Chapter 8 Part 1: Drill Presses
SAFETY
Safety needs to be the first concern with any piece of equipment in a machine shop, and the drill press is no different. It may seem like a simple, non-threatening piece of equipment, but it still has the capability to injure the operator. Machinists using the drill press need to follow all the standard safety rules of the shop (see [crossref:2]chapter 2[crossref]) in addition to knowing the specific potential hazards they may encounter.
Rotating hazards
Drill presses have a rotating spindle and tooling that can catch clothing, gloves, jewelry and hair. Removing or securing these items is necessary when operating a drill press to avoid serious injury. The rotating components of a drill press can also be dangerous to fingers and hands. Keep all body parts at least 6” from rotating components.
Possible pinch points on a drill press are the belts and pulleys between the tool and the work, or the potential for loose rotating work to pinch the operator between the work and the column, just to name a few. Some large drill presses also have power feeds that could be hazardous if the operator becomes complacent. The operator must be aware of potential pinching situations and keep away from harm.
Sharp hazards
Cutting tools and chips produced on drill presses are sharp and can easily injure the operator. Tools must be handled gently and not held at sharp edges. Chips should be cleaned up with brushes, brooms, and dust pans to minimize the chance of the operator getting cut.
Slipping hazards
Cutting oil and chips, produced in the cutting process of the drill press, can be slippery and dangerous if allowed to accumulate on the floor around the machinery. Chips should be frequently swept up around the floor when they begin to accumulate during operation. Oil and cutting fluid should be used sparingly and in a manner that doesn’t collect on the floor. If the floor of the work area does become covered with oil and grease, it should be cleaned up immediately with a quality degreaser and a mop. Slippery work conditions often lead to falls and injuries to the operator.
MACHINE MAINTENANCE
Machine maintenance is a term for the periodic upkeep of a piece of equipment. Most machines have a section in the operator’s manual that covers the scheduled maintenance for that particular machine. Lubricating and cleaning of the equipment must be performed daily by the operator. Lubricating components with way oil or greasing mechanisms are a couple of the maintenance points an operator must be aware of.
Lubrication
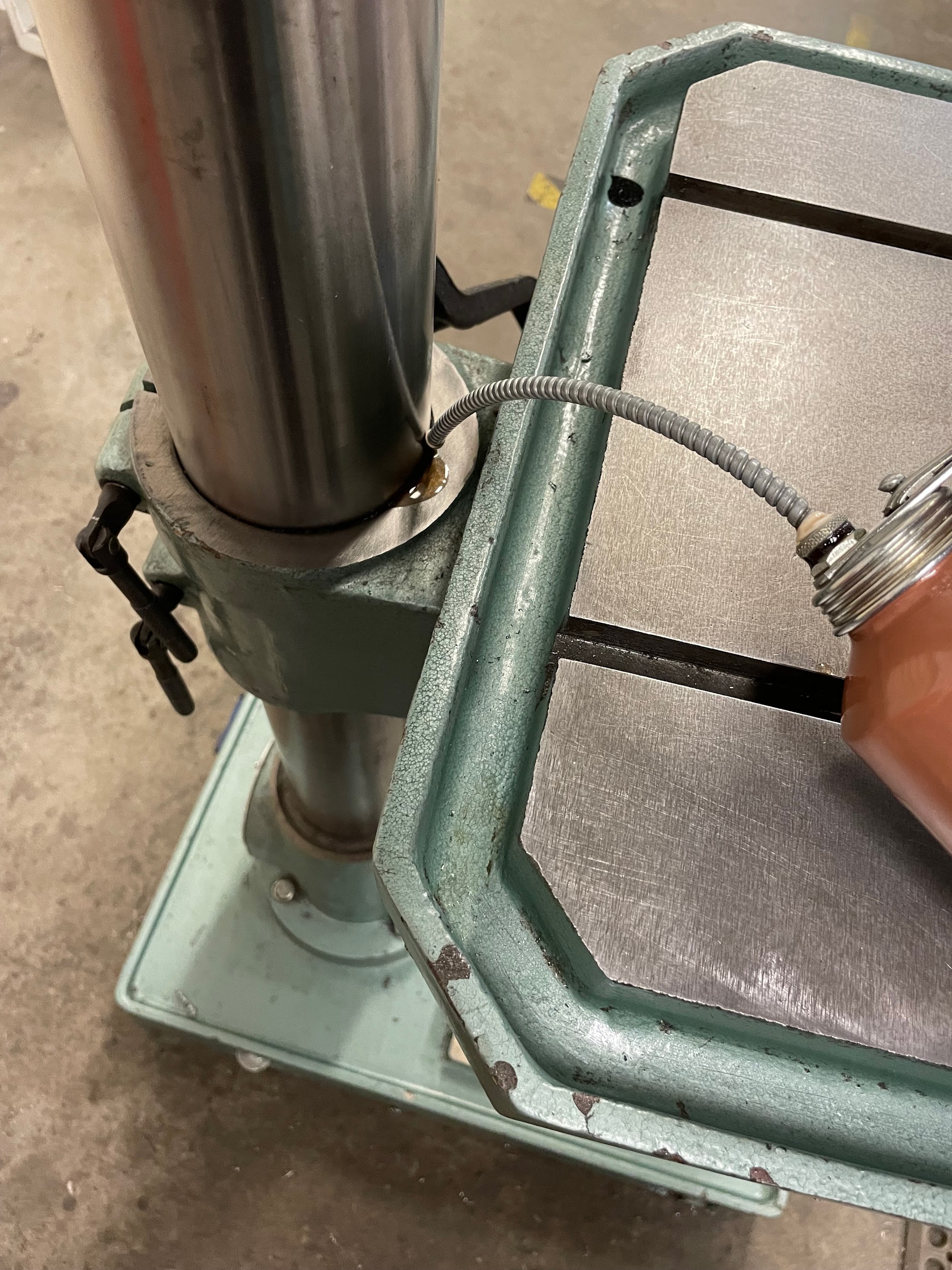
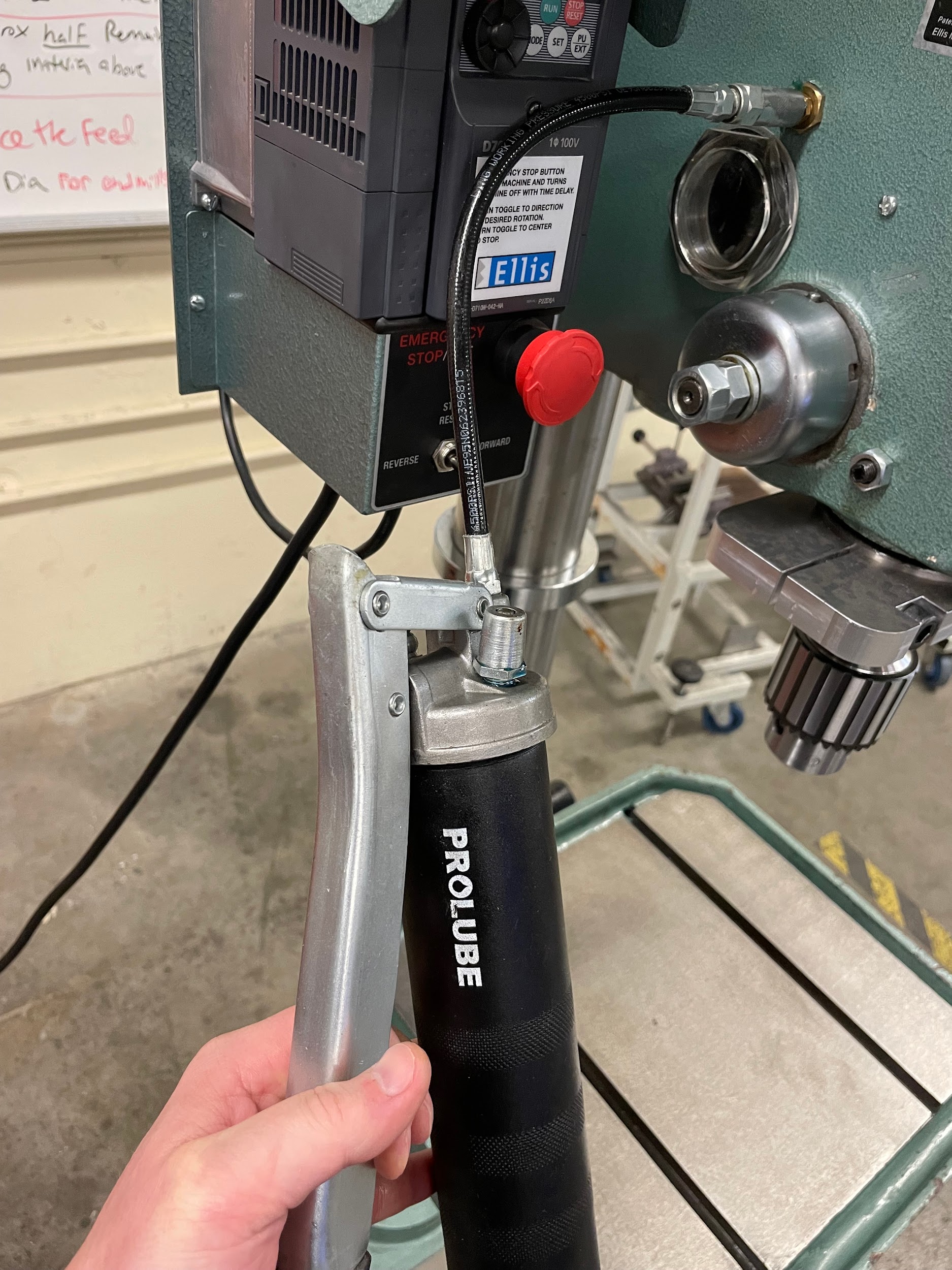
Depending on the style of drill press the machinist is using, there may be many grease zerks , oil cups and oil reservoirs that need attention. The amount of attention spent on lubrication of the machine is directly related to the amount of use the machine sees. If the machine is used heavily, the operator may need to attend to lubrication points multiple times during the shift. Sometimes, once at the beginning of use is plenty. Some lubrication points are designed to only need servicing weekly, monthly, or yearly, based on use. The best way to get the proper lubrication information for a machine is to consult the maintenance section of the instruction manual for lubrication type, amount, and schedule.
Cleaning
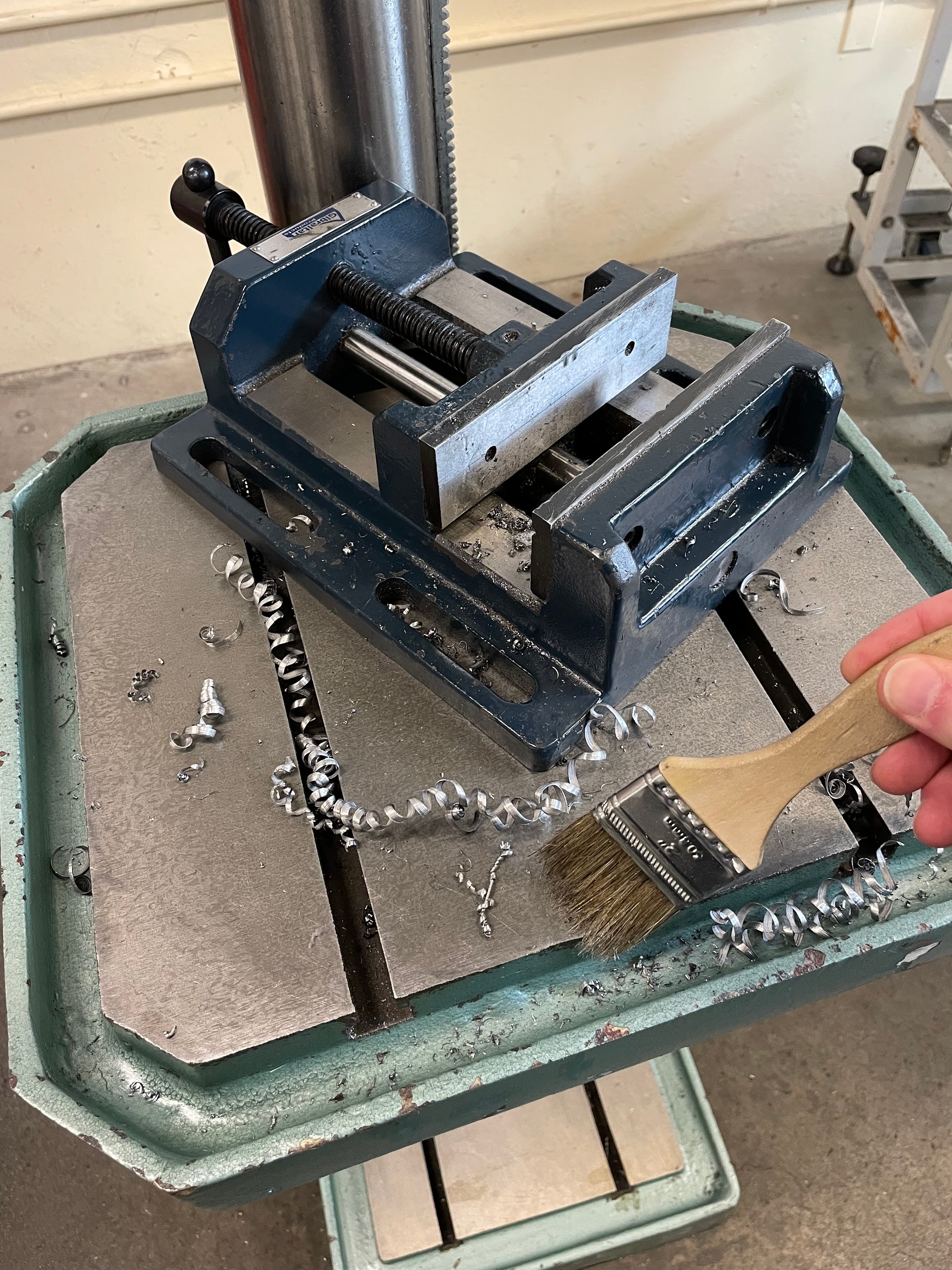
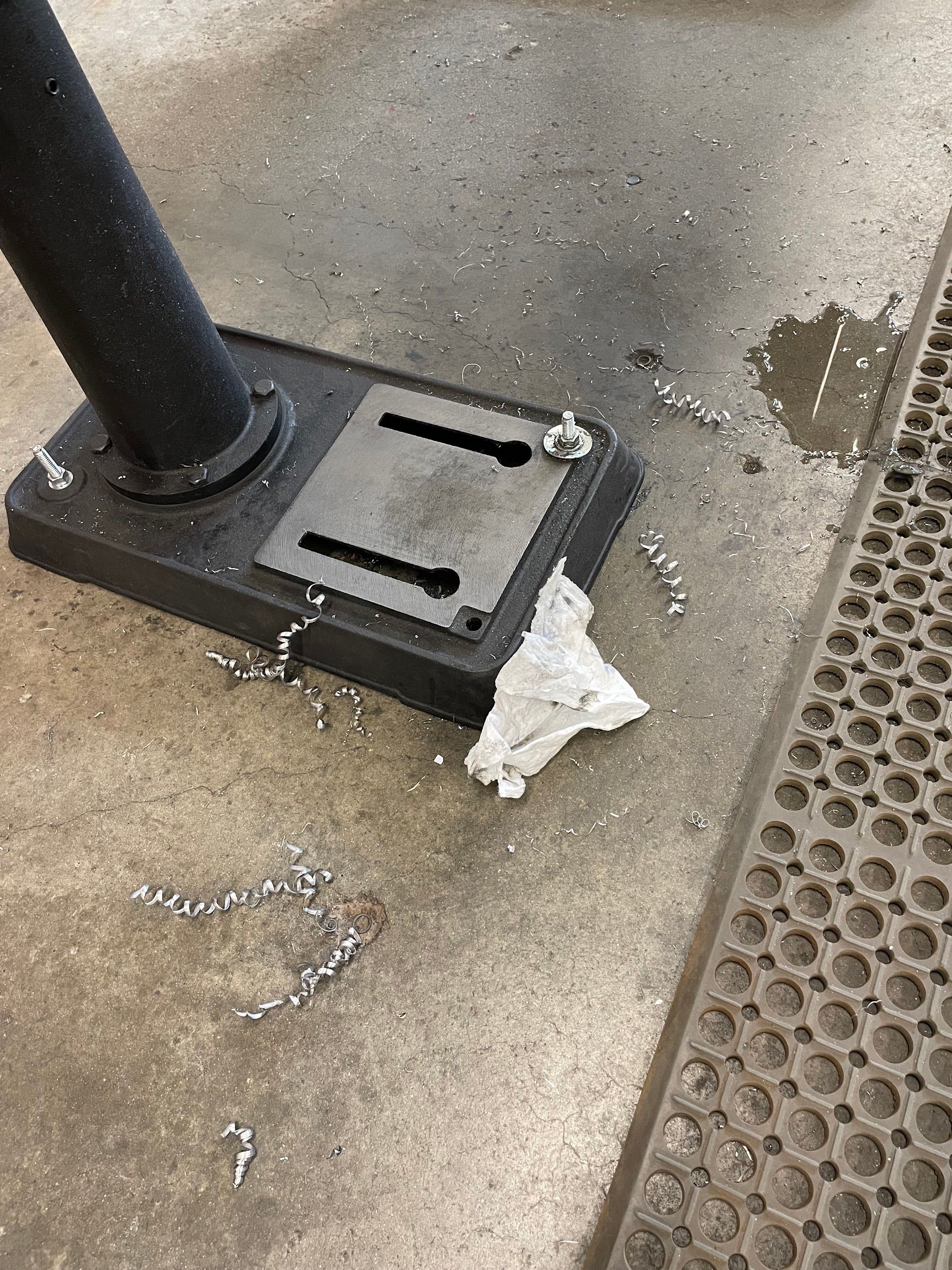
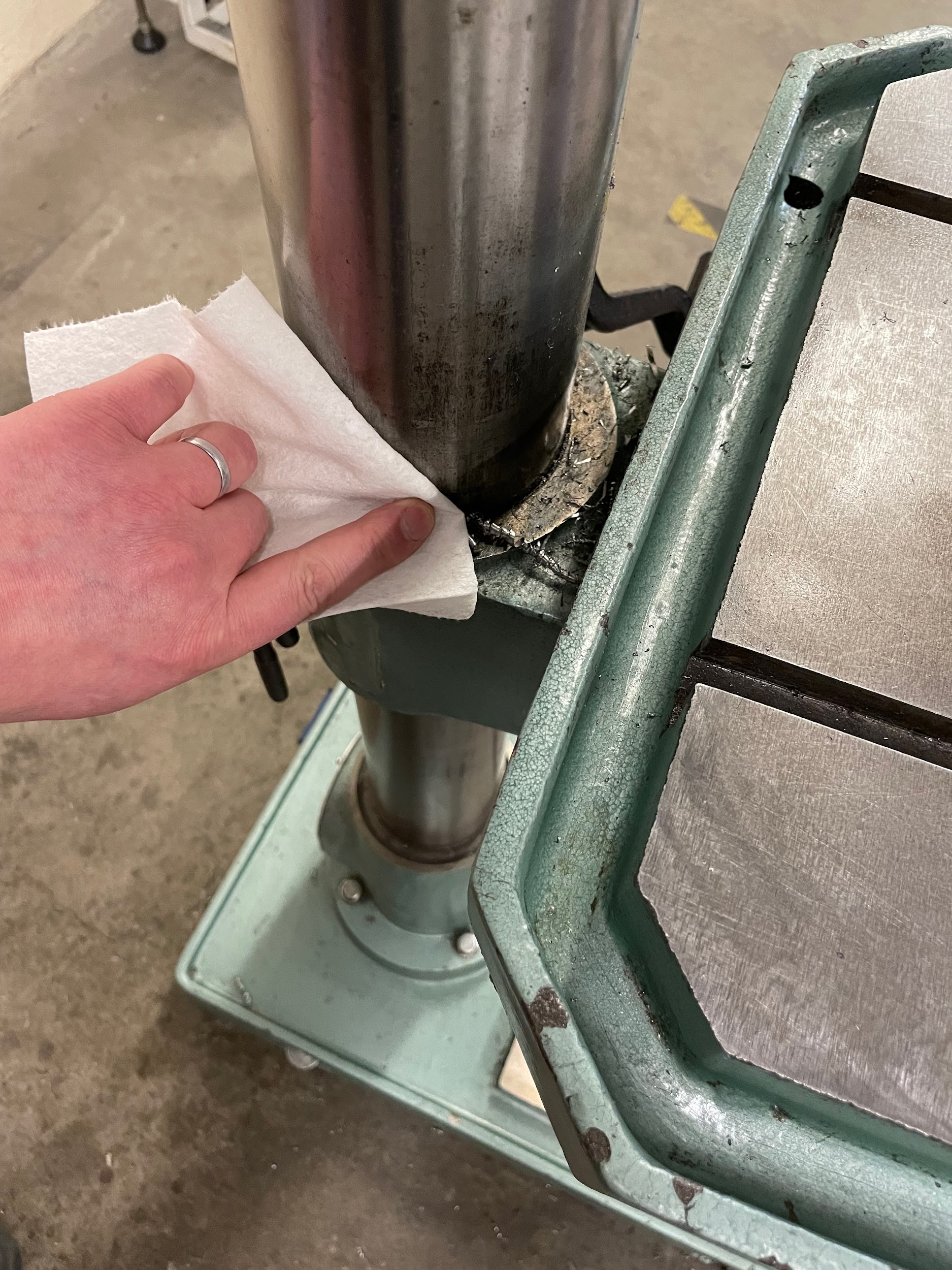
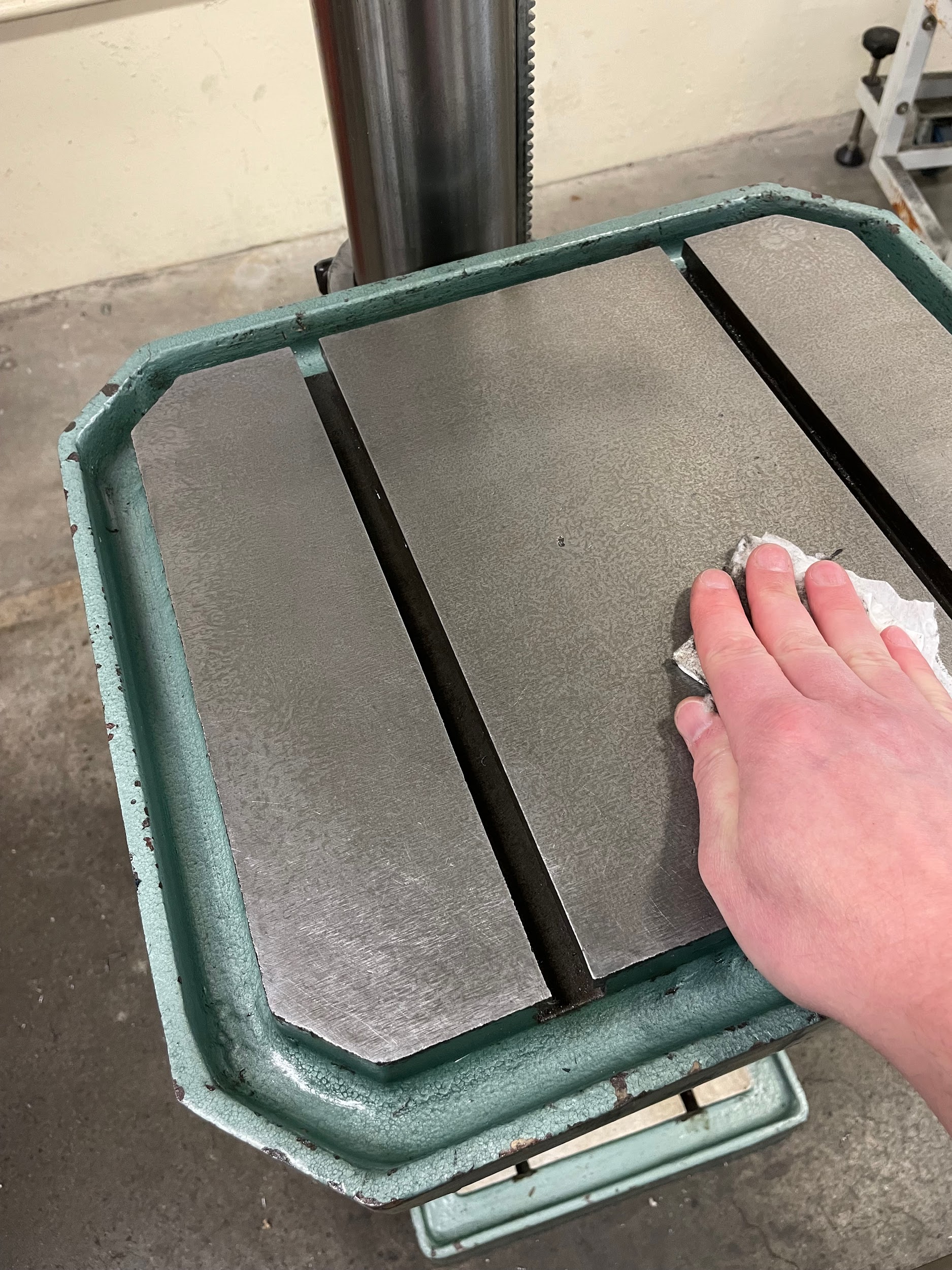
Any operation performed in a machine shop requires a high level of cleanliness. Although a drill press is a basic machine in a shop, it still requires clean tools and work surfaces in order to hold tolerances and insure safety. The table of the drill press should be kept free of grease, rust, burrs, and chips. Drill chucks and tooling should have chips and burrs removed. Vises, parallels, and clamps should be checked and cleaned frequently when machining multiple parts. At the end of a job, chips should be swept up, oil removed, and all tools returned to their storage area. The machine should look as clean or cleaner than before the operator started using it.
MACHINE COMPONENTS
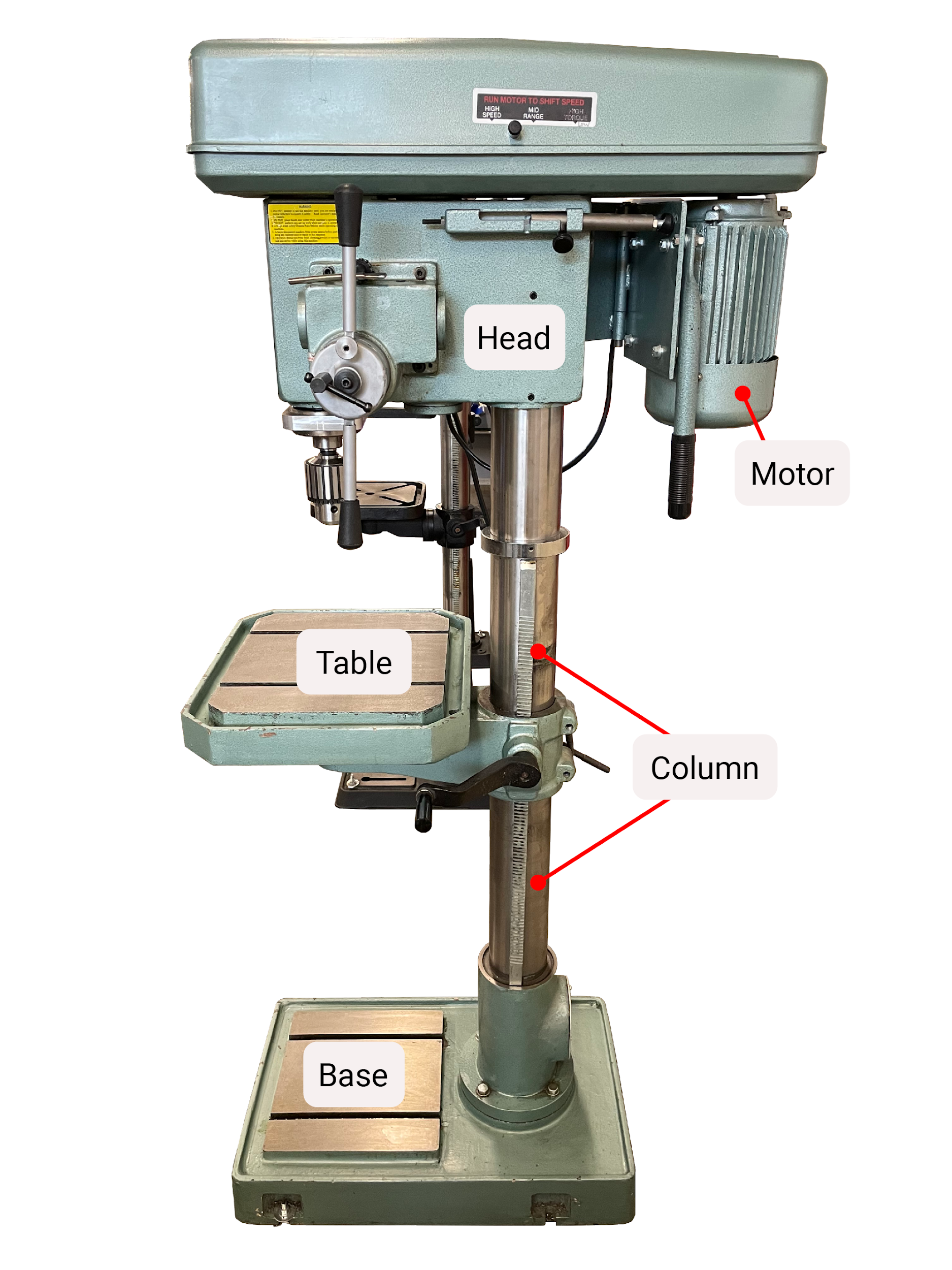
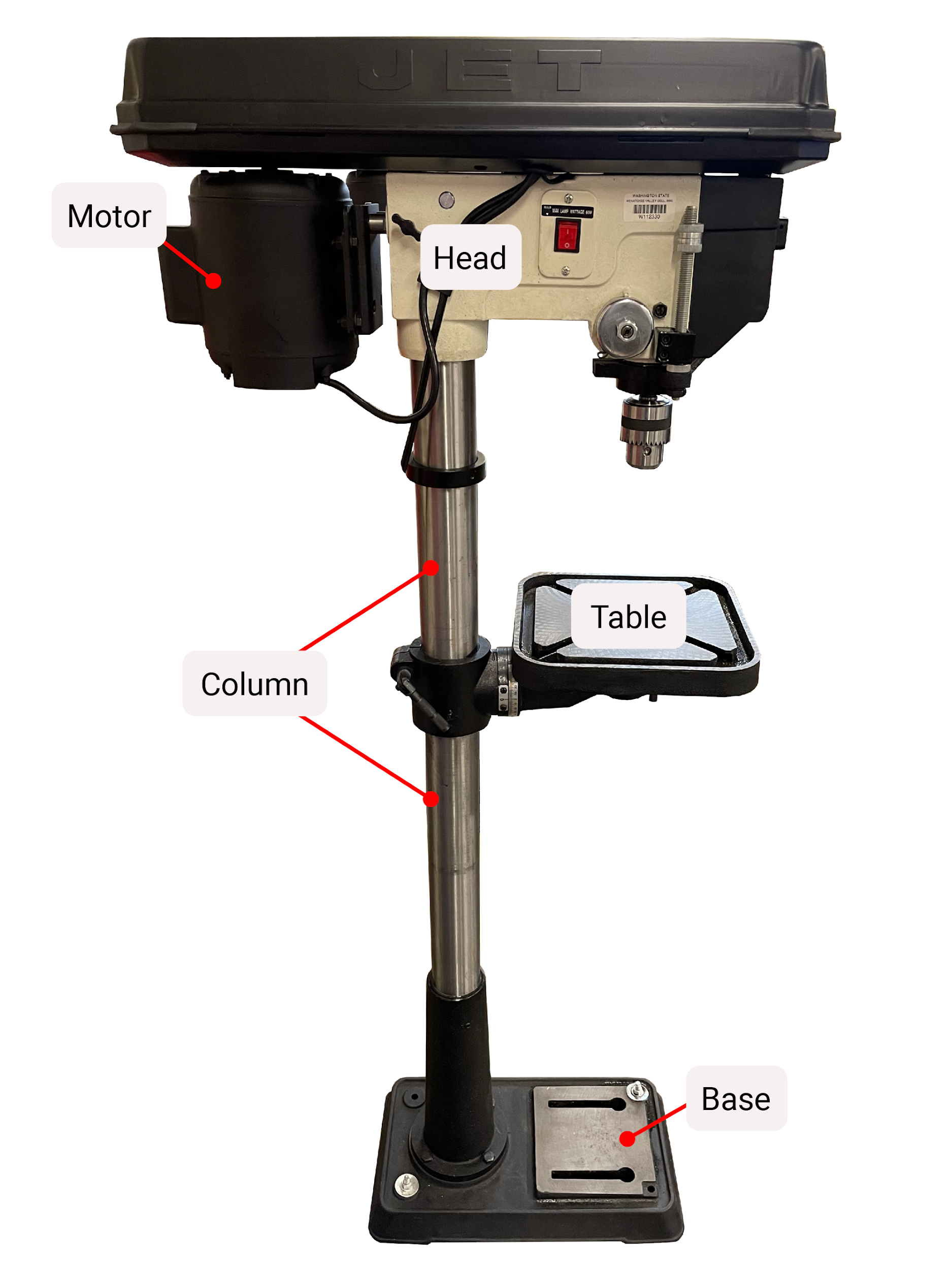
It is important that all drill press operators are familiar with the components of the machinery they are using. Getting to know the equipment, features, and functionality will help the machinist perform work in the safest and most efficient manner, as well as give them the industry specific nomenclature necessary to effectively communicate with coworkers.
Base
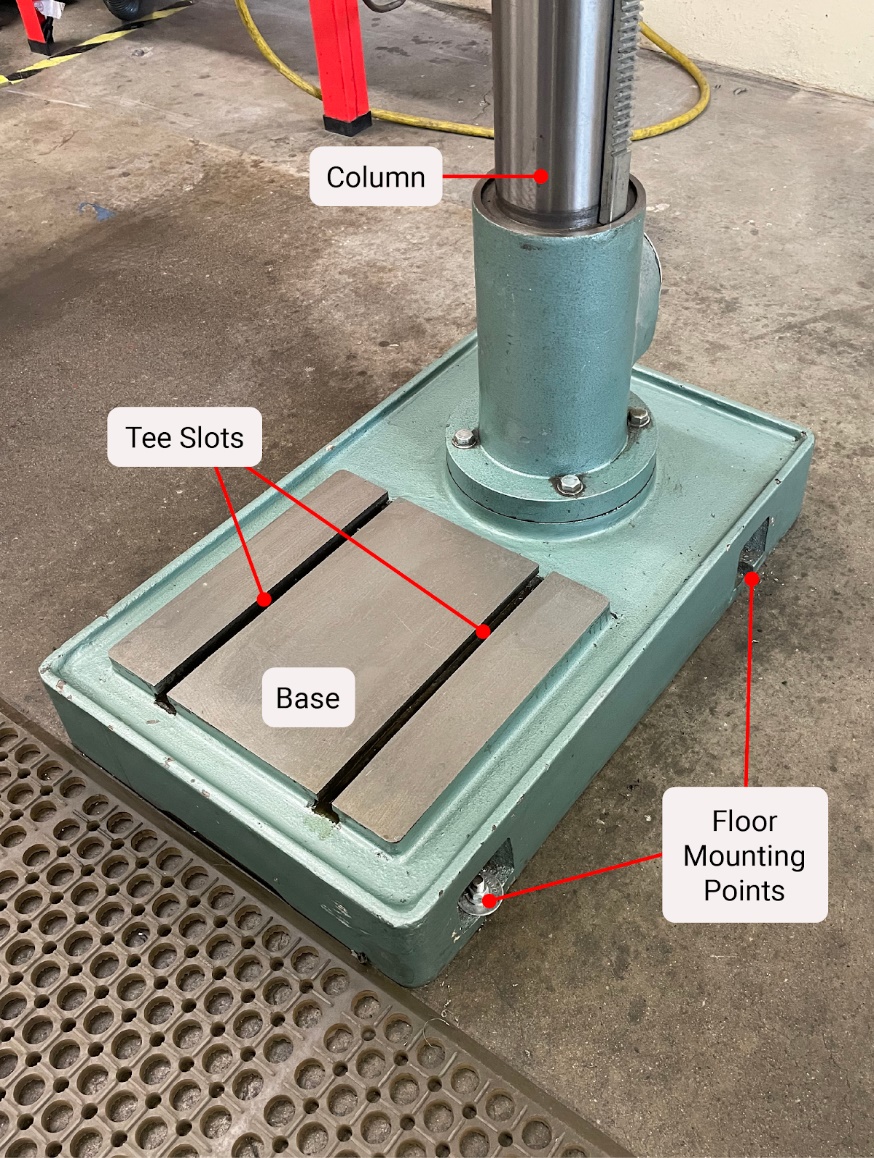
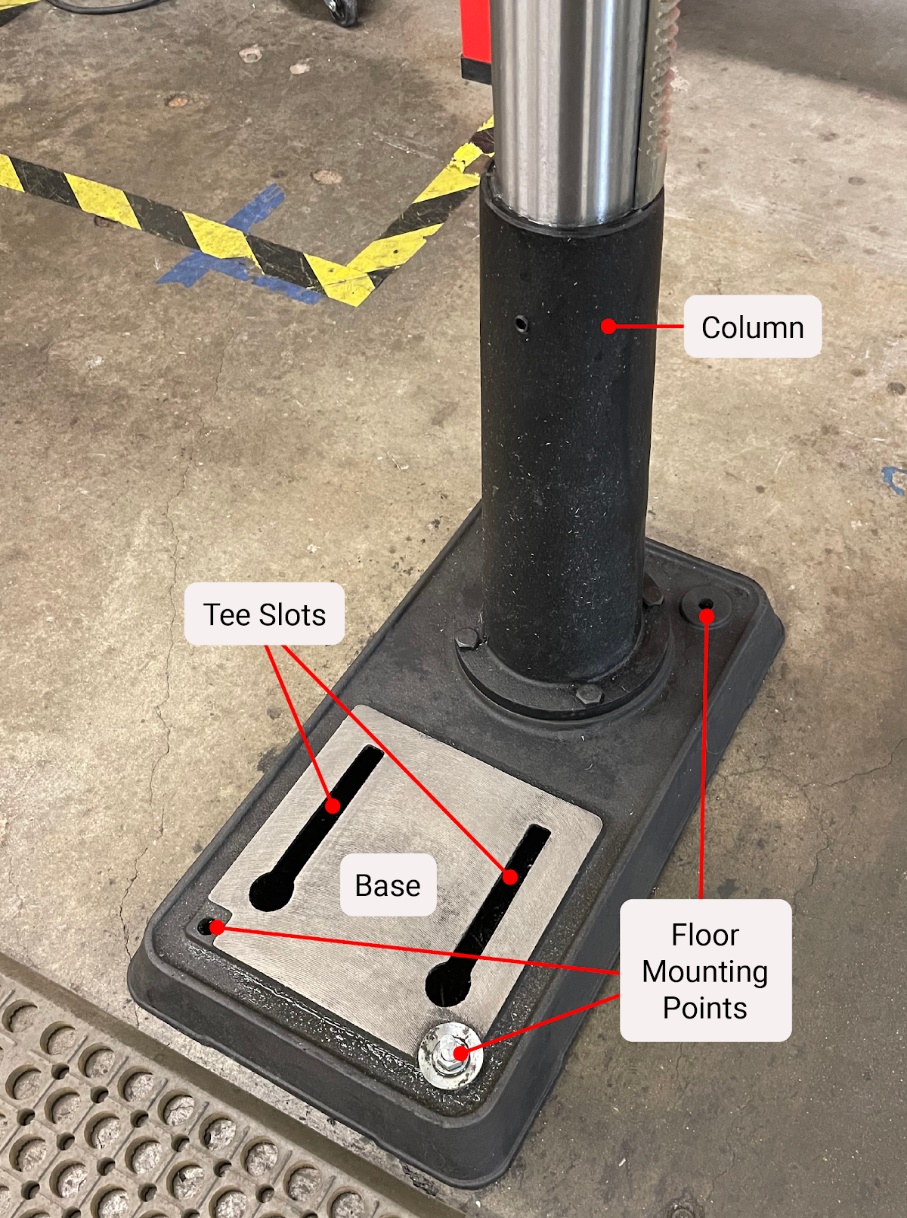
A drill press base bolted to a concrete floor. A drill press column is bolted to the base. The column, tee slots, base, and floor mounting points are labeled.
The base of the machine is the supporting feature, often made of heavy cast iron. It is often bolted to the floor for maximum stability. The base includes a flat surface used to bolt large parts by way of the integrated tee slots. The back of the base is where the column is attached.
Column
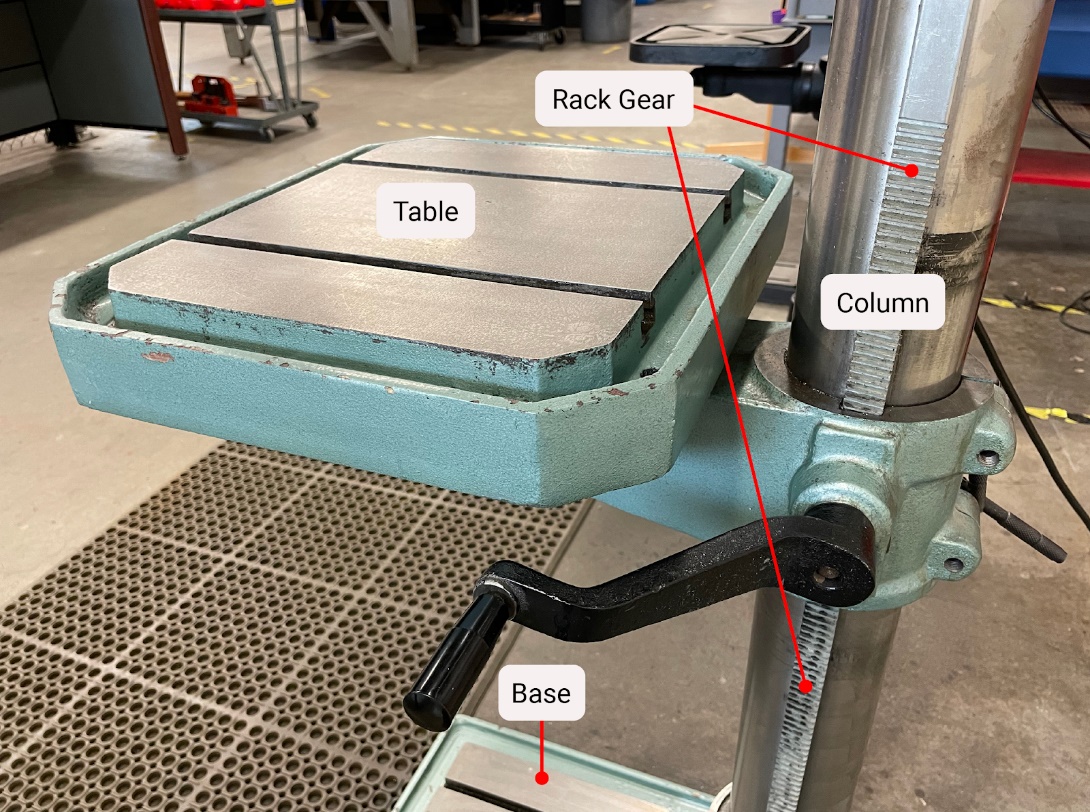
A drill press column with a drill press table attached. The table, rack gear, column and base are labeled.
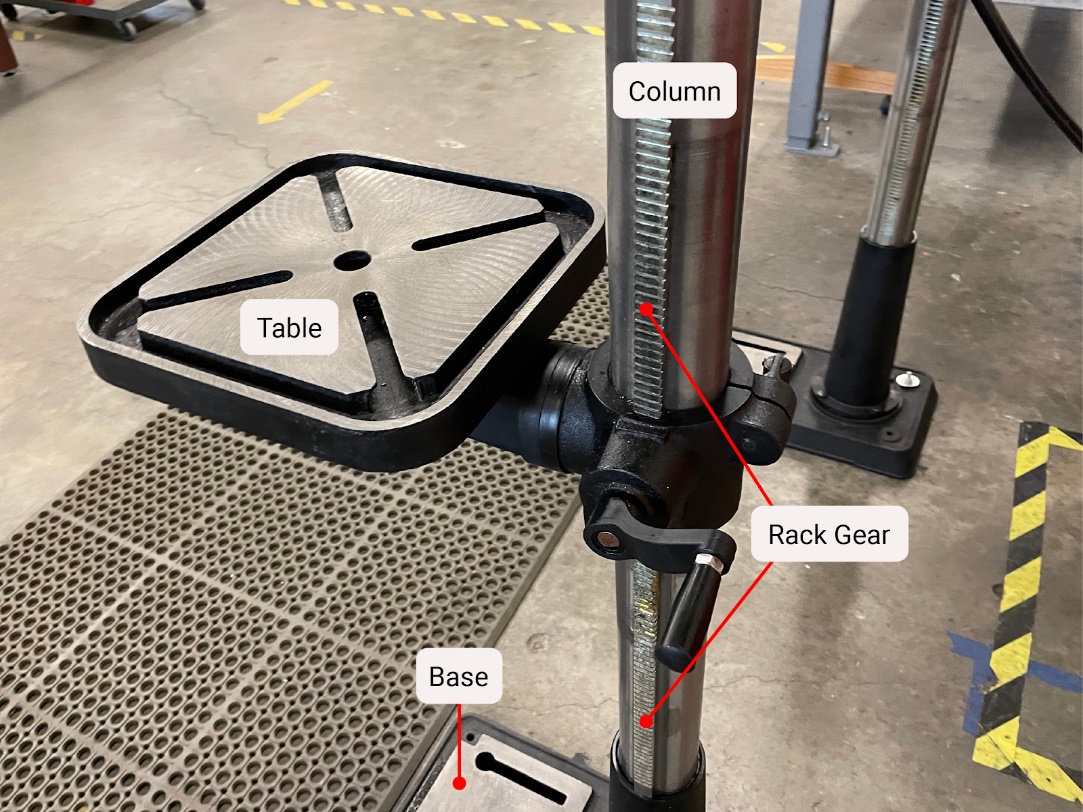
The column is a precision cylindrical shaped rigid tube that is attached to the base. The column provides support for the other components, tying them to the base. The head of the drill press is located at the top of the column, while the table travels between the base and head.
Table
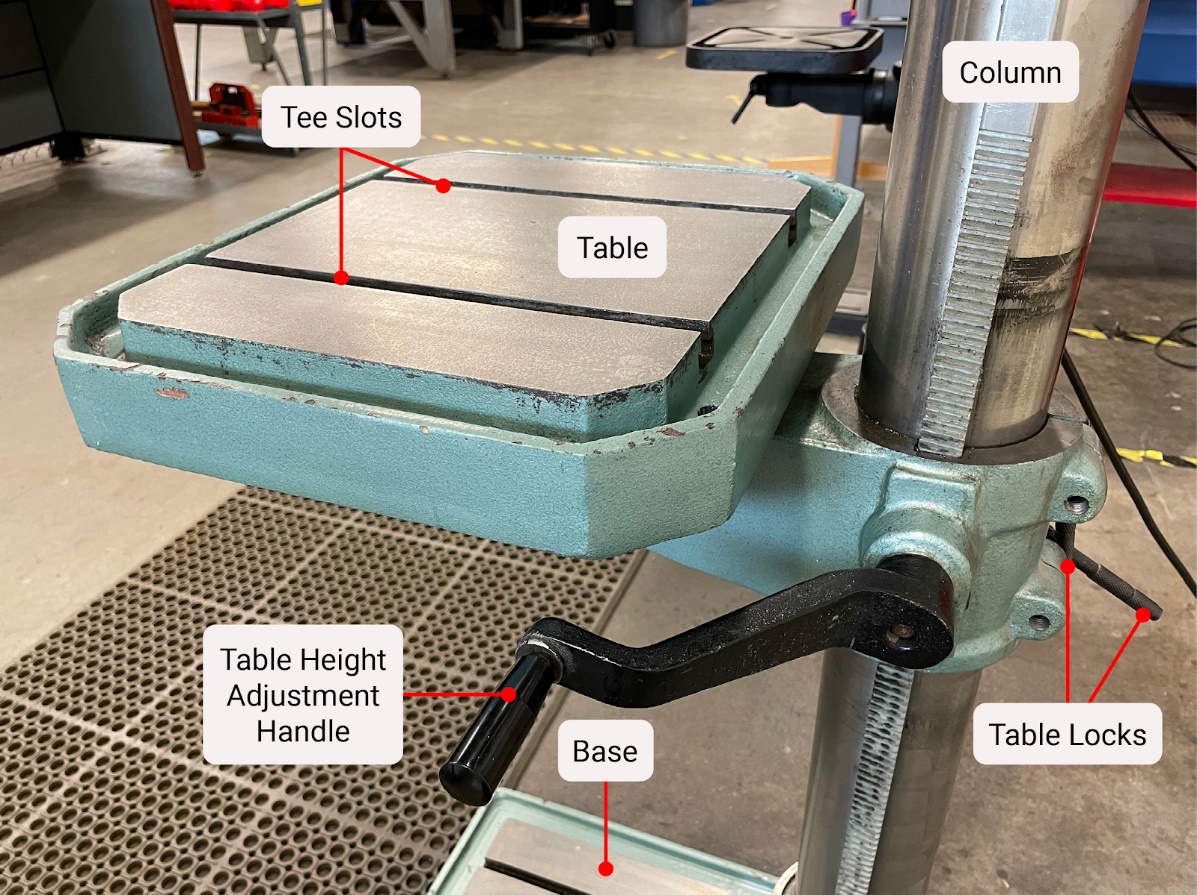
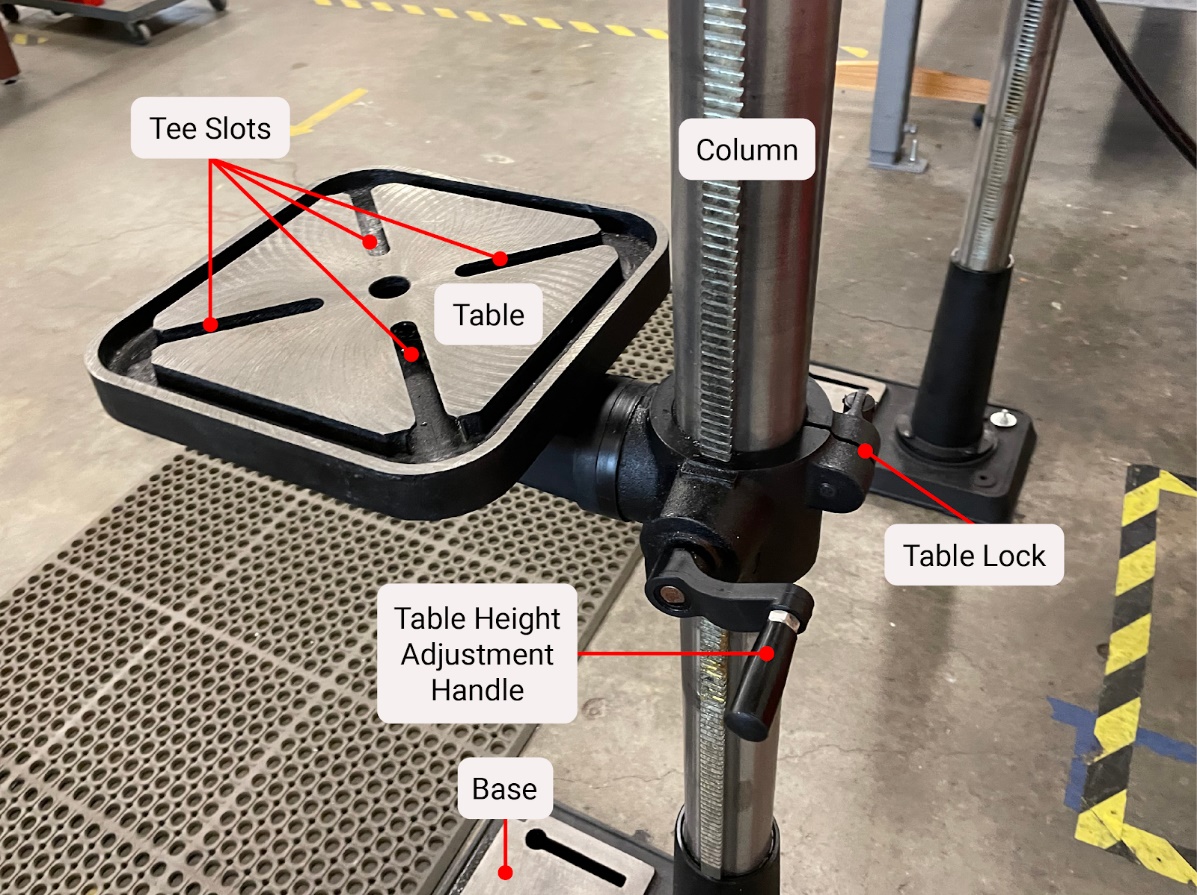
The table of the drill press is designed to support the work. The operator positions the table along the column and locks it in place. It is adjustable up and down, rotates side to side, and may rotate or twist to suit different hole making operations. The up and down movement sometimes employs a mechanism for ease of adjustment.
Head
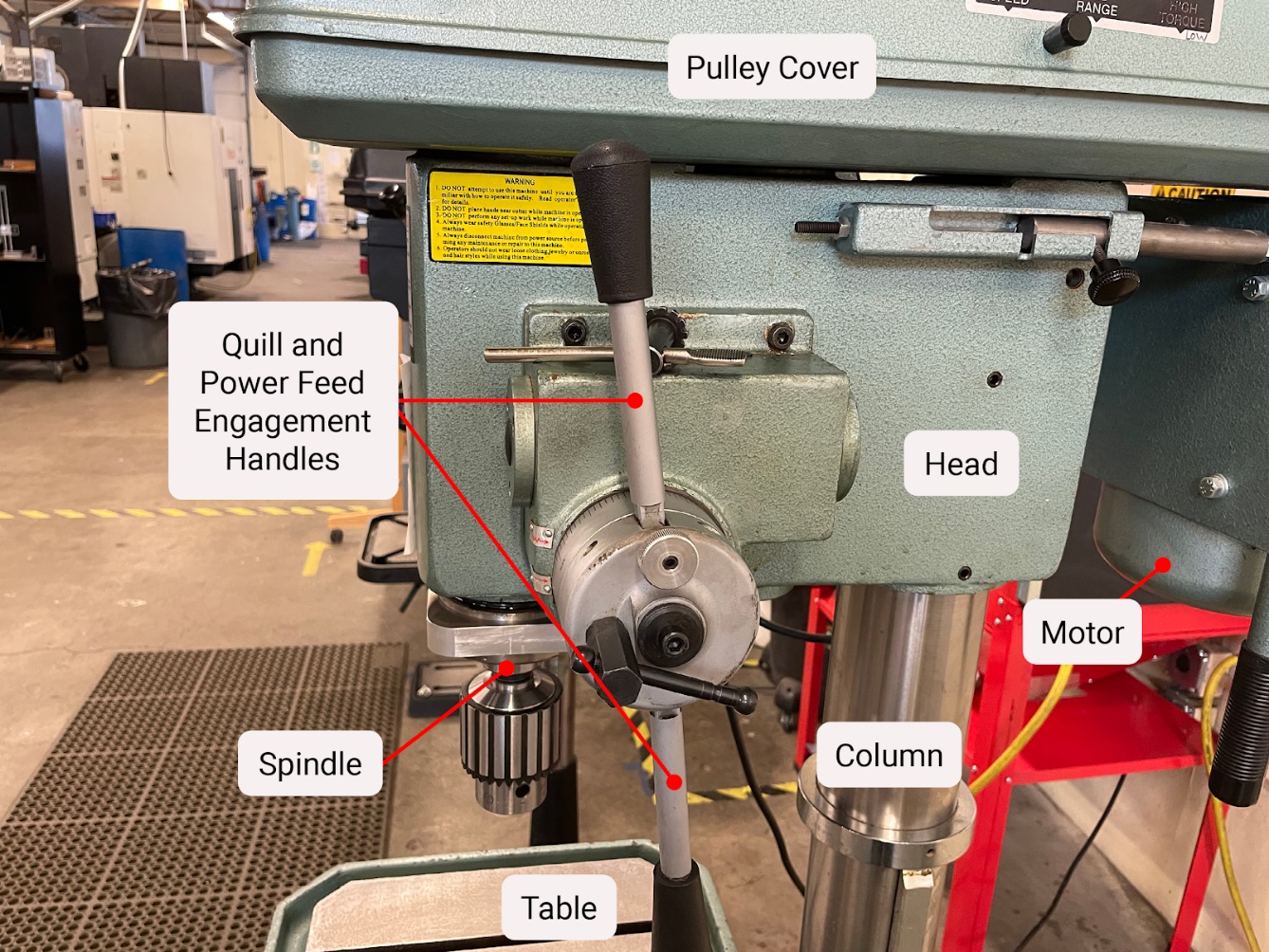

The head is attached at the top of the column and contains the electrical components, on/off switches, gearing, pulleys, quill, and spindle. On the right side of the head is a handle for moving the quill up and down to create movement for the hole-making operations. The motor is mounted at the back of the head.
Motor
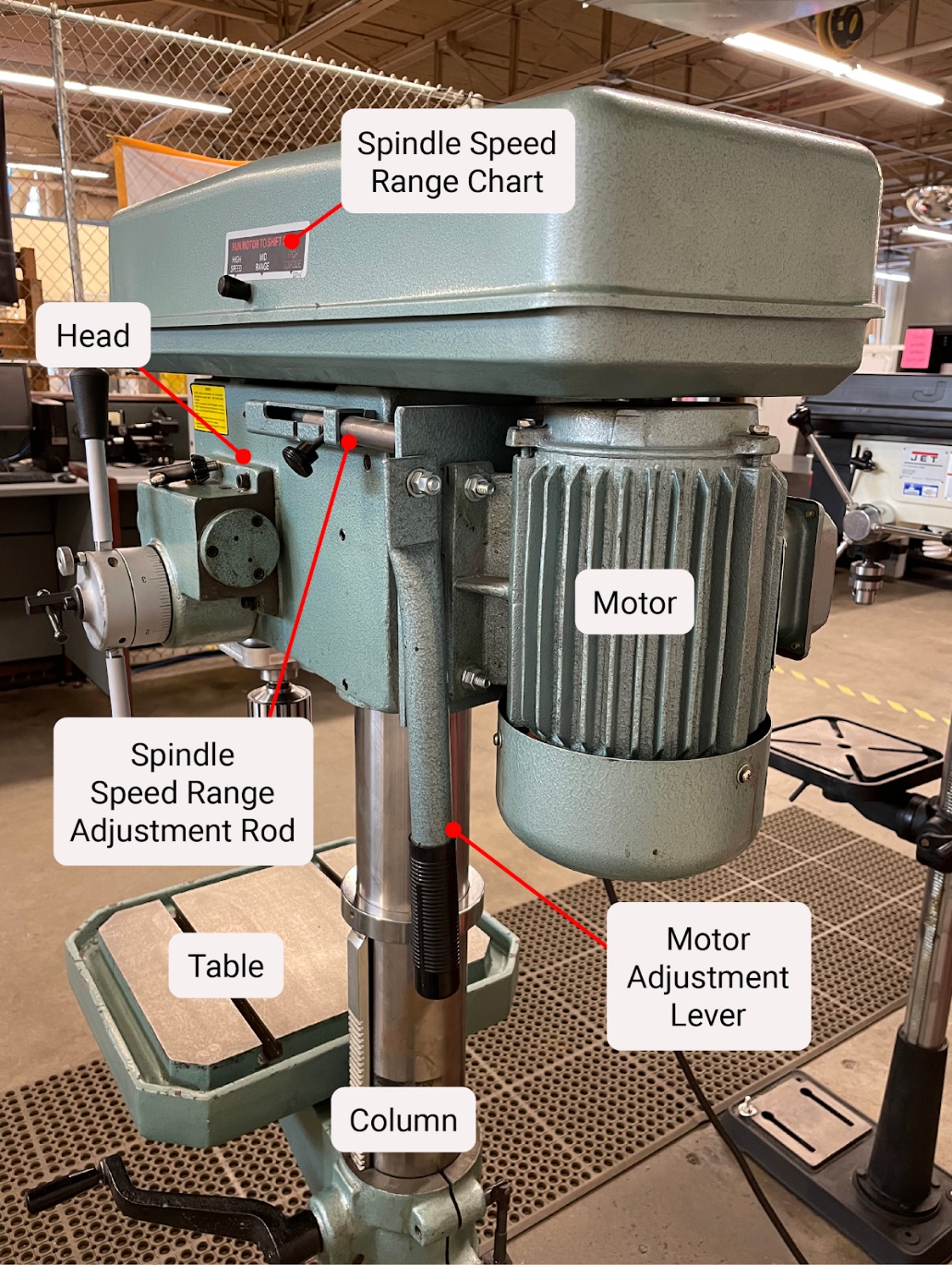
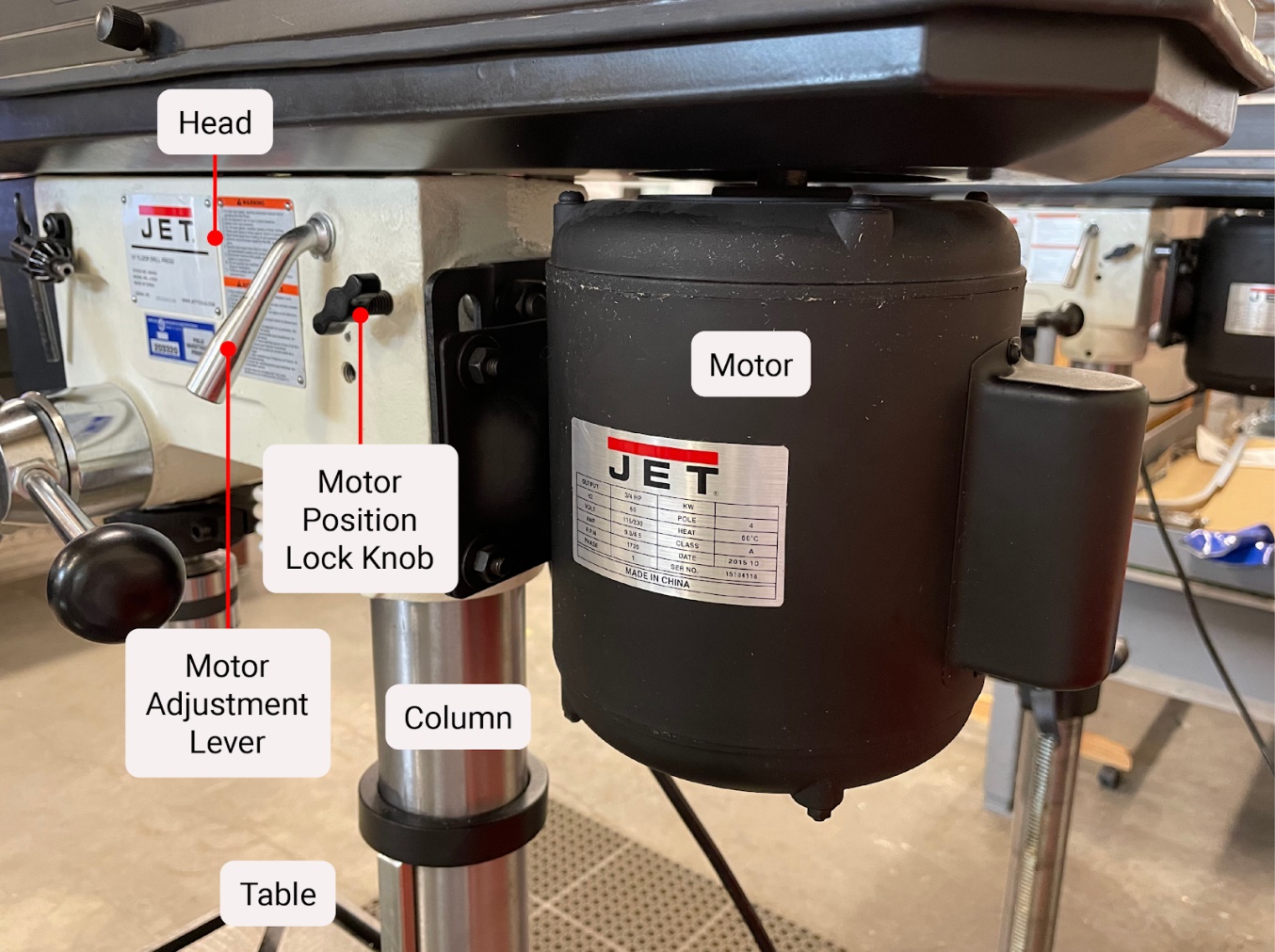
The motor is attached to the drill press head and is the power source for the drill press. Motors come in various horsepower ratings, depending on the size of the drill press and the intended work performed. During operation, the motor turns a series of belts and pulleys to rotate the spindle.
Pulleys
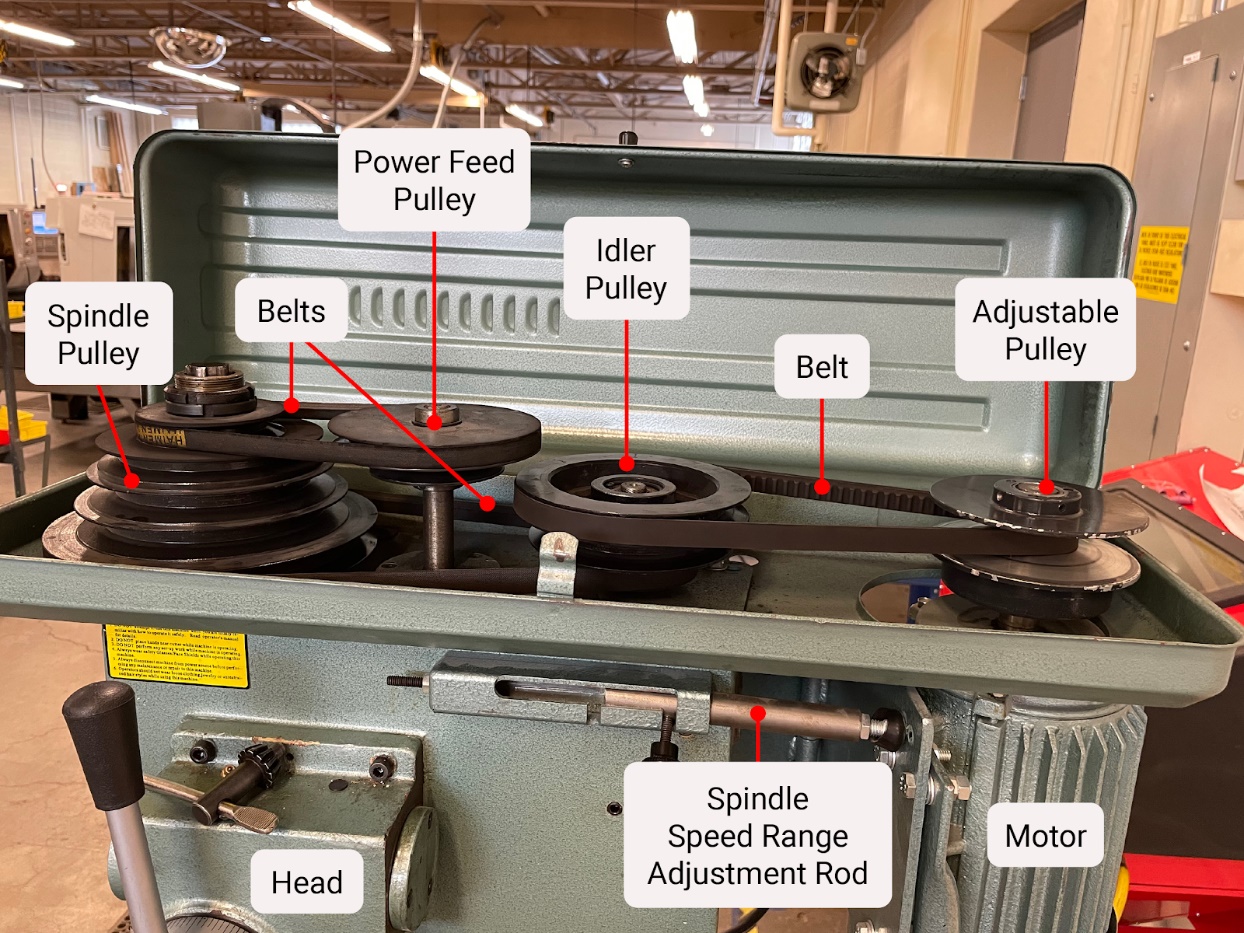
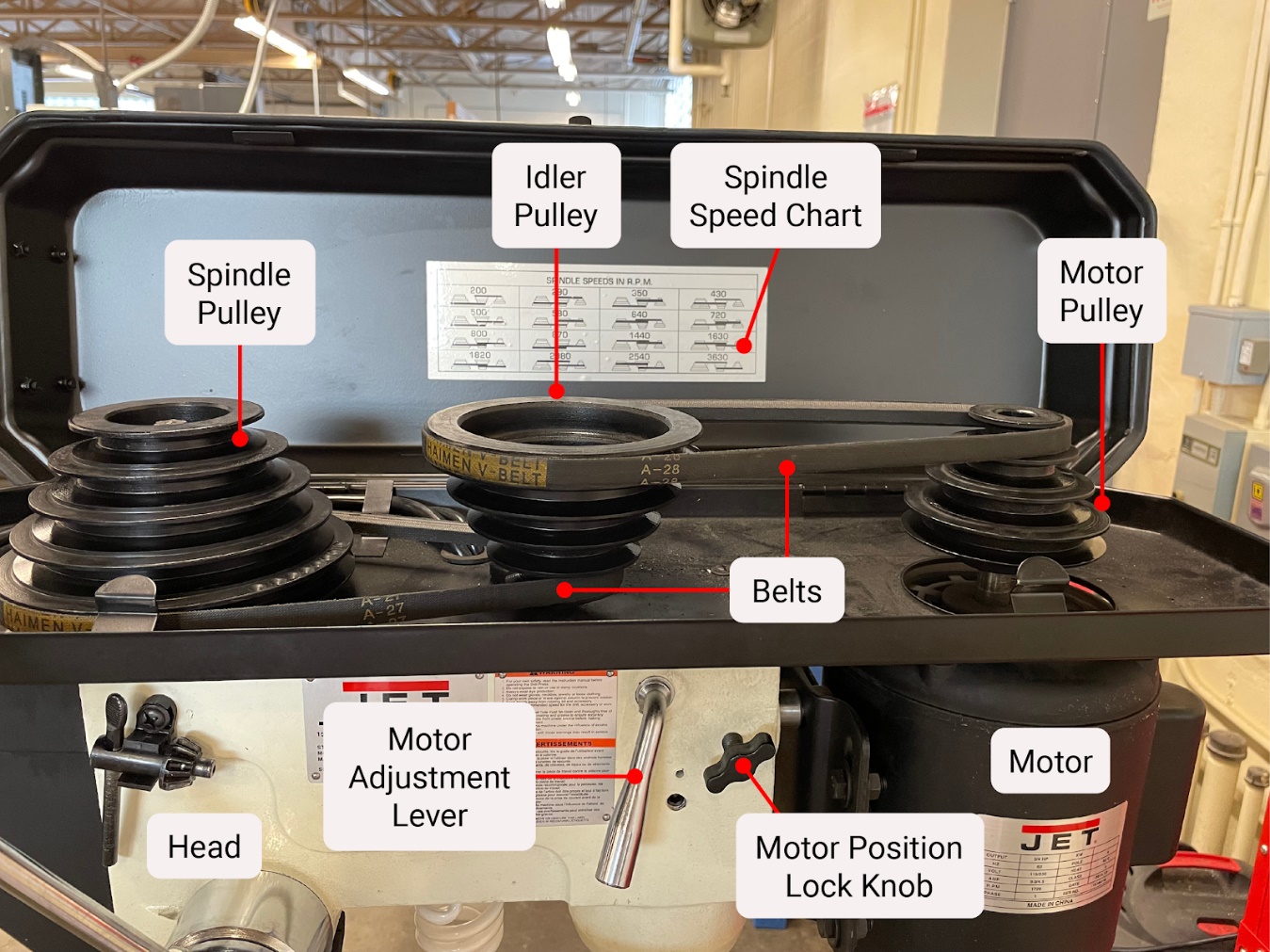
The pulleys of the drill press are utilized to transmit rotational movement from the motor to the spindle by way of vee belts. The belts can often be moved to different pulley steps in order to select spindle speeds. Some drill presses may utilize an adjustable pulley to select spindle speed ranges, while finer adjustments are made with a variable frequency drive.
Spindle
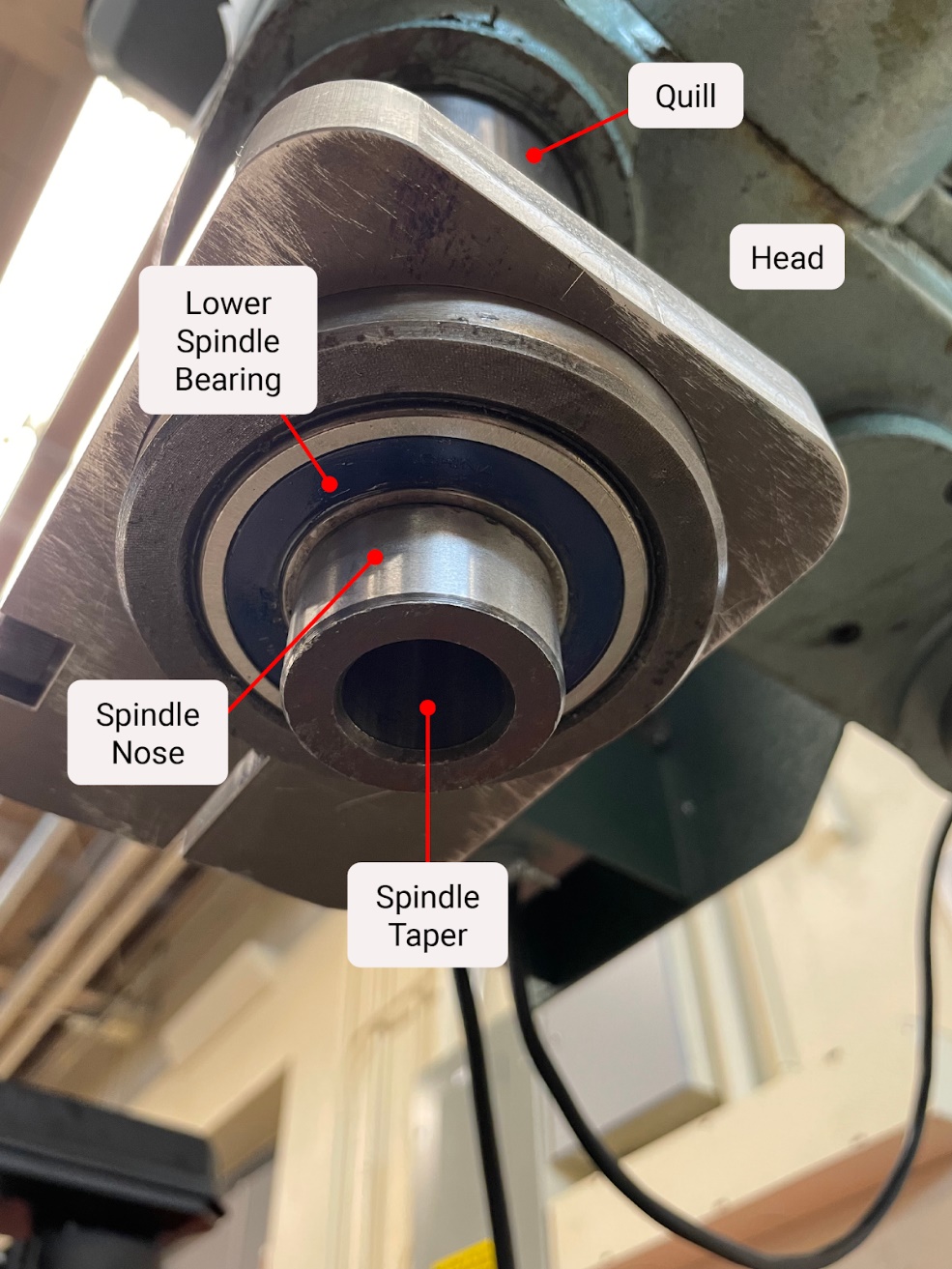
The spindle is located within the drill press head and holds the tooling by way of a Morse taper. The spindle rotates on bearings inside the quill and provides the rotational movement necessary to perform the machining operations. It is connected to the motor by a series of belts and pulleys.
Quill
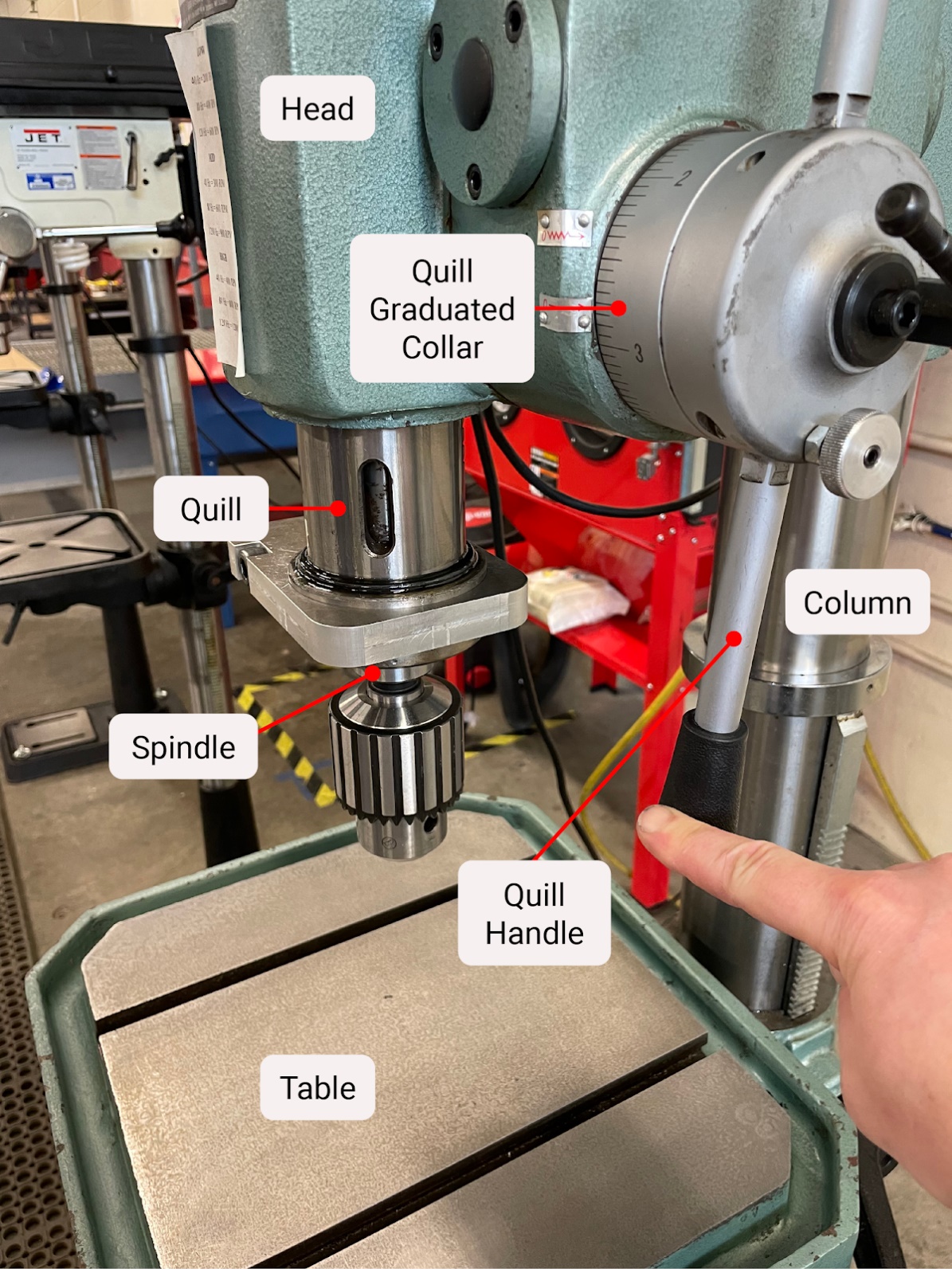
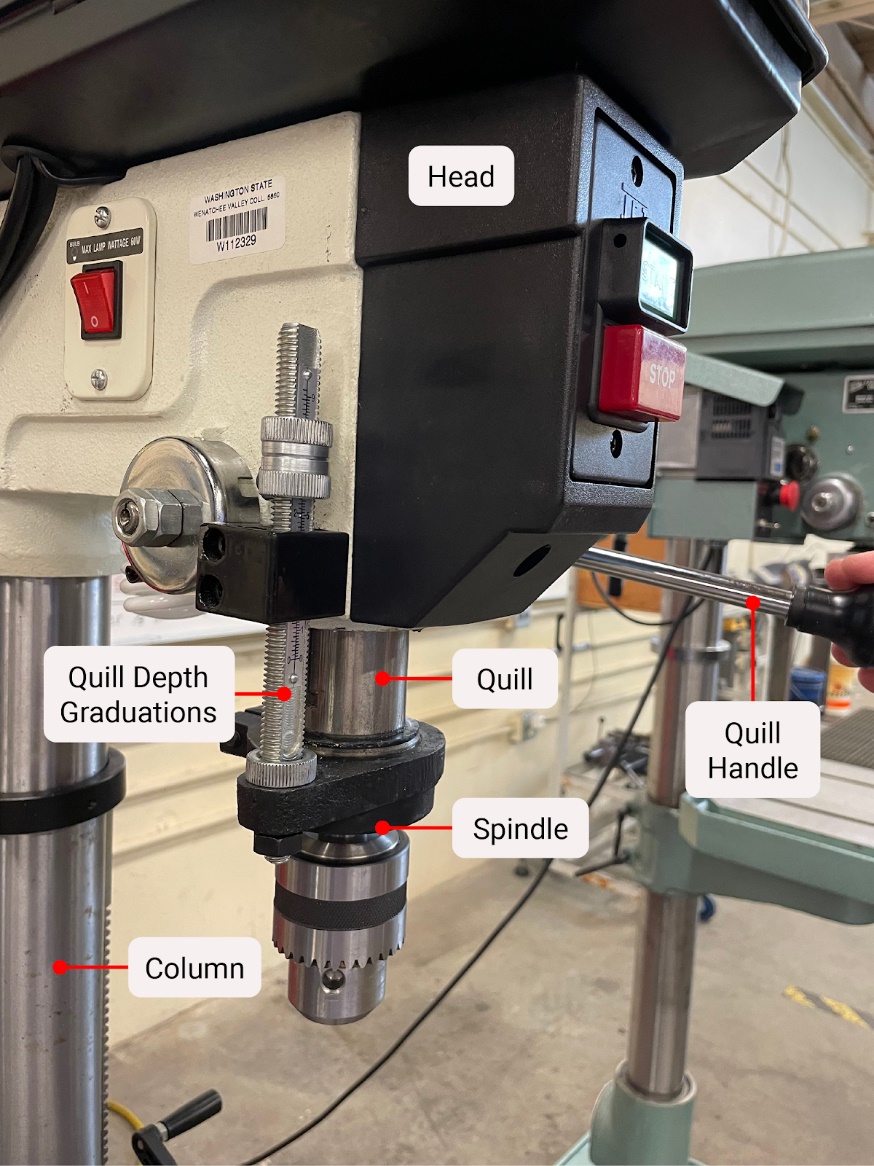
The quill is a cylindrical component that rides up and down in the head when the machine’s quill handle is pulled. The quill handle of the drill press is attached to a spur gear and meshes with a rack machined into the back of the quill. The spindle is located inside the quill and rotates on bearings.
Quill Stop
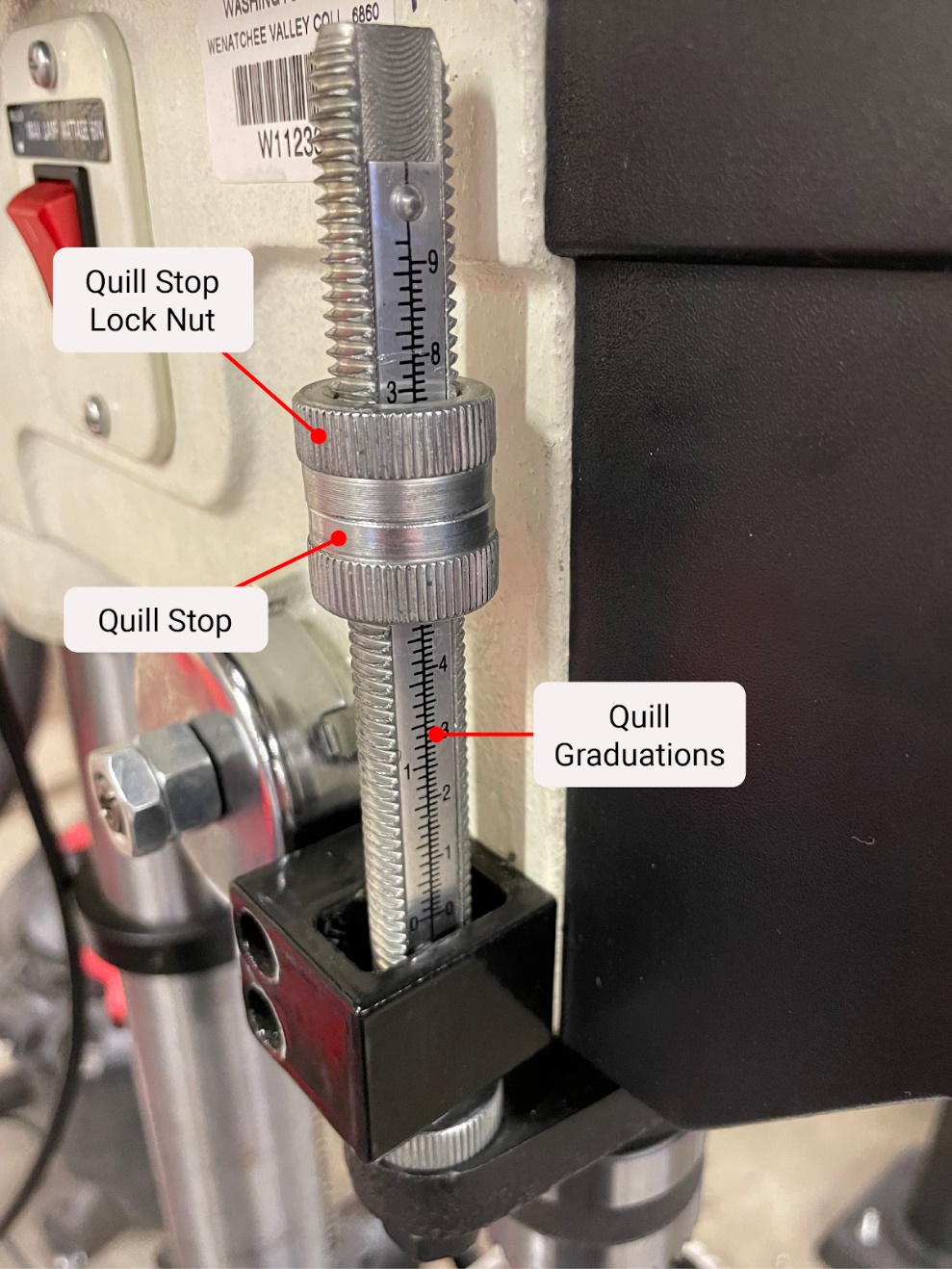
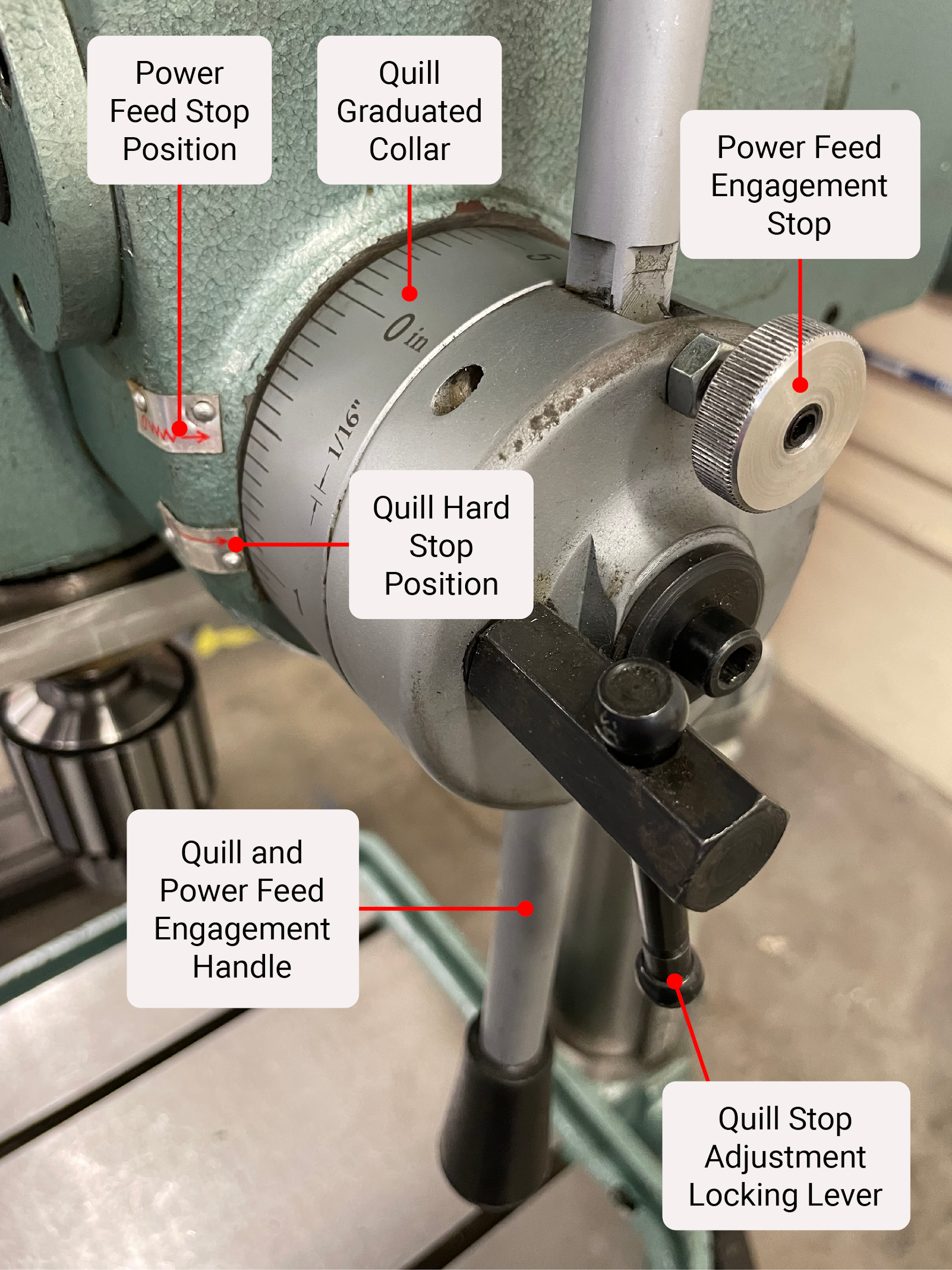
The quill stop is a device that allows the operator to limit the downward movement of the quill. By limiting the quill’s movement, the operator can accurately adjust and set the depth of features. This is especially handy for machining the same feature in multiple locations. Quill stops come in a few different styles. One uses a simple threaded rod with nuts that can be positioned to limit movement. Another type uses a more complex mechanism that is incorporated into the quill handle.
Author’s Tip
I prefer the threaded rod style because of its ease of use and the systematic way it can be adjusted. All I need to know is the pitch of the threaded rod and I can easily adjust the stop nuts in very fine increments by rotating them fractions of a turn. I often find the more complex mechanisms difficult to adjust in small increments, as they often just rely on rotating a graduated collar with respect to a pointing device. The graduated collar is often in course increments like 1/16” and not very useful for precise depth cuts.