13.3 CAC Operation and Techniques
Stephanie Oostman
General Uses
CAC can be found in several different types of welding environments. Some of them include fabrication shops, pipeline work, construction trades, even in underwater construction and demolition.
If a weld joint has shallow penetration, then the root can be back-gouged from underneath, cleaned with a grinder, then re-welded to add a better joint penetration. Back-gouging is the process in which the root of a joint is carved away via CAC-A from the backside. This allows the welder to then add a new root pass from the underside of the weld, adding reinforcement.
CAC is also used in superficial situations such as washing to remove material from a wide surface area. In washing, a welder weaves the electrode from side to side across the metal surface, maintaining a shallow depth as they push and weave the electrode across. This process will sweep or wash away superficial material in the electrode’s path, and is often used when the area needs to undergo hardfacing.
Another term you may hear in conjunction with CAC-A is scarfing. Scarfing is another shallow material removal process that does not damage the base metal like removing a backing bar from a weld test sample. The intention is to remove the metal backing strip without nicking or gouging into the base plate. The difference between gouging and scarfing is a matter of the depth of the cut, as scarfing does not dig into the base material and only removes surface items.
To repair a crack, it must be first dug out via gouging. In this scenario, the welder would need to carve into the base material as deep as necessary to remove the crack or discontinuity such as porosity. Because CAC leaves surface carbon behind, the welder will then need to grind and clean the area after gouging and prior to making a repair weld.
CAC can also be utilized to cut material and put a bevel on a groove. For example, this could be done to create a joint fit-up calling for a J-groove or a double U-groove. While this could be machined into the joint in some fabrication shops, it’s not always economical, practical, timely, or accessible to do so. In those cases, the welder can use round CAC-A electrodes to assist in carving the needed bevel into the joint to be welded.
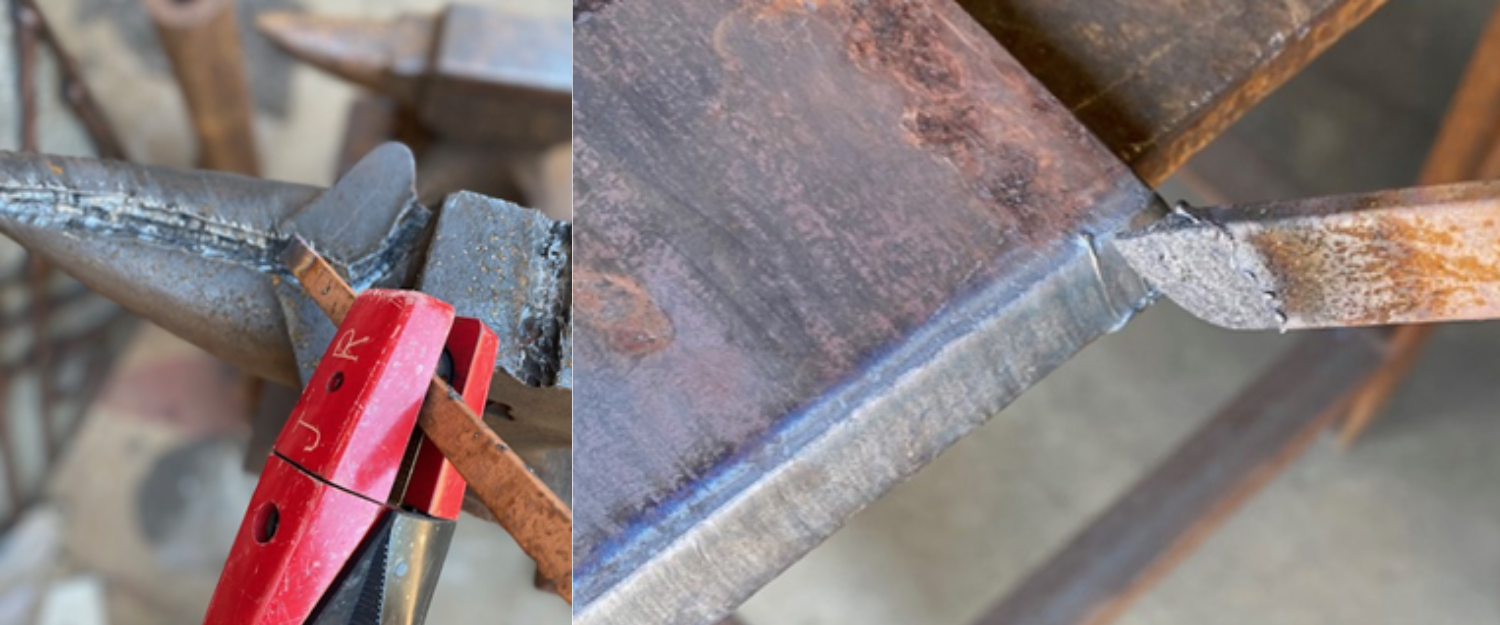
Operation Techniques
CAC-A can be performed in any position, however there are some basic techniques or considerations when operating a CAC machine.
When a vertical cut or gouge needs to be made in a work area, it is recommended to move the electrode in the vertical down position, also known as downhand. This ensures that the molten slag stays out of the path and moves downward more easily with the assist of gravity. Start your work at the top of the joint or area to be gouged and move towards the bottom. This will also reduce the volume of sparks produced.
When making a deep cut or gouge, welders will have to slow their speeds to keep the cut effective and maintain control. However, a shallow gouge will allow for the welder to move more quickly. The gouge left behind is typically 0.125 inches wider than the electrode used. Keep this in mind when making a cut so as to not exceed any tolerance callouts.
We have already learned that the electrode should be kept at a distance of 2–7 inches from the end of the holder; however, when cutting aluminum it is recommended to keep the electrode slightly closer, at more like 2–4 inches from the electrode holder. The welder must continuously adjust the rod position as it is consumed in the cutting process.
Initial gouges should not be deeper than one and a half times the diameter of the carbon electrode being used. If a deeper cut is needed, the welder would need to complete multiple passes until they reach the desired depth. Cleaning between passes may or may not be required.
Safety Considerations
CAC is a very loud process, capable of producing noises in a range of 108–120 dB. When subjected to this level of noise, both the welder and surrounding workers are at risk of hearing loss or damage. Therefore, it is recommended that anyone in the area wear appropriate ear protection and personal protective equipment (PPE).
The CAC process produces fumes such as carbon monoxide, and the electrodes contain irritants that include copper, graphite and silica crystalline. Some metals—such as stainless steels and metals containing zinc—release toxic fumes when welded or cut. All of these pose health risks, so welders should wear properly fitted respirators and safety glasses during cutting and gouging.
CAC-A is an electric arc cutting process; therefore, a welding helmet with the appropriate shade is needed to protect the user’s eyes from flash burns and potential blindness. As with all welding and cutting processes, operators should use flash screens to protect people and equipment from flying sparks, dross, and debris. Never point the debris at gas cylinders or electric cabling. Welders must keep the tops of their shoes covered to avoid molten metal from dropping down the tops of their work boots, uncuff their pant legs and sleeves if applicable, and only wear natural fiber clothing to avoid severe burns.
Attributions
- Figure 13.9: Carbon arc uses in the field by Stephanie Oostman, for WA Open ProfTech, © SBCTC, CC BY 4.0
the process in which the root of a joint is carved away via CAC-A from the backside.
to remove material from a wide surface area
A shallow material removal that does not damage the base metal.