Chapter 15: Weld Identification
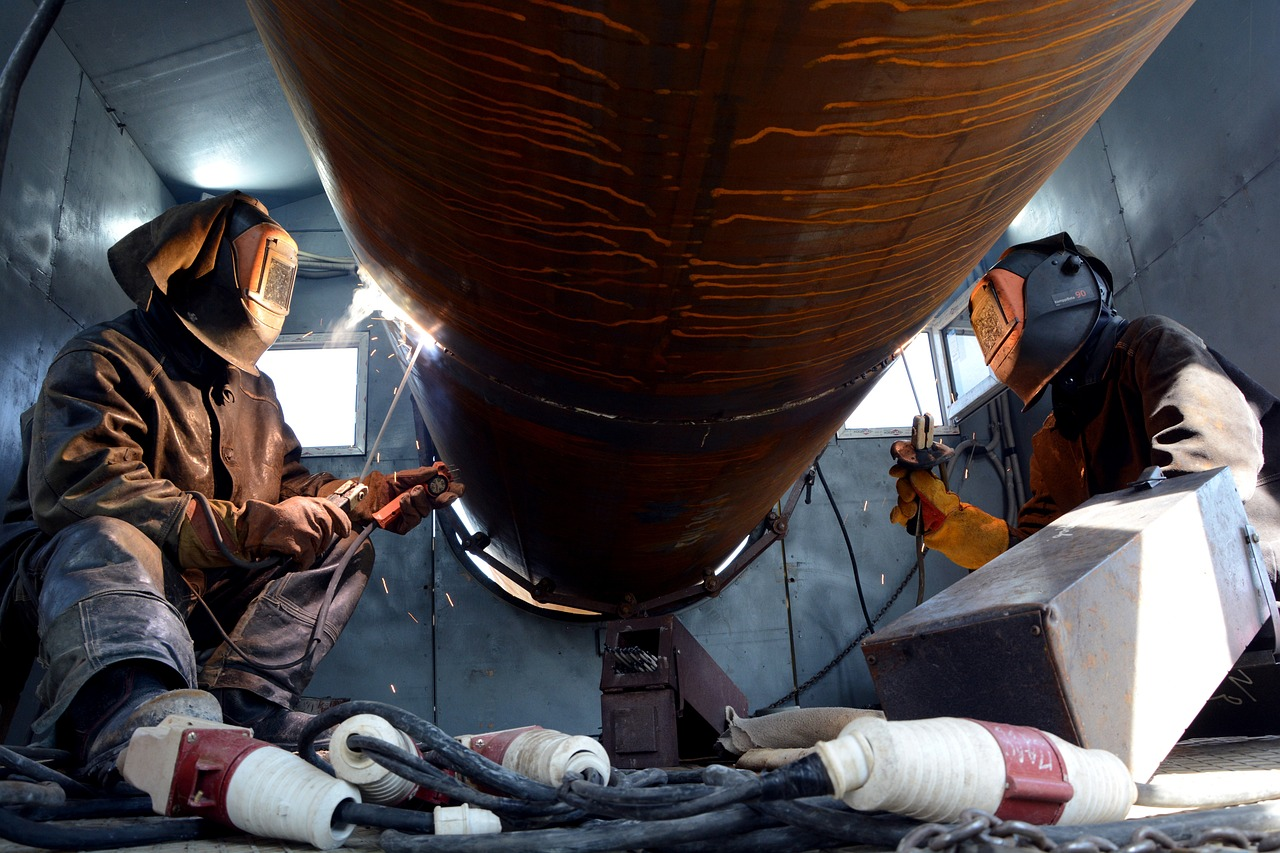
Overview
“Is there enough throat on that fillet weld”?
“Make sure the root opening on that butt joint is a least one-quarter inch.”
“Don’t forget that V-groove is supposed to have complete penetration.”
“We’ll need you to pass a 3G test if you’d like employment here.”
What information can you glean from these statements? Any? They contain a lot of terms that are unfamiliar for the uninitiated, so if you can’t interpret their meanings right now, it’s no reason to worry. However, these statements are everyday shop talk in a fabrication environment, and necessary for communicating about common welding tasks.
The goal of this chapter is to help you build a vocabulary for a competent career in welding. In the following pages, we’ll cover the terms and principles necessary to identify different types of welds, the parts of those welds, how their size is determined, and the different welding positions.
Objectives
After completing this chapter, students will be able to:
- Identify joint types.
- Identify weld types.
- Define different welding positions.
Key Terms
- Base metal
- Bevel
- Edge preparation
- Filler metal
- Fillet weld
- Groove angle
- Groove welds
- Joint root
- Manual
- Resistance welding
- Root opening
- Semiautomatic
- Splice joint
- Weld axis
- Weld face
- Weld joint
- Weld legs
- Weld metal
- Welding position
- Weld profile
Attributions
- Chapter opening image: image released under the Pixabay License