertical Mill |
Flat End Mill |
Rotary Table |
7 |
Profile |
Through holes with fixture in three jaw |
Vertical Mill |
Flat End Mill |
Rotary Table |
8 |
Knurl |
Through holes with fixture in three jaw |
Lathe |
Pinch Knurl Tool |
|
9 |
Turn |
Through holes with fixture in three jaw |
Lathe |
Turning tool |
|
|
|
|
|
|
|
1.5 |
Square up stock |
Vice |
Vertical Mill |
Face Mill |
|
option |
Counter Bore |
Three jaw Chuck or Form jaws |
Lathe |
Boring Bar |
|
option |
Profile |
Through holes with fixture in three jaw |
Lathe |
Turning tool |
|
|
|
|
|
|
|
|
|
|
|
|
|
Here are the steps to create an individualized project plan:
- Create a spreadsheet for the different features that need to be cut.
- Set up a table with five columns on the page.
- List the different features that need to be cut in the first column. For example, having holes in a part will require a spot drill to start the hole.
- Select the appropriate drill to complete the hole. The size after drilling will indicate whether or not a boring bar is needed to make the hole larger to meet the dimensions on the drawing.
- Organize the list into a sequence. For example, the holes need to be spot drilled before drilling through the part.
The second column describes how to hold the part. The third column will specify the machine where the work is being done. The fourth column will be for tooling. The final column is used for any specific notes. A special note might be to call out a specialized piece of equipment, such as a Rotary Table. The Rotary table can be mounted on a Mill with a vise on top of the table. By turning the handle, an arc or circle can be created when milling.
Number the features to indicate the sequence in which they will be cut. This process may have to be rewritten a few times until the order makes sense. Creating a job plan is ultimately about deciding what features to cut in the best order. If the square piece of material is cut into a circle, it will require more work and special tooling to hold the part to continue working on it. If the V groove is cut before the holes are drilled, when the drill starts to cut into the V, it will bend and move off of its location. This will damage the tool, the part, or both.
Minimal material is to be removed on the large sides of the square. Cutting the scale off the material may take up to .05 inches off of the overall thickness. Grinding should be used for this step to retain the most material possible.
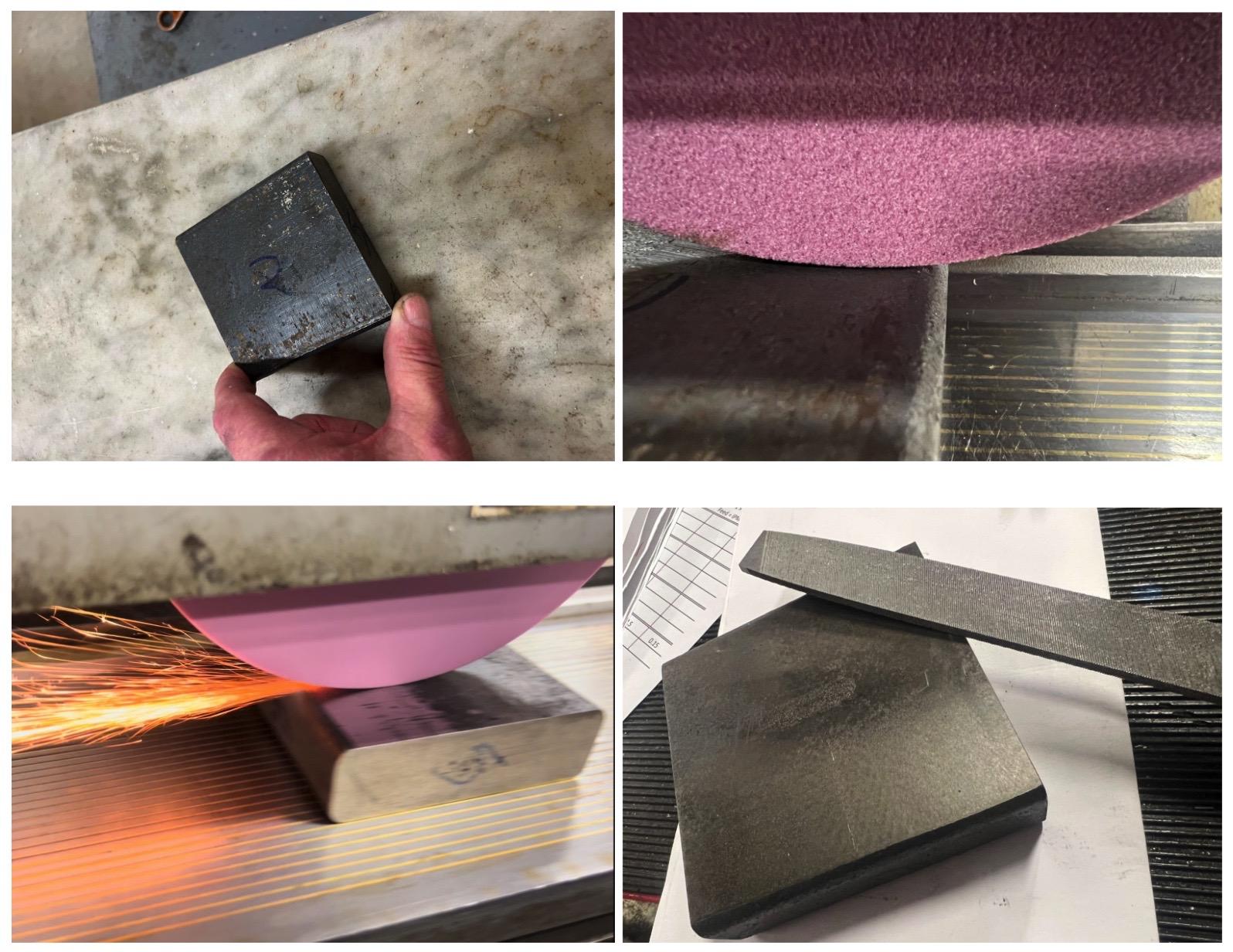
Cut the four 1.0 inch thick sides of the square so that the opposite sides are parallel. This will allow the part to be better held in a vise so that further work can be done.
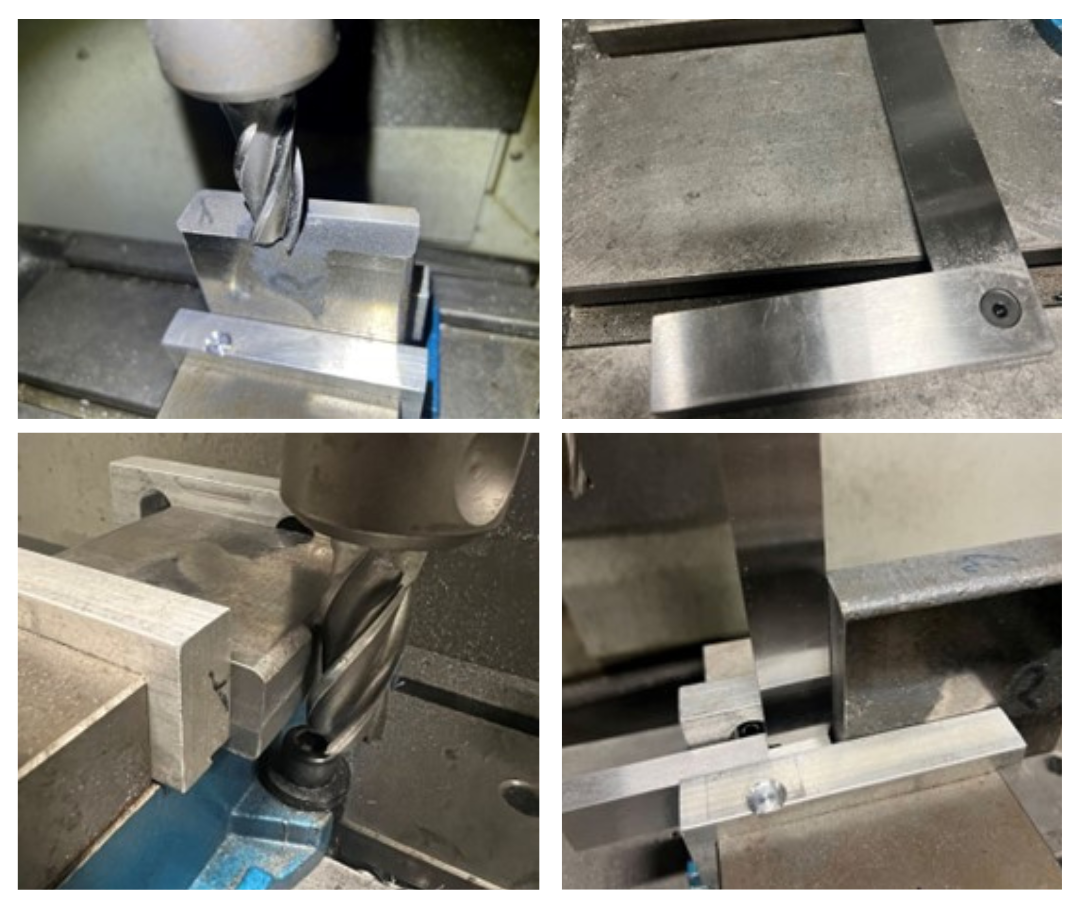
Spot, Drill, and Bore the holes before the groove is cut. Drilling into a slanted surface like the V groove will make the drill bend, and the hole will have a step in it. Trying to drill into a slanted surface is an advanced technique that requires cutting a flat spot into the slanted surface to provide a suitable area to start drilling.
Cut the groove on the top of the part by nodding the head of the mill to 45 degrees. More information about this may be found in [crossref:11]Chapter 11.
A rotary table on a manual mill could be used to rotate the part while cutting. This would create the pocket on the bottom of the part. Another option is to hold the part in a three jaw chuck on a lathe, and use a boring bar to make the pocket.
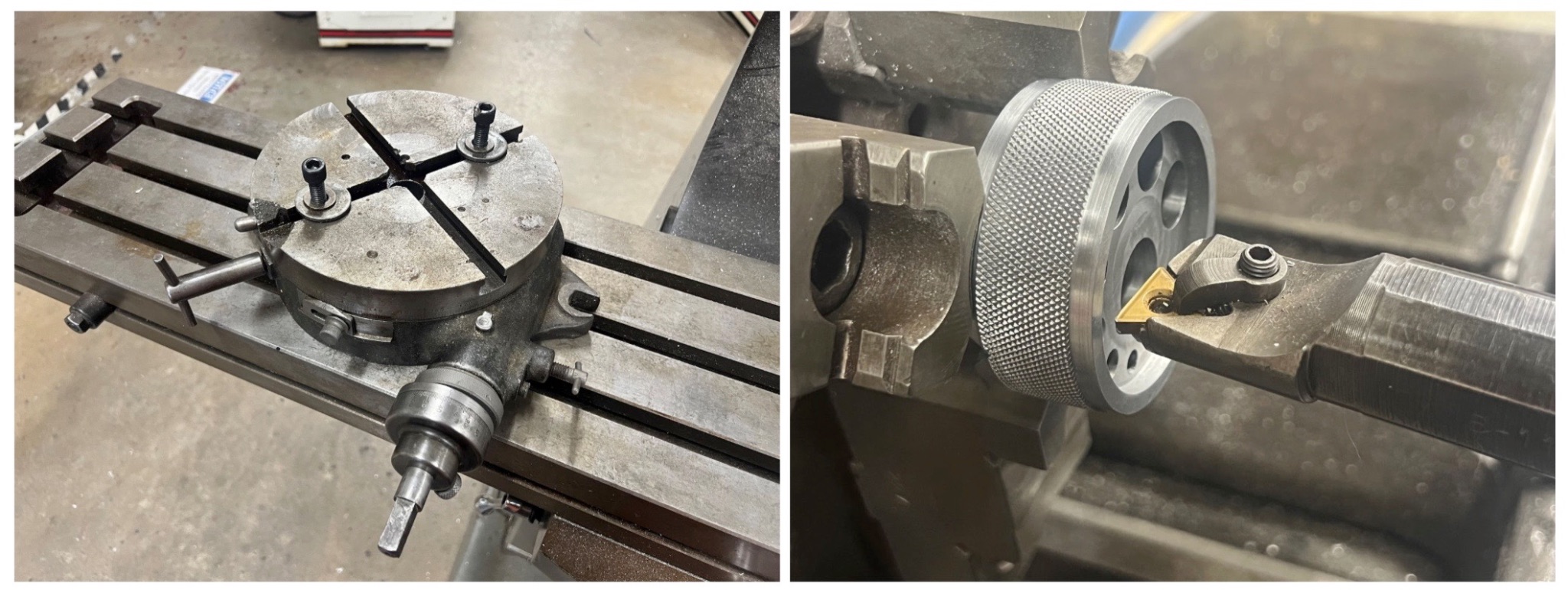
AUTHOR’S TIP
The pocket on the bottom of the part is to allow chips from tapping to exit the hole instead of being dragged up through the bench block.
At this point, a fixture will need to be built to hold the part using the holes that were created. This will allow the outside of the part to be turned down on the lathe.
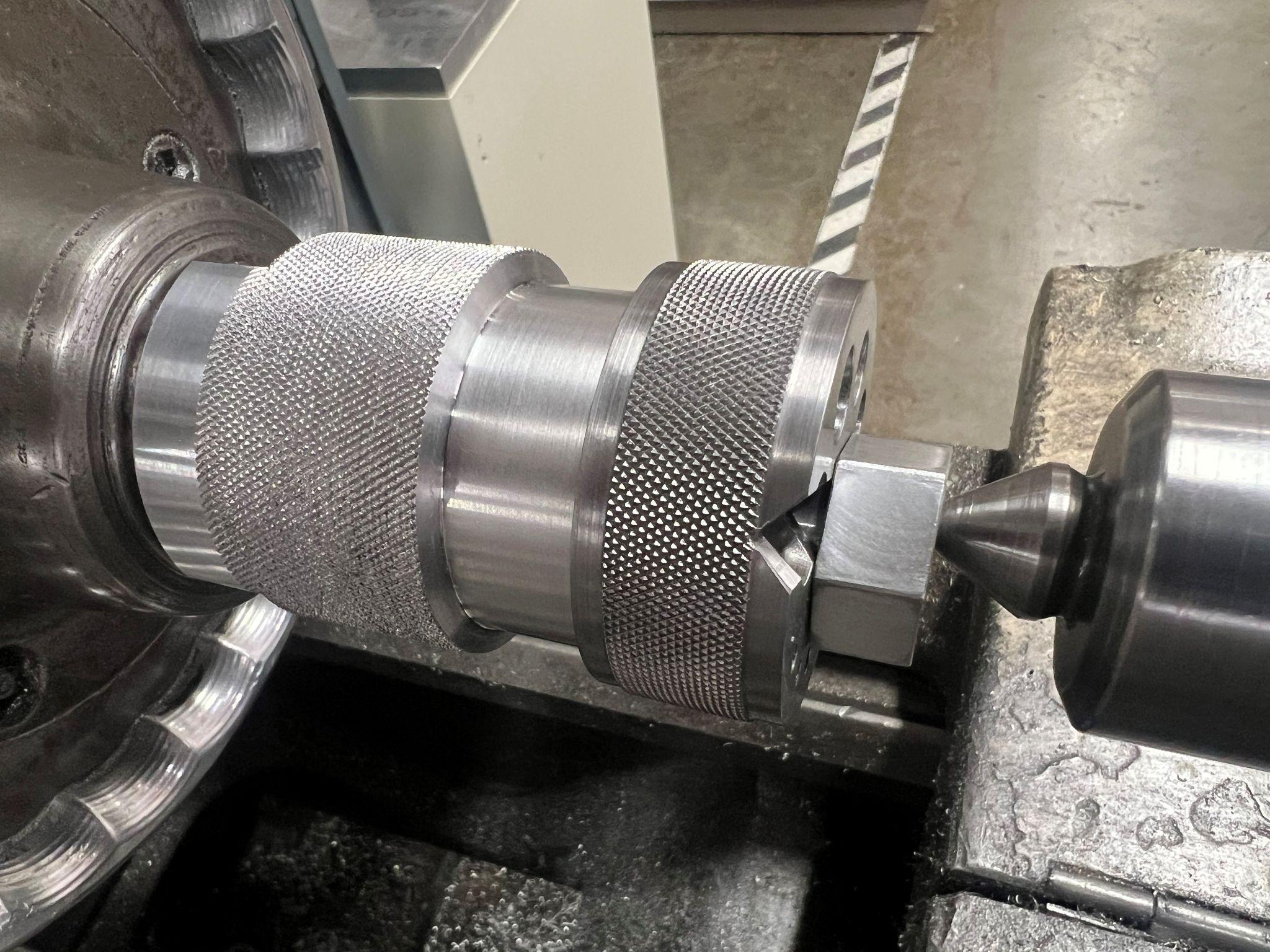
Turning the square into a circle can be done on the lathe next.
Knurl the outside of the round shape
Turn the steps on the outside.
6.7.2 Find the Tools
Once the planning is set, make a list of the tools needed and gather them up. This is when changes may need to be made. If a tool is unavailable, the choice may be to buy one. But that usually takes time that you don’t have. Making or modifying a tool is a possibility, depending on your skills. Likely, the quickest solution is to substitute. For example; the bench block calls out for a 6.5 mm drill. The holes are toleranced at -0/+.002. The 6.5 mm drill measures .256 inches. So a letter F drill, which measures .257 will work and still be within tolerance.
6.7.3 Material
This specific project is made from mild steel, though given the different levels of resources at various training institutions, a different material may be substituted. Recall that this information is typically found in the title block of the drawing.
6.7.4 Machines, Workholding
Identifying the machine to use and how to hold the part can happen together. For example, if a lathe is chosen as the machine, the part will likely be held in a three or four jaw chuck.
Every machine is different; they have their own capabilities. This is the accuracy at which a machine will cut parts without any significant effort from the machinist. Influencing the process may entail artificially controlling the temperature as a means to control material expansion. Heat can build up in the part, or it can be generated from the machine that is cutting the part. This can make the part measure bigger than it really is when at room temperature.
Different processes will produce different finishes or surface qualities. Depending on the requirements of the part, an acceptable finish may be obtained from the initial material removal. A higher quality of finish can demand that a subsequent machining process is needed. This bench block project will adhere to the industry standards of a 32 micron finish or better. Please refer to Chapter 3 for further discussion of finishes.
One of the first concerns of a machinist should be to ask, “How tight is the tolerance?” Do I need to make a cut that is less than a sheet of paper thick? This would be within .003, spoken as three thousandths. Or, do I need to make a cut within an 1/8th, .125 of an inch? (Spoken as one hundred and twenty five thousandths.) The degree of precision will start to bring into focus the processes, and tools needed to make the parts.
Using a surface grinder will remove the least amount of material. The part can be held with the magnetic chuck to accomplish this. Grind the large surfaces first. This will provide an accurate locating surface when holding the part in the vise when cutting the smaller sides.
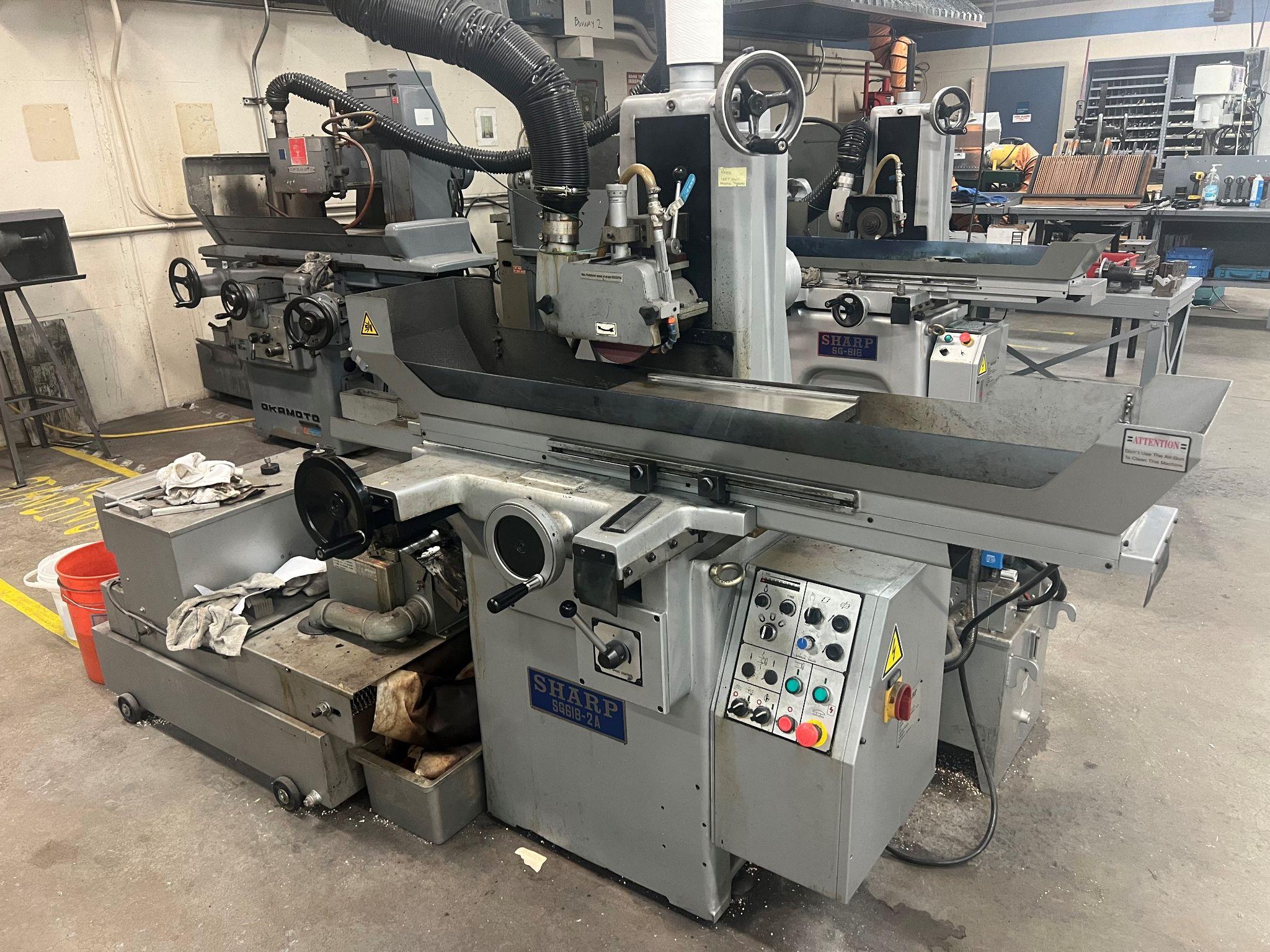
Using a face mill, or end mill, the short sides can be cut so that the opposite sides are parallel. This can be done in the mill while holding the part in a vise.
Drill, End Mill 4 flute, and 2 flute, Face Mill with inserts. / Photo Credit: by T Bacon, for WA Open ProfTech, © SBCTC, CC BY 4.0
At this point, any scribe lines that were on the part are gone. Layout the center, the orientation of the V groove, and the width of the V groove before continuing. For more discussion on laying out a part, turn to chapter 5.
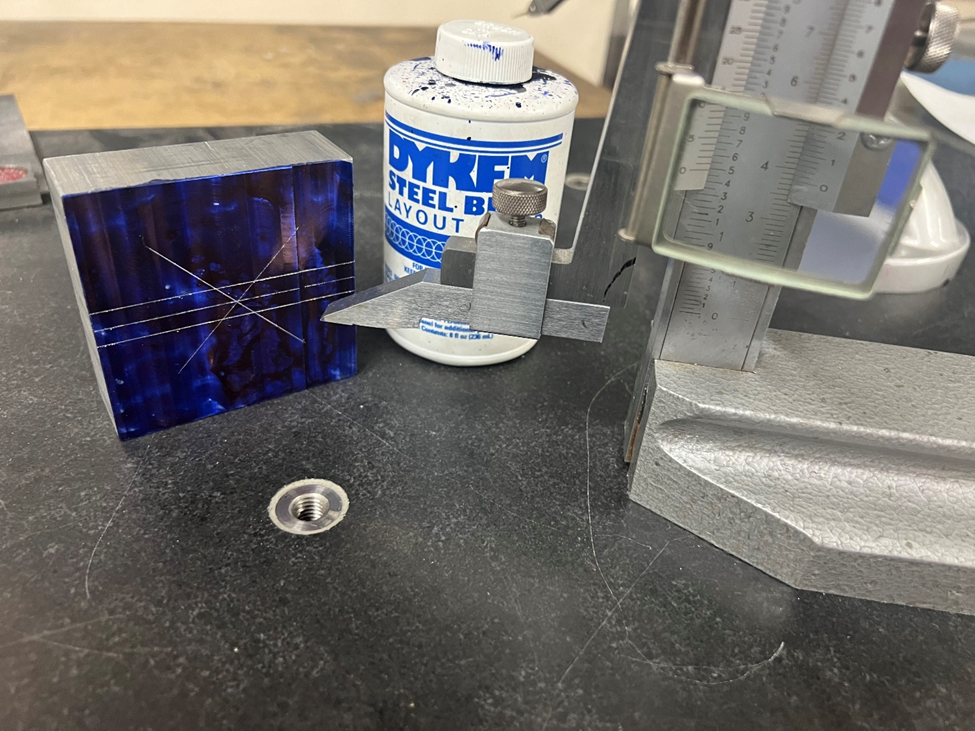
Put the part in the vise on the manual mill to drill the holes. Find the center of the part, and then move to the first hole location. To increase accuracy, and cut down on the work of locating each hole multiple times, complete each hole before moving to the next location. Locate the hole, spot drill, drill, and bore if needed, then move to the next hole.
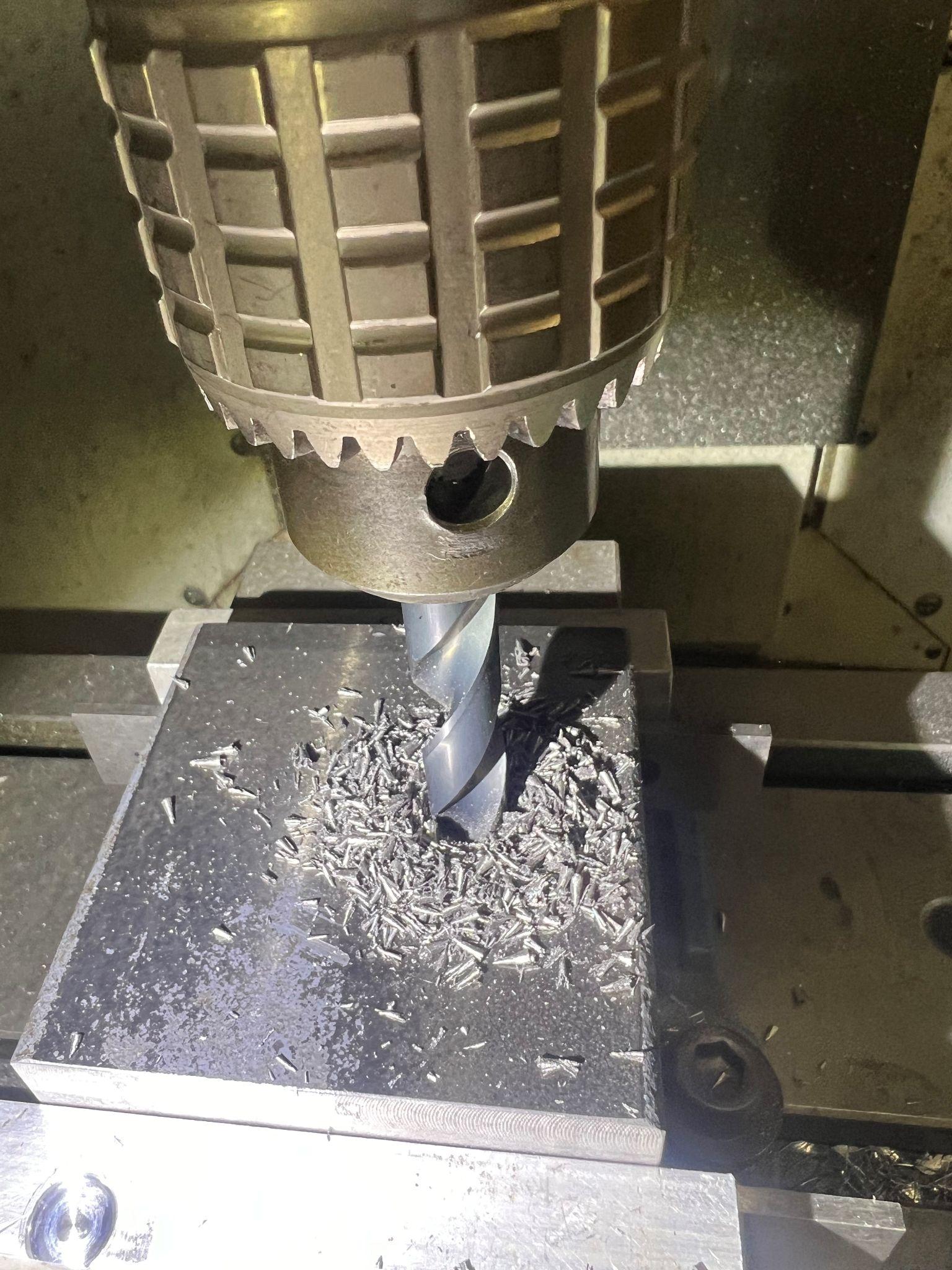
AUTHOR’S TIP
If this job were on a CNC machine, the sequence would be to spot drill all of the holes, then drill all of the holes, and finally bore the last four holes. This process takes advantage of the CNC machine’s ability to locate the holes repeatedly, and consistently. The time savings on this machine are in reducing tool changes.
Without taking the part out of the vise, drop the nod of the mill to 45 degrees and cut the V groove. Use the scribe lines to determine how much to cut.
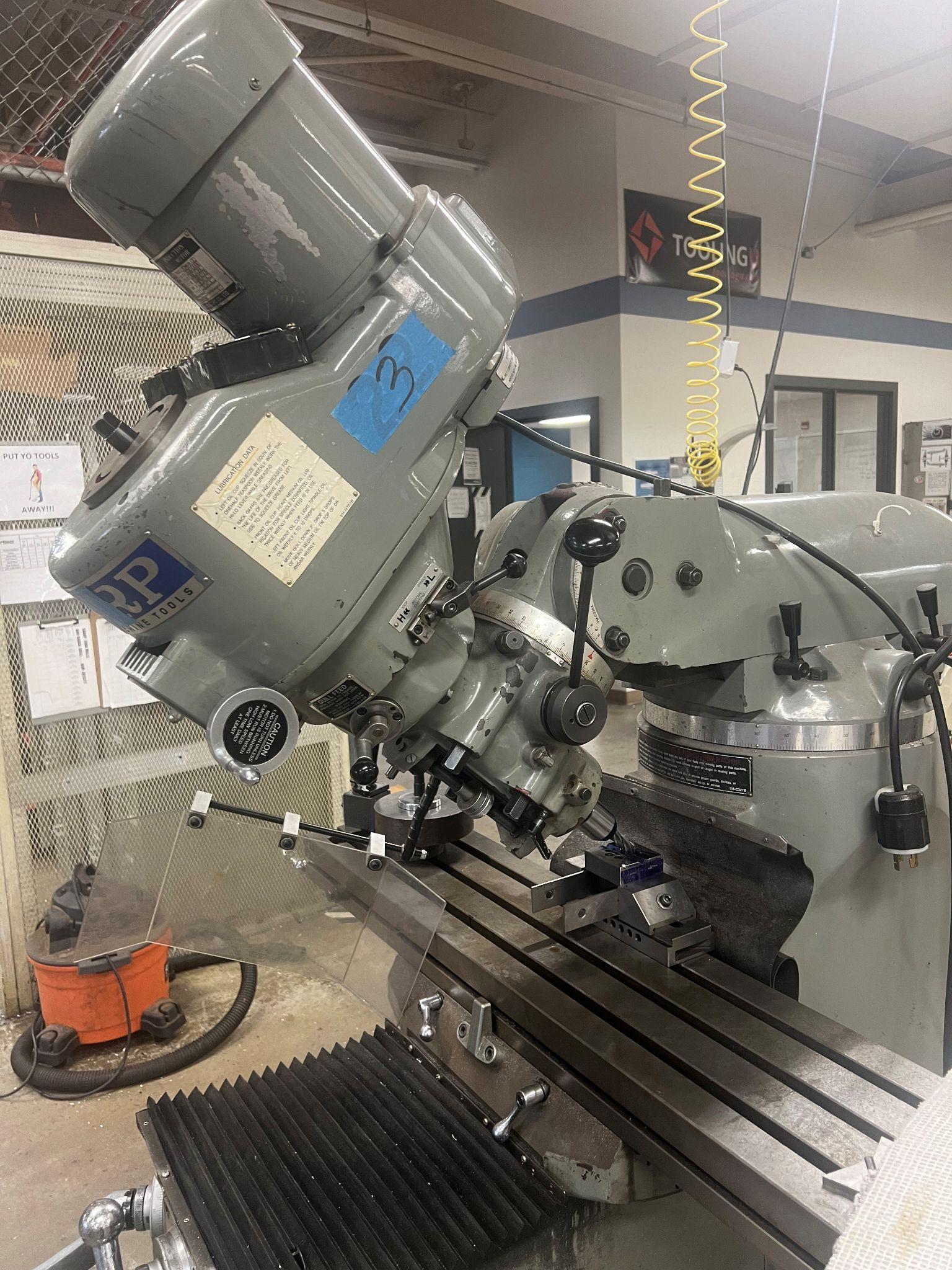
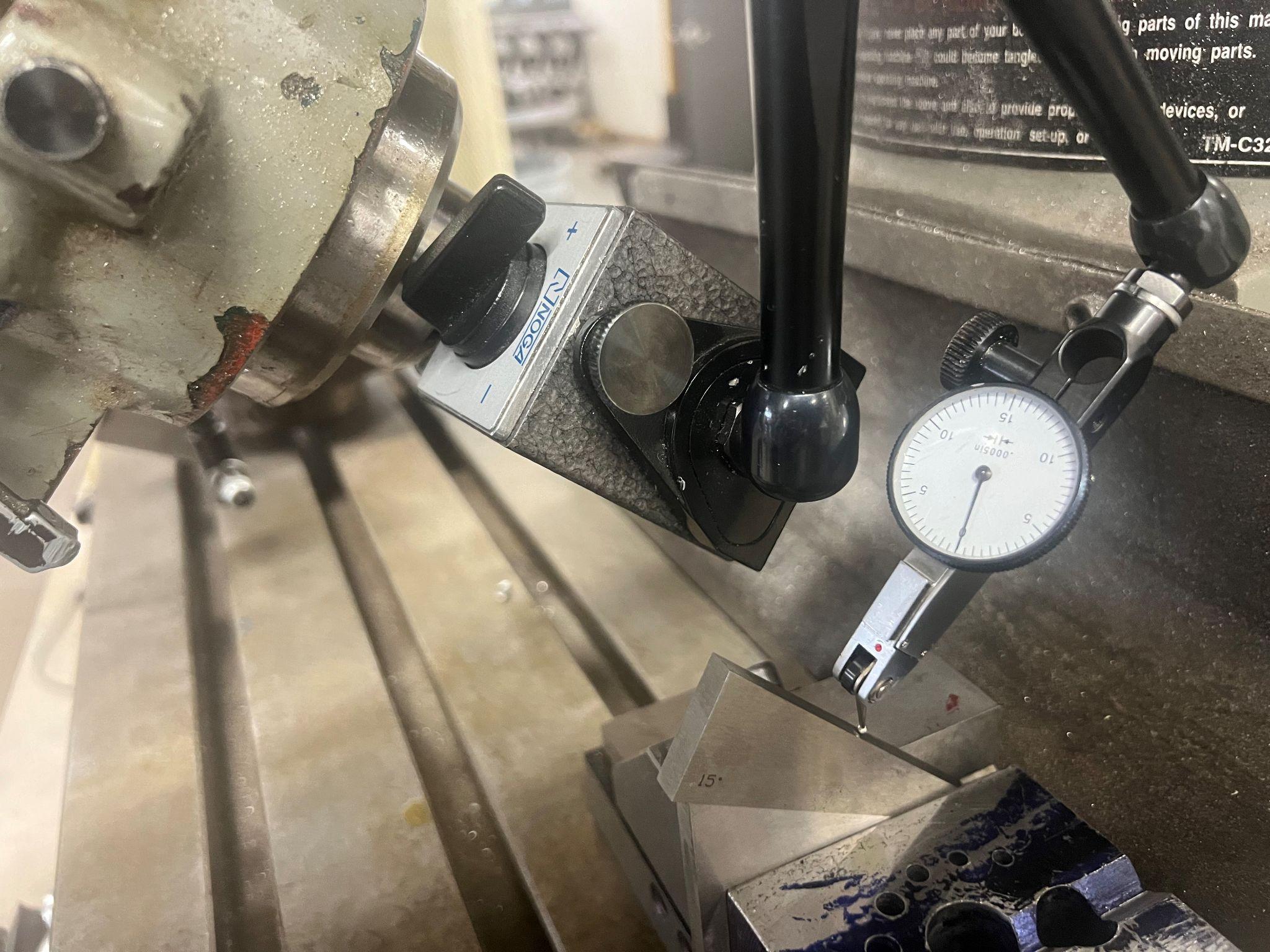
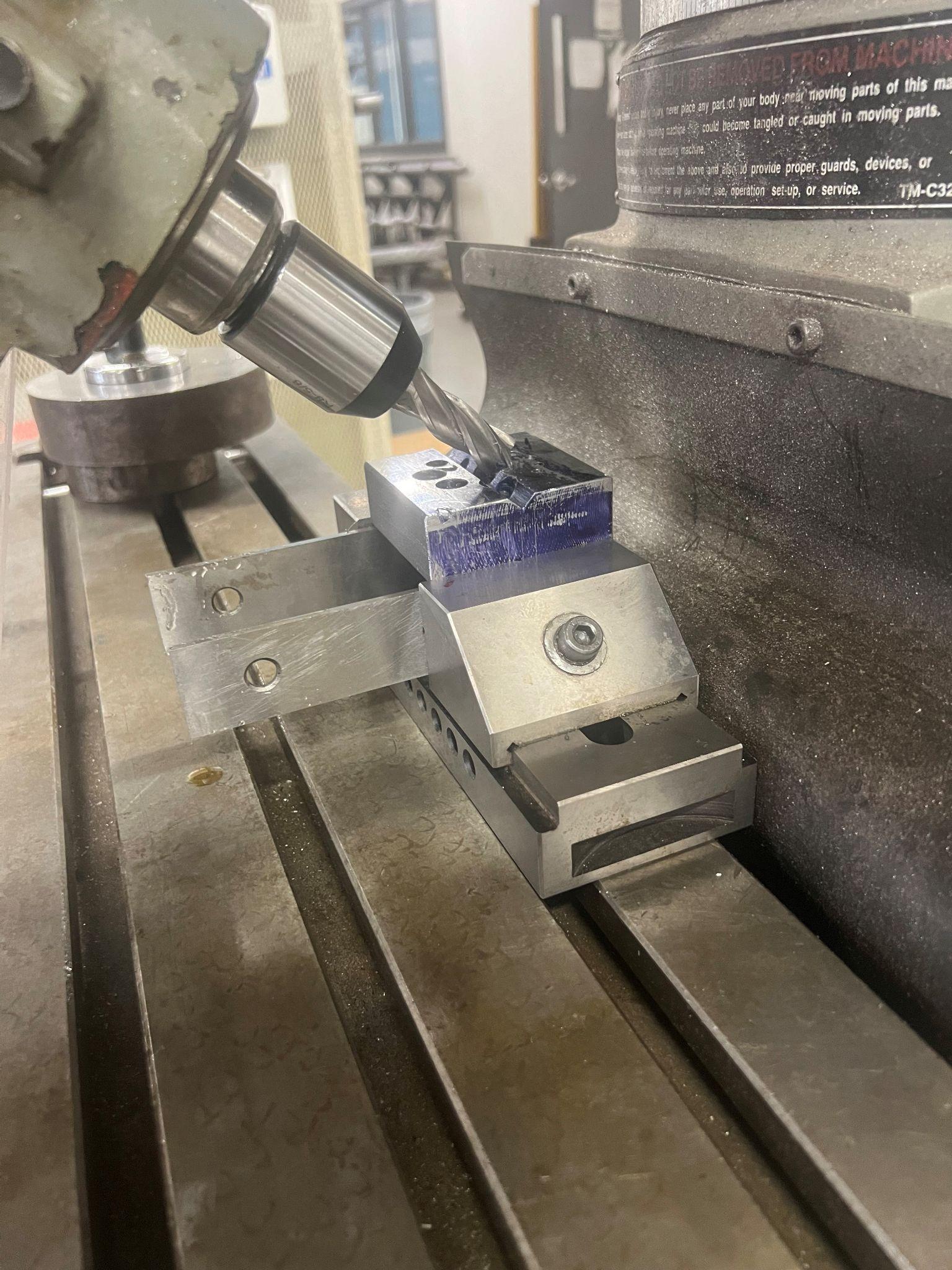
Now the part can be turned upside down, and placed onto a rotary table. Locate the center of the part. Using an end mill, the pocket can be milled out by bringing the end mill down to the depth of the pocket and rotating the table. Start at the center, working the end mill out to create the final diameter of the pocket. The part, while it is still square, can be held similarly to the part in the picture below.
AUTHOR’S TIP
The mill will need to be trammed back in before continuing. Tramming realigns the spindle to a 90 degree, perpendicular, position to the table.
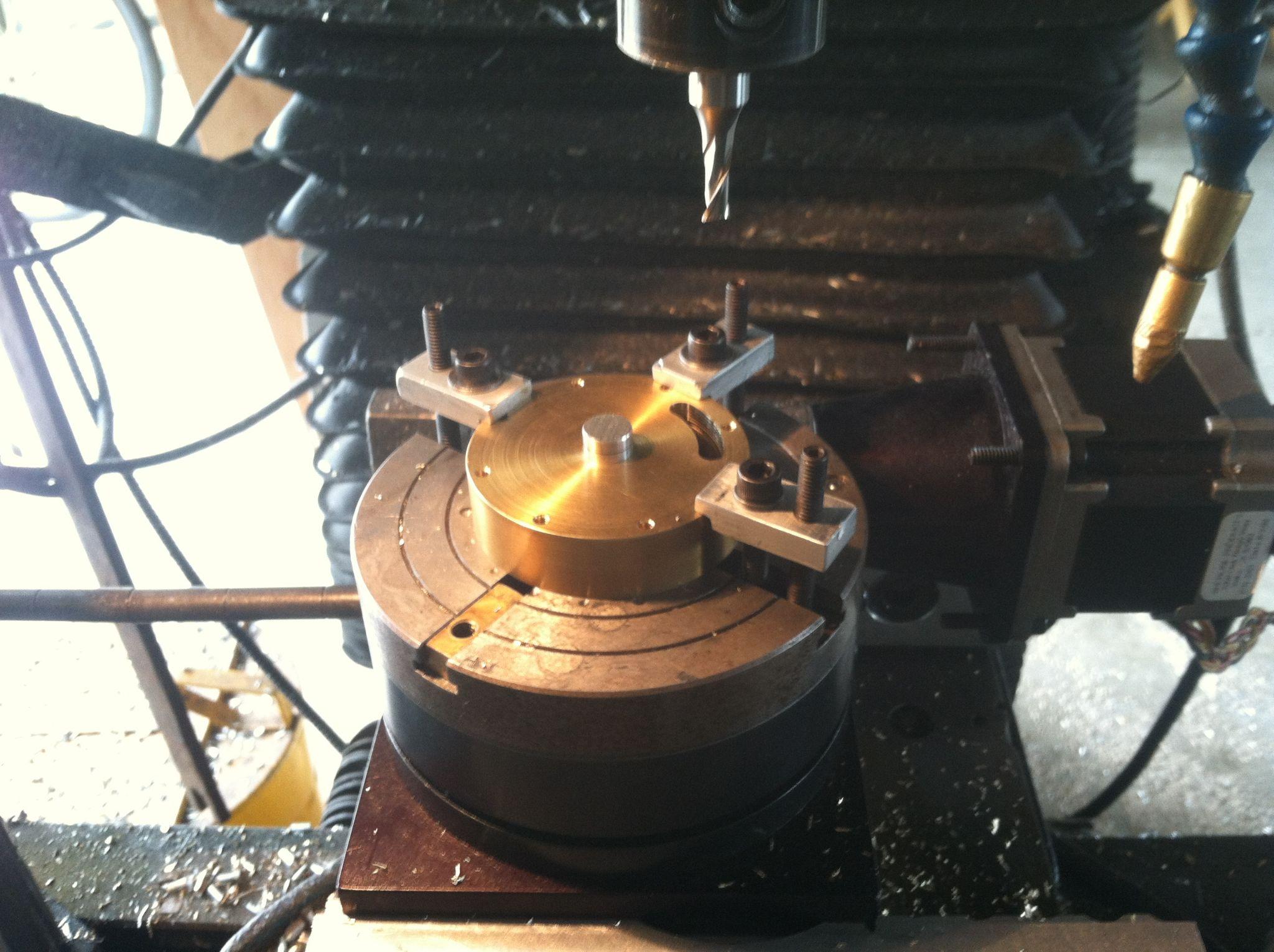
Now the outside of the part is ready to be turned into a circle. A fixture will need to be made to hold the block. A three cubic inch square piece of mild steel, or aluminum will be adequate. The fixture will need to be squared up so that it can be held properly. After locating the center, use the coordinates of the two fixture holes from the drawing, drill, and tap the two holes. One hole will be for a ⅝-11 bolt that will hold the block to the fixture. The smaller hole will be for a ⅜-16 cap head shoulder bolt (CHSB). The head of the bolt will need to be turned down to .375, or removed. This bolt will keep the bench block from spinning on the fixture while being worked on.
Attach the bench block to the fixture using a standard bolt and the modified one from above. Hold the fixture in a four jaw chuck on a manual lathe. Leave some room between the bench block and the jaws for tool clearance while turning. Using the four jaw chuck will require the part to be dialed in. That means that it will rotate on the center of the part with minimal amount of wobble. Turn the part down to the finish diameter of 2.25 inches with a right hand turning tool.
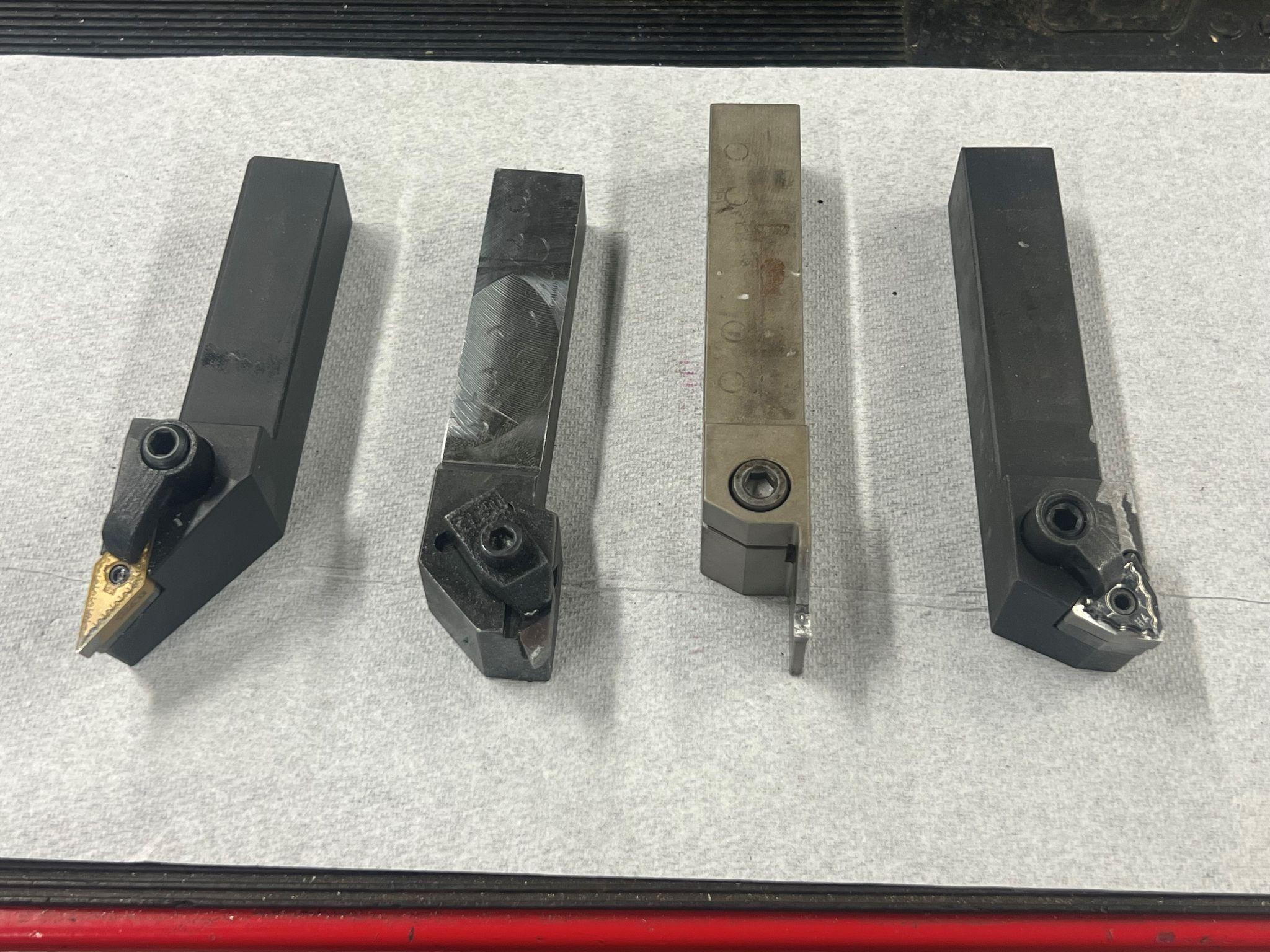
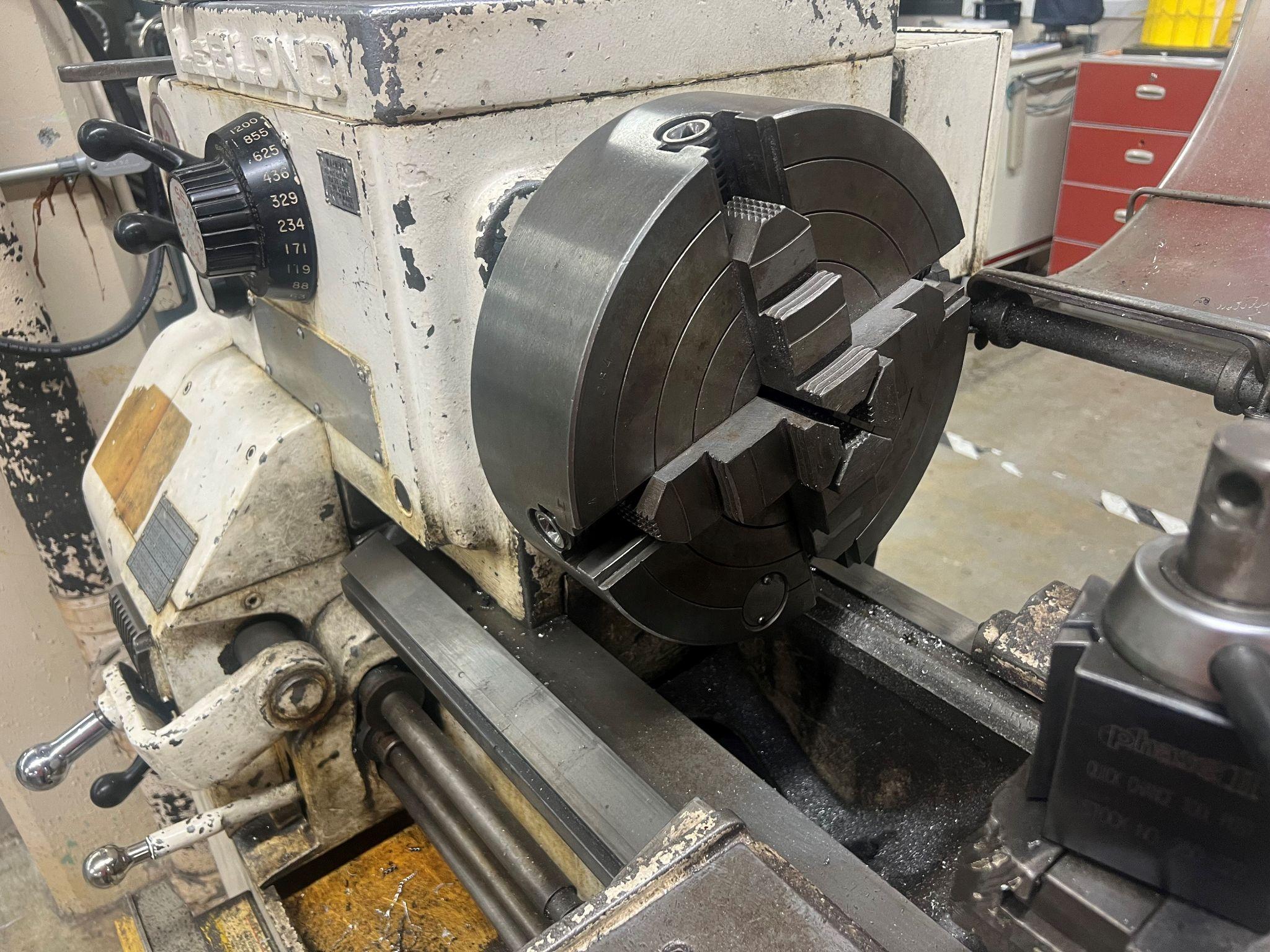
Leave the part and fixture in the four jaw chuck. Change from a turning tool to a knurling tool. The wheels on the knurling tool push the material around until the pattern forms. The wheels are available in different diameters. For this project, the .75 inch diameter wheels need to be used. A liberal amount of cutting oil should be used while running to keep the pattern clean.
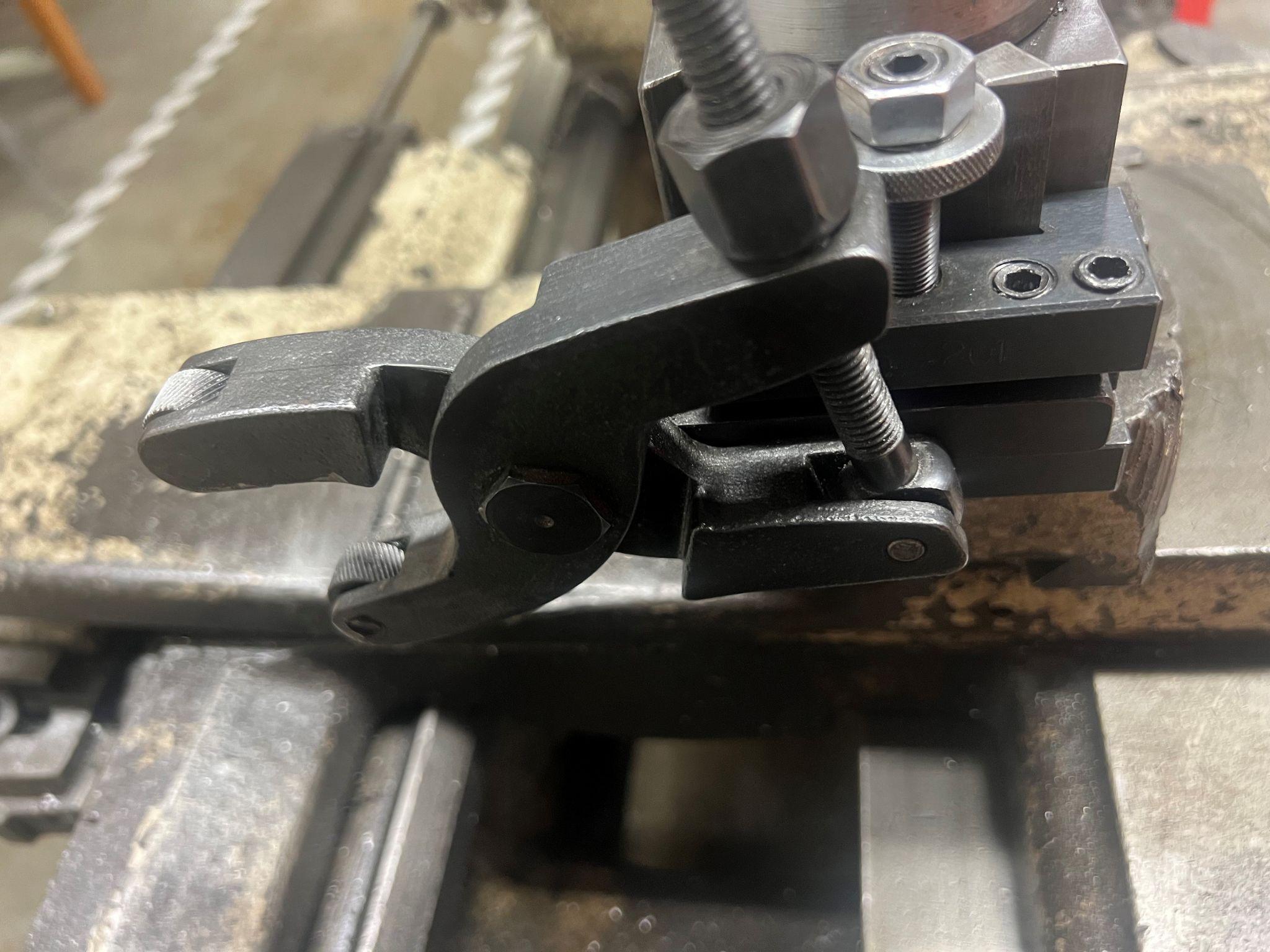
Knurling pushes the material around, and a small bulge may be present on the ends of the part. Put the turning tool back in the lathe and turn each side down .01 by on the diameter, and .150 inches from each face. This will give the part a nice, crisp transition between the features.
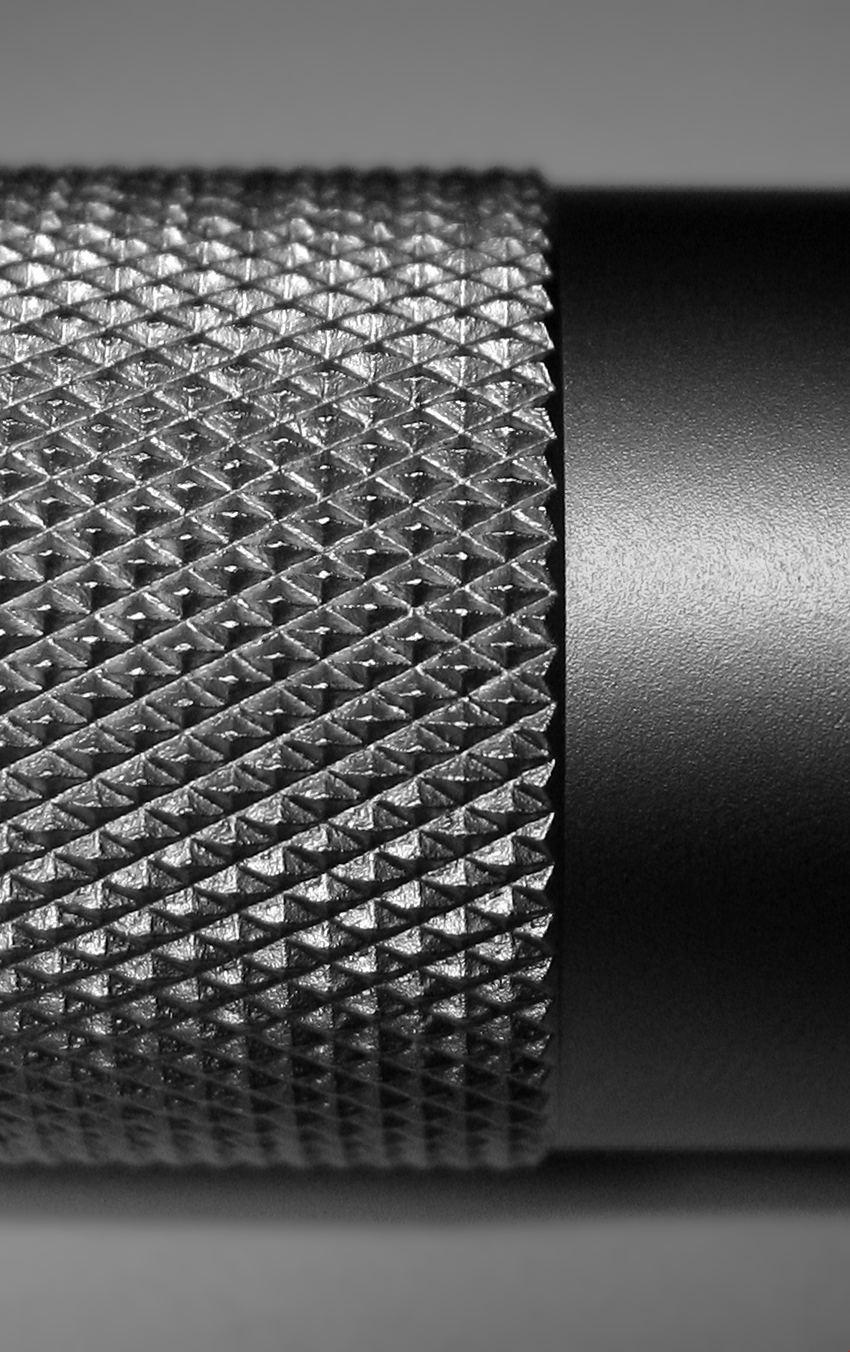
The last step in any project is to clean it up. Remove any oil, chips, and most importantly, deburr the part. A small file is commonly used to remove sharp edges, and frayed material that is still connected to the part. Making the part finger-friendly shows you care about what you are doing. People who have been working in the industry will value your attention to detail. After all, it was your attention to detail that helped you put together a successful job plan.
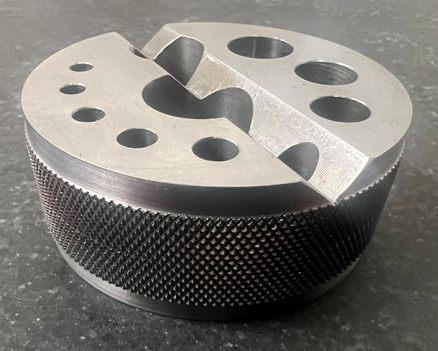
SUMMARY
A Project Plan shows the method for performing a machining operation, or series of operations. It may list items such as features to be machined, workholding required, machines to be used, and tools needed.
A job plan will always improve the process of building a part, but it will not always be required of the machinist to create one. When a person is newly hired as a machinist, a job plan will typically be provided. Parts from customers may contain a partial planning structure to help start the planning. The customer may require only metal cutting, and no grinding. As experience is gained on the job, the machinist may be called upon to help create a job plan for new products that come into the shop. Remember, though, that it is important to determine at the start of a job if a plan has been provided before spending time on planning that has already been done. Having said that, if a plan is provided, and the process of creating a plan is understood, the machinist may find an opportunity to improve the plan by implementing a change.
By visualizing the steps in the process and being detailed in writing the process, the ability to produce parts productively, and with less trouble, will increase. Start with a plan, and the project will be more enjoyable.
REVIEW QUESTIONS
- Name four parts of the Project plan.
- Why is tolerance important to the process plan?
- Why would you match the feature to be cut to a machine?
- Would an outside process affect the project plan?
- What role does workholding play in the manufacturing of a part?
- What does documenting the process do for the project?
- What is one factor to consider when choosing a tool to cut a feature?
- How will the sequence of features being cut yield different results?
- Why is it important to be specific about the workholding?
- What type of additional work could be done to a part after machining?
REFERENCES
Mitsubishi Materials. (n.d.). History of cutting tools. Retrieved May 14, 2024, from https://www.mmc-carbide.com/permanent/courses/91/history-of-cutting-tools.html
O*Net Online. (2024, April 30). Machinists. U.S. Department of Labor. Retrieved May 14, 2024, from https://www.onetonline.org/link/summary/51-4041.00 CC BY.