20.3 Welding Stainless Steel
David Colameco, M.Ed.
Basics of Welding Stainless Steel
Stainless steels are used in corrosive environments where steel would rust and eventually fail. Similarly to carbon steel, stainless steels come in shapes that you are familiar with such as plates, pipes and tubes, angle iron, C-channels, etc. The cost of stainless steel fabrication, in terms of base materials and labor, limits its use.
Stainless steel, as its name suggests, stains less than steel—but that does not mean it won’t ever stain or rust. As a welder you can definitely destroy the corrosion resistant properties of stainless steel if you are not actively following the WPS and its temperature ranges, techniques, and other essential variables that have been used on a successful weld for the joint you are welding.
Stainless steel contains iron along with the alloying elements of chromium, nickel, molybdenum, and other alloying elements depending upon the alloy’s chemical composition. Each of these alloying elements improves the mechanical properties of the steel but also adds a cost to the stainless steel’s price. For example, stainless steel used in kitchen utensils would be a different alloy than that used for a more corrosion-resistant surgical tool. Likewise, the stainless steel in a vehicle’s muffler will be a different grade of stainless steel than what is used in the food and beverage industry.
The addition of these alloying elements changes the properties of the metal, including its thermal conductivity: Stainless steel has lower thermal conductivity than carbon steel. This means that the heat you put into the metal when welding stainless steel does not “flow” through the metal as fast as it does with carbon steel. This leads to distortion and potentially higher temperatures in the HAZ. Distortion in metal can occur when a weldment expands at different rates at different locations. Table 20.7 has thermal expansion coefficients for some stainless steel and other alloys for comparison.
Alloy | Coefficient of Expansion (32–212 °F) 10-6 in/in/F |
---|---|
Type 302 stainless steel, Annealed and Cold Rolled | 8.0 |
Type 304L stainless steel, Annealed | 8.0 |
Type 321 stainless steel, annealed and cold rolled | 8.3 |
Type 410 stainless steel, annealed and heat treated | 5.1 |
AM-350, solution treated and hardened | 6.8 |
AISI 4340 steel, annealed | 6.3 |
AISI 1020 Steel, annealed | 6.5 |
Nickel | 7.2 |
Aluminum | 13.1 |
Note. From Welding of Precipitation-Hardening Stainless Steels, Table XXXI (Vagi, J. J., Evans, R. M., & Martin, D. C., 1968).
Note that the 300 alloys of stainless steel have higher values for thermal expansion. This means that the stainless steel metal is going to expand more than the alloys and metals with lower values.
Metallurgically, sensitization is a problem that you will encounter if you are not careful when welding stainless steels. These precipitates, which are chromium carbide, move to the grain boundaries and reduce the chrome content that enable corrosion to occur. Figure 20.20 shows grains that started at 18% chromium content with less than 12% at their boundaries.
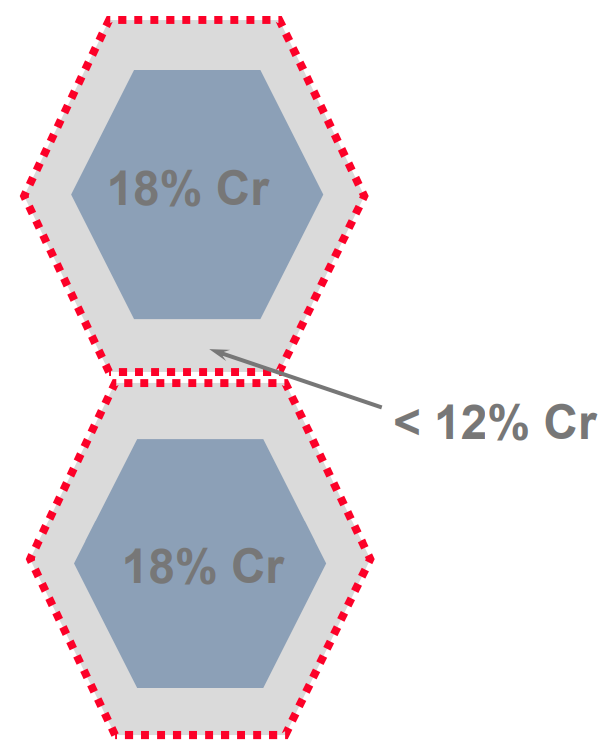
With the chromium content in the grain being reduced near the grain boundaries, the stainless steel is free to corrode. Figure 20.21 shows an illustration of the corrosion that occurs on both sides of the weld in the HAZ due to sensitization. These are sometimes referred to as wagon tracks.
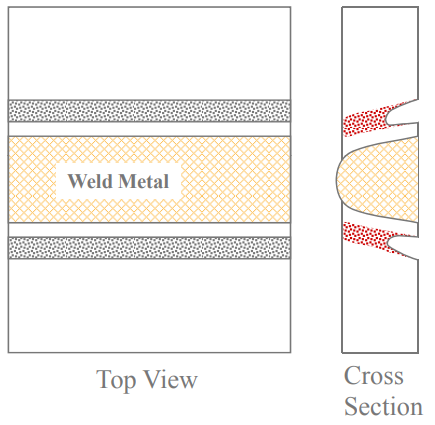
As a welder, you do not want to find out months after working on a project that your welding led to rework from ruined stainless steel. To avoid sensitization, don’t allow your weldment to stay within the temperature range of 800–1,600 degrees Fahrenheit for longer than necessary because carbon will bond with the chromium to form chromium carbide precipitates. Further, following the interpass temperature, welding technique, and other variables on a WPS will help prevent sensitization.
Uses of Stainless Steels in Industry Today
Stainless steels are used throughout our daily lives on handrails; elevators; commercial kitchens on their countertops, bowls and containers; and in food and beverage processing facilities for their tanks and piping. This is referred to as sanitary welding. Stainless steels are used structurally in corrosive environments.
Figure 20.22 and Figure 20.23 show tanks made with stainless steel for storing hydrogen and hydrazine rocket fuel respectively. Both of these substances are used as fuel and are highly combustible, therefore the safe storage of the contents in a container that is free of leaks is very important for the safety of workers and the public. You can see in Figure 20.23 a worker is wearing a protective suit as a safety precaution in the event of a leak.
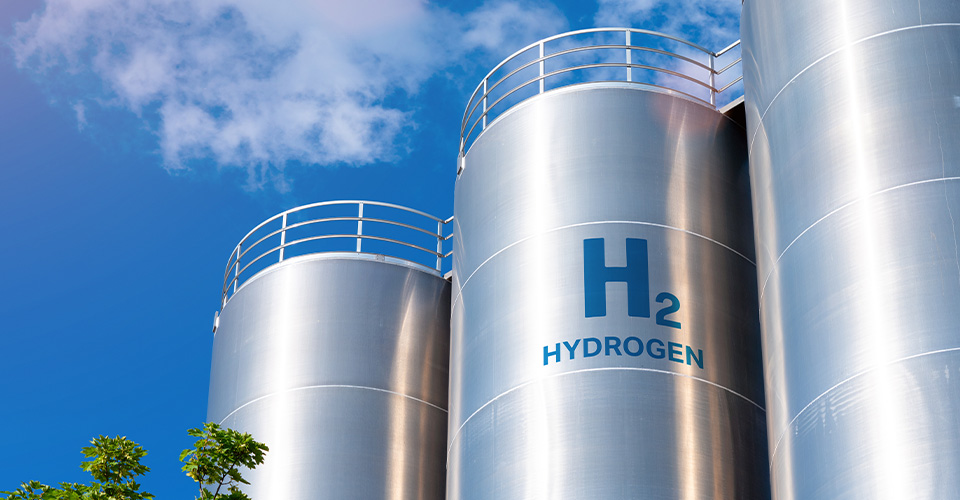
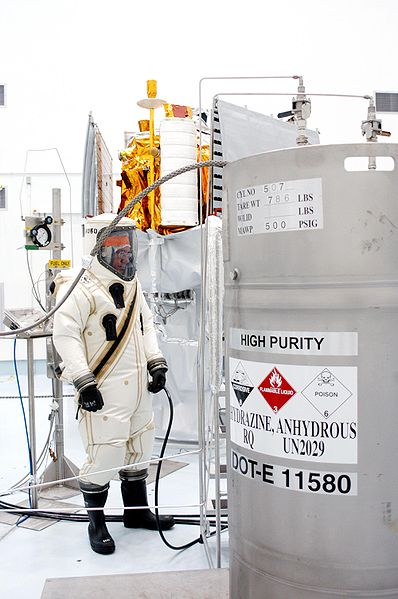
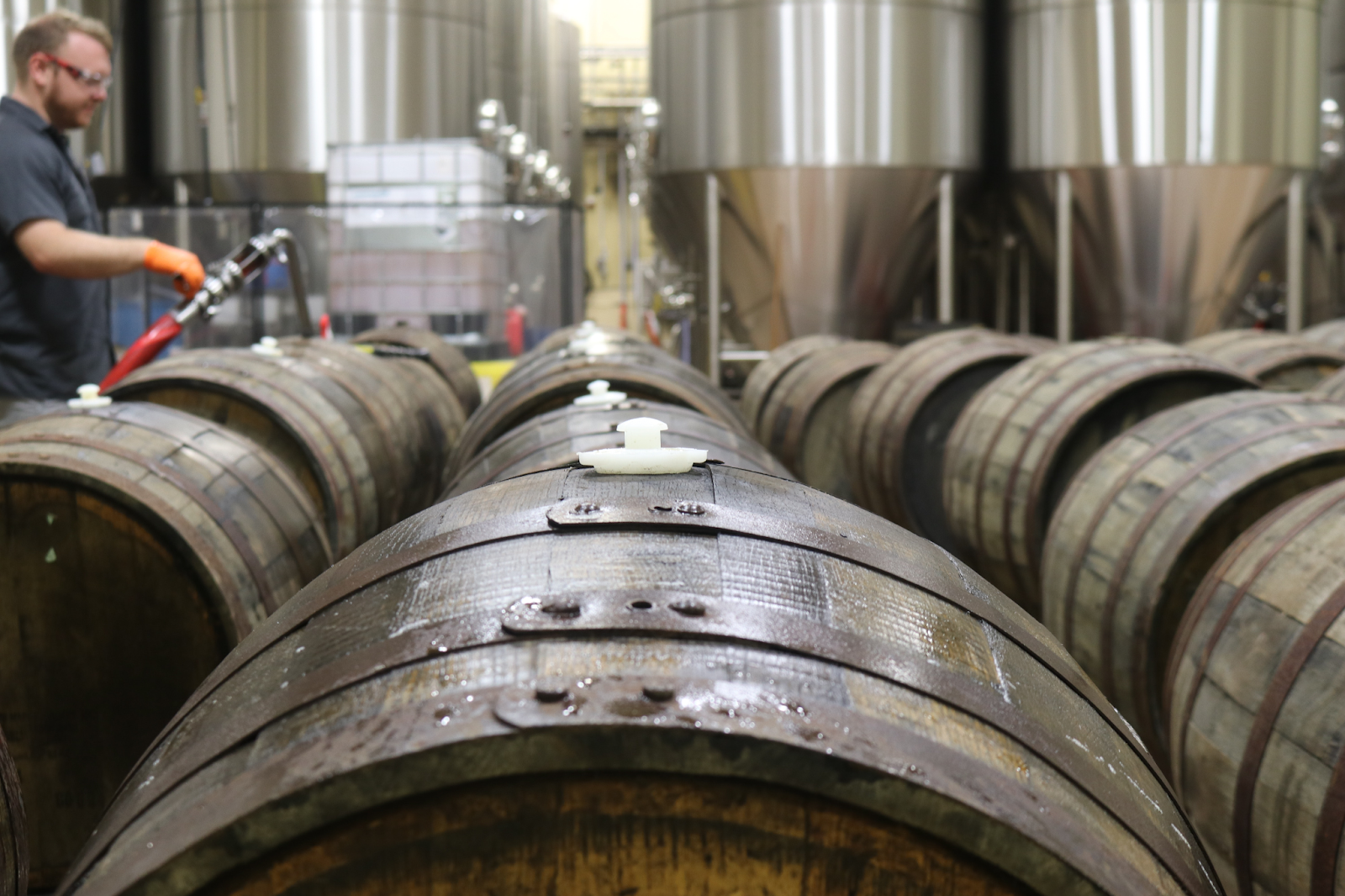
Stainless steel is also used in breweries because the taste of the product is very important. Welds that do not have the appropriate profile on the inside of the tanks and pipes may have pockets or crevices where bacteria can collect and then change the taste of the product.
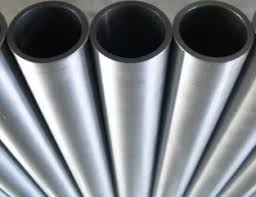
Other stainless steel shapes that can be used are pipes, as seen in Figure 20.25, and even artwork. Iconic stainless steel structures in America include the 630-foot-tall Gateway Arch in St. Louis, MO (Figure 20.26) and the 110-ton Cloud Gate sculpture in Chicago, IL (Figure 20.27). They are tourist destinations and part of the local culture. Are you interested in welding fabrications like these?

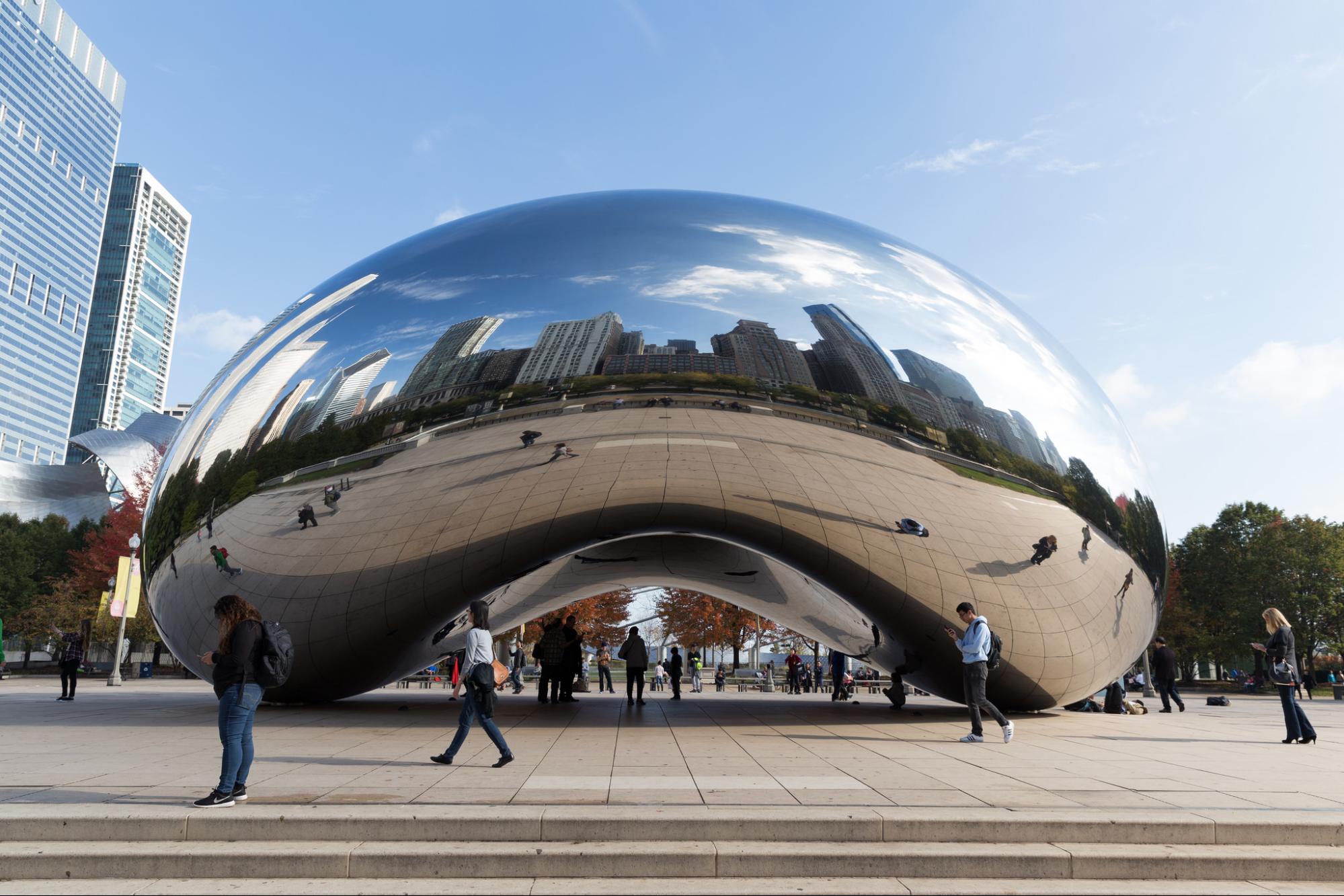
Stainless steel can be found in pop culture, too. For instance, a stainless steel car called the DeLorean (Figure 20.28), with its gull-wing-style doors, was an icon in the Back to the Future movies of the 1980s and 1990s. These cars are now rare and a collector’s item.
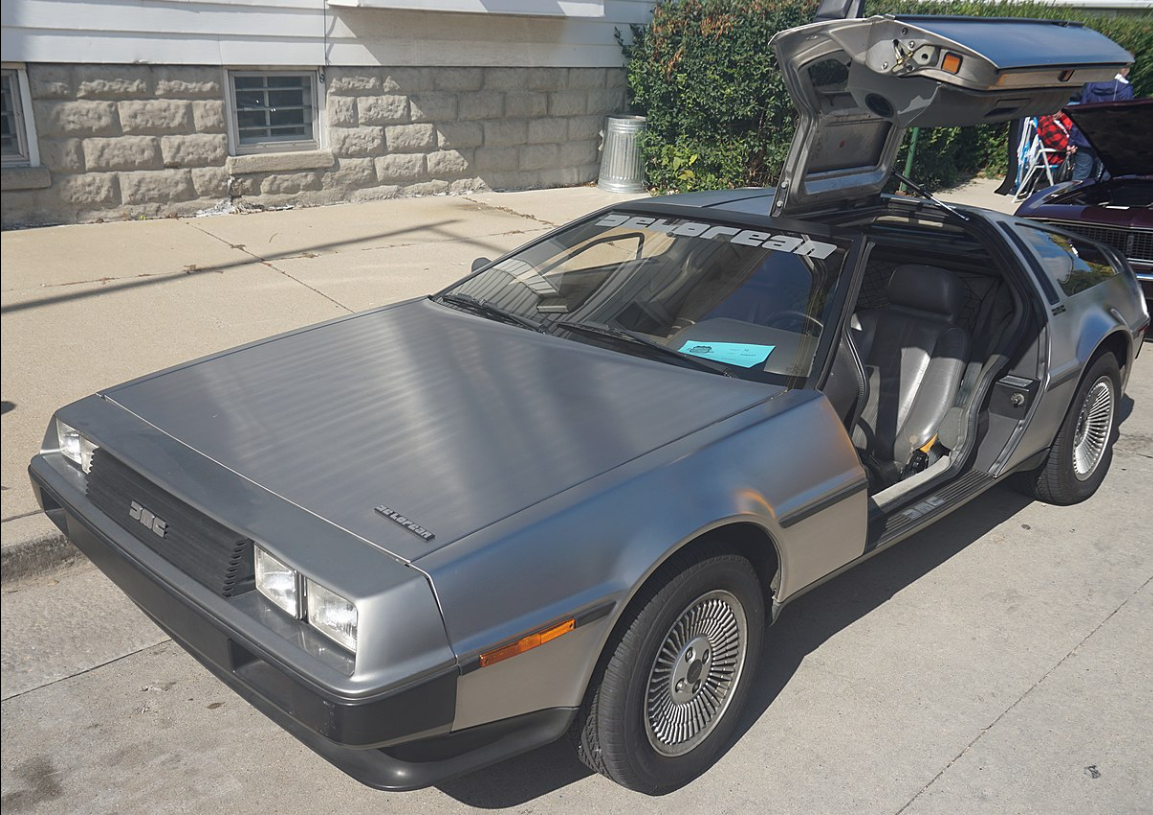
If your welding program offers stainless steel welding, ask your instructor about local welding career opportunities with stainless steel.
Welding Processes Used With Stainless Steels in Industry Today
Stainless steel is commonly welded in industry using SMAW, GMAW, FCAW, and GTAW. You will read more about these processes in this section. Before that, however, it is important to know the safety concerns of welding stainless steel.
Many of the alloying elements that give these metals their amazing properties are harmful to your health. When stainless steel is welded, chromium will form hexavalent chromium. OSHA provides the following precautions for working with hexavalent chromium:
- “Eyes: Direct eye contact with chromic acid or chromic dusts can cause permanent eye damage. Avoid eye contact with dusts, fumes, smoke, liquids, mists, and aerosols containing hexavalent chromium.
- Respiratory tract: Hexavalent chromium can irritate the nose, throat, and lungs. Repeated or prolonged exposure can damage mucous membranes of the nasal passages and result in ulcers. In severe cases, exposure causes perforation of the septum (the wall separating the nasal passages). Some employees become allergic to hexavalent chromium so that inhaling chromate compounds can cause asthma symptoms such as wheezing and shortness of breath..
- Skin: Prolonged skin contact can result in dermatitis and skin ulcers. Some workers develop an allergic sensitization to chromium. In sensitized workers, contact with even small amounts can cause a serious skin rash” (Occupational Safety and Health Administration, n.d.-a).
Welding stainless steel is a very rewarding career direction when it is done safely with proper precautions such as the use of personal protective equipment and ventilation. It is important for you to be aware of some of the dangers associated with welding stainless steel so you can follow the appropriate safety precautions.
Cleanliness is very important when preparing your stainless steel base material. Only use brushes and other abrasive materials that are meant for stainless steel. Stainless steel brushes, wire wheels, and other consumables are also used when cleaning and preparing other metals such as aluminum, titanium, and zirconium. It is important to label these items with notices that read “Stainless Steel Only” or something similar so they are not used for different metals, which would then cause contamination of your base material.
The next few sections provide a high-level overview of the welding processes that can be used to weld stainless steels. Please see the dedicated chapters on these respective welding processes for more information.
Shielded Metal Arc Welding
SMAW is used for welding stainless steel for code welds. You will notice right away two big differences between the E309 welding electrodes used to weld stainless steel as compared to the E6010 electrodes you may have used for mild steel. The first is how, due to the lower thermal conductivity of stainless steel, the electrode will heat up a lot more and will glow cherry red when you burn it down to the remaining few inches. In addition, the electrode will be used up more quickly, making your starts and stops an essential part of your welding.
Gas Metal Arc Welding
When welding low-carbon steel, many shielding gasses are a mixture of inert and non-inert (reactive) gasses. Inert gasses do not react with other materials; for instance, helium stays as helium during and after the welding is completed. Carbon dioxide (CO2), on the other hand, is not an inert gas and it will dissociate, meaning that the molecule will break apart, and some oxygen will react with the hot weld metal, HAZ, and hot base material to form oxides. In the end, this negatively affects the weld through undesired mechanical properties, porosity, and discoloration.
If you use GMAW, you should always check to make sure the shielding gas is the proper mixture for your application, but this is especially important when welding stainless steel to ensure that the welds are properly protected. In addition, the shielding gas will also affect the transfer mode of GMAW, the depth of penetration into the base material, and the heat and shape characteristics of the arc. The proper shielding gas will be listed on the WPS. If you are welding as a home hobbyist, then information on shielding gasses can be found from the manufacturer of the welding machine you are using. Likewise, the machine settings to use can be found in the welding electrode manufacturer’s documentation.
Flux-Cored Arc Welding
FCAW can also be used on stainless steel. As with GMAW, the choice of shielding gas is very important because inert gasses must be used to prevent reactions of the shielding gas with the weld and heated metal. Cleanliness of everything, from the base material to the wire electrode and the purity of the shielding gas is important. Similar to the discussion for welding stainless steel with GMAW, the machine settings and other parameters can be found on the WPS or, if welding at home or without a WPS, from the manufacturer.
Gas Tungsten Arc Welding
GTAW is a very precise and clean process due to the control a welder has over the welding variables such as current, travel speed, and deposition rates. This added control makes GTAW an excellent welding process for specialty metals such as stainless steel. As discussed with the other processes, cleanliness of the filler rods is very important. It is common for welders to wipe down their welding rods with acetone to remove any dust or dirt prior to welding just as they would do to clean the surfaces of their base material.
One common message taught throughout welding metallurgy classes is the control of hydrogen due to its harmful effects of hydrogen-induced cracking (HIC). HIC is still being studied and many models have been proposed over the decades, but an explanation without going into the weeds is this: HIC is caused by hydrogen interactions in the metal, which cause cracks to elongate into weldment failures. So you might be surprised to hear that a specialty gas mixture of 98% argon and 2% hydrogen was specifically produced for welding austenitic stainless steel, which is a subset of stainless steel alloys. When burned in the welding arc, the hydrogen in the shielding gas produces more heat and provides for greater penetration.
Hydrogen is a very reactive gas, but its chemical attraction for oxygen is much stronger than iron’s attraction. When pure hydrogen comes in contact with iron oxide it rips the oxygen from the iron to convert the iron oxide into pure iron, and the hydrogen combines with the oxygen to form water. In this case the reaction of hydrogen with the base material is a helpful process because it removes iron oxide and improves the penetration of the weld.
The use of a reactive gas, such as hydrogen, in a shielding gas mixture for one process but never for others is another example of how there can be exceptions to rules. Generalizations are important because they simplify our welding work, but we must always keep an open mind to possible exceptions to these rules.
Other Processes
Other welding processes, such as SAW, electron beam welding, and laser welding, can be used to weld stainless steel. Because these processes are not likely to be found in a community college or technical school’s welding fabrication instruction, they are beyond the scope of this book. Students who are interested in learning more about these processes for stainless steel are encouraged to investigate further.
Attributions
- Figure 20.20: “Sensitization” of Austenitic Stainless Steels by U.S. Nuclear Regulatory Commission in the Public Domain; United States government work
- Figure 20.21: Example of Intergranular Attack by U.S. Nuclear Regulatory Commission in the Public Domain; United States government work
- Figure 20.22: Example of Intergranular Attack © Los Alamos National Laboratory As stated on the LANL Web Policy: Terms of Use and Privacy webpage: “The public may copy and use this information without charge, provided that this Notice and any statement of authorship are reproduced on all copies.”
- Figure 20.23: Hypergolic Fuel for MESSENGER by NASA in the Public Domain; United States government work
- Figure 20.24: ENERGY STAR Focus on Energy Efficiency in Distilled Spirits Production by U.S. Department of Energy and U.S. Environmental Protection Agency in the Public Domain; United States government work
- Figure 20.25: image by U.S. Department of Energy, National Nuclear Security Administration, Office of Nonproliferation and Arms Control in the Public Domain; United States government work
- Figure 20.26: St. Louis Arch by United States Geological Survey, Office of Youth and Education in Science in the Public Domain; United States government work
- Figure 20.27: The Bean – Cloud Gate and reflection, Chicago, Illinois by GPA Photo Archive, U.S. Department of State is released under CC BY-SA 2.0
- Figure 20.28: 1983 DMC DeLorean by Michael Berera is released under CC BY-SA 4.0
An alloying element that is added to steel to provide corrosion resistance.
The temperature of the base material about an inch or two away from the weld pool.