11.3 GTAW Electrodes and Filler Rods
Karl Fulton
Electrode Classification
The tungsten electrode has many different alloys that affect the arc starting, stability, and longevity. These tungstens are color-coded for ease of identification. This section covers a few of the main alloys of tungsten you will see and use. It is important to be aware that new alloys are still being developed for specific purposes, such as for stainless steel, aluminum, and robotic welding. Let’s discuss old and new tungsten.
The Old Guard: Green and Red Tungsten
Green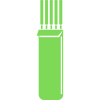
The color green indicates that the tungsten electrodes are 99% pure. Green tungsten is used in AC welding of aluminum and magnesium. The end of the tungsten will ball as you weld, giving good arc stability and relatively good resistance to contaminating the weld. Green tungsten is to be used with transformer machines only.
Red: 2% Thoriated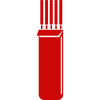
The color red indicates that the tungsten contains 2% thorium. For a number of years, this was the most commonly used tungsten because of its versatility. It has a long service life, easy arc starting, high current capacity, and good resistance to contaminating the weld.
Red 2% thoriated tungsten is used for welding carbon steel, stainless steel, nickel alloy, titanium, and copper. However, it cannot be used for AC welding. The tungsten will not ball and it will contaminate the weld. Proper caution should be taken when using this tungsten because thorium is radioactive.
New and Improved Tungsten
Gold:1.5% Lanthanated and Blue: 2% Lanthanated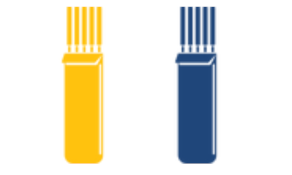
Gold and blue tungsten are alloyed with lanthanum, giving them very strong characteristics such as easy arc starting, reignition, and arc stability. Gold 1.5% and Blue 2% tungsten each have a long service life and resistance to thermal shock when pulse welding. They have high resistance to contamination and will maintain an arc at a very low current. These can be used in DC and AC welding, making them incredibly versatile.
Gray: 2% Ceriated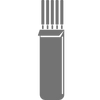
Gray tungsten contains 2% cerium. It is excellent for very low amperage starting, and it has good arc stability and a long life. This tungsten performs very well with both AC and DC welding.
White: 0.8% Zirconiated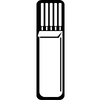
White tungsten produces an extremely stable arc, maintains a balled end, and is highly resistant to contamination and spitting. White 0.8% zirconiated tungsten is used for AC welding when contamination is intolerable. This tungsten handles high amperage for welding aluminum and magnesium alloys. It is a good replacement for green (pure) tungsten if needed.
Purple: Rare Earth Trimix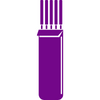
Purple tungsten contains some lanthanum, zirconium, and yttrium. It is a good substitute for red 2% thoriated tungsten. It is very durable and produces reliable arc starts, and performs well in both AC and DC welding applications. Purple tungsten is used for welding aluminum alloys, magnesium alloys, titanium alloys, nickel alloys, copper alloys, low-alloyed steels, and non-corrosive steels.
Maintaining Tungsten
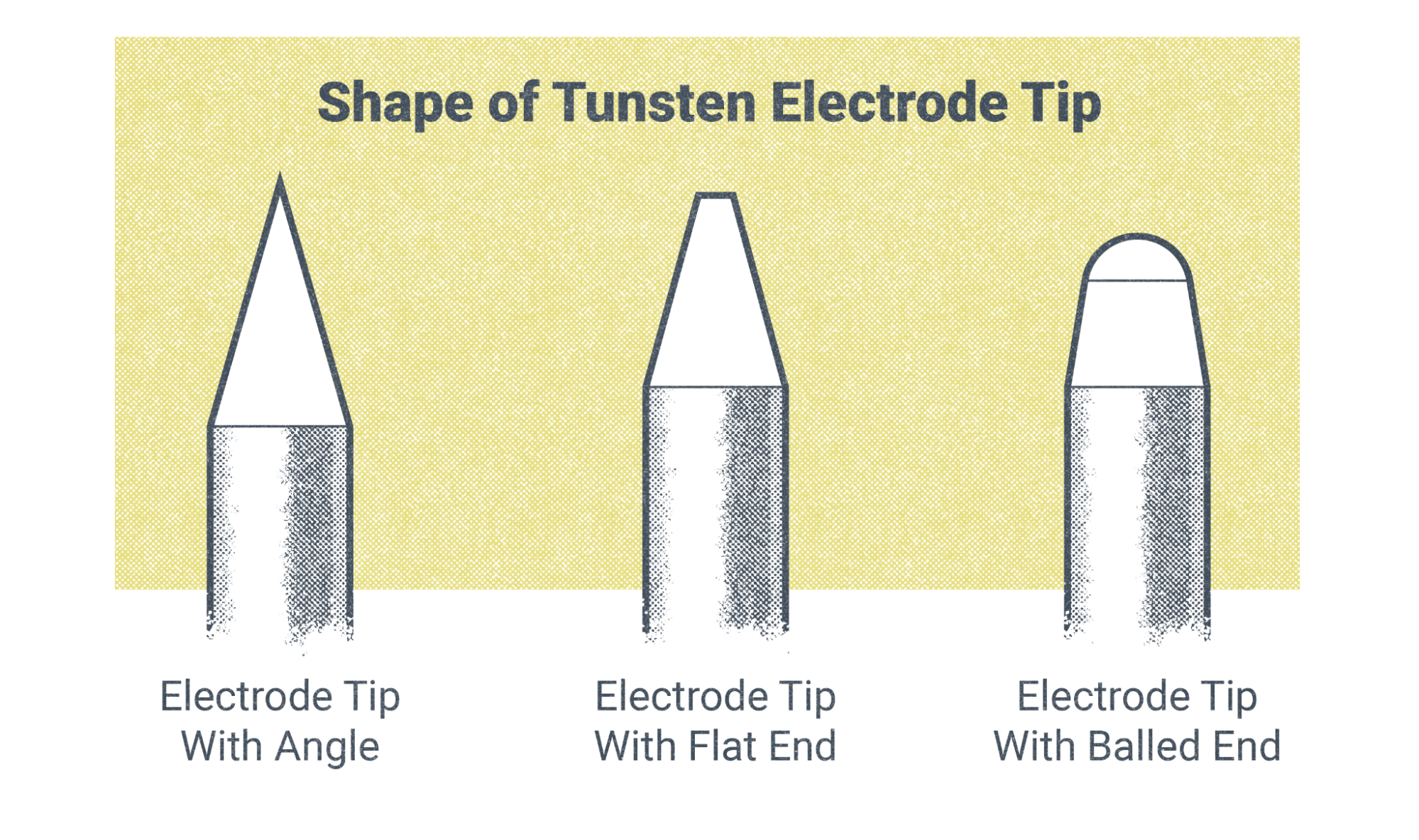
Maintaining your tungsten tip is critical. When welding with a DC application, you will want to sharpen the tip to a point to give you maximum control of your arc. After sharpening, blunt the tip slightly to prevent small bits of tungsten from falling into the weld and creating inclusions. It’s also a good practice to strike an arc on a piece of scrap for a few seconds before you start to weld—this further reduces the possibility of tiny bits of tungsten from falling into the weld.
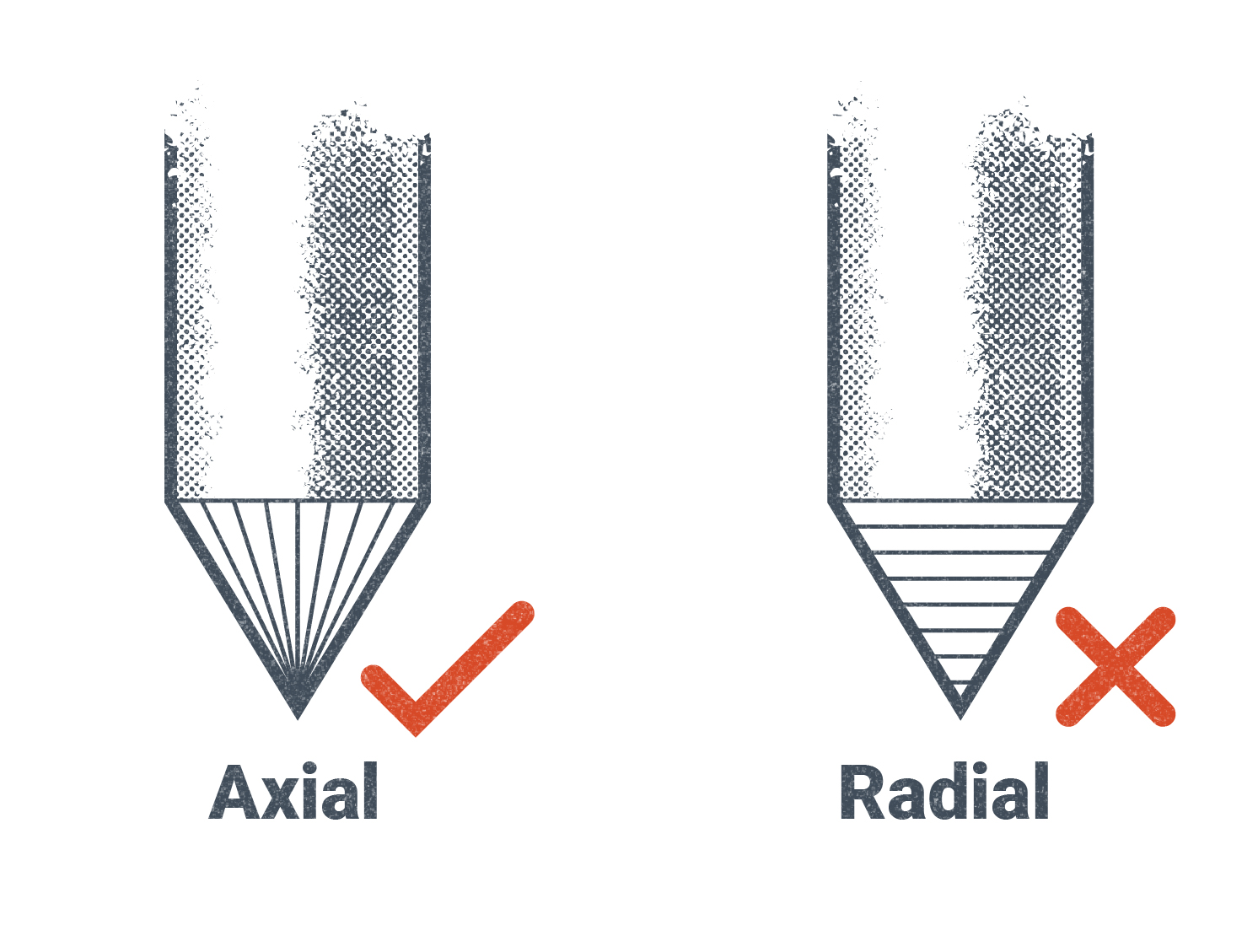
When sharpening, make sure all grooves are axial, or vertical in relation to the tungsten (see Figure 11.12). This helps direct the arc to the tip of your tungsten. Grooves going around the tungsten, in contrast, would create an unstable arc.
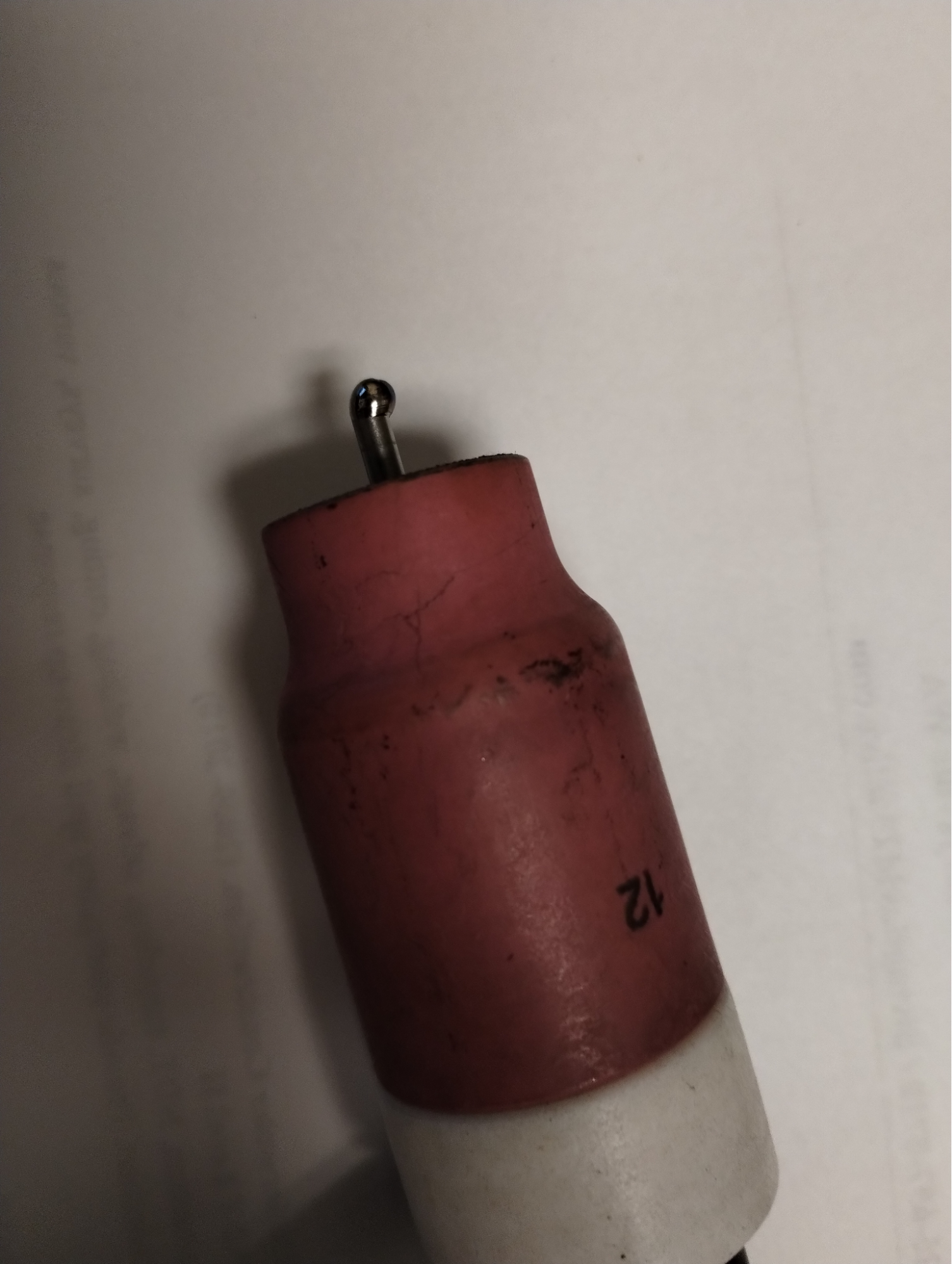
Another important factor in maintaining tungsten is knowing how to properly ball a tungsten tip to clean and remove oxidation for the weld pool. The profile of the tip you are looking for is rounded like the tip of your pinky, not like your fist. This practice is used with pure (green) tungsten electrodes when welding with a transformer-type power source and can be accomplished in multiple ways.
One method is to set the machine to reverse polarity and strike an arc for a second or two. Watch your tungsten closely as the end begins to ball up. You do not want to overdo it; just let the end round a little.
Another balling method is to set the machine on AC and strike an arc on a piece of scrap metal. It will take a little longer for the tungsten end to ball with this approach, but eventually it will happen. You can adjust the balance of your machine to favor DCEP or the cleaning action, and your tip will ball more quickly. Be sure to adjust the balance after completing this task, as it would put excessive strain on your tungsten.
Electrode (Filler Rod) Classification
Classifications are the same for GMAW and GTAW even though the current is not conducted through the filler rod for GTAW. Let’s review some different filler rods and the classifications for each.
The classification for carbon steel filler rod is ER70S-2. The letters ER stand for “electrode” and “rod.” The number 70 alludes to the electrode’s tensile strength (in thousands of pounds per square inch). The letter S indicates the electrode is composed of solid wire. And the concluding digit 2 is its chemical composition, which shares how much deoxidizer is in it or if it’s a certain type of alloy.
The classification for stainless steel filler rod is ER309-L. The ER prefix is the same as in carbon steel filler rods. For this filler rod, three numbers, 309, indicate the alloy for stainless steel. The letter L identifies that the electrode is low carbon.
The classification for aluminum filler rod is ER4043. Again, the ER prefix is the same as with the other filler rods. This time four digits, 4043, indicate the allow for aluminum.
Attributions
- Figure 11.11: Shape of Tungsten Electrode Tip by Nicholas Malara, for WA Open ProfTech, © SBCTC, CC BY 4.0
- Figure 11.12: Grind Grooves on Tungsten Tips by Nicholas Malara, for WA Open ProfTech, © SBCTC, CC BY 4.0
- Figure 11.13: Pure Tungsten with a Balled Tip by Karl Fulton, for WA Open ProfTech, © SBCTC, CC BY 4.0