Chapter 9 Part 6: Manual Vertical Milling Machines
SIDE MILLING
What is it?
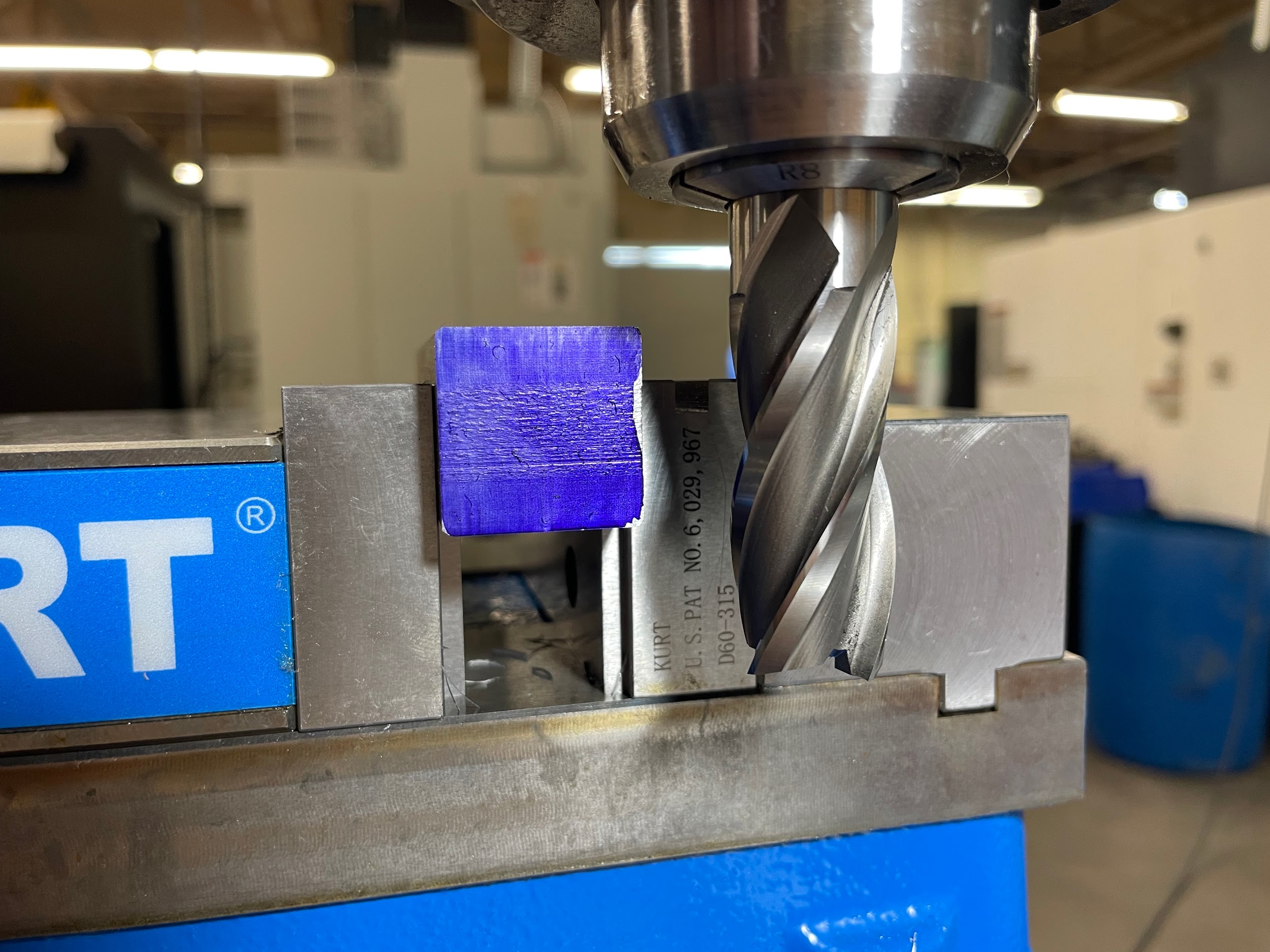
Side milling is the process of using an end mill to create features on a part. Side milling is generally performed in a sideways motion, utilizing the periphery of the tool to make the cut. Plunging motions can be performed with an end mill if the tool is center cutting, but this movement isn’t as efficient and should be done lightly to keep from loading the flutes at the end of the tool.
Step by step process for side milling:
- Load an end mill into the milling machine using a solid holder or a spring collet. When putting a tool into a collet, make sure to choke up on as much of the shank as possible without the collet going over the flutes. Clamping the tool within 1/8” of the flutes will help with tool rigidity.
- Lock the quill.
- Load stock into the vise on parallels. Select parallels to clamp on as much material as the cut will allow. Doing so increases rigidity in the part.
- Apply layout dye to the side of the part to be machined. This will allow the operator to see the tool touching off on the work better.
- Raise knee and position the work using the saddle and table to just above part.
- Calculate RPM for the end mill, turn on the spindle, and adjust to the correct speed.
- Gently raise the knee until the edges of the end mill touch the top of the work.
- Zero the graduated collar on the knee handle.
- Move the tool fully off the edge of the part.
- Move the knee up to the desired depth.
- Move the table until the tool touches the side of the part.
- Zero the graduated collar of the table handwheel.
- Move the work off to one side in preparation for making a conventional milling cut.
- Move the table in by the desired depth of cut.
- Lock table movement in that direction.
- Apply a small amount of cutting oil to the surface that will be milled.
- Feed the part across the cutter to complete the cut.
- Inspect the cut for full clean up
- Adjust the table another .005”
- Climb mill back across the part.
- Turn off the spindle.
- Inspect cut repeat if necessary.
- Flip the part end for end and repeat.
- Touch off, alternatively, with paper on this side.
- Make conventional roughing cuts to within .005” to .010
- Make one finish climb cut to size.
“Step 4: Apply layout dye to the side of the part to be machined. This will allow the operator to see the tool touching off on the work better.“
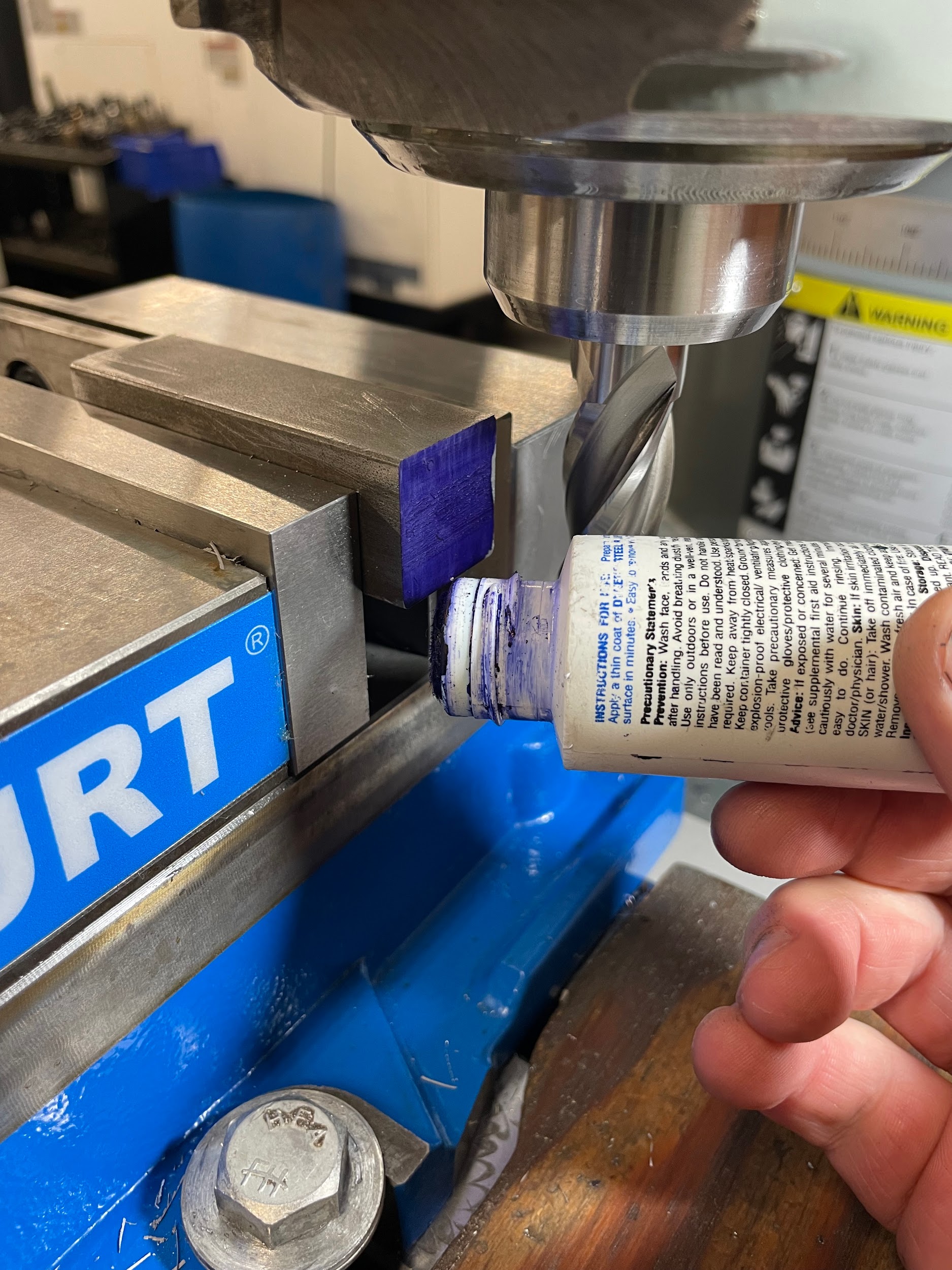
“Step 4: Apply layout dye to the side of the part to be machined. This will allow the operator to see the tool touching off on the work better.“
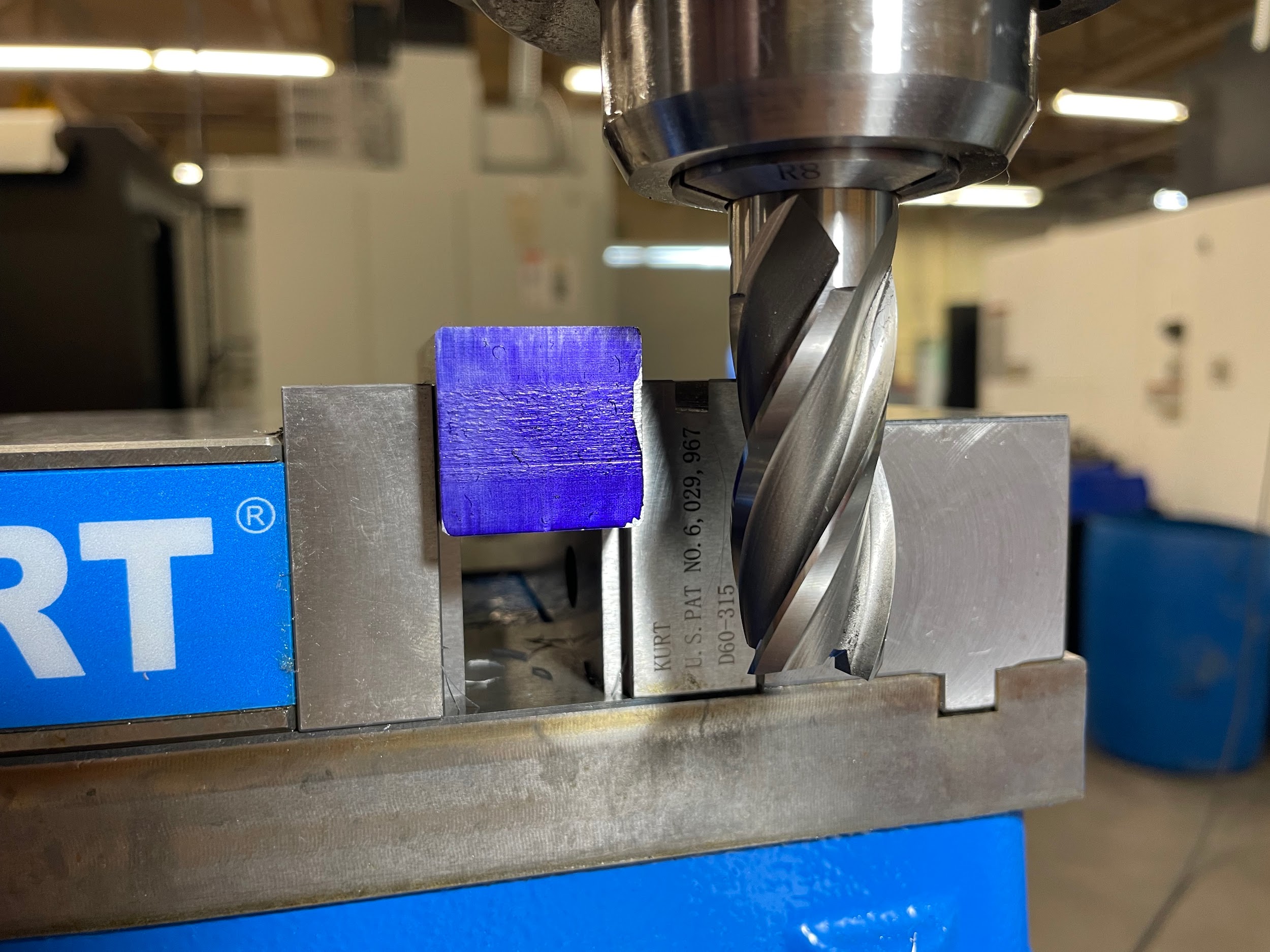
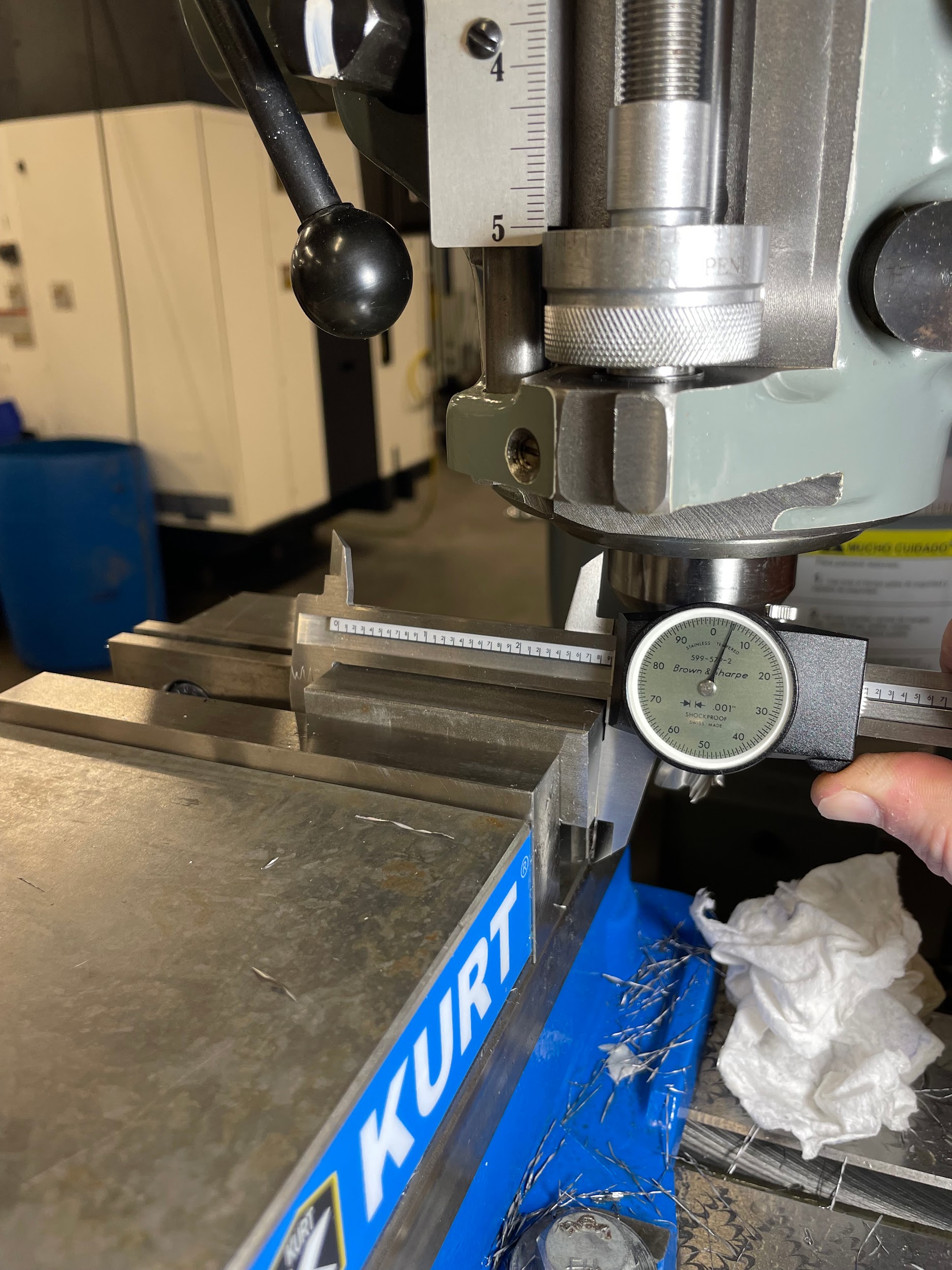
SLOTTING
What is it?
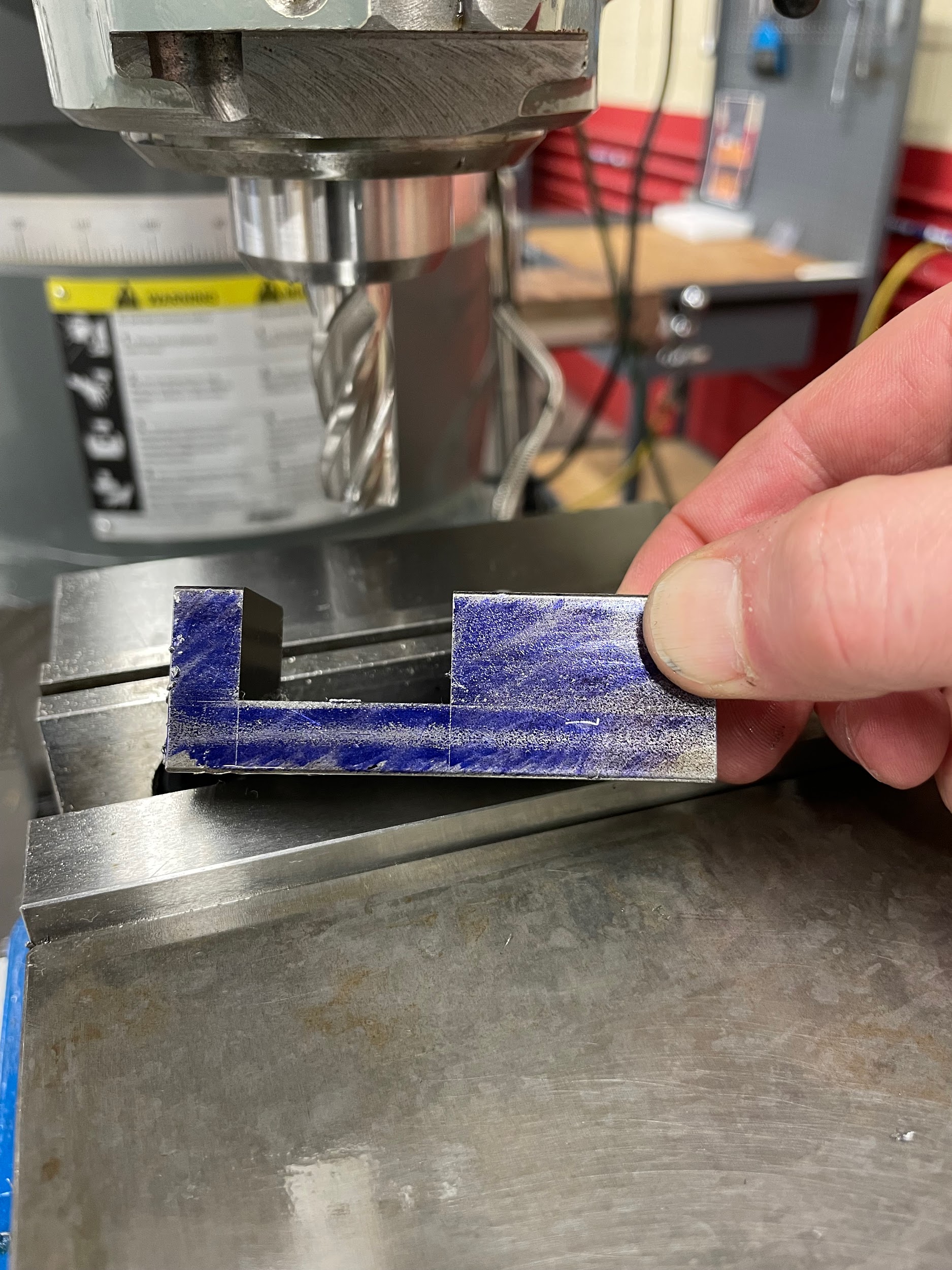
Slotting is the process of using an end mill to create a slot or groove in a part. A precision slot is generally performed in multiple passes, allowing the operator to adjust the machine for position and size. Attempting a slot in a single pass may result in an oversized and out-of-position slot that has a poor surface finish.
Step by step process slotting:
- Load material into a vise.
- Apply layout dye to the top of the part.
- Using odd legged calipers, scribe lines on the top of the part to indicate the position of the slot.
- Load an end mill for roughing, one size smaller than the slot, into the milling machine.
- Calculate the spindle speed and feed rate for the cut.
- Turn the spindle on and adjust the machine to the calculated speed.
- Position the machine so that the tool is visually in the center of the slot.
- Zero and lock the table handwheel.
- Touch the tool off to the top of the work.
- Set the graduated collar of the knee to zero.
- Move the saddle so the tool is off the work.
- Move the knee up the desired depth of cut, minus .015”.
- Lube the tool and the work.
- Make the initial cut through the length of the slot at the calculated feed rate.
- Take a measurement to determine the amount needed to be removed in one direction.
- Conventional cut the remaining material, leaving material on walls for finishing.
- Load a separate finishing tool if needed.
- Make a test cut just skimming the bottom and the side of the slot.
- Zero the table and knee handwheels.
- Accurately measure the part.
- Set the knee to the full depth of the slot.
- Adjust the machine and make successive cuts in order to finish one side.
- Make a skim cut on the other side of the slot.
- Zero the table handwheel.
- Measure the slot and calculate the material needed to be removed to finish the slot.
- Adjust the machine and make successive cuts in order to finish the slot.
“Step 4: Load an end mill for roughing, one size smaller than the slot, into the milling machine.“
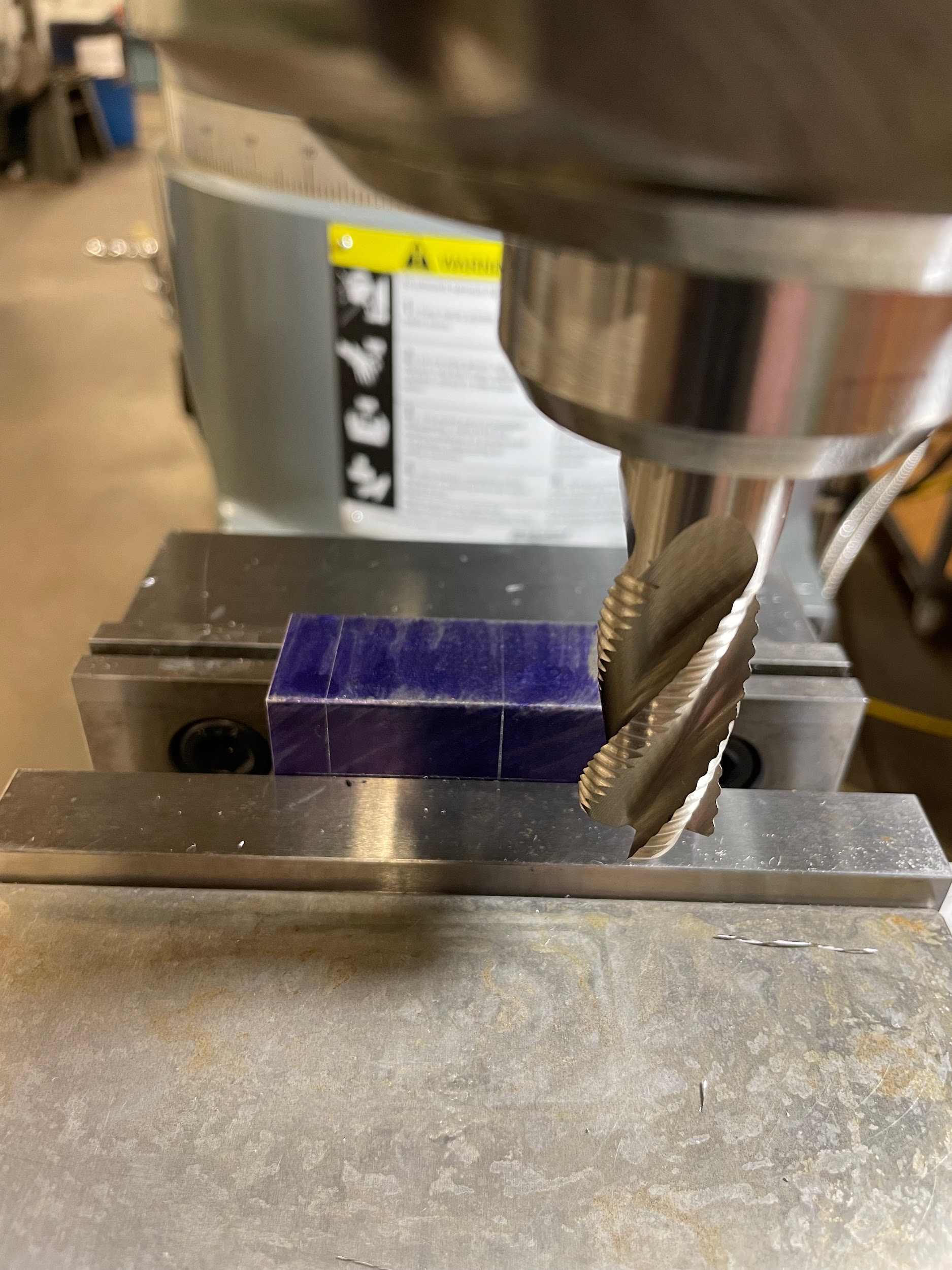
“Step 7: Position the machine so that the tool is visually in the center of the slot.“
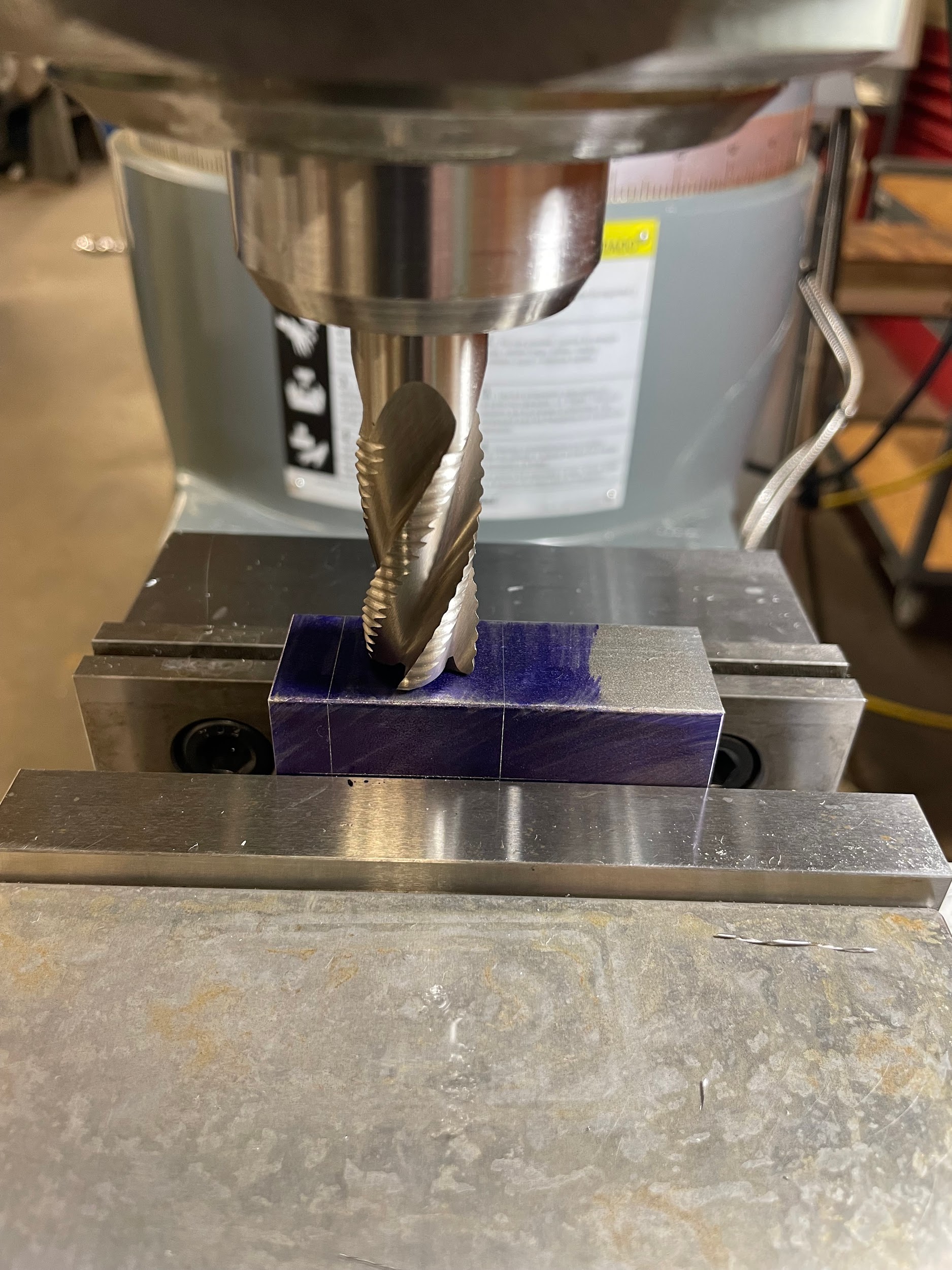
“Step 12: Move the knee up the desired depth of cut, minus .015”.“
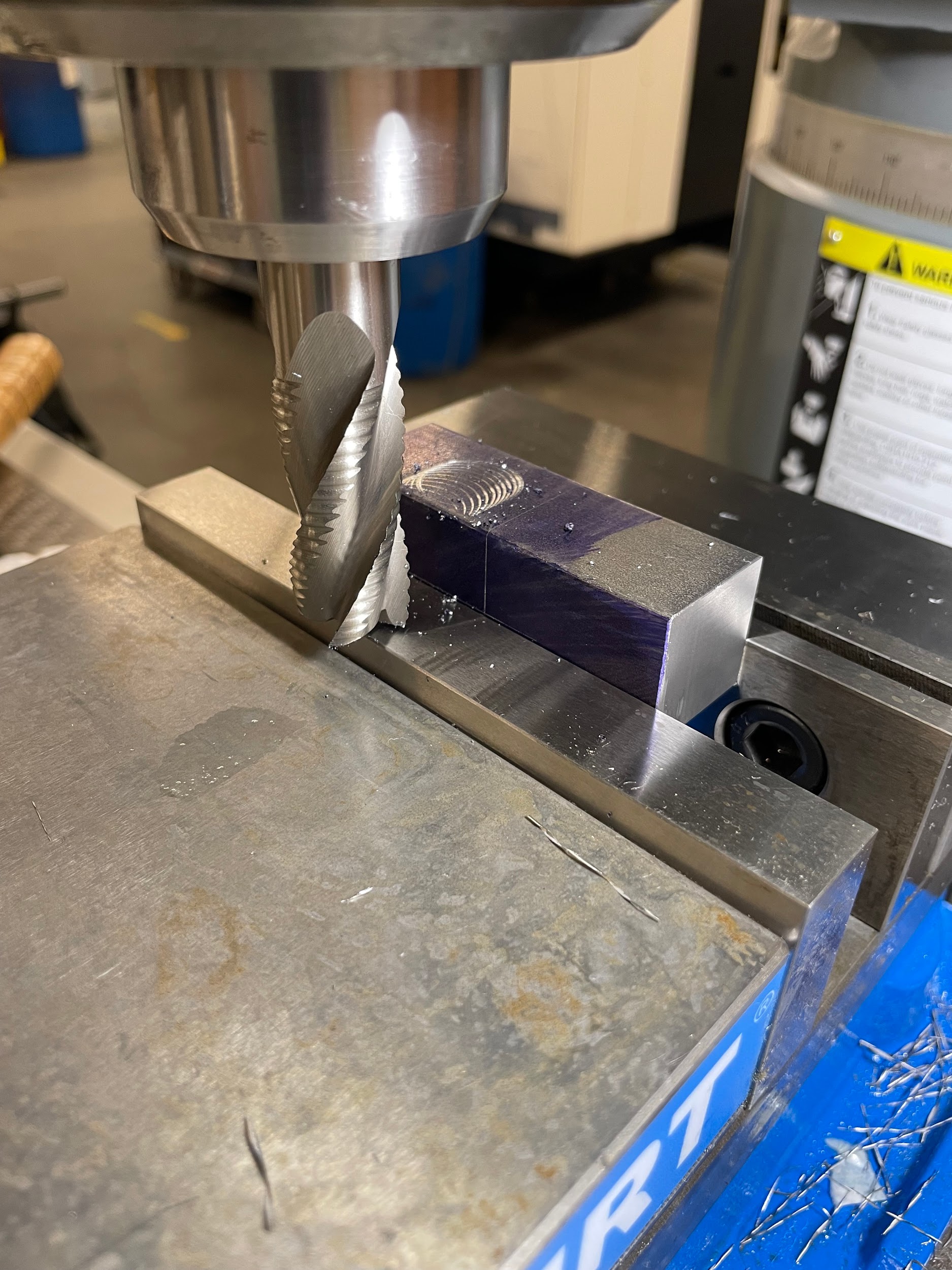
“Step 13: Lube the tool and the work.“
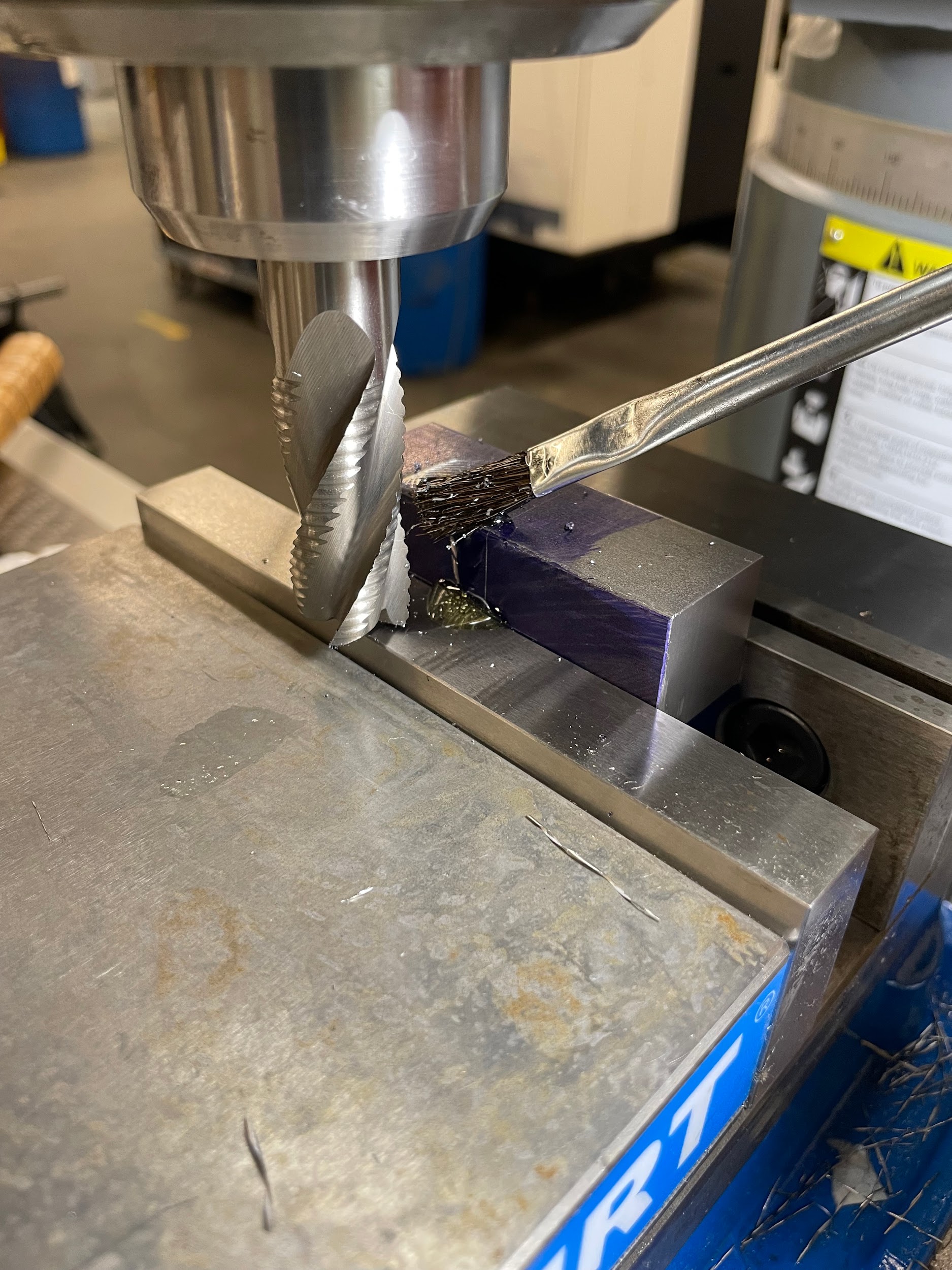
“Step 14: Make the initial cut through the length of the slot at the calculated feed rate.“
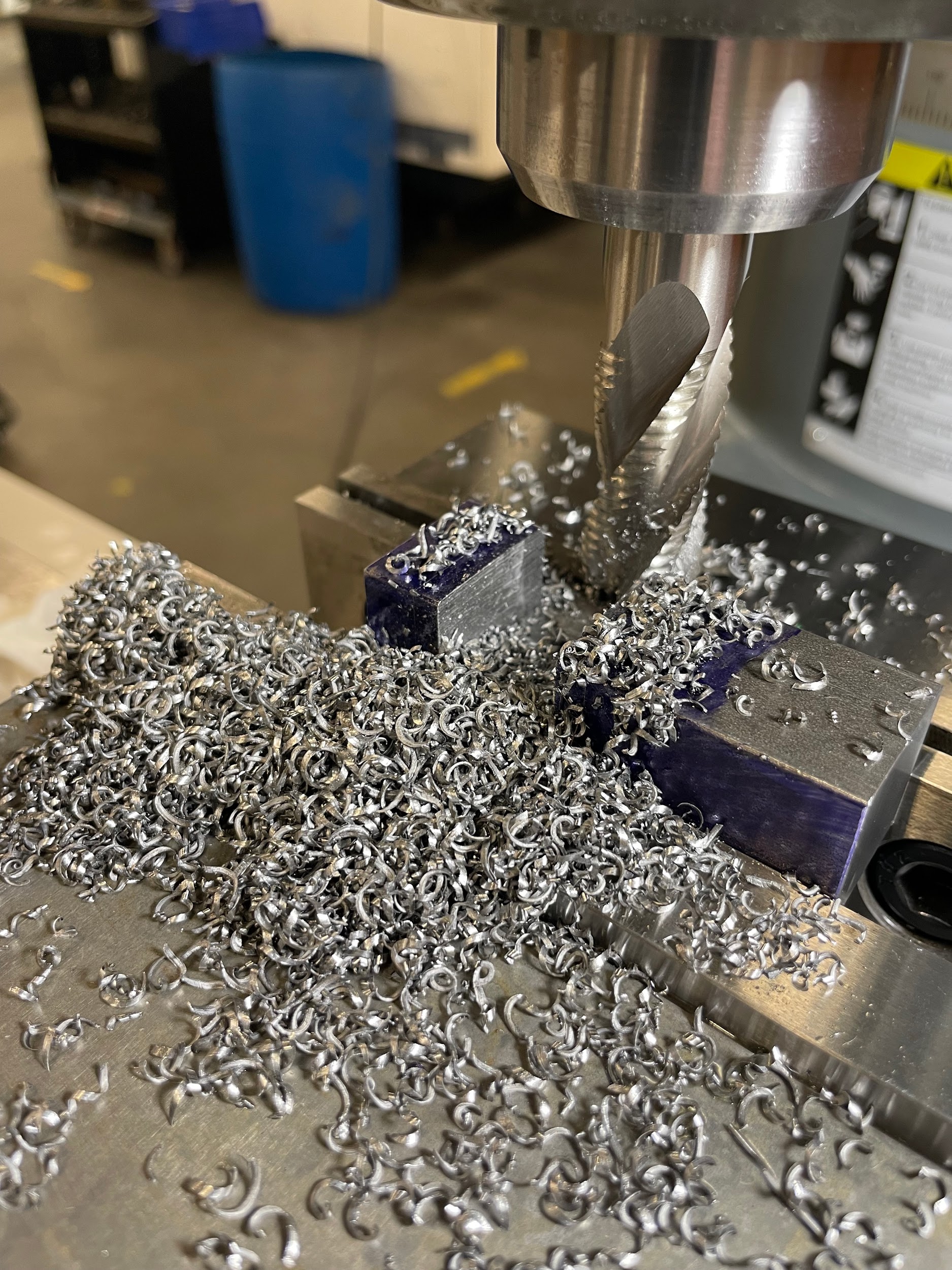
“Step 14: Make the initial cut through the length of the slot at the calculated feed rate.“
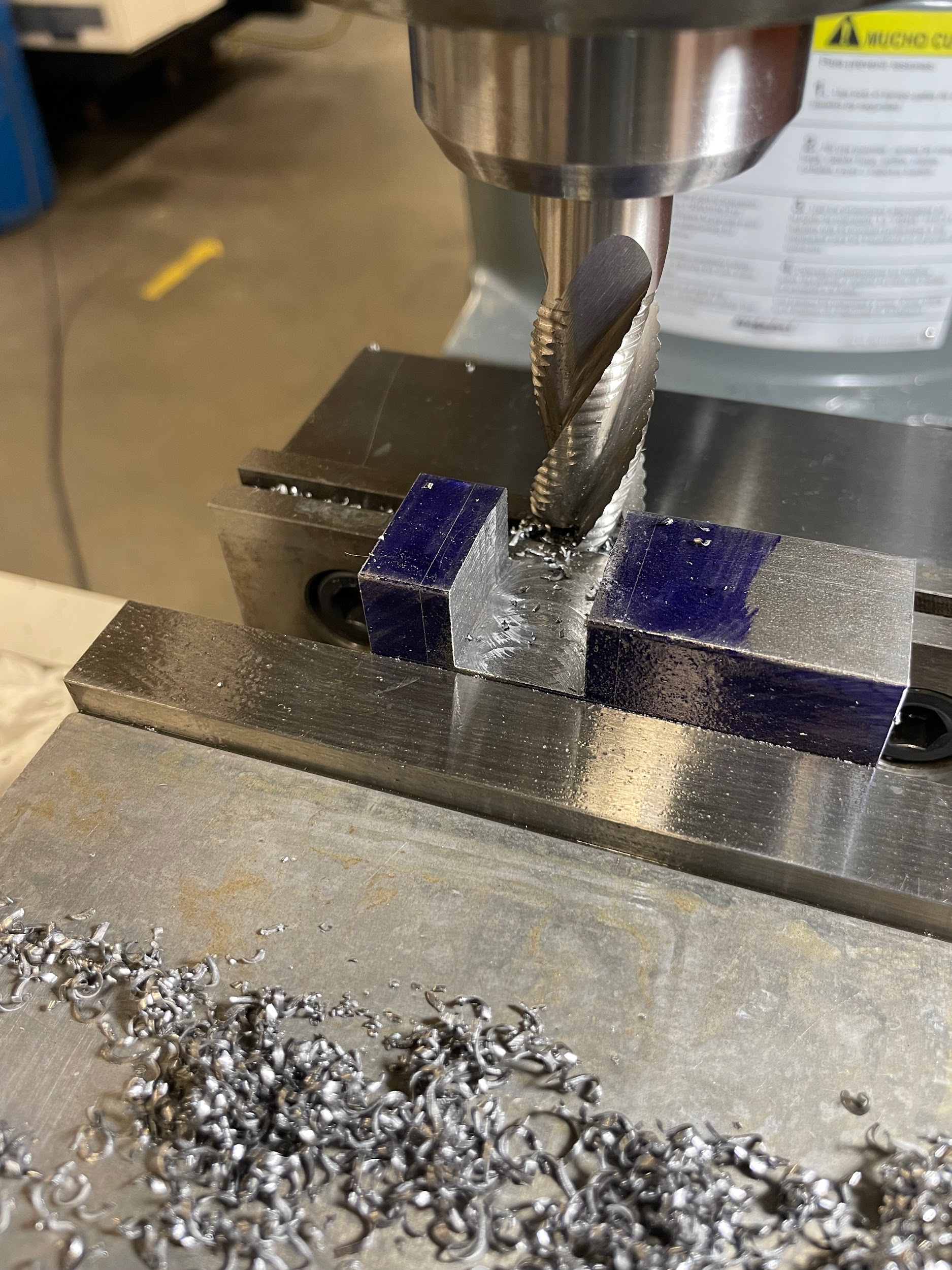
“Step 15: Take a measurement to determine the amount needed to be removed in one direction. “
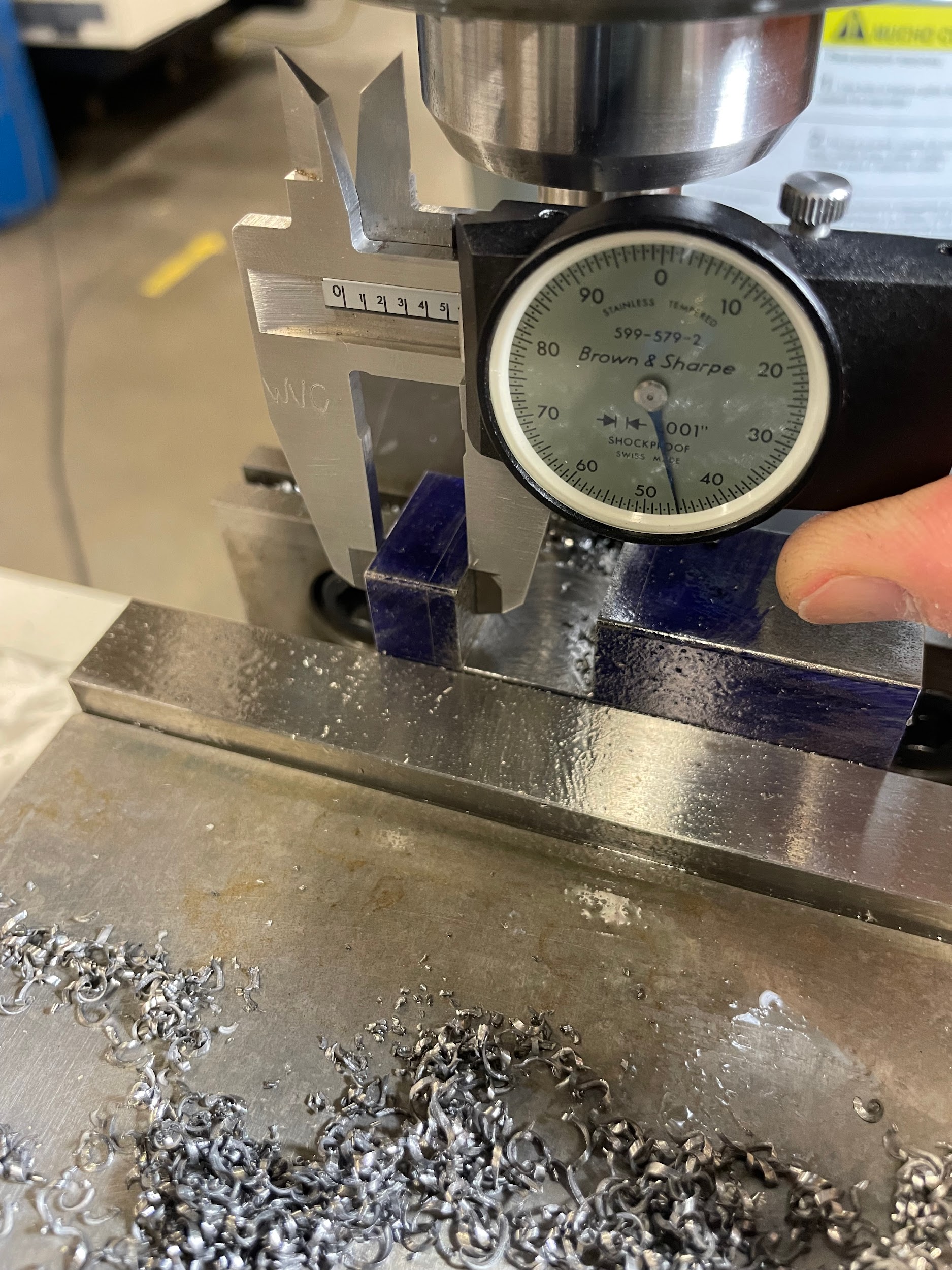
“Step 16: Conventional cut the remaining material, leaving material on walls for finishing.“
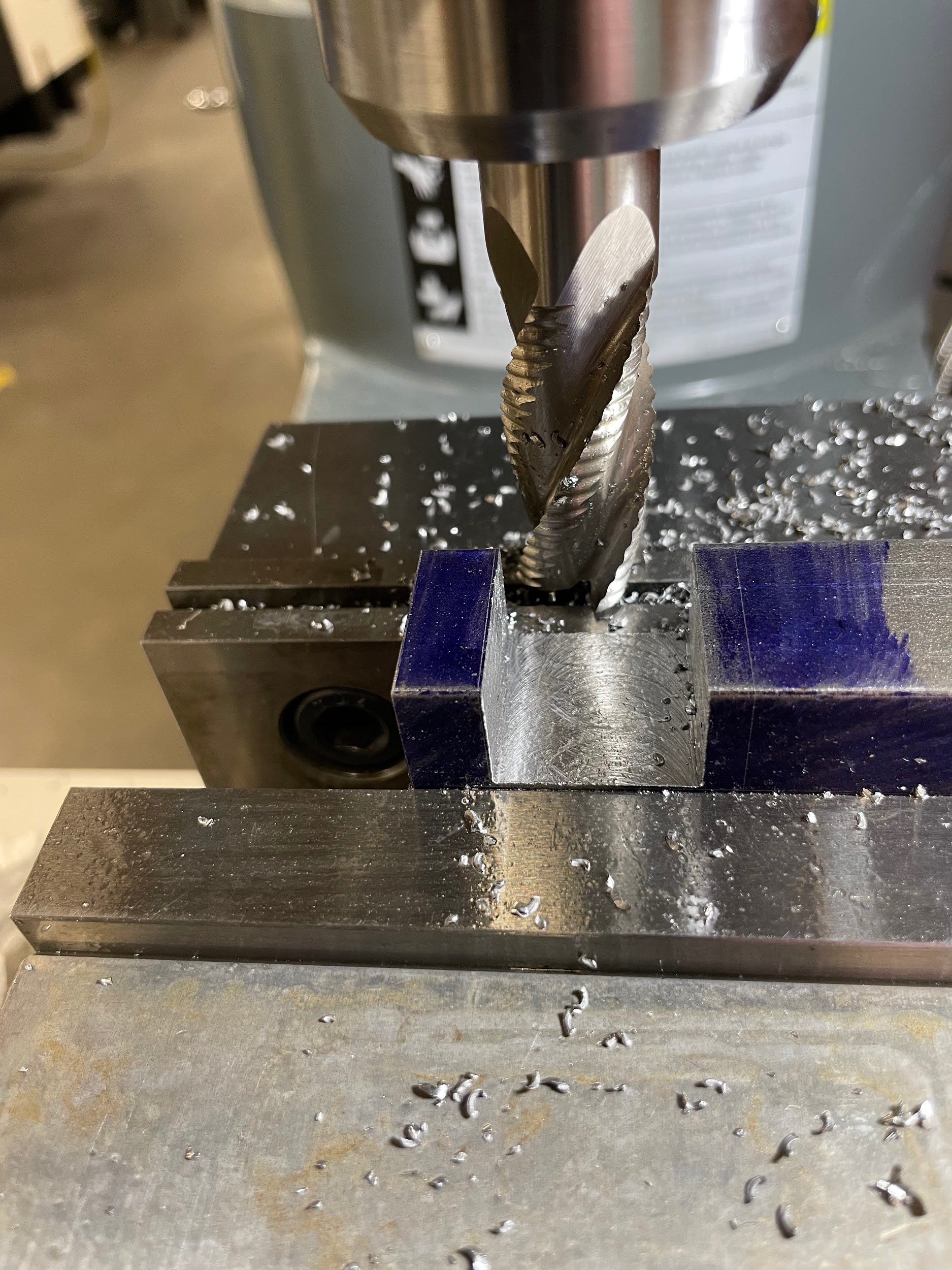
“Step 16: Conventional cut the remaining material, leaving material on walls for finishing.“
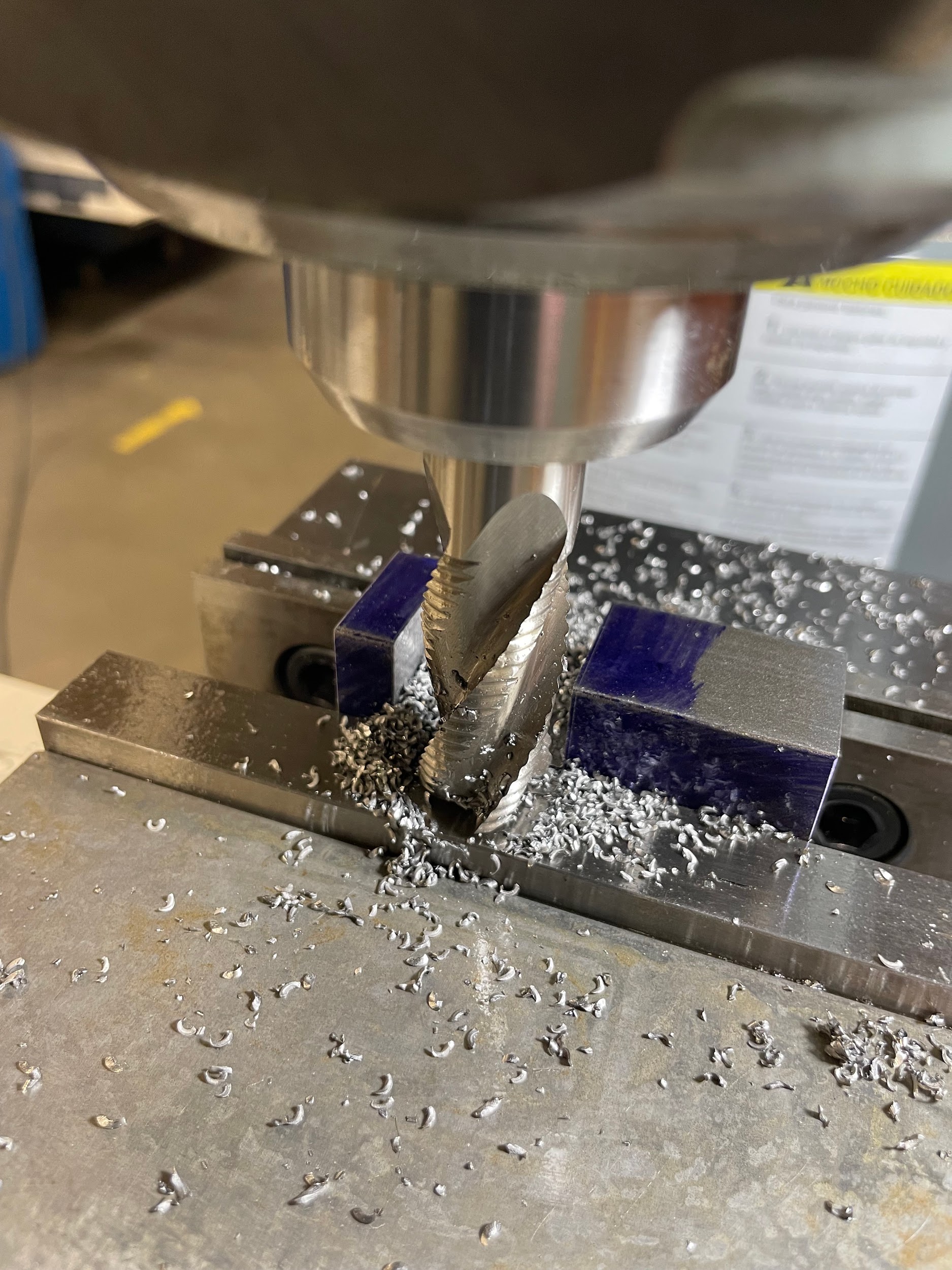
“Step 20: Accurately measure the part.“
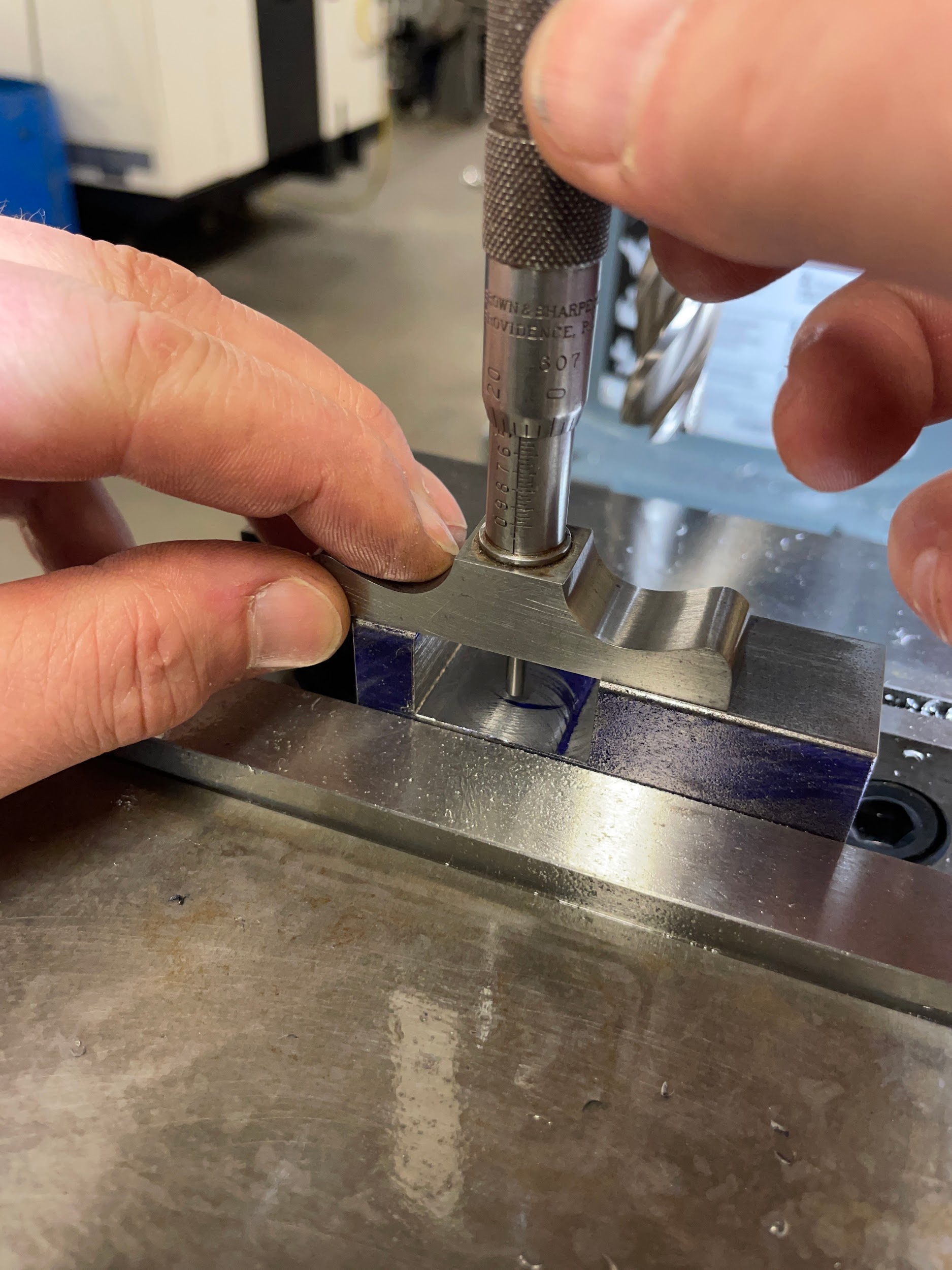
“Step 20: Accurately measure the part.“
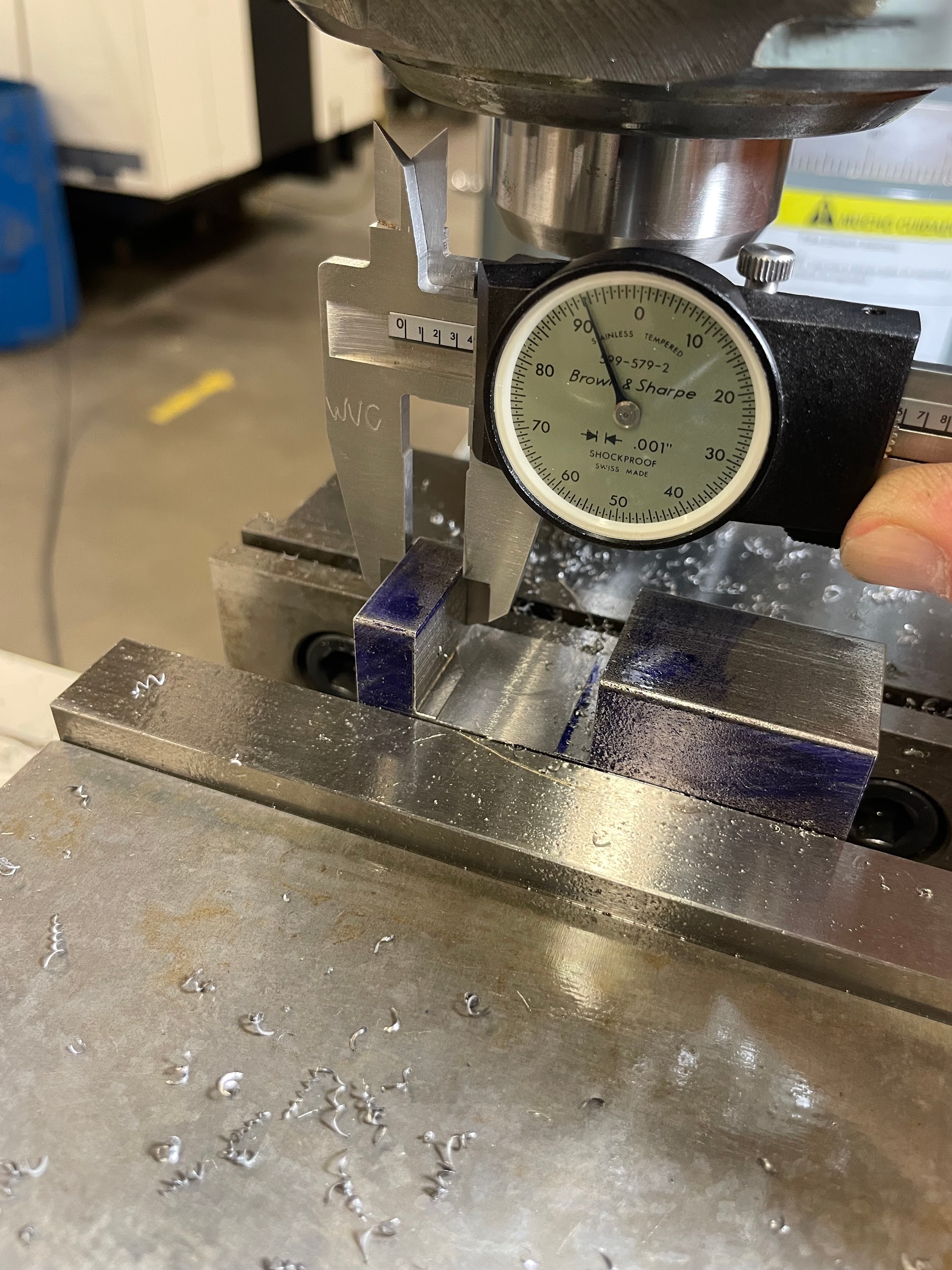
“Step 22: Adjust the machine and make successive cuts in order to finish one side.“
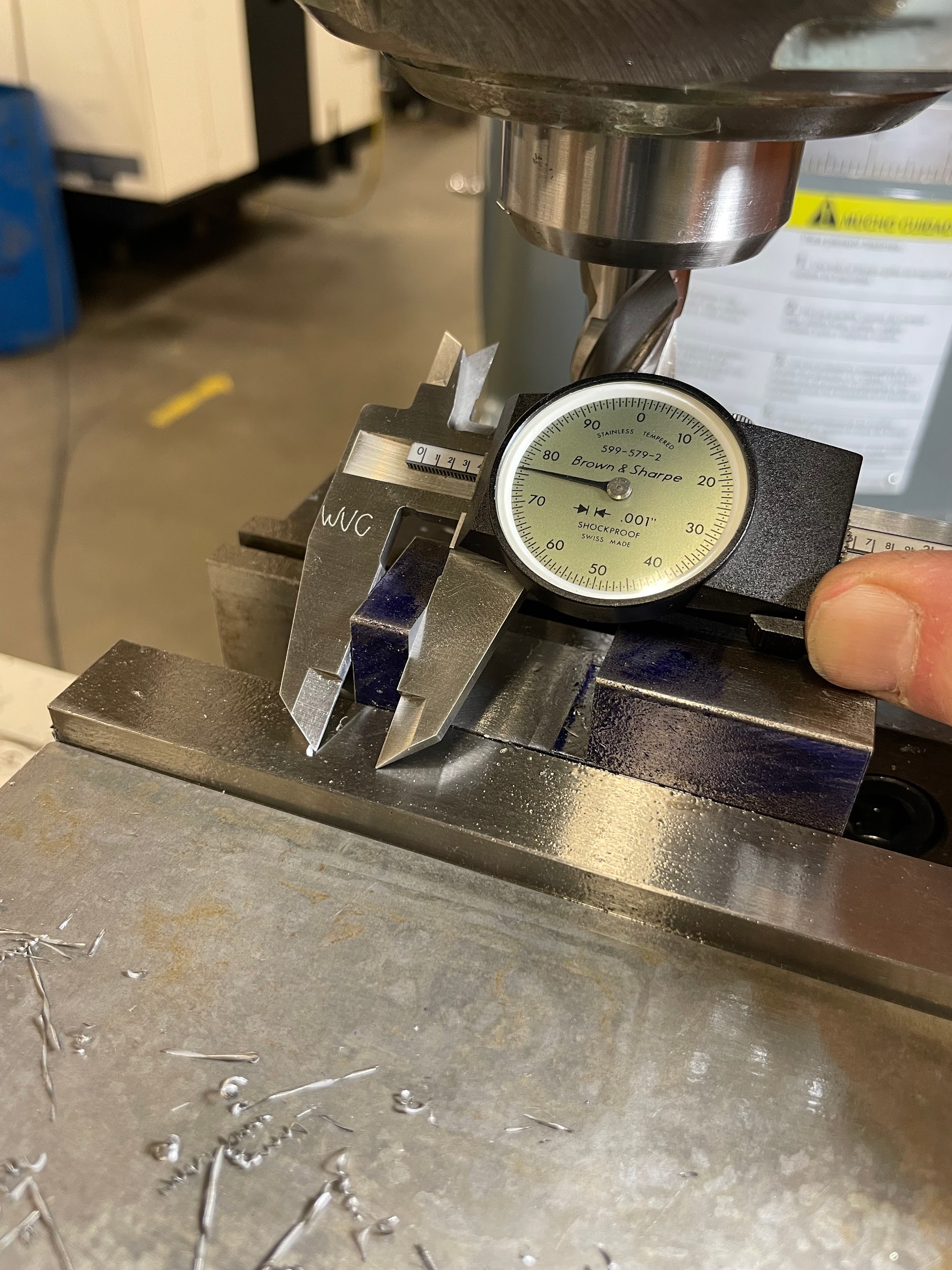
“Step 25: Measure the slot and calculate the material needed to be removed to finish the slot.“
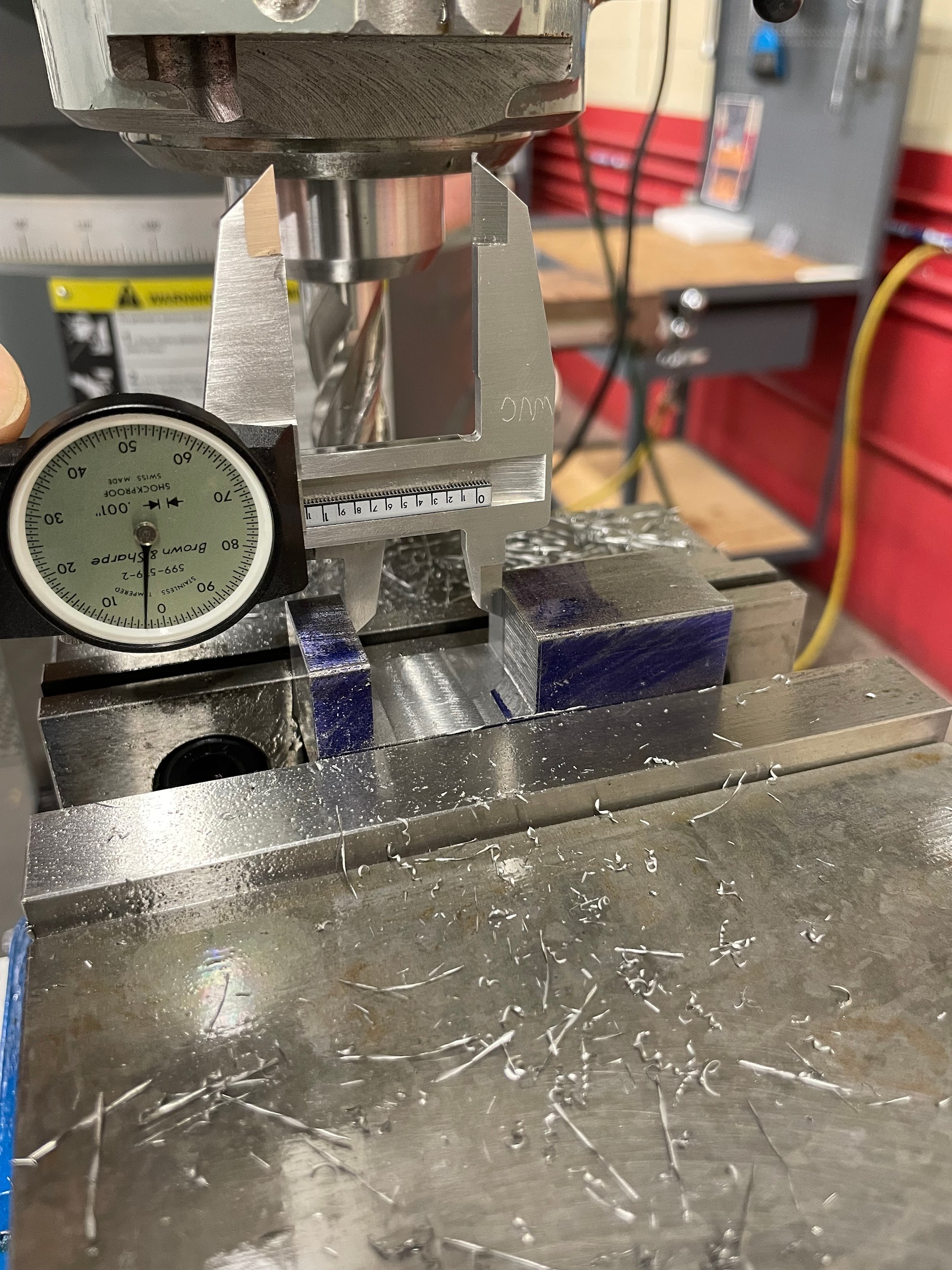
“Step 26: Adjust the machine and make successive cuts in order to finish the slot.“
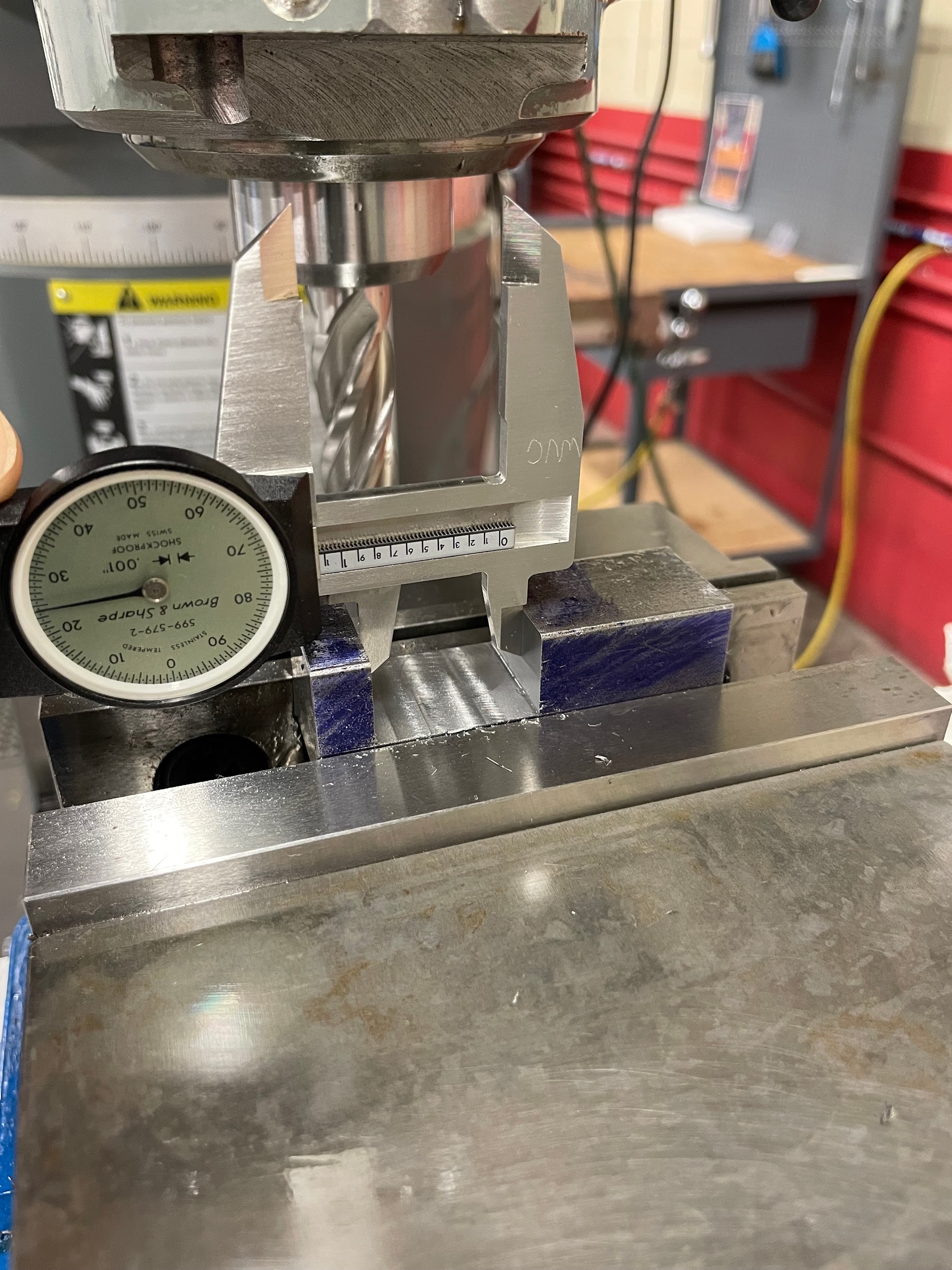
“Step 26: Adjust the machine and make successive cuts in order to finish the slot.“
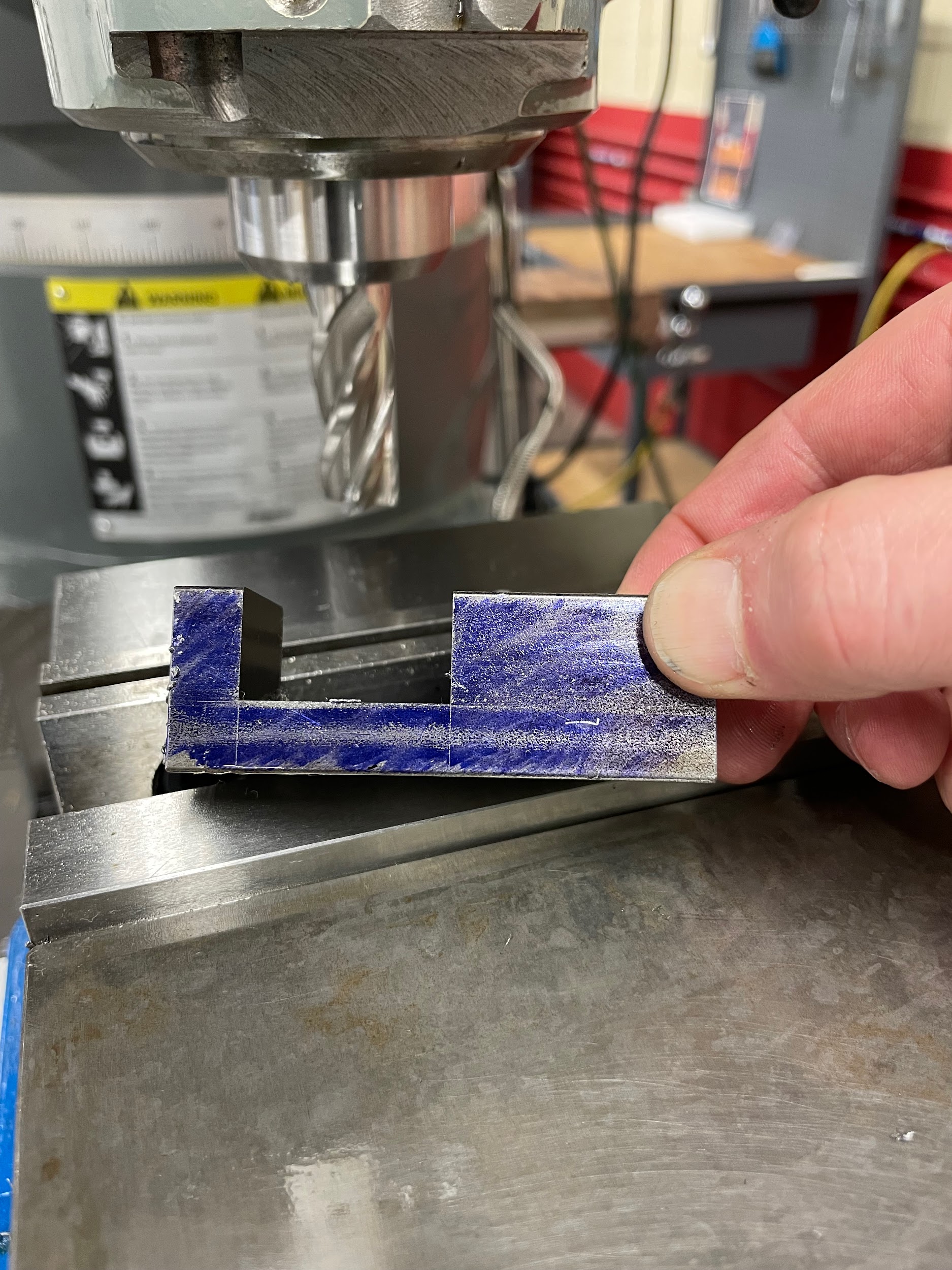
POCKETING
What is it?
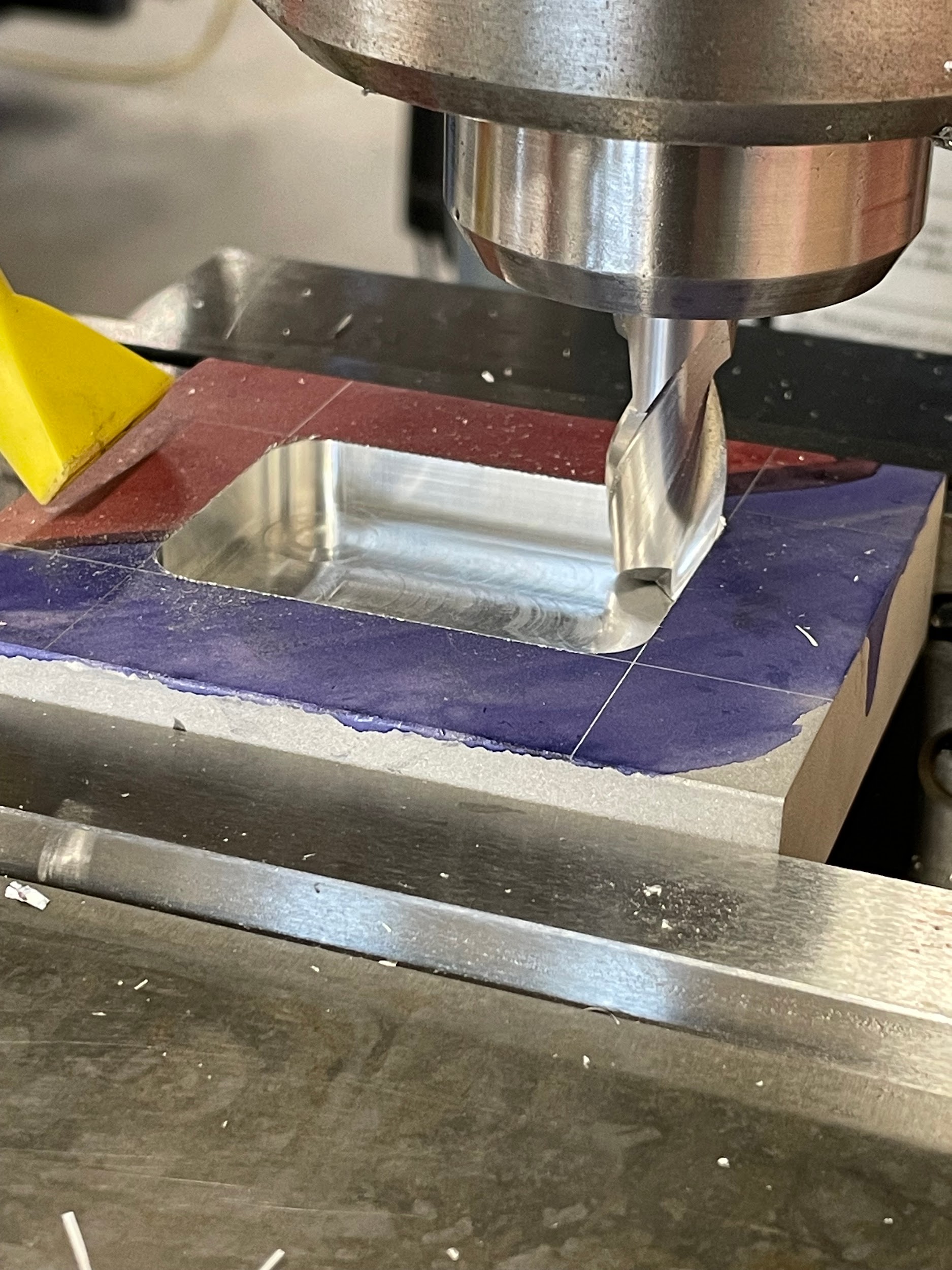
Pocketing is the process of creating a recessed cut, of variable shape, inside of the outer contour of a part. A simple pocket is generally round or rectangular shaped and at one depth. However, pockets can be any shape the designer desires and can contain multiple steps and depths.
Step by step process for pocketing:
- Apply layout dye to the area that will receive a pocket.
- Layout the pocket’s boundary.
- A hole may be drilled of similar size to the endmill required to mill out the pocket. Generally the same size as the internal radii. Drill the hole to about 1/64” from finished pocket depth.
- Load an end mill into the milling machine equal to the interior radii of the pockets corners.
- Calculate the spindle speed of the endmill chosen.
- Turn on the spindle.
- Engage the end mill into the workpiece to depth:
- Use a previously drilled hole:
- Lock the quill.
- Touch the tool off the top of the work with the knee.
- Zero knee collar.
- Raise the knee inside the drilled hole.
- Use the endmill to plunge to depth:
- Touching off the top of the work with the quill.
- Set the quill stop.
- Zero knee collar.
- Raising the knee to set the depth.
- Gently plunge the endmill to depth using the quill, breaking chips when needed.
- Lock the quill at final depth.
- Ramp into the work with an endmill:
- Lock the quill.
- Touch the tool off the top of the work with the knee.
- Zero knee collar.
- Gradually move the knee and table/saddle handwheel simultaneously to create a shallow ramp.
- Continue back and forth until the desired depth is reached.
- Use a previously drilled hole:
- Apply some initial cutting oil and continue throughout the cutting process.
- Rough the material from the inside of the pocket visually, leaving 1/32” of an inch on the walls and 1/64” on the floor for a finishing operation. An air blast can aid in chip removal and help prevent re-cutting chips and damaging the tool.
- Load a finishing end mill if needed, touch off the top of the work, and bring the tool to the full depth inside the pocket.
- Finish the bottom of the pocket.
- Gently make skim cuts along all four sides, recording the handwheel positions on each side.
- Measure the part and calculate the material remaining on the four surfaces.
- Calculate the positions of the tool to remove the rest of the material, minus .010” for a final finish.
- Conventional mill to the calculated positions.
- Measure the part and calculate the material remaining on the four surfaces.
- Calculate the positions of the tool to remove the rest of the material, making a final finish pass.
- Climb mill to the calculated positions.
- Measure the finished pocket size.
“Step 2: Layout the pocket’s boundary.“
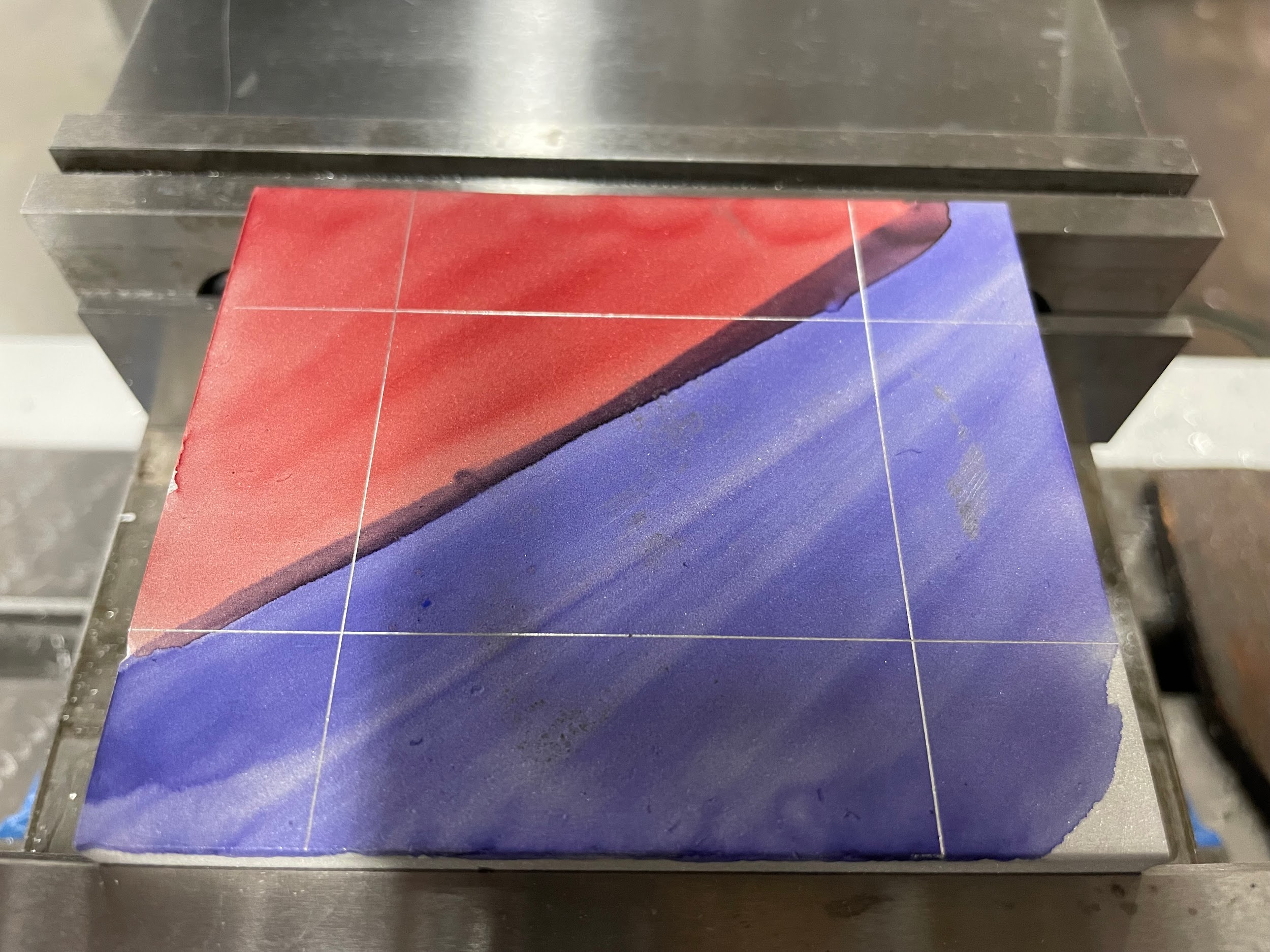
“Step 7-b-i: Toughing off the top of the work with the quill.“
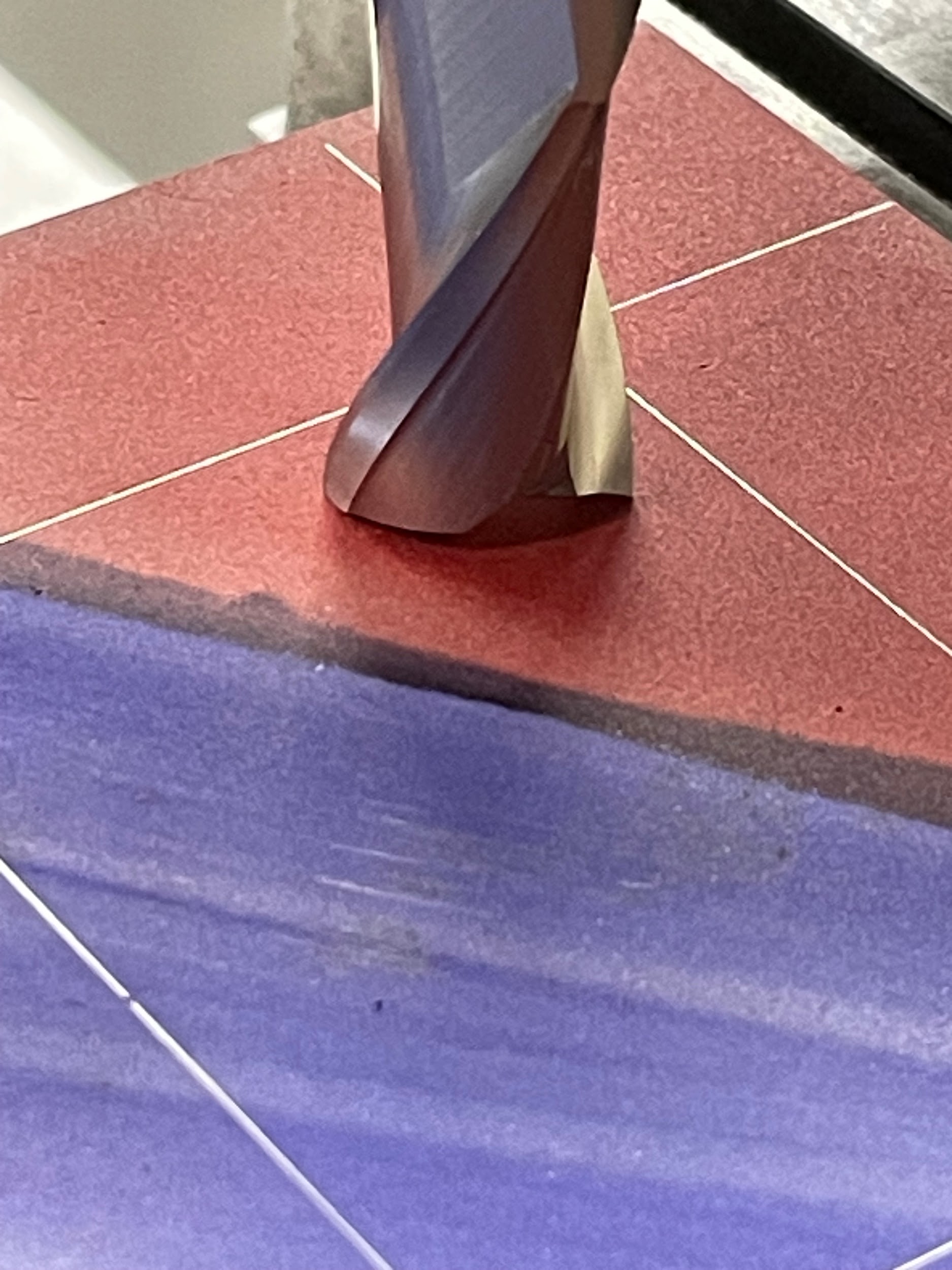
“Step 7-b-ii: Set the quill stop.“
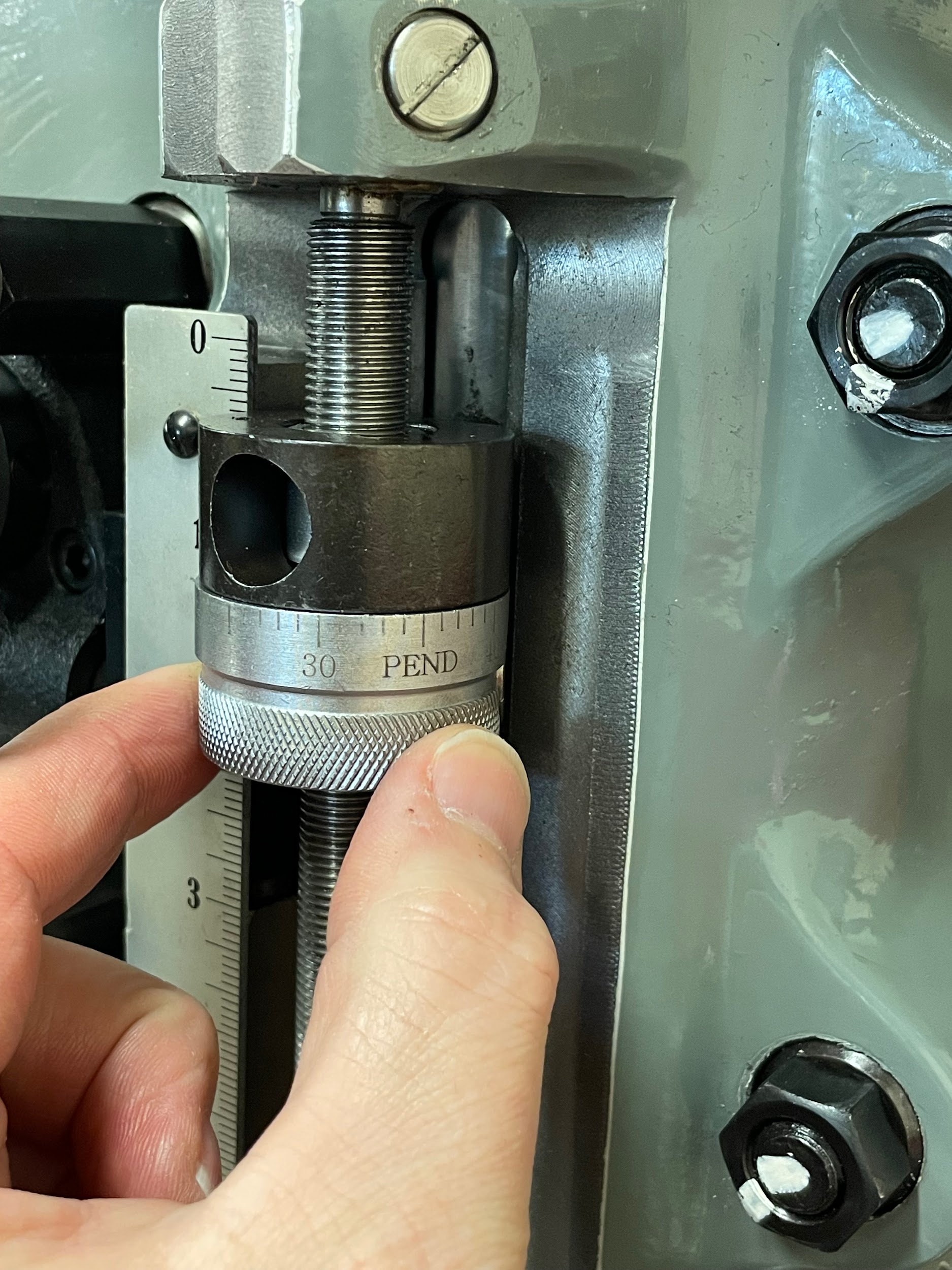
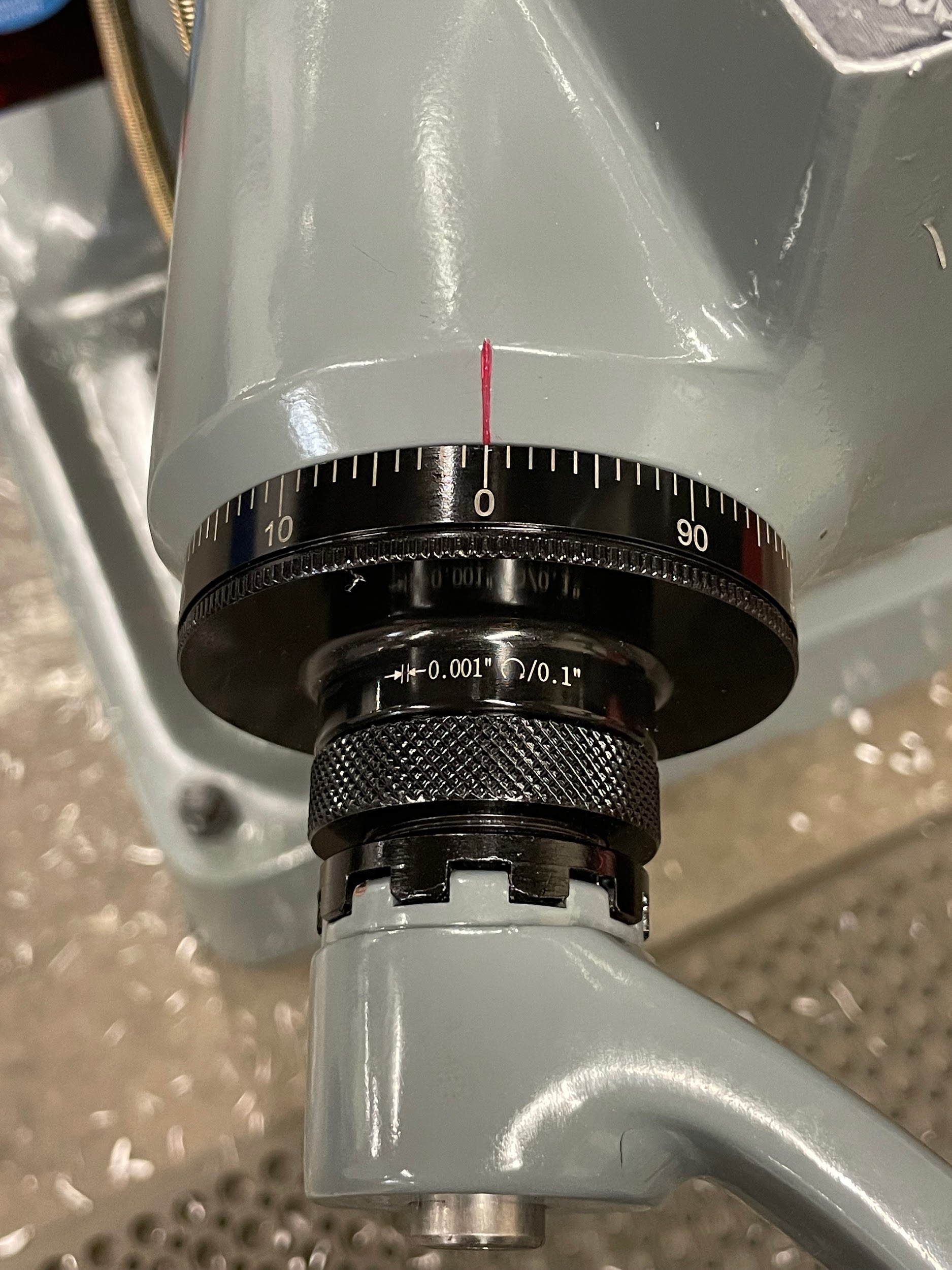
“Step 13: Measure the part and calculate the material remaining on the four surfaces.“
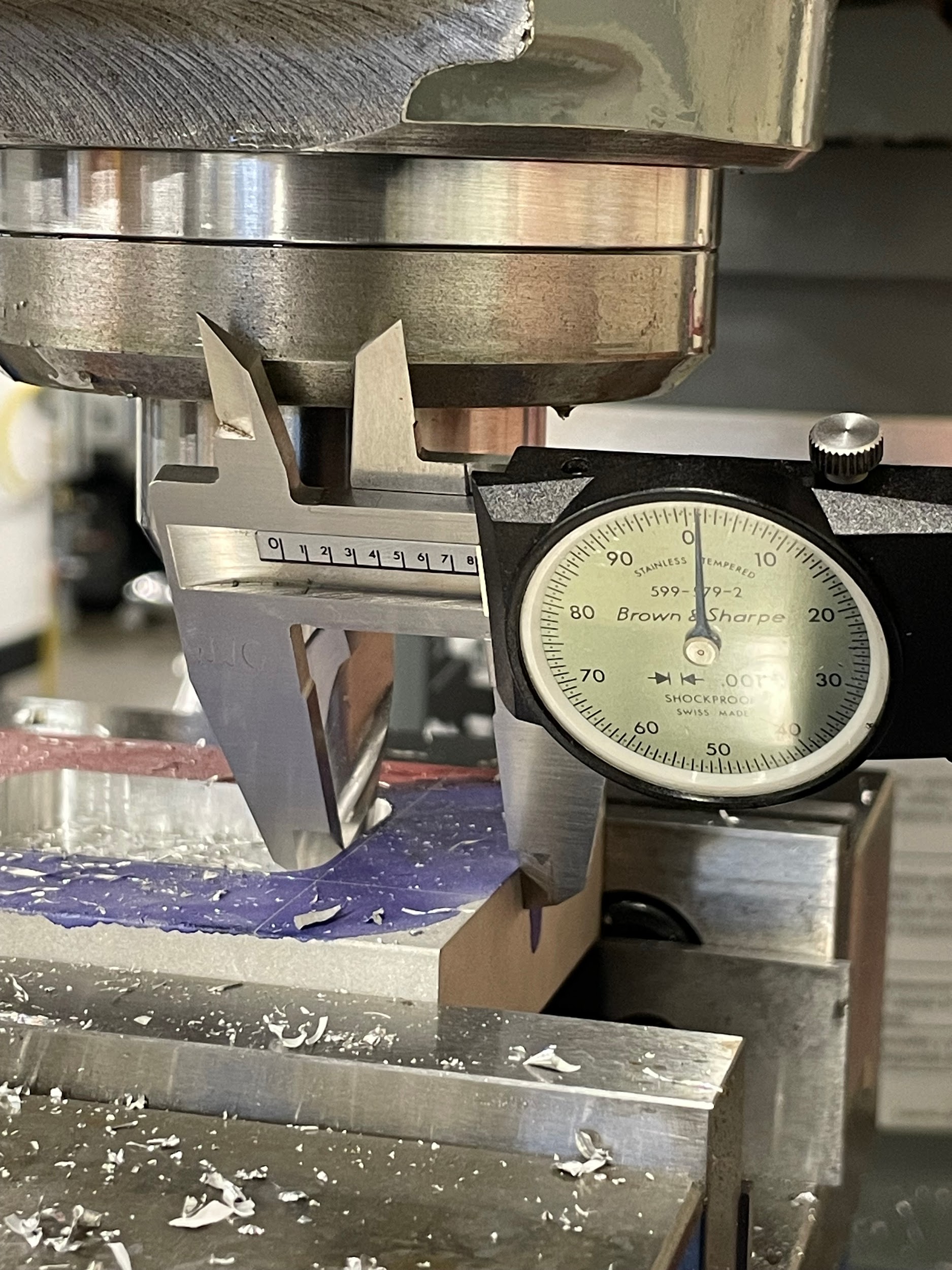
“Step 13: Measure the part and calculate the material remaining on the four surfaces.“
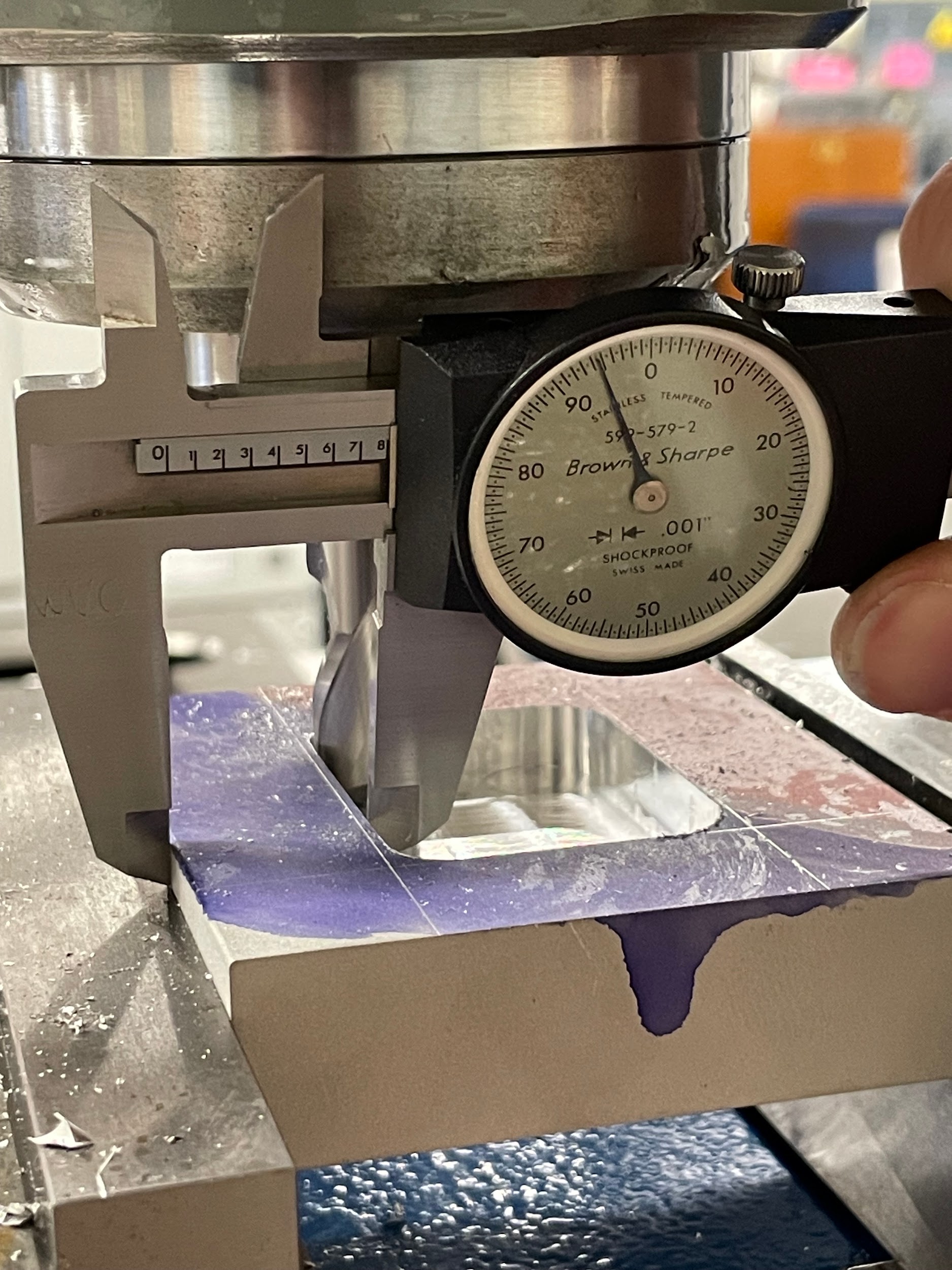
“Step 16: Measure the part and calculate the material remaining on the four surfaces.“
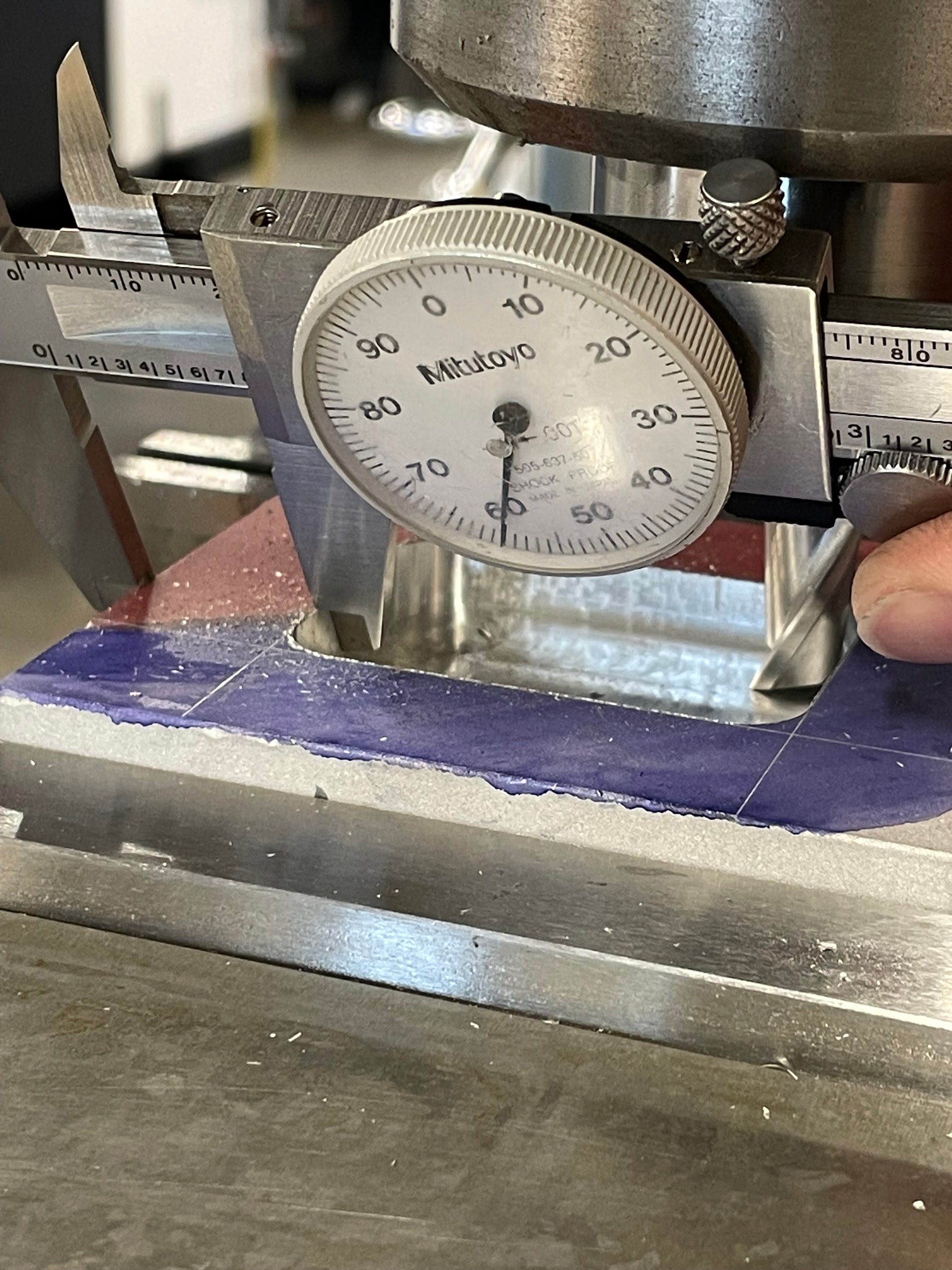
“Step 18: Climb mill to the calculated positions. “
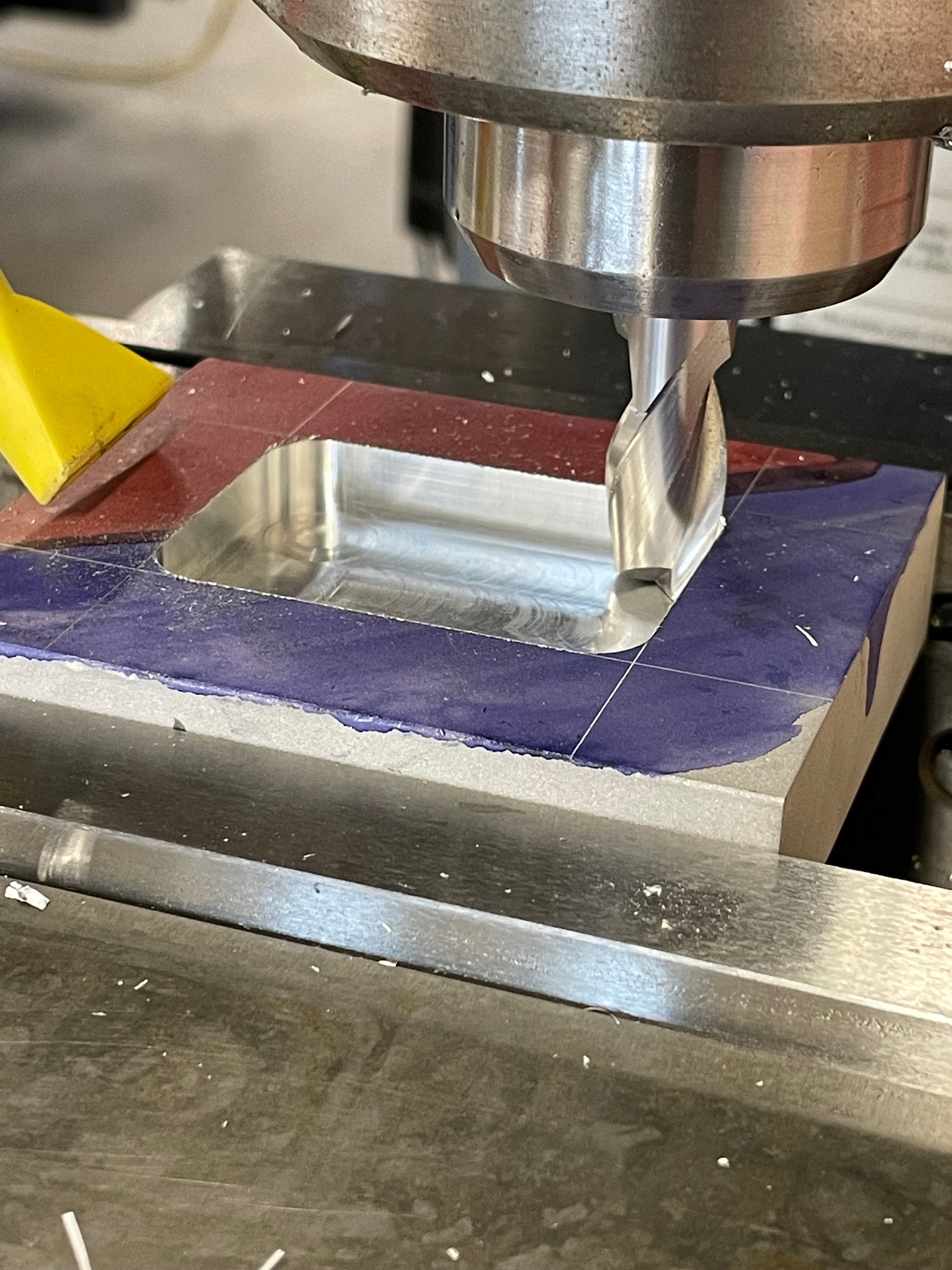
“Step 19: Measure the finished pocket size.“
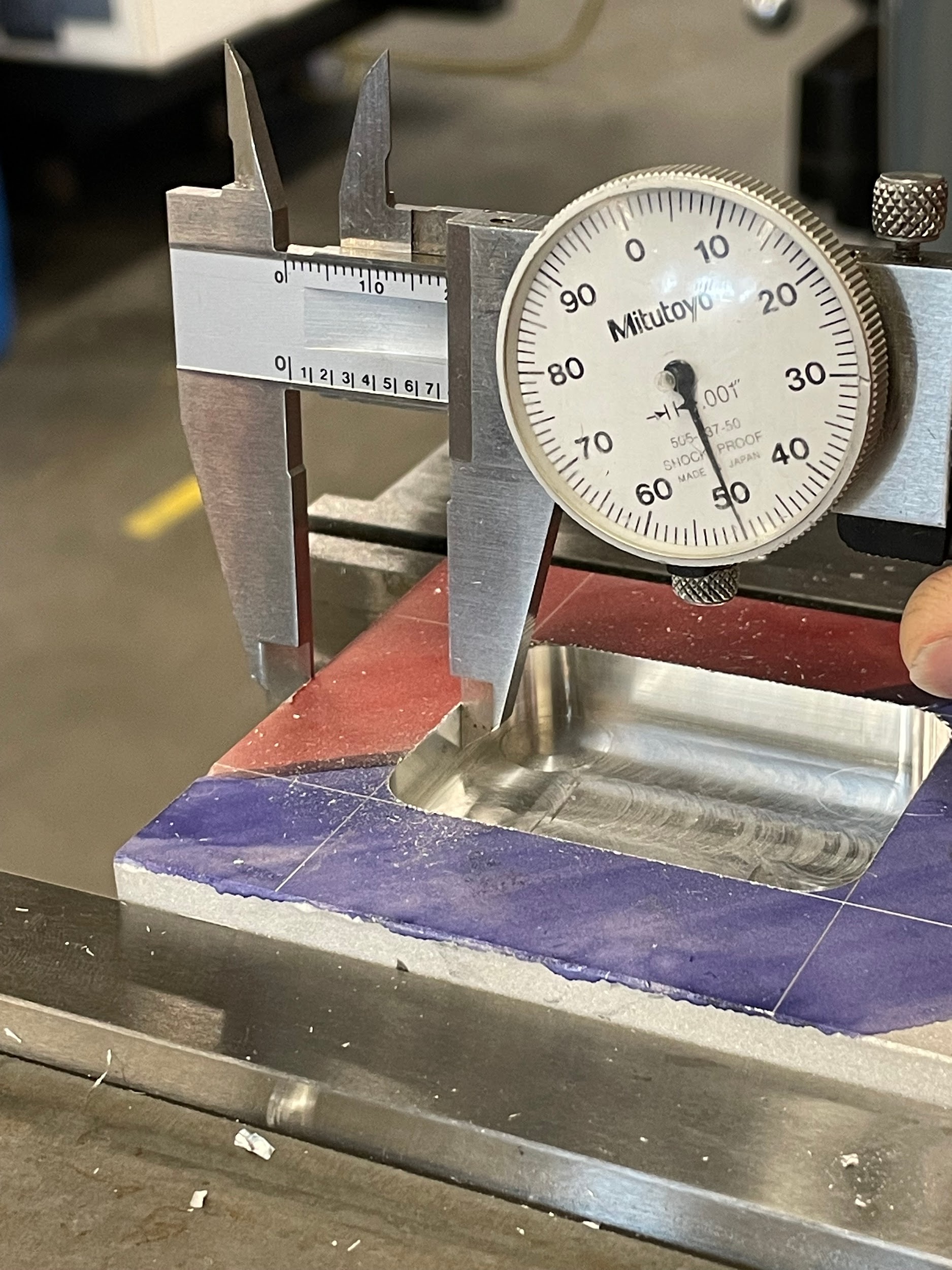