20.1 History of Welding Ferrous Metals
David Colameco, M.Ed.
The American Welding Society (AWS) defines welding as such: “A joining process producing coalescence of materials by heating them to the welding temperature, with or without the application of pressure or by the application of pressure alone, and with or without the use of filler metal” (American Welding Society, 2020). This definition covers a lot of different joining techniques, which is what makes the world of welding such a rewarding experience and career that can go in many different directions.
Welding has been performed for thousands of years. Metals were likely discovered by our ancestors when they were making fires near stones on sand. The heat from the fire melted the metal contained within the stones, which then oozed out. The importance of sand is that it makes solidified metal more visible to the naked eye, especially if there are only small quantities of metal that exit the stones. Our ancestors then found ways to use the metal to change their lives through improved quality of life, hunting, and defense or military purposes. Metals played such an important role in the development of civilizations that historians named whole periods of time after them, such as the Bronze Age and Iron Age.
The benefits of metal to societies are the driving force for metallurgical advancements. The authors of this book and your instructors are introducing welding to you so you can enter a rewarding career that benefits not only your life but society as well.
Before we start discussing welding, it is important to cover some other joining processes you may have worked with or heard of to put them into context: these are soldering and brazing. The main difference between welding, soldering, and brazing is the temperature at which each process operates. Soldering generally occurs at the lowest temperatures such that only the solder (applied like a filler metal) melts and the base metal does not. Brazing does not melt the base material, either. However, because welding has expanded so much, some welding processes may operate at lower temperatures that were previously used to define soldering and brazing regimes. For this reason, more modern definitions of the processes may remove the temperature difference—but, for our purposes of introducing the concepts, the older definitions are acceptable.
Mass production welding used oxy-fuel processes, such as oxy-acetylene. Today, oxy-acetylene is used more for cutting base material than it is used for welding (your technical program at school probably offers oxy-acetylene welding with a focus on cutting). Oxy-acetylene is a high-heat process that is great for metals that have high thermal conductivities (such as copper), which makes heating them up a time-consuming process.
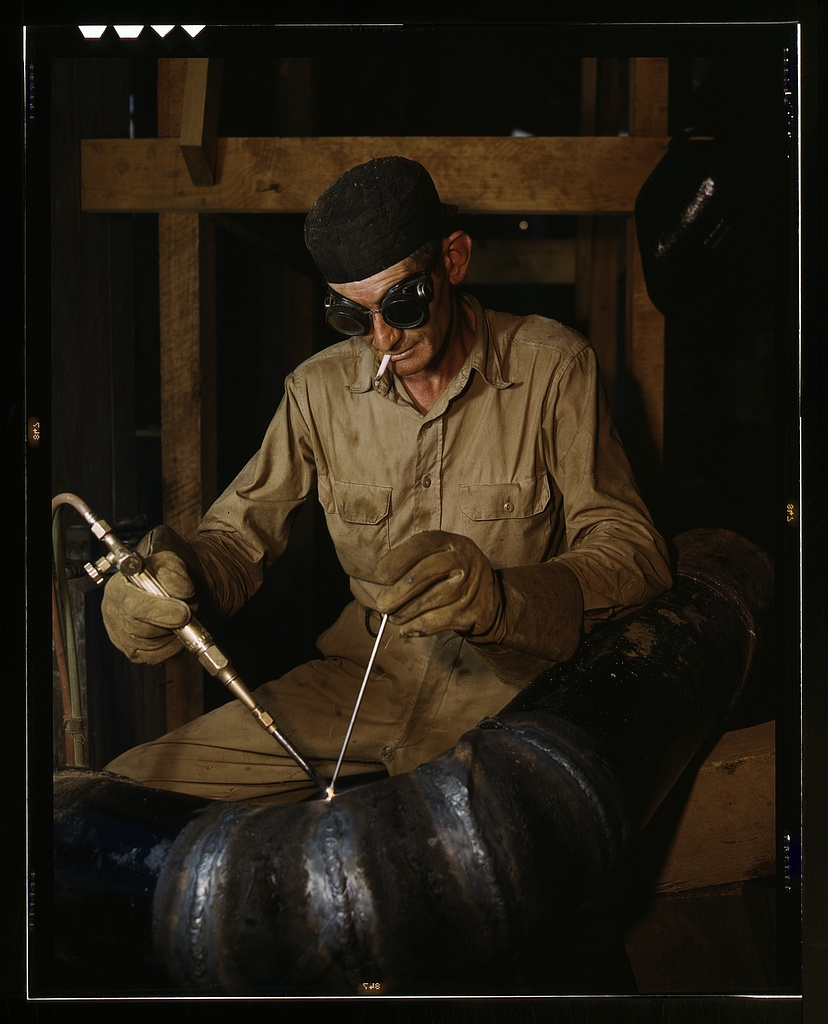
Chapter 12 in this textbook covers oxy-fuel cutting. As an overview, acetylene gas was first discovered by chemist Edmund Davy in 1836. It would be many years later that the oxy-acetylene welding process was invented: this occurred in 1903 by French engineers Edmond Fouché and Charles Picard (Aquasol Corporation, n.d.). Similarly in history, electricity generation was invented much earlier than many of its practical uses were implemented. For instance, electric generators were invented in the 1830s and Thomas Edison invented the lightbulb in 1879.
An early use of shielded metal arc welding (SMAW) is shown in Figure 20.2 with a farmer at a Farm Security Administration warehouse depot in Atlanta, GA.
Figure 20.3 depicts a farmer who benefited from an initiative called the U.S. Rural Electrification Administration in which the U.S. government made low-cost loans to farmers who banded together to bring electricity to the rural areas that housed their farms. The significance of this is that as electricity was made available at a reasonable price, processes such as electric arc welding were widely adopted by the masses.
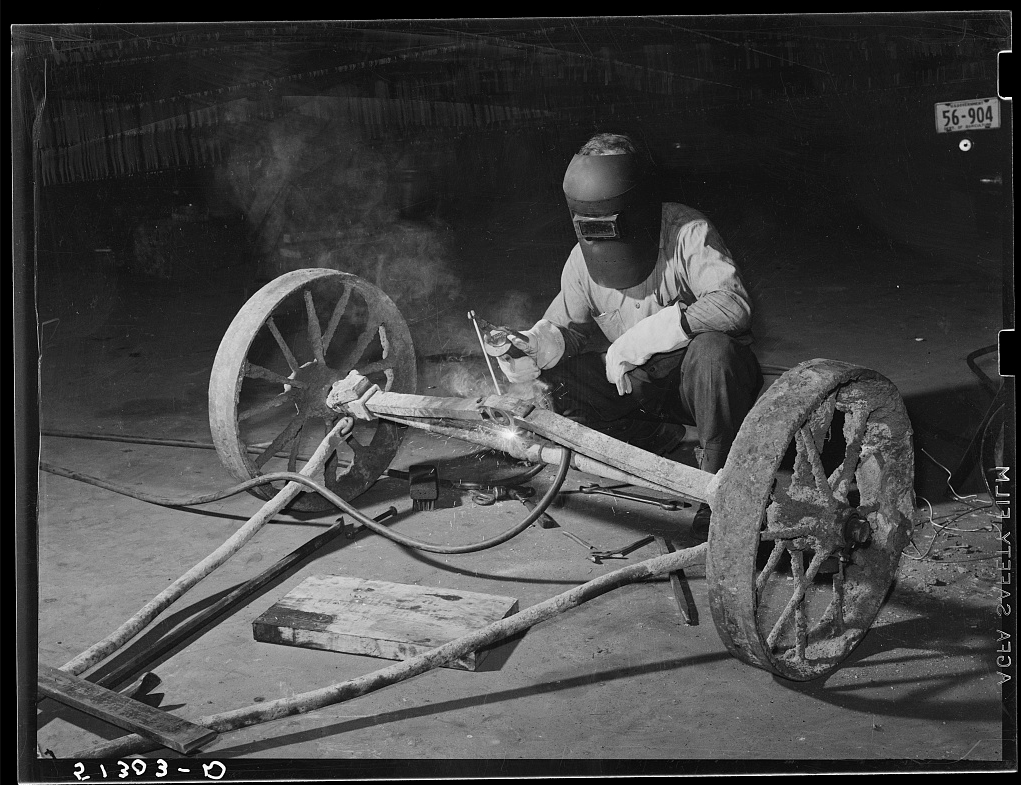
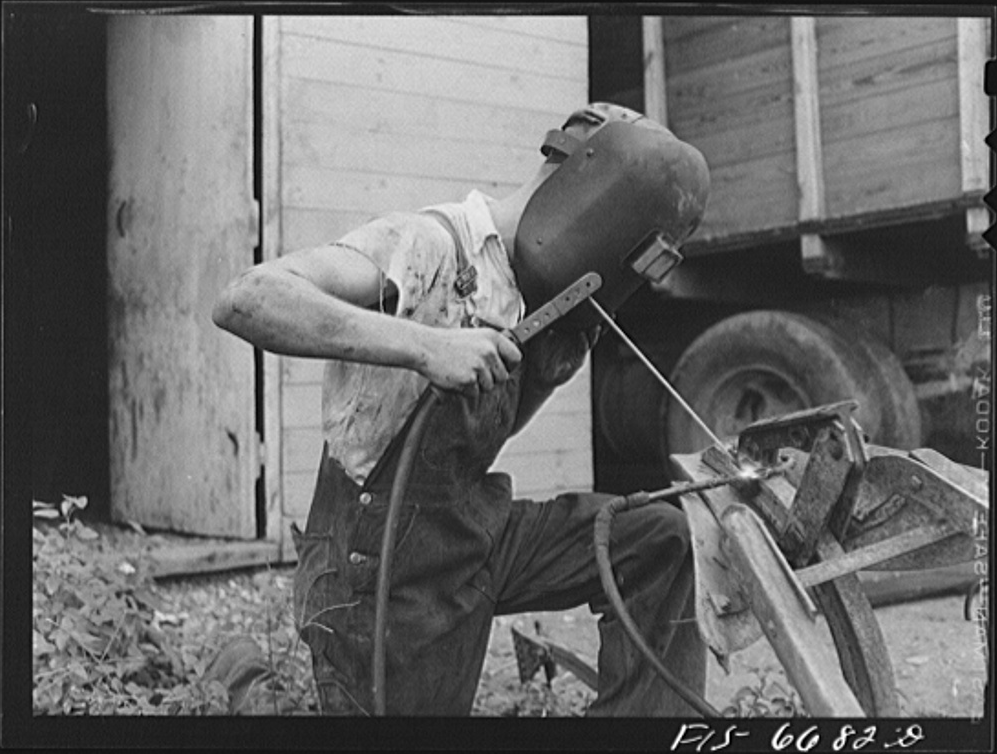
Welding as a process adopted by industry really took off during World War II. World War II was significant in U.S. history because it led to the large mobilization of a fighting force that was sent across the globe. This resulted in large numbers of fighting-age men being shipped overseas and working-age women being recruited to industrial work to help with the war effort. The contributions of women like those shown in Figure 20.4 are part of our proud history and contributions to America.
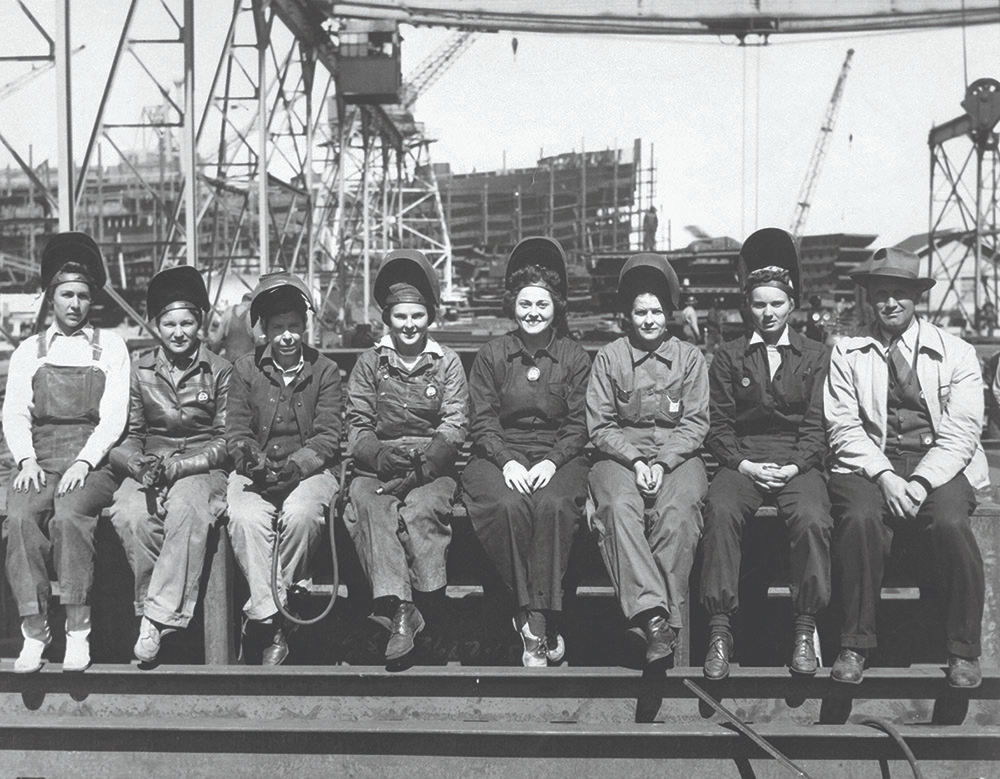
Today, welding of ferrous metals continues to be a process that is found in large institutions such as industry, government, and academia, but also for the everyday hobbyist wanting to weld in their shop to make small repairs.
Development of Welding Ferrous Metals
Welding ferrous metal requires a ferrous base metal (meaning the metal is mostly iron), a controllable heat source capable of melting the base material and, if used, the filler metal, and the application of the heat source to the base material in a manner that produces a weld that meets mechanical and quality requirements.
As mentioned above, oxy-acetylene welding was one of the first welding processes used in modern history to join metals. Figure 20.5 shows a welder working on the base material, with the oxy-acetylene torch in the welder’s right hand and the filler metal in their left hand.
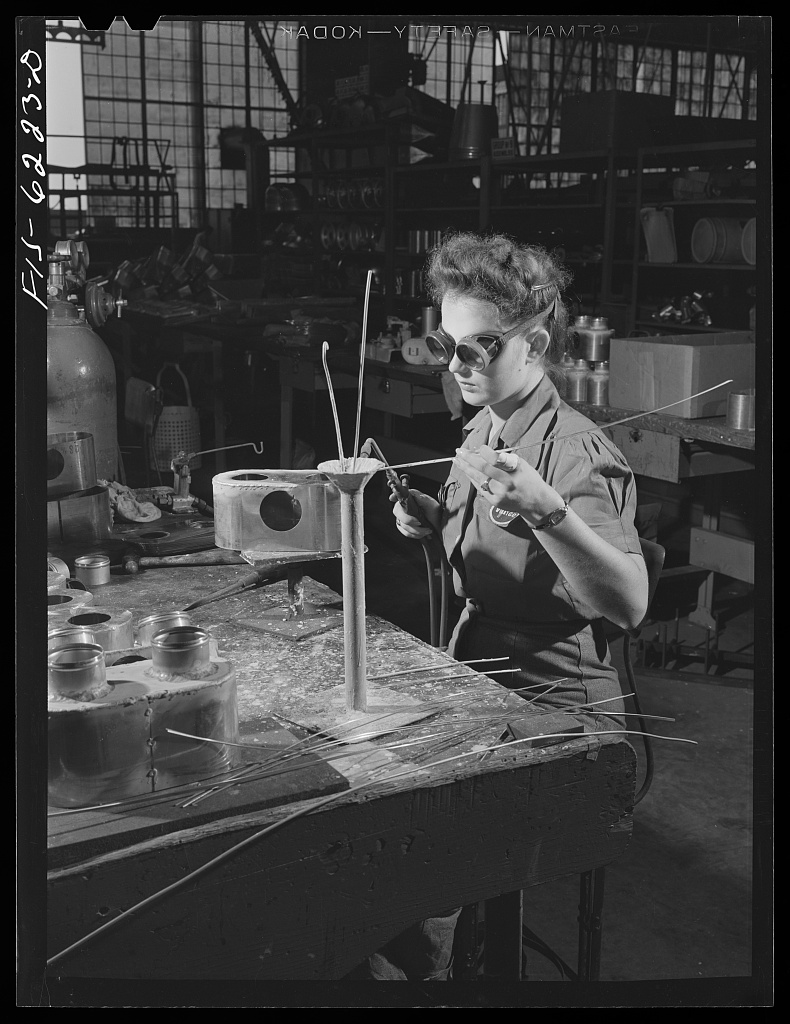
Oxy-fuel welding can be a dirty process that produces a lot of soot. If your school has an oxy-acetylene welding station, you may have noticed that a black coating of soot exists on the surfaces of the station . Excessive carbon can be created depending on the type of flame that is used. Options include carburizing, neutral, and oxidizing flames—with carburizing flames producing the most carbon of the three.
Electric arc welding is a much more convenient and controllable welding process. Great advances have been made in welding power supplies and filler materials to improve the quality and durability of weldments. Welding power supplies are complex, just like other consumer electronics that we use today (such as cell phones). With processes such as gas metal arc welding (GMAW), flux-cored arc welding (FCAW), and gas tungsten arc welding (GTAW), these power supplies are used to produce higher quality welds by making corrections to the arc and heat input due to the inconsistencies of having a person welding versus a robot. Highly trained welders are fairly steady in maintaining an arc length; however, even the best welder may deviate slightly closer or further away from the weld pool unintentionally. (Chapter 5 discusses power supplies in more detail.)
SMAW was the welding process that was adopted broadly by industry due to its versatility and relatively inexpensive equipment. A motor generator or building wall receptacle that can supply enough power for a welding machine, welding leads, electrodes, and base material are all that is required. The first electrodes were bare wire electrodes. Some theories state that the original experimenters using wire electrodes discovered that rusty electrodes welded better (Miller Electric Manufacturing Co., 2025). This led to the use of flux coatings on a solid metal wire that we are all familiar with today.
As time progressed, the flux coatings for SMAW electrodes got more complex with the addition of elements that remove unwanted impurities that have negative impacts on the weld. Aluminum is one such element that is used as a deoxidizer because aluminum readily bonds with oxygen. These unwanted elements then float to the top of the weld pool and form the coating we, as welders, know as slag.
Basics of Welding Ferrous Metals
Welding metallurgy is the study of welding metals based upon the chemical and mechanical properties of the weldment once all welding processes pre-weld, during the weld, and post-weld have been completed.
The most important thing a welder can do when performing code welds is to follow the Welding Procedure Specification (WPS) word for word. A certified welder’s value comes not only in their demonstrated skill to perform a weld to specifications, but also the assurance that the welds they produce are of the expected quality and material properties. By following the WPS, you are producing a weld that has been tested and approved for the in-service application as intended. If you do not follow the welding procedure, your value as a certified welder ceases to exist and may lead to loss of certification and possibly disciplinary action by the organization you received your certification from, such as the AWS.
The reason the WPS is so important to follow is because the materials, temperatures, processes, allowed cleaning methods, and procedure for placing weld beads specified within it were all determined through experience followed by destructive testing to produce a weld with the required material properties (such as strength) to successfully operate in in-service conditions. When a weld or other fabrication fails on a bridge, building, ship, or other structure where public safety is threatened, there is an investigation by government authorities and other organizations such as insurance companies. The records for that fabrication are reviewed and its authors interviewed, if needed, the fabricators and engineers are interviewed, and destructive testing is carried out to determine the cause of failure. As a welder, you are a professional in a rewarding career; don’t jeopardize losing your ability to continue in your career by not welding to the specifications you are provided. (See Chapter 18 for more information on WPSs.)
Welding ferrous materials (whether to a code or not) requires welders to use their experience and good welding practices along with professional judgment. Weld joints, base material, welding process, and filler metals, if used, all come together as inputs that determine which guidance is used for welding.
Uses of Ferrous Metals in Industry Today
Ferrous metals are the most widely used in the world today because of their material properties of both strength and durability, as well as their weldability (the ease with which a material can be welded) and relatively low material cost. Most welding schools start students out welding ASTM A36 mild steel because it is used throughout industry for structural applications, it is relatively inexpensive , and most importantly because it is easily weldable. Starting a student out on a material that first requires mastery of welding would only lead to frustration.
Ferrous metals are used in structural applications, as mentioned above, but more specifically they are used in the steel that comprises buildings, bridges, ships, pipelines, and other containers. In applications where ferrous metals would corrode, they are sometimes clad with stainless steel or other corrosion-resistant material In this way the steel provides most of the strength of the fabrication and the thinner clad material (what comes in contact with the corrosive substance, such as in a tank)provides the corrosion resistance required, but at a reduced cost.
Attributions
- Figure 20.1: Gas welding a joint in a line of spiral pipe at the TVA’s new Douglas Dam on the French Broad River, Tenn. This dam will be 161 feet high and 1,682 feet long, with a 31,600-acre reservoir area extending 43 miles upstream. With a useful storage capacity of approximately 1,330,000 acre-feet, this reservoir will make possible the addition of nearly 100,000 kw. of continuous power to the TVA system in dry years and almost 170,000 kw. in the average year by Alfred T. Palmer, Library of Congress, Prints & Photographs Division, Farm Security Administration/Office of War Information Color Photographs in the Public Domain; The contents of the Library of Congress Farm Security Administration/Office of War Information Color Photographs are in the public domain and are free to use and reuse.
- Figure 20.2: Welding axle. FSA (Farm Security Administration) warehouse depot. Atlanta, Georgia by Marion Post Wolcott, 1910-1990, Library of Congress, Prints & Photographs Division, Farm Security Administration/Office of War Information Black-and-White Negatives. in the Public Domain; The contents of the Library of Congress Farm Security Administration/Office of War Information Black-and-White Negatives are in the public domain and are free to use and reuse.
- Figure 20.3: Dunklin County, Missouri. Farm boy using welding equipment on a farm that receives U.S. Rural Electrification Administration (REA) power by Arthur Rothstein, 1915-1985, Library of Congress, Prints & Photographs Division, Farm Security Administration/Office of War Information Black-and-White Negatives. in the Public Domain; The contents of the Library of Congress Farm Security Administration/Office of War Information Black-and-White Negatives are in the public domain and are free to use and reuse.
- Figure 20.4: Line up of some of women welders including the women’s welding champion of Ingalls [Shipbuilding Corp., Pascagoula, MS] by Department of Labor, Women’s Bureau in the Public Domain; United States government work
- Figure 20.5: Nashville, Tennessee. Welding parts for fuel pumps. Vultee Aircraft Corporation plant by Jack Delano, 1914-1997, photographer; Library of Congress, Prints & Photographs Division, Farm Security Administration/Office of War Information Black-and-White Negatives. in the Public Domain; United States government work. The contents of the Library of Congress Farm Security Administration/Office of War Information Black-and-White Negatives are in the public domain and are free to use and reuse.
A process where the base material does not melt but the filler metal does melt. Soldering is similar to brazing but is performed at a lower temperature than brazing.
A process where the base material does not melt but the filler metal does melt. Brazing is similar to soldering but is performed at a higher temperature than soldering.
Refers to the gasses of oxygen and acetylene that are used for welding.
A metal where iron is the main base consituent.
Welding metallurgy is the study of welding metals based upon the chemical and mechanical properties of the weldment once all welding processes pre-weld, during the weld, and post weld have been completed.
The operating environment a weldment will experience such as temperatures and pressures.
Stainless steel is a group of steel alloys that contain levels of chrome and other corrosion resisting alloying elements that give the materials properties that it "stains' less than ordinary steel. See the chemical compositions of stainless steel grades for quantities of alloying elements.