17.6 American Bureau of Shipping (ABS) Welding Rules and Guides
David Colameco, M.Ed.
Development of the ABS Rules and Guides
The ABS was founded in 1862 with a mission “to serve the public interest as well as the needs of our members and clients by promoting the security of life and property and preserving the natural environment.” (American Bureau of Shipping, 2023). In Washington state you will find ABS welding standards for ferries, cruise ships, and barges, to name a few.
The ABS uses a consensus-based approach for developing and maintaining ABS rules and guides through committees.
ABS has developed its Rule Requirements for Materials and Welding (Part 2), which, similar to ASME, separates materials and welding from many other ABS rules and guides and allows common requirements and recommendations for materials and welding to be placed in a single document. The documents that reference the Rule Requirements for Materials and Welding are:
- Rules for Building and Classing Marine Vessels
- Rules for Building and Classing Steel Vessels for Service on Rivers and Intercoastal Waterways
- Rules for Building and Classing Mobile Offshore Units
- Rules for Building and Classing Steel Barges
- Rules for Building and Classing High-Speed Craft
- Rules for Building and Classing Floating Production Installations
- Rules for Building and Classing Light Warships, Patrol and High-Speed Naval Vessels
- Rules for Building and Classing Yachts
- Guide for Building and Classing Liftboats
- Guide for Building and Classing International Naval Ships
The ABS rules and guides are available for free download.
Basics of the ABS Rules and Guides
ABS Rule Requirements for Materials and Welding (Part 2) focuses on hull construction and other subjects such as materials, different welding applications, welding and fabrication rules, examinations, and qualification of welders and welding operators. A list of the chapter titles of Part 2 provides a very good overview of what is contained within:
- Chapter 1: Materials for Hull Construction
- Chapter 2: Equipment
- Chapter 3: Materials for Machinery, Boilers, and Pressure Vessels
- Chapter 4: Welding and Fabrication
- Chapter 5: Materials for Hull Construction – Aluminum
- Chapter 6: Materials for Hull Construction – Fiber Reinforced Plastics (FRP)
- Appendix 1: Tests Required for Materials and Responsibility for Verifying
- Appendix 2: Requirements for the Approval of Filler Metals
- Appendix 3: Application of Filler Metals to ABS Steels
- Appendix 4: Procedure for the Approval of Manufacturers of Hull Structural Steel
- Appendix 5: Hull Structural Steels Intended for Welding with High Heat Input
- Appendix 6: Nondestructive Examination of Marine Steel Castings
- Appendix 7: Nondestructive Examination of Hull and Machinery Steel Forgings
- Appendix 8: Steel with Enhanced Corrosion Resistance Properties
- Appendix 9: Welding Procedure Qualification of Steels for Hull Construction and Marine Structures
- Appendix 10: Procedure for Approved Aluminum Manufacturers
- Appendix 11: Qualification for Welders and Welding Operators
- Appendix 12: Comparison of Existing Materials and Welding Rules vs. 2018 Materials and Welding Rules
Chapter 1: Materials for Hull Construction discusses inspection and weld repair of material found to have defects. Chapter 2: Equipment mainly discusses the rules and requirements for anchors and anchor chains, which may be welded during manufacture and repair. Chapter 3: Materials for Machinery, Boilers, and Pressure Vessels discusses the requirements of materials used in machinery, boilers, pressure vessels, and piping, as well as repair of some casting. Similar to Chapter 1, inspection and testing of materials for acceptance is discussed along with heat treatment for each application for example.
Chapter 4: Welding and Fabrication discusses the many aspects of welding from joint preparation, the required use of qualified welders, production welding and repairs. One item of interest that is different from most other welding codes is the idea of welding with water backing. The use of a backing strip prevents the weld pool from falling through the joint. Water backing, for the purposes of Chapter 4 in Part 2, means welding on a weld joint that has base material with water on one side, such as welding on the hull under the water line. A full penetration weld has backing that prevents water from coming in contact with the root of the weld.
The remaining chapters in the Rule Requirements for Materials and Welding (Part 2) discuss welder qualifications that are discussed in a section below or topics that are beyond the scope of this chapter.
If any of the topics from Part 2 interest you, you are highly encouraged to search for jobs in the maritime industry. Most ABS-related and maritime-related welding jobs are located in ports with access to the Pacific Ocean in Washington state. However, there are many waterways, such as the Columbia River and Snake River, and larger lakes, such as Moses Lake, throughout the state where opportunities may exist to weld on water going vessels. You are encouraged to search for these opportunities if this is a career direction you are interested in.
Uses of the the ABS Rules and Guides in Industry Today
The United States Coast Guard accepts and recognizes many ABS rules and guidelines.
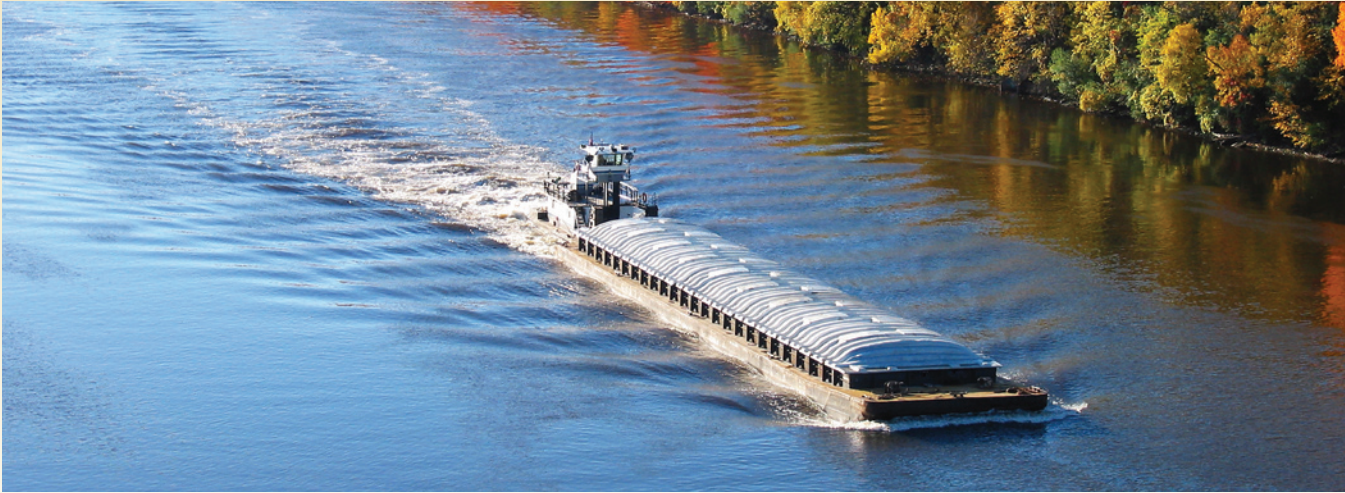
ABS rules and guides govern many larger water vessels from barges, tub boats and assist boats, yachts, cruise ships, ferries, and even offshore oil rigs.
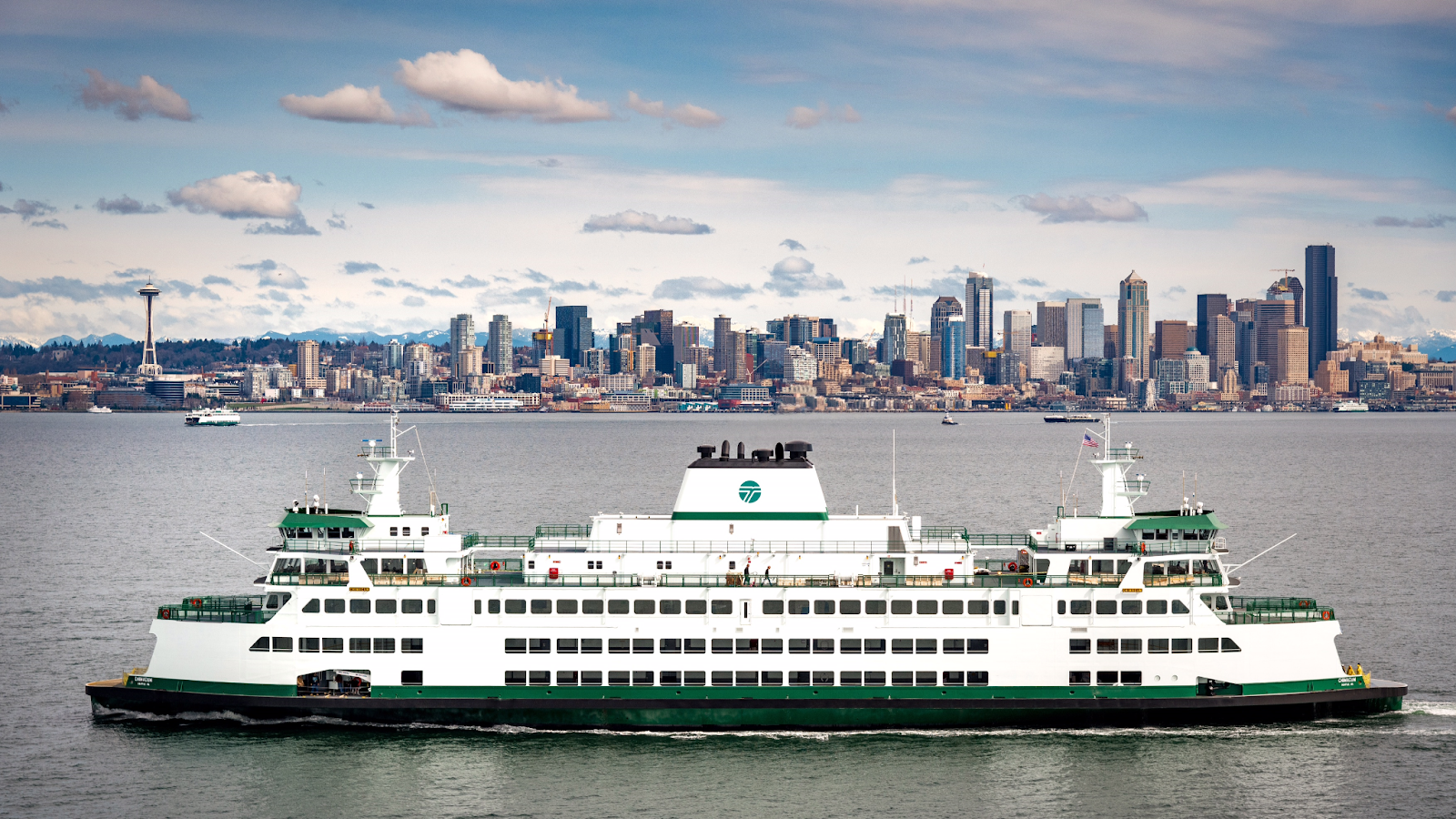
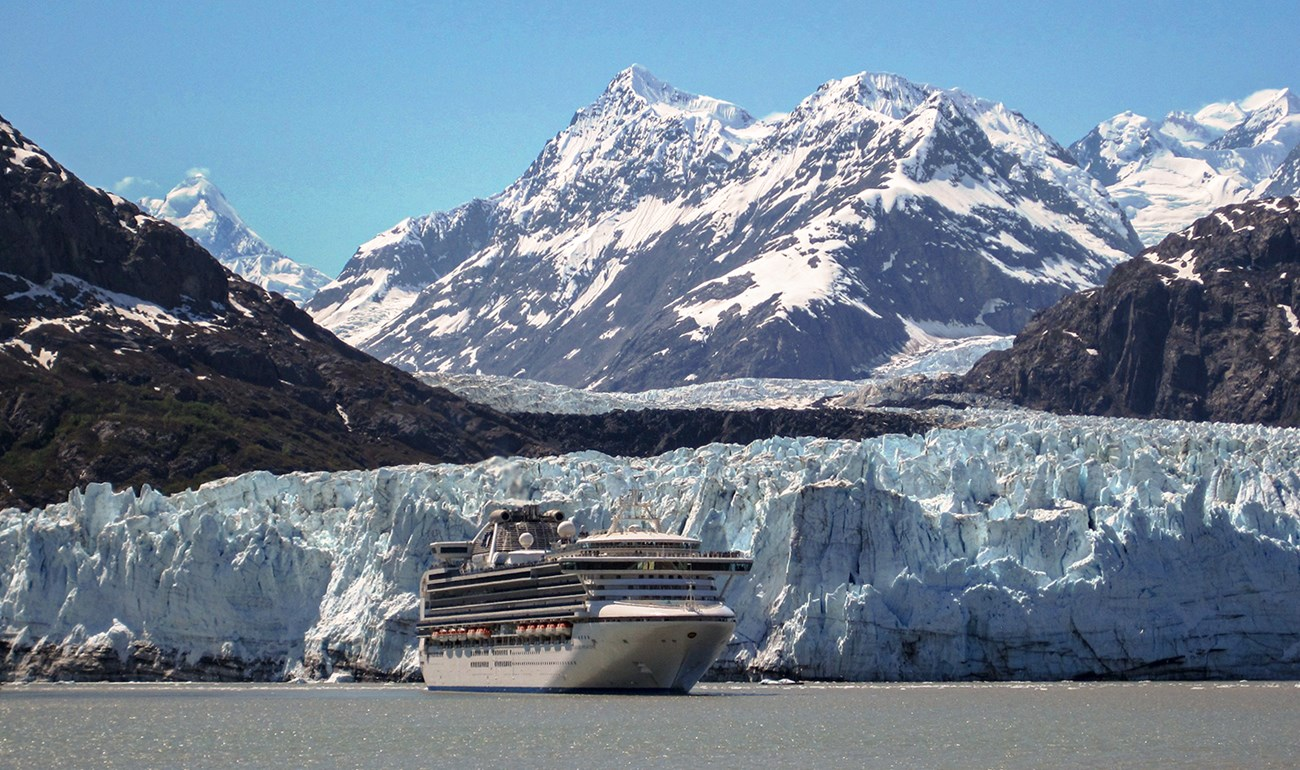
ABS does have some rules and guides that were written for smaller coastal naval vessels, but it is not clear how widely that document is used in place of NAVSEA welding standards, which are discussed later in this chapter.
The cruise ship tourism and the fabrication of cruise ships are industries that has been ongoing in the Seattle area. More than 430,000 passengers from Alaska cruise ships pass through Puget Sound annually, with almost half starting and ending their journeys here (McDowell Group, 2015).
Tug boats transport a significant amount of cargo between the Puget Sound Area and Alaska by pushing or pulling barges with containers of goods (McDowell Group, 2015). Tug boats are likely more commonly known for the assistance they provide water craft that can’t easily or safely maneuver in narrow waterways or into port. Tug boats come in all sizes, ranging from 50–250 feet in length and having 4,000–22,000 horsepower (Dann Ocean Towing, 2023).
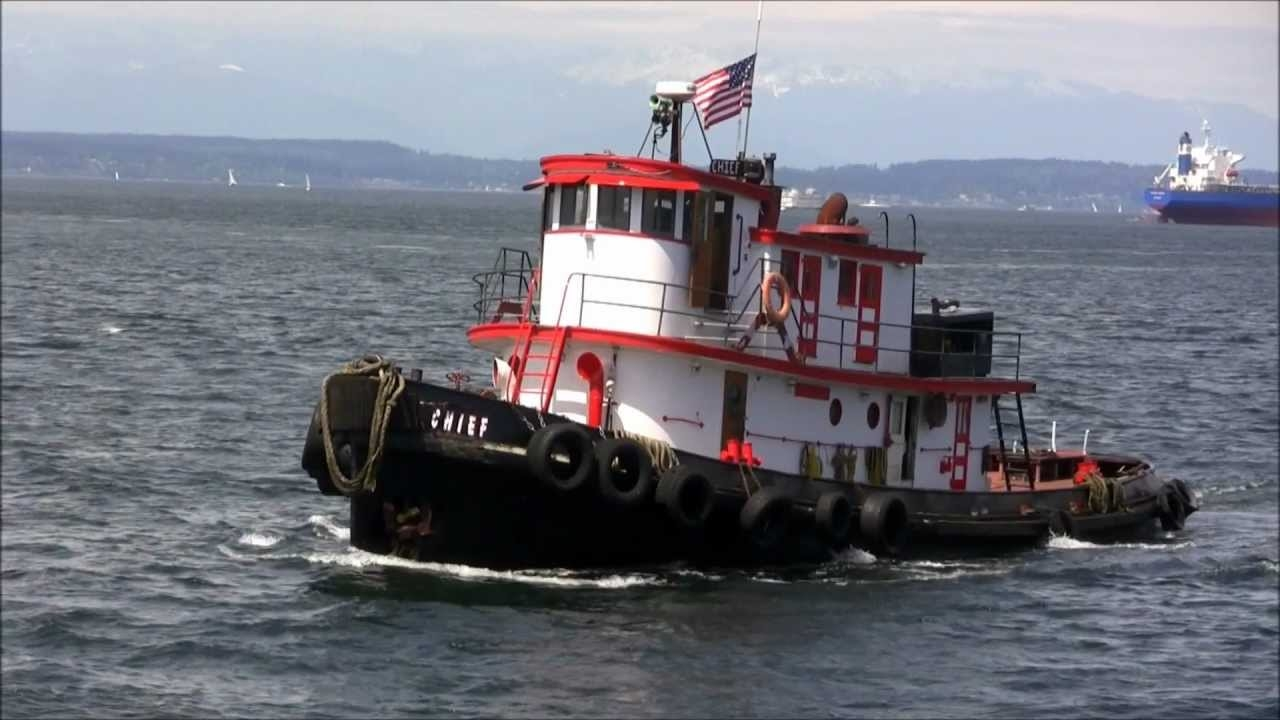
Figure 17.22 shows an offshore oil drilling rig in the Gulf of Mexico. These structures are also classified by ABS and have rules and guides. As you can see, there are many different applications of ABS structures in Washington state and the United States.
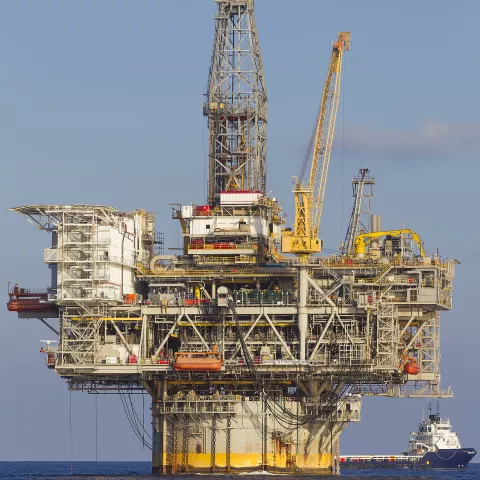
Getting Certified to the ABS Rules and Guides
In Rule Requirements for Materials and Welding (Part 2), Chapter 4: Welding and Fabrication describes the tests to qualify not only welders but also procedures and filler materials:
- Test Q1 is a plate material 0.375 inches thick and is 10 inches wide by 6 inches long, V groove with backing.
- Test Q2 is a plate material 0.75 inches thick and also 10 inches wide by 6 inches long, single bevel with backing.
- Test Q3 is a pipe weld in 1G, 2G, 5G, 6G, or 6GR (restriction ring).
- Test Q3R is a pipe weld within 12 inches of the bulkhead above and to the left of the pipe.
- Test Q4 is a fillet weld break test.
The requirements for qualifying procedures and filler materials are more stringent than the tests for qualifying a welder. See Figures 9–12 of ABS Rule Requirements for Materials and Welding (Part 2), the 2023 publication, for figures showing the tests and their positions.
Aluminum has similar tests that are outlined in Chapter 4: Welding and Fabrication, Section 5: Aluminum Welding in Hull Construction. These tests are:
- Test Q1 is a plate material 0.375 inches thick and is 12 inches wide and 6 inches long, V groove with backing.
- Test Q2 is a plate material 1.5 inches thick and also 12 inches wide by 6 inches long, single bevel with backing.
- Test Q3 is not applicable for this section.
- Test Q4 is a pipe weld within 12 inches of the bulkhead above and to the left of the pipe.
- Test Q5 is a plate weld that is tack welded, 0.375 inches thick, 10 inches wide, and 6 inches long.
See Figures 14–17 of ABS Rule Requirements for Materials and Welding (Part 2), the 2023 publication, for figures showing the tests and their positions.
It is important to note that ABS specifies that welders can be qualified under other welding codes and standards, such as AWS and ASME, with the approval of the ABS surveyor. Appendix 11: Qualification for Welders and Welding Operators in Part 2 has alternative methods for qualification using fillet welds, groove welds, and tack welds. Similar to other welding codes and standards, bend tests are performed to determine acceptability of the welds along with visual examination. Welders are qualified to base materials, welding consumables, welding process, type of weld joint, plate thickness, and welding position (American Bureau of Shipping, 2023, p. 688)
ABS has a separate document for stainless steel: ABS Requirements for Materials and Welding for Stainless Steels. This document covers stainless steel plates, forgings, castings, pipes, and clad plates, to name a few. Chapter 4: Welding of Stainless Steels describes the following training and skills required:
- groove dimension,
- groove cleanliness,
- protecting against weather and wind,
- weld stop, start and terminations,
- weld repair,
- storing and handling of welding consumables, and
- general maintenance of equipment.
The above list is provided as an example of some of the skills that you will need when qualifying for ABS certification. As a welding student learning to weld, it is important to note that you get out of your education what you put into it. If you aren’t focusing some time on your weld starts, stops, and terminations, then consider starting. Do not rely only on your instructor to give you guidance; you should take charge of your welding career and discuss areas for training and questions you have with your instructor.
ABS specifies tests for welder qualification: visual examination and bend tests for butt welds, visual examination and fracture test for fillet welds, and tack welders must be fully qualified. Welder certification is verified by shipyards, manufacturers, and subcontractors every six months. As with other welding codes, if there is a reason to question a welder’s ability to weld, then the welder needs to re-qualify. For a full list of requirements and maintaining certification, please see Chapter 4, Section 2 of ABS Part 2.
Attributions
- Figure 17.19: Moving forward, saving energy by National Waterways Foundation, U.S. Department of Transportation, Maritime Administration, and Texas Transportation Institute in the Public Domain; United States government work
- Figure 17.20: M/V Chimacum and the Seattle skyline by Washington State Dept of Transportation is released under CC BY-NC-ND 2.0
- Figure 17.21: Visiting Glacier Bay on a cruise ship is an unforgettable experience! by U.S. Department of Interior National Park Service in the Public Domain; United States government work
- Figure 17.22: A file photo of the tug vessel Chief. The vessel sank in November 2017 in Salmon Bay, Washington and has since become a pollution concern. by NOAA Office of Response and Restoration in the Public Domain; United States government work
- Figure 17.23: Gulf of Mexico Region by U.S. Department of the Interior Home, Bureau of Safety and Environmental Enforcement in the Public Domain; United States government work