2.3 Surviving Welding Industry Hazards
Douglas Rupik, M.Ed., JIW
General Industry Hazards
When beginning employment in a large fabrication shop or other similar environment, it is easy to be overwhelmed. Noise, flashing of arc lights, sparks, smoke, overhead cranes moving materials, and large machines in an area that may or may not seem organized or clean can also be a bit frightening at first. Hopefully your experience in a school welding lab will prepare you for your first work day in the industry.
OSHA identifies the most common health hazards associated with welding as exposure to metal fumes and UV radiation, and the most common safety hazards as injuries such as burns, eye damage, and electrical shock. See the OSHA Welding, Cutting, and Brazing website for specific hazards and safety solutions associated with welding.
Welding, by its nature, presents hazards: fumes and particulates; UV and infrared (IR) rays, heat, flames, and sparks; high amounts of electrical energy and electromagnetic pulses; and gasses that may be explosive or could cause suffocation due to oxygen displacement. These are hazards that directly result from welding processes and are in addition to the immediate and long-term hazards already discussed.
Let’s review these hazards and what can be done about them in more detail.
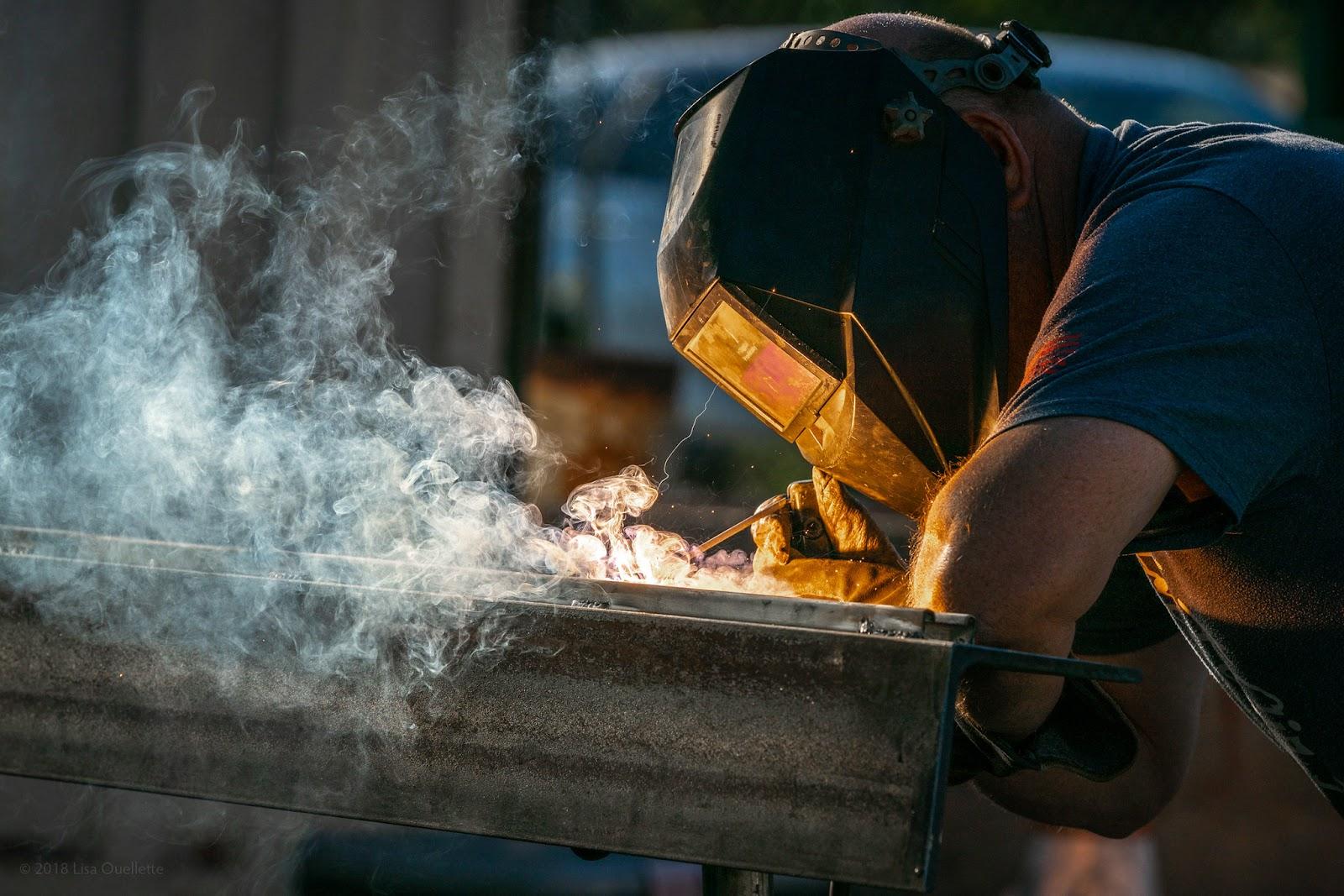
Welding produces smoke and fumes. GMAW and GTAW tend to produce less visible smoke than SMAW or FCAW-S, but do not be deceived into believing this means they are without hazards. For example, welding stainless steel produces hexavalent chromium, which is a known carcinogenic. Yet the lack of a heavy smoke plume in the process of GTAW on stainless steel makes it appear to be relatively harmless. But a welder may weld on stainless steel for years without using respiratory protection and not feel any immediate ill effects, yet be stricken with cancer as a result of that exposure.
Lead (from welding on lead paint), zinc oxide (from welding galvanized steel), stainless steel, and exotic metals such as Invar (an iron–nickel alloy) all produce hazardous fumes, so welders should use respiratory protection. Many of these heavy metals accumulate in the body’s tissues and, over time, can cause severe chronic illness. This buildup of toxins in your body does not give you resistance to the effects of exposure; instead, as you are exposed to more toxins over time, the likelihood of illness increases. For example, the illness known as metal fume fever results from welding on galvanized steel and creates fever, chills, nausea, and other flu-like symptoms. Each time you are exposed to fumes, it takes less exposure to bring on a possibility of sickness. Do not believe your veteran coworker who tells you milk is an antidote for welding on galvanized steel: milk only masks the bad taste of the zinc oxide.
Other fumes in the workplace can be dangerous. Welding on chlorinated brake cleaner residue can produce phosgene gas, which is the same as nerve gas used during WW1. Welding on cyanoacrylate glue (instant-bonding glue) can produce cyanide gas. Some degreasers or solvents produce toxic or explosive fumes and may cause illness, as they can be absorbed into your body simply by coming into contact with your skin. Know that every shop is mandated to maintain a Safety Data Sheet (SDS). These documents contain important information regarding every chemical you may be exposed to in your workplace so you can be aware of the risks.
Particulates, such as silica, carbide, and asbestos, become airborne by grinding, drilling into concrete, or disturbing fireproofing in buildings or ships. Once breathed in, they may become embedded in your lungs. Being an irritant, yet too small for your lungs to expel, your lungs form scar tissue over the particles. You may then develop silicosis or mesothelioma. Both are incurable, take a long time to kill you, and you get sicker and weaker the whole time you are slowly dying. Be aware that clothing may trap contaminants as well, and they can then be brought home, exposing your family members. In the future, OSHA may require all employers to provide fume extractors and other respiratory protection.
While you are in welding school, get in the habit of wearing a respirator at all times in the shop. Although once you start your first welding job you are likely to meet industry veterans who do not wear respiratory protection, pay that no mind. Wear your mask even if they don’t!
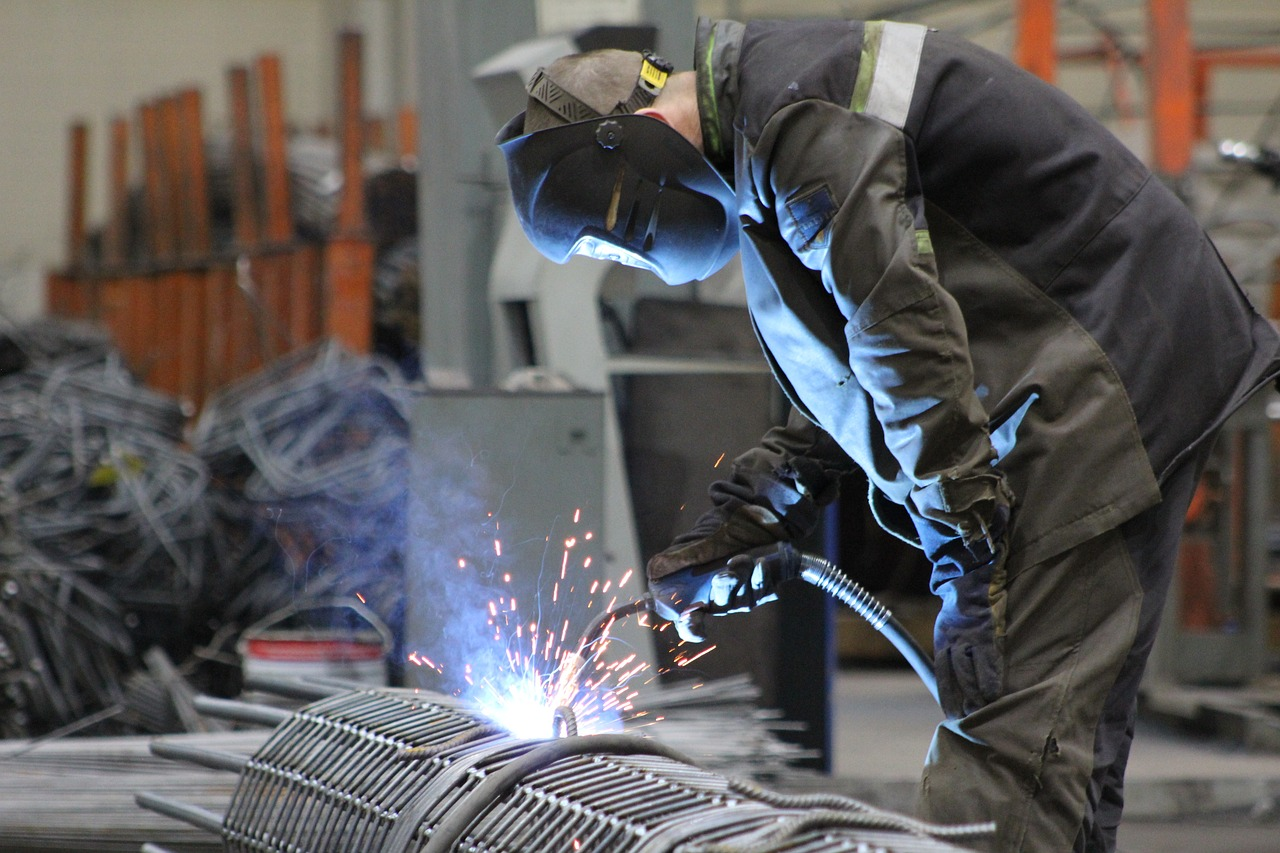
Arc welding processes produce visible, IR, and UV light waves. UV and IR are both capable of causing third-degree burns on the skin and capable of causing permanent damage to the eyes, including blindness. IR light waves give off heat that can be felt on your skin. Examples of IR are heat lamps in restaurants that keep food warm before serving. In contrast, UV light doesn’t feel like heat physically, yet it can produce third-degree burns in a short amount of time. This author first experienced a third-degree burn after one shift of GMAW welding on a factory assembly line. My welding helmet did not cover the base of my neck, which was exposed to the arc flash. The resulting burn and the medical treatment required was excruciatingly painful. You have been warned: never weld without adequate skin protection such as leather sleeves, gloves, and eye protection with the appropriate shade as described in this OSHA fact sheet about eye protection. Notice that the American Welding Society recommends a darker shade than OSHA does. You should weld using the darkest shade that will still allow you to see the puddle clearly. Make sure you keep your clear cover plates clean and replace them when your vision becomes obscured. Also, remember that reflected light from behind you can do as much harm as direct light exposure. Set up flash screens whenever possible to protect yourself and others from light and sparks.
Welding produces heat and often sparks that can cause burns or fires. Sparks are not merely tiny bits of flame but rather tiny bits of molten or glowing hot metal. Sparks produced by grinding can travel over long distances and some sparks, such as from aluminum, are not visible yet can still cause severe eye injuries. When grinding or otherwise producing sparks, wear appropriate personal protective equipment (PPE) such as leather sleeves, gloves, safety glasses, ear plugs, and a face shield (See Chapter 3). Be sure sparks are not directed toward people or machines that could be damaged. Glass is susceptible to being pitted and damaged by sparks and should be protected. Remove flammable materials from hot work areas. Fires can start and spread quickly. Always have a fire extinguisher handy when doing hot work.
Arc welding equipment, including plasma arc and carbon arc cutting equipment, operates with high primary and secondary electrical energy that can produce a fatal electrical shock. It is a good practice to wear gloves when handling electrodes, grounds, and other components that may be “live.” If possible, avoid working in wet environments or out in the rain. If you must work in wet conditions, wear rubber gloves and rain gear, and be aware that if you become the component that completes the electrical circuit, you will experience an electric shock, which could be fatal. GTAW, especially when using alternating current (AC) polarity, can introduce a powerful shock via the handheld filler metal.
Do not wear metal rings or bracelets while welding! These currents can melt a ring worn on your finger, resulting in a severe burn. Also avoid wrapping your welding lead around your arm or draping it across parts of your body, especially your reproductive organs. The electromagnetic pulse produced by the current may be harmful to you, and a welding lead wrapped around you can cause injury if it becomes snagged or entangled when you are passing heavy equipment.
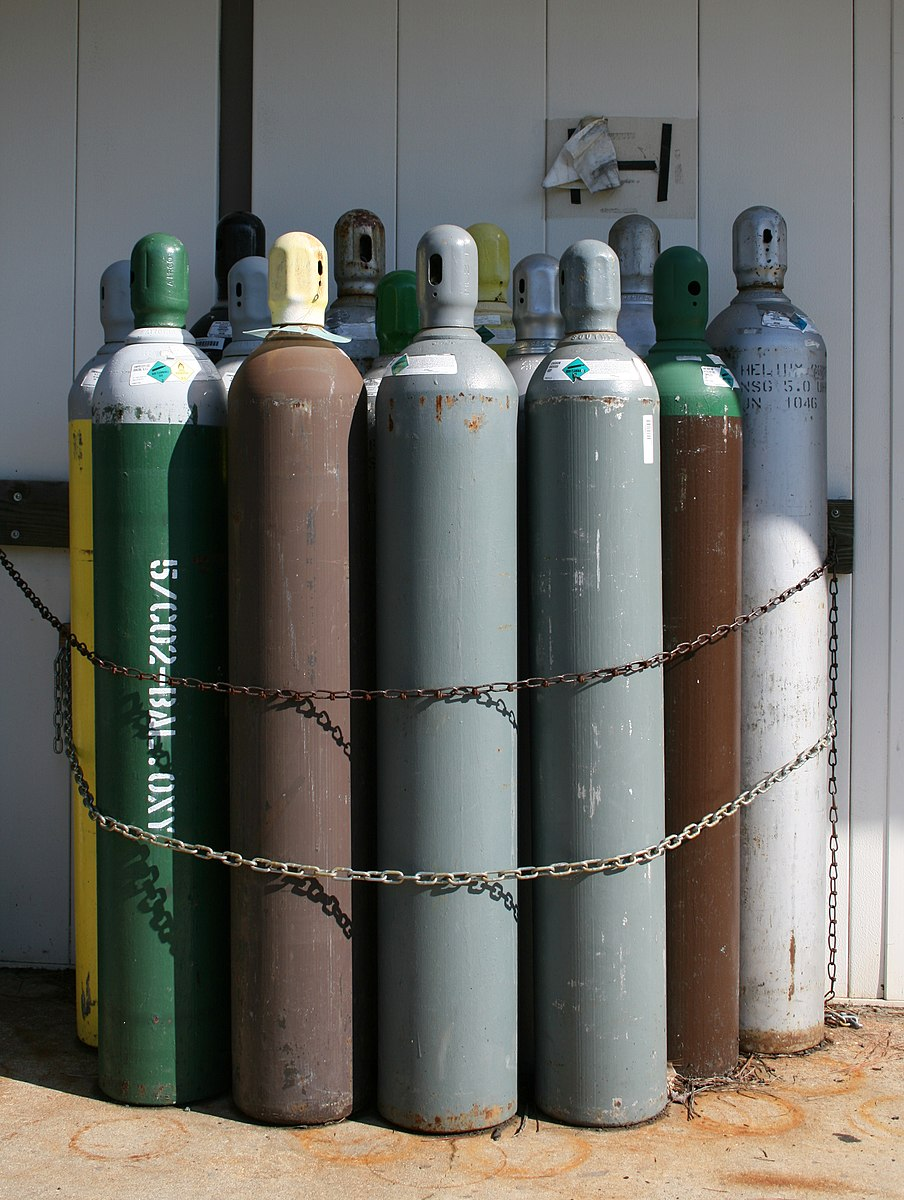
Many types of welding use gasses either as a source of combustion or as a shielding gas. If a coworker tells you breathing in argon or other gasses is good for curing a hangover, do not believe them. Rather, it could kill you. Acetylene, propane, and other petroleum-based gasses are combustible or explosive. If you smell gas, cease all hot work immediately and, if possible, locate the source and correct the hazard. You may have to notify your supervisor or warn everyone on the job site and ask them to evacuate, depending on the size of the leak and the workplace.
Also, never weld or cut on a tank or barrel that once contained fuel gasses or petroleum products! As a welder, you will likely be asked to fabricate a barbecue grill from an empty metal barrel. People die from cutting or welding on barrels that explode due to tiny amounts of fumes contained in them. If you wish to safely do hot work on a barrel, first determine what it originally contained. If it is a metal barrel, it likely contained petroleum, whereas plastic barrels that do not rust usually contained water. To safely weld or cut on a steel barrel that still has both ends attached, first thoroughly steam clean it using trisodium phosphate. It should then be filled with water or an inert gas such as argon or CO2 to displace any remaining fumes before proceeding with hot work.
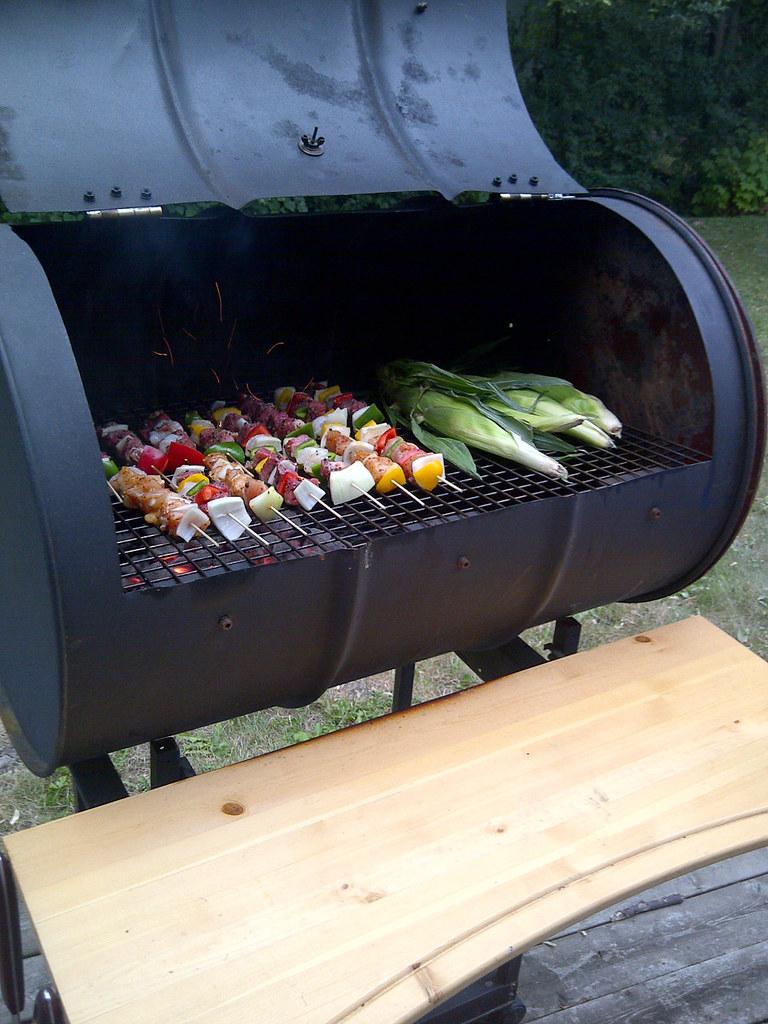
Shielding gasses such as argon are heavier than air, and may displace air in the same way water pushes air out of a ditch or pool when it is poured in. When working in a low area or confined space, be aware that heavier-than-air gasses may accumulate there and suffocate you. In one report from 2008, OSHA recorded that a welder in the bottom of a ship died from argon shielding gasses filling the bottom of the ship.
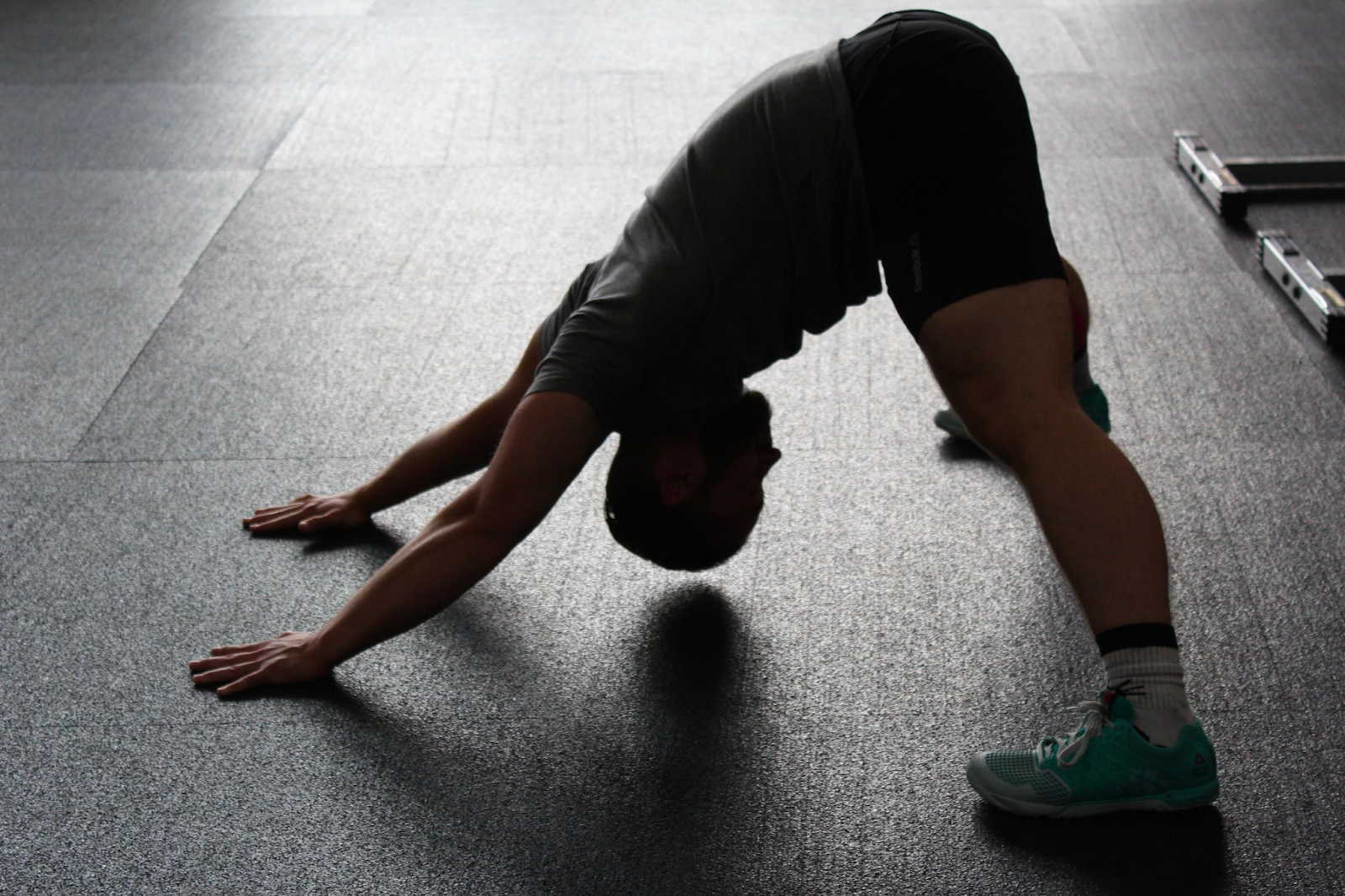
Welders must maintain fine motor control and often contort themselves into uncomfortable positions for long periods of time. In addition, many welding jobs require the worker to do more than just weld. Often you’ll need to lift heavy materials or equipment by hand (up to 100 pounds). For these reasons, you should keep yourself physically fit and practice pre-work stretches to reduce the chance of injury. Use your legs rather than your back to lift heavy items, and use machines such as forklifts and cranes to assist you whenever possible. When carrying long materials with others, avoid placing your hands in a “pinch point”—for example, when lifting a large pipe with another person, putting your hand on the end of the pipe can result in injury if your coworker pushes the end of the pipe you are holding into a wall. This author has seen people nearly lose fingers to pinch point accidents on two different occasions. Chains or wire ropes can also cause injury. When using them to hoist or drag materials, keep your hands clear of them at all times.
Never put your hand or finger in a place that could cut it off if something were to go wrong! And never use your hand when you can use a tool, be it a hammer or pry bar.
Most welding shops are noisy places due to grinding, sledgehammers hitting steel, or high-frequency AC GTAW. You should use earplugs to protect yourself not only from sparks but also from hearing loss. Once hearing is lost, it cannot be restored. If you work in a loud environment, try the radio test: Before leaving your car to begin work, turn your car stereo volume down to the lowest setting at which you can still hear it. After your workday is complete, see if you can still hear the radio when you return to your car. If you cannot hear your radio, it is likely you are slowly losing your hearing and need better hearing protection.
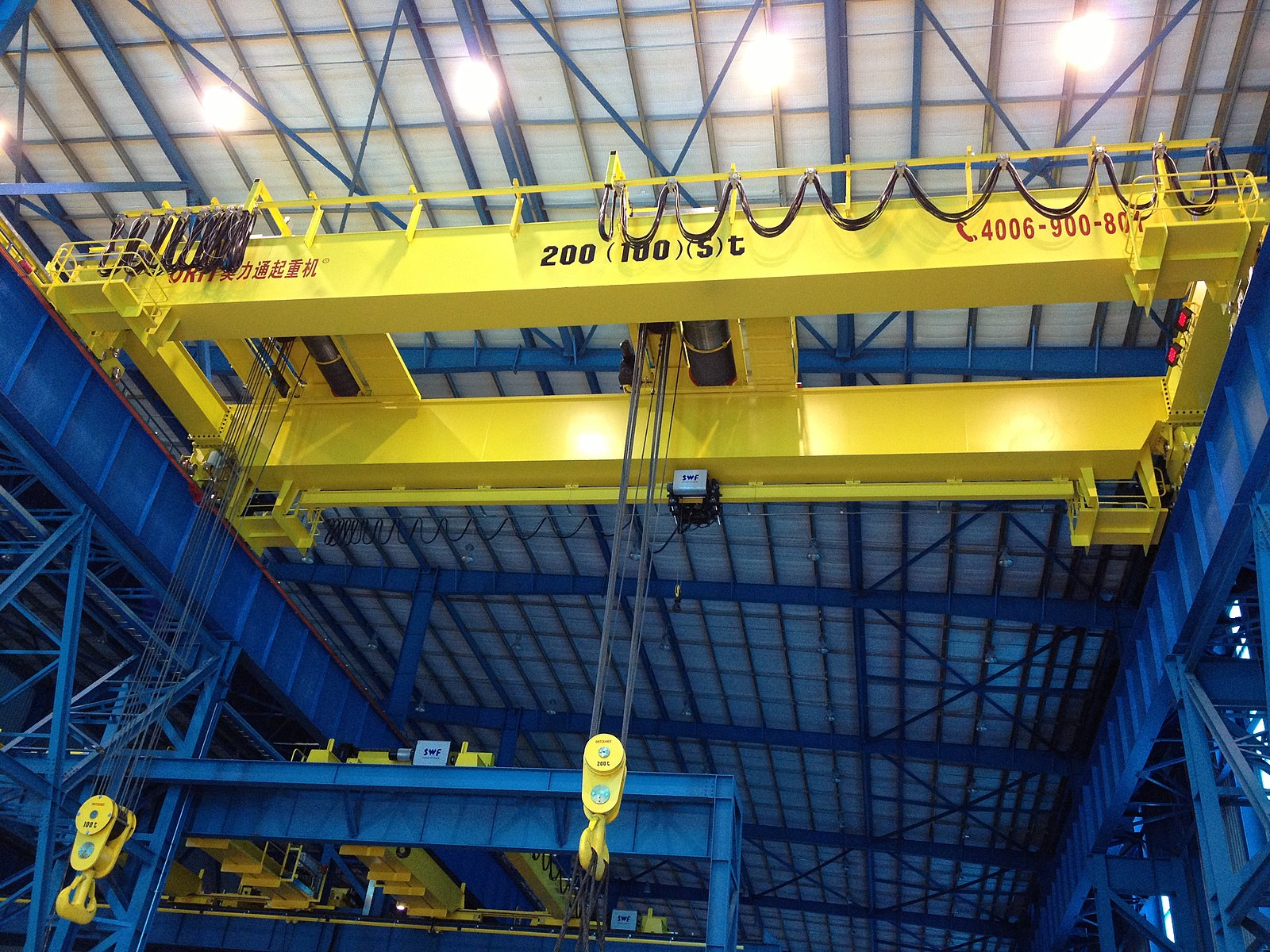
Many shops have overhead cranes and use large machines and other equipment. Do not operate any shop equipment without proper training from your employer or a qualified trainer. Maintain an awareness of any moving equipment. Avoid wearing earbuds to listen to music or podcasts, as they distract or isolate you from your surroundings. Do not let an overhead crane transport a load over you—instead, move out of its path of travel. Be aware of forklifts or other vehicles. Make eye contact with the operator and get approval from them before crossing their path. Many employers require their workers to wear high-visibility clothing to minimize the chance of workers being struck by heavy equipment. Follow these prudent guidelines.
Maritime Industry Hazards
Working in maritime, such as in shipyards, can expose you to all the hazards a welder encounters in shops and construction. But there are some additional hazards that other welders may not encounter, such as performing hot work around fuel tanks, working over water, working in confined spaces that pose potential hazards (such as physical entrapment and a dangerous atmosphere), and exposure to chemicals such as lead paint and asbestos if working on boats and ships that have been in use for years.
Welders in maritime industries are at risk for chronic illness influenced by workplace hazards such as respiratory hazards from fumes, chemicals, and particulates containing heavy metals. Shipyard welders in particular have higher rates of lung cancer and leukemia.
According to the National Institution of Occupational Safety and Health (NIOSH), fatal and nonfatal illness rates are higher among maritime workers than welders in other industries (NIOSH, 2022).
Construction Industry Hazards
Construction sites, especially on large projects, can be intimidating to a new hire. Often, you are exposed to the weather, you may be required to work high off the ground, and there may be heavy equipment, including cranes operating around you. Add to this the fact that the jobsite is constantly changing: new walls are going up, holes may be cut into the floors, and a staircase you used a couple of days ago may have been demolished and removed. Due to the changing nature and activity of other workers, you must be alert at all times.
The number one cause of fatalities in construction is falls (36%), followed by struck-by incidents (15%), electrocution (7%), and caught-between (5%) (NIOSH, 2023).
Falls are a hazard on many construction sites. A fall from an eight-foot-tall stepladder is often fatal due to the worker’s feet becoming entangled in the ladder rungs, resulting in the person falling backward onto their head versus recovering from the fall on their legs. Be sure to follow basic safety rules when working at elevated heights: Stay on the proper side of the safety railing, use appropriate fall protection PPE, use appropriate tie-off points, and follow the manufacturer’s recommendations for ladders and aerial lifts.
Struck-by injuries often involve heavy equipment or heavy objects being moved. Therefore, always wear a high-visibility vest, never turn your back on a crane load or even an empty hoisting hook when it is moving in your vicinity, and be sure heavy equipment operators are aware of your presence.
Electrocution is death by a fatal electric shock. Beware of overhead high power lines. The rubber coating on the lines is there primarily to protect the wires from corrosion, not to prevent electric shock. Coming in contact with them via the load line of a crane or other equipment can result in a fatality. Many construction-grade welding machines operate with a primary power of 480V. Accidentally cutting into a power cable, becoming grounded while wet, or otherwise exposing yourself to shock can result in your death.
Caught-between injuries usually means getting in between heavy equipment and a wall or other stationary object. Again, be sure the equipment operator is aware of your presence and never put yourself in a pinch point or a place where you can be crushed.
When considering a career in construction, you should seriously consider entering an apprenticeship training program that can provide industry-specific safety training on the job and/or in a classroom. Further, OSHA 10, OSHA 30, and Contractors Safety Orientation Program (C-STOP) are all construction-specific safety training certifications that you should obtain at the beginning of your construction career.
The Importance of Lockout/Tagout Procedures
A lockout/tagout standard involves physically disabling and de-energizing equipment before working on it or in its vicinity. There are many examples of people being killed while working on equipment because someone else turned on the machine without knowing it was being worked on. Powering the machine on could result in electrocution or result in the physical crushing or entrapment of a worker. According to one Accident Report Detail from OSHA, In 2012, a worker was cooked to death in an oven load of tuna due to the oven he was cleaning not being properly locked out/tagged out (OSHA, 2012). Lockout/tagout is a practice intended to prevent these types of death and injury.
In its simplest terms, when working on equipment that has the potential to cause injury the lockout/tagout process involves disabling or disconnecting the power supply and placing a lock over the connection point. Modern power disconnects have a special eyelet allowing a padlock to be placed on them to prevent access. The worker who places the lock is the only authorized person to have the key for that lock. A tag is also placed on the disconnect with a written note identifying the reason for the disconnect, the time and date, and the name and contact information of the person who placed the lock. The person with the key is the only person authorized to remove the tag and lock. If multiple people are working on a piece of equipment, a special “gang lock” mechanism will accept each person’s padlock. It will remain locked out until each person removes their individual lock.
It is the employer’s responsibility to develop and enforce a lockout/tagout procedure applicable to their job site that protects their employees.
Attributions
- Figure 2.7: Melting by Lisa Ouellette is released under CC BY-NC-ND 2.0
- Figure 2.8: image released under the Pixabay License
- Figure 2.9: 2008-07-24 Bundle of compressed gas bottles by Ildar Sagdejev (Specious) is released under CC BY-SA 4.0
- Figure 2.10: 55-Gallon Drum BBQ by James Bastow is released under CC BY-SA 2.0
- Figure 2.11: image released under the Pexels License
- Figure 2.12: Overhead Crane 200(100)(5)T by ORITCRANES by Alex.huang is released under CC BY-SA 4.0
A printed description of the hazards and safe use practices of chemicals found on a job site.
Tiny particles easily suspended in the air.
Work done on a job site that produces sparks or other means of accidentally starting fires.
Industries centered on shipping over water.
Step-by-step instructions on how to disable or de-energize equipment to make it safe to work on.