Chapter 2 : General Machine Shop Safety
Overview
Safety in the manufacturing industry in general has improved over the years due to a deliberate effort to reduce hazards (Occupational Safety and Health Administration [OSHA], 2022). A hazard is a potential source of harm or adverse health effect. Hazards are an inherent byproduct of many manufacturing processes that must be consistently and deliberately managed to prevent workplace injury.
However, the nature of manufacturing will always have hazards associated with it. The machining industry uses powerful equipment, which must withstand the forces generated during the machining process. A byproduct of the metal removal process is hot, sharp, and abundant amounts of chips and debris. Chips are created through the metal removal process inherent in metal working. When utilizing modern CNC machines, most of that is contained within the machine enclosure, and the operator works in relative safety if all equipment performs as intended. Tooling and work pieces have come loose during the machining process, and the only barrier between the fast-moving material and you is the guards and reinforced windows. If the windows become compromised or safety mechanisms are bypassed, allowing machines to operate with the doors open, you have a dangerous situation on your hands.
When operating manual mills, lathes, drill presses, surface grinders, sanders, saws, and other related machines, these typically do not have the engineered barrier between you and the hazard. Any tool breakage or work holding failure can directly impact the operator.
No matter where you find yourself in the machining manufacturing industry, you must be aware of the hazards and know how to protect yourself from them because, ultimately, you are the person responsible for your safety.
After completing this chapter, you will be empowered with the necessary knowledge to identify hazards and minimize their impact on your wellbeing.
OBJECTIVES
- Given a specific safety topic, select the governing government agency.
- Utilizing Safety Data Sheets, identify the correct Personal Protective Equipment (PPE), health hazards, safe handling, and emergency control measures.
- Select the correct firefighting agent for specific fire classifications.
- Select the correct PPE for common machine shop hazards.
- Describe common machine shop best practices that promote safe working environments.
2.1 Federal Government Safety Agencies
2.1.1 The Occupational Safety and Health Act of 1970 (OSH Act)
The Occupational Safety and Health (OSH) Act of 1970 led to the establishment of the Occupational Safety and Health Administration (OSHA) and the National Institute for Occupational Safety and Health (NIOSH). These two agencies were created to ensure safe and healthy working conditions for employees in the United States.
Occupational Safety and Health Administration (OSHA) is a federal agency under the U. S. Department of Labor. Its primary responsibility is to set and enforce standards for workplace safety and health. OSHA’s role includes inspecting workplaces, providing training and educational resources, and implementing regulations to prevent workplace injuries, illnesses, and fatalities.
National Institute for Occupational Safety and Health (NIOSH) is a research agency within the Centers for Disease Control and Prevention (CDC), which is part of the U.S. Department of Health and Human Services. NIOSH conducts research and provides recommendations aimed at preventing workplace-related injuries, illnesses, and hazards. NIOSH’s work informs the development of OSHA standards and policies.
These agencies were established to collaborate in order to improve workplace safety, reduce occupational hazards, and protect the well-being of workers across various industries in the United States.
The OSH Act (1970) is a law created to govern employee exposure to unsafe working conditions. The law requires employers to provide employees with working conditions free of known hazards. The OSH Act (1970) also created the Occupational Safety and Health Administration (OSHA), a federal agency of the U.S. Department of Labor that establishes and enforces workplace safety and health standards.
Under the OSH Act (1970), workers have rights to a safe work environment and the right to participate in activities to help ensure safe work environments. Workers have the right to file confidential complaints to have OSHA inspect work conditions. Workers have the right to receive training about workplace hazards and methods to prevent harm. Workers have rights to records and reports pertaining to their workplace. The OSH Act (1970) also gives workers the right to file complaints against an employer who may be in violation of workplace standards. The same law protects employees from retaliation from employers who seek retribution due to legal complaints.
Employers have the responsibility to provide a safe work environment for their employees. In simple terms, the employer MUST provide employees a workplace that does not have serious hazards and must follow all OSHA safety and health regulations.
Table 2.1
OSHA Poster: Job Safety and Health | IT’S THE LAW!
All workers have the right to: |
Employers must: |
A safe workplace. Raise a safety or health concern with your employer or OSHA, or report a work related injury or illness, without being retaliated against. Receive information and training on job hazards, including all hazardous substances in your workplace. Request a confidential OSHA inspection of your workplace if you believe there are unsafe or unhealthy conditions. You have the right to have a representative contact OSHA on your behalf. Participate (or have your representative participate) in an OSHA inspection and speak in private to the inspector. File a complaint with OSHA within 30 days (by phone, online or by mail) if you have been retaliated against for using your rights. See any OSHA citations issued to your employer. Request copies of your medical records, tests that measure hazards in the workplace, and the workplace injury and illness log. |
Provide employees a workplace free from recognized hazards. It is illegal to retaliate against an employee for using any of their rights under the law, including raising a health and safety concern with you or with OSHA, or reporting a work-related injury or illness. Comply with all applicable OSHA standards. Notify OSHA within 8 hours of a workplace fatality or within 24 hours of any work-related inpatient hospitalization, amputation, or loss of an eye. Provide required training to all workers in a language and vocabulary they can understand. Prominently display this poster in the workplace. Post OSHA citations at or near the place of the alleged violations. On-Site Consultation services are available to small and medium-sized employers, without citation or penalty, through OSHA-supported consultation programs in every state. Contact OSHA 1-800-321-OSHA (6742) TTY 1-877-889-5627|www.osha.gov |
Note. Reprinted from poster (Occupational Safety and Health Administration, 2019).
Employers are required to prominently display the official OSHA poster, which describes the rights and responsibilities under the OSH Act (1970).
Employers are required to provide training to their employees explaining workplace hazards and create systems such as labeling and information sheets that identify hazards.
In addition to the federal OSHA-approved safety programs, states have OSHA-approved plans that are partially federally funded. State plans must be at least as effective as the federal OSHA program. This simply means a state may not have a plan that provides less protection than the federal program.
Examples of OSHA standards are:
Hearing protection, establishing safe noise levels.
Machine guardian that protects workers from moving parts.
Exposure levels, such as asbestos, and respirators for breathing hazards.
Personal Protective Equipment (PPE) Personal Protective Equipment refers to specialized clothing, equipment, or devices designed to protect individuals from potential hazards, injuries, or health risks in the workplace or other environments. Examples of PPE are respirators, goggles, earplugs, gloves, face masks and footwear.
2.2 Hazardous Materials (HAZMAT)
Hazardous Materials (HAZMAT) refers to substances or materials that pose a risk to human health, the environment, or property due to their inherent physical, chemical, or biological properties.
If you are uncertain if something is a hazardous material, best practice is to treat it as one until you are able to ascertain it is not. To find out if something is a hazardous material, you should consult the Safety Data Sheet which can be obtained from the manufacturer or retailer.
2.2.1 Safety Data Sheets (SDS)
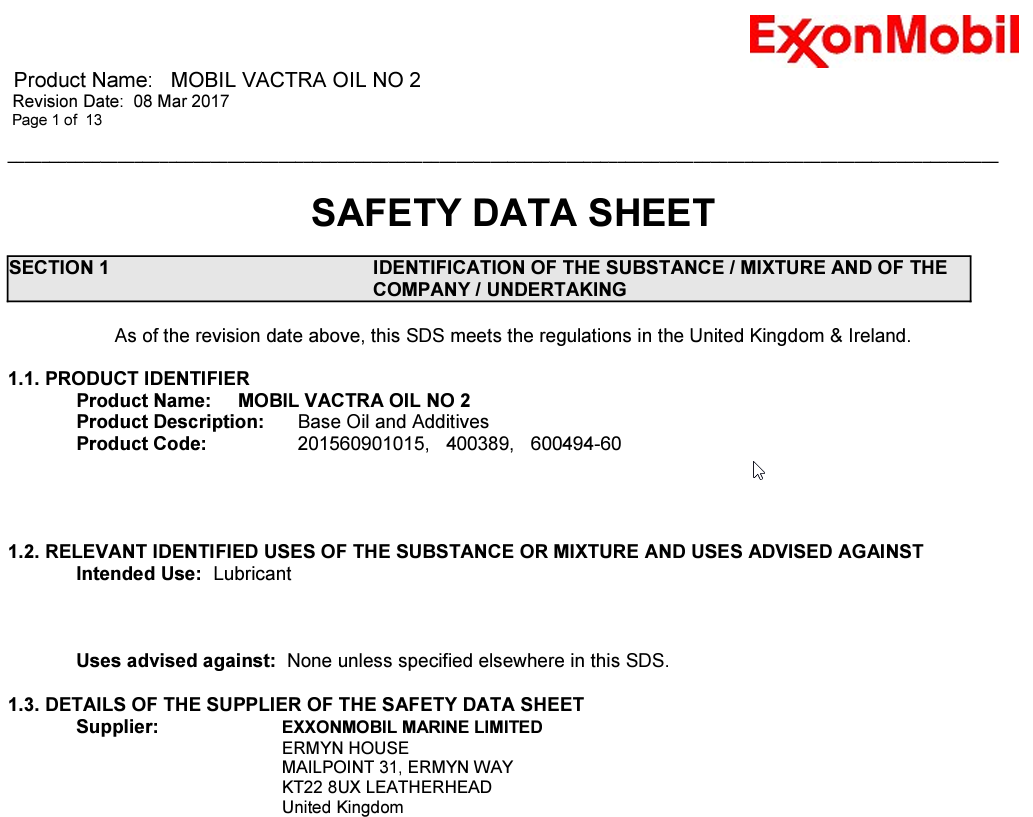
Safety Data Sheets (SDS), formerly known as Material Safety Data Sheets (MSDS), are essential documents that provide comprehensive information about hazardous chemicals or substances. These sheets are used to communicate critical safety information to employees, emergency responders, and other stakeholders who handle, store, transport, or work with potentially dangerous materials.
The SDS format is standardized and regulated by various agencies worldwide, including the Occupational Safety and Health Administration (OSHA) in the United States, the European Chemicals Agency (ECHA) in Europe, and similar agencies in other countries.
The 16 component sections of Safety Data Sheets typically include:
Identification: This section provides essential details about the chemical, including its name, brand, manufacturer, supplier information, and emergency contact numbers.
Hazard Identification: This part describes the potential hazards associated with the chemical, including its physical, health, and environmental hazards. This information is crucial for understanding the risks and taking appropriate safety precautions.
Composition/Ingredients: The SDS lists the chemical ingredients and their concentration ranges. This helps users identify any substances that might cause allergies or other health concerns.
First Aid Measures: In case of accidental exposure or ingestion, this section outlines the immediate steps to take for providing first aid to affected individuals.
Fire-Fighting Measures: Describes appropriate fire-fighting methods and any specific hazards related to fires involving the chemical.
Accidental Release Measures: Provides guidance on how to contain and clean up spills or leaks safely.
Handling and Storage: Offers advice on the safe handling, storage, and transportation of the chemical to prevent accidents and exposures.
Exposure Controls/Personal Protection: Lists recommended exposure limits, engineering controls (e.g., ventilation), and personal protective equipment (PPE) necessary for handling the chemical safely.
Physical and Chemical Properties: Provides information on the chemical’s appearance, odor, boiling and melting points, solubility, and other relevant characteristics.
Stability and Reactivity: Discusses the chemical’s stability and potential reactivity hazards, such as incompatibilities with other substances.
Toxicological Information: Details potential health effects and toxicological data based on studies and known information about the chemical.
Ecological Information: Discusses the potential impact of the chemical on the environment.
Disposal Considerations: Offers guidance on proper disposal methods for the chemical, considering its environmental impact.
Transport Information: Provides information about the safe transport of the chemical, including any regulatory requirements.
Regulatory Information: Highlights relevant regulations and requirements concerning the chemical.
Other Information: Additional information that may not fit into other sections, including date of preparation or revision.
Safety Data Sheets are essential tools for ensuring the safe handling and management of hazardous chemicals. Employers must make SDS accessible to their employees, and individuals should familiarize themselves with SDS before working with any potentially hazardous substance.
2.2.2 Hazardous Material Labeling
The standards for hazardous material labeling are primarily governed by two key systems: the Globally Harmonized System of Classification and Labeling of Chemicals (GHS) an internationally agreed-upon system developed by the United Nations to standardize the classification and labeling of chemicals, and the Hazardous Materials Identification System (HMIS) a hazard communication system developed by the National Paint & Coatings Association (NPCA), now known as the American Coatings Association (ACA), to provide consistent hazard ratings for chemicals used in the workplace. Both systems provide standardized labels to communicate the potential hazards of chemicals and hazardous materials in the workplace.
Globally Harmonized System (GHS): The GHS is an internationally agreed-upon system developed by the United Nations to standardize the classification and labeling of chemicals (United Nations Economic Commission for Europe, n.d.). The GHS aims to harmonize hazard communication globally, making it easier for countries to understand and implement consistent labeling and safety data sheets. GHS labels typically include the following elements:
Pictograms: Easily recognizable symbols representing the type of hazard (e.g., health hazard, flammability, corrosivity, etc.).
Signal Word: A single word (either “Danger” or “Warning”) that indicates the level of severity of the hazard.
Hazard Statements: Standardized phrases describing the nature of the hazard.
Precautionary Statements: Recommended measures to be taken to minimize or prevent adverse effects.
GHS labels are designed to be easily understood by workers, consumers, and emergency responders worldwide.
Hazardous Materials Identification System (HMIS): The HMIS is a hazard communication system developed by the National Paint & Coatings Association (NPCA) to provide consistent hazard ratings for chemicals used in the workplace. HMIS labels use a color-coded system and include the following elements:
Hazard Rating: A numerical rating from 0 to 4 indicating the degree of the hazard (0 represents minimal hazard, and 4 indicates severe hazards).
Health, Flammability, and Physical Hazard: Each hazard category is assigned a color (blue for health, red for flammability, and yellow for physical hazards) with a corresponding symbol and label text.
2.2.3 PERSONAL PROTECTION
A: Safety glasses should be worn when handling this material. This is the minimal rating given to any material.
B: Safety glasses and protective gloves should be worn when handling this material. This rating is given to materials that have the potential for skin irritation or may be harmful if absorbed through the skin.
C: Goggles, protective gloves, and a laboratory apron should be worn when handling this material. This rating is given to materials that have the potential for splashing and are listed as having a HEALTH HAZARD RATING of 2 or higher.
D: A face shield, goggles, protective gloves, a laboratory apron, and an exhaust fume hood should be used when handling this material. This rating is given to materials that are capable of detonation or explosive reactions. This rating would apply to all materials receiving a REACTIVITY HAZARD rating of 3 or 4.
E: Safety glasses, protective gloves, and an exhaust fume hood should be used when handling this material. This rating is given to materials that have the potential to release harmful vapor, mist, or dust into the air.
H: Splash goggles, a laboratory apron, protective gloves, and an exhaust fume hood should be used when handling this material. This rating is given to materials that, in addition to having the potential for releasing harmful vapor, mist, or dust into the air, also have the potential for splashing. Strong acids, strong bases, and strong organic solvents would fall into this category.
HMIS labels are commonly used in the U.S. and are often found in conjunction with other labeling systems, such as GHS.
It’s important to note that individual countries or regulatory agencies may have specific requirements for hazardous material labeling, and employers should ensure compliance with applicable regulations when handling and labeling hazardous materials in the workplace. Both the GHS and HMIS systems are widely used and recognized, providing valuable information to help workers and emergency responders understand and respond appropriately to the hazards of chemicals and hazardous materials.
2.2.4 Hazardous Waste (HAZWASTE)
Managing hazardous waste is crucial to protecting human health and the environment. Hazardous waste includes materials that are toxic, flammable, corrosive, or reactive. Proper management ensures safe handling, storage, transportation, treatment, and disposal. Here’s a general guide on how to manage hazardous waste:
Identify and Classify Waste: Determine if the waste is hazardous by assessing its characteristics (ignitability, corrosivity, reactivity, toxicity) and comparing it to regulatory definitions. Classify the waste based on its hazardous properties.
Waste Minimization: Minimize waste generation by adopting practices like source reduction, process modification, or using less hazardous materials. This reduces the overall quantity of hazardous waste.
Segregation and Storage: Segregate different types of hazardous waste to prevent chemical reactions and ensure compatibility. Store hazardous waste in appropriate containers that are in good condition and designed to handle the specific waste type. Label containers with clear, legible information about the waste’s contents and hazards.
Handling and Transportation: Train personnel in proper handling procedures, including the use of personal protective equipment (PPE). Use suitable equipment for loading and unloading to prevent spills or accidents. Comply with transportation regulations, including proper labeling, placarding, and paperwork.
Treatment and Recycling: If feasible, treat hazardous waste on-site to reduce its toxicity or volume. Explore opportunities for recycling, reusing, or reclaiming waste materials, following applicable regulations.
Disposal: Choose disposal methods based on the waste’s characteristics and regulatory requirements, such as landfilling, incineration, or deep-well injection. Ensure that disposal facilities are properly permitted and comply with environmental regulations.
Documentation and Record Keeping: Maintain accurate records of waste generation, handling, treatment, and disposal. Keep records for the required time period as mandated by regulations.
Training and Awareness: Provide regular training to personnel involved in hazardous waste management to ensure they understand proper procedures and safety measures. Promote awareness of hazardous waste management practices throughout the organization.
Regulatory Compliance: Stay informed about local, state, and federal regulations governing hazardous waste management. Obtain necessary permits and licenses for handling and disposal activities.
Emergency Preparedness: Develop and communicate emergency response plans for spills, leaks, or other accidents involving hazardous waste. Provide appropriate emergency equipment, containment materials, and PPE.
Auditing and Continuous Improvement: Regularly audit your hazardous waste management practices to identify areas for improvement and ensure compliance. Implement corrective actions based on audit findings to enhance safety and environmental protection.
The shop supervisor can provide information relating to best practices within specific shops. Not all shops handle the information found in this chapter in the same manner. Getting to know the specific culture within a shop will assist you in understanding specific shops’ interpretation of safety guidelines.
2.2.5 Hazard Communication Standard
Hazard Communication, HAZCOM short for Hazard Communication training, is a workplace safety program designed to educate employees about the potential hazards of chemicals and how to safely handle, use, and store them. The “right-to-know” standard requires employers to inform and train workers about hazardous chemicals in the work area (OSHA, n.d.). Employer responsibilities for HAZCOM are:
Provide workers with training and information.
Maintain a current list of hazardous materials.
Ensure hazardous chemicals are labeled with the chemical’s identity and its hazards
Maintain Safety Data Sheets (SDSs) : formally known as Material Safety Data Sheets (MSDSs) which provide detailed information about chemical hazards, their effects, how to prevent exposure, and emergency treatment if an exposure occurs.
2.3 Fires In The Workplace
2.3.1 The Chemistry of Fire

Before we can discuss fire safety awareness in the workplace, you first need to understand how fire works. One of the simplest techniques for understanding fire is to use the fire triangle, a simple and fundamental concept used to understand the three essential components required for a fire to occur and sustain itself; fuel, heat, and oxygen. The process referred to as a fire is more accurately defined as combustion. Combustion is the process of combining a fuel and oxygen and then adding an ignition source. It is the process of combining a fuel and oxygen and then adding an ignition source. Once you have those three elements in the proper proportion, the end result is fire. Fire, like a three-legged stool, will fail if you remove one of the supporting elements. Fuel provides the base substance, which, when heated enough, breaks down into molecules, releasing gaseous energy, which then ignites, creating heat and light. Heat is the energy that must be maintained to sustain the chemical breakdown of the fuel, providing the base for combustion. The final side of the fire triangle is oxygen, which reacts with the fuel molecules that break apart and combine with other atoms and molecules.
To extinguish a fire, you will need to remove one of the three key elements: fuel, heat, or oxygen. This is performed by different processes depending upon the fuel or ignition present, which defines what classification of fire it is. Classes of fire will be discussed later.
2.3.2 Classifications of fire
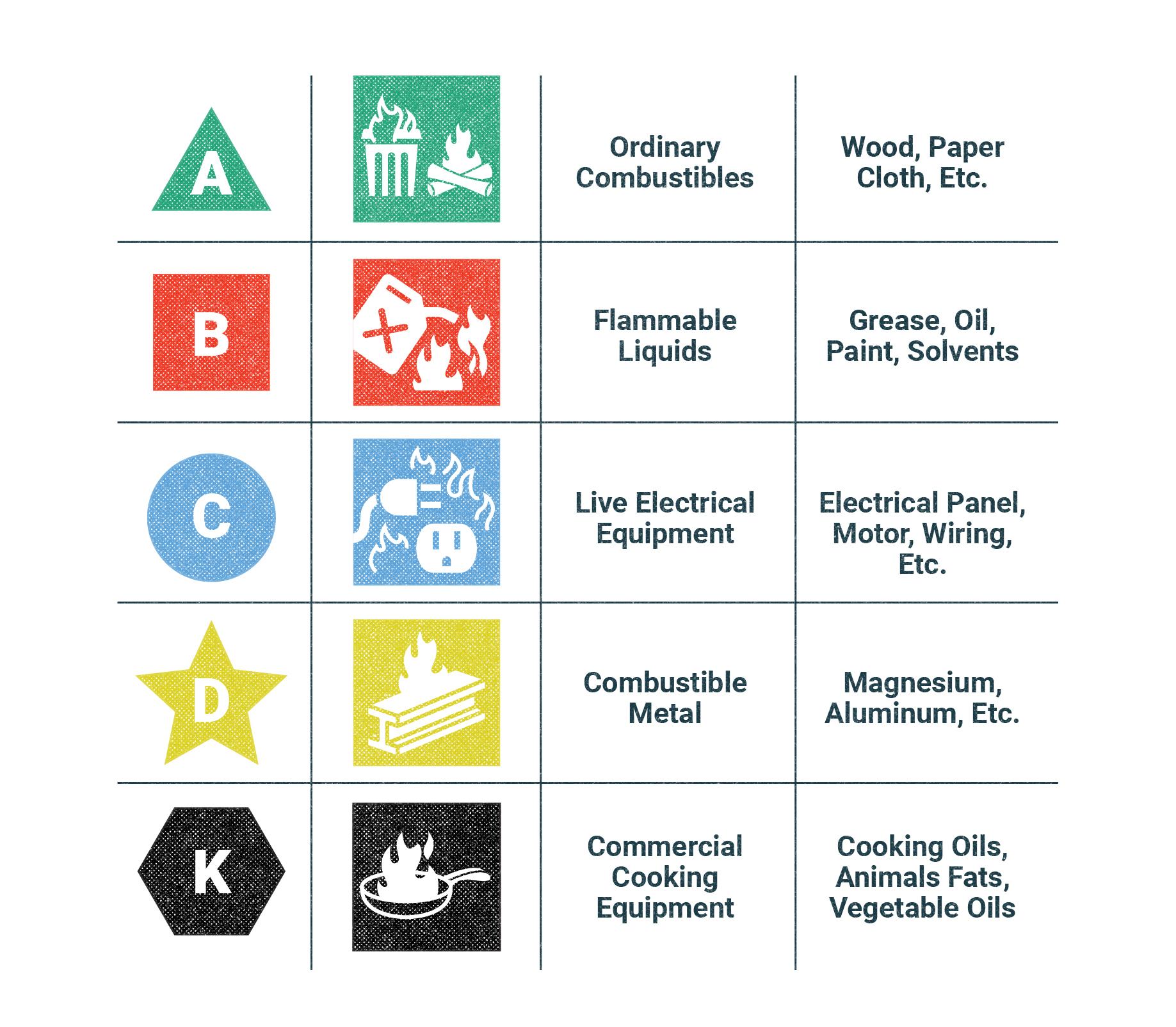
Alt text: A graphic displaying the five types of fire extinguishers and what they mean. Class A: solid materials such as wood or paper, fabric, and some plastics. Class B: liquids or gas such as alcohol, ether, gasoline, or grease. Class C: electrical failure from appliances, electronic equipment, and wiring. Class D: metallic substances such as sodium, titanium, zirconium, or magnesium. Class K: grease or oil fires specifically from cooking.
Fires are classified into different categories based on the type of fuel involved. The classification system helps in understanding the nature of the fire and determining the appropriate firefighting methods and extinguishing agents to be used. The most commonly used classification system is the one developed by the National Fire Protection Association (NFPA) in the U.S., which categorizes fires into five classes (O’Connor, 2023):
Class A Fires: Class A fires involve ordinary combustible materials, such as wood, paper, cloth, rubber, and some plastics. These fires typically leave behind ash after combustion. Class A fires are extinguished using water, which cools the fuel and removes heat from the fire triangle.
Class B Fires: Class B fires involve flammable liquids or gases, such as gasoline, oil, grease, propane, butane, and certain paints and solvents. These fires are characterized by their ability to spread rapidly and may produce large flames or explosive conditions. Class B fires are extinguished using foam, carbon dioxide, or dry chemical agents that smother the fire and eliminate the oxygen supply.
Flammable liquid , a flammable liquid is any liquid having a flashpoint at or below 199.4 °F (93 °C) is any liquid having a flashpoint at or below 199.4 °F (93 °C).
As per its standard on flammable liquids (OSHA, 1970a), the OSHA Office of Training and Education (n.d.) emphasizes that:
It should be mentioned that flash point was selected as the basis for classification of flammable liquids because it is directly related to a liquid’s ability to generate vapor, i.e., its volatility. Since it is the vapor of the liquid, not the liquid itself, that burns, vapor generation becomes the primary factor in determining the fire hazard. (p. 3)
Class C Fires: Class C fires involve energized electrical equipment, such as electrical appliances, wiring, and circuit breakers. The key hazard in these fires is the risk of electrical shock rather than the actual burning of materials. It is important to note that water should never be used to extinguish class C fires, as it conducts electricity and can lead to electrocution. Class C fires are extinguished using dry chemical agents or carbon dioxide, which do not conduct electricity.
Class D Fires: Class D fires involve combustible metals, such as magnesium, titanium, potassium, sodium, and certain types of powdered metals. These fires require specialized extinguishing agents, such as dry powder extinguishing agents specifically designed for use on metal fires. Water, foam, or carbon dioxide should not be used to extinguish class D fires, as they can react with the metal and potentially exacerbate the fire.
Class K Fires: Class K fires are found primarily in commercial kitchens. The use of high temperature cooking oils creates a unique environment, which requires this classification. This classification of fire also has a unique fire extinguisher. They use a fine wet mist consisting of an alkaline mixture, such as potassium acetate, potassium carbonate, or potassium citrate, that forms a soapy foam as it is applied to the cooking oil or other substance. Class K fires should only be extinguished with Class K extinguishers and should never be sprayed with water as this can increase the spread of the cooking liquids.
2.4 Fire Extinguishers
A fire extinguisher is a handheld device that is used to extinguish or control small fires. They are usually filled with a dry or wet chemical. The six main types of fire extinguishers are water, foam, CO2, powder, water mist, and wet chemicals.
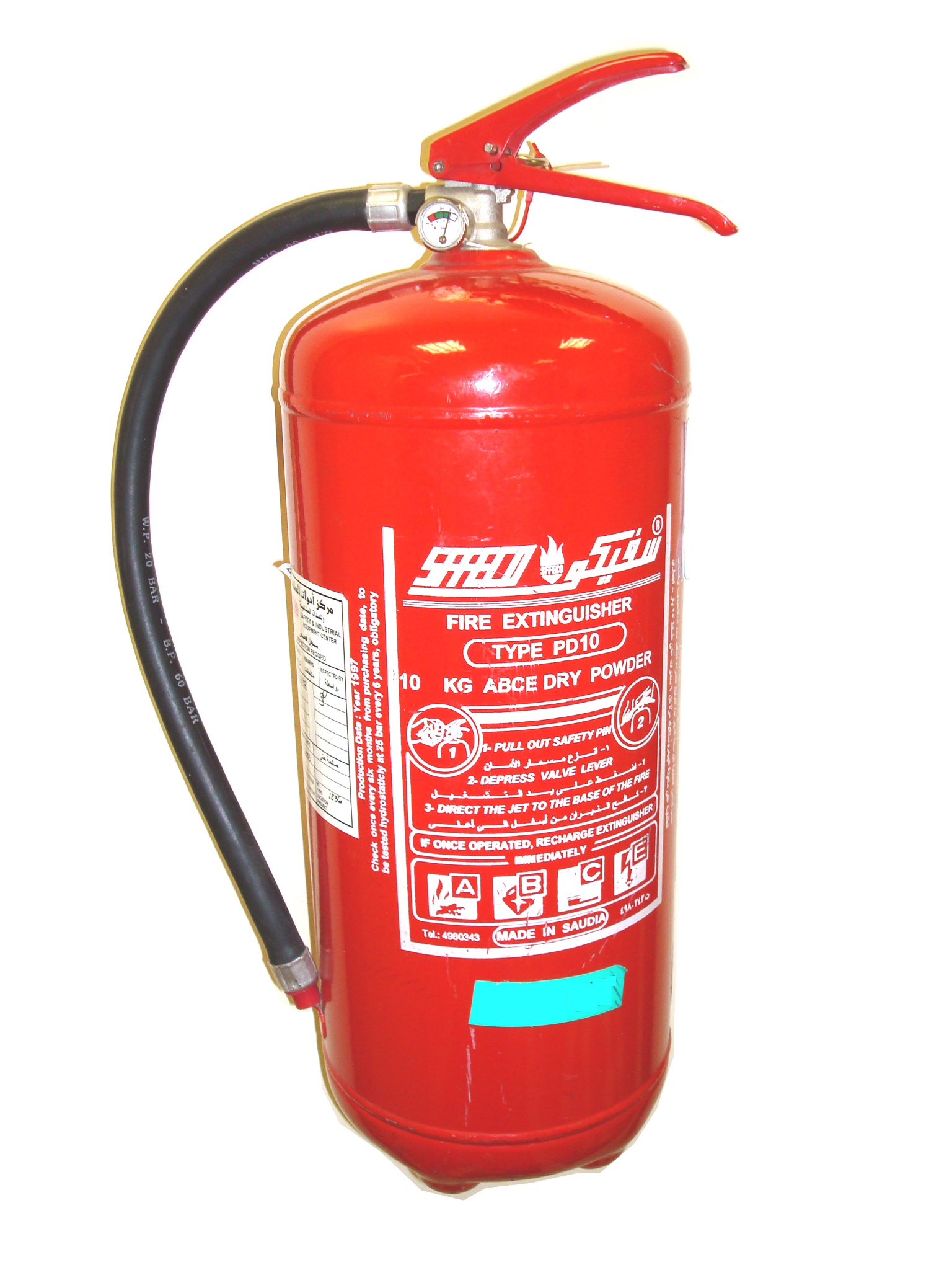
2.4.1 When to use a Fire Extinguisher
Below is safety advice about when to use a fire extinguisher (Bellingham Fire Prevention Bureau, n.d.).
2.4.2 How to Operate a Fire Extinguisher
This is advice for how to operate a fire extinguisher (Bellingham Fire Prevention Bureau, n.d.).
You should fight a fire with a fire extinguisher only when all the following are true:
- The fire department is being called. (9-1-1)
- The building is being evacuated. Activate fire alarm, if available.
- The fire is small and confined to the immediate areas where it started, such as in a wastebasket, cushion, small appliance, stove, etc.
- You can fight the fire with your back to a safe exit/escape route.
- Your extinguisher is rated for the type of fire you are fighting, is in good working order, and you already know how to operate it.
- You have had training in how to use the extinguisher and are confident that you can operate it effectively.
If any of these are not true, get out immediately and dial 9-1-1. (paras. 20-22)
2.5 Personal Protective Equipment
Personal protective equipment (PPE) is protective clothing or equipment that protects the wearer against injury. PPE is the last line of defense from injury when all other options have been exhausted. Before selecting PPE for protection, the hazard must be evaluated for possible controls. The hierarchy of controls for hazards are; elimination, substitution, engineering controls, administrative controls, and then PPE.
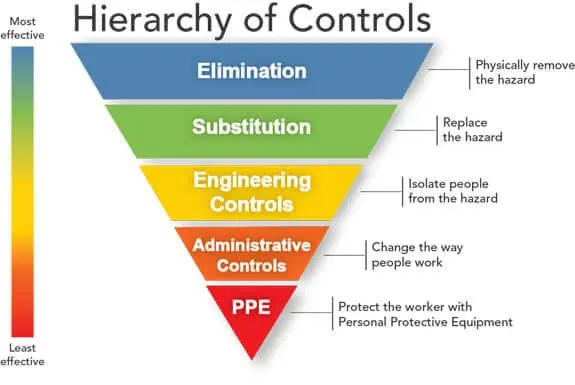
Consider workers who operate rotating equipment such as manual lathes and milling machines. One of the hazards associated with the operation of this equipment is the creation of hot and sharp metal chips caused by the cutting process. Can this hazard be eliminated from the process? If so, use that method. If not, proceed to substitution. Can another process be used that has fewer hazards? Has a new process been created that may be used in place of the current process? 3D printing and other additive methods do not have the same hazards. Next is engineering controls; can we isolate the worker from the hazards? CNC lathe and milling centers do this by creating an enclosure around the cutting operation, which solves the problem. However, this is not feasible for small quantities or repair operations. Administrative controls are processes tailored to reduce injuries. These are often referred to as best practices, and they vary from shop to shop. Using rough cutting passes on the mill, which sends the chips away from the operator, is a good best practice if possible.
Finally, we get to PPE. For all the hazards that have progressed through our efforts at mitigation, we must find equipment or clothing to protect the operator. The list of PPE for manual lathes and mills includes:
- Machine Shields to intercept chips coming off the cutter.
- Face shields
- Eye protection
- Cotton clothing to protect skin
Let’s take a look at PPE commonly used in the machining industry.
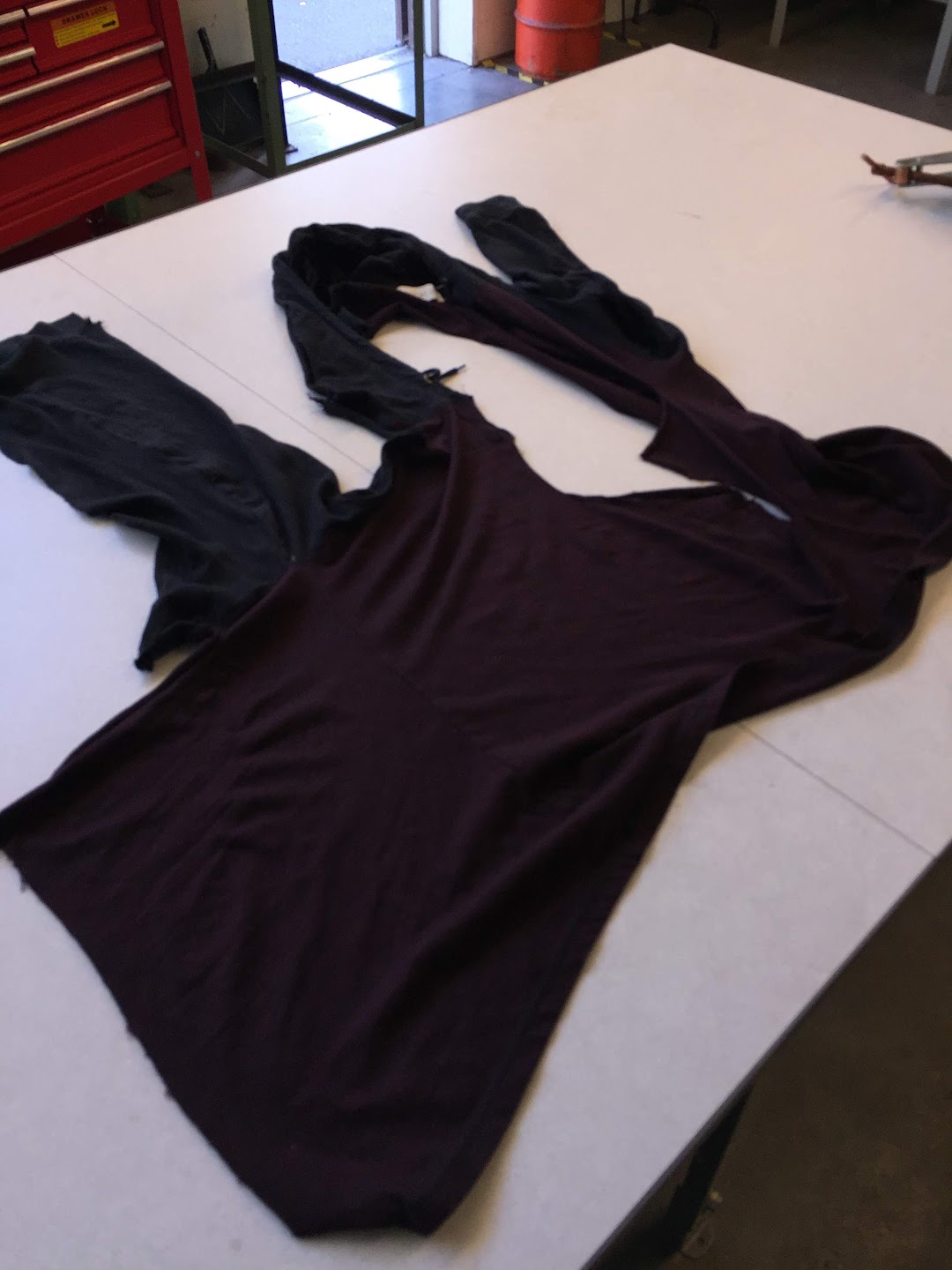
2.5.1 Clothing
What you wear in a machine shop impacts your safety. Long sleeves and loose fitting clothes found on most “hoodies” present the hazard of getting the clothes caught in the rotating assemblies of equipment and pulling you into the rotating mechanisms.
In the image above, a shirt sleeve caught in the knurling of a part being turned on the lathe. The garment quickly wrapped around the part, and the lathe’s powerful motor tore the shirt off the operator as he braced himself against the machine.
To prevent getting caught in the rotating assemblies of machines, roll sleeves above the elbow, and do not wear gloves while operating equipment. Remove jewelry from around your neck, wrists, and hands. Tie long hair up and away from the front of your body.
Synthetic materials such as nylon and polyester will melt when in contact with hot metal chips formed during cutting processes. Cotton is a better choice when selecting work clothes for the machinist. A close fitting neck will also aid in preventing hot chips from contacting your neck and causing burns.
Wearing the correct footwear will protect you from several hazards, such as dropping materials on your feet, slipping on oil spills, and preventing hot metal chips from imbedding in the soles of your shoes. Some shops will require steel toes, and they may offer to supplement the purchase. Leather is the best choice of shoe material, and an oil non-slip sole will help you avoid losing your footing when walking in slippery areas.
Synthetic materials found in shoes should be avoided due to the hot nature of chips that melt the materials. For convenience, an operator will often bring a second pair of shoes/boots to work to change into before heading home after work. Metal chips get embedded in the soles of your footwear and can cause damage to nice flooring found in most homes.
2.5.2 Hearing Protection
When choosing hearing protection, you should consider the following:
- Noise Reduction Rating (NRR) which determines the device’s ability to reduce sound exposure.
- Comfort. Hearing protection that isn’t comfortable will most likely not be worn.
- Style. Ear plugs, which come in several varieties, or muffs, which fit over the ears. These can be combined to reduce sound levels further.
Noise Reduction Rating (NRR) is a measure of the effectiveness of a hearing protection device to reduce noise levels. Higher values indicate greater noise reduction. NRR values range up to approximately 30 dB.
Technology has made advancements in noise canceling devices that only filter out background noise and permit conversational sound through. These devices may reduce some noise, but only approved hearing protection that is certified to use a NRR should be used.
The primary OSHA standard related to hearing protection is titled “Occupational Noise Exposure” (1970b). Here are some key provisions of the standard:
Permissible Exposure Limit (PEL): The PEL for occupational noise exposure is 90 decibels (dBA) as an 8-hour time-weighted average (TWA). This means that over the course of an 8-hour work shift, employees should not be exposed to noise levels exceeding 90 dBA. If noise levels exceed this limit, employers must take action to reduce noise exposure.
Action Levels: OSHA has defined two action levels:
- 85 dBA: When employee noise exposures reach or exceed 85 dBA as an 8-hour TWA, employers are required to implement a hearing conservation program.
- 90 dBA: If noise exposures exceed 90 dBA as an 8-hour TWA, more stringent requirements apply for the hearing conservation program. 140 dBA: Exposure to noise greater than 140 dBA can cause permanent hearing loss.
Hearing Conservation Program: Employers are required to establish and maintain a hearing conservation program whenever employees are exposed to noise levels at or above the action level. The program includes noise monitoring, annual audiometric testing for exposed employees, the provision of hearing protection devices (HPDs), employee training, and recordkeeping.
Hearing Protection Devices (HPDs): When noise exposures exceed the PEL or action level, employers must provide suitable hearing protection devices (e.g., earplugs or earmuffs) to affected employees. The employer is responsible for ensuring the proper use and maintenance of the hearing protection provided.
Employee Training: Employers must provide training to employees exposed to high noise levels. Training should cover the risks of noise exposure, proper use of hearing protection, the purpose and procedures of audiometric testing, and other relevant information.
Audiometric Testing: Employers are required to provide free annual audiometric testing to employees exposed to noise levels at or above the action level. Audiometric testing is used to monitor changes in hearing and identify any potential hearing loss.
2.5.3 Health Effects of Excessive Noise Exposure.
Excessive noise exposure can have a range of negative health effects on both physical and mental well-being. The effects can vary depending on the intensity, duration, and frequency of the noise exposure, as well as individual susceptibility. Some of the health effects of excessive noise exposure include:
Hearing Loss: Prolonged exposure to loud noises, especially those above 85 decibels (dB), can lead to permanent hearing loss. This is often gradual and cumulative, affecting the ability to hear high-frequency sounds.
Tinnitus: Excessive noise exposure can lead to tinnitus, which is the perception of ringing, buzzing, or hissing sounds in the ears. It can be temporary or chronic and can significantly affect quality of life.
Stress and Anxiety: Noise pollution can cause chronic stress and anxiety, which are associated with an increased risk of cardiovascular diseases, high blood pressure, and other stress-related health issues.
Sleep Disturbances: Noisy environments can interfere with sleep, leading to difficulties falling asleep, staying asleep, or experiencing restorative sleep. This can result in fatigue, impaired cognitive function, and an overall reduced quality of life.
Cardiovascular Issues: Chronic noise exposure, particularly to loud and persistent noises, has been linked to an increased risk of cardiovascular problems such as hypertension, heart disease, and stroke.
Cognitive Impairment: Noise pollution can impair cognitive function and concentration. It may lead to reduced attention spans, learning difficulties, and decreased performance in tasks that require focus.
Social Isolation: High noise levels can lead to social isolation and communication difficulties, as people may avoid noisy areas or situations where conversation is challenging.
Workplace Safety: In workplaces with high noise levels, employees are at risk of occupational hearing loss. Furthermore, noise can reduce workers’ awareness of their surroundings, leading to safety hazards.
Annoyance: Excessive noise can cause annoyance and dissatisfaction, impacting overall well-being and mental health.
It’s important to note that the impact of noise exposure varies depending on individual susceptibility, age, and health status. To mitigate the health effects of excessive noise exposure, individuals can take measures such as using ear protection in noisy environments, limiting exposure to loud noises, and advocating for noise reduction in communities. Public health policies and regulations related to noise control and urban planning can also play a crucial role in reducing noise pollution and its associated health impacts.
2.5.4 Respirator Protection
The OSHA respiratory protection standard (1970d) is designed to protect workers from harmful airborne contaminants and ensure the proper use of respirators when necessary.
Here are some key elements of respiratory protection regulations:
Written Respiratory Protection Program: Employers must develop and implement a written respiratory protection program when respirator use is required in the workplace. This program should outline the procedures and policies related to respirator selection, fit-testing, medical evaluations, training, and maintenance.
Respirator Selection: Employers must ensure that the appropriate type of respirator is selected for the specific hazards present in the workplace. Different types of respirators (e.g., filtering facepiece respirators, half-face respirators, full-face respirators, and powered air-purifying respirators) may be necessary based on the nature of the airborne contaminants.
Fit Testing: Employees required to use respirators must undergo fit testing to ensure that the respirator fits properly and forms an effective seal on their face. Fit testing should be conducted before the initial use of the respirator and at least annually thereafter.
Medical Evaluations: Workers who are required to wear respirators must undergo a medical evaluation to determine if they are physically capable of using a respirator safely. This evaluation should be performed by a licensed healthcare professional.
Training: Employers must provide comprehensive training to employees who use respirators. The training should cover topics such as the proper use, limitations, and maintenance of respirators, as well as the potential health hazards associated with workplace contaminants.
Maintenance and Cleaning: Employers are responsible for ensuring that respirators are maintained in a clean and sanitary condition. Respirators should be inspected regularly, and any damaged or malfunctioning respirators should be removed from service.
Voluntary Use of Respirators: If employees choose to wear respirators voluntarily (when not required by the employer), certain requirements still apply, and the employer should provide information and training on the proper use and limitations of such respirators.
It’s important to note that respiratory protection regulations may be updated or revised over time, so employers in each state should regularly check the state’s Department of Labor & Industries website for the most current and specific requirements related to respiratory protection. Additionally, employers should always follow federal OSHA standards in addition to any state-specific regulations.
2.5.5 Health Effects of Respiratory Hazards
Respiratory hazards are substances or conditions that can negatively impact the respiratory system, leading to a range of health effects. These hazards can be present in various environments, including workplaces, homes, and outdoor spaces. The health effects of respiratory hazards can vary depending on the type of hazard, the duration of exposure, and individual susceptibility. Here are some common respiratory hazards and their associated health effects:
Airborne Particulate Matter: Fine particles and dust present in the air can be inhaled into the respiratory system. Prolonged exposure to high levels of particulate matter is linked to respiratory conditions such as bronchitis, aggravated asthma, decreased lung function, and an increased risk of respiratory infections.
Chemical Fumes and Vapors: Inhalation of harmful chemicals and gases, such as volatile organic compounds (VOCs), solvents, and industrial emissions, can cause irritation of the respiratory tract, lung inflammation, and exacerbation of respiratory conditions like asthma and chronic obstructive pulmonary disease (COPD).
Occupational Hazards: Workers in certain industries may be exposed to respiratory hazards like asbestos, silica dust, and other harmful substances. Prolonged exposure to these hazards can lead to occupational lung diseases such as asbestosis and silicosis.
Outdoor Air Pollution: Exposure to high levels of outdoor air pollutants like ozone, nitrogen dioxide, sulfur dioxide, and carbon monoxide can lead to respiratory irritation, worsened asthma symptoms, decreased lung function, and an increased risk of respiratory infections.
Respiratory Infections: Exposure to respiratory hazards can weaken the immune system’s defenses, making individuals more susceptible to infections such as pneumonia, bronchitis, and influenza.
Aspiration Hazards: Inhaling food, liquids, or foreign objects into the respiratory tract (aspiration) can lead to respiratory distress and infections like aspiration pneumonia.
Radon Gas: Radon is a radioactive gas that can accumulate in homes and buildings. Prolonged exposure to high levels of radon is a significant risk factor for lung cancer.
It’s important to address and mitigate respiratory hazards to protect respiratory health. This can be done through measures such as proper ventilation, the use of personal protective equipment, avoiding smoking and exposure to secondhand smoke, and minimizing exposure to pollutants and allergens. In occupational settings, following safety guidelines, implementing proper ventilation systems, and providing appropriate protective gear are essential to preventing respiratory hazards.
2.5.6 Dust Mask Respirator
Dust masks are flexible paper pads held over the nose and mouth by elastic or rubber straps for personal comfort against non-toxic nuisance dust. They are not intended to provide protection from toxic airborne hazards.
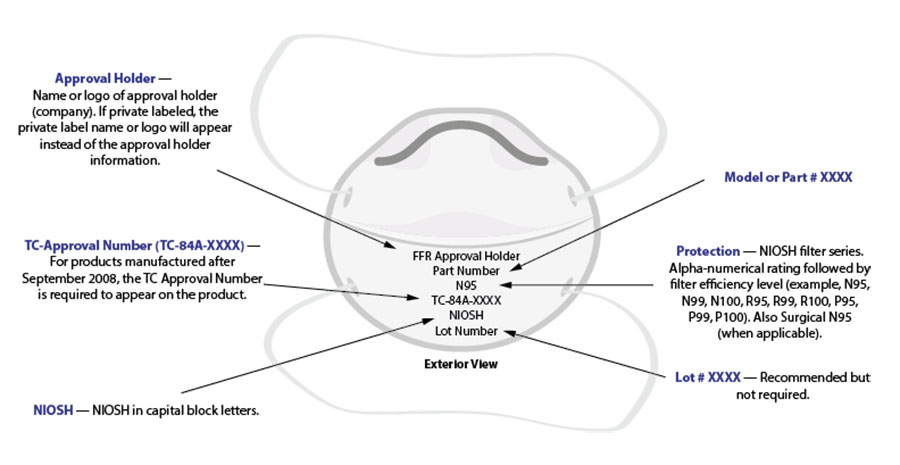
When selecting a respirator, be aware of the filtering efficiency of the mask. Quality masks are N95 rated to remove at least 95% of airborne particles when properly fitted (National Institute for Occupational Safety and Health, 2021).
If 95% filtration is all you need, the above respirator is fine. However, if you need 100% protection you must use a respirator that fits snugly on your face and permits a clean seal. These masks come in ¼ face and full face. They accept disposable cartridges designed to remove specific contaminants from the air. If your job requires this type of respirator, you will be fitted by a specialist to ensure the fit is correct.
These permit not only the removal of dust particles but also certain chemicals and gases that purify the air before respiration.
These types of respirators only filter the air; they do not supply breathable air. If the space in which you are working does not have sufficient air, you must use a forced respirator with its own air source. These types are beyond the scope of this text.
2.5.7 Eye Protection
The OSHA eye protection standard (1970c), and incorporates these requirements into its own state regulations.
Here are the key elements of the eye protection standards:
Eye Protection Requirements: Employers are required to assess the workplace for potential eye hazards and provide appropriate eye protection to employees where there is a risk of eye injury. Eye protection must be provided free of charge to affected workers.
Selection of Eye Protection: Employers should select eye protection devices, such as safety glasses, goggles, face shields, or full-face respirators with built-in eye protection, based on the specific hazards present in the workplace. The chosen eye protection should be suitable for the identified hazards.
Use of Eye Protection: Employees must wear the provided eye protection whenever they are exposed to potential eye hazards. Eye protection should be worn in designated areas or during specific tasks where eye injuries are likely to occur.
Training: Employers must provide training to employees on the proper use, maintenance, and limitations of the eye protection provided. Employees should understand how to wear, adjust, and clean eye protection for maximum effectiveness.
Maintenance and Replacement: Employers are responsible for ensuring that eye protection devices are maintained in good condition. Damaged or worn-out eye protection should be replaced promptly to ensure continued safety.
Emergency Eyewash and Shower Stations: If workers are exposed to corrosive substances or hazardous chemicals that can cause eye injuries, the employer should provide accessible emergency eyewash stations and safety showers.
Prescription Eyewear: If an employee requires prescription eyewear, the employer must ensure that the eye protection is capable of accommodating the prescription lenses or provide the necessary eye protection that incorporates the prescription.
Voluntary Use of Eye Protection: If employees choose to wear eye protection voluntarily (when not required by the employer), certain requirements may still apply, and the employer should provide information and training on the proper use and limitations of such eye protection.
It’s essential for employers to comply with these eye protection standards to prevent eye injuries and maintain a safe work environment. Employers should regularly review and update their eye protection program as needed, and employees should be informed and trained on the proper use and care of eye protection devices.
2.5.8 American National Standard for Occupational and Educational Personal Eye and Face Protection Devices
The American National Standards Institute, ANSI is a private, non-profit organization that oversees the development and implementation of voluntary consensus standards for various industries and sectors in the U.S. The standard for eye protection is the ANSI Z87.1 standard, titled “American National Standard for Occupational and Educational Personal Eye and Face Protection Devices.”
The ANSI Z87.1 standard establishes the requirements and performance criteria for eye and face protection devices used in occupational and educational settings (Kelechava, 2020). It covers a wide range of protective equipment, including safety glasses, goggles, face shields, and welding helmets. When purchasing safety glasses, ensure the “ANSI Z87.1” standard is printed on the glasses.
Key aspects covered by the ANSI Z87.1 standard include:
Impact Resistance: Eye protection devices must be capable of withstanding high-velocity impacts from flying objects or particles, protecting the eyes from potential injuries.
Optical Quality: The standard specifies optical requirements to ensure clear vision and minimal distortion through the protective lenses.
Lens Marking: The eye protection devices should be permanently marked with specific information, such as the manufacturer’s identification, lens type (e.g., basic impact, high impact, welding filter), and any additional markings indicating compliance with specific tests.
Face Shield Performance: For face shields, the standard sets requirements for coverage, thickness, and resistance to penetration and ignition.
UV Protection: The ANSI Z87.1 standard includes requirements for providing adequate protection against ultraviolet (UV) radiation.
Splash and Dust Protection: The standard addresses the performance of eye protection devices against liquid splashes and dust particles.
Flammability Resistance: Certain eye protection devices are tested for their resistance to ignition and flame spread.
Compliance with the ANSI Z87.1 standard ensures that eye protection devices meet specific performance and safety criteria, making them suitable for protecting against various workplace hazards. Employers should choose eye protection products that are ANSI Z87.1-compliant and provide proper training to employees on their correct use and maintenance.
2.5.9 Health Effects of Eye Hazards
Eye hazards can lead to a range of health effects, varying in severity from minor irritation to permanent damage. These hazards can arise from exposure to various substances, conditions, or activities that can harm the eyes. It’s important to protect your eyes from potential hazards to prevent these negative outcomes. Here are some common eye hazards and their associated health effects:
Chemical Exposure: Contact with corrosive or irritating chemicals, such as acids, alkalis, solvents, and cleaning agents, can cause eye irritation, redness, tearing, and even chemical burns. Severe chemical exposure can lead to permanent damage, vision loss, or blindness.
Foreign Objects: Particles, debris, or foreign objects like dust, wood chips, metal shavings, and grit can get into the eyes, causing discomfort, redness, pain, and potential damage. In some cases, foreign objects can scratch the cornea, leading to infection and impaired vision.
Sharp Objects: Accidents involving sharp objects like knives, shards of glass, or other sharp tools can cause cuts or punctures to the eye, leading to potential infections and damage to the eye’s structures.
Particulate Matter: Dust, sand, or other airborne particles can irritate the eyes and cause discomfort, redness, and tearing. Prolonged exposure to particulate matter may lead to chronic irritation and dry eyes.
Physical Impact: Accidental impact to the eye, such as a blow, can result in eye trauma, bruising, swelling, and potential damage to the eye’s structures.
It’s crucial to take appropriate precautions to protect your eyes from potential hazards. This includes wearing appropriate eye protection, such as safety goggles, face shields, or helmets with protective visors, when working in hazardous environments or participating in activities with potential eye risks. Regular eye check-ups and prompt medical attention following any eye injury are essential to ensure early detection and proper treatment of eye-related health issues.
2.6 Common Machine Shop Hazards
Machine shop hazards are related to the many processes used within the shop. For a better understanding of the common shop hazards, let’s list them by processes. We will list common machine shop processes and the hazards associated with them.
2.6.1 Receiving
The receiving clerk must unload the material from large trucks that material vendors have loaded. Stock material often arrives in bar form, with 12 foot lengths and larger being common. Bars are usually strapped together with metal bands, which prevent the load from shifting during transit. Depending on how the stock material was cut at the vendor, there may be sharp edges on the ends of the stock. When handling material, it is useful to have a pair of gloves to protect your hands from cuts due to sharp edges. The banks used to bind the stock are cut with snips, and these cut edges are very sharp. To mitigate the hazards from the sharp band edges, all banding should be gathered up and disposed of once the band has been cut.
Another hazard associated with managing materials is the weight involved with the quantities handled at a machine shop. When handling heavy materials, you must always be aware of falling objects.
2.6.2 Cutting
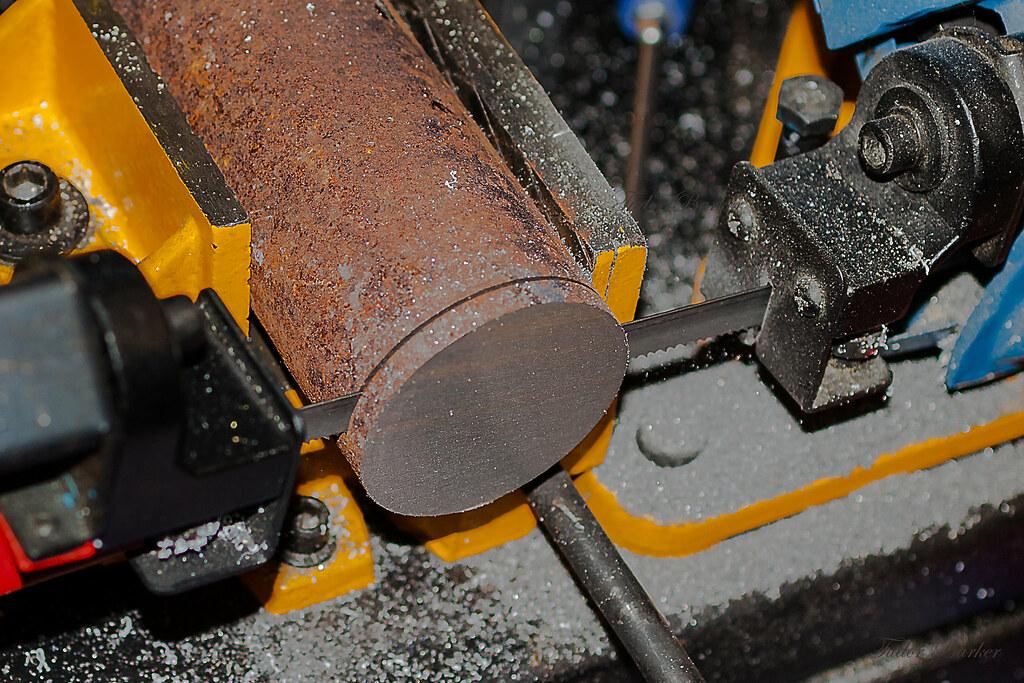
The need to cut stock to length creates many hazards. The band saw is the primary cutting tool used due to the saw’s ability to cut many different materials. Leather work gloves can protect your hands from the sharp edges created by the cutting process. The coolant used to lubricate the cut, as well as the quantity of chips created by the sawing process, can create slip hazards. If your skin is sensitive to cutting fluids, nitrile gloves are a good choice to protect your hands.
The saw stations create “drops”, which are the remnants of the original stock that are too short to be used for the intended purpose. These drops can accumulate and cause tripping hazards. Since stock is usually cut from long lengths, supports are used to align the long stock with the cutting surface. This long, supported stock can encroach on walking areas, creating a striking hazard for distracted workers. To help eliminate this hazard, avoid walking paths if possible when positioning the saw, cordon off the hazard area with flag tape, or at least place a brightly colored flag on the end of the stock to alert workers of the hazard.
2.6.3 Chips, Chips, Chips
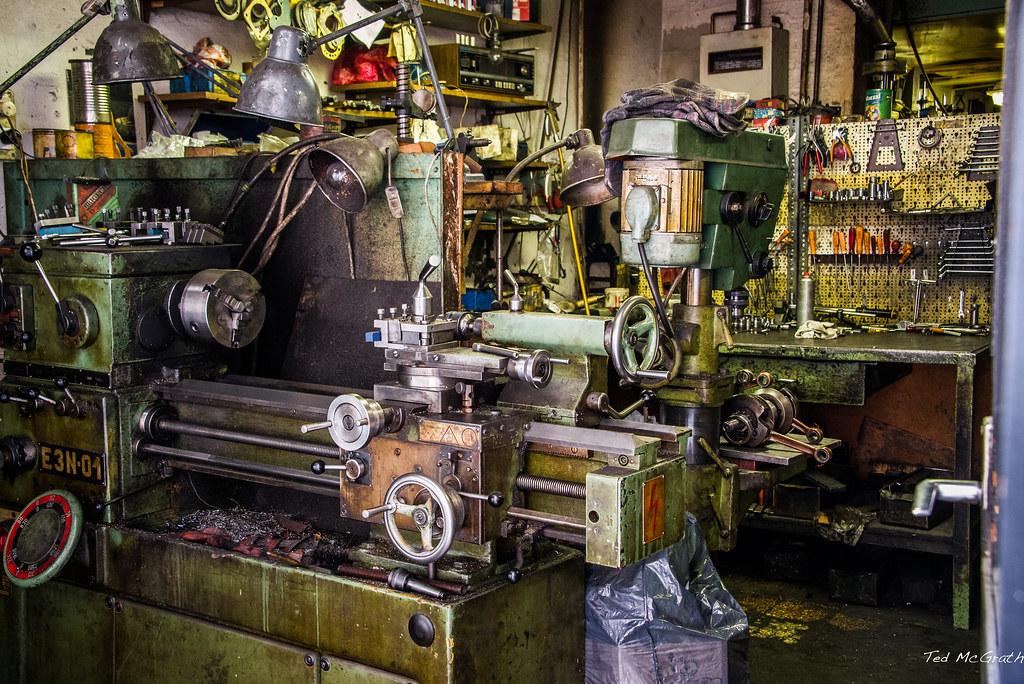
Almost every process of a machine shop generates chips. Chips are the waste product produced from all cutting tools. If it is being cut, there are going to be chips. Our band saws produce chips, and grinders produce chips so small we refer to them as fines. Lathes and mills generate chips, and most of these have coolant on them, so we have to have a process to remove as much coolant as we can from the chips before throwing them away.
Most machine shops try to recoup some cost by recycling all scrap material, which includes chips. Aluminum, steels, brass, magnesium, stainless steel and more all need to be placed into their collection bins. How can this possibly be discussed under safety, you may ask? The common hazards associated with chips are cuts. Secondary hazards associated with chips are trip hazards. Trip hazards are anything that contributes to losing your footing. Losing your footing can contribute to falls, sprains, and impacts with nearby equipment. To combat these hazards caused by the accumulation of chips, it is necessary to practice proper housekeeping. Housekeeping is a term used to express the general attitude of cleanliness around the shop. This may be one of the largest differences between machine shops. There are shops that sweep chips toward one wall and collect them once a week. Some shops have an apprentice whose job it is to clean up these messes. Hopefully, you will find that most machinists clean up after themselves on a regular basis and maintain good housekeeping standards around the shop.
Common shop tools used to maintain chips are brooms of varying sizes, dustpans and brushes. Figure ### demonstrates a shadow board application for managing these tools.
2.6.4 Slip, Trip and Fall
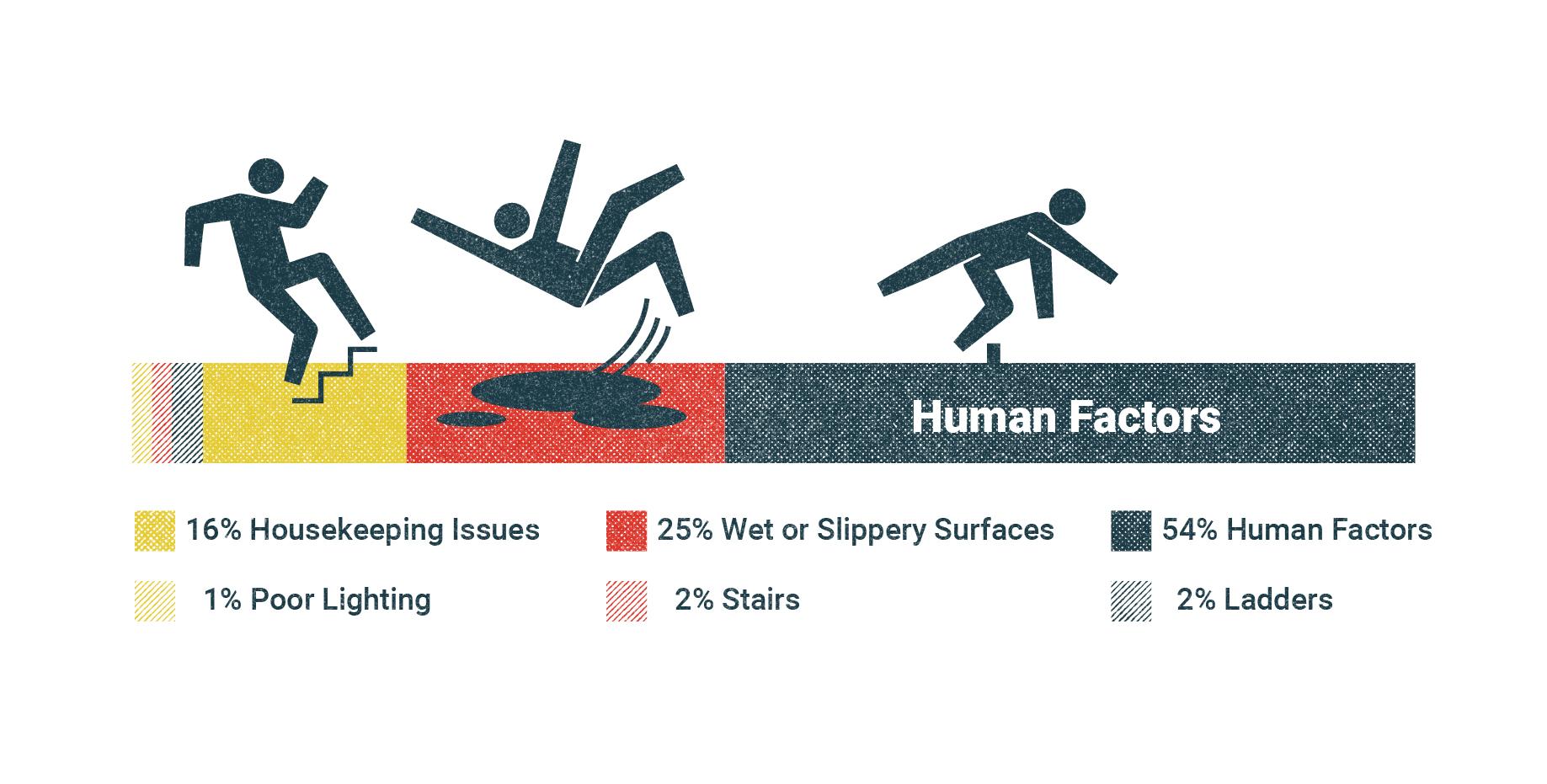
Machine shops create slip trip and fall hazards by poor housekeeping. Spilling coolant or cutting fluid and not cleaning it up will often cause such an incident. Machines use liquids in their normal operation and most of them leak. These leaks, if not attended to, can create puddles that can cause a worker to lose footing and slip. Packing materials, pallets, boxes, banding, and tools which are not properly disposed of or stored properly can create hazards for tripping. Falling is usually the end result of a slip or trip. Workers can easily become distracted during the work day and not notice hazards while walking through a work center. Falling into or onto equipment can cause injury, or falling to the floor and landing hard can break bones and cause lacerations. It is everyone’s responsibility to create and maintain a risk free work environment.
SUMMARY
This chapter discussed the topic of safety from the government agencies that dictate policy to the machinist in a local shop. This depth of explanation provides the machinist with the “why” behind standard operating procedures you will find in the machining industry.
It’s impossible to discuss in detail all the hazards associated with the machining industry; however, you now have a foundation in specific topics to ensure you have a safe experience in the new adventure of machining.
You should be able to handle hazardous materials,including storage and disposal. Knowledge of fire hazards can assist you in identifying and eliminating potential situations that may spark a fire.
The proper implementation of PPE will equip you with an understanding of how to protect yourself against the common hazards found in most machine shops, from eye and ear protection to cuts, trips, and slips.
REVIEW QUESTIONS
- Who is ultimately responsible for your safety in the workplace?
- What federal agency enforces safety standards within the workplace?
- Which state entity investigates complaints related to labor law violations, such as wage theft, workplace discrimination, and other unfair labor practices?
- What is a best practice for treating an unknown liquid?
- Which SDS component relates to how to contain and clean up spills?
- What is the primary hazard from a class C fire?
- Explain PPE worn while operating a milling machine?
- When is double hearing protection necessary?
- When would you NOT use gloves in the machining environment?
- What MUST always be worn in addition to a face shield?
- How does good housekeeping promote safety?
References
Bellingham Fire Prevention Bureau. (n.d.). Fire extinguishers. City of Bellingham, Washington. Retrieved May 14, 2024, from https://cob.org/services/safety/education-safety/extinguishers
Mobile (2017). Safety Data Sheet (SDS). https://cdn.lubefinder.net/media/attachments/m/o/mobil_vactra_oil_no.2_msds.pdf
Kelechava, B. (2020, April 20). ANSI/ISEA Z87.1-2020: Current standard for safety glasses. American National Standards Institute. Retrieved May 14, 2024, from https://blog.ansi.org/ansi-isea-z87-1-2020-safety-glasses-eye-protection/
National Institute for Occupational Safety and Health. (2021, September 15). NIOSH-approved particulate filtering facepiece respirators. Centers for Disease Control and Prevention, U.S. Department of Health & Human Services. Retrieved May 14, 2024, from https://www.cdc.gov/niosh/npptl/topics/respirators/disp_part/default.html
Occupational Safety and Health Administration. (n.d.). Hazard communication. U.S. Department of Labor. Retrieved May 14, 2024, from https://www.osha.gov/hazcom
Occupational Safety and Health Administration. (2019). Job safety and health. It’s the law! U.S. Department of Labor. https://www.osha.gov/sites/default/files/osha3165-8514.pdf
Occupational Safety and Health Administration. (2022). Commonly used statistics. U.S. Department of Labor. Retrieved May 14, 2024, from https://www.osha.gov/data/commonstats
O’Connor, B. (2023, October 4). Fire extinguisher types. National Fire Protection Agency. Retrieved May 14, 2024, from https://www.nfpa.org/news-blogs-and-articles/blogs/2023/08/01/fire-extinguisher-types
OSHA Office of Training and Education. (n.d.). Flammable and combustible liquids 29 CFR 1910.106 [Handout]. Retrieved May 14, 2024, from http://www.mississippi.edu/rm/downloads/osha_resources/flammable_combustible_liquids.pdf
SafeStart. (2016, May 16). 3 big causes of slips, trips and falls. Retrieved May 5, 2024, from https://safestart.com/news/3-big-causes-slips-trips-and-falls/
United Nations Economic Commission for Europe. (n.d.). About the GHS. Retrieved May 14, 2024, from https://unece.org/about-ghs