8.1 History of SMAW
David Ridge
Development of SMAW
The first arc welding process was developed in the early 1880s by Auguste de Meritens (Lincoln, 1933, p. 1.1-2). It used carbon electrodes. The circuit was connected in direct current electrode negative (DCEN) configuration and the electrode holder was fixed in position and moved on a pivot to lower the electrode. This process was later refined toward the end of the 1880s by Nikolas de Benardos and Stanislav Olszewski (Lincoln, 1933, p. 1.1-2). These two scientists used a bank of storage batteries charged by a steam engine as a power source. They also decided to connect the circuit to run on direct current electrode positive (DCEP), and developed a handheld electrode holder to allow manual manipulation of the carbon electrode. This carbon-arc welding process proved to be very limited in what could be welded with it, primarily because the disintegrating carbon rod contaminated the base material with excess carbon deposits.
In 1888, a Russian inventor named Nikolay Slavyanov improved the carbon-arc welding process by replacing the carbon electrode with a metal one (“Shielded Metal Arc Welding,” 2023). In 1889, the American Charles Coffin made roughly the same development to the process independently of Slavyanov (Lincoln, 1933, p. 1.1-3). Using metal electrodes worked markedly better than the carbon electrodes because they eliminated the carbon contamination problem and introduced additional filler metal into the weld as the electrode melted. However, they still were only marginally useful for welding metals. The main problems were the low quality of the metal used for the electrodes and the lack of any way to shield the molten weld metal from elements in the air. This led to weak, brittle welds that could not be relied on for strength in high-stress applications.
In the early 1900s, Oscar Kjellberg of Sweden and Arthur Percy Strohmenger, an American, developed the first covered metal electrodes (“Shielded Metal Arc Welding,” 2023). The first iterations were not much better than the bare metals ones. However, in 1912 Strohmenger produced a heavily coated metal electrode that could produce clean welds with good mechanical properties (“Shielded Metal Arc Welding,” 2023). Although it wasn’t named as such at the time, this was the first real version of shielded metal arc welding.
Because of the high cost of producing the covered electrodes, unfortunately this form of arc welding did not become widely used until World War I, when the need for faster production and repair of ships and other war-related vehicles became necessary. It wasn’t until after the war, in 1927—when a method of quickly and cheaply applying the coating to the electrodes by extrusion was developed—that the arc welding process really began to spread quickly as a means of production (“Shielded Metal Arc Welding,” 2023).
By the start of World War II, arc welding with covered metal electrodes was the most widely used method of welding for industries such as shipbuilding, vehicle manufacture, oil refineries, railroads, and pipelines (Lincoln, 1933, p. 1.1-6). As the process has progressed over the past century, the main advancements have been related to the metal alloys used for the electrodes, the composition of elements in the coating material, and the types of power sources available (Lincoln, 1933, p. 1.1-6). Aside from these things, SMAW’s basic principles and concepts haven’t changed in over 100 years.
Today SMAW has been largely replaced by the faster, more efficient flux-cored arc welding process. However, it still holds a place in industry due to the relatively low cost and portability of its necessary equipment and SMAW’s ability to weld almost any metal used in manufacturing thanks to the wide variety of electrodes available. SMAW remains one of the most important welding processes for any welder to master and is usually one of the first processes students and new welders encounter.
Basics of the Process
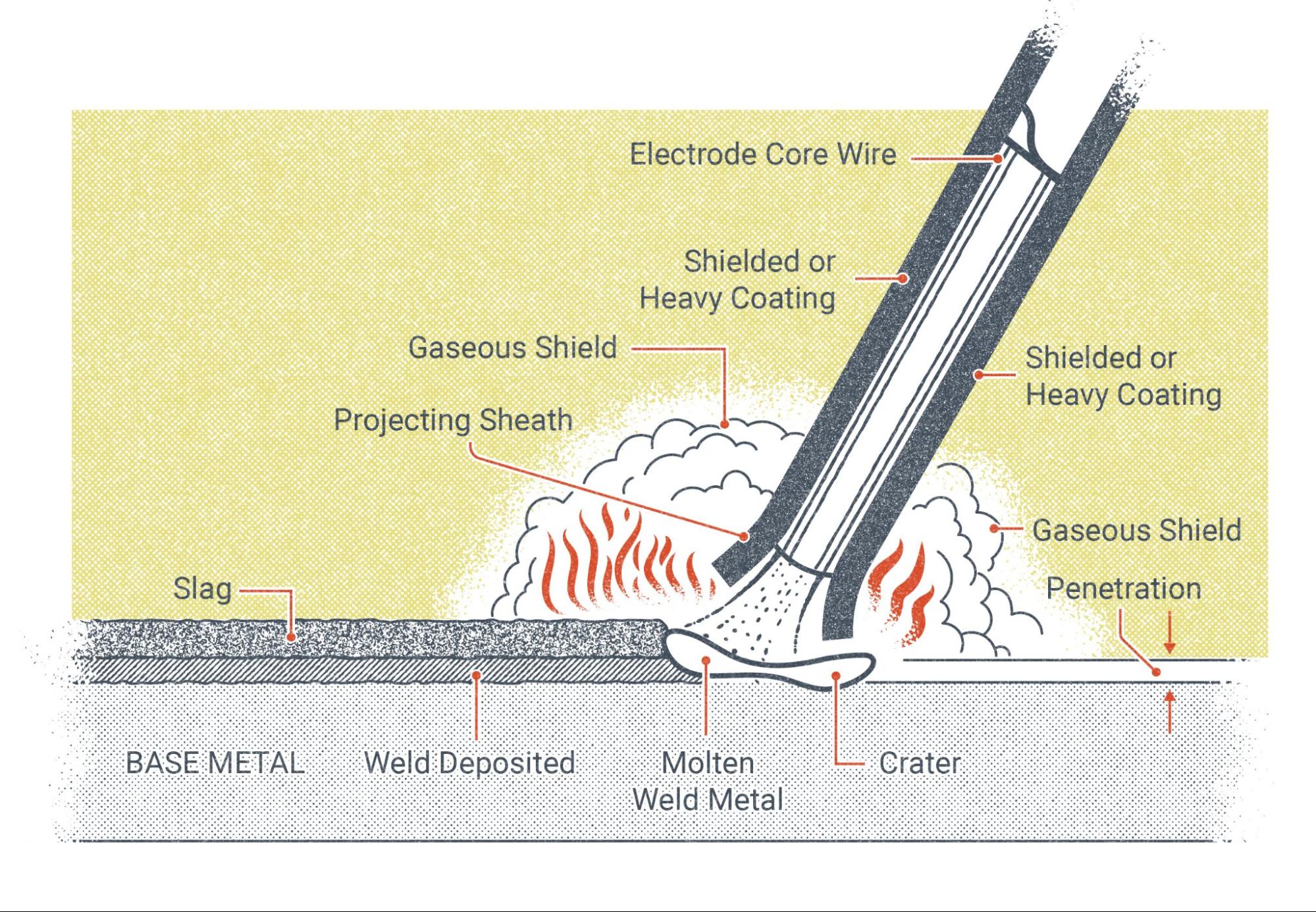
The SMAW process uses electricity to create an arc between a coated metal rod, called an electrode, and the metal to be welded, which is called the base metal. The electrode is coated in powdered material called flux, which is baked onto the rod. These coated electrodes are what led to the SMAW process being nicknamed stick welding.
The arc is somewhere between 6,000 and 11,000 degrees Fahrenheit (3,316–6,093 degrees Celsius). This is due to the resistance of the atmosphere to the flow of electricity (discussed in Chapter 5). The arc melts the base metal and the filler metal of the electrode together to form the weld. As the arc melts the electrode, some of the elements in the flux coating are burned to create CO2 gas, and others are melted to form a substance called slag. The gas cloud created by the flux protects the weld by pushing the air away from the weld area, which is necessary because molten metal reacts badly with elements in the normal atmosphere. The slag forms a covering over the molten weld metal as it solidifies, which further protects it from the atmosphere, helps it hold its shape, and helps the weld cool at the correct rate.
The size, shape, and direction of the weld are controlled manually by the operator. The welder is responsible for adjusting the welding machine’s electrical settings and manipulating the electrode completely by hand.
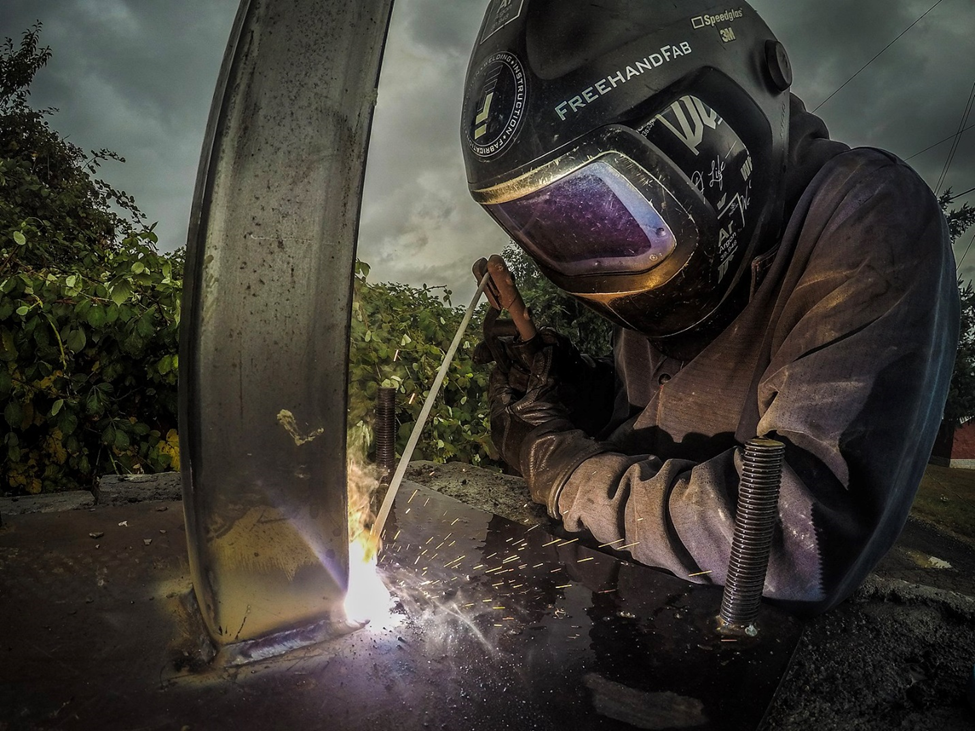
Uses of SMAW in Industry Today
One of SMAW’s greatest benefits is its ability to weld the most common types of metal, thanks to the wide variety of electrodes on the market. SMAW is capable of welding everything from thin sheet metal to material that is several inches (or several feet) thick, as well as a wide variety of metals and alloys. With the correct electrode, the proper settings, and a skilled operator, many things can be welded with SMAW.
The main drawbacks of the SMAW process are that it creates a significant amount of dirt and debris, is inefficient regarding material usage, requires a higher level of skill from the welder than some other processes, and is a relatively slow process. Because of the lack of speed and efficiency, SMAW has been replaced by the much faster wire-feed welding processes in most high-production environments, and the general filthiness created keeps it from being used in situations that require precision and cleanliness, such as aerospace welding.
Still, SMAW has many applications in the modern world. It has uses in the shipbuilding and construction industries. It is often seen in mobile welding businesses, machine repair, and agriculture. It is also used extensively in pipeline welding and exclusively in underwater welding. As far as anyone can predict, the process won’t die out anytime soon.
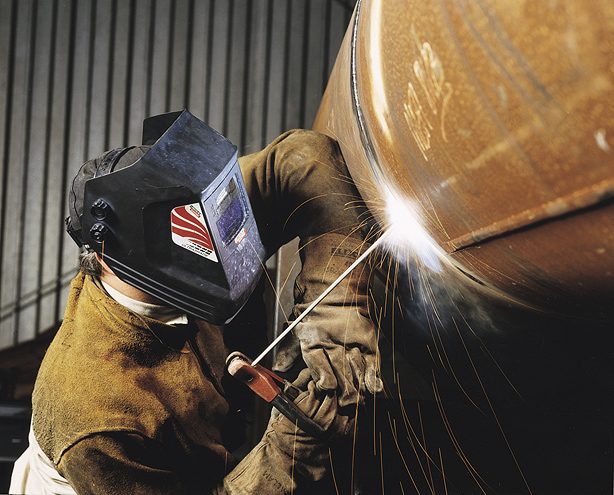
Jessica Y.’s Welding Story
I didn’t come into welding through your typical routes. I wasn’t raised by parents who had laborious jobs or worked out in the garage, and while the high school I attended did have a welding shop class, I dropped out of school long before I had the opportunity to take it. I fell in with the wrong crowd, doing drugs and committing crimes. I found myself sitting in prison by the age of 22. I knew it was time for me to grow up and make some serious changes. I was fortunate enough that the institution I was in had a very intensive in-patient treatment program. I was even able to enroll in college classes that were provided by the local community college that had a contract with the prison. This was all the catalyst of change. I worked hard on overcoming my addiction and behavior problems and was able to work on my education, learn how to be a decent student and pay my debt to society for the wrongs I had done. Three birds and one stone.
In the class, my instructor Ms. O was incredibly real and very honest that with multiple felonies, we would be more limited in employment opportunities and urged us to start thinking about a career field that would accept us felons. I knew I was comfortable in a shop environment, loved the thought of working with my hands, and wanted to build something I could be proud of. Ms. O passed out a career aptitude test where I was asked questions like, “Would you rather help a sick animal or build a fence?” I scored high in categories like construction worker, heavy equipment operator, and welder. I think it’s obvious which option I chose. Closer to my release date, Ms. O was able to put me in contact with the local community college in the area I was moving to. I applied for financial aid and enrolled in a two-year welding program the week that I got out. Once my mind was set on welding, I knew I had to follow through no matter how intimidated I might feel.
Not only was I in uncharted territory, but I had just spent time in prison and was still working to stay sober. I felt like I didn’t belong. I felt like I had a big scarlet letter “F” on me that everyone could see. But once I got my bearings, I found that school came easy to me and that my time locked up taught me discipline and good study habits. I also found that I wasn’t the only student that felt out of place, there were lots of students that were there battling their own adversities. I found comfort in knowing that we were all there working on the next step to building a better life than the ones we once lived. I was the only female student in my class, but as luck would have it, my welding instructor was a fellow woman. Ms. K was genuinely supportive of me and the work I had been doing to turn my life around. She would challenge me to dig deeper into things and assert myself more to projects in and out of my welding class. She would tell me to strive for progress; perfection would come later. But most importantly, she taught me to always build up the women around me as she was doing and how, because in this industry we are few and far between, we must support one another. I would have never thought this possible for someone like myself. Before deciding on a welding career, it was hard to imagine I would achieve something bigger than working fast food or bagging groceries. Fast forward two years, and I had graduated with high honors, completing an Associate’s degree.
Then, graduated and with a new sense of confidence, I had to get out there and find an employer that was willing to give me a chance (I still had all the felonies to explain). I told myself that if a potential employer had issues with my past, then it was a company I wouldn’t want to be a part of. Ms. K came through again and pointed me in the direction of a company that was hiring, and once again I lucked out. I met with Ms. S, the owner of a local weld shop. I was incredibly nervous for the interview but knew that I had worked my tail off to get to that point. While in the interview, I waited for the right opportunity to tell her about my past, knowing she would come to see it on the background check. I explained to her that while yes, I had seven felonies that were all drug-fueled, it was nothing in comparison to the work I had done to change my life. I explained the various twelve-step programs I was in while incarcerated as well as the work I continued to do since being released. I made sure to include all my certificates of achievements in my resume. I wanted her to know I was serious about working and ready to prove myself. A few days later, I got the call; Ms. S told me she valued my honesty and would like to give me a shot to come work for her. I have now been employed full-time with the same company for five years and look forward to many, many more.
Choosing a career in the welding industry has been life-altering for me. It has made me into a woman I and my family can be proud of. It has given me financial stability and instilled in me a good work ethic. I am now married and about to have a baby girl. My husband, who has also overcome similar adversities, is a heavy equipment operator, and together we look forward to teaching our daughter that it’s good to work with your hands and raising her to know that you don’t have to go to some big fancy college and that there are great jobs in the trades. What she does with that will be up to her.
I often hear my foreman say that the skill of welding is only 20% of the work. The rest is in your head. This couldn’t be more true. It’s all about gaining confidence in your abilities and not getting hung up on mistakes. Once you can achieve that, the rest will fall in place. No one ever becomes a journeyman welder overnight. It takes years of on-the-job training and thousands of hours of hood time. The key is to go into it with a good attitude, always be teachable, and remain humble; hard work pays off. And know that you belong there. I will forever be grateful for the strong women that helped build me up along the way and I am eager to pay it forward as new women come into the field.
Jessica Y.
Attributions
- Figure 8.1: How SMAW Works by Nicholas Malara, for WA Open ProfTech, © SBCTC, CC BY 4.0
- Figure 8.2: Shielded Metal Arc Welding by Prowelder87 is released under CC BY-SA 4.0
- Figure 8.3: SMAW by Mgschuler is released under CC BY 3.0
- Image of Jessica Y: © Jessica Y, used with permission.
- Image of Jessica Y welding: © Jessica Y, used with permission.
Direct current electrode negative is a type of direct current in which the welding electrode is set as the negative pole from which the electrons are emitted. Also called direct current straight polarity (DCSP).
Direct current electrode positive is a type of direct current in which the workpiece/base metal is set as the negative pole from which the electrons are emitted. Also called direct current reverse polarity (DCRP).
Filler metal is the external metal being added to the weld during welding.
An arc is the part of an electric current that passes through the air or other atmosphere between two conductors, and appears as a bright light.
An electrode is the part of a welding system that conducts electricity and produces the arc.
Base metal is the material being assembled to form the weldment, upon which the weld is made. An older term for base metal is parent metal.
Flux is a powdered mixture of chemicals designed to benefit the weld by forming shielding gas and slag to protect the weld, providing alloying elements to make the weld stronger, using deoxidizers to remove contaminants from the weld, and providing fluxing agents to help the weld wet into the base metal.
Slag is a byproduct of flux as it breaks down in the arc. Slag is used to cover the molten weld pool to protect it from the atmosphere, help it hold its shape, and slow the cooling process to prevent cracking.