Chapter 8 Part 4: Drill Presses
TOOL SETUP
What is it?
Setting up tooling on the drill press can be done in a couple different ways. Generally the tooling used on the drill press will have either a straight shank or a taper shank. Taper shank tooling can be placed directly into the spindle of the drill press, where straight shank tooling will require an additional tool holding device like a drill chuck. Regardless of the shank type, the operator should make sure that all mating surfaces are clean, free of burrs and nicks, and held securely before any cutting operation is performed.
Straight shank
During setup of twist drills, the full shank should be held onto, leaving about ⅛” of material before the flutes begin. At no time should the chuck jaws grip onto the margins of the drill. Doing so would reduce the gripping force and potentially damage the chuck jaws.
Reamers have a long shank that is intended to flex so the tool can follow the drilled hole. Only about an inch of the reamer shank should be gripped by the drill chuck. If the operator grips too far down the shank, it will add unneeded lateral rigidity to the tool, causing it to act more like a boring tool and enlarging the hole. For this reason, reamer shanks should not be shortened.
Tools like countersinks and counterbores often have a straight shank portion that is different from the overall body of the tool. This makes it much easier for the operator to know what area is acceptable for gripping on and what area isn’t.
Morse taper shanks
The spindle of the drill press has a Morse taper to accept tooling or tool holding devices. Many tools and accessories are available with taper shanks for installation directly into the spindle. Taper shanks are especially useful in holding the cutting forces generated by larger tooling that may be prone to spinning in drill chucks. These tapers must be disassembled and assembled properly to avoid damaging the tapers or the equipment.
Removing Morse tapers:
- Gather a hammer and the appropriate drill drift.
- Pull on the quill lever to expose the slot the drift will be inserted into.
- Lock the quill in place.
- Rotate the spindle by hand so that the slot in the spindle lines up with the slot in the quill. The quill is extended on a drill press allowing the operator to see if the slot in the spindle lines up with the slot in the quill.
Photo Credit: Photo Credit: Micky R. Jennings, CC-BY 4.0 - Insert the drill drift into the slot so that the rounded side of the drift is facing up against the slot and the flat end of the drift is against the tang of the tool.
- Tie a string to the end of the drill drift, or raise the table or use a block of wood to catch the ejected tool. This step is necessary to not shoot the drift across the shop or drop and damage the tool. It would be easy if the operator had three hands.
- Firmly hold onto either the drill drift or the tool, whichever is not taken care of by the previous step.
- Firmly tap the end of the drift with a hammer to dislodge the Morse taper. Tapping on the end of a drill drift with a hammer to remove a drill chuck from the spindle of a drill press.
Photo Credit: Micky R. Jennings, CC-BY 4.0
Installing Morse tapers:
- Clean both the drill press’s internal taper and the external taper with a rag.
- Check for damage, rust or corrosion.
- Wipe each with a clean finger to remove any lint
- Check the taper in the spindle to find the correct orientation for the tang.
- Pull the external taper out about 1” from bottoming out on the taper.
- In one quick and deliberate motion, slam the external taper into the spindle to firmly seat it.
Jacobs taper
The drill chuck is attached to an arbor that has a Morse taper on one end and a Jacobs taper on the other. The end of the arbor with the Jacobs taper is mated with the drill chuck. This arbor is generally not removed unless there is an issue with chuck performance. In the event that a chuck gets dropped, the taper may be disturbed and the arbor could become slightly crooked inside the drill chuck. This would cause tools installed in the chuck to have an unacceptable amount of runout. In this instance, the arbor should be removed, checked for straightness, and reinstalled in the drill chuck.
- Remove the drill chuck and its arbor from the drill press.
- Place the drill chuck into a vise that is set up to support the chuck and let the arbor hang free.
- Do not tighten the vise on the arbor. The jaws need to be very close to the arbor, but not holding it from coming out.
- Open the jaws of the chuck all the way so the end of the arbor can be seen.
- Get a punch appropriately sized to insert into the chuck and cover a large portion of the end of the arbor.
- Close the jaws so that they come close to gripping on the punch but do not tighten. This will align the punch with the end of the arbor.
- Firmly hold the end of the arbor so it doesn’t fall.
- Firmly hit the punch with the hammer to dislodge the Jacobs taper.
“Step 2: Place the drill chuck into a vise that is set up to support the chuck and let the arbor hang free.“
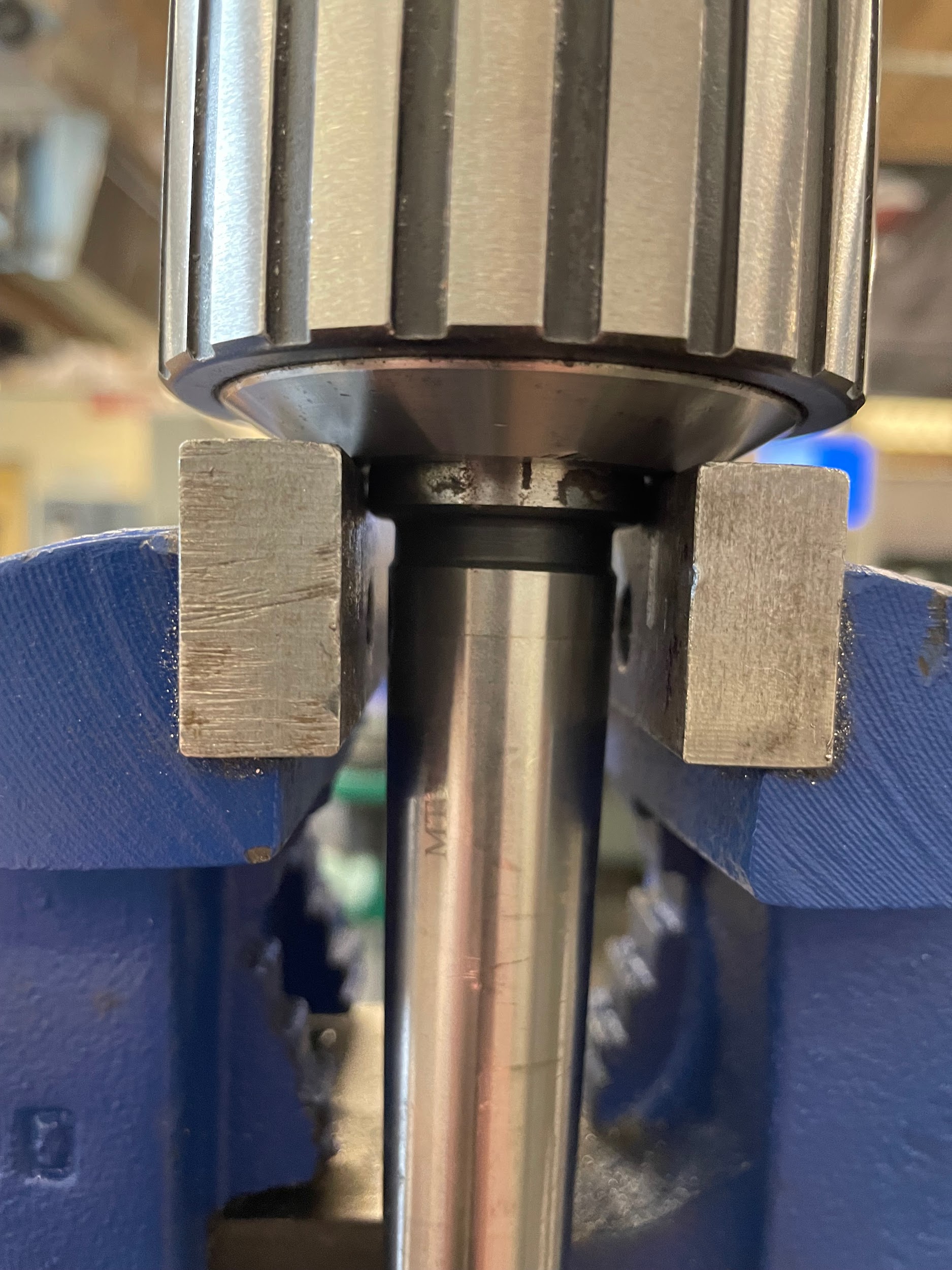
“Step 4: Open the jaws of the chuck all the way so the end of the arbor can be seen. “
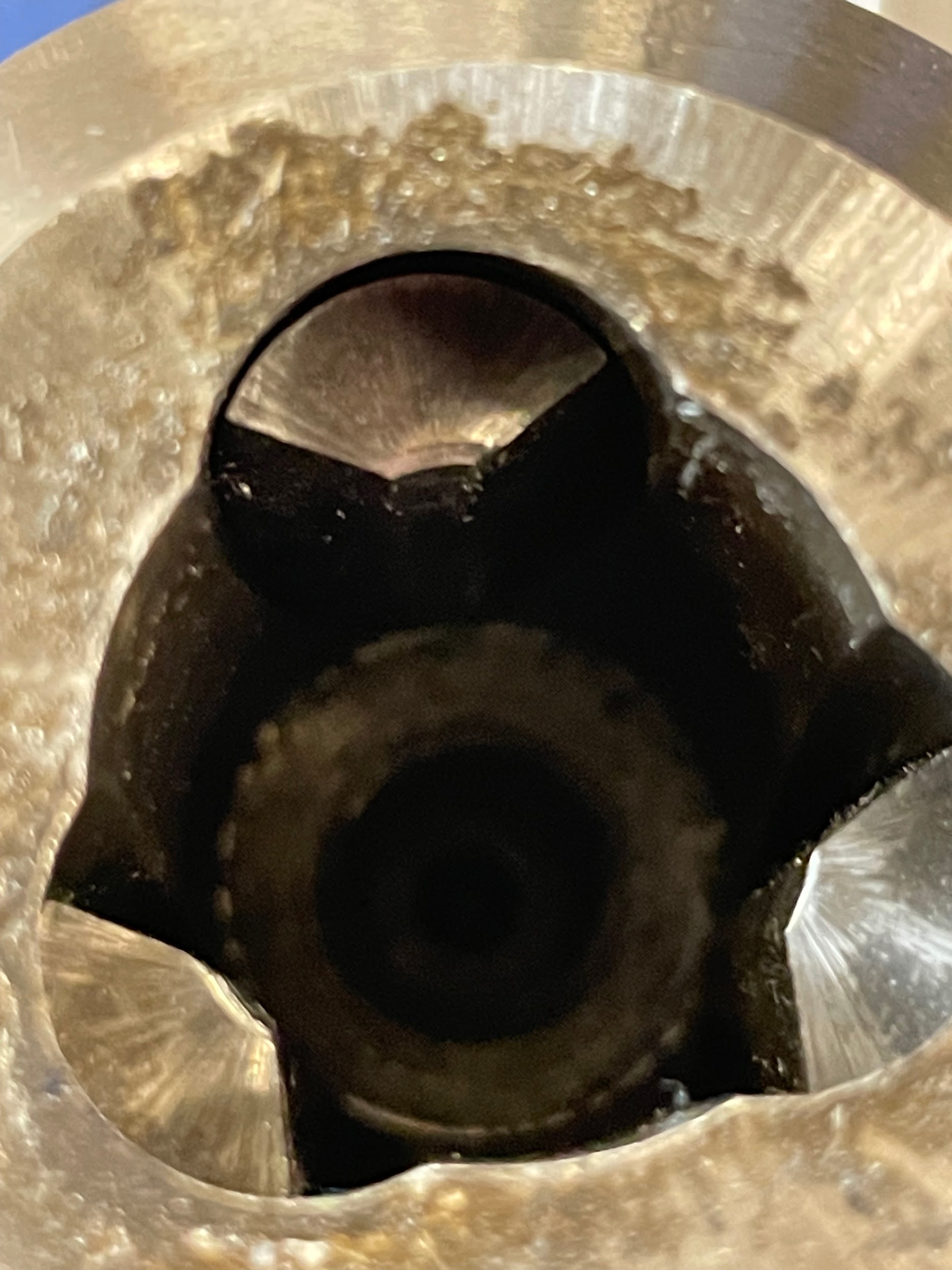
“Step 8: Firmly hit the punch with the hammer to dislodge the Jacobs taper.“
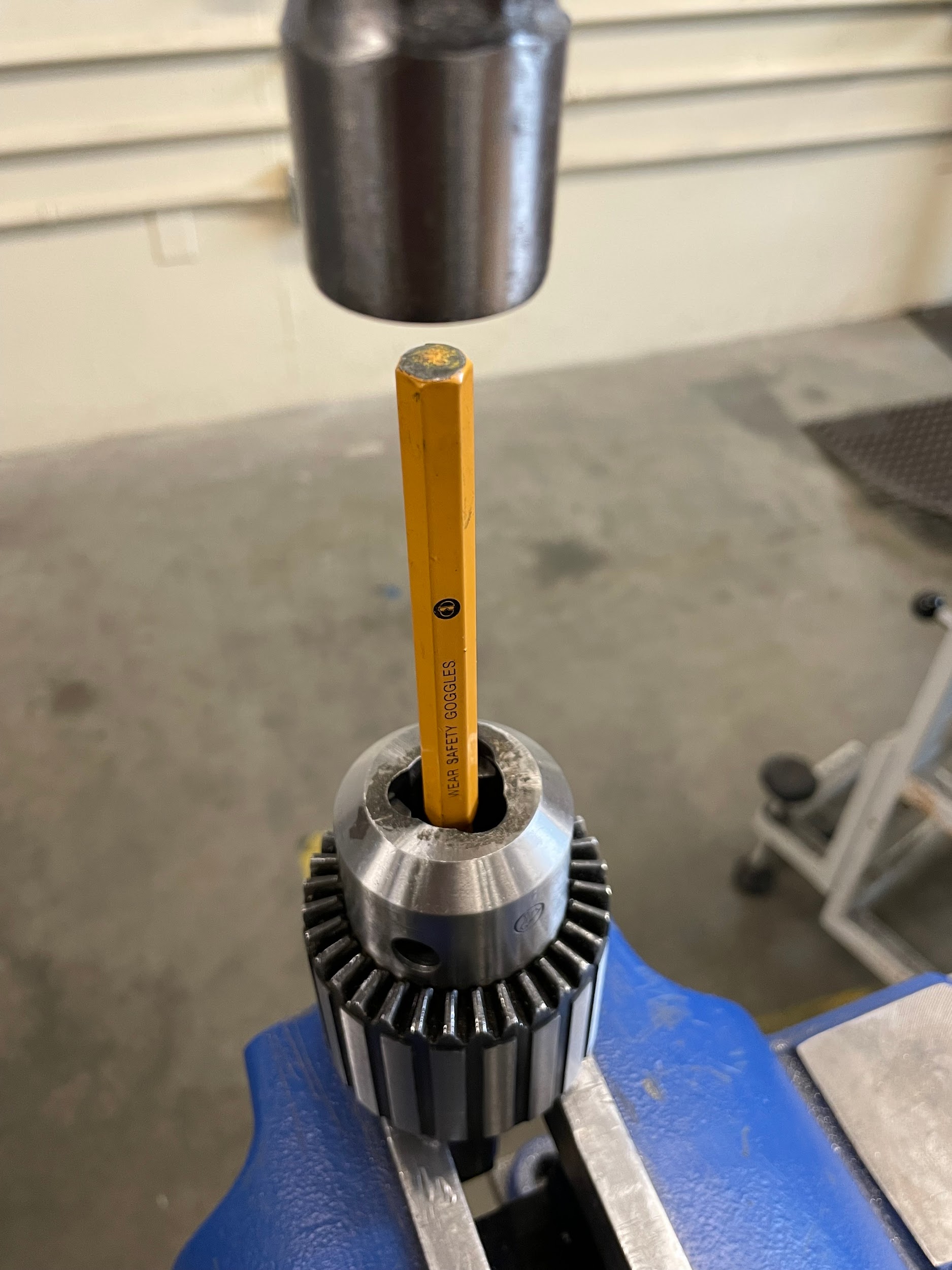
Clean both the drill chuck’s internal taper and the arbor’s external taper with a rag.
Check for damage, rust or corrosion.
Wipe each with a clean finger to remove any lint
Position the arbor inside the chuck leaving about ⅛” from bottoming out on the taper, holding the pair in one hand.
In one quick and deliberate motion, strike the tang of the arbor into a hard surface to firmly seat the taper.
“Step 2: Check for damage, rust or corrosion.”
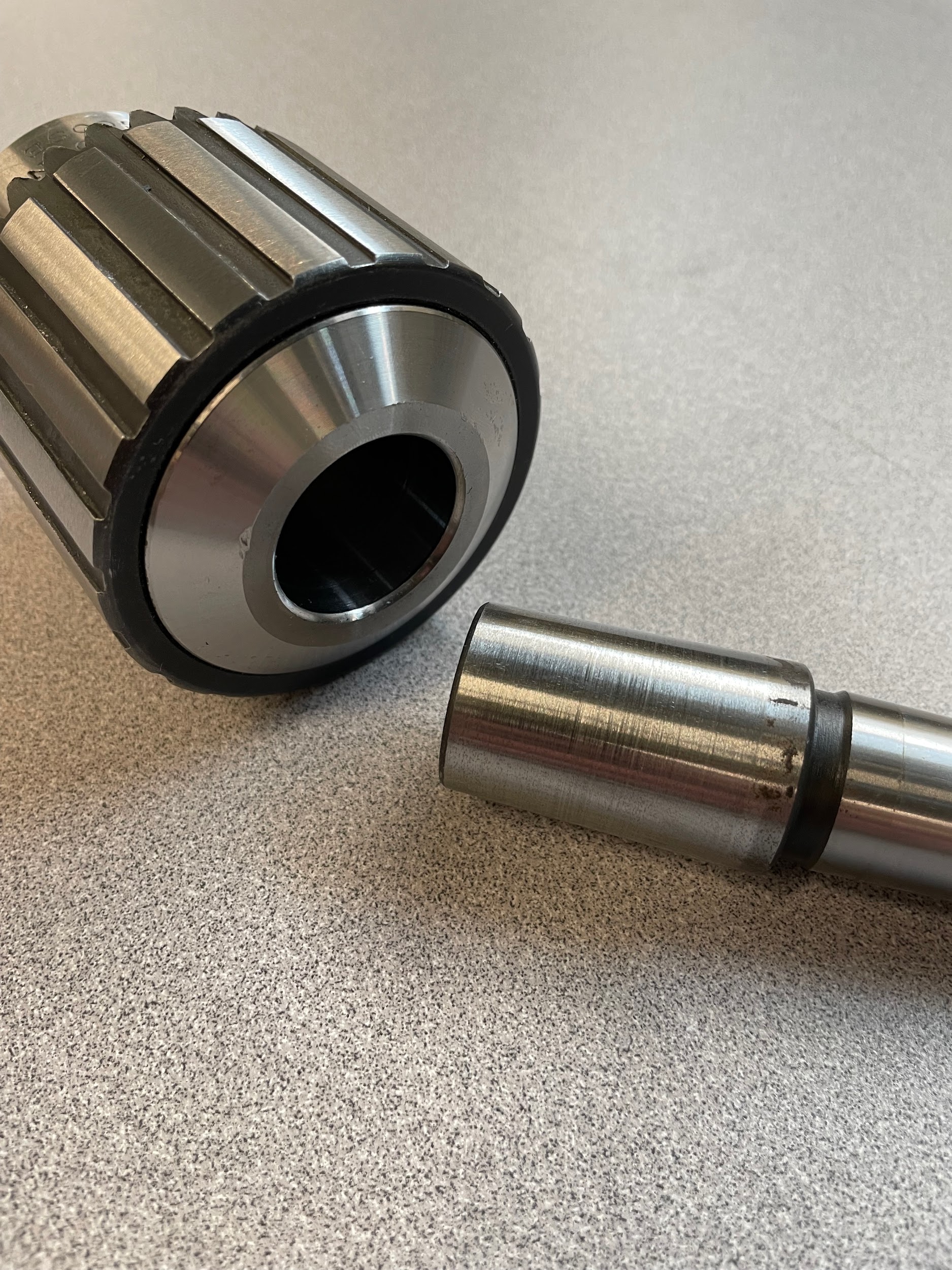