21.4 Welding Reactive Metals
David Colameco, M.Ed.
Development of Welding Reactive Metals
Reactive metals are ones that, when heated to elevated temperatures, react with the oxygen and nitrogen. The heat of welding raises the temperature of the weld and adjacent base material above the reaction temperature. Reactive metals are zirconium, titanium, and beryllium.
As a welder starting to learn the trade you will not be welding on these metals; however, it is important to know that they exist because reactive metals are used and welded on in Washington state. Due to the increased cost of the base materials and their use in critical applications, most welding of reactive metals is performed through automated processes with robotics in many industries. If you are interested in robotics, look into your school’s course offerings to see if an introductory class to robotics in a mechatronics program is offered.
Reactive metals are just that: metals that react during welding. They react with the gasses in the atmosphere at elevated temperatures in a negative way, leading to contamination of your weld and/or heavy oxidation of the nearby base materials. To avoid this contamination, special care is needed in applying protective shielding gasses.
If welding reactive metals requires more preparation and more care when welding, you may wonder why we weld them at all. The material properties of reactive metals are needed for applications used in aerospace, nuclear, and other demanding in-service environments where the extra cost of fabrication is required.
Basics of Welding Reactive Metals
Due to the reactive nature of zirconium, titanium, and beryllium, cleanliness and the application of inert shielding gasses is essential and even more important than for stainless steel welding. If you have welded on low-carbon steel and then switched to stainless steel, then you know the importance of cleanliness and shielding gas when welding.
GTAW is used to weld zirconium and titanium. GMAW can be used to weld titanium. Laser beam welding can also be used. When GTAW and GMAW are used to weld titanium, argon is normally used as the shielding gas. Helium alone and mixtures of argon and helium can be used as well, but the price of helium has increased significantly in the 2020s, resulting in its decreased use. As with all welding and especially so with these more expensive metals, welders are encouraged to test their machine settings on a scrap piece of material prior to production welding. This is especially important with reactive metals to help ensure quality welds.
Due to the low thermal conductivity of titanium, you will notice that the weld pool is larger than that of metals that more easily move heat into the base material. Large gas nozzles with high flow rates are used to compensate for these larger weld pools. Chill bars may also be used to help with heat dissipation.
For GTAW of titanium it is important for the welder to keep the filler metal covered in shielding gas while it is hot; otherwise, the filler metal will become contaminated by the atmosphere. For production welding out of position or of more complex shaped fabrications, it is important to protect the weld pool from air drafts with additional pieces of material to block air flow, such as with the use of baffles.
In some cases a welding chamber or glove box may be used when welding reactive metals, which essentially submerges the weldment in shielding gas. This is less common for titanium welding, but it may become necessary for complex shapes that would make it difficult to ensure proper shielding gas coverage. Common welding defects for titanium include porosity and cracks, which can be attributed to bad shielding gas coverage (though that is just one of the many possible causes).
Uses of Reactive Metals in Industry Today
Titanium is used in the aerospace industry for its strength-to -eight ratio and corrosion resistance. The X-3 Stiletto aircraft, built in 1953, was the first aircraft with major titanium airframe components. The plane was intended for Mach 2 speeds but had underpowered engines that limited it to Mach 1 speeds.
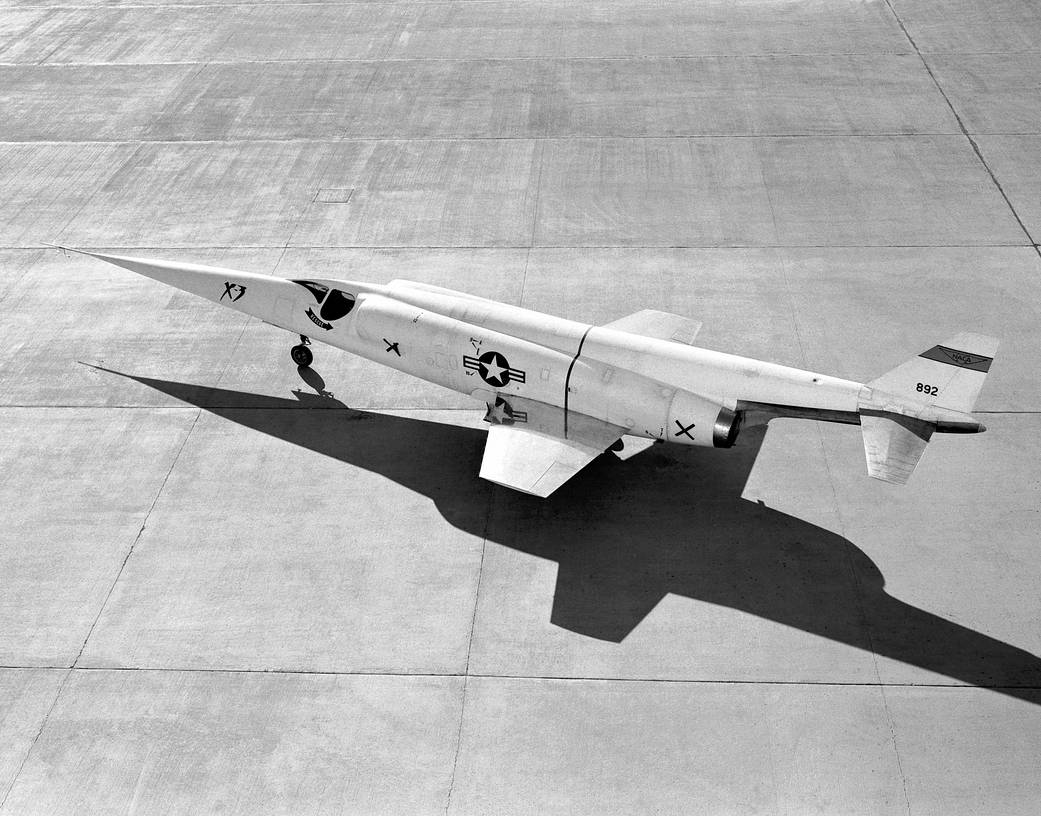
The X-3 represents the first major use of titanium for airplanes, but it was not the last. The SR-71 Blackbird “airframes were built almost entirely of titanium and other exotic alloys to withstand the heat generated by sustained high-speed flight” (National Aeronautics and Space Administration, 2017). The plane was capable of maintaining Mach 3 speeds for an hour. Many planes since then have been built with titanium components due to their desirable mechanical properties. For instance, Boeing’s 787 Dreamliner uses titanium since its lighter weight helps improve fuel efficiency.
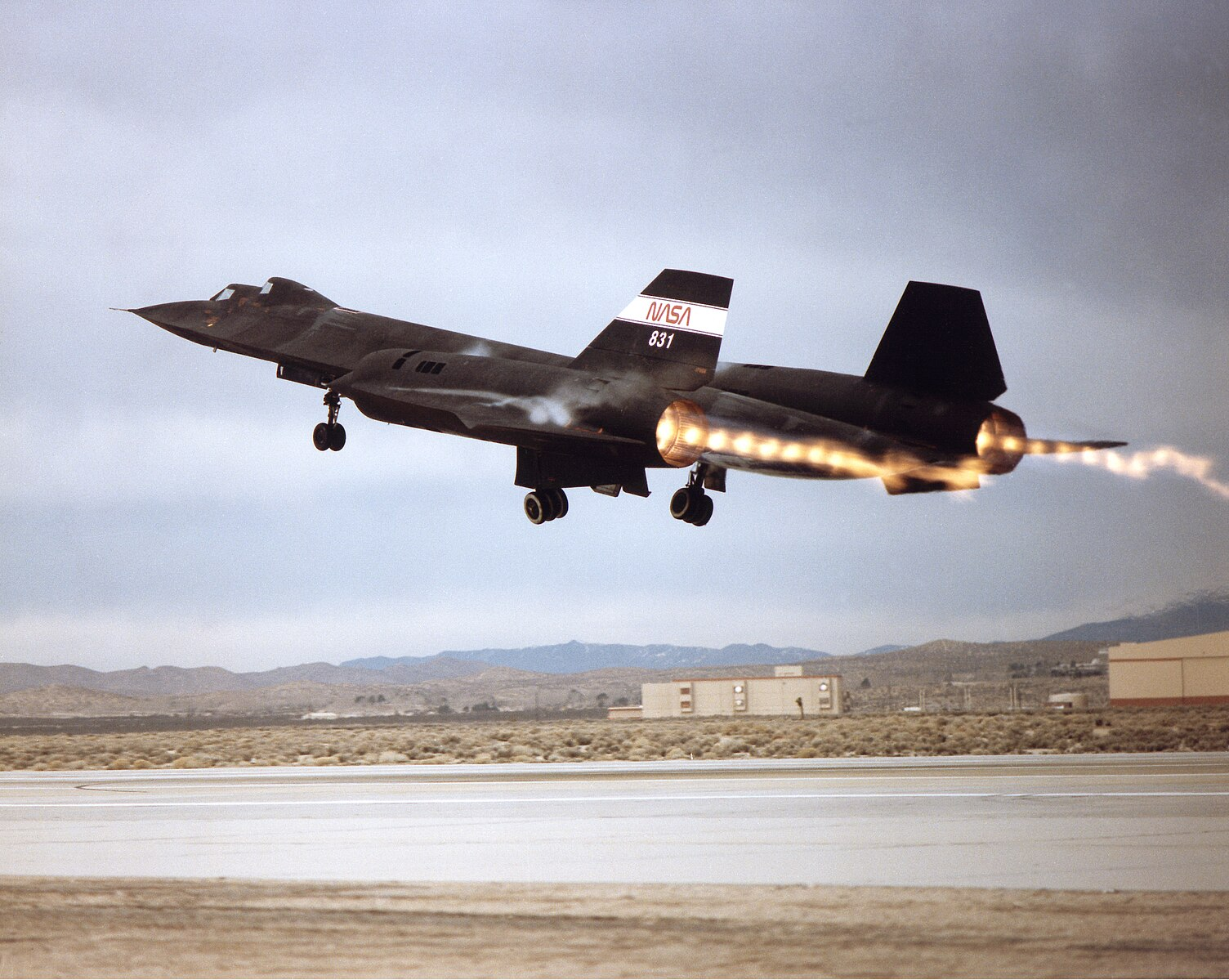
Titanium also has desirable antiballistic properties. Due to the limited availability of certain grades of titanium, these specialty alloys are mostly used for high-performance aircraft. However, it is also used for ballistic armor plating. The two ballistic test plates in Figure 21.12 show the test results and holes from an effort to develop titanium armor plating for ground vehicles.
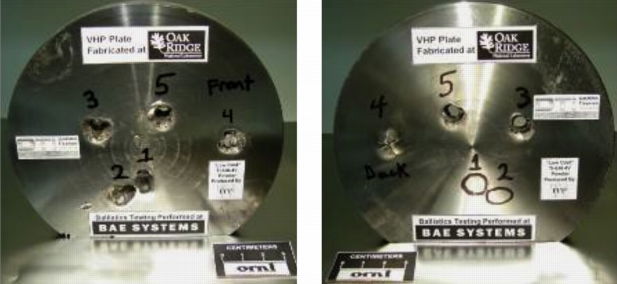
Titanium is used in high-end bicycle frames, as well. Figure 21.13 shows a cracked bicycle frame on a model bicycle that was recalled for safety reasons. Cracks on any weldment that is subjected to cyclical motion, such as vibration from riding on worn road surfaces, can speed up crack propagation. The failure in the titanium bicycle frame in Figure 21.13 goes through the weld and its heat-affected zone (HAZ). It is highly likely that the crack started in the HAZ and spread from there. Welds on bicycle frames are typically performed using GTAW.
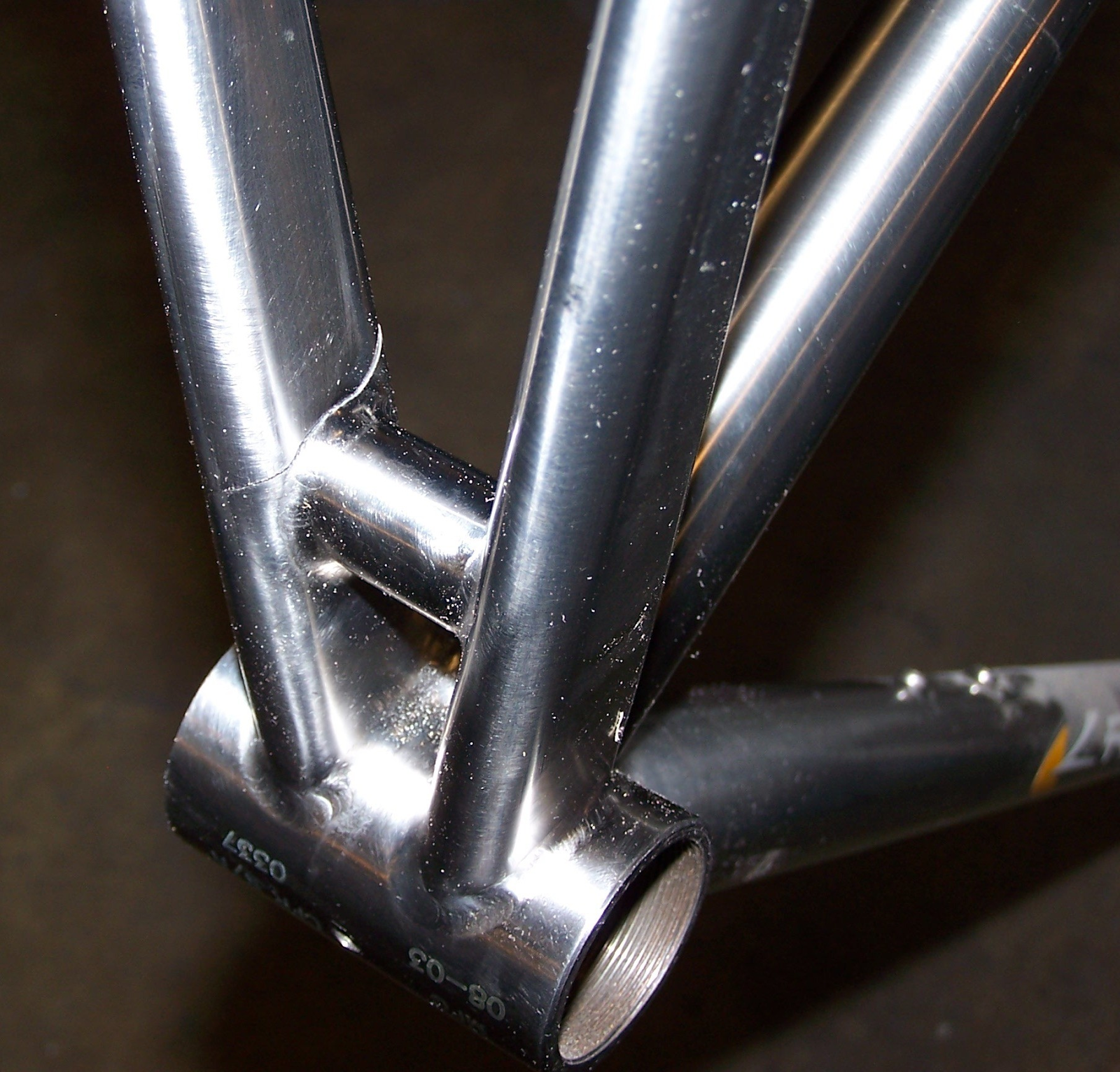
Zirconium is used for nuclear fuel cladding. Cladding is the metal tubing that contains ceramic uranium fuel pellets. They are about 12 feet long and are arranged into fuel bundles such as the one shown in Figure 21.14. These fuel rods are built by sliding the ceramic pellets into the zirconium rods and then performing circumferential welds on the end caps. GTAW is used for this, but in an automated process due to the large number of high-quality welds required. Each commercial nuclear reactor core in the U.S. contains approximately 52,000 of these fuel rods and about one-third of them are replaced every 18 to 24 months in what is called a fuel outage. This means each refueling campaign consists of about 35,000 circumferential welds on the fuel rods alone.
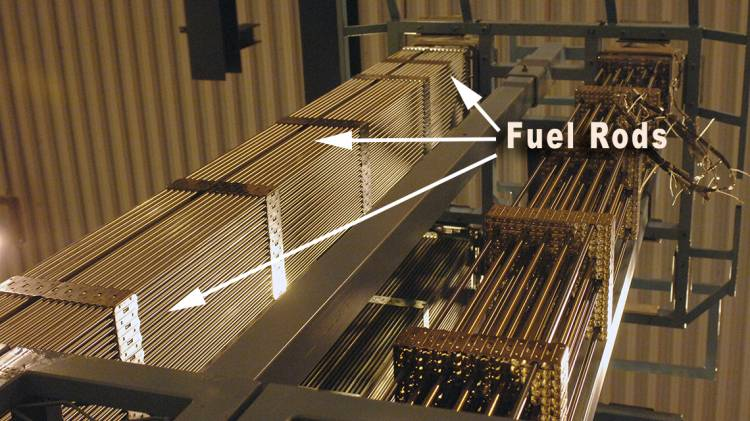
The final reactive metal we’ll cover, beryllium, has superior mechanical properties that make it useful for special applications. The James Webb Space Telescope, which has been returning amazing pictures of deep space that had not seen before, was fabricated with beryllium due to the material’s stiffness at low temperatures. When operating in space, the telescope experiences temperatures of about -415 degrees Fahrenheit.
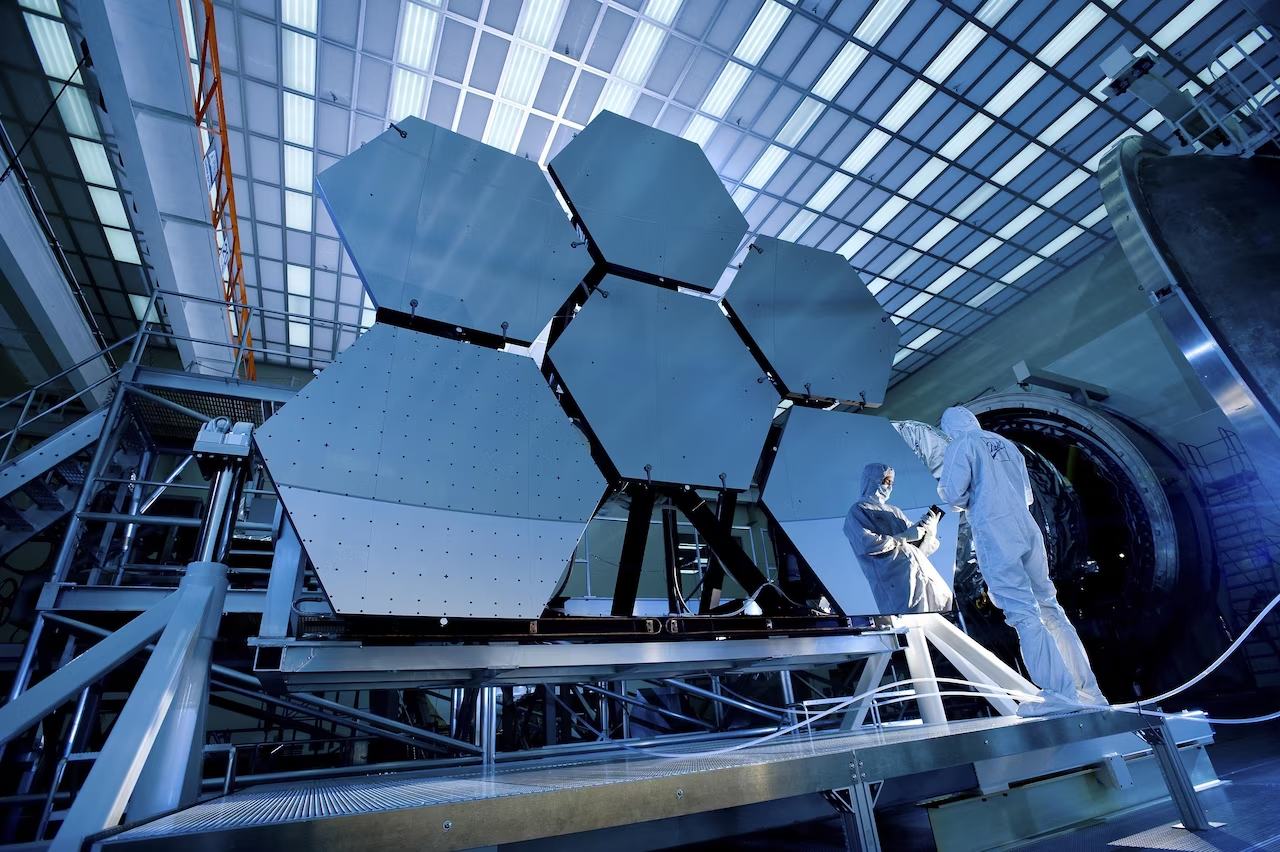
Beryllium is also used in many common applications due to it being “stronger than steel and lighter than aluminum” (Occupational Safety and Health Administration, n.d.). It also has a high melting point and excellent thermal conductivity and thermal stability. Table 21.4 lists some common uses for beryllium.
Industry | Industry Uses |
---|---|
Aerospace | Aircraft braking systems, engines, satellites, space telescopes |
Automotive | Antilock brake systems, ignition |
Ceramic Manufacturing | Rocket covers, semiconductor chips |
Defense | Components for nuclear weapons, missile parts, guidance systems, optical systems |
Dental Labs | Alloys in crowns, bridges, and dental plates |
Electronics | X-rays, computer parts, telecommunication parts, automotive parts |
Medicine | Laser devices, electro-medical devices, X-ray windows |
Nuclear Energy | Heat shields, reactors |
Sporting Goods | Golf clubs, bicycles |
Telecommunications | Optical systems, wireless base stations |
Note. From Beryllium: Overview (Occupational Safety and Health Administration, n.d.).
Beryllium is a dangerous metal if inhaled. Any fabrication activities need to follow all applicable safety precautions to help prevent severe damage to welders’ health.
Attributions
- Figure 21.10: X-3: First Use of Titanium in Major Airframe Components by National Aeronautics and Space Administration in the Public Domain; United States government work
- Figure 21.11: SR-71 Takeoff with Afterburner Showing Shock Diamonds in Exhaust by National Aeronautics and Space Administration in the Public Domain; United States government work
- Figure 21.12: Ballistic Tests of P/M Ti © Oak Ridge National Laboratory, U.S. Dept. of Energy Used with permission. Courtesy of Oak Ridge National Laboratory, U.S. Dept. of Energy. ORNL Security & Privacy Notice
- Figure 21.13: CPSC, CF Roark Welding & Engineering Announce Recall of Bicycle Frames by U.S. Consumer Product Safety Commision in the Public Domain; United States government work
- Figure 21.14: Fuel rods in a nuclear reactor are mainly made of zirconium alloys. These long metal tubes contain pellets of fissionable material, typically uranium oxide pellets. © International Atomic Energy Agency Used with permission. Courtesy of the International Atomic Energy Agency. IAEA Terms of Use
- Figure 21.15: Into the Looking Glass For Webb Telescope Tests by The National Aeronautics and Space Administration in the Public Domain; United States government work
These metals react with the gasses in the atmosphere at elevated temperatures in a negative way leading to contamination of your weld and/or heavy oxidation of the nearby base materials.