7.1 Equipment Used in the Construction Industry
Douglas Rupik, M.Ed., JIW
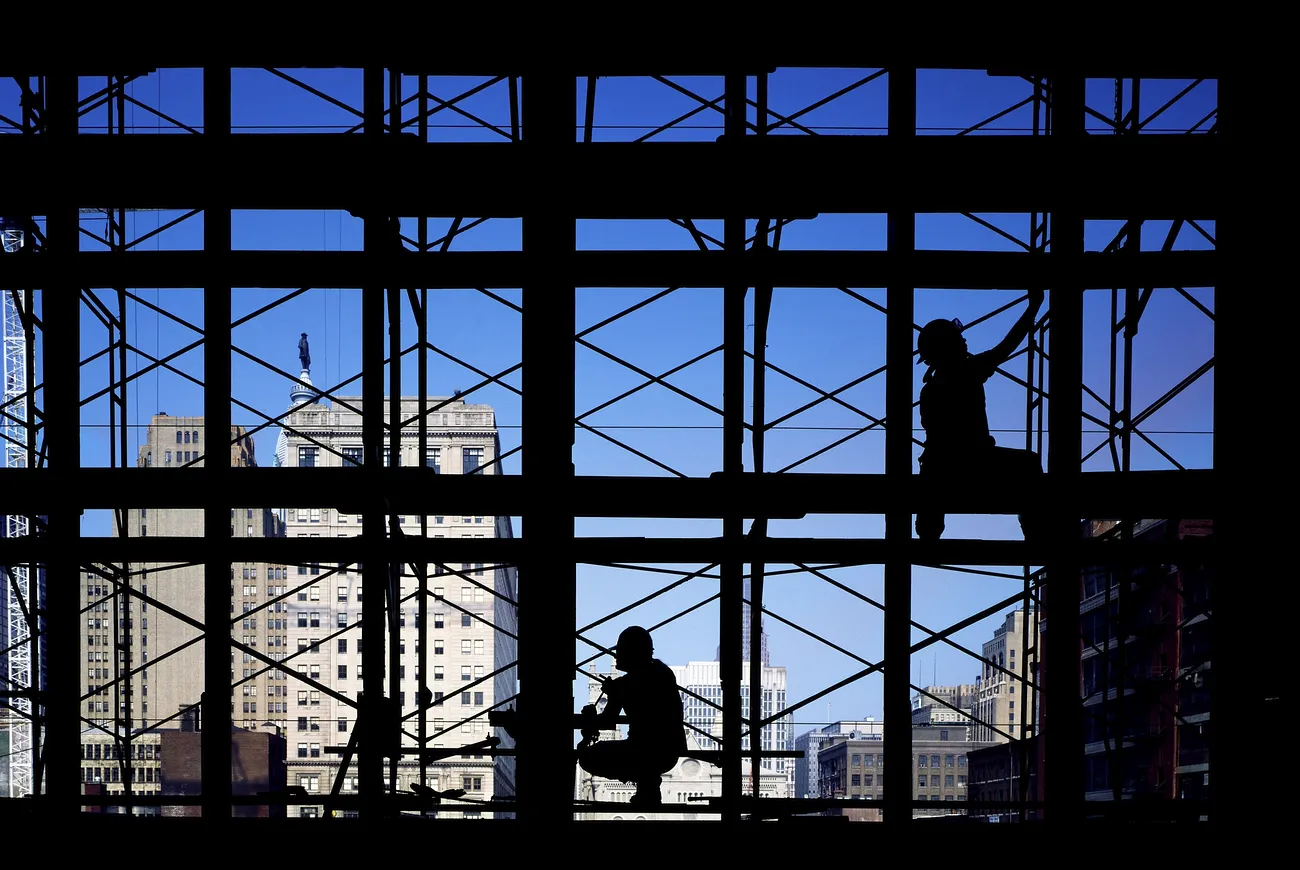
About 10% of welders work in the construction industry (Welder Demographics and Statistics, n.d.). Examples of building and construction trades that are commonly associated with welding are ironworkers; pipefitters, steamfitters, sprinkler fitters, and plumbers; piledrivers; millwrights; and boilermakers. If you pursue a career in construction, you will likely work in all types of weather and have to travel to jobsites. After a time, you will be able to point to different structures and proudly say, “I built that!”
Perhaps what most distinguishes a construction welder from a shop welder is the size of the objects they work on. Bridges and buildings are large and the parts used to build them are large, which means many of the tools used to assemble them are large. Your first time on a construction jobsite may be intimidating, so let’s discuss some of the equipment you may see.
Specialized Tools Used in Construction
Welding in the field usually requires a gas or diesel-powered welder generator rather than a welding machine that plugs into a wall outlet (110V/220V/480V). Flux-cored welding will likely be performed with a voltage-sensing wire feeder in a suitcase box that gets its operating power from the welding current and requires its own ground on the workpiece. Flux-cored welding performed outside will often involve high deposition, self-shielding wire electrodes.
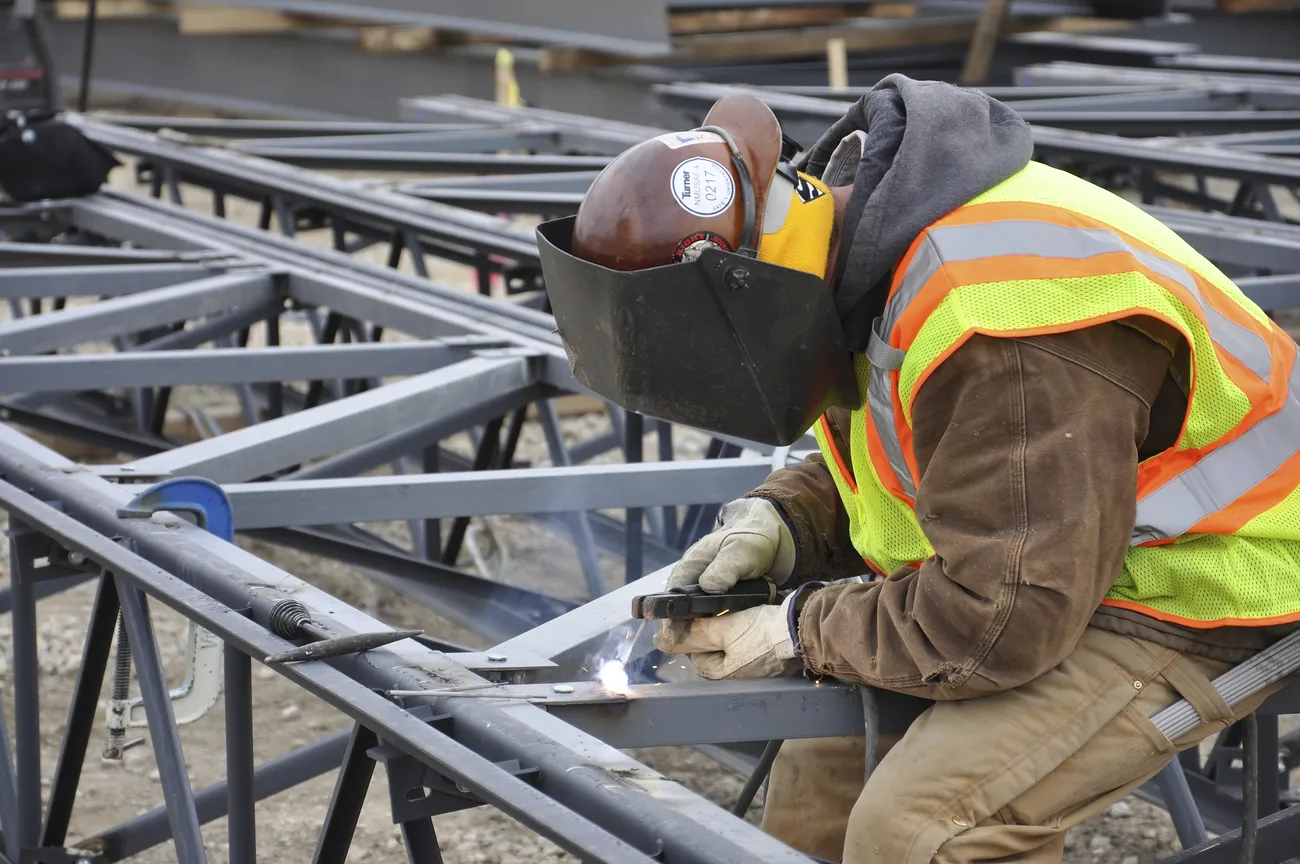
Working in the field will require you to wear several types of protective gear, namely your welding hood over a hard hat using special headgear and, if working at heights, a chinstrap to prevent your hood from dropping in addition to appropriate fall protection that is either engineered (such as guardrails and scaffolding) or a personal fall arrest system, such as a harness with a lanyard or retractable lifeline.
When working outside, you’re exposed to the elements. Dress appropriately for the weather with clothing made of cotton, wool, or other natural fibers. If the conditions include rain, you may work under an umbrella or need rain gear. This is definitely something that must be taken into account when deciding on welding as a career path.
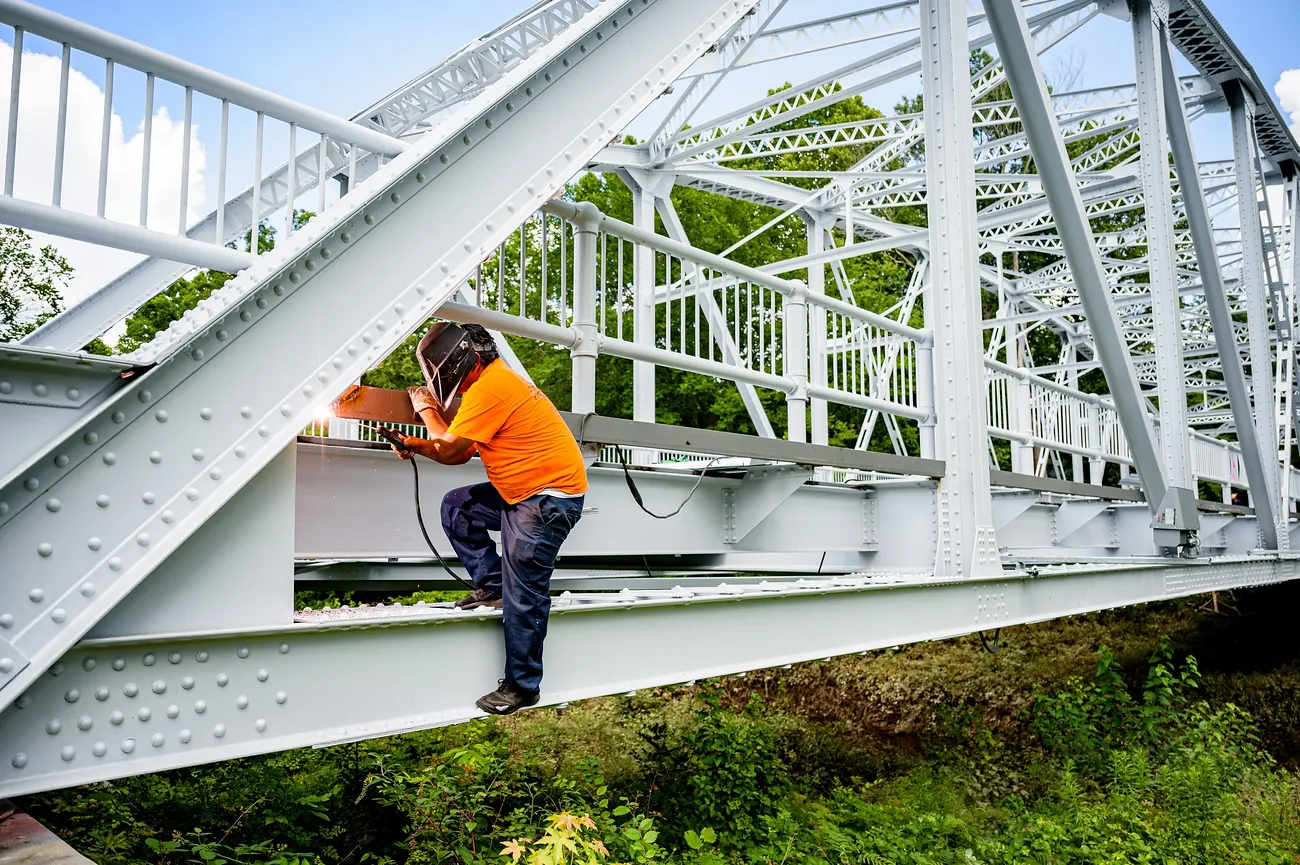
Hoisting and Lifting Equipment
Moving large building materials has been a problem since ancient times. The human figure statues of Easter Island, Stonehenge in England, and the ancient pyramids in Egypt, the Americas, and Asia were all constructed of stone blocks weighing up to several tons each, and we are still not entirely sure of the exact methods used to hoist or lift and transport the largest of these blocks. We do know, however, that wooden cranes powered by people in giant hamster wheel-like contraptions were used in ancient Rome and the Middle Ages in Europe.
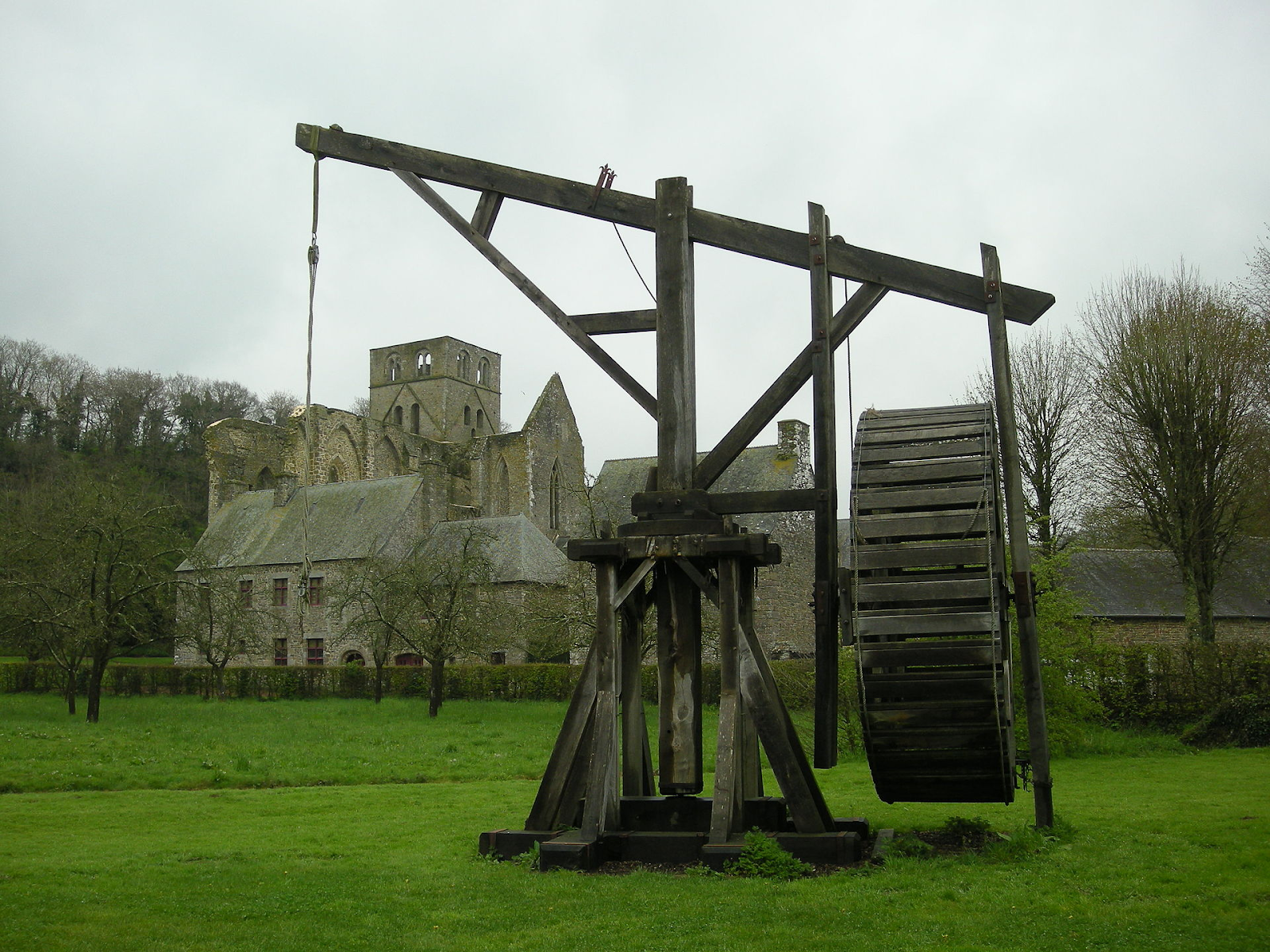
Modern cranes used to hoist heavy materials operate from a similar basic idea, minus the hamster wheel, but are much larger and capable of handling greater weights than their wooden ancestors. The size of the construction project determines the size and style of cranes used.
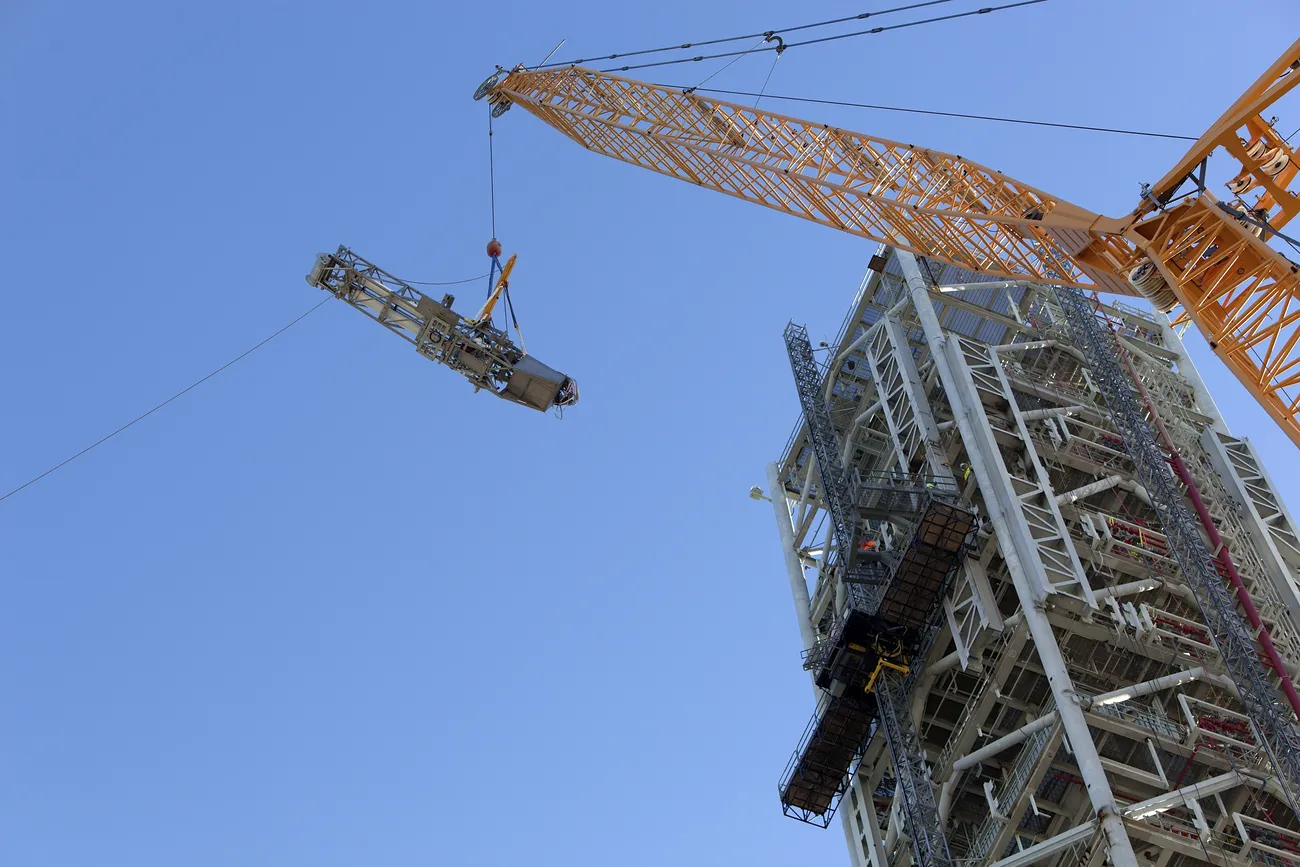
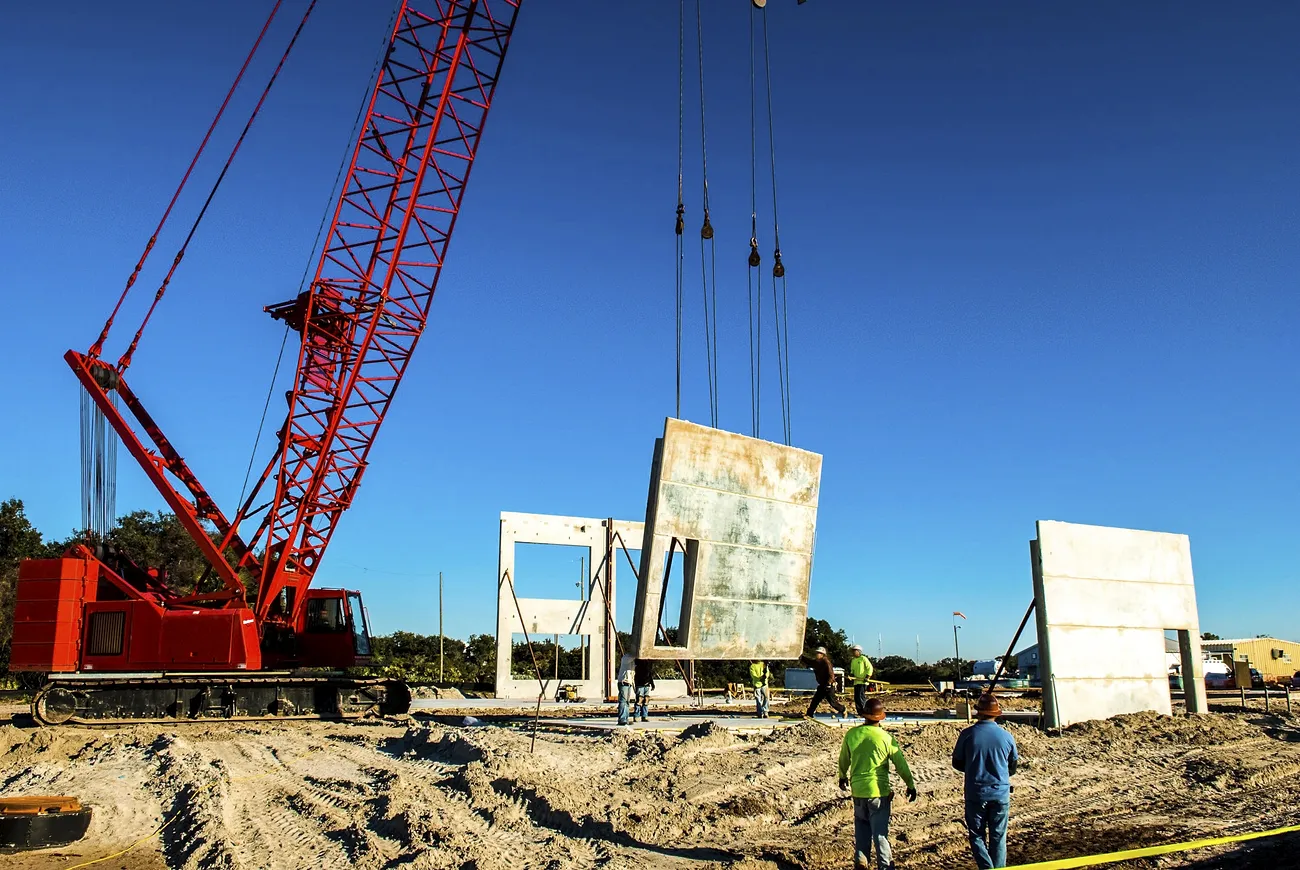
The cranes most likely to be used on the largest of jobsites are tower cranes or ones with lattice booms mounted on crawler treads (like tank treads) or railroad tracks because they have great capacity and reach, both in height and radius, that they can lift materials. These styles of cranes must be trucked to a jobsite in pieces and assembled over days or weeks before they are ready to be used.
Another style of crane uses hydraulic-powered telescoping booms on trucks that can travel on the highway (boom trucks) or have large off-road tires to be capable of all-terrain travel. These may be able to perform lifting when on their tires or, for a greater capacity, can have outriggers installed to stabilize the crane. Their sizes range from just large enough to move a load from the ground to the roof of a single-story building to over 100 feet high.
While operating and working with a crane that is rigging loads may look simple, cranes are dangerous pieces of equipment that require thorough training to use safely. Certifications for operators, signal persons, and riggers require extensive written and practical tests.
Other hoists you may use are winches and chainfalls. Hoists may be secured to an overhead part of the structure you are working on or suspended from a frame called a gantry. Be sure your anchor point is capable of supporting the load.
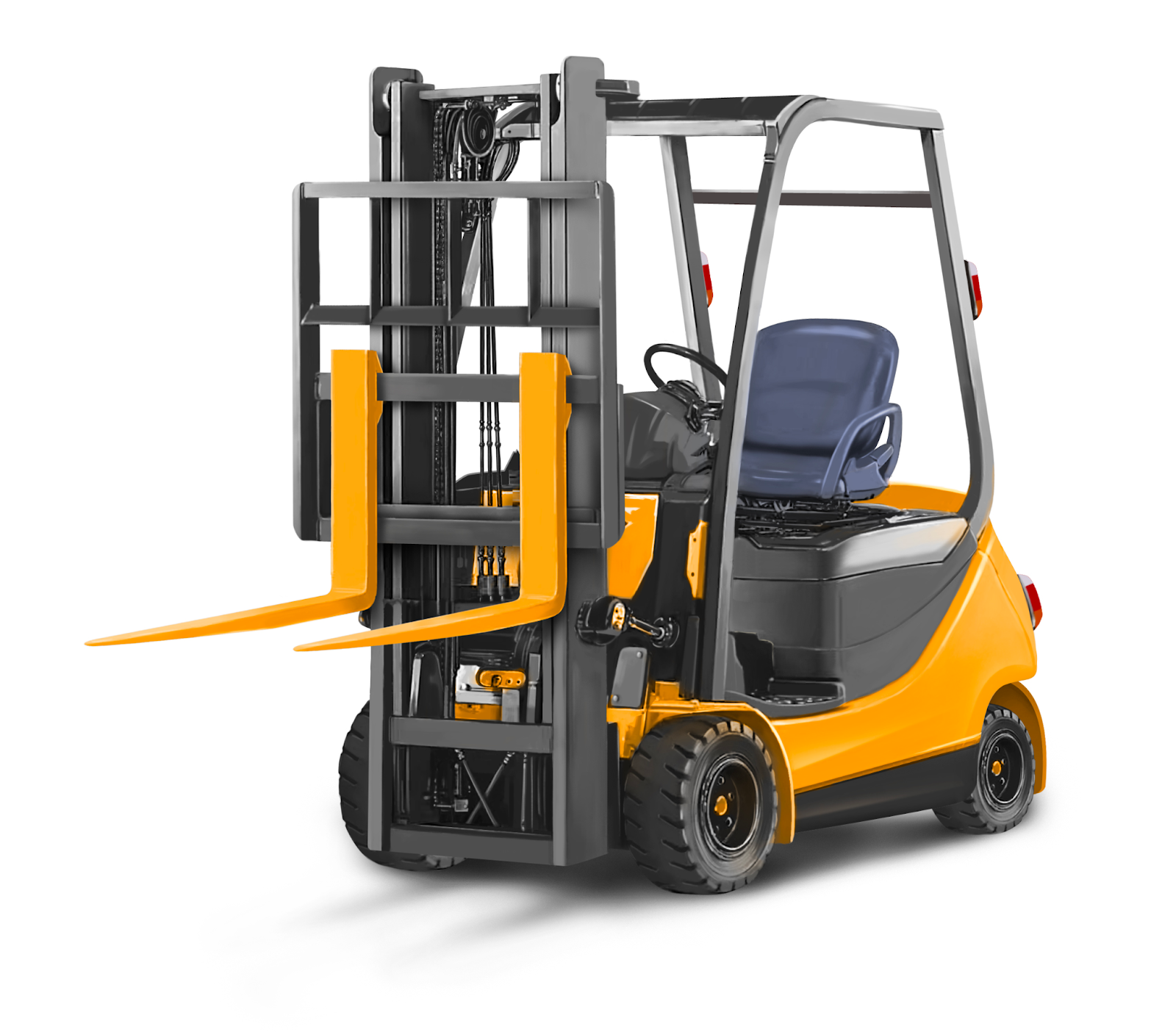
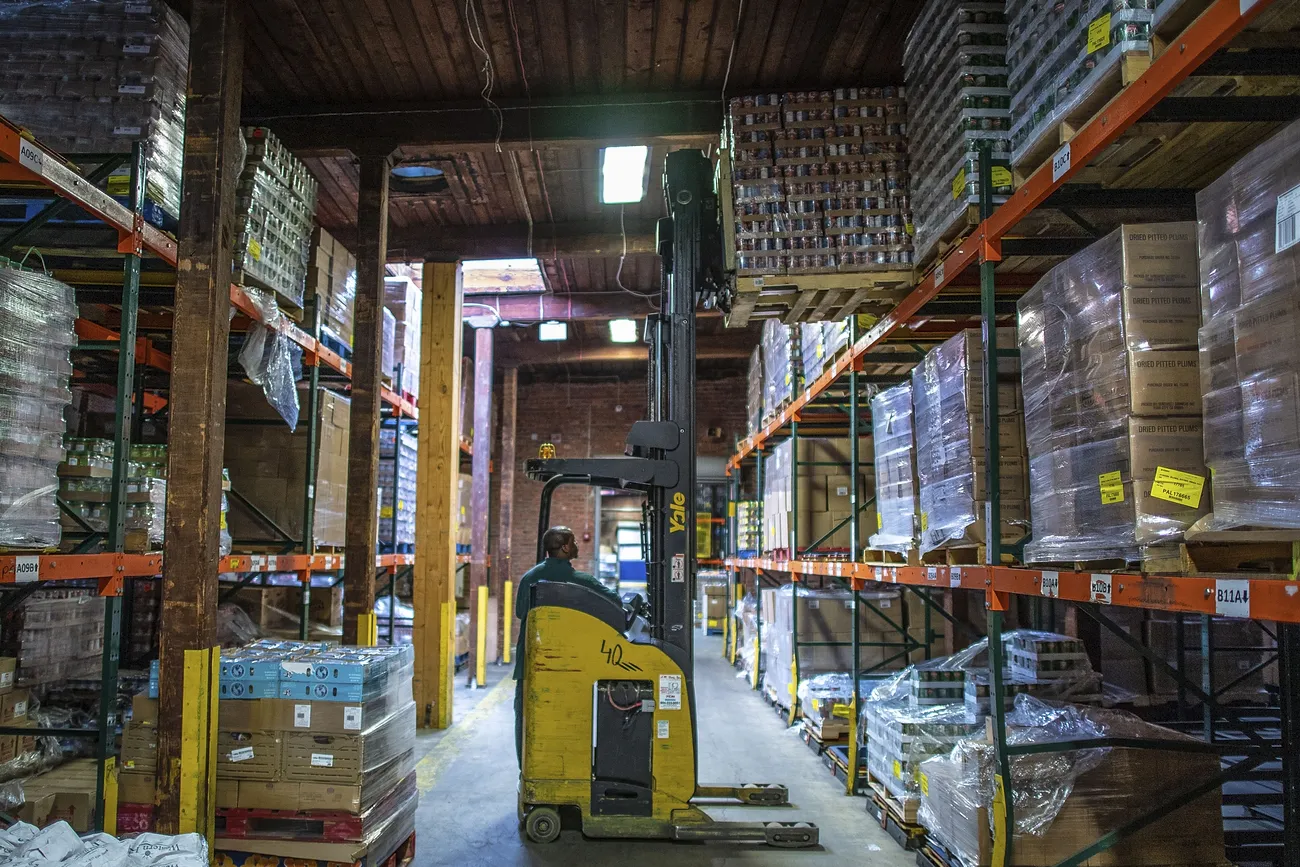
Forklifts are a common lifting equipment. Warehouse-type models use a vertical mast, but some have a telescoping boom which can raise and lower a load and extend it horizontally away from the cab. Forklifts with telescoping booms tend to be more complicated to operate because of their additional functions. They are often installed with large, all-terrain tires, can tilt their chassis, and have four-wheel steering that can be operated independently between front and rear axles. Some can also pivot their forks from side to side. All of these controls, no matter the kind of forklift, require training and practice for safe operation.
There are also smaller lifting devices called hand lifts have a maximum capacity of a few hundred pounds but are small enough to fit through a doorway. These resemble the mast and forks of a warehouse forklift, but instead of possessing a cab with a seat, engine, and counterweight, they utilize a hand-cranked winch.
Manual lifting devices known as grasshopper pipe dollies, drywall carts, pallet jacks, piano carts, and hand trucks are used to move materials in places that a forklift cannot access. Using these requires a certain level of physical strength and fitness.
Aerial Lifts and Platforms
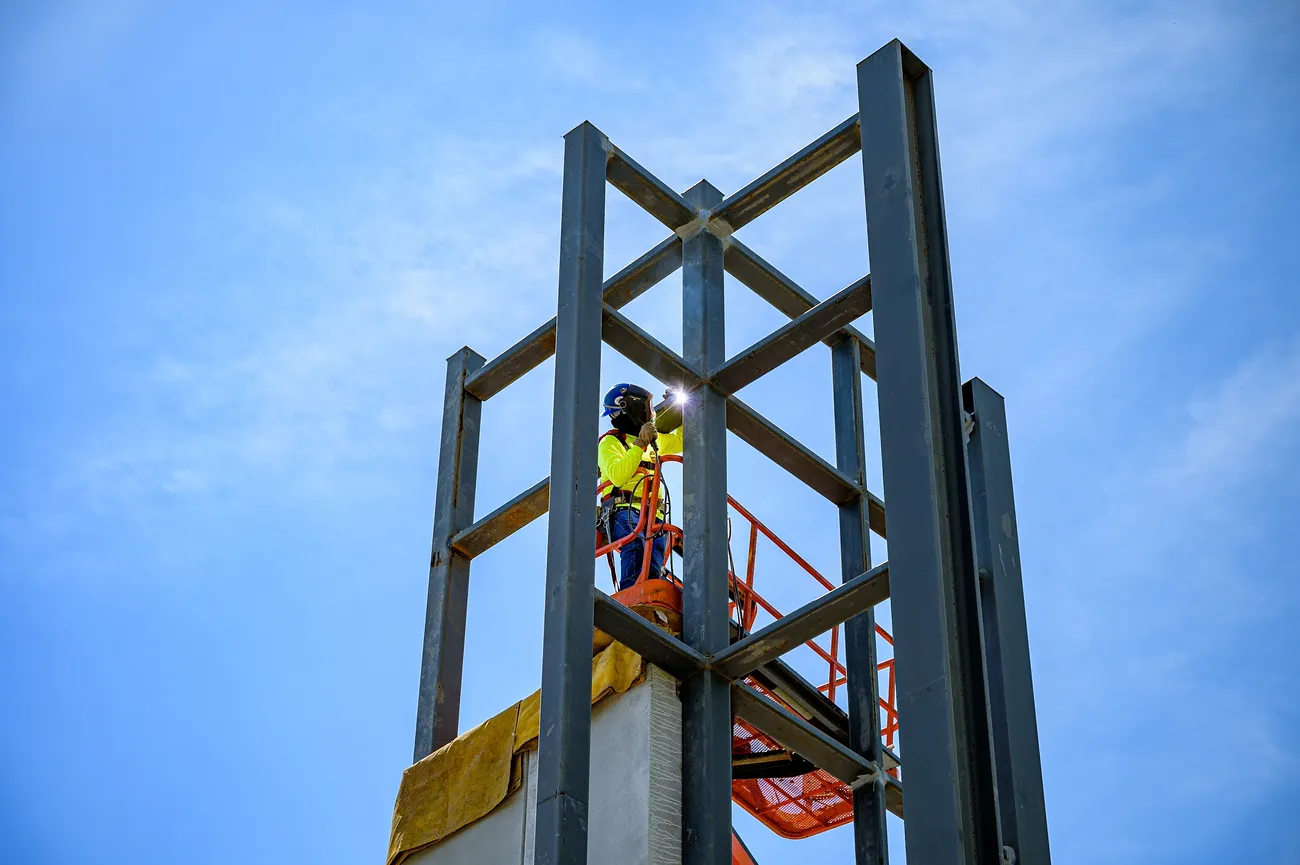
Once the structure you are working on becomes taller than you can reach, you have a problem. Drywall finishers have solved this by wearing stilts on the job, though I have yet to meet a welder who is interested in trying this. Using a ladder can get you in the air, but your reach is still limited, plus climbing up and down a ladder to move it constantly is much less productive than working with both feet on the ground.
Consider the Depression-era photo, shown in Figure 7.10, of ironworkers seated on a beam hundreds of feet in the air, eating their lunch. Safety and the ability of welders to access their work have come a long way since the 1930s. Today, we have fall arrest harnesses, aerial lifts, and work platforms, which make work at heights safer and increase worker productivity.
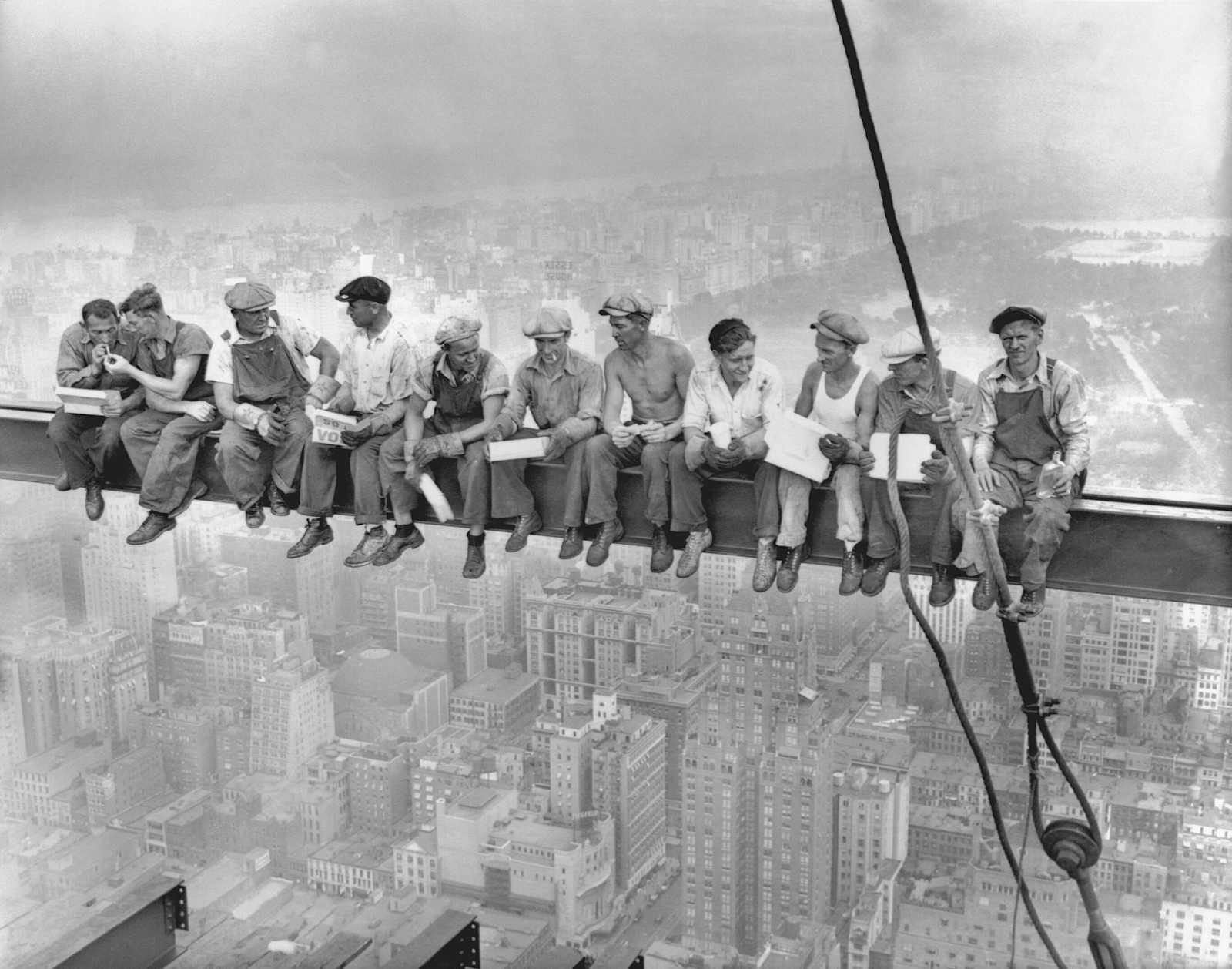
Modern aerial lifts typically have a heavy counterweight base with a telescoping boom. At the end of the boom is a basket or platform surrounded by a railing with space for two workers. The lift’s controls are normally operated from the basket, with a second set of controls at the base on the ground. These lifts can have a straight boom or different joint configurations to allow them to work around obstructions such as pipes. They can be all-terrain with independent front-rear steering and be diesel, electric, or gas/propane powered. Some of these boom lift aerial work platforms can reach over 125 feet in height. Proper training is required for the safe use of aerial lifts.
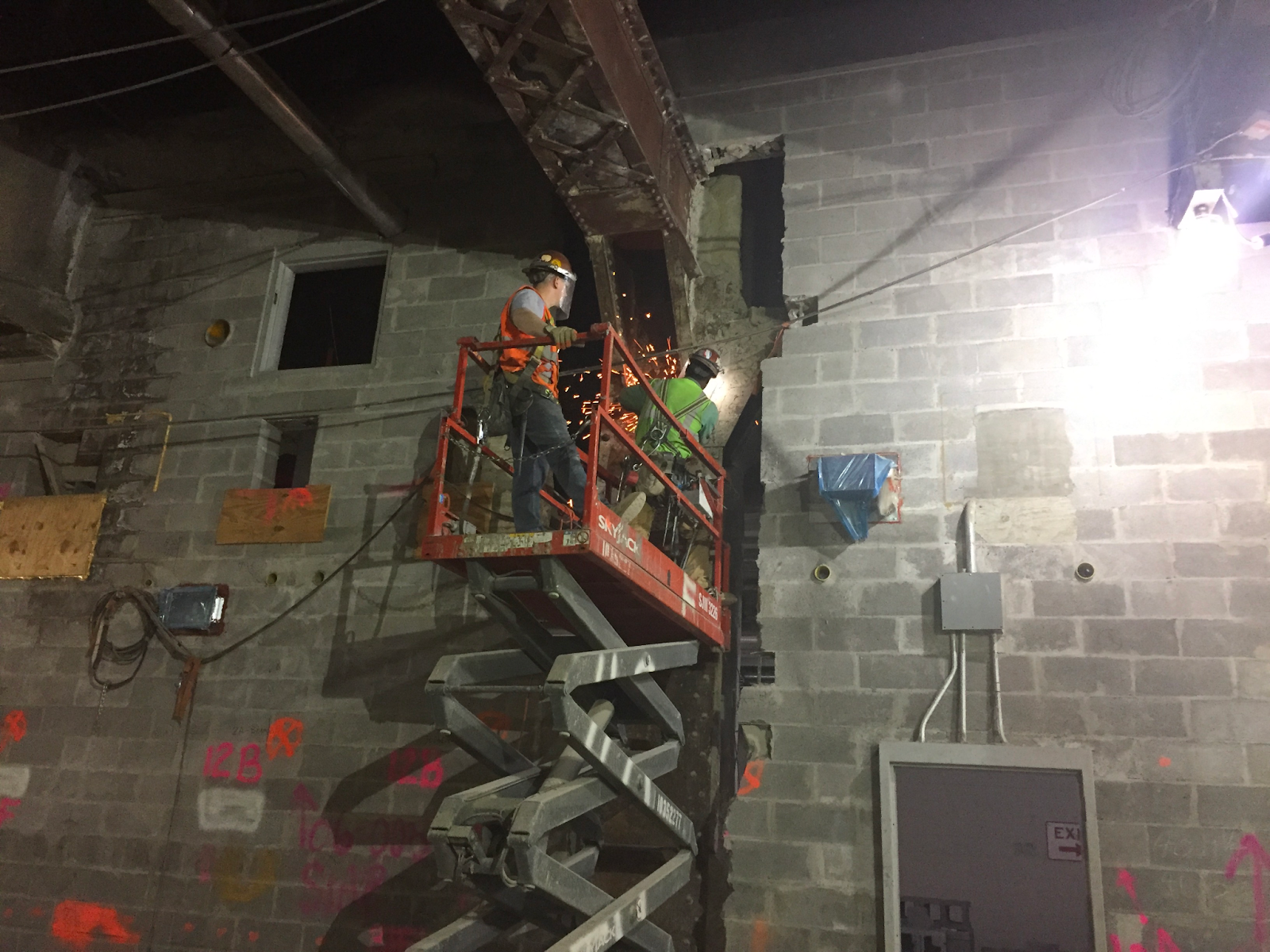
Platforms can be motorized, such as a scissor-type lift, or they can be built, like scaffolding. Vertical lifts can range in size from a one-person vertical lift (similar to working from the top of a telescoping car antenna) to a multi-person, all-terrain behemoth driven by an internal combustion engine. The most common size of lift accommodates two people, can fit through a doorway, and runs on rechargeable batteries. If using these, it’s important to plug them in for recharging at the end of your shift. Discovering dead batteries in your lift in the morning makes for an irate foreman and a long day at work.
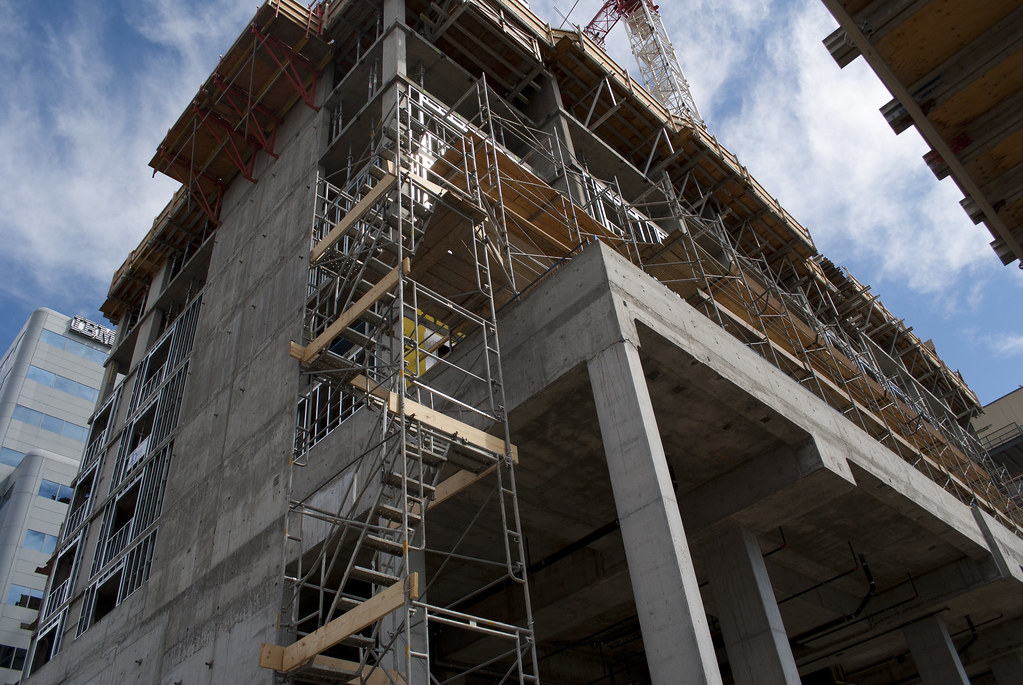
Scaffolding can be stationary, attached to the outside of a building, and reach dozens of stories in the air. It can also be in the form of a small wheeled unit that fits through a doorway.
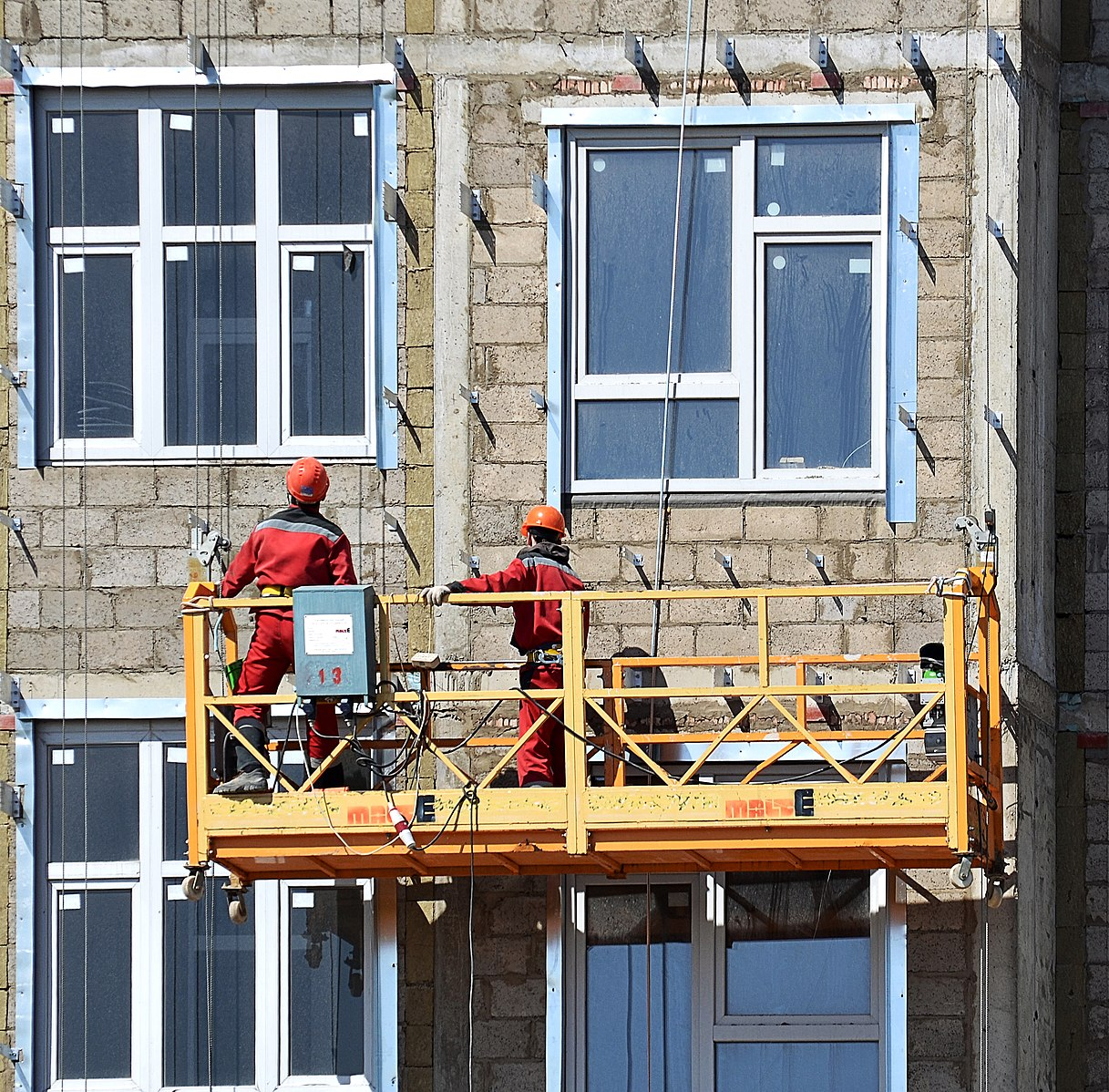
Adjustable suspension scaffolds, also called swing stage scaffolding, are suspended by wire ropes (cables) and can move up and down, usually powered by an electric motor. Window washers typically use this type of platform on the outside of high-rise buildings. The “arms” that remain overhead and raise and lower the cables are called davits, and they use counterweight to operate. The davits may be permanently attached or have a temporary anchoring system held in place by weights.
Always refer to the manufacturer’s recommendations regarding how much counterweight is to be used for the load on the platform, and always inspect the davits before each use. A welding instructor I once had related a story of how he and his coworker were returning to work after lunch to discover roofers had begun to disassemble and move the supporting arms and counterweights in order to perform their work on the roof. Had my instructor and his coworker simply hopped back in the swing stage on the ground and tried to ascend without first inspecting the scene, they would have pulled the davits off the roof and, likely, onto them.
Welders must keep two things in mind when welding from a swing stage to perform the work well. First, you may find yourself swaying while you weld, which will require you to learn how to steady yourself with one hand while you weld using the other. And second, your electrode and stinger may short (ground) themselves out on the swing stage platform while the building you are working on is the electrical ground. In this situation, you may get shocked if you touch the building. This is yet another reason you should remove stick electrodes from the holder when not actively welding.
A variation of the swing stage, called the bosun’s chair, is a single plank seat suspended by a single line of rope. There is also the float—a plywood platform suspended by rope—or an even smaller contraption called an angel wing basket.
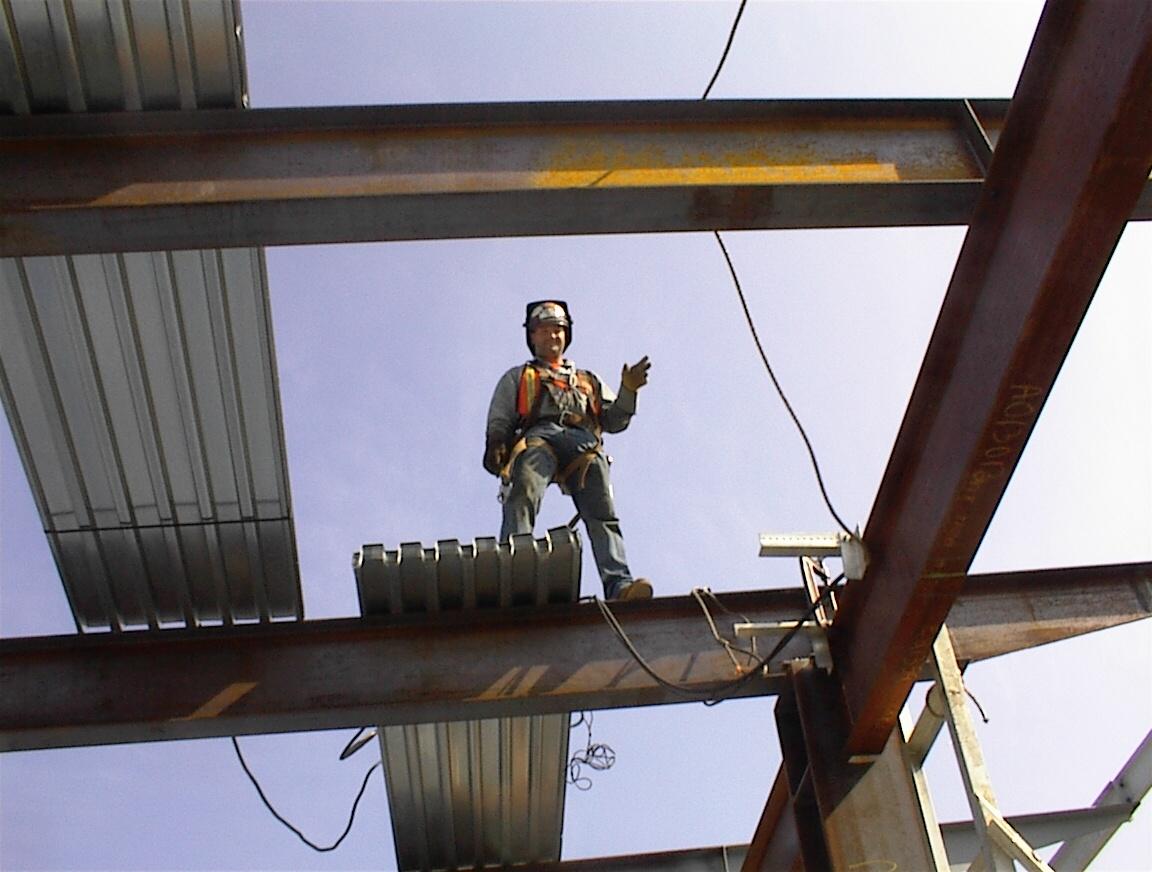
Earthmoving Equipment
Many of us had toy dump trucks when we were children, and surely all of us have played in the sand or dirt, digging and building miniature cities and landscapes. On a construction site, you will get to see real earthmoving equipment in action. Earthmoving equipment can be divided into two categories: digging and hauling.
Some examples of excavating or digging equipment are track hoes, front-end loaders, backhoes, trenchers, graders, bulldozers, and scrapers.
An excavator, sometimes called a track hoe, may come to mind first when discussing digging equipment. This piece of equipment has a cab that spins around on crawler or tank’ tracks and a long articulated boom arm. The end of this arm is fitted with digging accessories such as a bucket, jackhammer, or grabbing claw. These are particularly good at digging deep holes with steep sides, such as basements and foundations for buildings. The boom arm allows for a reach that is long and can go low, and the rotating cab allows for immediate loading and piling away from the hole it is digging.
A front-end loader is like a common farmer-style tractor that has a large blade or bucket across the front that is used to scoop up large loads of dirt or gravel. A backhoe loader tractor is a combination of an excavator and front-end loader.
A trencher resembles a truck or tractor with a giant chainsaw sticking out of the front or back. It cuts a narrow trench into the ground for pipelines or other utilities.
Motor graders look like long, skinny tractors with giant blades across their midsection. They are used in leveling ground, particularly in road construction. Scrapers are used for the same function, except they will also remove dirt from the area.
Bulldozers are heavy-duty track-mounted trucks that have a blade in the front designed for pushing dirt, rock, or other materials. They move dirt and gravel and are mostly used for leveling terrain for roads or parking lots
Equipment used for hauling includes front-end loaders and dump trucks in various configurations to scoop up large loads of earth and lift them into the air to load into trucks. Dump trucks may be single units or have trailers. They may also be small enough to travel on public roads or be massive units that may only do work in mining operations.
As a welder, you may work in excavations, welding pipes or pilings, and be around digging and hauling equipment, or you may perform repair work on them.
In excavation, large metal plates lining trenches are used for shoring. These are kept apart by pipe spacers and prevent the trench walls from collapsing. There is a significant, life-threatening hazard if these collapse or cave in.
Welding on digging equipment often involves a process called hard face welding in which weld metal is deposited on digging buckets or dozer blades to slow down wear or replace worn metal. This weld metal is harder than the base metal and is often welded in a cross-hatch pattern to provide abrasion resistance. Proper lockout/tagout procedures are necessary when repairing heavy equipment (see Chapter 2).
Attributions
- Figure 7.1: Restoration work on Reading Terminal by Carol M Highsmith is released under CC0
- Figure 7.2: Work progresses at National Air Force Museum by U.S. Army Corps of Engineers in the Public Domain; United States government work
- Figure 7.3: Town Common Pedestrian Bridge by City of Greenville, North Carolina is released under PDM 1.0
- Figure 7.4: Grue médiévale (reconstituée) devant l’abbaye de Hambye (Normandie) by Ji-Elle in the Public Domain; Public Domain dedication, not CC0
- Figure 7.5: A crane and rigging are used to lift the Orion Service Module Umbilical (OSMU) high up for installation on the mobile launcher tower at NASA’s Kennedy Space Center in Florida. by NASA in the Public Domain; United States government work
- Figure 7.6: In Launch Complex 39 at NASA’s Kennedy Space Center in Florida, workers guide one of the walls of the Propellants North Administrative and Maintenance Facility into place. by NASA in the Public Domain; United States government work
- Figure 7.7: Forklift-Truck by Compliance and Safety LLC is released under CC BY-SA 3.0
- Figure 7.8: 20180912-FNS-PJK-0699_TONED by U.S. Department of Agriculture in the Public Domain; United States government work
- Figure 7.9: Aerial lifts are used to allow workers to gain access to work that cannot be reached by ladder. by City of Greenville, North Carolina is released under PDM 1.0
- Figure 7.10: Lunch atop a Skyscraper – Charles Clyde Ebbets by Charles Clyde Ebbets in the Public Domain; This work is in the public domain because it was published in the United States between 1928 and 1963, and although there may or may not have been a copyright notice, the copyright was not renewed.
- Figure 7.11: Ironworkers are welding a column in the back-of-house area of the future LIRR passenger concourse. (CM014B, 05-22-2019) (47952892561) by MTA Construction & Development Mega Projects is released under CC BY 2.0
- Figure 7.12: Construction Update – Mayfair South by Marcel Schoenhardt is released under CC BY-SA 2.0
- Figure 7.13: Workers on suspended scaffold in Korolyov by Dmitry Ivanov is released under CC BY-SA 3.0
- Figure 7.14: Ironworker Welder by Doug Rupik, for WA Open ProfTech, © SBCTC, CC BY 4.0
A long arm that extends to move objects or employees to the location where they are needed, especially in terms of higher spaces.
a weight that adds balance to a mechanical device, such as an aerial lift.