11.1 History of GTAW
Karl Fulton
Development of GTAW
Working for Northrop Aircraft Inc., in 1942 Russell Meredith patented a welding torch that utilized inert gas. His invention was born from the challenge to produce a welding process that worked for magnesium and other non-ferrous materials that bring specific challenges. Magnesium was already being used in aircraft to reduce their weight, but was limited to extruded and riveted parts because magnesium burns at temperatures above 883 degrees Fahrenheit., making other welding processes unsuitable. Russell Meredith’s solution for this predicament was to blanket the electric arc and molten weld pool with inert gas. You can see the original sketch of the welding torch in Figure 11.2.
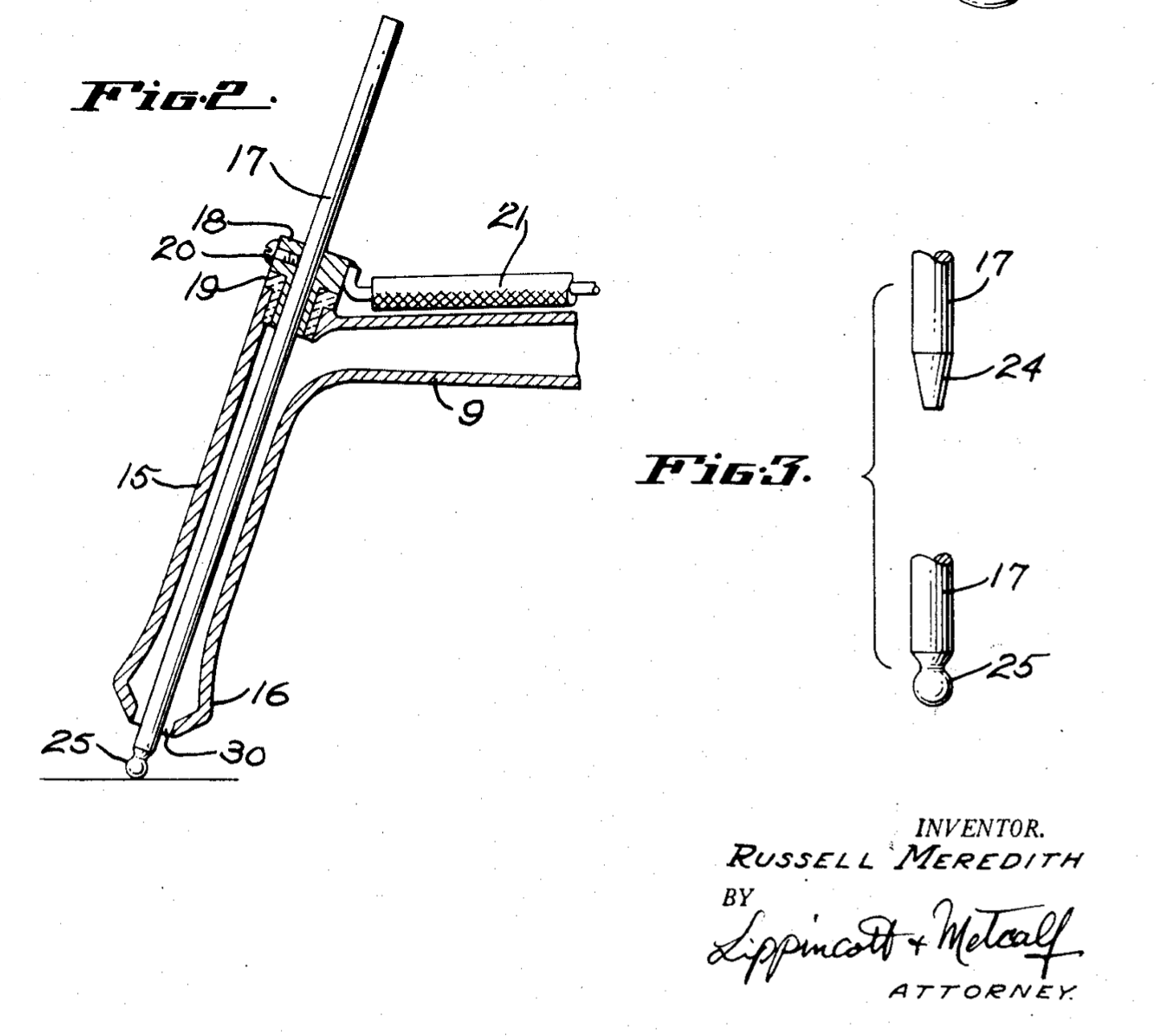
Since its initial invention there have been many advances in GTAW, from the alloying elements used in the tungsten to water-cooled torches, power sources using different polarities, the ability to customizing the alternating current (AC) wave, and even automation. Let’s look more closely at the process.
Basics of the Process
The GTAW process involves an intense arc between the base metal and a tungsten electrode to create a molten puddle. The intensity of this arc is controlled by a foot pedal or a handheld device that can vary the machine’s amperage. After establishing a molten puddle, filler material is added—however, there are applications where no filler material is added, called an autogenous weld. The arc, electrode, and weld zone are surrounded by an inert shielding gas (usually argon, helium, or a mixture of the two) that displaces the air and eliminates the possibility of weld contamination by the oxygen and nitrogen present in the atmosphere. The tungsten electrode has a high melting point that makes it virtually non-consumable. But that quality does not make it indestructible, and tiny bits of tungsten can spit into the weld and create inclusions.
Advantages of GTAW include the following:
- Welding can be done in all positions.
- The weld is usually equal to the base metal in composition.
- Flux is not used; therefore, finished welds do not require cleaning of corrosive residue.
- Smoke or fumes are not present to obscure vision; therefore, you can easily see the welding process.
- The process gives you a high level of control of the weld puddle.
- No spatter is produced because metal is not transferred across the arc.
Disadvantages of GTAW include the following:
- Material needs to be extremely clean, and material preparation takes more time.
- Portability is reduced because of the need for shielding gas.
- Welding outdoors requires extra caution; winds of 5 mph or more will disrupt your shielding gas, leading to contamination and porosity.
- It is a slower welding process and may lead to excessive heat input.
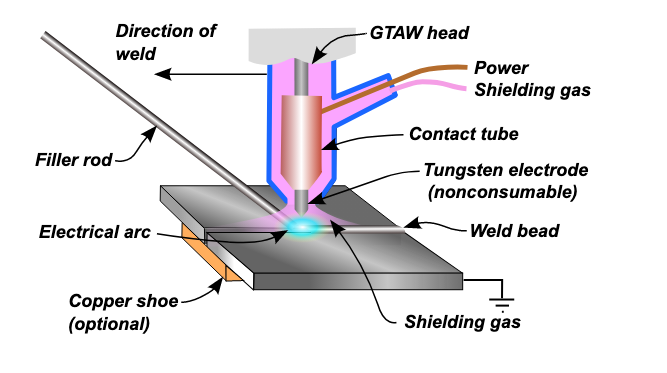
Uses of GTAW in Industry Today
An industry that frequently utilizes GTAW is aerospace and spacecraft due to the process’ ability to weld exotic materials like titanium and Inconel. GTAW is also used for making food processing equipment, which require extremely clean stainless steel welding; for casting repair for the wide range of materials that need miner repair; and in boilers and refineries because welding can be performed in tight spaces.
Attributions
- Figure 11.2: Welding Torch by Russel Meredith in the Public Domain; U.S. Patent: Subject to limited exceptions reflected in 37 CFR 1.71(d) & (e) and 1.84(s), the text and drawings of a patent are typically not subject to copyright restrictions (https://www.uspto.gov/terms-use-uspto-websites).
- Figure 11.3: GTAW by Duk is released under CC BY-SA 3.0
Elements that are virtually unresponsive to other elements. Inert gasses include: helium (He), neon (Ne), argon (Ar), krypton (Kr), xenon (Xe), and radon (Rn).
Welding with no added filler material