1.1 A (Very) Brief History of Welding
Douglas Rupik, M.Ed., JIW
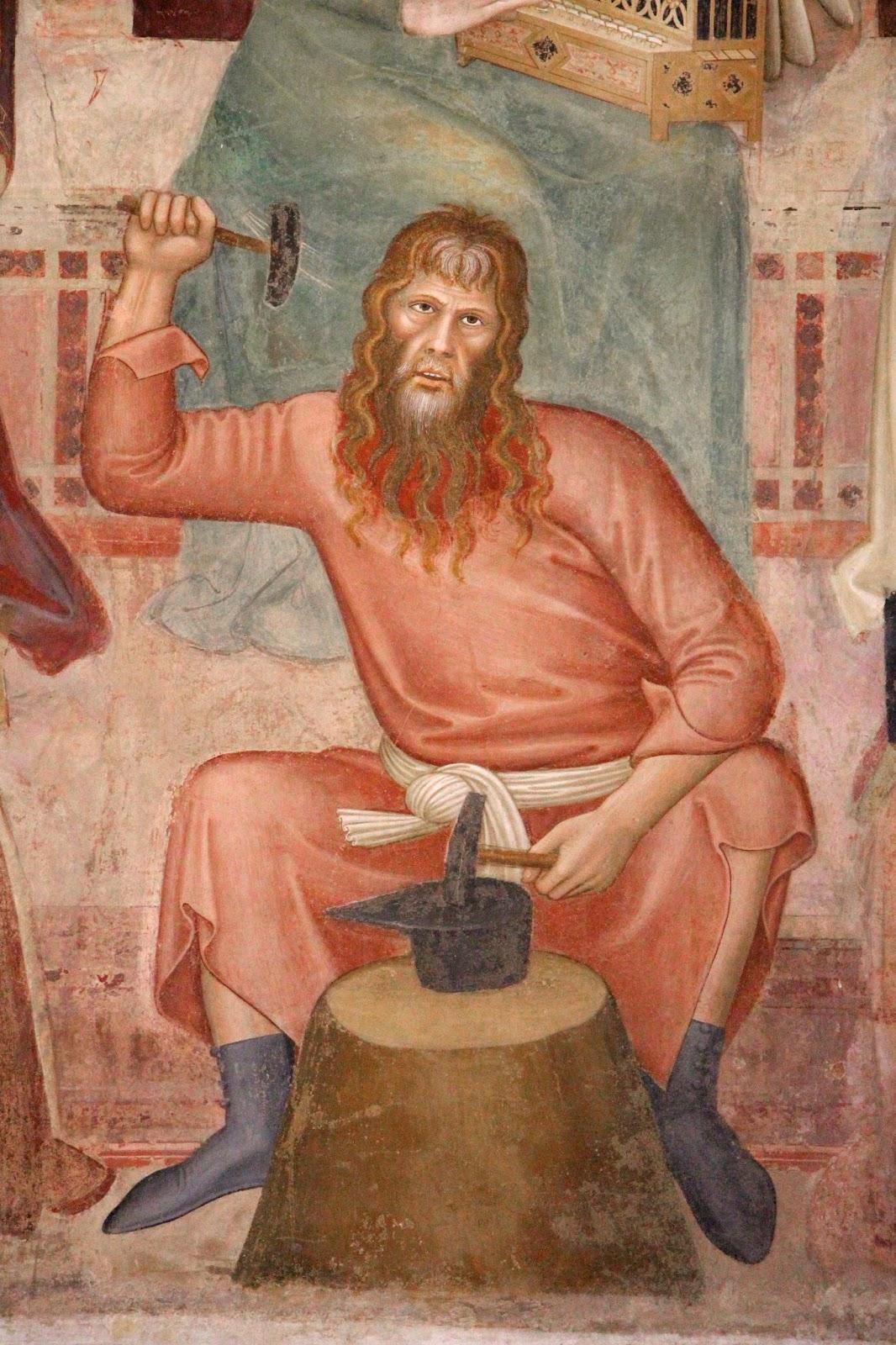
Metalworking in the Ancient World
Nobody today knows all the details regarding the beginnings of metalworking. Genesis 4:22 mentions “…Tubal-Cain, an instructor of every artificer in brass and iron…”, portrayed in Figure 1.1. The Ancient Greek historian Herodotus tells us that Glaucus of Chios was the man who single-handedly invented iron welding (Herodotus 2008, p. 25). Perhaps metals were first brought into use after being discovered in a fire pit, when the heat of a large fire melted metal ores contained in rocks that had accumulated in the bottom of the pit. Tools and weapons made from these metals would have been superior to those made from wood, stone, clay, or bone. Metals could be given a sharper edge and were more durable and stronger. Peoples who had the use of metals had an advantage over those that didn’t, and they were more likely to survive and prosper. Metal tools and goods lasted longer and enabled work to be done more efficiently.
Forge Welding
It may be that the first metal tools or weapons were beaten into shape, and were only later cast into shape. Casting is the process of pouring molten metal into a mold. While this is suitable for simply shaped objects, complex objects require multiple pieces to be attached. This may have been accomplished by riveting them, placing pieces together and pouring molten metal over them, or by forging.
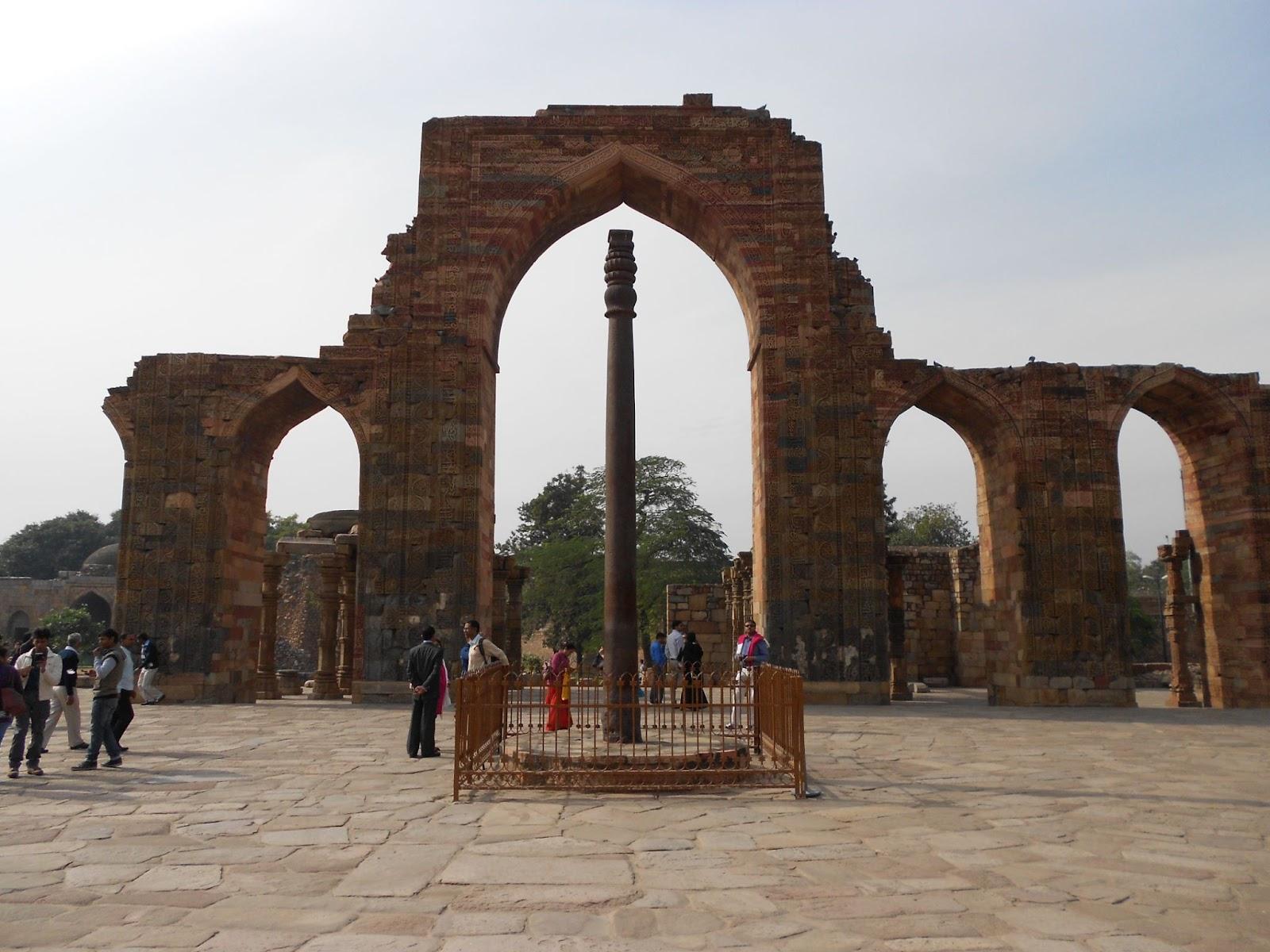
Forge welding is, in its simplest form, hammering two red-hot pieces of metal together until they bond. The Iron Pillar of Delhi, dated around 310 AD, was built using forge welding (Cary & Helzer 2005, p. 4).
From before the European Middle Ages up until the beginning of the 20th century, blacksmiths used forge welding to create a wide variety of metal objects used in daily life, from kitchen utensils to architectural features and weaponry. This made the blacksmith’s role an essential part of every community.
Then, with the advent of the Industrial Revolution in Western society and the necessity for increased productivity, the use of forge welding declined and fusion welding rose in its place.
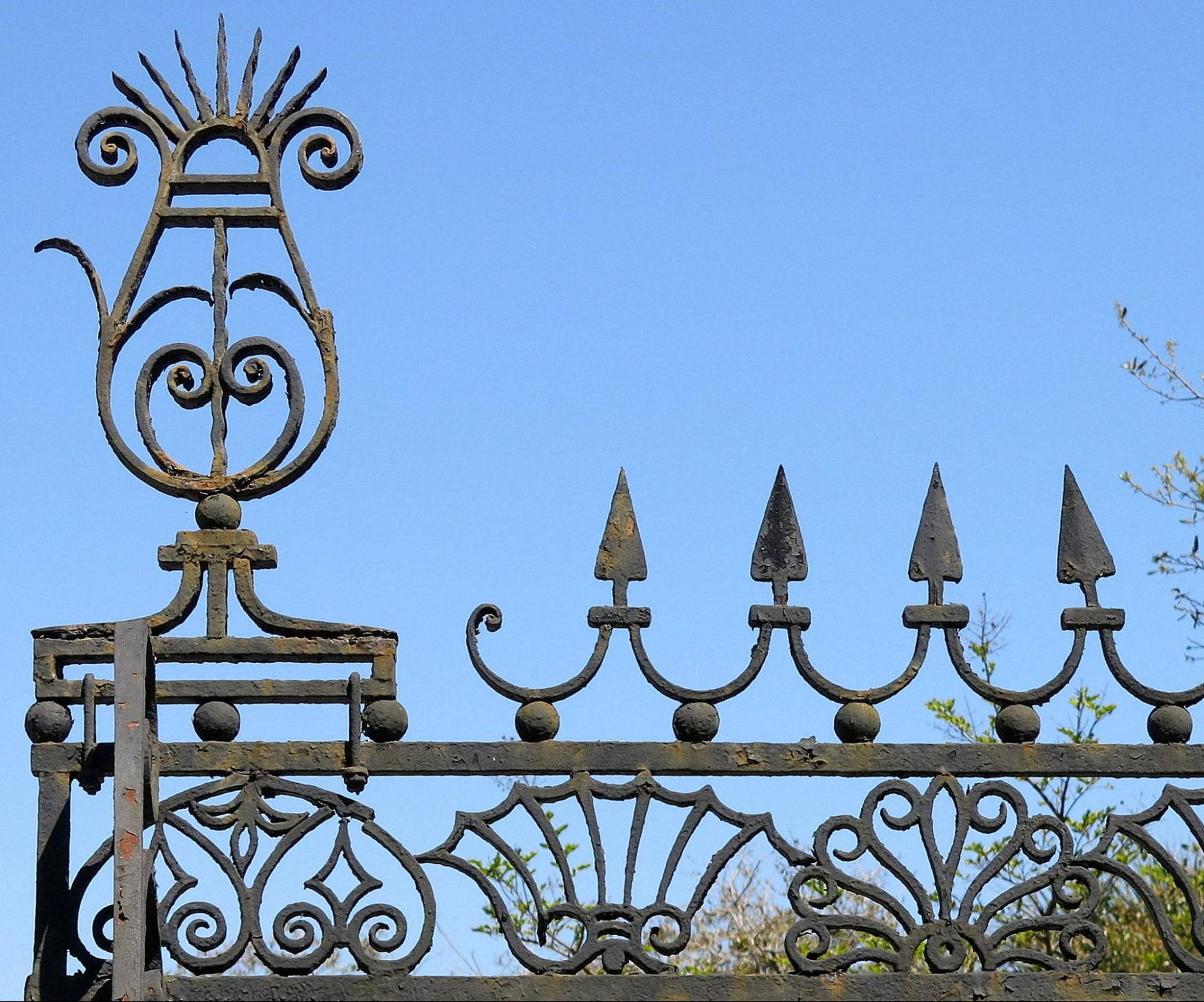
In ancient East Asia, cast bronze was used for creating ritual objects, musical instruments, sculpture, and weapons. By the end of the second century AD, bronze was being replaced by iron as the material of choice for casting metal objects, later even being used in architecture (East Asia, n.d.).
In ancient Sub-Saharan Africa, metals have been smelted, cast, and forged since before recorded history, with their use being nearly universal by 1000 AD. Copper, bronze, and iron were used for art, jewelry, tools, currency, and weapons. Interestingly, unlike in Europe the blacksmiths were often separated from the community and worked outside of villages (Reid 2005).
In pre-Columbian America, metalworking was largely limited to art and jewelry and primarily in copper, silver, and gold. Highly skilled smiths used a variety of techniques ranging from casting to cold hammering and heat treating (American Indian Peoples, n.d.).
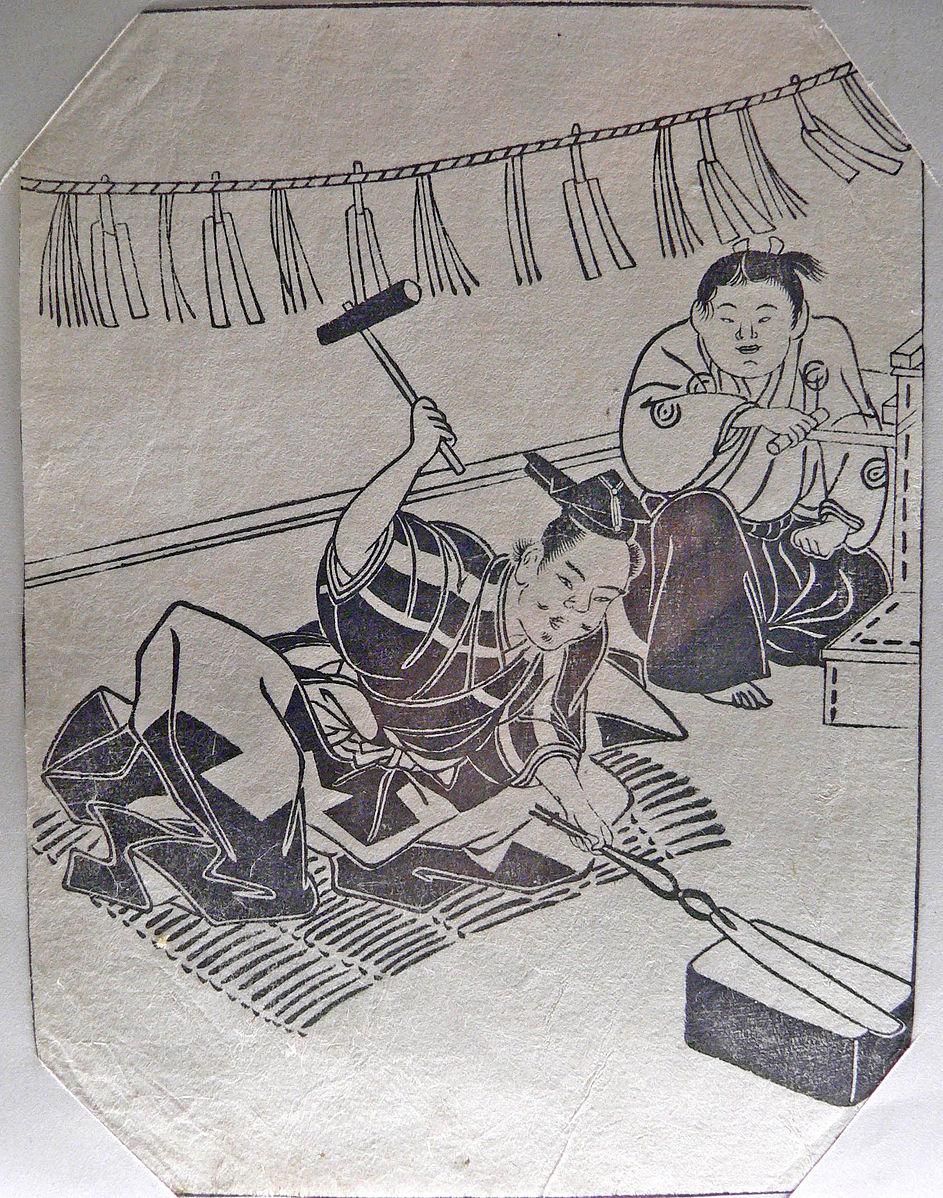
Development of Modern Welding Processes
Electric arc welding, resistance welding, and oxy-fuel welding processes were invented and being developed in the 19th century. The first practical arc welding process was carbon arc welding, developed by Nikolay Benardos of Russia in 1881. However, these modern welding processes did not become widely used until World War I (Miller Electric, 2020).
Arc welding was used primarily by England and Germany during WWI in the manufacture of ships and airplanes. Shortly after WWI, automatic wire feed welding was developed, followed by heliarc or gas tungsten arc welding (GTAW), then a variety of electric welding processes including inert gas shielded welding and flux-cored wire feed welding. Today there are over a hundred different welding processes, with more being developed (The Crucible, n.d.).
Metal alloys are also continually being developed by metallurgists to enhance weldability and mechanical properties. (Had the Titanic been built of modern steel alloys, it may have survived striking an iceberg.)
Modern civilization is dependent on metals and the people who join them together. This textbook will discuss the most popular forms of welding and basic information to help you begin your career as a welder.
Attributions
- Figure 1.1: Andrea di bonaiuto, apotesosi di san tommaso d’aquino, scienze ed arti 11 Musica e Tubalcain 3 by Sailko is released under CC BY 3.0
- Figure 1.2: Qutub Minar, Delhi by unci_narynin is released under CC BY-NC-SA 2.0
- Figure 1.3: Wrought iron gate detail, St. Philip’s Church, Charleston, SC by Spencer Means is released under CC BY-SA 2.0
- Figure 1.4: Scene-de-forge-edo-p1000665 by Rama in the Public Domain; Created in the Edo Period between 1603 and 1868.
bonding together of two objects of the same or similar materials, usually metal, through heat or force. This bond is at the molecular level and may include added filler material.
Welding that uses a flame heat source, often coal or coke, then physically forcing the the parts to bond by beating them with a hammer
craftspersons that use heat and hammering to fashion objects such as tools from metals, usually iron or steel. The term comes from the fact wrought iron objects oxidized to a black color.
Welding that melts the base metals together, bonding them at the molecular level.
A type of welding that uses the heat of electricity across an arc to melt the metal being welded.
An obsolete type of welding that creates an electric arc between two carbon electrodes.
process that adds filler metal in the form of a continuous wire that is mechanically fed into the molten weld
Gas tungsten arc welding is a manual welding process that uses a non-consumable tungsten electrode to produce the welding arc. A separate filler metal in rod form is added to the weld pool by hand. This process does not use flux and therefore requires an external shielding gas.
Welding that has a hollow continuous filler metal filled with flux. This flux protects the molten weld pool from that atmosphere and may also contain alloying elements.
Elemental metals that have other metals added to them to create a new metal with different characteristics than the pure, original metal.