Chapter 8 Part 5: Drill Presses
SPEED AND FEED
Speeds and feeds on a drill press refer to the correct rate at which each tool is rotated and advanced into the workpiece. This rate is important for efficient cutting and tool life. A machinist should know how to calculate the speed and feed for various tools and conditions. Being able to calculate efficient speeds and feeds is a skill that takes years to fully acquire, but knowing the basics of the process will give students the foundational knowledge to start cutting material without damaging tooling.
Spindle speed
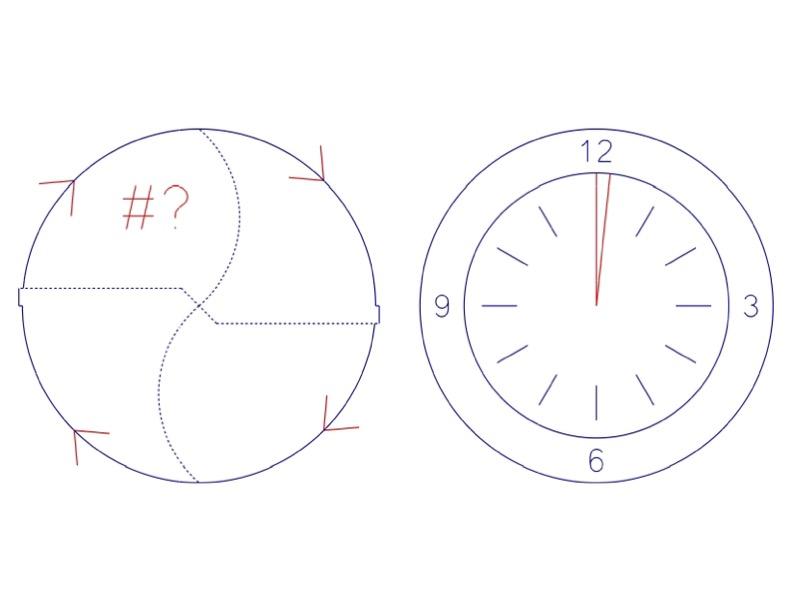
Spindle speed , in rotations per minute (RPM), is critical to efficient metal cutting operations and tool life. Documented knowledge of the speed of which a cutting tool, of a specific composition, can cut across a specified material, exists. This speed is referred to as surface feet per minute, or SFPM. SFPM is a linear speed and differs from rotational speed. Rotational speed is based on the amount of rotations per minute a given object is spinning. If the SFPM is known for a cutter machining a specific material, the RPM can be calculated using a formula. The basis of the formula is wrapping the SFPM around the cutting tool and counting the number of times it is covered. Taking a linear speed and turning it in a rotational direction. The outer circumference where the cutting tool is touching the work is key. The standard formula to calculate RPM from SFPM is:
RPM = (SFPM x 12) / (Diameter x Pi)
In the formula, multiplying SFPM by 12 takes it from feet per minute and converts it to inches per minute. The reason for doing this is to have common units in the equation, and the tool diameter will be input in inches. The diameter multiplied by Pi is how the circumference of a round object is calculated. Knowing these pieces, it makes a little more sense when looking at the formula.
RPM = Surface inches per minute / Circumference.
RPM = The number of times a linear distance wraps around the tool.
Drilling example:
When using a 1/2 high speed steel (HSS) twist drill cutting mild steel. The SFPM for this tool and material would be about 90.
RPM = (90 x 12) / (.500 x Pi)
RPM = 1080 / 1.571
RPM = 687
Some like to simplify the formula by removing Pi from the equation, doing so makes it easier to calculate on a basic calculator. A modified formula would look like this:
RPM = (SFPM x 3.82) / Diameter
RPM = 343 / .500
RPM = 686
3.82 is calculated by taking 12 from the numerator of the original formula, and dividing it by Pi of the denominator.
Author’s Tip
Keep in mind that these numbers are in a range of RPM this tool could run at and under optimal conditions. An experienced machinist will be able to use these numbers as a starting position and then adjust the speed based on factors like work holding, tool holding, cutting oil, chip temperature, etc. That said, the number calculated is a ballpark starting point. For that reason, I prefer to simplify this formula to the point that it is a little easier to remember, and adjust the numbers to a point I can calculate in my head. For example, the SFPM for cutting mild steel with HSS is approximately 90. I like to round that to 100. Likewise, I like to round the 3.82 up to 4. These adjustments make the calculation a little easier, as well as staying in the ballpark of acceptable cutting speed. The further refined formula would look like this:
RPM = (100 x 4) / .500
RPM = 400 / .500
RPM = 800
This number is approximately 110 RPMs faster than the RPM calculated by the original formula. This may scare many beginning machinists, however, remember I use this number as a starting point. When we look at our machine, we often don’t get to choose the exact RPM we have calculated, there will inevitably be two speed selections the calculated RPM will fall within. In these instances, I choose the slower of the two speeds.
Feed rate
Simple drill presses will often not have any automatic feed mechanism, relying on user feel to gauge the correct feed rate . For this reason it is important for an operator to gain hands-on experience with the proper feed. Correct feed during a drilling operation will result in curling and breaking chips flowing out of the flutes of the bit as it is pressed into the work. Too little feed will not allow the tool to bite into the material and the cutting edges will chatter around at the point of contact. The remedy for this is to pull harder on the drill press handle. Too much feed may result in tool slipping, stalling the spindle, or tool breaking. The remedy for these conditions is to pull on the handle more gently.
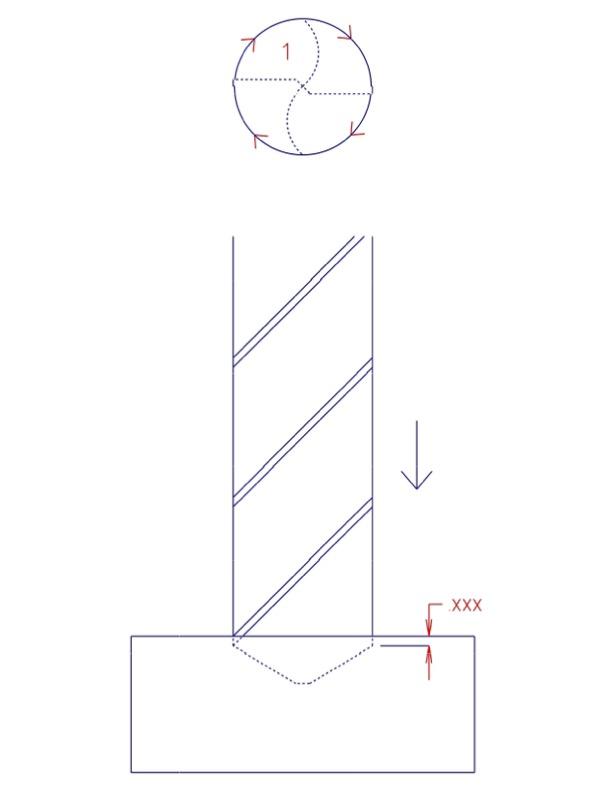
If using a drill press that has an automatic feed mechanism, the feed rate is often expressed in inches per revolution (IPR). A chart can be used to look up this information based on the size of the drill.
Author’s Tip
One trick I use is to remember that the force a drill can withstand is related to the drill size. For example, a 7/8 twist drill can handle more force than an 1/8 inch twist drill. I use .002 in feed for every 1/8 of an inch of twist drill diameter, as an easy to remember number to get me in the ballpark.
Speed and feed adjustments for different tooling
A common practice in drilling operations is to calculate the speed for an equally sized drill, and then apply feed or speed reductions based on that specific tool. A couple occurrences are with reaming, countersinking, and counterboring.
Reaming
For reaming it is recommended to use half the speed, and twice the feed of an equally sized twist drill.
Reaming example:
When reaming a 5/16 hole with a HSS reamer in steel, use the same formula as for a 5/16 HSS drill and then alter the result for reaming.
RPM = (SFPM x 3.82) / Diameter
RPM = (90 X 3.82) / .312
RPM = 344 / .312
RPM = 1102, for a twist drill.
Now apply the recommendation for reaming of one half the speed.
RPM = 1102 / 2
RPM = 551
When it comes to applying the feed portion of the formula the recommended feed for a twist drill is simply doubled. For example, if the feed for drilling a 5/16 hole was .005 IPR, then the feed for reaming would be .010 IPR. The reason for the increased feed is to reduce the chance of chatter in the hole. A reamer has more tool engagement than a twist drill and must be pushed faster to put sufficient pressure on the tool to keep it from chattering. Another reason to feed a reamer faster is the fact that the operator generally wants to get in and get out of the hole as quickly as possible. The longer the tool dwells inside a hole, the more rubbing occurs that could potentially alter the size of the finished hole.
Author’s Tip
A couple tricks I use to get an accurate ream are:
Dial in your reamer. Although reamers have a long flexible shank to aid in alignment with the hole, they can also end up with a decent amount of runout at the tip of the tool, especially if you aren’t using a high precision drill chuck. To do this, you simply mount an indicator on the table of the machine with the tip movement perpendicular to the rotation of the tool. Adjust the indicator to touch the end of the reamer just above the cutting edge. Rotate the reamer by hand backwards and observe the runout between all the cutting edges. At this point I may try different tools if another is available, or simply loosen the drill chuck, rotate the tool a little bit, retighten and check again. I am usually happy if I can get within .003 runout. Sometimes gentle pulling or tapping of the reamer in one direction or the other can get it a little closer for those tighter tolerance ream callouts.
Turn off the spindle before you pull the tool out of the hole. If the reamer has any runout in it, it will generally straighten itself as you apply the 2x feed into the drilled hole. The tapered cutting edges of the reamer will have equal pressure on them while cutting and the tool will center itself with the hole. However, once you reach the bottom of the reamed section and you start to pull out, there is no longer pressure on the tapers of the reamer keeping it aligned with the hole, so it will want to start running out again. As it puts slight side pressure on the hole in one direction, the cutting edge on that side will slightly score a helix on the inside of the nicely rearmed hole. For that reason I stop the spindle as soon as I reach the bottom of the hole and pull the tool straight out.
Countersinking and Counterboring
For countersinking and counterboring, around a quarter the speed of an equally sized drill should be used. The reason for this is that, generally, they have multiple flutes and a larger surface area in contact with the work. A slower spindle speed will allow the operator to make sure the feed is adequate to keep chatter at bay. One thing to consider when making the calculation for countersinks and counterbores is the largest diameter of the tool that will be in contact with the work. For countersinks, this can be difficult because the print sometimes doesn’t say. It may just call out a countersink for a ½” flathead bolt. The same could be said for counterbores, the print may just call out a counterbore for a 1⁄2” socket head cap screw. Measuring the tools isn’t much help because the countersink will have a fractional outer diameter that is irrelevant, and many counterbores have three cutting edges and can’t be measured for diameter accurately. The fasteners could be measured, but unless the operator is doing the assembly, they might not be available. The answer to this is by looking in Machinery’s Handbook (or another manufacturing reference book) to find the correct diameters. For the countersink, the theoretical point of the fastener is a good indication of the largest diameter to be cut. For the counterbore, the actual diameter of the counterbore is given. From these diameters, an accurate spindle speed can be calculated.
Countersinking example:
When creating a ⅞” diameter countersink with a 1” HSS countersinking tool, in steel, use the same formula as for a ⅞” HSS drill and then alter the result for countersinking. The reason for using ⅞” instead of 1” is because that is the largest size where the tool will be touching the material.
RPM = (SFPM x 3.82) / Diameter
RPM = (90 X 3.82) / .875
RPM = 344 / .875
RPM = 393, for a twist drill.
Now apply the recommendation for counterboring of one quarter the speed.
RPM = 393 / 4
]RPM = 98
Counterboring example:
When using a ⅜” HSS counterboring tool, in steel, use the same formula as for a ⅜” HSS drill and then alter the result for counterboring.
RPM = (SFPM x 3.82) / Diameter
RPM = (90 X 3.82) / .375
RPM = 344 / .375
RPM = 917, for a twist drill.
Now apply the recommendation for counterboring of one quarter the speed.
RPM = 917 / 4
RPM = 229