1.3 Careers in the Welding Trade
Douglas Rupik, M.Ed., JIW
Industries That Use Welding
The main industries that you can build a welding career in are manufacturing (production or custom), maintenance and repair, construction, maritime, and pipelining. However, many careers or occupations may utilize welding yet not be classified as a so-called “welding career.” For example, an automotive or diesel mechanic may be expected to perform welding as part of their job, though that is not their primary responsibility. And in the construction industry, ironworkers, piledrivers, millwrights, and other tradespeople may be expected to have the ability to weld.
According to Zippa (2023), welders work in a variety of industries:
- 31% work in manufacturing,
- 14% are considered “professional,”
- 10% work in construction,
- 9% work in the transportation industry,
- 7% work in automotive,
- 5% work in technology,
- 4% work in energy,
- and the rest work in a variety of industries ranging from retail to education.
As you learn about welding while reading this book and consider which industry you wish to work in, ask yourself some questions. First, which welding process might you prefer to work with? Flux-cored arc welding (FCAW) is commonly used in construction, maintenance and repair of equipment, building facilities, and in the maritime industry. FCAW, gas metal arc welding (GMAW), and GTAW are commonly used in manufacturing and custom fabrication work. GTAW and shielded metal arc welding (SMAW) are commonly used in pipe welding.
The next question to consider is in regards to your temperament—what would you want in a welding job? For instance, working in construction may pay well, often requires you to work in inclement weather, may offer less job predictability, is often hazardous, and frequently involves travel. Working in manufacturing usually offers more consistent work hours, is inside work, and allows you the consistency of going to work at the same shop each day. Manufacturing tends to be repetitive but provides fairly stable employment. Custom fabrication is similar to manufacturing with the added challenge of building unique items per blueprint specifications, often requiring welders to have extensive creativity and problem-solving skills. Pipe welding is considered a specialty and requires a high degree of welding skill, frequently accompanied by higher pay rates. Working as a pipeliner often means traveling to jobsites with your own welding machine and other required tools.
No matter the direction you choose for a career path, a solid education in welding and the ability to weld with different processes not only increases your employability but also allows you to move between industries. A skilled welder can usually find a job almost anywhere.
In Washington state, welding job opportunities vary by region. On the coast and in the Puget Sound region on the western side of the state, there are numerous shipyards. In urban areas, the construction industry has been steady despite national fluctuations in the economy. Statewide, there are many manufacturers that employ welders, both in production and in building/plant maintenance realms. Many vendors supply the aerospace industry with fabricated components, too. There is also the potential for self-employment as a mobile repair or fabrication welder serving agriculture, industry, and the community at large.
Essay by April Cyaltsa Finkbonner
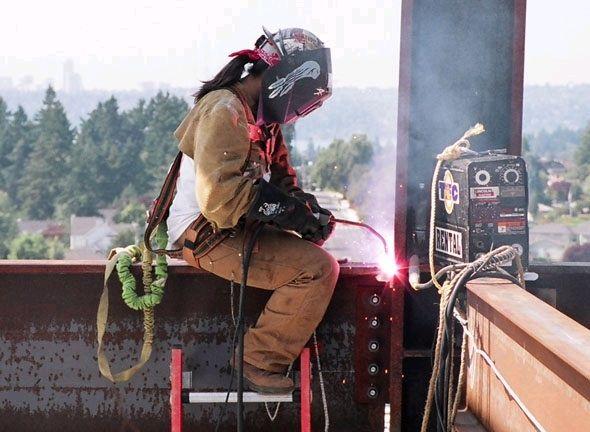
My name is April Cyaltsa Finkbonner and I am a journeyman ironworker from Local 86, Seattle, WA. I joined the ironworkers apprenticeship in 1995 and I am currently a welding instructor for the Local 86 apprenticeship program.
I was introduced to welding in my early twenties when my dad was doing some repair work on our commercial fishing boat. I was curious about what he was working on, and he said, “Grab that hood and come watch me.” After he finished welding a broken piece back together, I said, “Wow, that was cool.” He said, “You should look into welding. They say women make pretty good welders with their steady hands.” At that moment, I was immediately hooked on welding. I took his advice and registered at a technical college for a nine-month welding course. It was there that I found that FCAW was my favorite welding process. My welding instructors were suggesting that I pursue an apprenticeship program. I wanted to know what trade welded a lot with the self-shielded FCAW process, and they said, “The ironworkers.” I asked, “And what do they do?” My instructor replied, “They build bridges and skyscrapers and stuff.” I said, “Oh yeah? That’s what I want to do!”
So, I joined the ironworkers with my FCAW certification in hand. As an apprentice, I was able to take some of the welding dispatches that were not able to be filled by the journeymen, which meant that I was able to receive journeyman’s pay. As a journeyman, I invested most of my ironworker career as a production welder. In 2005, I was recruited to be a welding instructor for the apprenticeship and I consider myself blessed to have the opportunity to teach what I love. I highly encourage people who like to work with their hands to take a welding course and learn all of the different processes. They’re bound to find something that piques their interest. Once you have the welding skills, the career possibilities are endless, especially for the creative minds. If you need it, you can weld it. If you can imagine it, you can weld it. The opportunities are vast when you own the technical skills of welding.
Developing Industries and Technologies
As stated previously, there are over a hundred different welding processes today, with more in development. While most welders perform manual welding or semi-automatic welding, there are many career opportunities in specialized, high-tech welding.
Additive Manufacturing (AM) is quickly gaining ground in the industry. Complex metal parts can be precisely fabricated with different forms of additive manufacturing. Some resemble 3D printing, using a wire feeder and an electric arc or laser to continually melt and fuse the filler metal to the previous deposit. Other forms of AM use a metal powder that is melted with a laser in specific places, then covered with a layer of more metal powder, melted by laser to the previously melted metal, covered with another layer, etc., until the object is created.
Robotic welding has been around for decades, changing automotive manufacturing into an almost completely automated process. However, the cost of purchasing and maintaining robots as well as quality control issues in production have limited their use. Operators of robotic welders typically monitor the robot’s performance and perform welding repairs to any defects in the robot’s work.
Computer Numerically Controlled (CNC) welding incorporates computer control of robotic or automatic welding and may integrate the welding machine into other machining during the manufacturing process. For instance, metal parts may be loaded into the machine and then automatically welded and machined per the computer program.
The skills and training required to operate these various systems will influence the welder’s pay rate. Less training and skill required will likely mean lower wages, while more training and skill will likely ensure higher salaries for the welding operator.
With the increase of robotic/automatic welding process jobs, there will be a need for a skilled workforce to operate the equipment. However, we are still a long way away from a robot replacing people climbing a ladder and welding connections in a building or crawling around in a ship’s bilge to patch a hole in a leaky fuel tank.
Niche or “Boutique” Jobs
Along with the emerging automated welding jobs there are also opportunities in specialized careers. Due to the high level of skills and training required and the limited pool of available labor, some of these can pay quite well.
Commercial diver-welders may work underwater, though welding is performed “in the dry” whenever possible. Pay rates can be high because there are a limited number of workers in the field, the hazards inherent in the work, and the expense of required training. Careers in commercial diving and underwater construction are challenging and rewarding due to the job’s physical demands.
Many artists use metal as a sculptural medium and employ welders, blacksmiths, and other helpers in their studios. Like other artists, one’s income depends on the success of selling the art produced and the amount of money patrons are willing to invest in the artist and studio.
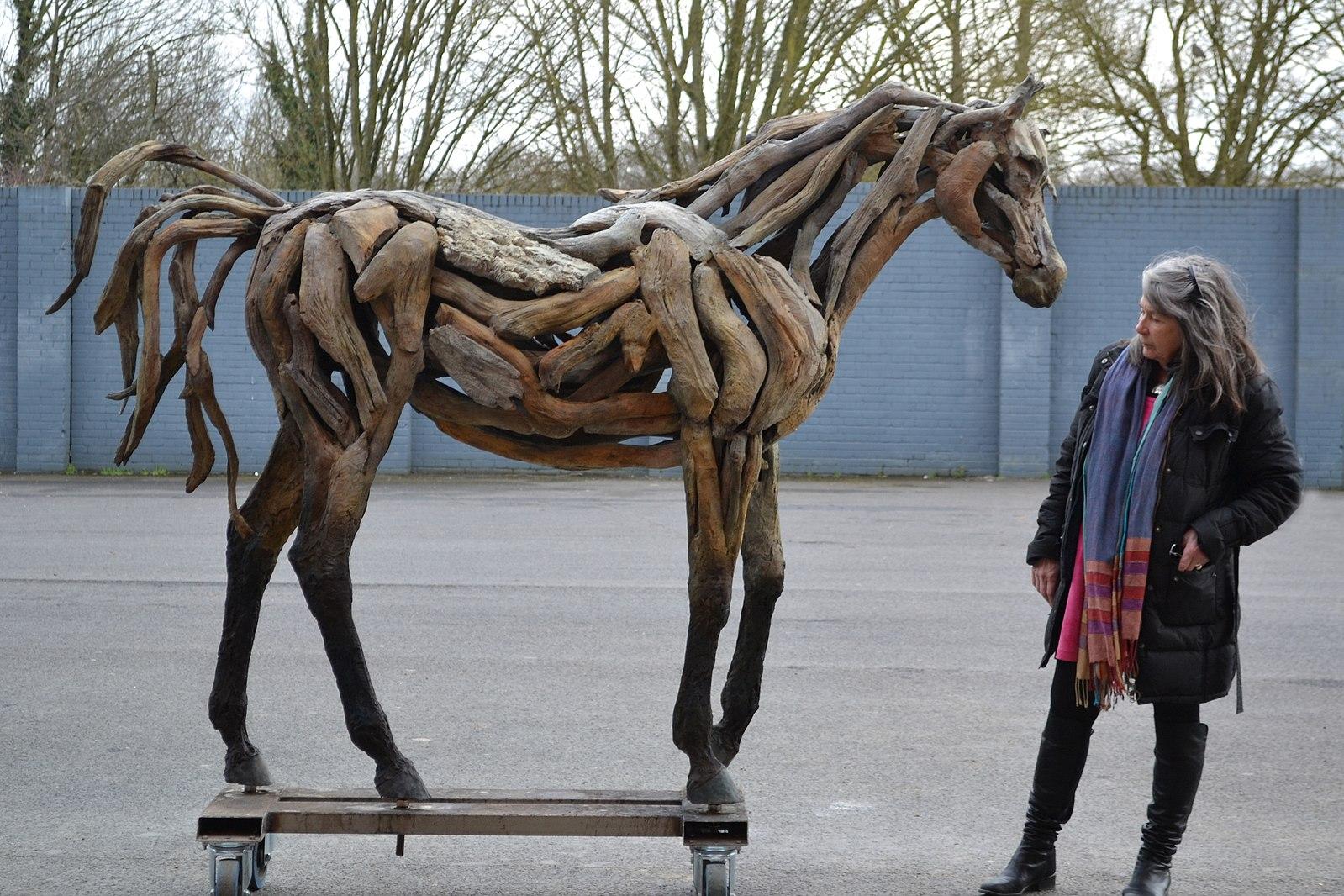
Restoration of classic cars or custom fabrication of cars requires the ability to work with thin metals and produce not only safe but visually unidentifiable welds. If new body components like fenders are added or modified, the welded seams must be invisible after painting. Frames or roll bars of race cars must be strong enough to endure the constant punishment of a track or off-road race without failing. Welding of custom exhaust headers must be leakproof and aesthetically pleasing.
Creating custom architectural features such as fireplace surrounds, exotic handrails, or furniture requires a high level of fabrication skills, including blueprint reading, precise layout, and quality welding. Many welds will be visible on the finished product and must be uniform and strong. Attractive welds are frequently preferred over welds that are ground flush and hidden.
Privatized space travel and emerging space tourism have opened up new jobs in the aerospace industry, not only in fabricating parts for spacecraft but in the building infrastructure and jig assemblies required to facilitate constructing spacecraft.
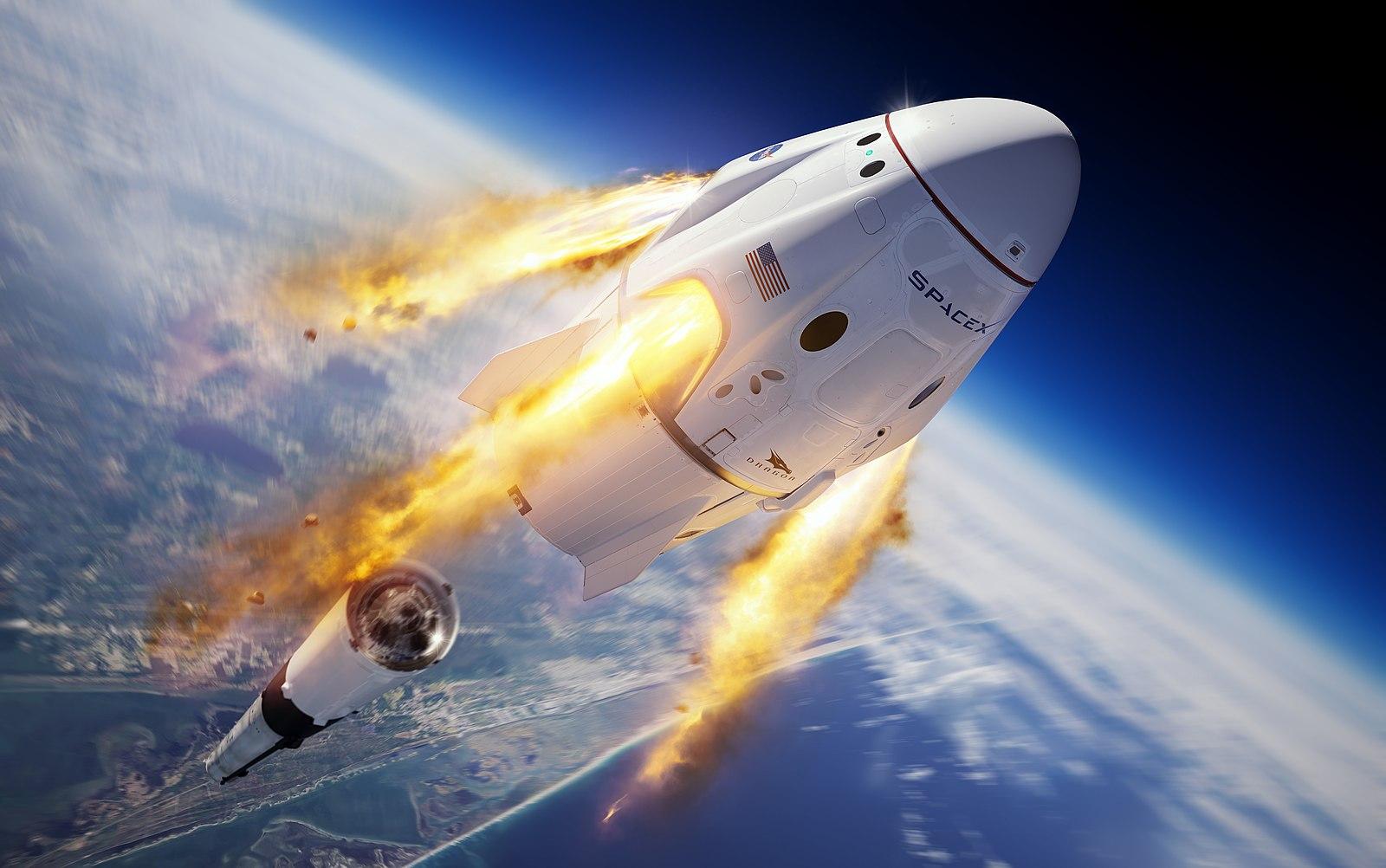
What Employers Look For When Hiring
Of course, employers desire specific welding and fabrication skills, namely time in the trade (journeymen level represents several years of experience). They usually administer pre-employment skills testing through a welding or fabrication test to verify your skills. Jobs requiring welding certifications or proficiency in multiple welding processes often pay more than jobs that do not.
Usually employers focus on only one or two welding processes and only expect their employees to show proficiency in those processes. Custom fabrication shops are the jobs that most likely expect welders to be proficient in multiple welding processes, like SMAW, GTAW, GMAW, and FCAW. However, this is not expected in every fabrication shop. The obvious advantage of attending a trade school or college for welding training is that you are more likely to receive training in multiple processes, thus increasing employability.
Fabrication, or “fitting,” is a skill distinct from welding. While fabricators use welding, their main task is to read and interpret blueprints and use that information to build the assembly described in the blueprint. The fabricator may weld the assembly or simply tack it together with small welds for a welder to complete welding afterward. Fabricators must be able to read tape measures to the one-sixteenth of an inch, use other measuring tools, accurately mark and cut out parts, build jigs and fixtures to facilitate building multiple assemblies at a time, and safely use various hand and power tools. In short, employers depend on a fabricator to be able to look at a blueprint and create the object in real life.
While training for a career in the welding industry, developing strong welding and fabrication skills is essential. Today, these soft skills are also becoming a high priority with employers:
- good attendance,
- social skills,
- ability to receive training and feedback,
- openness to working with diverse groups of people,
- capacity to clearly communicate (orally and in writing), and
- knowledge for how to use technology to find work-related information.
Make good attendance a priority and arrive early enough to start on time. The best welder in the world is useless to their employer if they are not at the jobsite welding. Avail yourself of opportunities to take diversity, equity, and inclusion training to learn about others and develop a self-awareness of how your words and actions impact others around you. The world’s best welder has increased value if they can get along well with their coworkers. Typically, a degree in welding requires you successfully complete other academic classes such as English and psychology—it is advantageous to view these classes as opportunities to develop the communication and social skills that employers value. The same is true of computer literacy courses: manufacturing more and more uses CNC and other computer-controlled processes, and even the construction industry is using tablets in the field for functions such as accessing digital blueprints and recording data (including the hours you work and expect to be paid for).
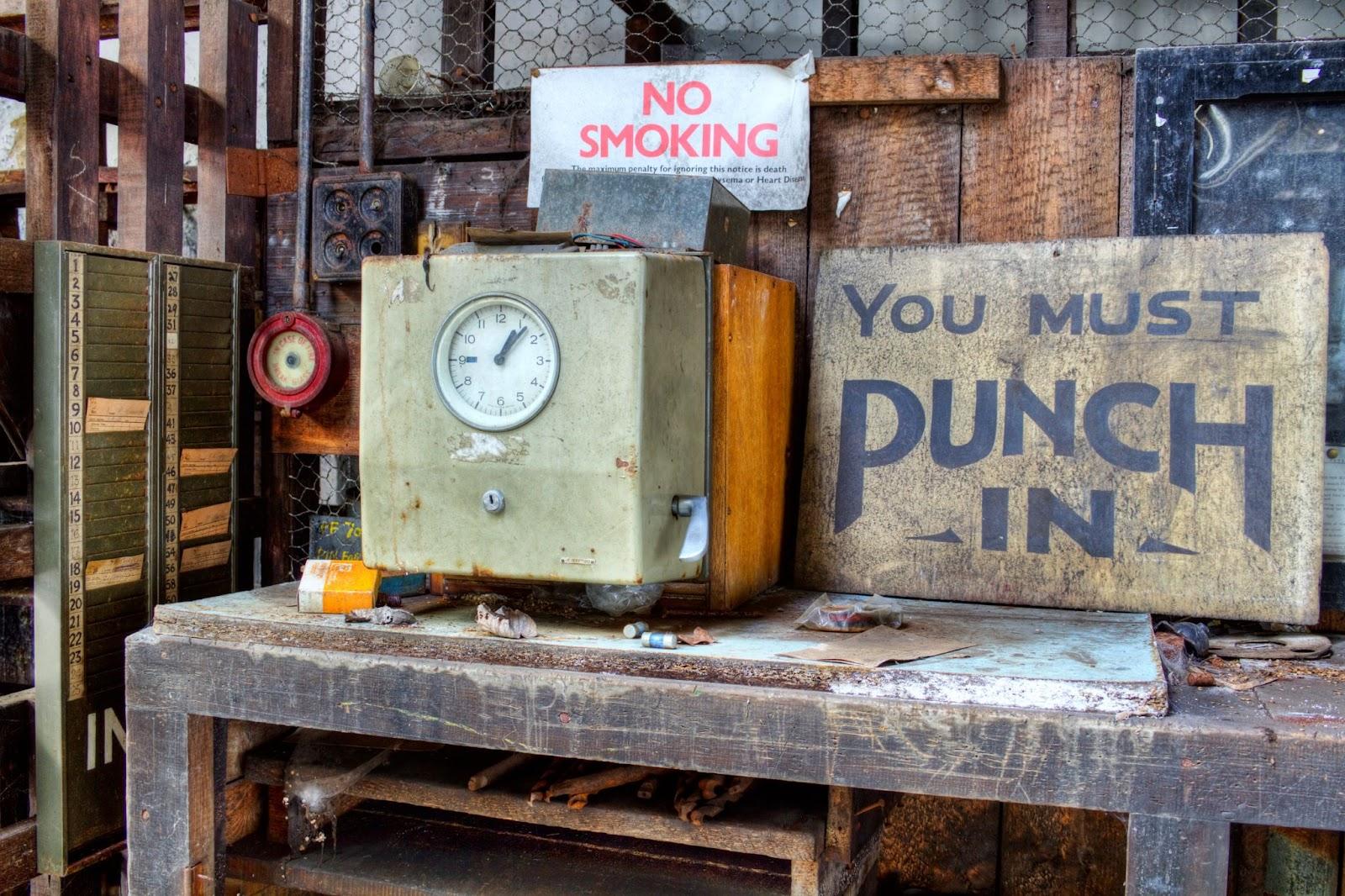
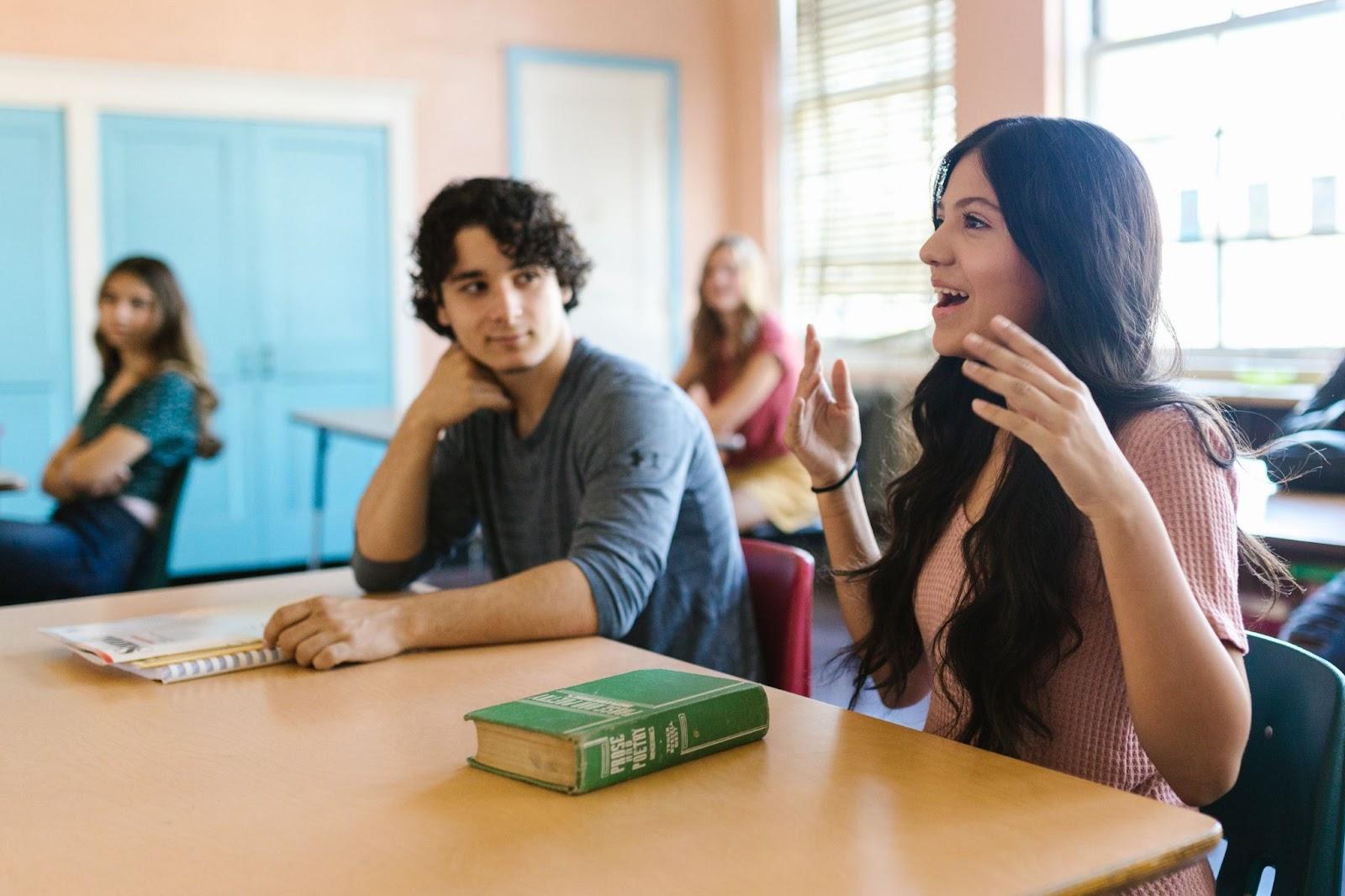
Attributions
- Figure 1.6: © used with permission
- Figure 1.7: Sculptor Heather Jansch next to her work “The Young Arabian” by Kieronjansch is released under CC BY-SA 4.0
- Figure 1.8: SpaceX In-flight Abort Illustration by SpaceX is released under CC0
- Figure 1.9: Punch Clock by Tom Blackwell is released under CC BY-NC 2.0
- Figure 1.10: image released under the Pexels License
Flux cored arc welding is a semi-automatic welding process that uses a tubular wire electrode filled with flux that is fed from a wire feeder through a welding gun. Depending on the type of flux, this process may or may not require an external shielding gas.
acronym for gas metal arc welding
Shielded Metal Arc Welding. Commonly known as stick welding.
Type of arc welding that is done by hand. The length of the welding arc is controlled by the welder’s hands.
A type of arc welding that has an electrode/filler metal that is automatically fed into the weld by a machine. The welding power source controls the length of the welding arc.