8.3 SMAW Electrodes
David Ridge
Electrode Classification
There are dozens of different SMAW electrodes on the market today to go along with the wide variety of metals that need to be welded. In all welding applications that require a filler metal, it is important to match that filler metal with the base metal since not all metals bond well to each other and welds made with metals that are too dissimilar to each other are likely to fail. For example, you would want to weld a steel alloy base metal with a steel alloy filler metal, a stainless steel with a similar stainless steel, and a titanium alloy with titanium. You would not try to weld steel with titanium filler metal, as the two would not mix well. Even within these broad categories of metals, it is necessary to accommodate the many variations in the type of base metal alloy. For instance, a high-strength steel would need to be welded with a similar high-strength steel filler metal. Additionally, some elements in the flux make different electrodes suitable for some applications but not others, such as electrodes that keep a weld low in hydrogen, a major cause of weld failure, versus an electrode that can weld underwater, a major source of hydrogen.
With all that being said, it is very important to be able to identify the filler metal you are working with. Since most metals cannot be easily identified just by looking at them, the AWS has devised the filler metal classification system, which is composed of letter and number codes that are printed on the electrodes themselves or on their packaging (American Welding Society, 2012).
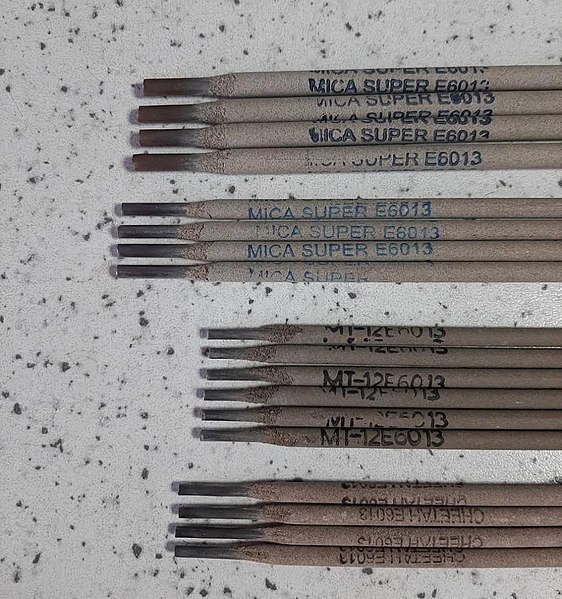
With a quick glance, this system allows you to have the basic information needed in order to use the electrode properly. Each letter and number in the system has a meaning, appearing in the following order: prefix, tensile strength, welding position, flux type/polarity requirements, and suffix/additional requirements met (if any). The sections that follow discuss each component of this system in detail.
Before we begin, it is worth mentioning that it is in your best interest to memorize the order of the classification system so you can pick up how to read a SMAW electrode classification more quickly.
Finally, in the following sections the system covered is for identifying SMAW electrodes for welding carbon steel. There are separate filler metal classification systems for each different type of filler metal/electrode for each welding process. Those will be discussed in their respective chapters.
Prefix
The basic filler metal classification system for carbon steel electrodes takes this form: the capital letter E followed by four or five numbers.
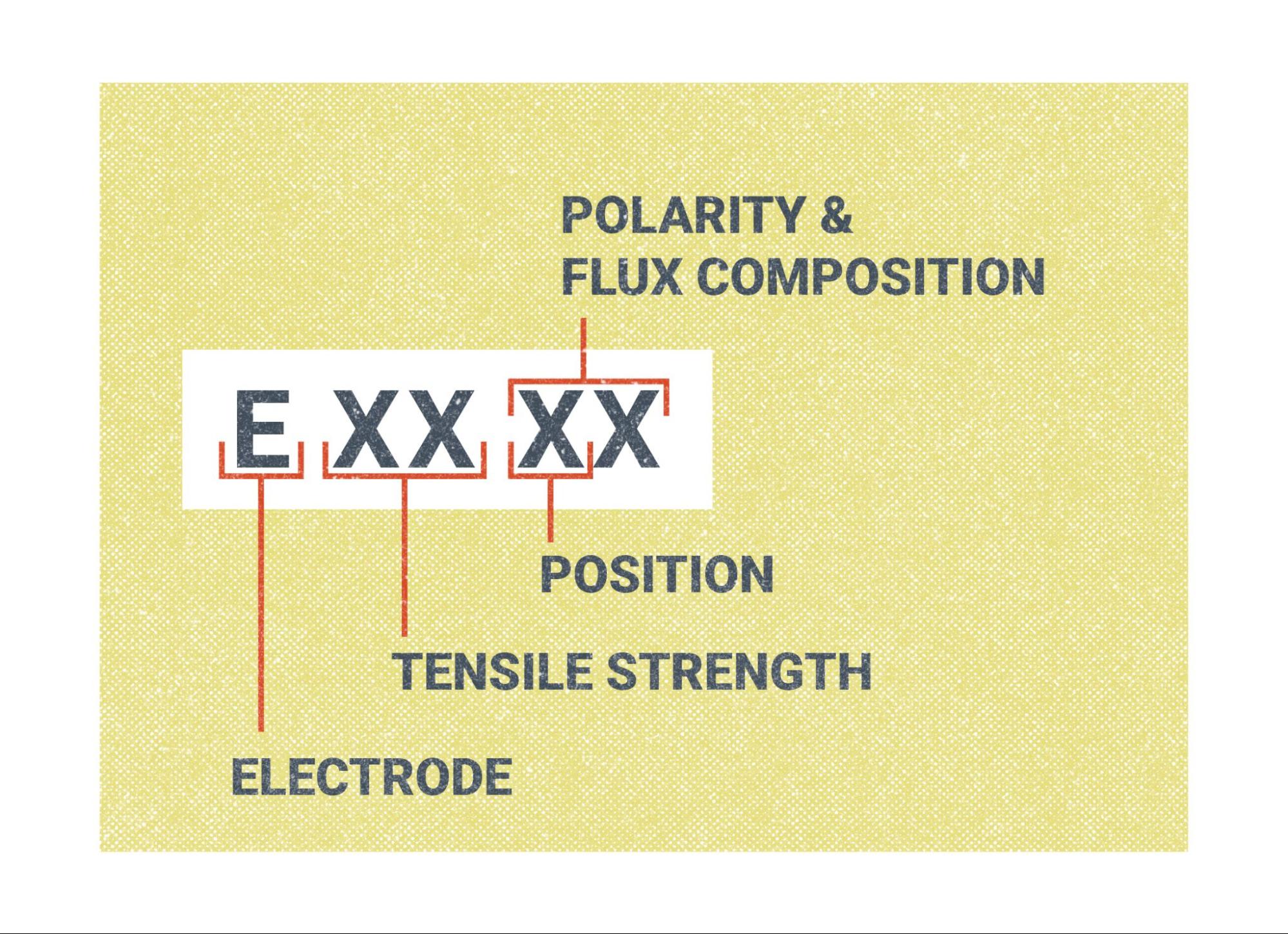
The letter at the beginning of the classification is called the prefix and it tells you what form the filler metal takes. In the case of SMAW, the prefix will always be the letter E, which stands for “electrode.” For a filler metal to be classified as an electrode, the welding current must pass through it to complete the circuit. This is always true for the SMAW process. Not all welding processes use an electrode as a filler metal, so the prefixes for those classifications will differ.
Tensile Strength
Tensile strength is a measure of the force required to pull something apart. In the case of a weld, it is the force required to break the weld by pulling it apart. This is measured in thousands of pounds per square inch (example: 70,000 psi or 70 ksi).
The two or possibly three numbers that follow the prefix in the classification indicate the filler metal’s minimum tensile strength in the as welded condition (see Figure 8.17). For example, in the classification E6010, the 60 indicates that the minimum tensile strength for a weld made with this electrode is 60,000 psi. For a classification like E7018 the tensile strength would be 70,000 psi, and for E11018 it would be 110,000 psi. Be sure to look out for whether this portion of the classification is indicated by two or three digits.
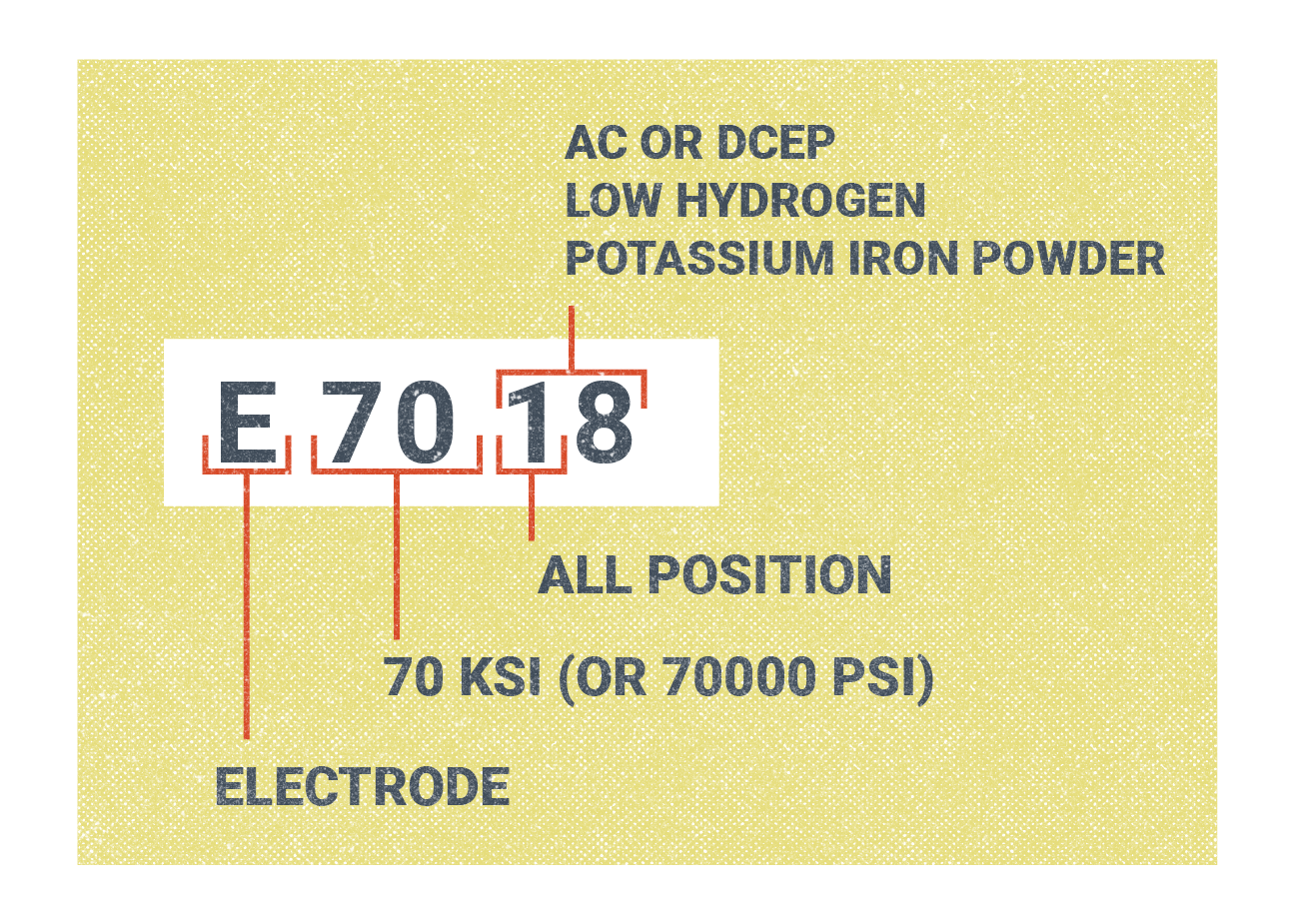
Class | Min. Tensile Strength | Min. Yield Strength |
---|---|---|
E60xx | 62,000 psi | 50,000 psi |
E70xx | 70,000 psi | 57,000 psi |
E80xx | 80,000 psi | 67,000 psi |
E90xx | 90,000 psi | 77,000 psi |
E100xx | 100,000 psi | 87,000 psi |
E110xx | 110,000 psi | 95,000 psi |
E120xx | 120,000 psi | 107,000 psi |
One thing to note is that this rating is designed to meet the minimum tensile strength required for the weld if welding is performed correctly. These electrodes can generally produce a weld with a tensile strength anywhere from 1% to 20% higher than they are rated for. This is not an excuse for any welder, fabricator, or design engineer to exceed the rated tensile strength for a filler metal when designing or building a weldment or welded structure, however. It is generally better to have more strength in a weld than necessary.
Welding Position
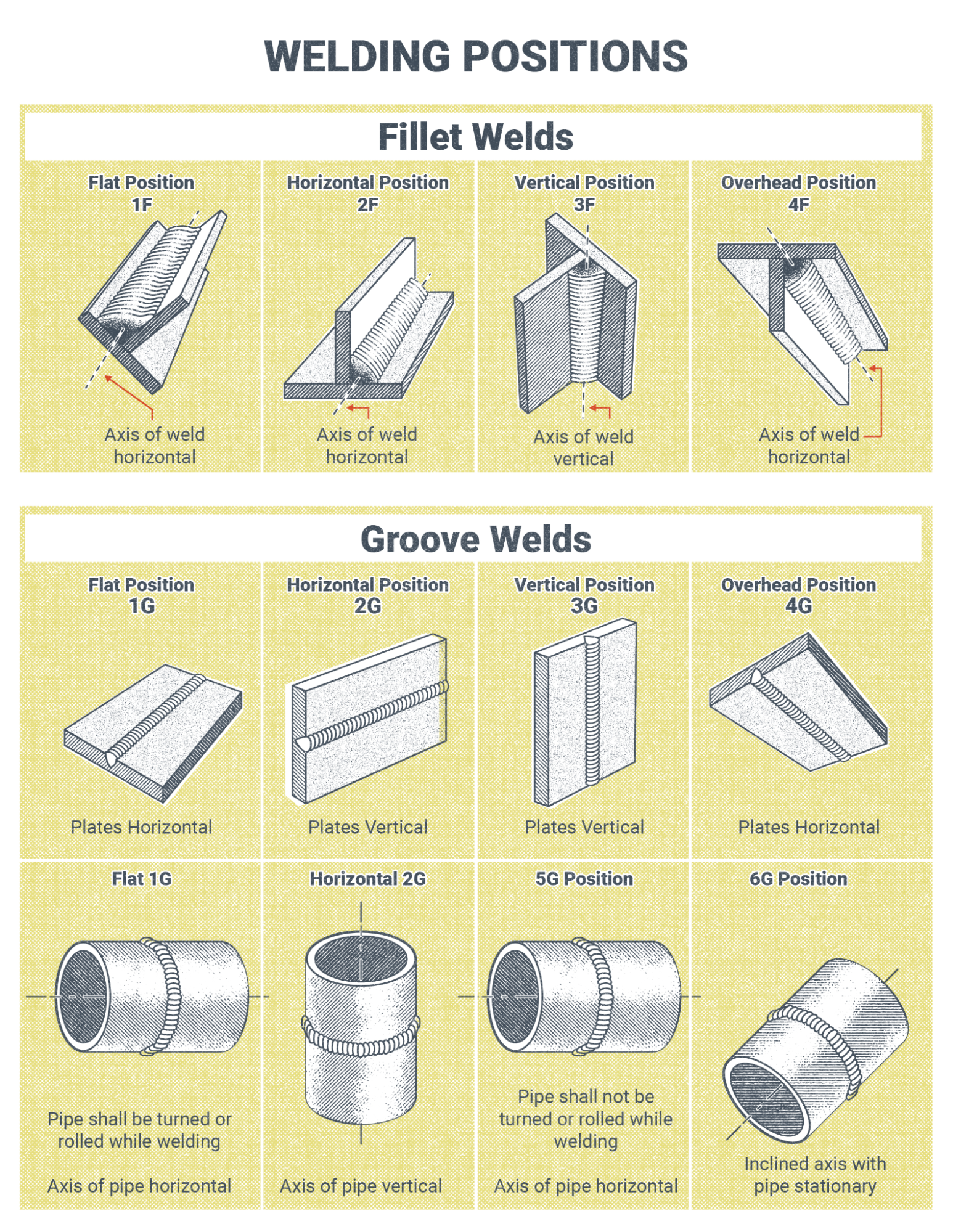
The single number after the tensile strength designator indicates the welding position(s) that this electrode can be used in (see Figure 8.19). The number 1 in this space indicates that the electrode can be used in all positions. The number 2 indicates that the electrode can only be used for welds in the flat position (1F, 1G) and for horizontal fillet welds (2F). The number 4 indicates that the electrode can be used in all positions—but when welding in the vertical position (3F, 3G) the weld progression must be down instead of up. (Welding positions are discussed in greater detail in Chapter 15.)
Electrode Classification | Type of Flux Coating | Welding Position(s) | Type of Current |
---|---|---|---|
E6010 | High cellulose sodium | Flat, Vertical, Overhead, Horizontal | DCEP |
E6011 | High cellulose potassium | Flat, Vertical, Overhead, Horizontal | AC, DCEP |
E6012 | High titania sodium | Flat, Vertical, Overhead, Horizontal | AC, DCEN |
E6013 | High titania potassium | Flat, Vertical, Overhead, Horizontal | AC, DCEP, DCEN |
E6018 | Low-hydrogen potassium, iron powder | Flat, Vertical, Overhead, Horizontal | AC, DCEP |
E6019 | Iron oxide titania potassium | Flat, Vertical, Overhead, Horizontal | AC, DCEP, DCEN |
E6020 | High iron oxide | Flat, Horizontal fillet | AC, DCEP, DCEN (Flat only) |
E6022 | High iron oxide | Flat, Horizontal fillet | AC, DCEN |
E6027 | High iron oxide, iron powder | Flat, Horizontal fillet | AC, DCEP, DCEN (Flat only) |
E7014 | Iron powder, titania | Flat, Vertical, Overhead, Horizontal | AC, DCEP, DCEN |
E7015 | Low-hydrogen sodium | Flat, Vertical, Overhead, Horizontal | DCEP |
E7016 | Low-hydrogen potassium | Flat, Vertical, Overhead, Horizontal | AC, DCEP |
E7018 | Low-hydrogen potassium, iron powder | Flat, Vertical, Overhead, Horizontal | AC, DCEP |
E7018M | Low-hydrogen iron powder | Flat, Vertical, Overhead, Horizontal | DCEP |
E7024 | Iron powder, titania | Flat, Horizontal fillet | AC, DCEP, DCEN |
E7027 | High iron oxide, iron powder | Flat, Horizontal fillet | AC, DCEP, DCEN (Flat only) |
E7028 | Low-hydrogen potassium, iron powder | Flat, Horizontal fillet | AC, DCEP |
E7048 | Low-hydrogen potassium, iron powder | Flat, Overhead, Horizontal, Vertical down | AC, DCEP |
You may have noticed that the number 3 was skipped in the system with 1, 2, and 4 used. The AWS no longer uses the number 3 to indicate welding position because the electrodes that had a 3 designation are now obsolete.
Flux Composition and Polarity
The last number, when combined with the position designator, indicates the type of flux coating the electrode has, which in turn determines which polarity (or polarities) the electrode can be used with (see Table 8.2).
Last Digit | Type of Flux Coating | Type of Current |
---|---|---|
EXXX0 | High cellulose sodium | DCEP |
EXXX1 | High cellulose potassium | AC, DCEP, DCEN |
EXXX2 | High titania sodium | AC, DCEN |
EXXX3 | High titania potassium | AC, DCEP, DCEN |
EXXX4 | Iron powder, titania | AC, DCEP, DCEN |
EXXX5 | Low-hydrogen sodium | DCEP |
EXXX6 | Low-hydrogen potassium | AC, DCEP |
EXXX7 | High iron oxide, iron powder | AC, DCEP, DCEN |
EXXX8 | Low-hydrogen potassium, iron powder | AC, DCEP, DCEN |
EXXX9 | Iron oxide titania potassium | AC, DCEP, DCEN |
As previously stated, the flux coating is a very important part of the SMAW process. During welding, it provides shielding for the weld in the form of a shielding gas and a coating of slag. It also provides alloying elements, deoxidizers, fluxing agents, and arc stabilizers. Additionally, the makeup of the flux determines the polarity required for each specific electrode and affects the arc’s electrical characteristics.
While all of these elements are true of each type of flux, they are all achieved in different proportions through different mixtures of flux components. The flux is a powder made from a mixture of different metals and minerals that is baked onto the electrodes. The numbers 0-8, in combination with the position designator, indicate the type of flux mixture used (refer to Table 8.3). Each different flux mixture produces different welding characteristics for each type of electrode.
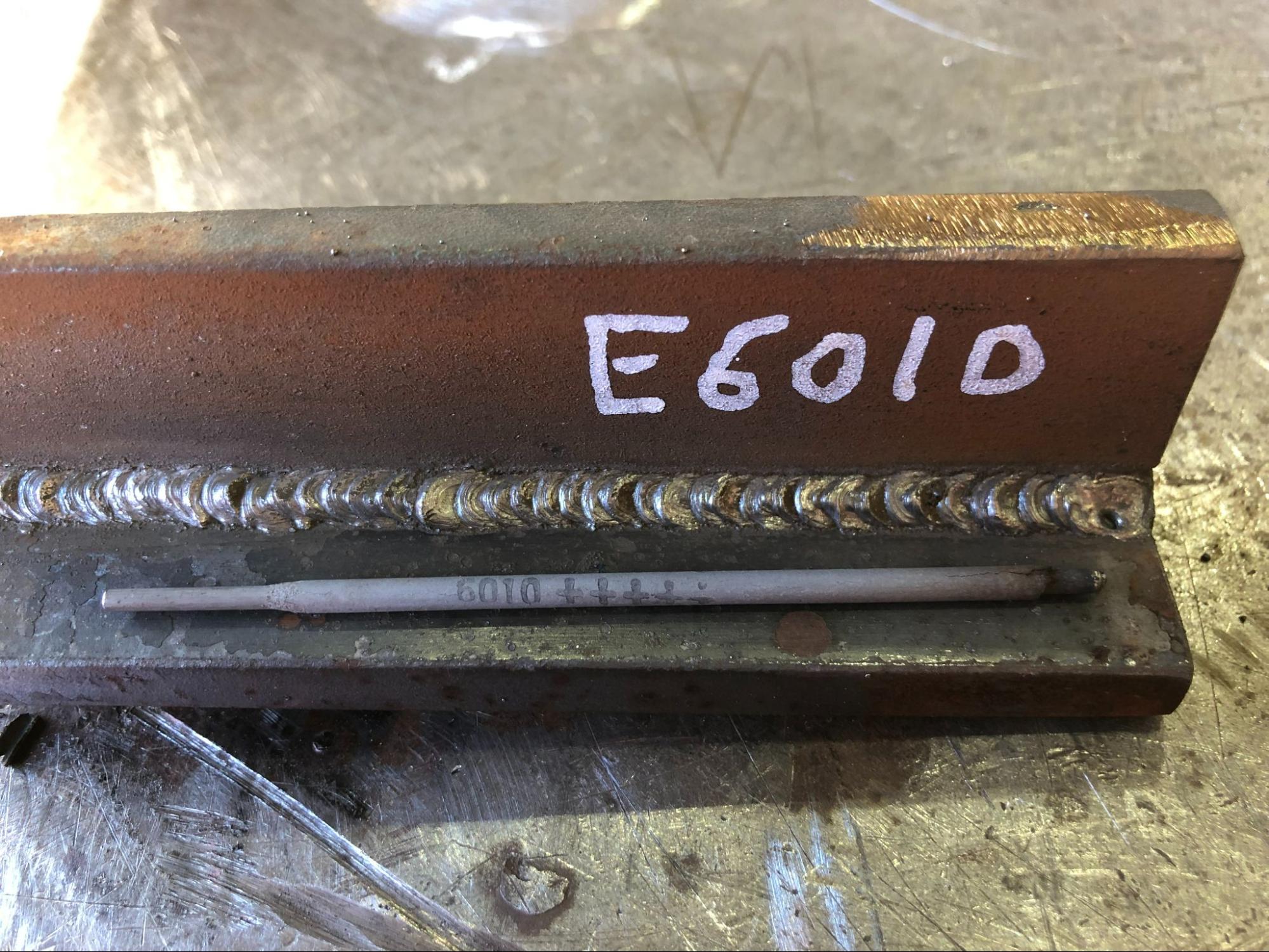
For example, E6010 has a cellulose-based flux. This flux makes a violent digging arc that achieves greater weld penetration than other fluxes and leaves a small weld with a rough surface texture and a light coating of slag. It also causes the weld to solidify quickly (called a “fast freeze”) and allows this electrode to be less affected by surface contamination, such as oxides (rust) or moisture. In fact, E6010 is the electrode used for underwater welding. The primary use for E6010 today is tacking and making the root pass on multi-pass welds.
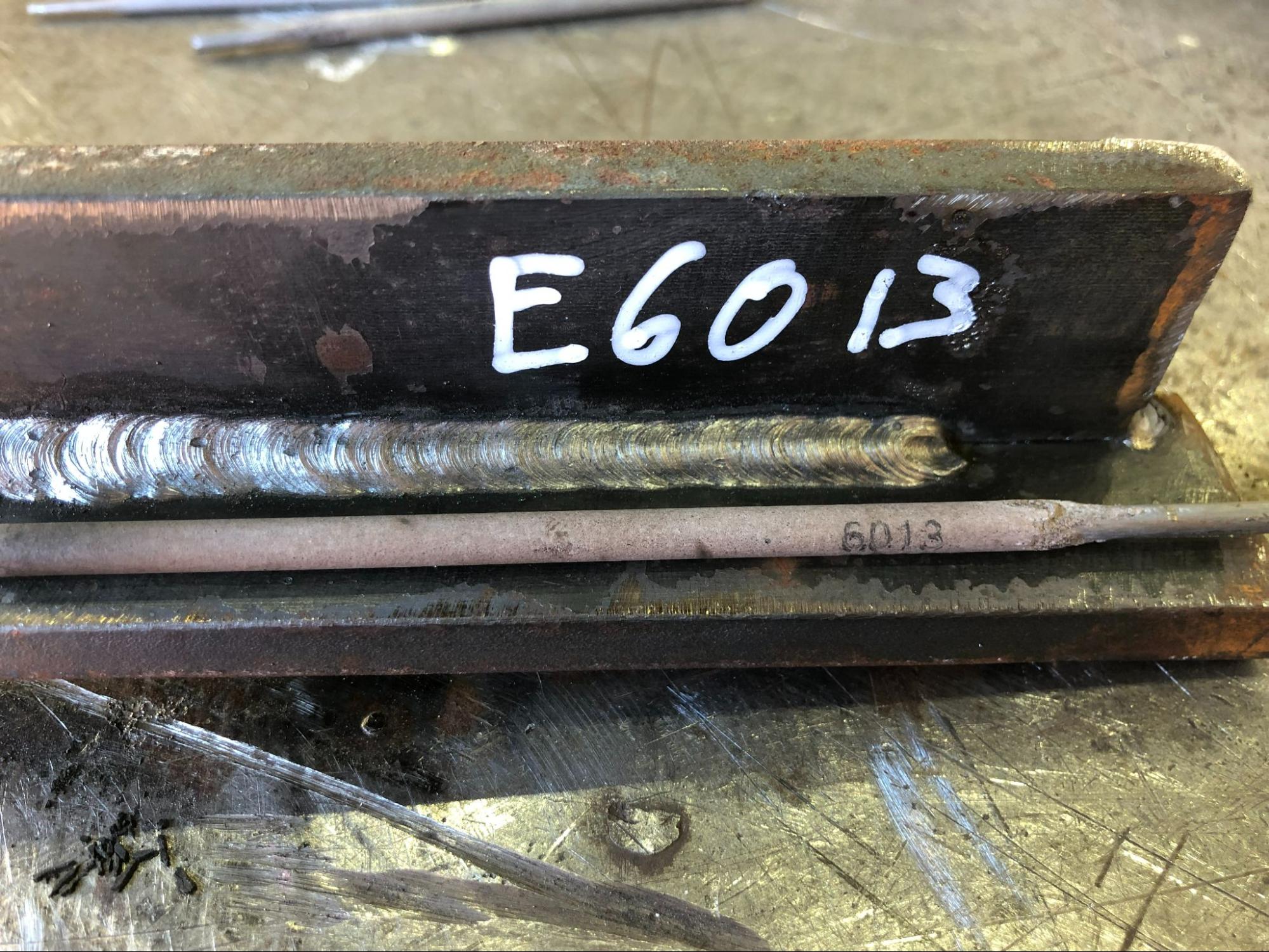
In contrast, E6013 has a titania-based flux, which gives it a soft arc with little penetration. The weld tends to be wide and smooth and has a heavy slag cover. These electrodes are more susceptible to contamination on the base metal surface, requiring more cleaning to be done before welding. E6013 was designed for use on sheet metal and light-duty steel parts.
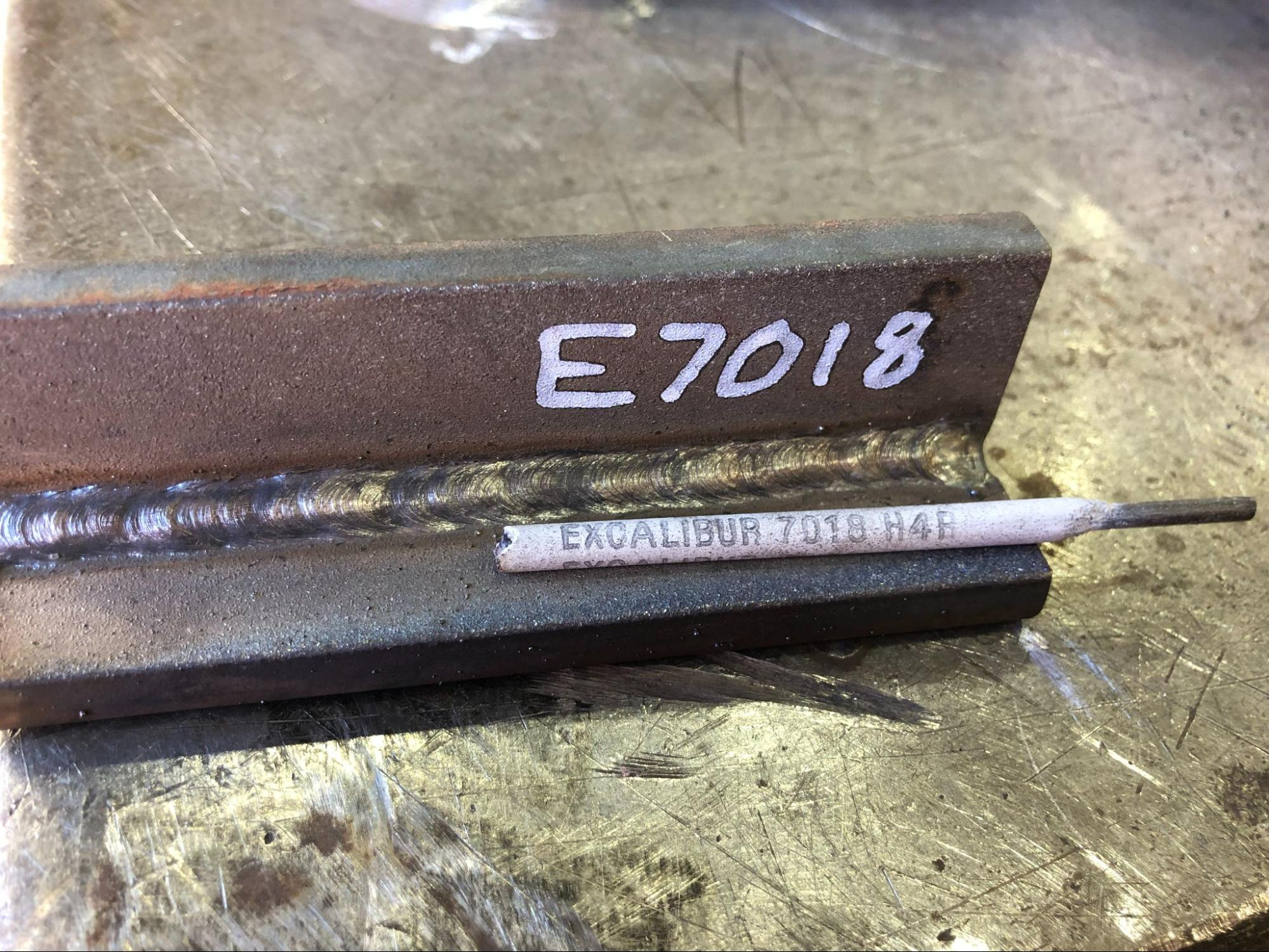
The workhorse of the stick welding industry is E7018. The potassium/iron powder flux creates a soft arc with moderate weld penetration. The weld produced is wide and smooth with a heavy slag cover and high strength and ductility properties. This makes the electrodes highly susceptible to contamination, especially from hydrogen (the primary element in water). Called low-hydrogen electrodes, they must be kept in a special rod oven to prevent moisture in the air from saturating the flux. Proper cleaning and weld zone preparation are also necessary before welding when using these electrodes. Industrial steel fabrication and construction projects requiring stick welding are often welded with E7018.
As a reminder, the polarity for each electrode is determined by the chemistry of the flux. For example, E6010 has a cellulose/sodium flux and can only be run on DCEP. However , because of certain equipment needs, welders wanted to be able to run E6010 on AC instead. By changing the flux to a cellulose/potassium mixture, the manufacturers created E6011, which is essentially the same electrode as E6010 but has the capability to run on either AC or DCEP. The titania/potassium flux of E6013 allows it to be run on AC, DCEP, or DCEN.
While it is useful to memorize the order of the classification system, it is less important that you memorize the characteristics of each individual electrode based on the flux number—as long as you know where to look the information up when you need it. Every type of electrode has product information that can easily be obtained from the manufacturer for free. You can find the polarity and amperage requirements for each electrode and some indications of the techniques used in welding with them. If you cannot locate this information, be sure to ask your instructor or welding supervisor for help.
Learning how to run each electrode correctly is a matter of experience. In the welding industry, the type of electrode to be used on any job is determined by the project engineer, so you will not be responsible for electrode selection (unless you are running your own welding business). Rather, your responsibility as a welder is to know how to weld with electrodes.
Suffix and Additional Requirements Met
On some electrodes you may see several additional letters and numbers following the primary electrode classification. These are the suffix and the additional welding requirements met by this electrode.
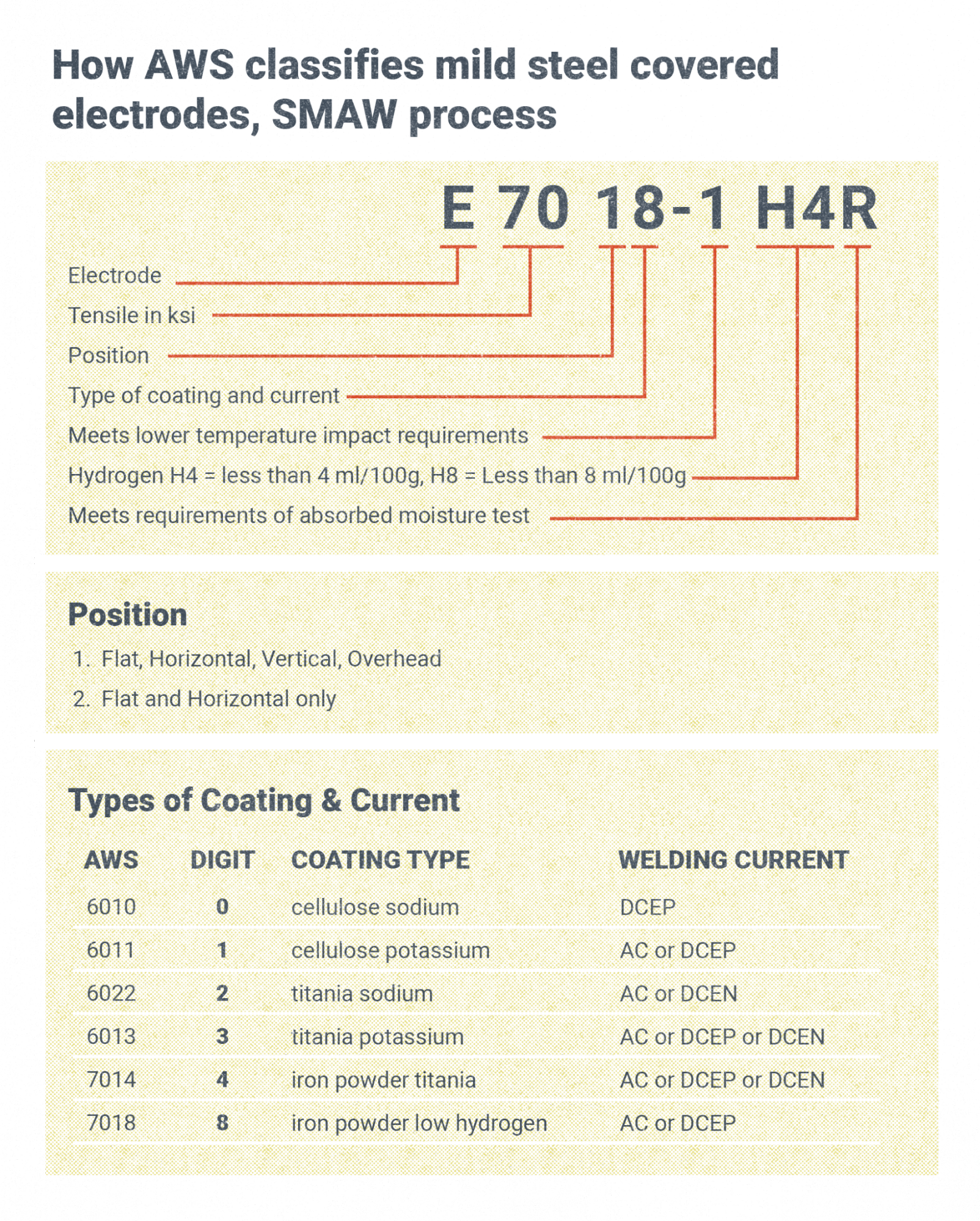
If it is present on the electrode, the suffix will be a combination of one letter and one number, such as A1 or C3. They stand for the approximate alloying composition of the finished weld. For example, H4 indicates that the finished weld will contain no more than four parts per million of diffused hydrogen. This is often seen on E7018 rods, as these are low-hydrogen electrodes.
If there are letters or numbers after the suffix, they indicate certain welding requirements that specific type of electrode meets. In Figure 8.24, the R indicates the electrode meets the requirements of absorbed moisture tests.
While this additional information can be helpful to you in certain circumstances when selecting or using electrodes, it is not critical for you to memorize.
Attributions
- Figure 8.16: Types of welding electrode by Ghasemimoshref is released under CC BY-SA 4.0
- Figure 8.17: SMAW Electrode Classification © American Welding Society, illustration by Nicholas Malara (SBCTC Illustrator) Used with permission from the rights holder, the American Welding Society.
- Figure 8.18: Example of SMAW Electrode Classification © American Welding Society, illustration by Nicholas Malara (SBCTC Illustrator) Used with permission from the rights holder, the American Welding Society.
- Figure 8.19: SMAW AC Setup by Nicholas Malara, for WA Open ProfTech, © SBCTC, CC BY 4.0
- Figure 8.20: E6010 by David Ridge, for WA Open ProfTech, © SBCTC, CC BY 4.0
- Figure 8.21: E6013 by David Ridge, for WA Open ProfTech, © SBCTC, CC BY 4.0
- Figure 8.22: E7018 by David Ridge, for WA Open ProfTech, © SBCTC, CC BY 4.0
- Figure 8.23: Weld Beads Made By Different Electrodes by David Ridge, for WA Open ProfTech, © SBCTC, CC BY 4.0
- Figure 8.24: Suffix and Additional Requirements © American Welding Society, illustration by Nicholas Malara (SBCTC Illustrator) Used with permission from the rights holder, the American Welding Society.
Flux is a powdered mixture of chemicals designed to benefit the weld by forming shielding gas and slag to protect the weld, providing alloying elements to make the weld stronger, using deoxidizers to remove contaminants from the weld, and providing fluxing agents to help the weld wet into the base metal.
Carbon steel is any of the various steel alloys whose primary chemical elements are iron and carbon in varying amounts.
A weldment is anything composed primarily of metal and is held together by welding.
Weld penetration is depth to which the weld has intermingled with the base metal.