9.1 History of FCAW
Cameron Kjeldgaard
Development of FCAW
To discuss the development of FCAW, it may be best to review some history of both the gas metal and shielded metal arc welding processes. The first use of a mechanically fed continuous wire electrode was in the 1920s, ushering in GMAW. This same time period saw the development of coated stick (SMAW) welding electrodes, too, and they were rapidly accepted across a wide range of industries due to their versatility, portability, and quality weld metal.
Initial efforts aimed to coat continuous electrodes, but by the late 1940s, GMAW was applied widely. There was a growing incentive to find a way to combine the benefits of both processes: GMAW with its continuous wire electrode and operator appeal and SMAW with the cleaning and metallurgical benefits of its flux coating.
At first, there were efforts to coat continuous electrodes, but any attempt to roll the coated wire electrode into a coil cracked and ruined the flux. Then, at an American Welding Society exposition in May of 1954, the FCAW process debuted to the public (Lincoln, 1994). A continuous wire electrode consisting of a tubular metal sheath filled with powdered flux had succeeded in marrying the productive benefits of GMAW with the metallurgical benefits of SMAW.
The earliest FCAW electrodes required a supplemental shielding gas in the form of carbon dioxide, which remains one of the most popular shielding gasses for the process to this day. Then in 1956, the Lincoln Electric company debuted its Innershield® process—the first FCAW electrodes to be completely self-shielded, with no external gasses required. This invention split FCAW into two sub-processes, each with its own special considerations: FCAW-G, or gas-shielded FCAW, and FCAW-S, or self-shielded FCAW. FCAW-G, often referred to by the Lincoln Electric trade name Dualshield®, is still frequently used in indoor shop welding environments. FCAW-S has gained widespread use in outdoor field-welding environments.
Basics of the Process
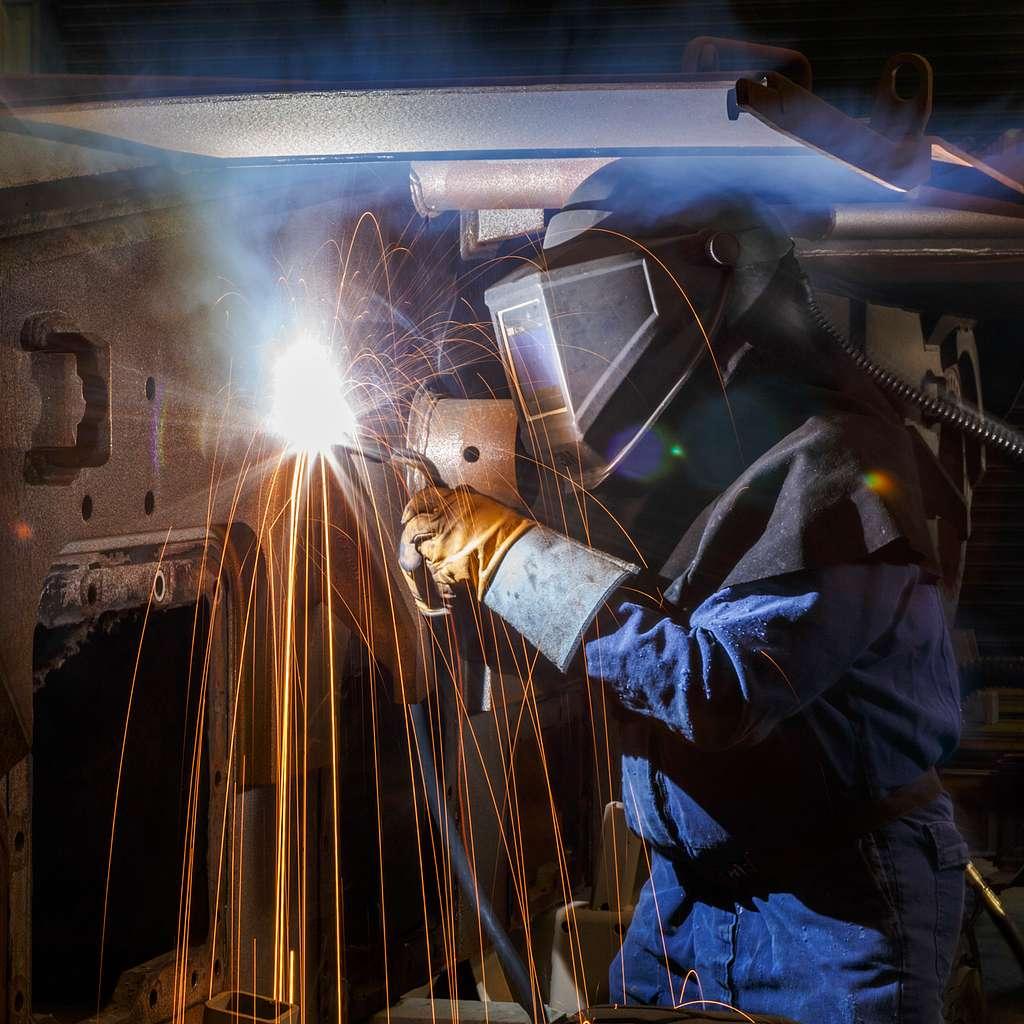
FCAW is a high-production process employed to weld a variety of ferrous materials, particularly in industries where the materials being joined are heavy-weight and thick. As with other arc welding processes, the heat of an electrical arc is used to melt and fuse two pieces of base metal with the addition of weld filler metal provided by a consumable welding electrode.
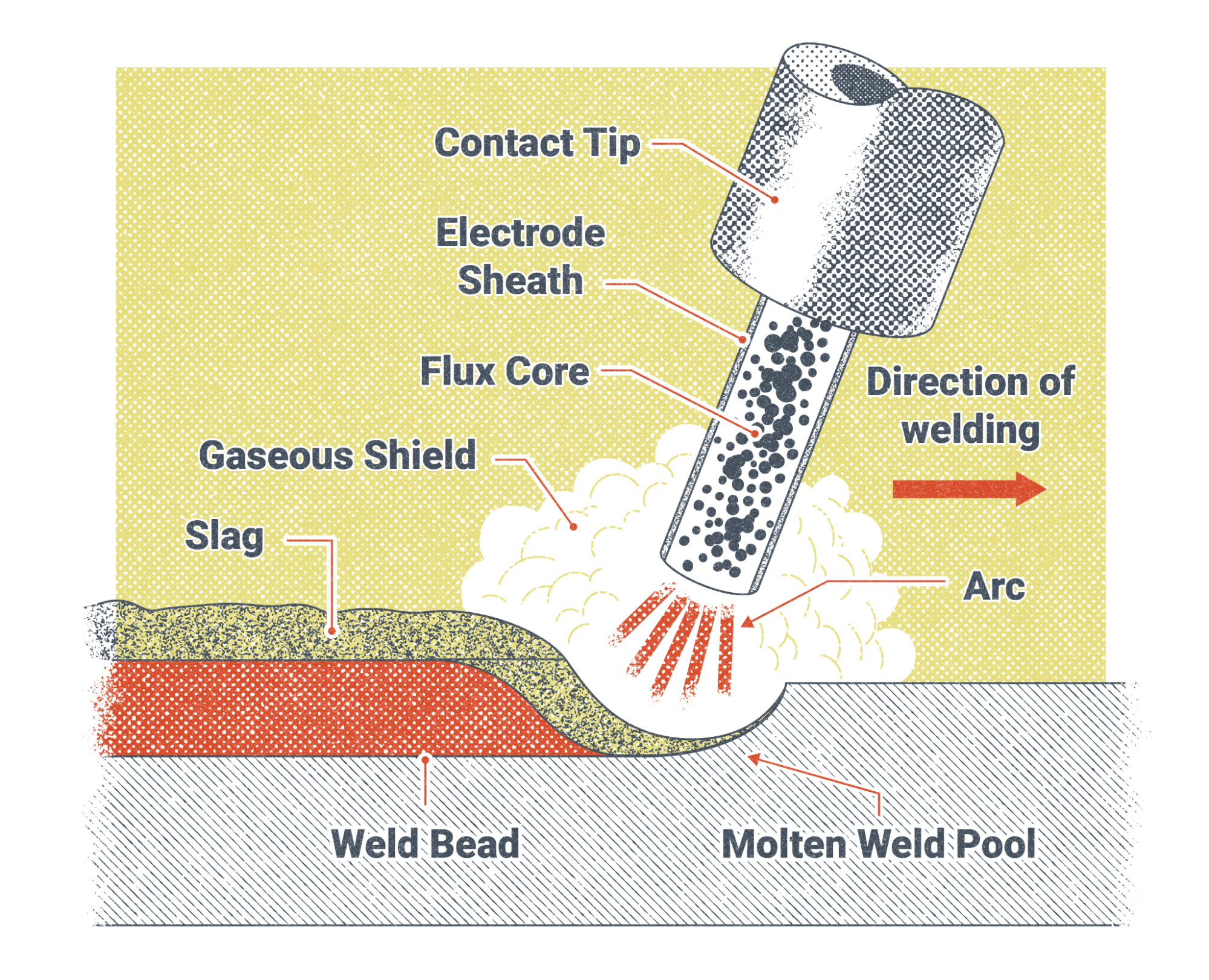
The most distinguishing characteristic of the FCAW process is the flux core electrode from which it gets its name. The electrode is hollow (referred to as a tubular electrode), with its exterior consisting of a metal sheath and its interior filled with powdered flux. The flux elements in FCAW are deoxidizing and denitrifying, shielding, and alloying, and they are also responsible for arc stabilization and slag formation. SMAW electrodes can do the same, but FCAW electrodes also come in the form of long continuous coils, ranging in size from just a few pounds to large 500 pound coils packaged in drums. They are available in a range of diameters from as small as 0.035 inch up to 0.125 inch. The larger diameter wires can deposit a large amount of weld metal in a short amount of time, while smaller diameter wires are more suitable for thinner materials and vertical or overhead welding.
The benefits of continuous wire electrodes, particularly in high-production environments, cannot be understated. The development of coated stick electrodes and SMAW greatly improved weld quality. However, the slow welding speed, downtime to change electrodes, and “stub loss” gave rise to a motivation to combine the advantages of SMAW with those of a continuous, mechanically fed electrode. FCAW is capable of producing welds with comparable or superior quality to those of the SMAW process but in much shorter times and with less welder training.
These advantages are further buttressed by the fact that FCAW is considered a semiautomatic process: since the electrode is fed into the weld pool mechanically by a wire feeding unit, less operator skill is required as compared to SMAW, for which the electrode is fed into the weld pool manually. The mechanization of feeding the electrode also results in much faster travel speeds along the joint and much higher weld metal deposition rates as compared to SMAW. All other aspects of welding—electrode angle, electrode manipulation, and travel speed—are still under the direct control of the welder. Additionally, in manual processes, like SMAW and GTAW, the welder is in direct control of the arc length, but in FCAW and GMAW, the arc length is largely determined by settings at the power source and wire feeder. However, the welder must still maintain a constant electrical stickout, which is the length of wire electrode extending out of the tip of the welding gun. The further the gun is held from the work during welding, the longer the stickout. Electrical stickout greatly impacts shielding, welding current, and arc stability. Though FCAW is most commonly employed in this semiautomatic fashion, the process also lends itself well to mechanization or full automation.
That the FCAW electrode is continuous and mechanically fed is not the only characteristic that gives it advantages over other processes. For instance, GMAW also employs a continuous, mechanically fed wire electrode, but unlike FCAW, the electrode is solid, uncoated, and totally reliant on a shielding gas to protect the weld puddle from the atmosphere. This reliance on shielding gas makes GMAW unsuitable for outdoor use. In contrast, the shielding provided by the flux in FCAW electrodes has seen the process, particularly FCAW-S, gain wide outdoor use across a number of industries. Beyond providing shielding, the flux also contains deoxidizers and denitrifiers, which serve to soak up contaminants that would otherwise lead to weld defects. This reduces the amount of cleaning required on the base metal prior to welding. Alloying elements are also present in the flux, improving weld quality and allowing the electrode to be tailored to weld a variety of materials. The flux also produces a slag coating, which solidifies atop the weld metal; this layer of slag slows the cooling rate of the solidifying weld metal and protects it from atmospheric contamination as it cools. Other elements in the flux aid in arc starting and serve to stabilize the welding arc, improving weld quality and increasing operator appeal.
Though FCAW boasts many great advantages, the process is not without limitations. It is a dirty process, producing large amounts of welding fumes, especially with use of self-shielded electrodes. Not only can these fumes cause visibility issues, obscuring the welder’s view of the puddle, but they can become a health concern if welders don’t take care to properly ventilate the welding environment.
The layer of slag produced by the process also introduces a few special considerations. Firstly, the slag must be cleaned between each successive pass of a multi-pass weld, and even single-pass welds must have their slag removed to permit a visual inspection of the weld. This cleaning requirement limits the process’s ability to be fully automated. And secondly, as with any welding process that produces slag, FCAW has the possibility of slag inclusions—cavities within the weld caused by the metal solidifying around a pocket of slag. Slag inclusions are discussed in greater depth in Chapter 19.
Finally, FCAW is mostly limited to ferrous materials, including cast iron and stainless steel. Nickel-based alloys, such as Hastelloy and Inconel™, are the exception to FCAW’s general limitation to ferrous metals. Commonly welded non-ferrous metals like aluminum, titanium, copper, and copper alloys (brass, bronze, etc.) must be joined by another process.
Uses of FCAW in Industry Today
Although FCAW is limited to ferrous metals, it is used in various industries, as these metals, steel in particular, make up the majority of materials joined by arc welding in our present day. The process’s fast travel speeds, high weld metal deposition rates, and suitability for outdoor welding environments make FCAW extremely popular in what’s considered heavy industry: structural fabrication and construction, maritime, railroad, automotive, mining, and heavy equipment manufacturing industries. They all share a need for high-quality welds produced quickly and at an economical cost.
Another characteristic that ties these industries together is that they all employ a variety of steels. Later in this textbook, there will be a discussion of how the alloy content of steel, and the carbon content in particular, is an important determinant of how difficult it is to weld. FCAW can be successfully employed to weld a wide variety of carbon and low-alloy steels. Hardened and abrasion-resistant steels may also be readily welded with FCAW, provided the proper electrode and welding techniques are used. There are also FCAW electrodes for welding stainless steel and nickel alloys.
Attributions
- Figure 9.1: Roy Bearden performs flux cored arc welding on an M1 tank by Mark Cleghorn in the Public Domain; United States government work
- Figure 9.2: FCAW Weld Pool Diagram by Nicholas Malara, for WA Open ProfTech, © SBCTC, CC BY 4.0
An electrode is the part of a welding system that conducts electricity and produces the arc.
Flux is a powdered mixture of chemicals designed to benefit the weld by forming shielding gas and slag to protect the weld, providing alloying elements to make the weld stronger, using deoxidizers to remove contaminants from the weld, and providing fluxing agents to help the weld wet into the base metal.
A, usually, non-reactive gas piped into the weld area to purge away reactive atmospheric gasses which would negatively interact with the molten weld pool
A metal where iron is the main base consituent.
Deoxidizing and denitrifying are accomplished by the addition of certain elements, like aluminum and magnesium, to the welding flux. In the molten weld puddle these elements bond with nitrogen and oxygen present in the weld area which prevents the formation of nitrides and oxides in the completed weld, which can impact the integrity of the weld
The distance the wire electrode extends past the contact tip before engaging with the work. It can often be referred to as electrode stickout or just stickout. Stickout is commonly abbreviated as CTWD, or Contact Tip to Work Distance, on welding documentation.
A welding process in which the welder manipulates all aspects of the weld by hand, except for the wire-feed speed which is controlled by the feed unit.
In mechanized welding all aspects of the process, travel speed, electrode angle, and electrical stickout, are maintained by a machine, however that machine must be under constant observation of a welder-operator to ensure proper welding.
in automated welding all aspects of the welding process are pre-programmed into an automatic welding machine, typically a CNC robotic arm. The machine can weld without the constant observation and intervention of a human operator
Refers to materials which contain no iron.