17.5 American Petroleum Institute (API) Welding Standard
David Colameco, M.Ed.
Development of API Standards
The API was founded in 1919 “as a standards-setting organization” (American Petroleum Institute, n.d.). Similar to how AWS and ASME publish standards for the many industries they each serve, API publishes standards for the industry it serves: the petroleum industry. The API has developed more than “800 standards to enhance the operation safety, environmental protection and sustainability across the industry, especially through these standards being adopted globally” (American Petroleum Institute, n.d.)
API develops standards through committees that consist of people and organizations that have direct interest in the standard being developed or maintained. These committees discuss proposed content and use a consensus approach, which is defined by API as reaching a “substantial agreement” (American Petroleum Institute, 2013, p. 1). These committees develop specifications, standards, codes, and recommended practices.
An API specification is written to allow for communication between purchasers and manufacturers. An example would be a pipe specification for its material properties of 5L pipe. Manufacturers would know what the requirements were so they could successfully manufacture pipe to the API 5L standard, and consumers would know what they were getting when buying pipe manufactured to the API 5L standard.
A recommended practice is a document that contains industry-identified best ways of performing activities, such as fabricating. This is a great example of why feedback from companies and fabricators in the industry is so important, because recommended practices may change over time as new techniques are developed and older techniques are retired.
A standard is a document that combines different aspects of specifications and recommended practices together to form requirements and suggestions for specific fabrication activities or groups of fabrication activities. API Standard 1104 is for welding pipelines and related facilities.
A code is a standard that has been adopted by government agencies having jurisdiction in an area that applies the fabrications being made. That agency having jurisdiction makes following the standard a legal requirement, which then turns the standard into a code.
Basics of the API Standard 1104
API Standard1104 Welding Pipelines and Related Facilities is a standard for just that: welding pipelines and related facilities. Similar to the AWS and ASME codes for welding, API 1104 has a scope and covers qualifications for procedures, qualifications for welders, weld design, inspection, repair, and other topics.
API 1104 covers the gas and arc welding of butt, fillet, and socket welds in carbon and low-alloy steel piping used in the compression, pumping, and transmission of crude petroleum, petroleum products, fuel gasses, carbon dioxide, nitrogen, and, where applicable, covers welding on distribution systems (American Petroleum Institute, 2013, p. 1).
The welding processes recognized by API 1104 are:
- shielded metal arc welding,
- submerged arc welding,
- gas tungsten arc welding,
- gas metal arc welding,
- flux-cored arc welding,
- plasma arc welding,
- oxy-acetylene welding,
- flash welding, and
- combinations of the above.
Rather than reinvent the wheel by recreating identical standards, API 1104 references many AWS specifications for electrodes as well as ASTM standards for testing materials and welds.
Uses of the API Standard 1104 in Industry Today
API 1104 is used throughout the oil and natural gas industry to build, maintain, and repair its facilities . It defines materials, designs, inspection, and repairs of welded pipelines and related facilities.
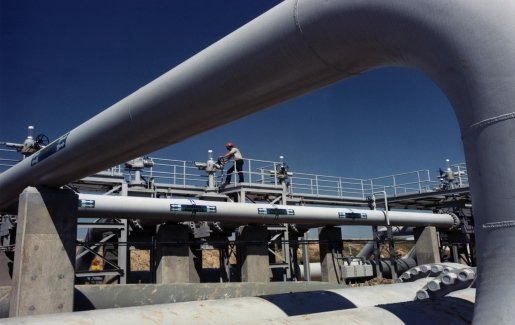
If fabricating, installing, or maintaining such facilities or working in the oil and natural gas industry interests you, you can perform an internet search for relevant career opportunities as you pursue your career in welding.
Getting Qualified to the API Standard 1104
Qualification of welders is similar to that of AWS and ASME in terms of performing welds on specified joints followed by nondestructive and destructive testing. API 1104 uses visual or other nondestructive examinations (such as radiography and ultrasonic testing) followed by destructive bend tests, tensile tests, and nick break tests as appropriate. The number of destructive tests performed is determined by the size of the outside diameter of the pipe being welded.
Welders can be qualified to a single welding procedure or multiple procedures. Single procedure qualification tests are done for configurations like branch connections and fillet welds. The multiple procedure qualification has prescribed tests, which are described as follows:
- “For the first test, the welder shall make a butt weld in the fixed position with the axis of the pipe either horizontal or inclined from horizontal at an angle of not more than 45 degrees. This butt weld shall be made on pipe with an OD of at least 6.625 in. (168.3 mm) and with a wall thickness of at least 0.250 in. (6.4 mm) without a backing strip.
- For the second test, the welder shall lay out, cut, fit, and weld a branch-on-pipe connection in which the specified diameters of the run and the branch pipes are equal. This test shall be performed with a pipe diameter of at least 6.625 in. (168.3 mm) and with a specified wall thickness of at least 0.250 in. (6.4 mm) (American Petroleum Institute, 2013, pp. 26–27).
For this multiple test description, you can see that layout, math, and cutting classes are equally as important as the act of welding is when testing to the API Standard 1104.
Attributions
- Figure 17.18: Strategic Petroleum Reserve by U.S. Department of Energy, Office of Fossil Energy and Carbon Management in the Public Domain; United States government work