Chapter 7: Saws
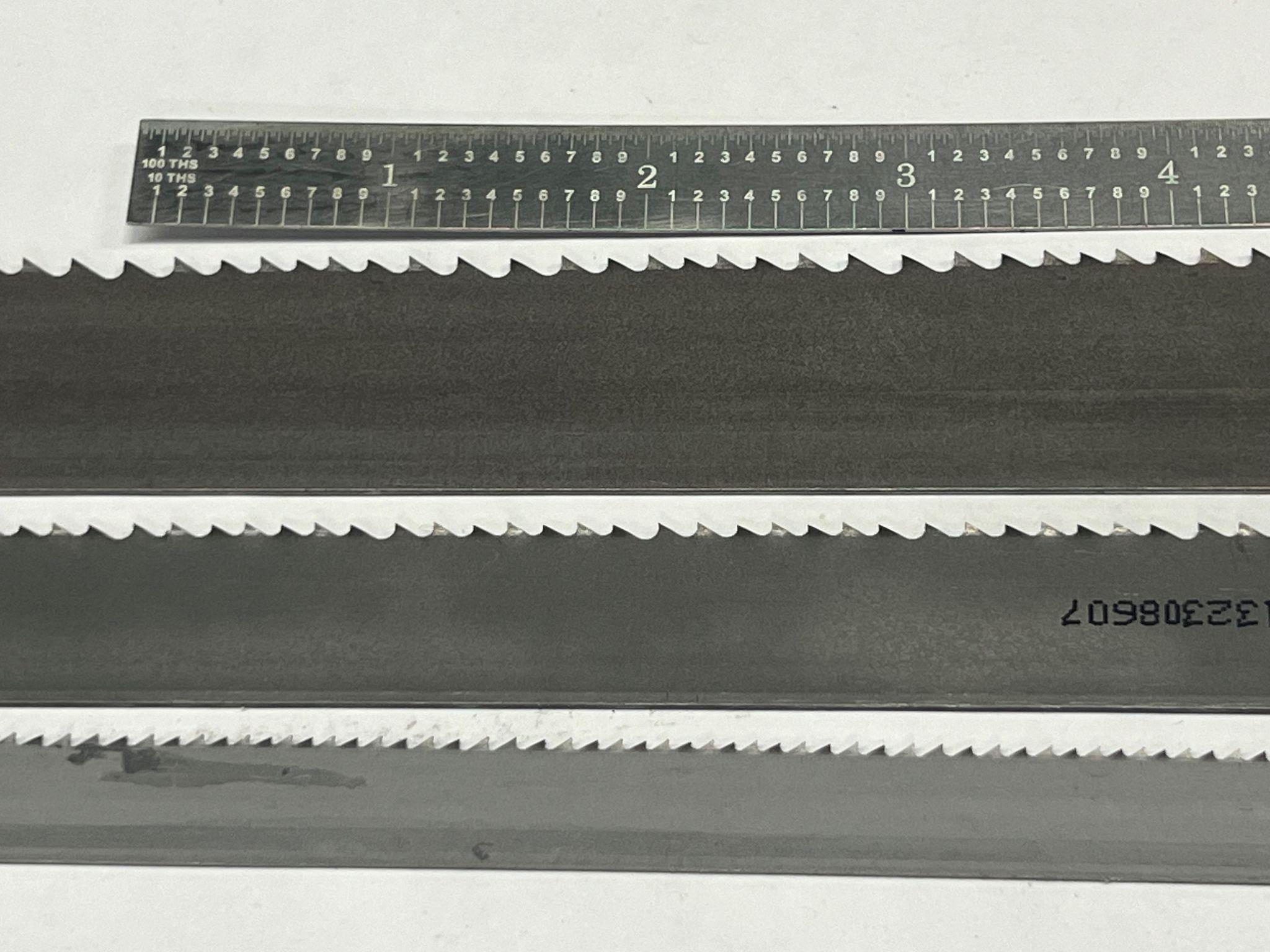
Overview
It can be an art as much as a science to make little parts out of big parts. One of the first steps usually starts with the material being cut by a saw.
The three basic saws commonly found in a machine shop are the vertical bandsaw, the horizontal bandsaw, and the chop or abrasive saw. The horizontal saw uses gravity to feed the blade through the part. Typical vertical saws require the part to be pushed into the blade. The abrasive saw holds the part in a vise while the blade is lowered onto the part to make the cut.
The goal of this chapter is to increase awareness of the variables involved with cutting material while ensuring that safe practices and procedures are followed. The topics covered in this chapter will assist students in making informed decisions when selecting a saw to prepare material for machining. Students will be able to directly apply the information in this chapter to produce a successful cut with the best saw for the job.
OBJECTIVES
- Explain proper safety procedures when using saws.
- Differentiate between basic types of saws and their purposes.
- Determine saw blade characteristics associated with different materials.
- Determine proper work holding when setting up a saw.
KEY TERMS
- Vertical band saw
- Horizontal band saw
- Three tooth rule
- Push stick
- Abrasive saw
- pitch
- kerf
- blade width
- TPI
- Carbon Steel
- Bi-Metal
- Carbide
- Aluminum Oxide
- Silicon Carbide
- Diamond blade
7.1 Safety / Introduction
7.1.1 Keep your fingers away from anything moving, at least the ones you want to keep…
Some general guidelines when using saws;
- Keep your hands and fingers away from the blades until everything has stopped moving, and not before.
- No gloves. The part may get hot, and wearing gloves may seem like a good idea. Do Not do it! The glove could get caught in the blade, and pull your hand and fingers into the saw. OUCH!
- On the vertical bandsaw, use something other than fingers when pushing material through the saw. Keeping your fingers away from the blade is a good way of ensuring that you will still have them at the end of the day. Use a stick of wood to push parts into the blade.
- When making cuts on a vertical bandsaw, it might be tempting to pull back on the part instead of pushing straight through when the blade gets stuck. The hazard with this is that if the material catches the saw blade, it will pull the blade off of the track and possibly damage it.
- The three tooth rule says that the thickness of the material being cut needs to be at least as thick as the distance across three teeth or more. If less than three teeth are engaged in the part, try stacking parts to make the material thicker. Another option would be to place the part on top of a scrap piece of material to increase the number of teeth that are cutting. See section on saw operations for more detail.
- The same relationship applies to the RPM (speed) and the feeds of saws as they do with other cutting methods. In general, use a fine-tooth blade with a slow rpm for steels, and a coarse blade with a high rpm for aluminum.
- If you need gloves to clean up, make sure that none of the equipment is running.
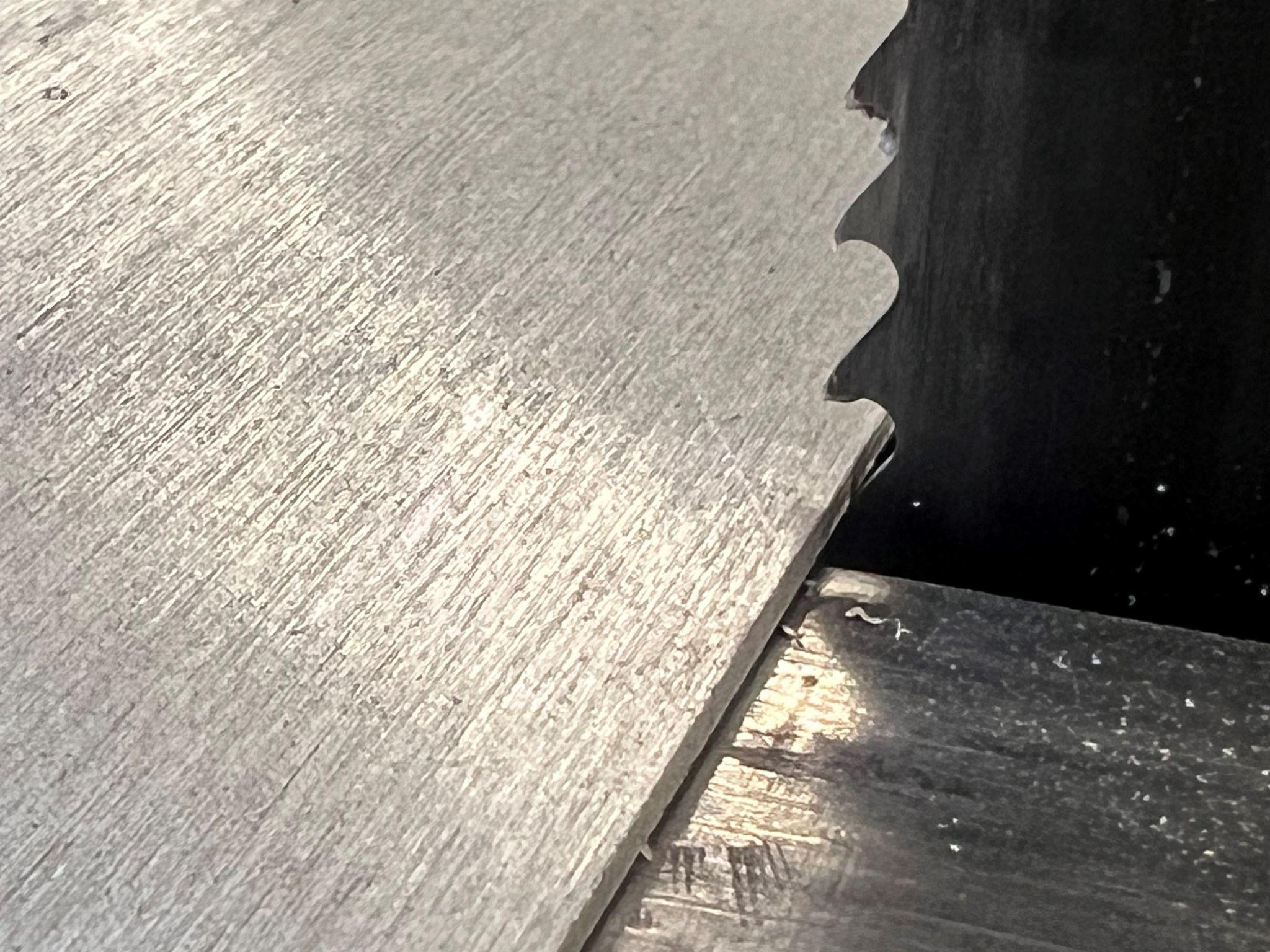
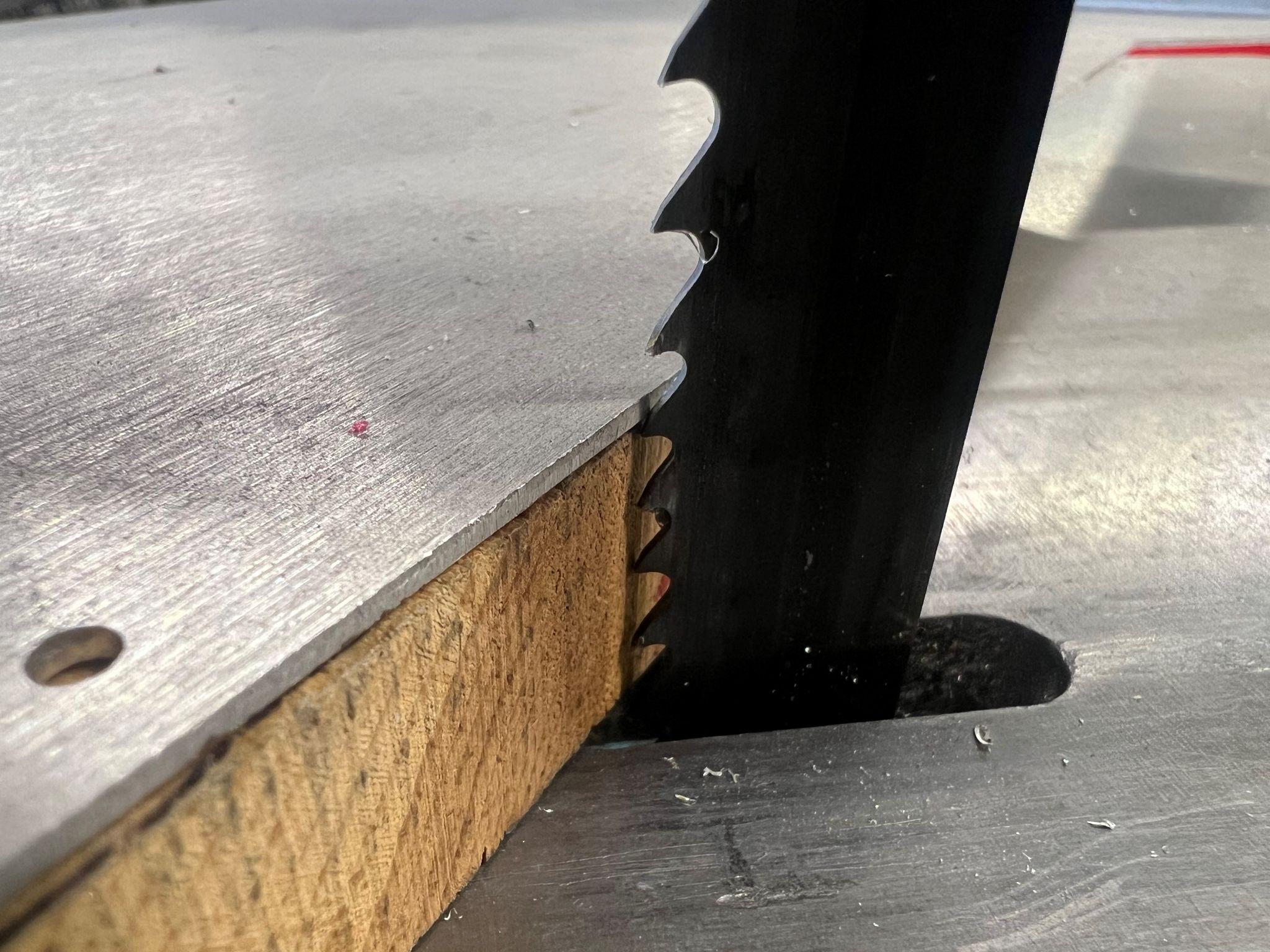
A chip is a splinter of material that comes off of a larger piece of material being cut by a tool. There is a more detailed discussion of types of chips in the chapter on General Machine Shop Safety. Two things need to be present to make a chip: Heat and pressure. The heat comes from the saw moving over the top of the part, and the pressure comes from the force applied to push the blade into the part. In some cases, the part is pushed into the blade.
One of the first operations in the machining process is to saw material down to a size slightly larger than the finished part. This smaller piece of material is referred to as the stock. Consideration of how the stock will be held during machining and the cost of the material will dictate the final stock size. If the material comes into the shop in long lengths of bars, it is cut up on the horizontal bandsaw. If the material is smaller in size and can be readily handled, it is cut on the vertical bandsaw. If the material has been hardened, it may be necessary to use an abrasive saw to cut the material.
AUTHOR’S TIP
Fingers and moving parts should never exist in the same place at the same time.
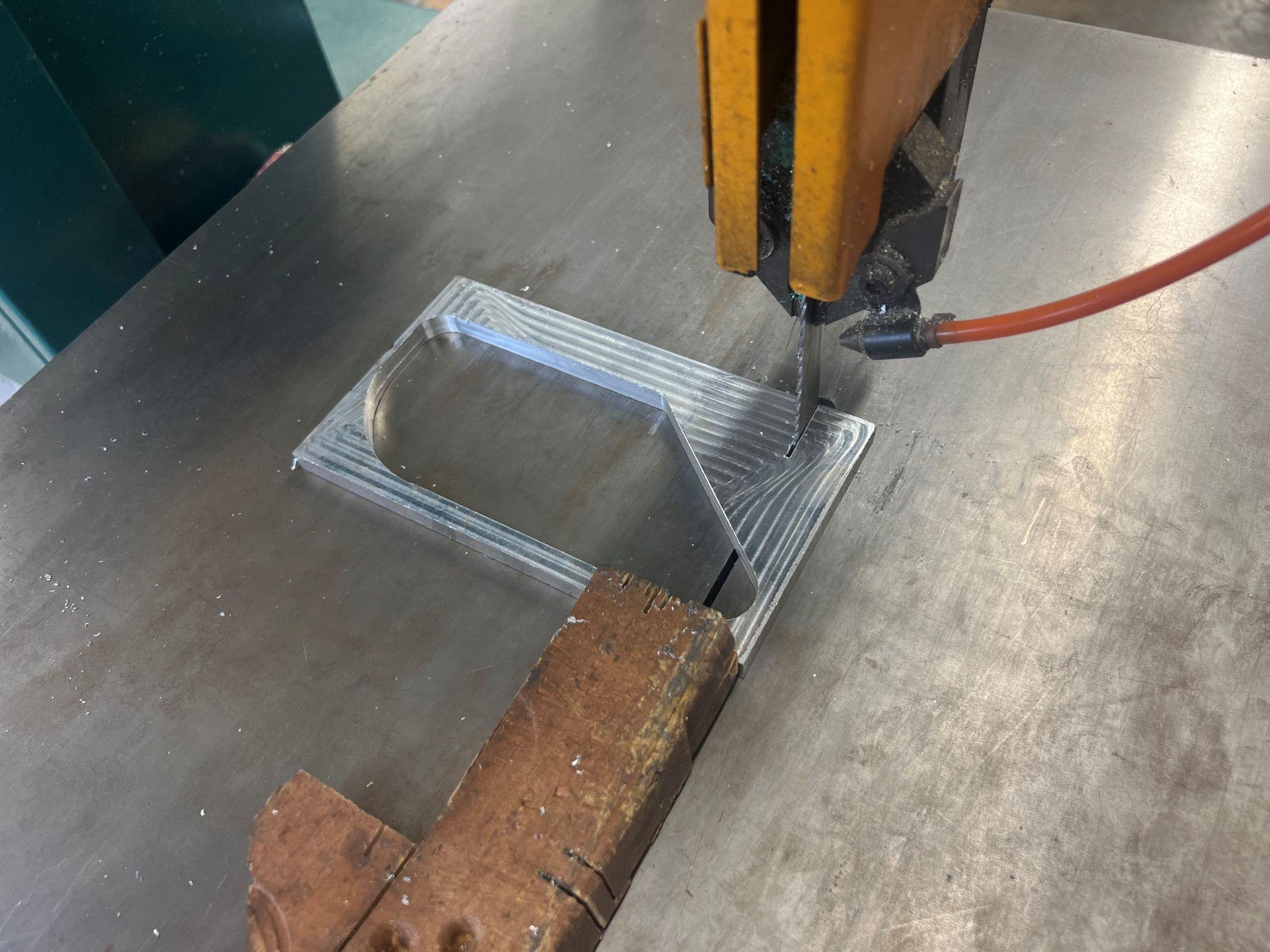
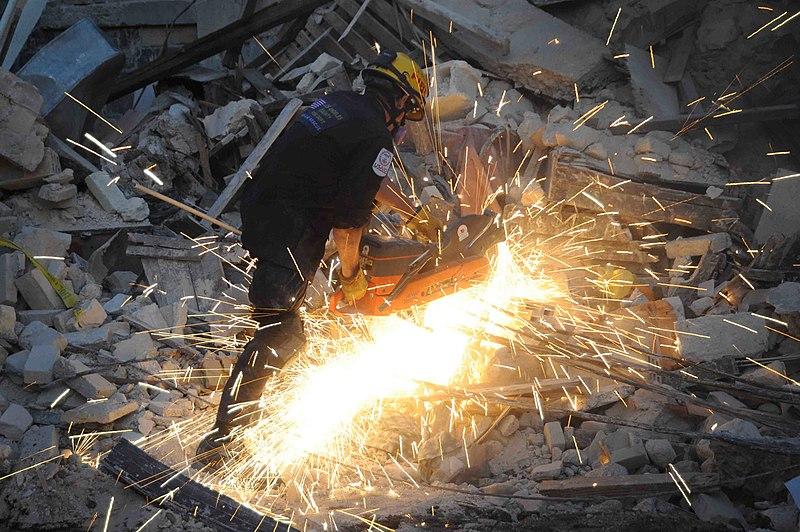
7.1.2 Housekeeping and Preventative Maintenance
The tools and machines in a shop are used to make a living. If a piece of hardened material is put into a horizontal bandsaw, the blade will become dull in a short amount of time. This will cause a loss of production time while the blade is replaced and a loss of expense in purchasing another saw blade. Properly matching the job to the saw will ensure that it lasts for a long time to come. Taking care of the equipment should also be a routine event. Cleaning off the table, making sure there is coolant in the tank, and mopping up the splashes from the coolant are just some of the common housekeeping activities that take place in the shop.
Grit from the chop saw will be like dust and spread out in a wide area when cutting material. The grit is abrasive and can promote excessive wear on moving parts. Because of this, the chop saw is commonly placed in an area that will help control the spread of the grit.
Aside from keeping the equipment clean, preventative maintenance involves ensuring that a proper blade is matched to the material being cut. If the wrong blade is selected or something happens to damage the blade, a new one will be needed. To replace the blade, the cabinet that covers the wheels on either side of the cut area will be opened. There is a handle that will relieve the tension on the blade so it can be removed. When handling saw blades, care must be taken to avoid personal injury. Note the direction of the teeth on the blade before removing the bad one to ensure the blade is placed into the saw properly. After the saw blade has been installed, rotate the wheels as the tension is increased to ensure the blade is seated before operation. Close the doors to cover the wheels before starting the saw for safety.
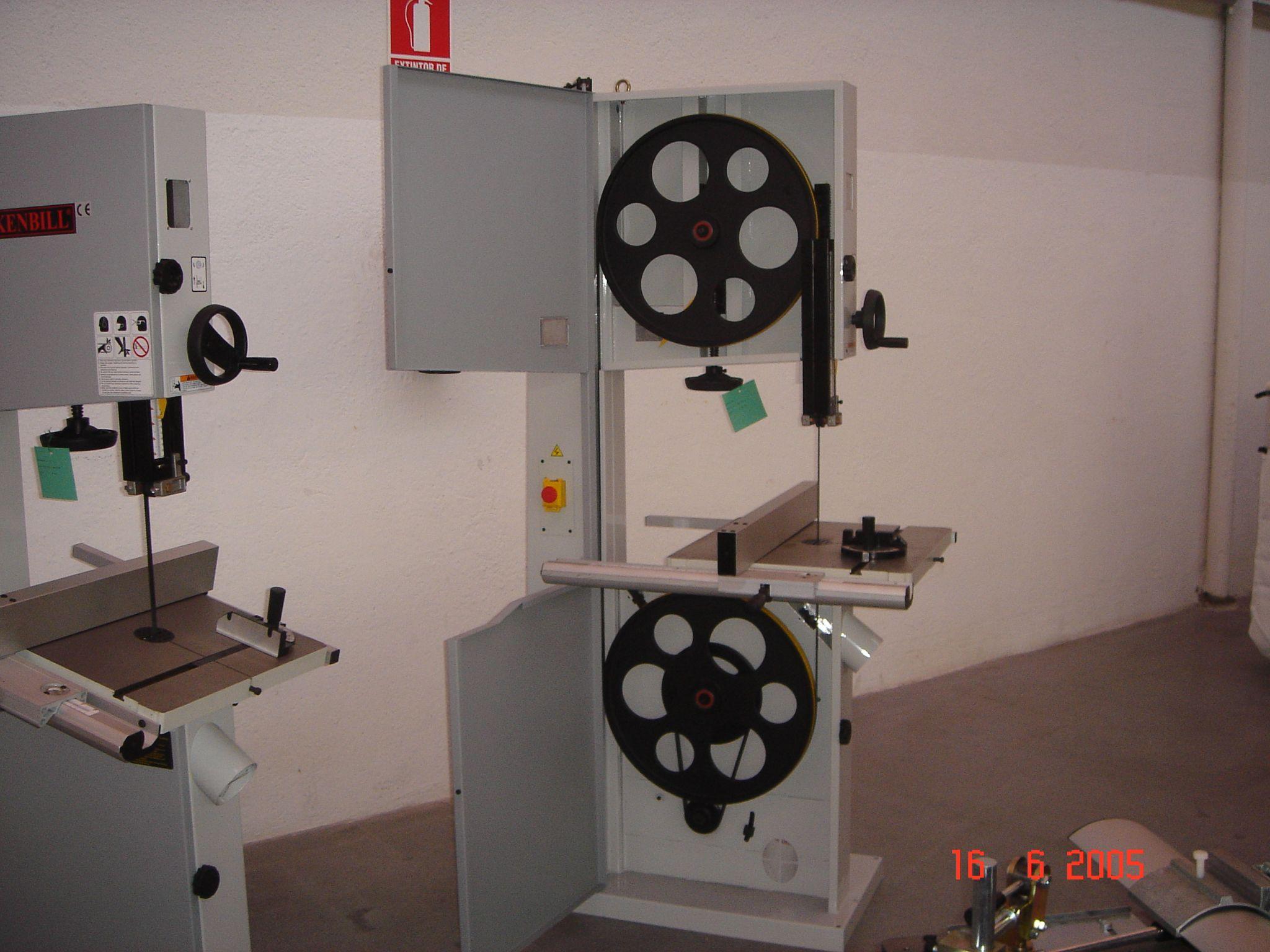
7.1.3 Workholding
The material to be cut will have a variety of shapes. Square, rectangular, and round shapes tend to be the most common. Small parts can be cut by hand on the vertical saw, while longer parts need to be cut on the horizontal saw. On either style of saw, the round parts are a challenge because they will want to rotate with the blade. Clamping an angle bar, or another piece of material to the round bar will help to keep it from rotating when it is being cut. Assertive clamping pressure with a conservative feed rate of the blade will assist in providing a successful cut.
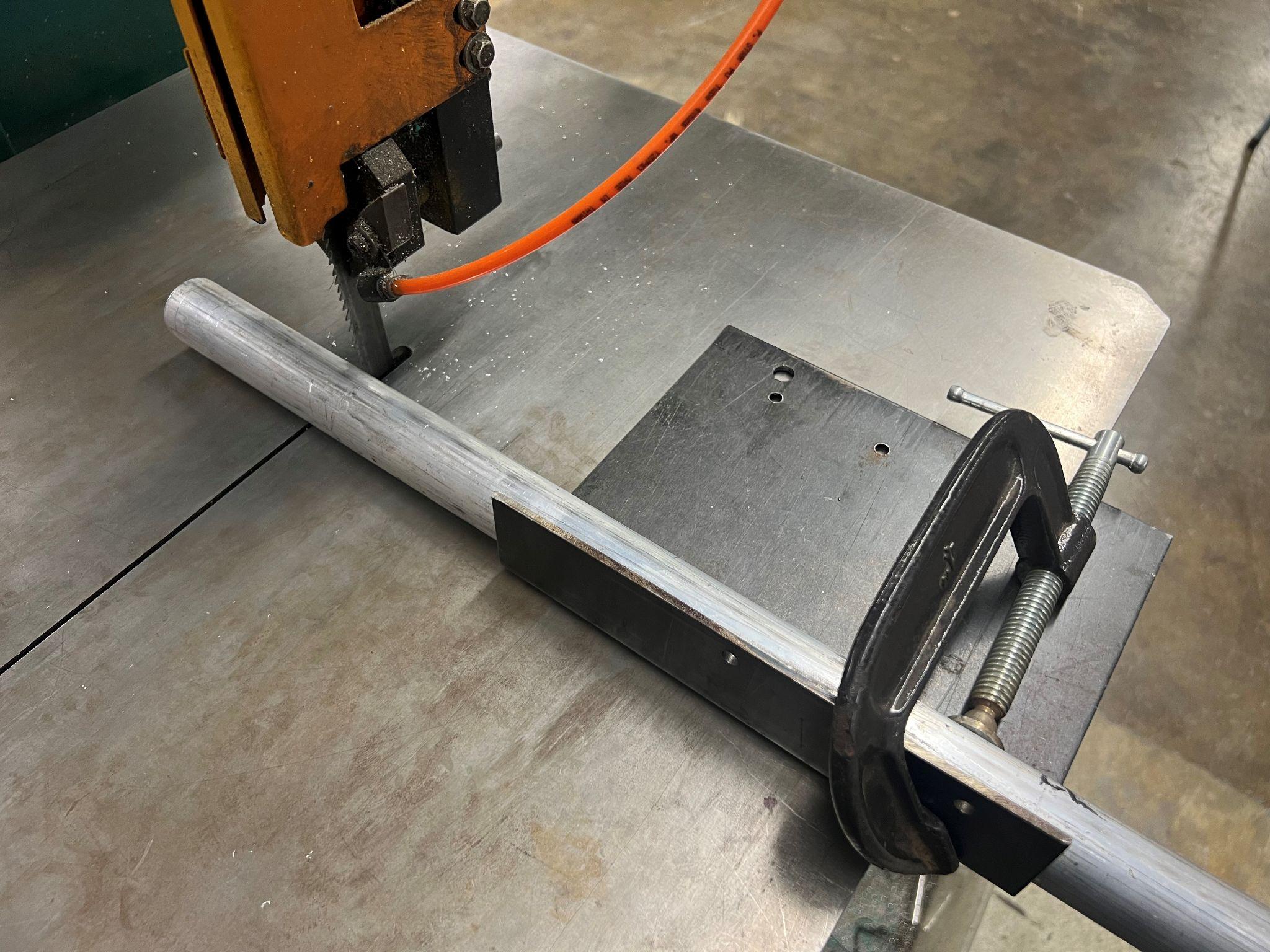
Use a level to ensure material on a stand or table is at the proper height to cut on a horizontal bandsaw. This will help the blade make a perpendicular cut on the part, which will save material and money. If the blade cuts at a slant across the material, material is wasted.
The horizontal saw has a vise that pivots to conform to material that does not have parallel sides. When cutting short parts on the horizontal saw, both sides opposite the pivot point on the vise need to be supported. If only one side is used to clamp the part, the vise will clamp at an angle and likely release the part while it is being cut. When the part comes out of the vise while it is being cut, there may be damage to the part and/or the saw blade.
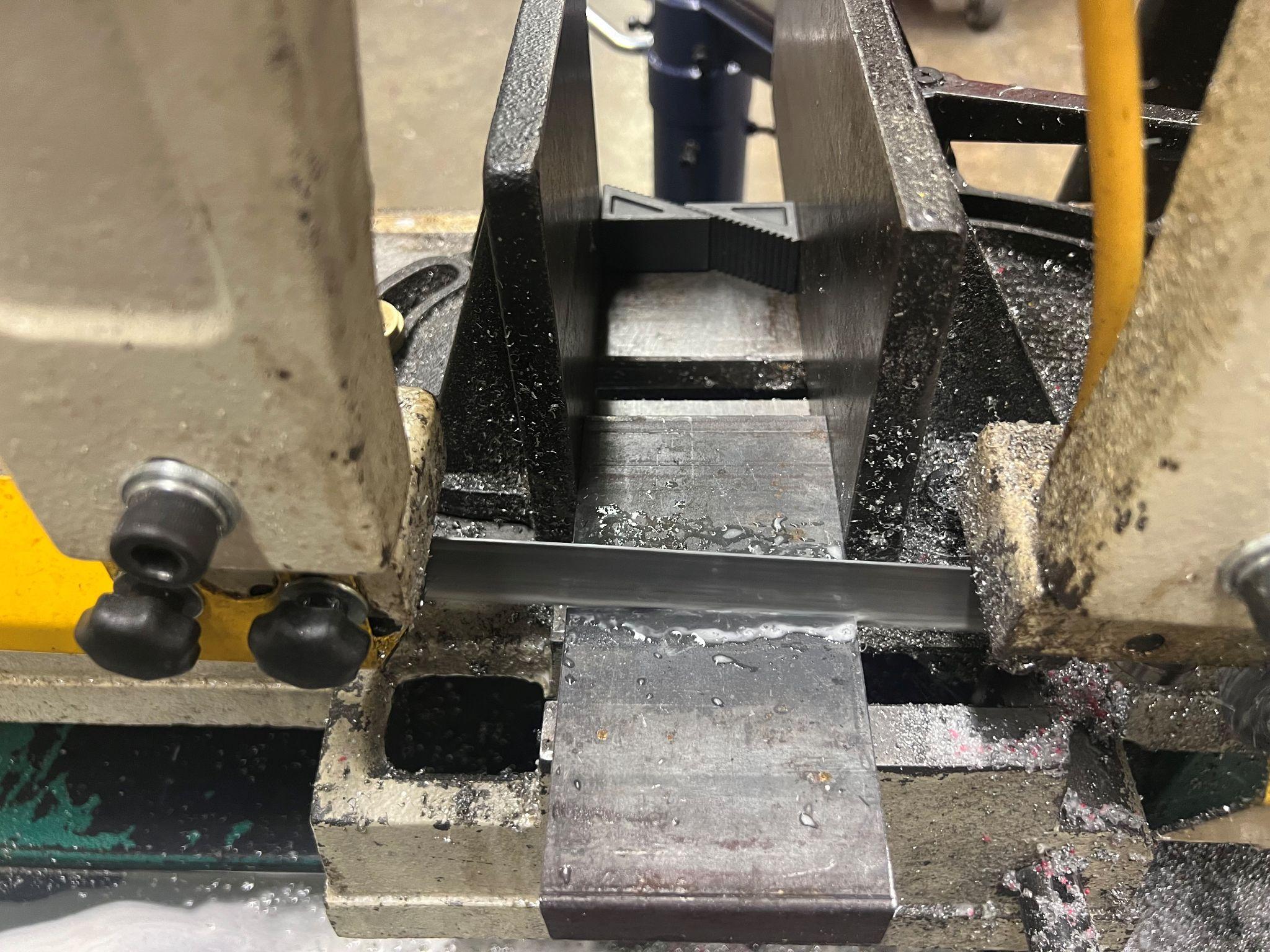
The chop saw uses a pivoting vise similar to the horizontal bandsaw. It can accommodate parallel parts. When a short part is being cut, both sides of the pivot point on the vise must be supported to ensure proper clamping of the material.
7.2 Types of Saws
7.2.1 Horizontal Saws
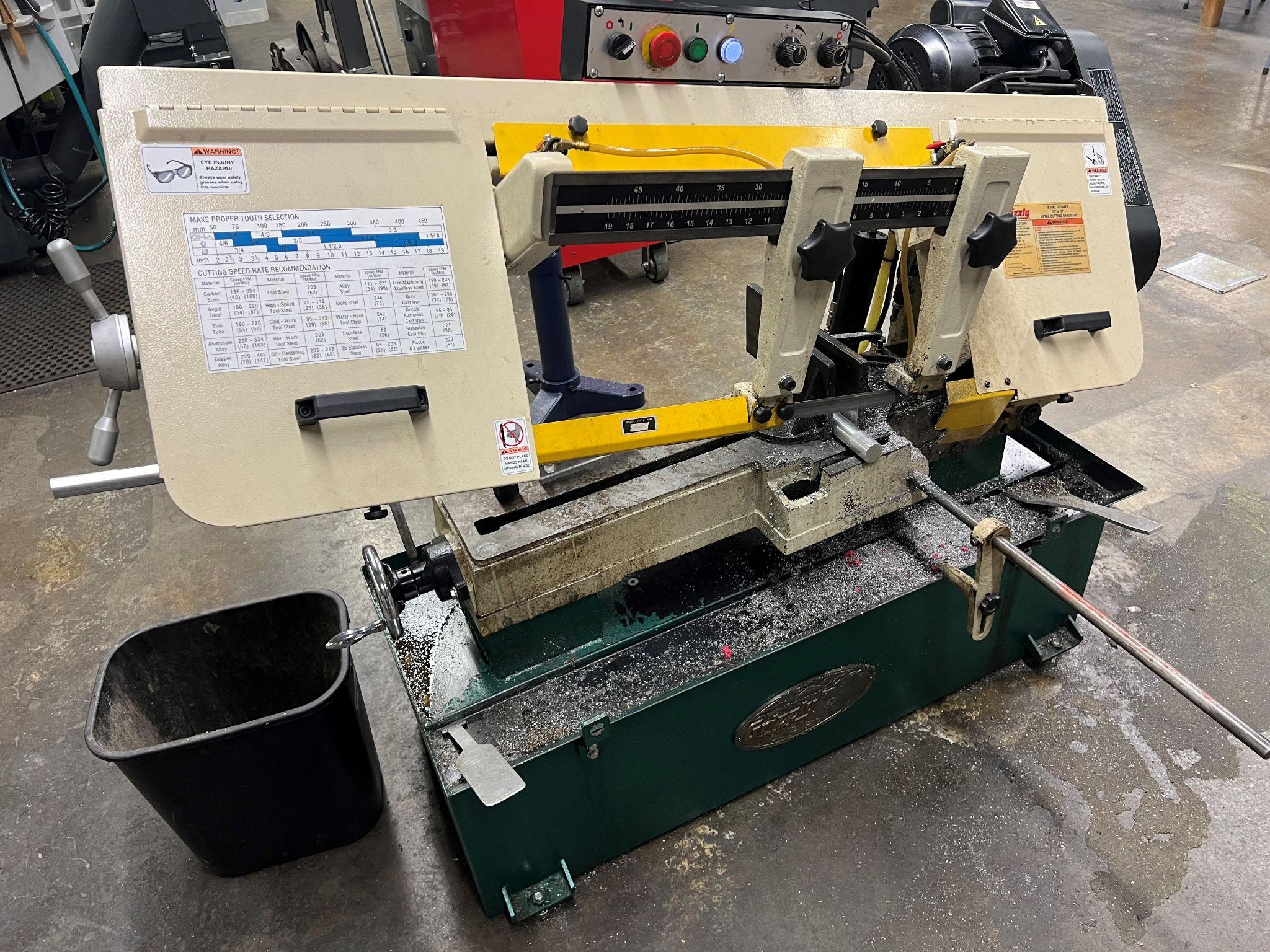
The saw that is parallel to the floor of the shop is called the Horizontal band saw. It is capable of cutting large pieces of stock quickly and accurately. These saws are gravity fed using a hydraulic cylinder to control the rate of drop, or feed, of the blade. The Horizontal saw has a pivoting vise integrated into the frame to facilitate holding the material when being cut. Most of these saws also have some type of fluid system that floods the cut area to control temperature and remove chips.
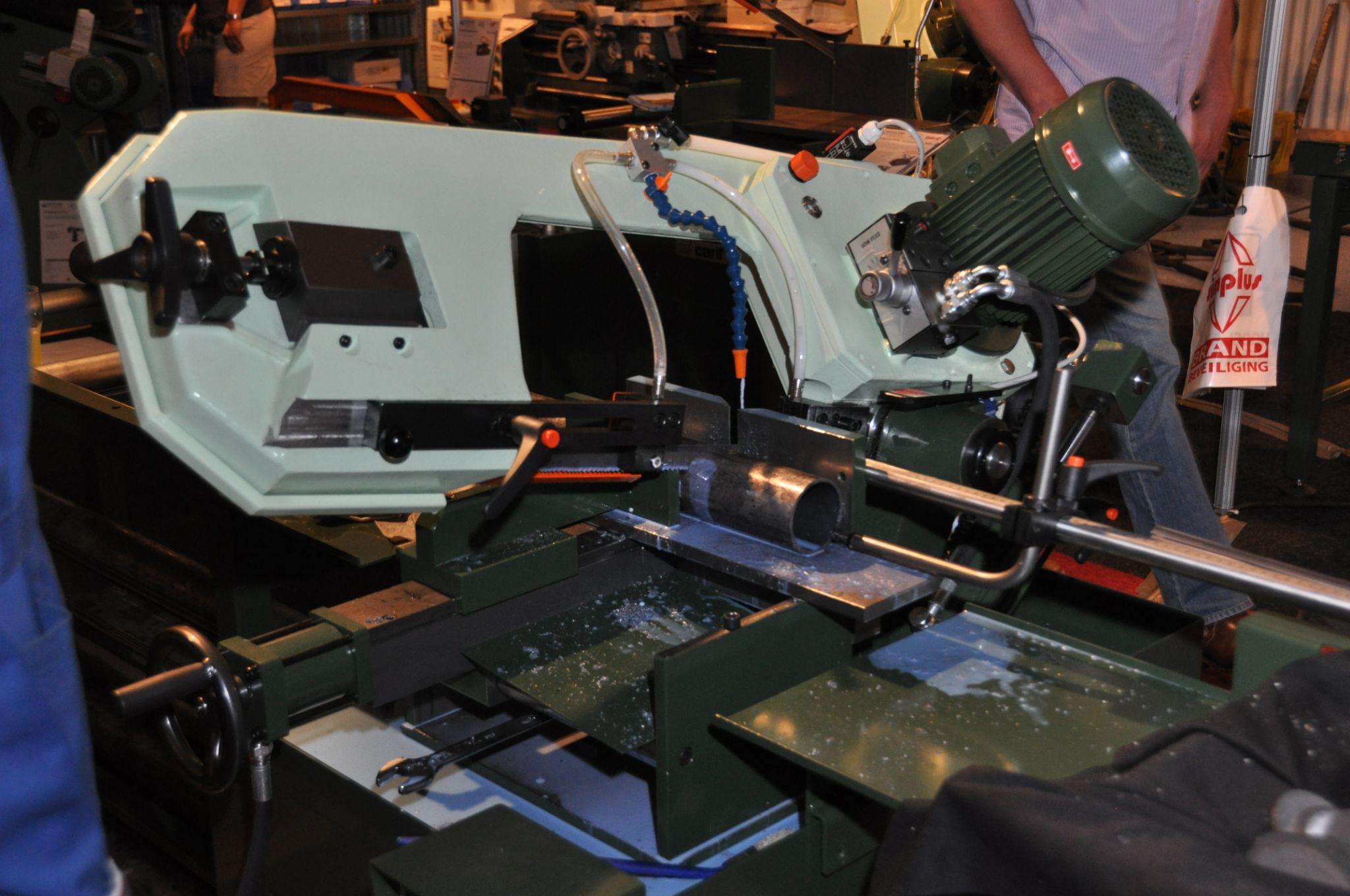
Because of the automatic nature of the blade feeding through the material, the horizontal bandsaw can be set up to cut large pieces of material while unattended. The material is supported by a stand or table that will allow the bars being cut to slide forward once the vise is released, and another part ready for cutting.
Horizontal band saws use a vise to hold parts that are typically very long. Bar stock comes in from the suppliers at around five feet in length or more. The material is cut to a smaller size that matches more closely to the finish dimensions of the part being made.
7.2.2 Vertical Saws
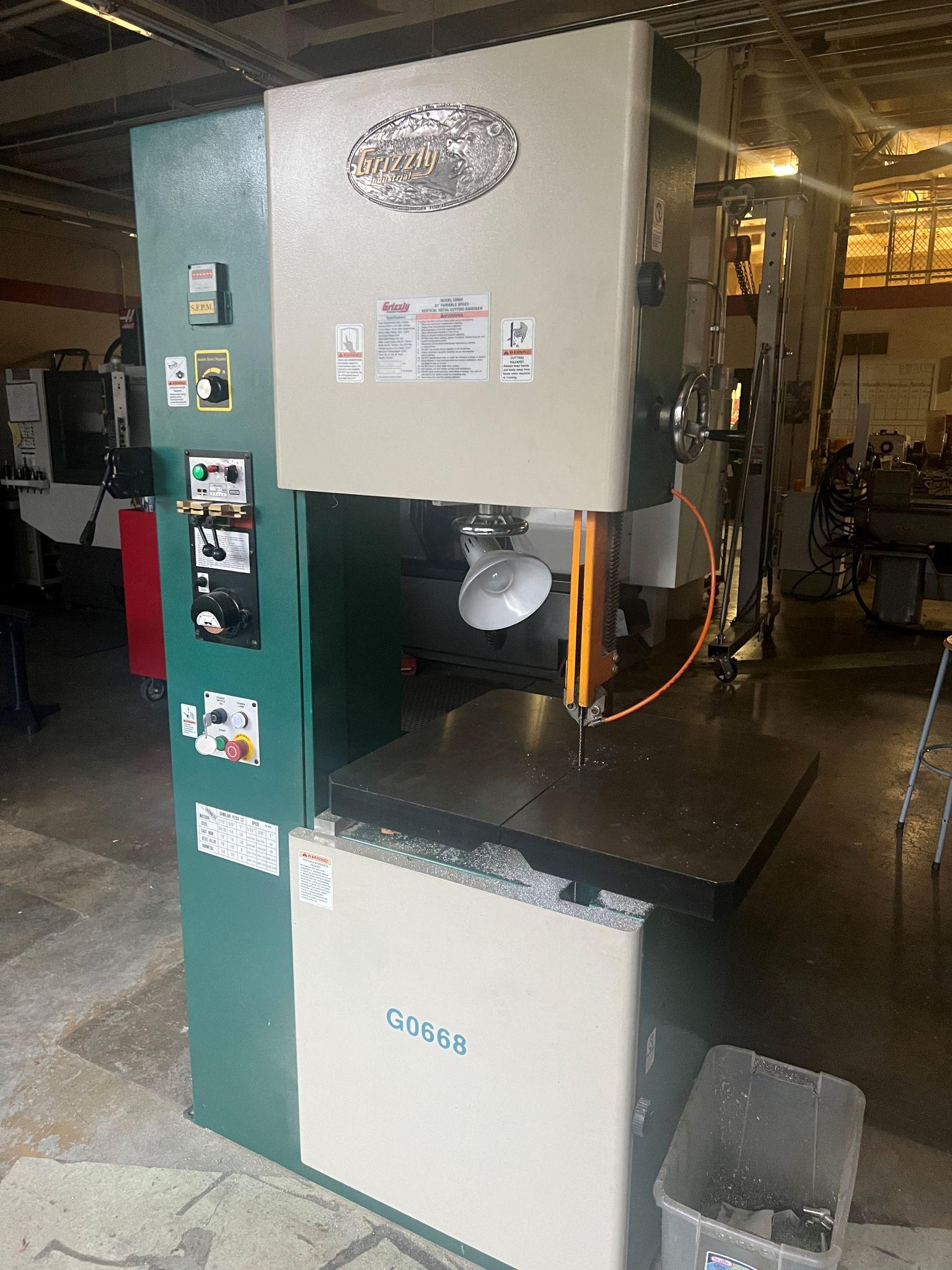
The Vertical saw is very similar to the horizontal saw, and as the name implies, it stands upright. It shares several common characteristics with the horizontal saw. Some of the differences are the lack of a vise to hold the parts or coolant when cutting material. The benefit of a vertical saw is that the machinist can control the cut path by using their hands when they are at a safe distance from the blade. Using a push stick will help keep fingers away from the blade when the parts are small.
The most challenging parts to cut on these saws are small parts and round parts. For small parts, try to clamp them down to a sacrificial plate or nest them between other material when they are being cut. Using a push stick can aid in cutting small parts and keep the heat away from fingers. For round parts, a square or “C” channel piece of material can be clamped to the part to keep it from rotating while being cut. The parts will become hot; DO NOT wear gloves. A glove can get caught in the blade and pull the hand and fingers into the blade.
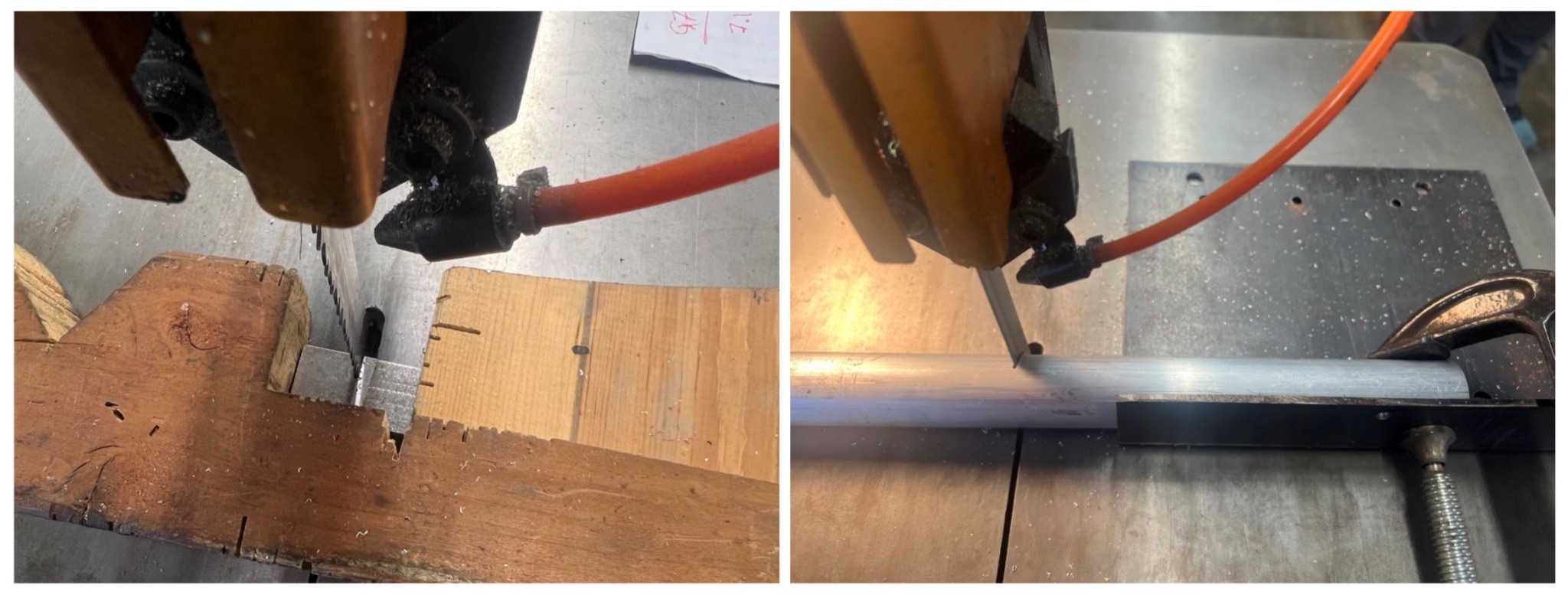
7.2.3 Abrasive Saws
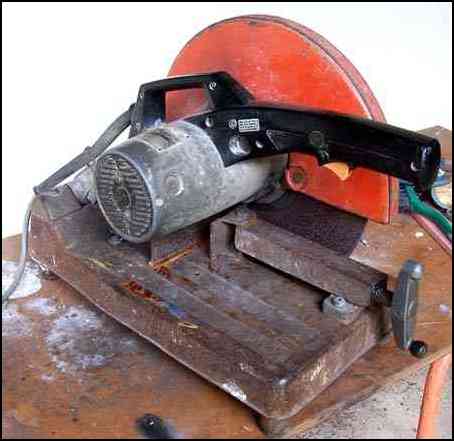
The Abrasive saw is also referred to as a cutoff, or chop, saw. These saws are a good choice in a production environment where accuracy is less of an issue. Note that the type of material being cut should be in an annealed or non-hardened state and in the family of carbon steels. Hardened materials can be cut, but will require a special blade and a coolant source.
A shower of sparks will be created when using a chop saw. This is a fire hazard. Know where the sparks are going, and have a fire extinguisher at hand. For a more indepth discussion of safety, please refer to the earlier chapter on Machine Shop Safety.
When using the chop saw, maintain awareness of the heat-affected zone. This is the area on either side of the blade where the cut is being made. It will get hot and can change the structure of the material, making it harder to cut later on. In simple terms, the abrasive disc is rubbing on the material and creating heat. The abrasive nature of the disc will wear away the material. The disc is similar to a grinding wheel. It is made of bonded abrasive particles. Each of the particles acts as a small cutting edge and can produce a cut. With the high rotational speed of the blade, these saws are relatively quick at cutting material. The trade off is that they create a great deal of dust and sparks, which can be harmful to the equipment or personnel if proper personal protective equipment (PPE) is not used. Safety glasses, and ear protection are always required.
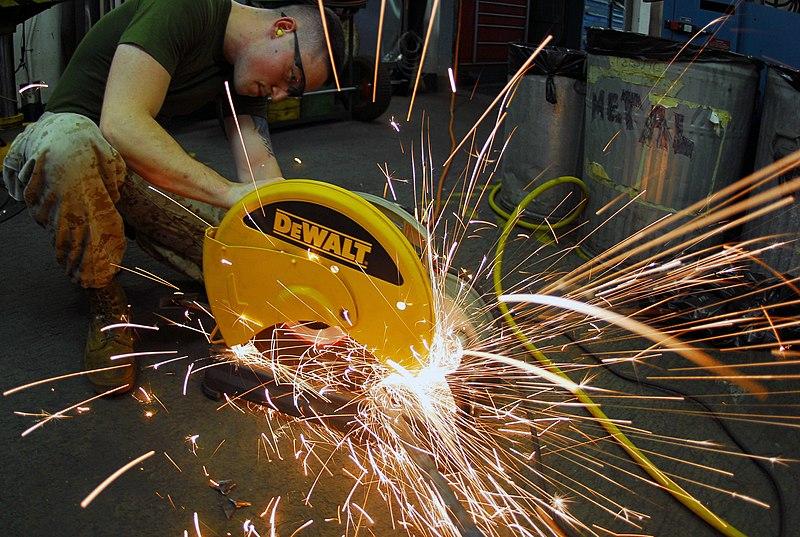
7.3 Blade Characteristics
7.3.1 Important characteristics of a band saw blade.
The Band saw is the most common machine found in the shop. Material will be supplied in a bulk plate or bar shape. It is important to consider the characteristics of a band saw blade when selecting one for a job. The choice will affect the quality of the cut, the life of the blade, and the time needed to make the complete cut. The first step is to cut the material down into small blank stock sizes for the job. The blade is a continuous metal band with a series of teeth on one edge. Blades are classified by the number of teeth per inch, or TPI. The distance between the teeth is known as the pitch.
(TPI and Pitch examples)
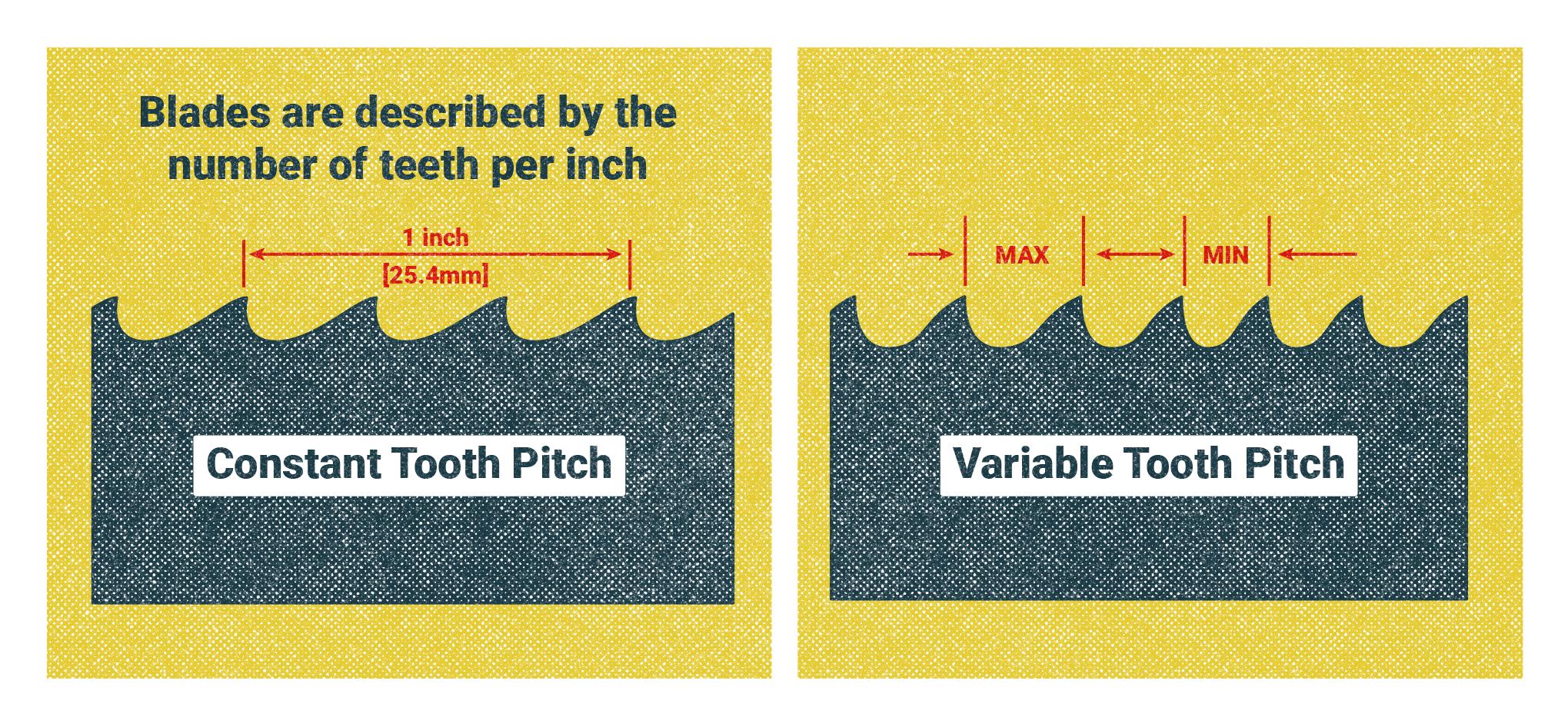
A high number of TPI will indicate a fine-tooth blade for hard material or thin parts due to the three tooth principle. A low number of TPI will be used for softer materials. There are also variable teeth for blades. A blade might be described as a 6-10 blade. That means the number of teeth in an inch varies between six and ten. Because of the variety of blade selections, a variety of materials can be cut. Choose the best blade and settings for the material.
The blade width will help keep the saw running straight or allow the part to be turned so that corners can be cut. A horizontal bandsaw that is set up to precut material will have a .75 or 1.0 inch width blade. This will help it cut straight over longer cuts. Smaller parts cut on the vertical bandsaw may need to have a corner or radius cut. This blade has a .5 inch width to allow it to curve around the part.
Other characteristics of the blade to be aware of are the Kerf, and the width.
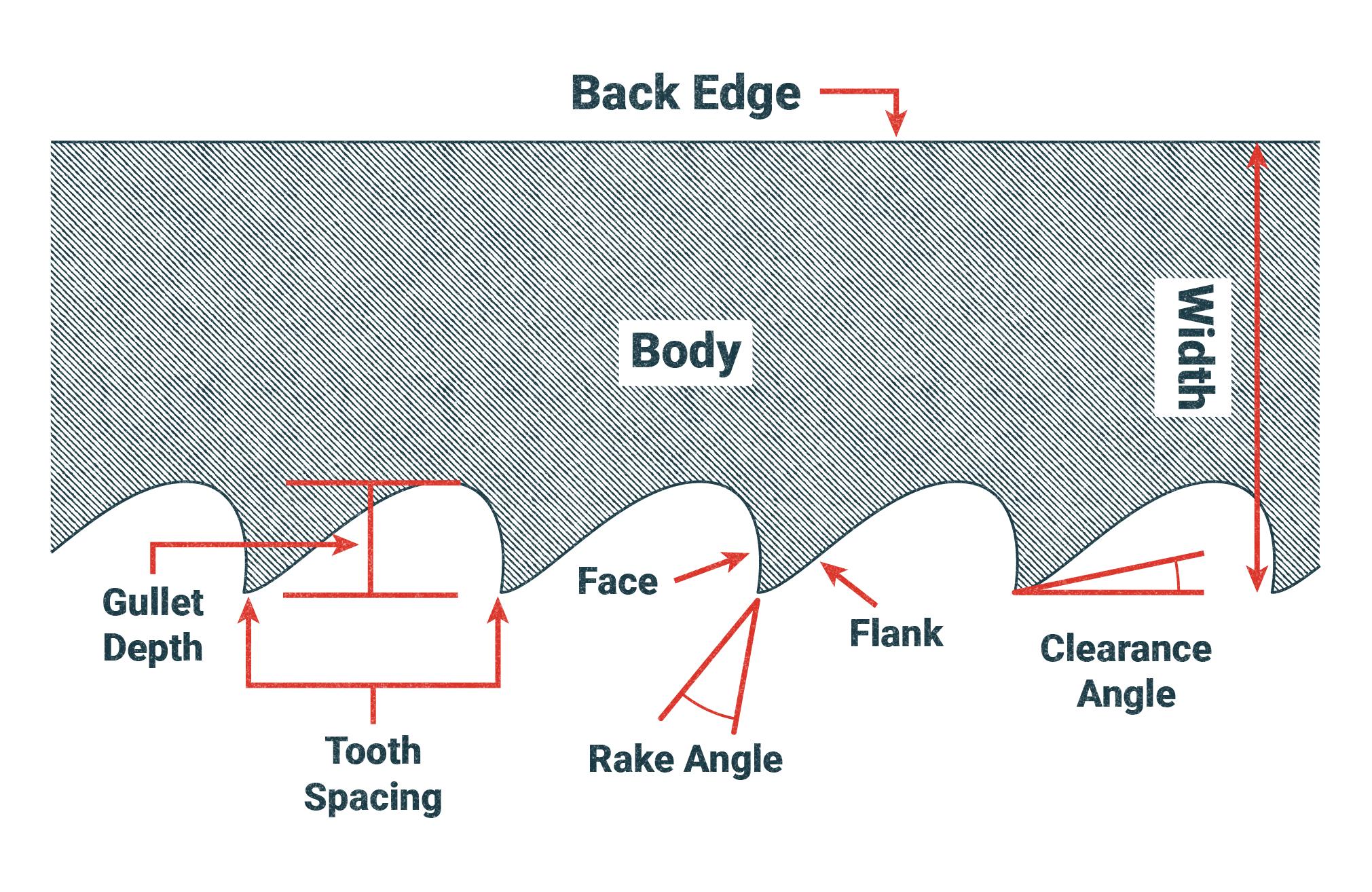
The thickness of the blade is an approximation of the Kerf. The kerf is the amount of material that the blade removes. When cutting several parts out of bar stock, the kerf must be considered to get an accurate number of parts that one bar can provide.
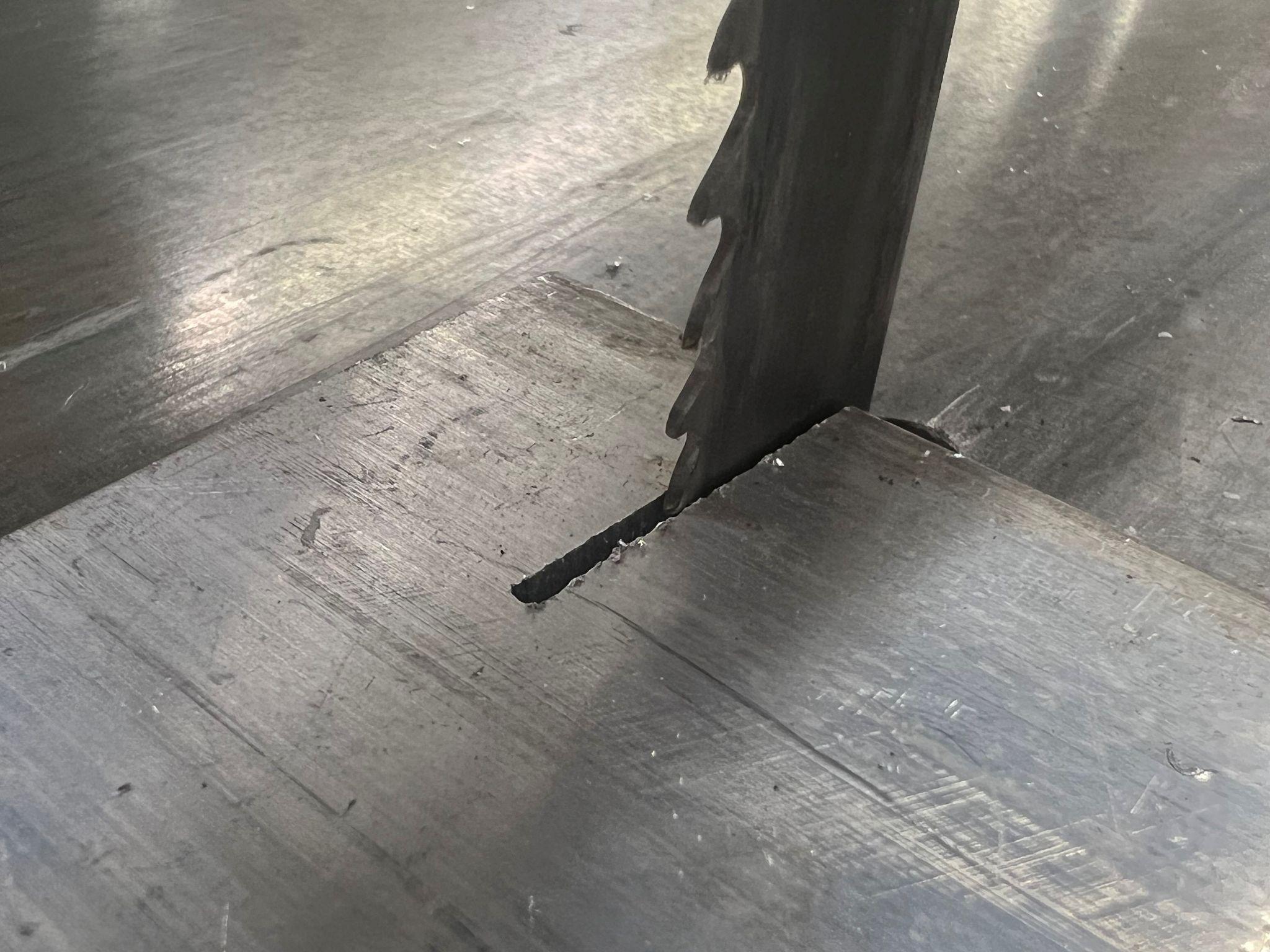
Width is the distance from the teeth to the back of the blade. The larger the width, the straighter the blade will cut. Saw blades that have a width of less than 1/8 inch will allow corners to be cut. When preparing material in the shop, straight cuts are needed.
Tooth spacing is measured in teeth per inch. The number of teeth in one inch is how blades are characterized. The number of teeth is also related to the gullet. The number of teeth in an inch should increase with the hardness of the material. A blade used for steel might have 14 teeth per inch. The blade will run slowly and make small chips. If this blade were used for aluminum, the RPM would be higher. More heat will result from the faster moving blade, bigger chips will be made, and ultimately, those chips will build up in the gullet, and the blade will quit cutting.
The back of the blade is on the opposite side of the teeth. It is usually supported by bearings to provide the pressure of the blade on the material.
There are two large wheels that the blade rides on as the material is cut. There is also a follower that supports the blade as the material is pushed into it. Without the follower, when the part is pushed into the blade, the blade would come off of the wheels and likely be damaged. The continuous nature of the band saw allows it to run cooler than a reciprocation style. The wider the blade is, the straighter and more accurately the blade will cut. (At least until the teeth are worn or damaged.) Using the movable guide supports will help keep the saw cutting straight.
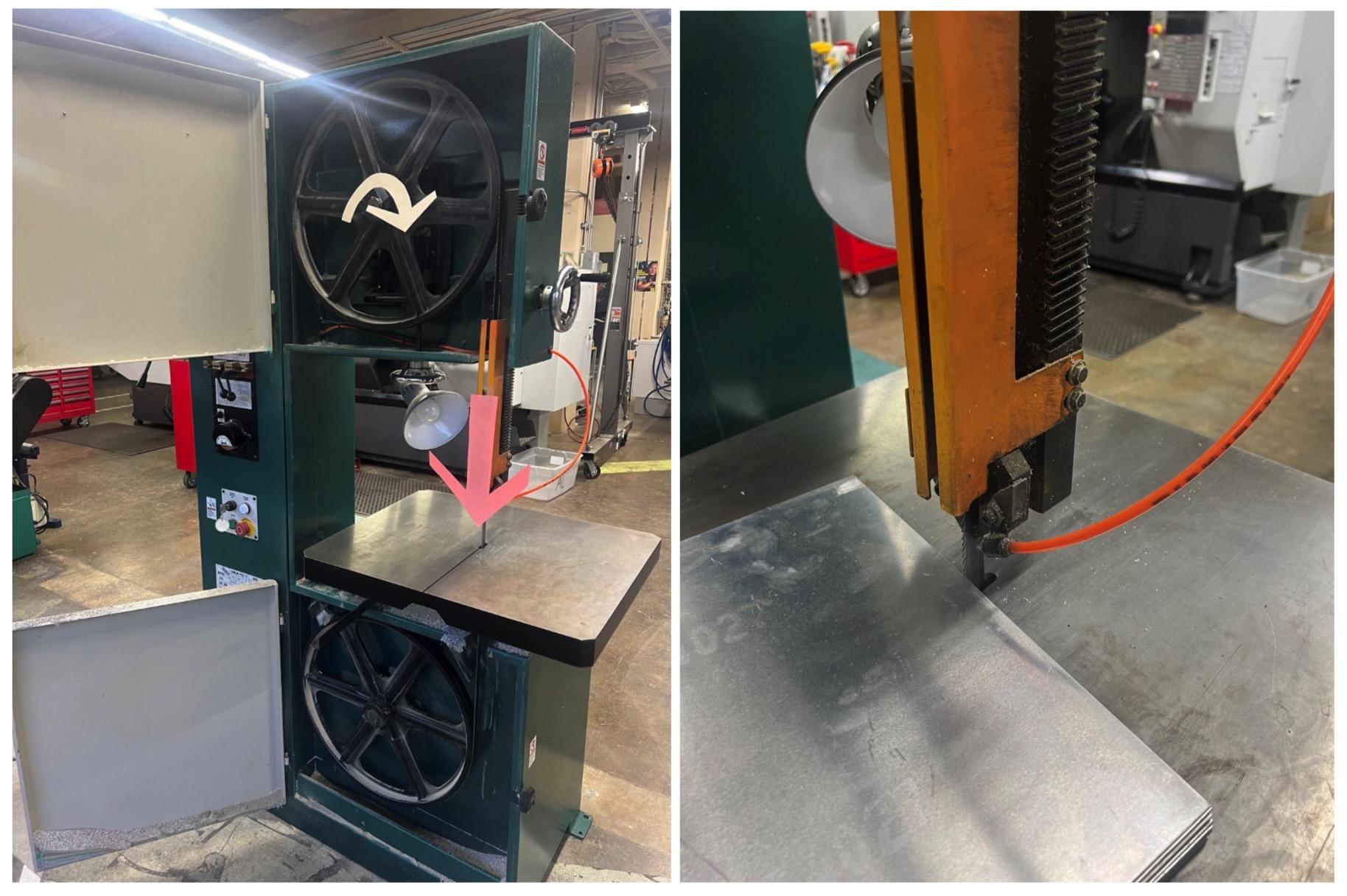
A band saw blade will commonly fall into one of the three following material types:
a. Carbon Steel blades
A carbon blade is a good choice due to these blades being the least expensive. The downside is that they need to be run at a slower RPM than other blades. This means it will take longer to make the same cut than when using a bi-metal, or carbide blade. If curves need to be cut, the carbon steel blade is typically the only type of blade available in a width of .25 or less inches.
b. Bi-Metal blades
These blades have a carbon steel body with a strip of High Speed Steel (HSS) on the side with the teeth. This makes the blades more expensive than the carbon blades. With teeth made of HSS, these blades can run at higher RPMs. This will enable them to cut through material in less time.
c. Carbide tooth blades
These blades are the most expensive because they have brazed-on carbide teeth. In extreme production applications, these blades are often chosen. They can handle a very high RPM and cut through a wide variety of materials.
7.3.2 Choosing an abrasive blade
The type of abrasive blade used in a chop saw depends on the material being cut. Here are a few applications;
- Aluminum Oxide – These blades are designed to cut ferrous materials. They are composed of abrasive grains bonded with aluminum oxide.
- Silicon Carbide – The silicon blade is suitable for cutting non-ferrous materials such as aluminum, brass, and copper. They are capable of fast cuts and have a long life.
- Diamond blades – These are useful in cutting hard materials such as concrete, stone, and ceramic materials.
7.4 Saw Operations, and Handling
7.4.1 Horizontal Saw Operations
Prior to starting your job, tie back long hair, secure loose clothing, remove jewelry, and always wear safety glasses. Here are some basic steps to follow when using a horizontal band saw to cut material.
Determine the proper RPM for the saw. It is common for the saw to be set up for Surface Feet per Minute (SFM). This is based on the type of material to be cut. Aluminum has an average SFM around 700; mild steel is closer to 66 SFM. In general, cut hard material with fine teeth at a slow speed and soft material with coarse teeth at a high speed.
Recall that the three tooth principle states that the material to be cut should be thicker than the three teeth on the blade. Otherwise, you’re likely to break off the teeth of the blade. By having three teeth of the blade always in contact with the material while cutting, the blade and material are supporting each other, and there is constant pressure between the blade and the material. When there is only one tooth engaged with the part, there will likely be damage to the blade as a result of the single tooth hitting the material. If the material is too thin, less than three teeth thick, the force of a single tooth hitting the material will cause a fracture or chip the tooth. This will destroy the blade and require that a new one be installed. Choose between changing the blade to a larger tooth per inch (TPI) blade or getting a piece of sacrificial material to increase the thickness of the material being cut.
AUTHOR’S TIP
Stack up several parts to be cut. This will increase the material thickness AND increase the productivity of the project. In fact, when the boss sees this, you may get the employee of the month parking spot!
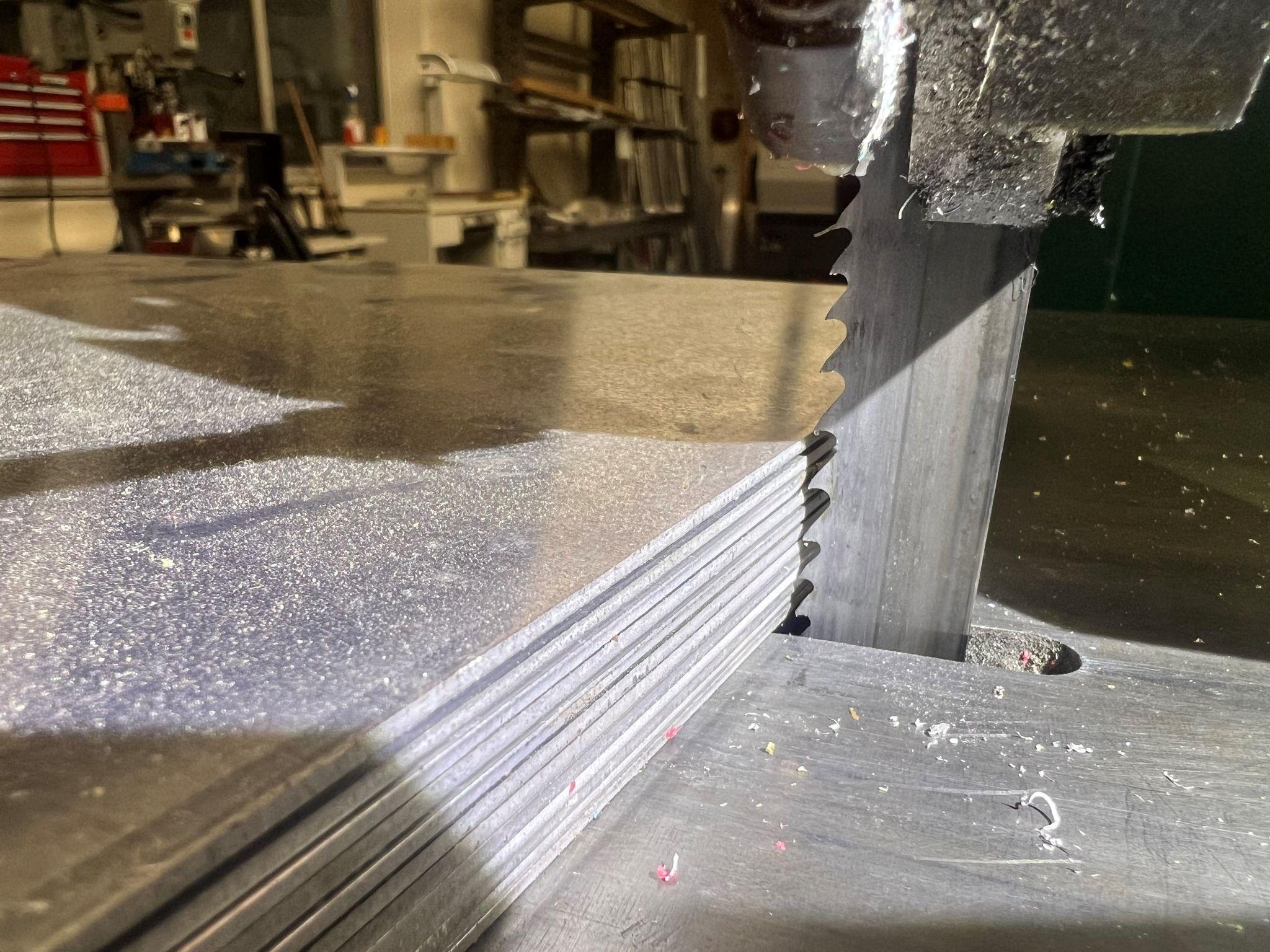
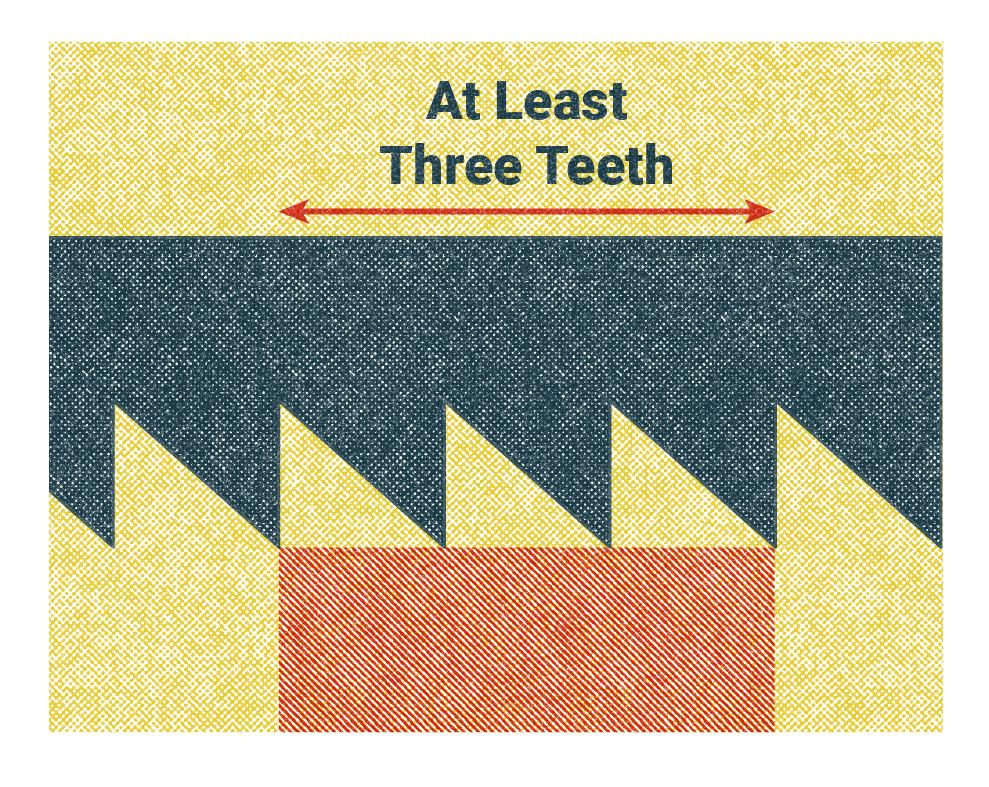
Adjust the guide arms on the leading and trailing sides of the part as close as possible to help support the blade during the cut. If the arms are too far apart, the blade may be damaged. Having the guides significantly away from the material being cut will also allow the blade to bend or twist. This can damage the blade and waste material.
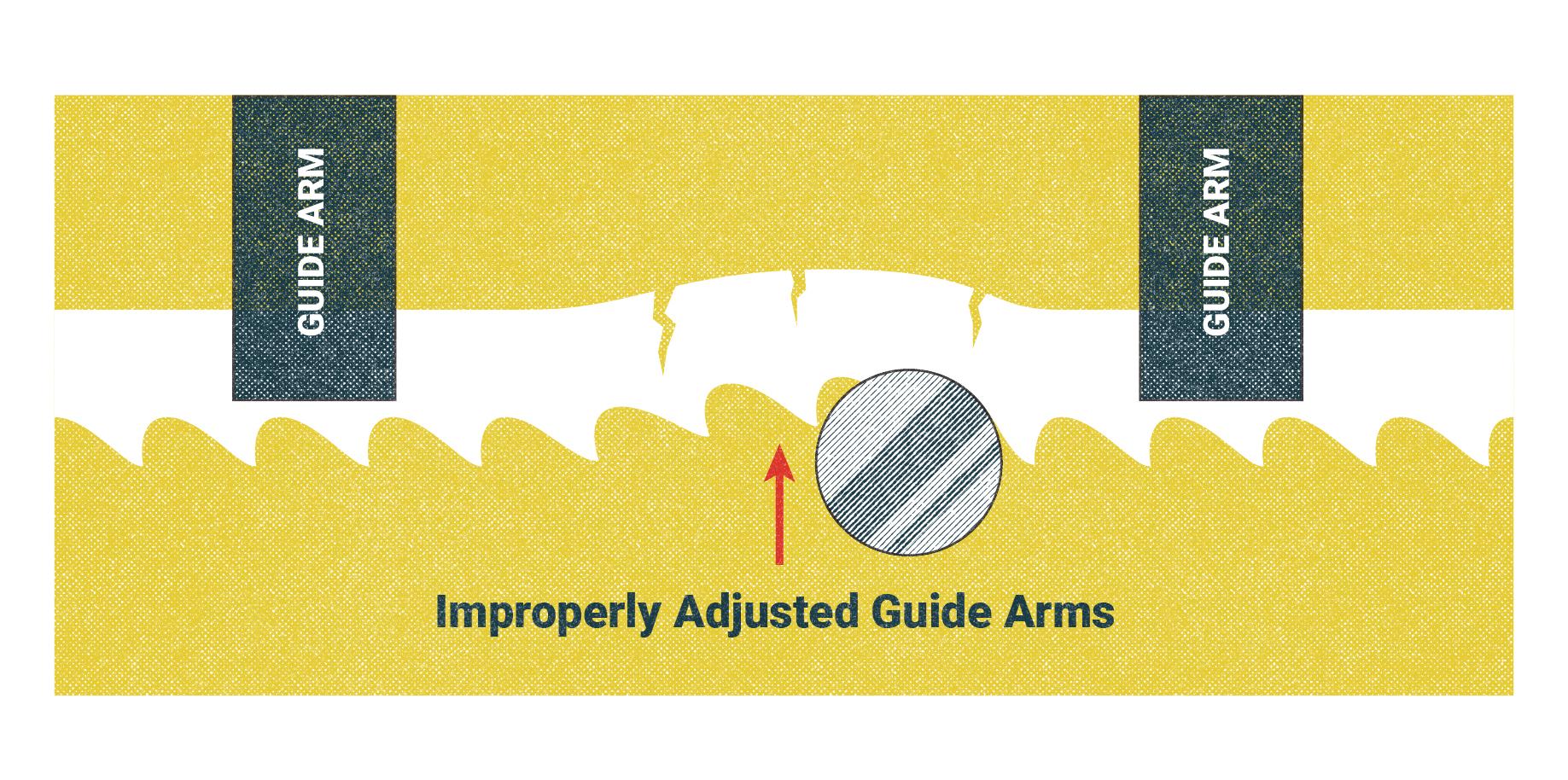
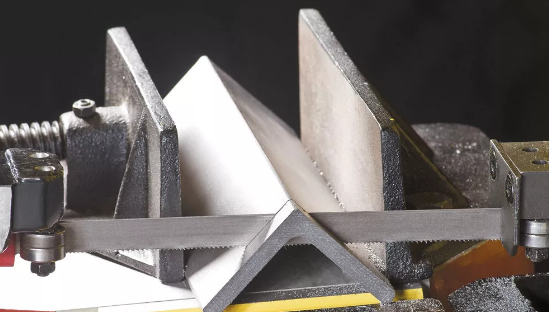
Most machines have a chart as a guide to reference the speed of the blade needed for a given material. Adjust the speed (RPM) if needed.
Never start the blade when it is in contact with the part. It is common practice to start the blade when it is about a ¼ inch away from the part.
Lower the blade slowly to engage the material. Dropping it fast can damage the blade. Verify that the blade is creating chips. If the feed is too slow, it will be rubbing more than cutting, which generates heat and hardens the part. This will also shorten the life of the saw blade. Increase the feed once the blade has made contact to produce a proper chip.
After every operation where material is removed, the part should be deburred in preparation for the next step.
Set up the horizontal saw with the guides close to the part, as shown.
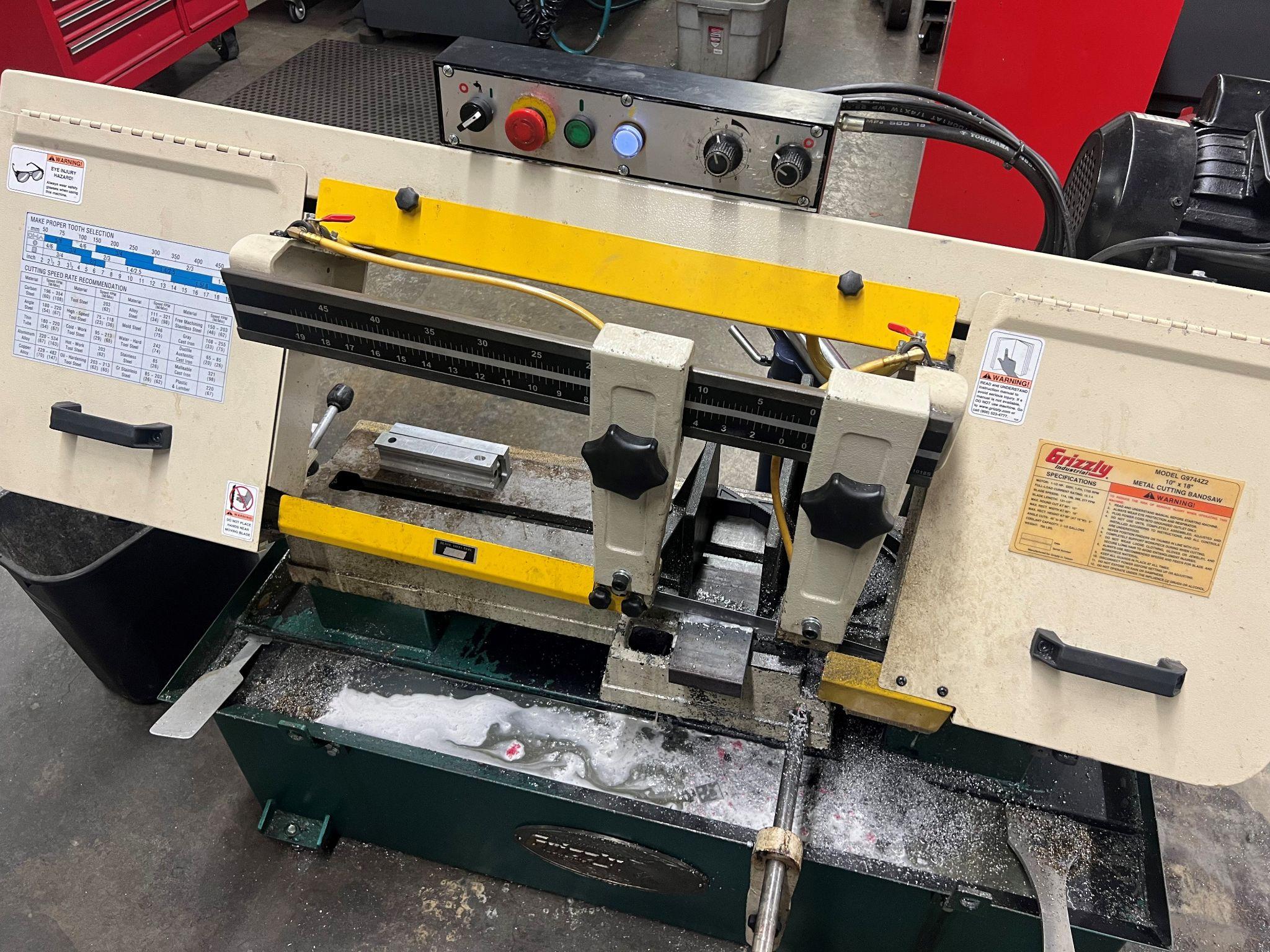
To cut long bar stock, just pull the amount of material past the bandsaw blade, tighten the vise, and cut.
When cutting long pieces of material, it may be necessary to use a moveable stand to support the end away from the saw. This will help keep the material on the table and keep the stock oriented properly to the blade. (see picture below.)
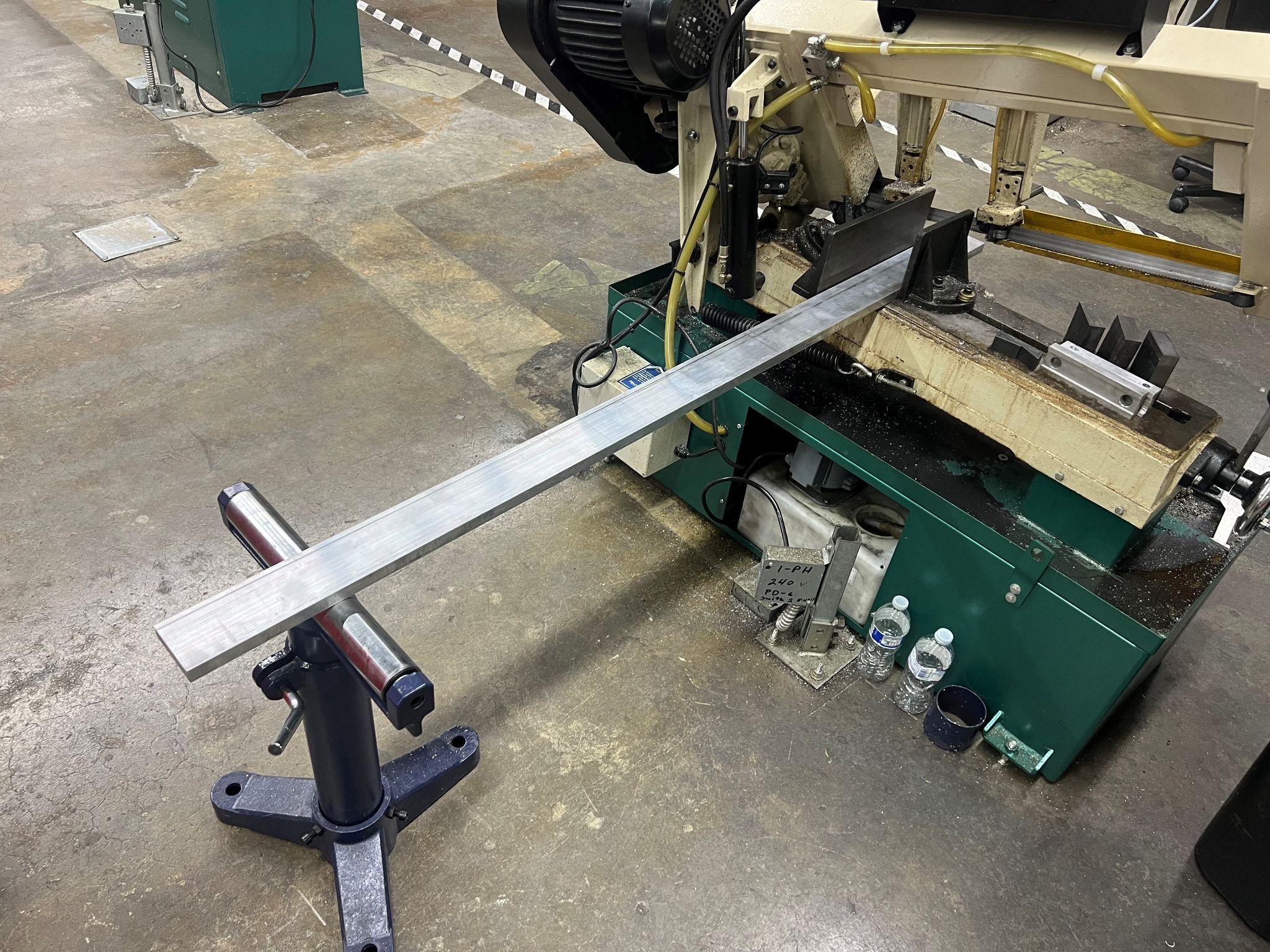
The center of the vise is a pivot point. The part being held needs to extend past this point, away from the saw, to ensure positive holding. If the part is shorter, use different material or remnant stock to extend the jaws out. Also, a set of step blocks can be used opposite the saw blade side to allow the vise to properly hold the small part.
When it comes to shorter parts, step blocks can be used on the opposite side of the pivot point on the vise. Use step blocks stacked to the same size as the material being cut to support the pivot vise on the opposite side of the material being cut.
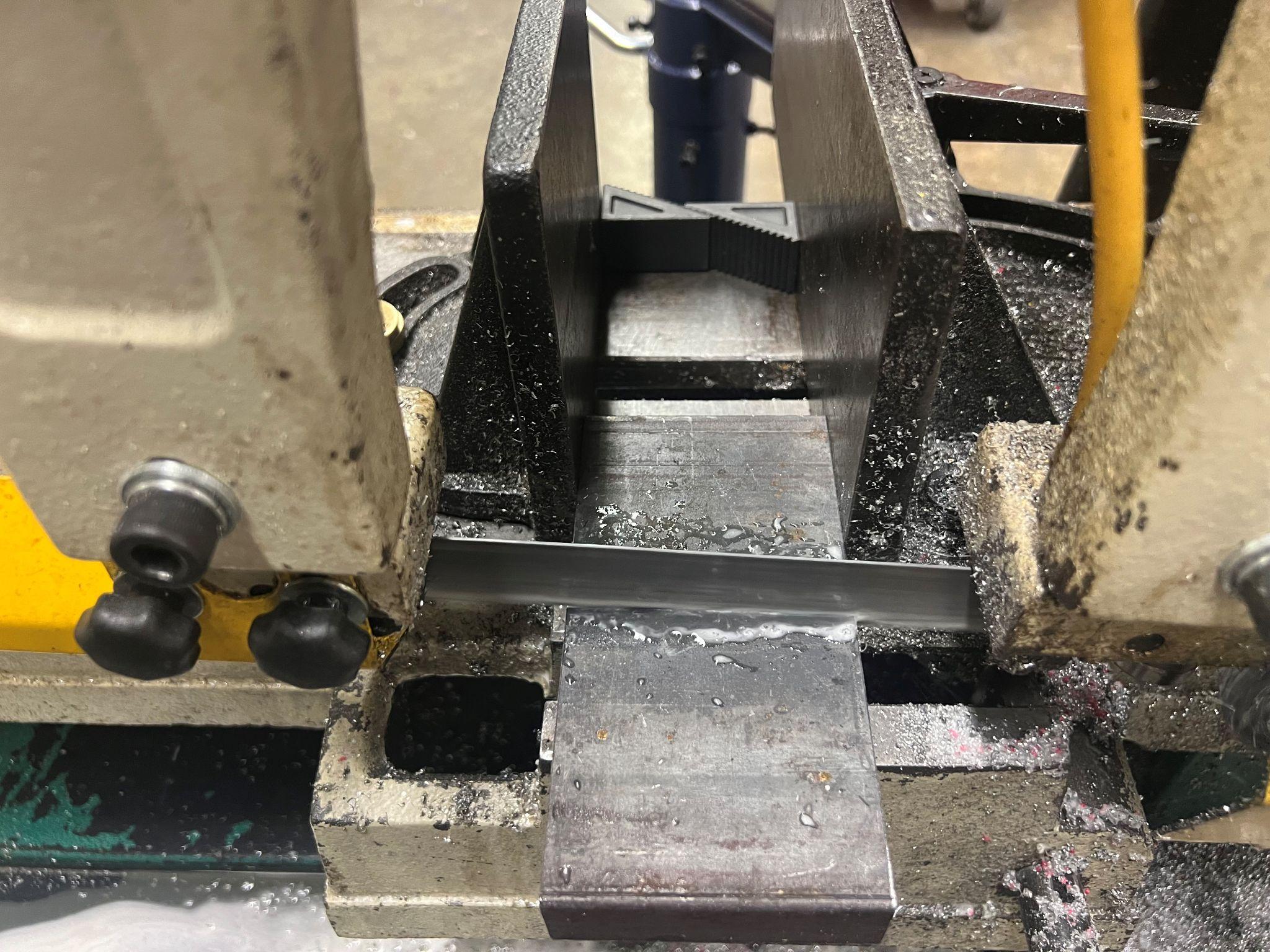
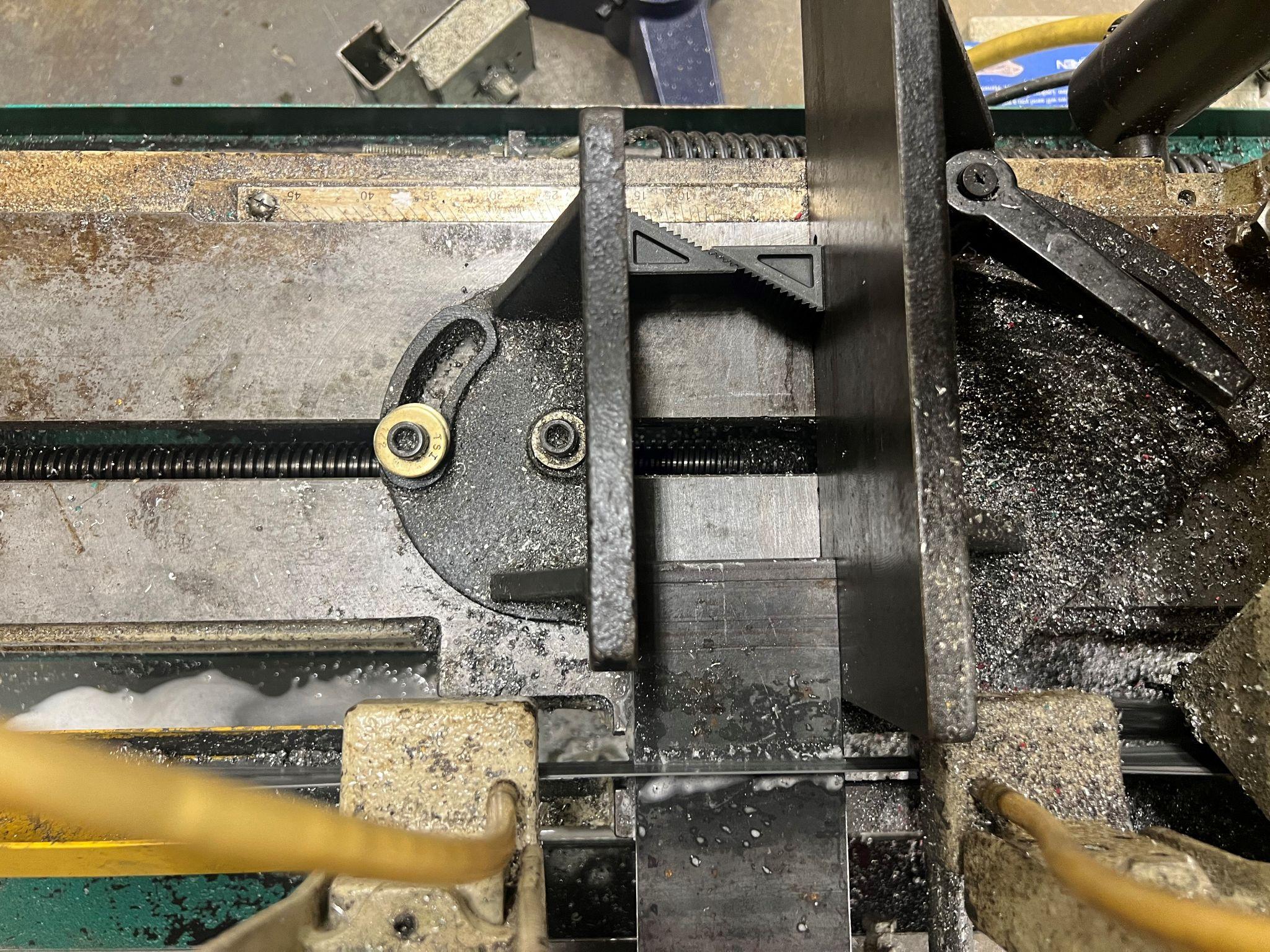
7.4.2 Vertical Saw Operations
Like the horizontal saw, the vertical saw is used to rough-cut material to something close to the finished size of the part. This helps to increase productivity and profitability. It can also be used to remove excess material that is not needed.
The cut made on a vertical saw may be just a simple straight cut (a wide blade) or something with more complex curves or shapes (a narrow blade). Drilling holes in the part at a corner can aid in the cutting of irregular shapes.
Steps to keep in mind when using the vertical saw.
- Assess the thickness of the part to be cut. Add material if it has a thickness of less than three teeth. As an option, a person could change the blade to a finer pitch.
- Adjust the overhead guide arm so that it is just above the part.
- Always keep your fingers away from the blade. (At least the ones you want to keep!) It is strongly suggested that you use a piece of wood to push the part through.
- Cutting a round piece of material on the saw is very dangerous because the blade will want to grab the material, and spin it. This can ruin the finish on the material and/or damage the saw. Clamping a square piece of material to the bar stock may help to inhibit the rotation.
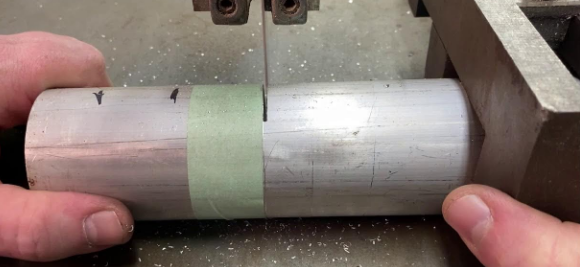
This picture demonstrates a square being clamped onto a round part when using a vertical saw. The square will keep the round part from spinning as it is being cut.
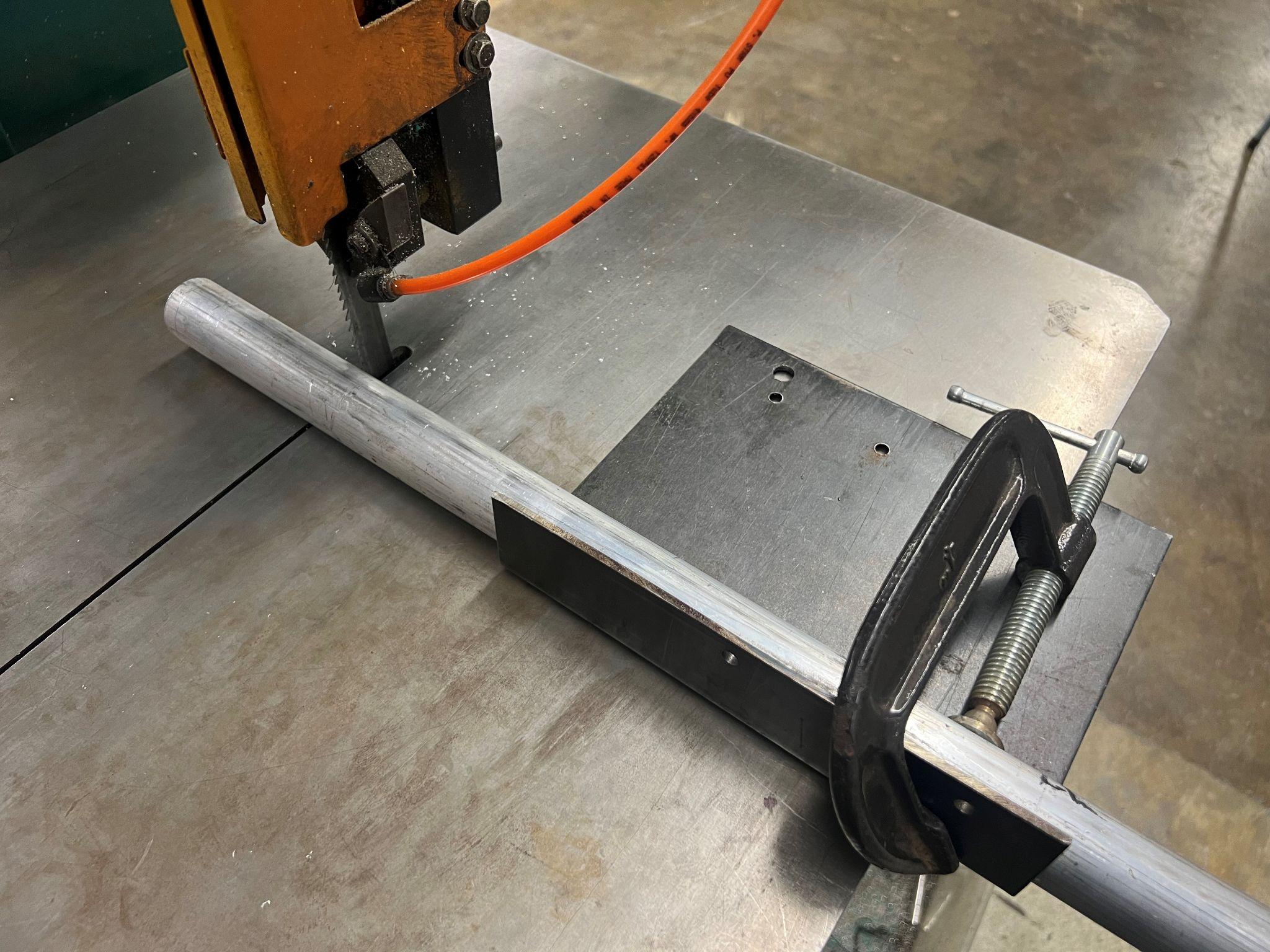
7.4.3 Abrasive Saw Operations
The abrasive saw is a fairly basic piece of equipment. Points to keep in mind when using these saws include:
- Proper clamping in the vise. This is similar to the horizontal band saw. Ensure that both sides of the vise are engaged.
- Long pieces of material will need to be supported.
- These saws produce sparks and dust. Be aware of where the exhaust of sparks and dust is going. Fires have been started by something as simple as an unmonitored spark.
- This piece of equipment is quite loud, and hearing protection, along with eye protection, is necessary when using it.
- Care must be exercised when cutting. The area around and near the cut in the material will be very hot. Burning injuries are possible.
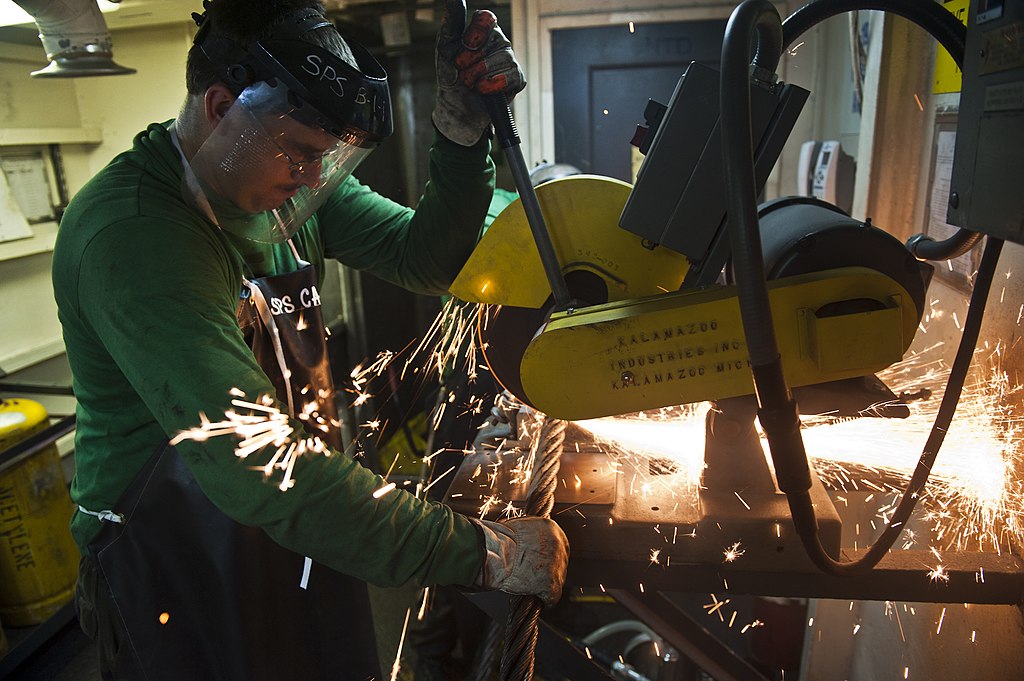
SUMMARY
REVIEW QUESTIONS
- How would you cut .031 thick material with a vertical bandsaw using an 8-10 tooth blade?
- Why choose a Horizontal saw over the other two types of saws that are discussed?
- Why choose a Vertical saw over the other two types of saws that are discussed?
- Why choose an Abrasive saw over the other two types of saws that are discussed?
- What is the pitch of a saw blade?
- Explain the importance of the kerf of a blade.
- Abrasive saws create what types of hazards?
- Which abrasive saw blade would be good to use for a wide variety of steel?
- What is the significance of a variable pitch saw blade?
- What should you use to push material through the saw when cutting?